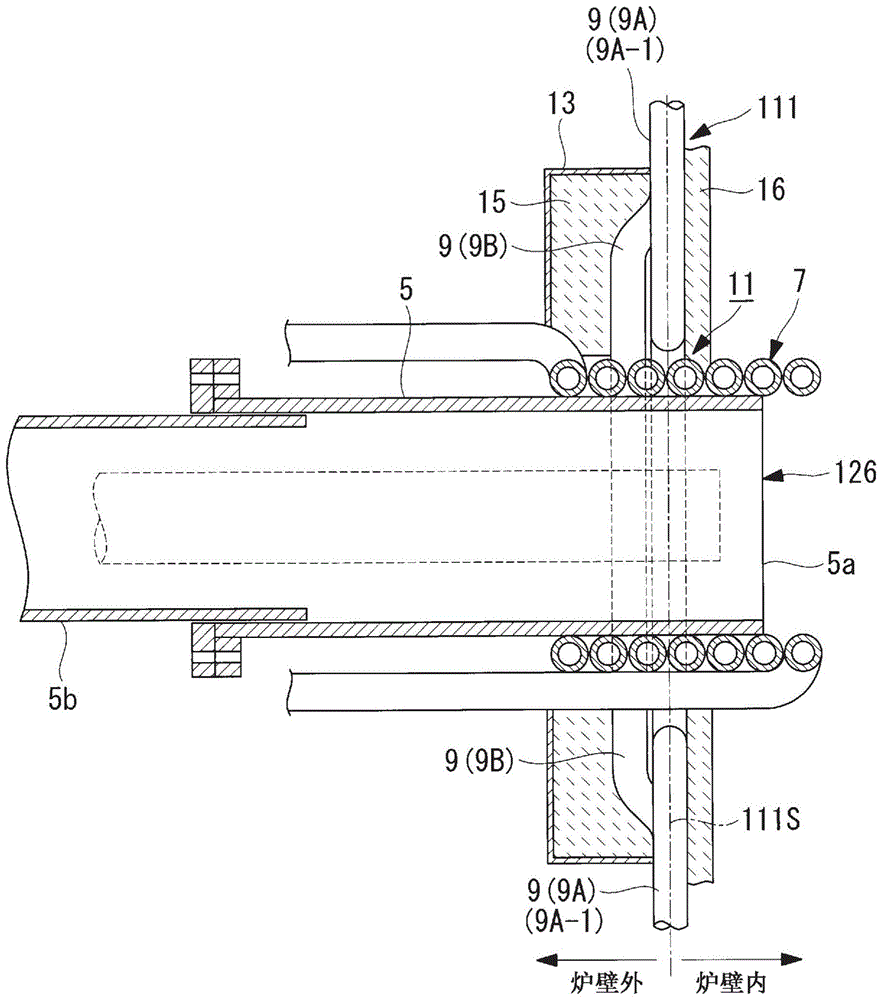
本公开涉及冷却壁、气化炉、气化复合发电设备及冷却壁的制造方法。
背景技术:
以往,作为气化炉设备,已知有将煤等含碳固体燃料向气化炉内供给,使含碳固体燃料部分燃烧而气化,从而生成可燃性气体的含碳燃料气化设备(煤气化设备)。
例如,气化炉通过利用氧化剂(空气、氧)使被供给到内部的将煤粉碎后的煤粉即燃料粉(含碳固体燃料)及焦炭(煤的未反应部分及灰分)部分燃烧来使其气化,生成可燃性气体。气化炉具有压力容器和设置于压力容器的内部的气化炉壁。
在气化炉壁的内部的空间,从铅垂方向的下方侧(即,生成气体的流通方向的上游侧)起依次形成有燃烧室部、扩散器部、减压器部。在燃烧室部中的气化炉壁插入配置有多个燃烧器。
气化炉壁例如也在下述的专利文献1中公开那样,由在内部流通水等冷却介质的多个冷却管(炉壁管)构成为壁状,燃烧器由燃烧器用冷却管包围而设置。
现有技术文献
专利文献
专利文献1:日本特开2014-152988号公报
技术实现要素:
发明所要解决的课题
气化炉壁具有配置于多个炉壁管(冷却管)之间的由金属板构成的翅片。炉壁管与翅片彼此通过焊接而接合(该结构也被称作膜构造。)。由此,向气化炉壁的炉壁管内有效地传热而向比气化炉壁靠外侧的传热减低,比气化炉壁靠内侧的内部空间的气密性得以保持。另外,2根炉壁管之间的翅片宽度根据向炉壁管内的传热性而设为上限值(规定值)以下,防止翅片的烧损。
在燃烧室部的气化炉壁,与燃烧器的设置部位相匹配地,形成多个供燃烧器插入的开口部。各开口部通过使炉壁管的一部分朝向炉外侧且在周向上也弯曲而形成。此外,在开口部以外的区域,炉壁管通常保持着直管的状态而配置。以往,配置于开口部的周围的多根炉壁管以上述的翅片宽度不超过上限值的方式,且以通过多根炉壁管形成渐扩的大致圆台(立体)形状的方式,分别被进行管弯曲加工而弯曲。
另外,为了减小燃烧器与炉壁管之间的间隙,配置形成为弯曲的炉壁管,并且在比气化炉壁靠炉外侧设置密封盒,从而防止气体从内部空间泄漏。而且,在密封盒内部填充耐火材料。
上述的以往的配置于开口部的周围的多个炉壁管,为了形成燃烧器插入用的开口部,向比气化炉壁的壁面靠炉外侧弯曲而配置。在此,所谓壁面,是由多个炉壁管的直线状部分构成的面。越是靠近燃烧器的中心轴的炉壁管,则弯曲至越远离气化炉壁的壁面的位置,多个炉壁管以大致圆台形状围绕燃烧器。大致圆台形状内部的燃烧器是暴露于炉内部空间的高温气体的部分,且燃烧器的顶端向比气化炉壁的壁面部分靠炉内部空间侧突出而设置。因而,另外于炉壁管,在燃烧器的周围,以缠绕为螺旋状的状态设置有具有筒形状的燃烧器用冷却管,冷却管防止了燃烧器的高温化。
另外,形成大致圆台形状的炉壁管的形状复杂,且要求用于确保与燃烧器外周的紧贴性的加工精度。而且,为保持密封盒内部的耐火材料,需要高精度地配置炉壁管。从这一点来说,炉壁管也要求相应的加工精度,存在作业工时增加这一问题。
本公开是鉴于这样的情形而完成的,其目的在于,提供一种能够减低配置于炉壁内而暴露于炉内部的高温气体的部分且简化开口部构造的冷却壁、气化炉、气化复合发电设备及冷却壁的制造方法。
用于解决课题的技术方案
本公开的第一方案的冷却壁具备:壁面,由在内部流动冷却介质的多个冷却管的轴中心排列形成;和开口部,形成于所述壁面的一部分,能够供燃烧器插入设置,形成所述开口部的所述多个冷却管分别具有直线形状部分和弯曲形状部分,所述多个冷却管具有:第一冷却管,在所述直线形状部分的轴向上延长的第一假想轴与所述开口部重叠;和第二冷却管,在所述直线形状部分的轴向上延长的第二假想轴位于比所述开口部外周靠径向外侧处,所述第一冷却管的所述弯曲形状部分沿着所述开口部的外周面,在沿着所述壁面的面内形成弯曲而配置,或者,以规定间隔以下从所述壁面向正交的方向分隔并形成弯曲而配置,所述第二冷却管的所述弯曲形状部分在与所述壁面正交的方向上与所述第一冷却管分隔并形成弯曲而配置。
由此,不会使第一冷却管的弯曲形状成为复杂的形状,能够沿着壁面以被多个第一冷却管包围的方式形成开口部。并且,燃烧器以配置于壁面内的第一冷却管为界,插入开口部而设置。另外,第二冷却管不会使弯曲形状成为复杂的形状,能够避免与第一冷却管的干涉。因而,与冷却管的被弯曲的部分从壁面突出而配置成大致圆台状的以往的结构相比,能够简化开口部构造。
也可以是,在上述第一方案的基础上,所述第一冷却管的所述弯曲形状部分将所述规定间隔设为与所述第一冷却管的直径同一长度的间距量以下,从所述壁面向正交的方向分隔而配置。
根据该结构,通过将第一冷却管的弯曲形状部分从壁面分隔而配置,不将设置于多个第一冷却管之间的翅片的间隔扩大到规定间隔以上而第一冷却管变得容易配置,所以,能够抑制第一冷却管的传热量的减少。
也可以是,在上述第一方案的基础上,在所述多个冷却管之间配置翅片,所述壁面形成为筒状,相对于所述壁面在内侧通过所述燃烧器生成燃烧气体。
根据该结构,在多个冷却管之间配置翅片,壁面形成为筒状。在壁面的炉内侧,通过燃烧器生成燃烧气体。因而,与冷却管的成为了弯曲形状的部分从壁面突出而配置成大致圆台状的以往的结构相比,燃烧器暴露于高温的燃烧气体的部分减低。
也可以是,在上述第一方案的基础上,多根所述第一冷却管的所述弯曲形状部分配置于沿着所述壁面的面内。
根据该结构,多根第一冷却管配置于沿着壁面的面内,简易地形成开口部。
也可以是,在上述第一方案的基础上,多根所述第二冷却管的所述弯曲形状部分相对于所述第一冷却管配置于所述壁面的径向外侧。
根据该结构,多根第二冷却管配置于比多个第一冷却管靠壁面的径向外侧,所以,简易地形成开口部。
也可以是,在上述第一方案的基础上,还具备密闭部,该密闭部相对于所述开口部的周围的所述壁面设置于内侧,具有耐火材料。
根据该结构,密闭部具有耐火材料,设置于开口部的周围的壁面的内侧,所以,通过使冷却壁的热传递降低,设置于冷却管之间的翅片宽度的制约减低,能够成为平面弯曲构造而简易地形成开口部。
也可以是,在上述第一方案的基础上,还具备密闭容器,该密闭容器相对于所述开口部的周围的所述壁面设置于外侧,与所述壁面的外侧和所述燃烧器连接,在所述密闭容器内部填充有耐火材料。
根据该结构,在密闭容器内填充有耐火材料,密闭容器设置于开口部的周围的壁面的炉外侧与燃烧器之间,所以,防止燃烧气体从壁面的炉内侧的空间泄漏。
也可以是,在上述第一方案的基础上,所述密闭容器内的所述耐火材料从设置于所述燃烧器的周围的燃烧器用冷却管分隔并以能够拆装所述密闭容器的方式配置。
根据该结构,密闭容器内的耐火材料不与燃烧器用冷却管紧贴而是分隔地配置,所以,能够使从耐火材料卸下燃烧器用冷却管时的更换变得容易。
本公开的第二方案的气化炉,具备上述第一方案的冷却壁。
本公开的第三方案的气化复合发电设备具备:气化炉设备,通过使含碳固体燃料燃烧、气化而生成生成气体,具备上述第一方案的所述冷却壁;燃气涡轮,通过使在所述气化炉设备生成的生成气体的至少一部分燃烧而旋转驱动;蒸气涡轮,通过在导入从所述燃气涡轮排出的涡轮废气的废热回收锅炉生成的蒸气而旋转驱动;以及发电机,连结于所述燃气涡轮和/或所述蒸气涡轮的旋转驱动。
本公开的第四方案的冷却壁的制造方法具备如下步骤:将在内部流动冷却介质的多个冷却管的轴中心排列而形成壁面;和利用分别具有直线形状部分和弯曲形状部分的多个冷却管形成能够供燃烧器插入设置的开口部,形成所述开口部的步骤具有如下步骤:将在所述直线形状部分的轴向上延长的第一假想轴与所述开口部重叠的第一冷却管配置成所述第一冷却管的所述弯曲形状部分沿着所述开口部的外周面在沿着所述壁面的面内形成弯曲,或者,配置成以规定间隔以下从所述壁面向正交的方向分隔并形成弯曲;和将在所述直线形状部分的轴向上延长的第二假想轴位于比所述开口部外周靠径向外侧处的第二冷却管配置成所述第二冷却管的所述弯曲形状部分在与所述壁面正交的方向上与所述第一冷却管分隔并形成弯曲。
发明效果
根据本公开,能够减低配置于炉壁内而暴露于炉内部的高温气体的部分,且简化开口部构造。
附图说明
图1是示出本公开的一实施方式的气化炉壁的纵剖图,示出了设置有燃烧器的气化炉壁的开口部。
图2是示出本公开的一实施方式的气化炉壁的横剖图,示出了设置有燃烧器的气化炉壁的开口部。
图3是示出本公开的一实施方式的气化炉壁的主视图。
图4是本公开的一实施方式的煤气化复合发电设备的概略结构。
图5是示出本公开的一实施方式的气化炉的概略结构图。
图6是示出本公开的一实施方式的气化炉壁的变形例的纵剖图,示出了设置有燃烧器的气化炉壁的开口部。
具体实施方式
以下,关于本公开的一实施方式,参照附图进行说明。图4中,示出应用了本实施方式的气化炉设备的煤气化复合发电设备的概略结构图。
此外,以下,使用上方及下方的表达而进行说明的各构成要素的位置关系,分别示出铅垂上方侧、铅垂下方侧。
应用本实施方式的气化炉设备14的煤气化复合发电设备(igcc:integratedcoalgasificationcombinedcycle,整体煤气化联合循环)1使用空气作为氧化剂,在气化炉设备14中,采用了由燃料生成可燃性气体(生成气体)的空气燃烧方式。并且,煤气化复合发电设备1将在气化炉设备14生成的生成气体在气体精制设备26精制而使其成为燃料气体之后,向燃气涡轮17供给而进行发电。即,实施方式1的煤气化复合发电设备1成为了空气燃烧方式(空气吹入)的发电设备。作为向气化炉设备14供给的燃料,例如使用煤等含碳固体燃料。
如图4所示,煤气化复合发电设备(气化复合发电设备)1具备供煤设备21、气化炉设备14、焦炭回收设备25、气体精制设备26、燃气涡轮17、蒸气涡轮18、发电机19、废热回收锅炉(hrsg:heatrecoverysteamgenerator,余热蒸汽发生器)20。
供煤设备21供给作为含碳固体燃料的煤来作为原煤,通过利用磨煤机(图示略)等将煤粉碎,来制造粉碎成细微的颗粒状的煤粉。在供煤设备21制造出的煤粉,在供煤线21a出口被从后述的空气分离设备42供给的作为搬运用惰性气体的氮气加压,朝向气化炉设备14供给。所谓惰性气体,是含氧率为大约5体积%以下的非活性气体,氮气、二氧化碳气体、氩气等是代表例,但不一定限制为大约5%以下。
在供煤设备21制造出的煤粉向气化炉设备14供给,并且,在焦炭回收设备25回收的焦炭(煤的未反应部分和灰分)返回而以能够再利用的方式向气化炉设备14供给。
另外,在气化炉设备14连接有来自燃气涡轮17(压缩机61)的压缩空气供给线41,在燃气涡轮17压缩了的压缩空气的一部分在升压机68升压为规定压力而能够向气化炉101供给。空气分离设备42从大气中的空气分离生成氮和氧,通过第一氮供给线43将空气分离设备42与气化炉设备14连接起来。并且,在该第一氮供给线43连接有来自供煤设备21的供煤线21a。另外,从第一氮供给线43分支的第二氮供给线45也连接于气化炉设备14,在该第二氮供给线45连接有来自焦炭回收设备25的焦炭返回线46。而且,空气分离设备42通过氧供给线47而与压缩空气供给线41连接。并且,由空气分离设备42分离出的氮流过第一氮供给线43及第二氮供给线45,从而作为煤、焦炭的搬运用气体而被利用。另外,由空气分离设备42分离出的氧流过氧供给线47及压缩空气供给线41,从而在气化炉设备14中作为氧化剂而被利用。
气化炉设备14例如具备两段喷流床形式的气化炉101(参照图5)。气化炉设备14通过利用氧化剂(空气、氧)使被供给到内部的煤(煤粉)及焦炭部分燃烧来使其气化从而使其成为生成气体。此外,气化炉设备14设置有将混入煤粉的异物(废料)去除的异物去除设备48。并且,在该气化炉设备14连接有朝向焦炭回收设备25供给生成气体的生成气体线49,能够排出包含焦炭的生成气体。在该情况下,如图5所示,也可以通过在生成气体线49设置合成气体冷却器102(气体冷却器),在将生成气体冷却至规定温度之后再向焦炭回收设备25供给。
焦炭回收设备25具备集尘设备51和供给料斗52。在该情况下,集尘设备51由1个或多个旋流器、多孔过滤器构成,能够将在气化炉设备14生成的生成气体所含有的焦炭分离。并且,分离出焦炭后的生成气体通过气体排出线53而被送向气体精制设备26。供给料斗52储存在集尘设备51从生成气体分离出的焦炭。此外,也可以构成为在集尘设备51与供给料斗52之间配置料仓,将多个供给料斗52连接于该料仓。并且,来自供给料斗52的焦炭返回线46连接于第二氮供给线45。
气体精制设备26通过针对由焦炭回收设备25分离出焦炭后的生成气体去掉硫化物、氮化物等杂质,来进行气体精制。并且,气体精制设备26将生成气体精制而制造燃料气体,将其向燃气涡轮17供给。此外,分离出焦炭的生成气体中还包含硫分(h2s等),所以,在该气体精制设备26中,利用胺吸收液等去除回收硫分,进行有效利用。
燃气涡轮17具备压缩机61、燃烧器62、涡轮63,压缩机61与涡轮63通过旋转轴64连结。在燃烧器62连接有来自压缩机61的压缩空气供给线65,并且连接有来自气体精制设备26的燃料气体供给线66,另外,连接有朝向涡轮63延伸的燃烧气体供给线67。另外,燃气涡轮17设置有从压缩机61向气化炉设备14延伸的压缩空气供给线41,在中途部设置有升压机68。因此,在燃烧器62中,通过将从压缩机61供给的压缩空气的一部分与从气体精制设备26供给的燃料气体的至少一部分混合并使其燃烧来产生燃烧气体,将所产生的燃烧气体朝向涡轮63供给。并且,涡轮63通过利用被供给的燃烧气体使旋转轴64旋转驱动来使发电机19旋转驱动。
蒸气涡轮18具备连结于燃气涡轮17的旋转轴64的涡轮69,发电机19连结于该旋转轴64的基端部。废热回收锅炉20连接有来自燃气涡轮17(涡轮63)的废气线70,通过在供水与涡轮63的废气之间进行热交换,生成蒸气。并且,废热回收锅炉20在与蒸气涡轮18的涡轮69之间设置有蒸气供给线71并且设置有蒸气回收线72,在蒸气回收线72设置有复水器73。另外,在废热回收锅炉20生成的蒸气也可以包含在气化炉101的合成气体冷却器102与生成气体进行热交换而生成的蒸气。因此,在蒸气涡轮18中,利用从废热回收锅炉20供给的蒸气而涡轮69旋转驱动,通过使旋转轴64旋转来使发电机19旋转驱动。
并且,在从废热回收锅炉20的出口到烟囱75,具备气体净化设备74。
在此,对本实施方式的煤气化复合发电设备1的工作进行说明。
在本实施方式的煤气化复合发电设备1中,当向供煤设备21供给原煤(煤)时,煤在供煤设备21中被粉碎成细微的颗粒状从而成为煤粉。在供煤设备21制造出的煤粉通过从空气分离设备42供给的氮而在第一氮供给线43流通从而向气化炉设备14供给。另外,在后述的焦炭回收设备25回收的焦炭通过从空气分离设备42供给的氮而在第二氮供给线45流通从而向气化炉设备14供给。而且,在从后述的燃气涡轮17抽取的压缩空气在升压机68升压之后,与从空气分离设备42供给的氧一起通过压缩空气供给线41向气化炉设备14供给。
在气化炉设备14中,被供给的煤粉及焦炭利用压缩空气(氧)而燃烧,通过煤粉及焦炭气化,生成生成气体。并且,该生成气体从气化炉设备14通过生成气体线49排出,被送向焦炭回收设备25。
在该焦炭回收设备25中,生成气体首先被向集尘设备51供给,从而生成气体所含有的微粒的焦炭被分离。然后,分离出焦炭的生成气体通过气体排出线53被送向气体精制设备26。另一方面,从生成气体分离出的微粒的焦炭堆积于供给料斗52,通过焦炭返回线46返回气化炉设备14而再循环。
由焦炭回收设备25分离出焦炭后的生成气体在气体精制设备26中被去除硫化物、氮化物等杂质而进行气体精制,制造燃料气体。压缩机61生成压缩空气并向燃烧器62供给。该燃烧器62将从压缩机61供给的压缩空气与从气体精制设备26供给的燃料气体混合并使其燃烧,从而生成燃烧气体。通过利用该燃烧气体使涡轮63旋转驱动,经由旋转轴64而使压缩机61及发电机19旋转驱动。这样一来,燃气涡轮17能够进行发电。
并且,废热回收锅炉20通过在从燃气涡轮17中的涡轮63排出的废气与供水进行热交换来生成蒸气,将该生成的蒸气向蒸气涡轮18供给。在蒸气涡轮18中,通过利用从废热回收锅炉20供给的蒸气使涡轮69旋转驱动,经由旋转轴64而使发电机19旋转驱动,能够进行发电。
此外,燃气涡轮17与蒸气涡轮18也可以不设为同一轴而使1个发电机19旋转驱动,也可以设为不同的轴而使多个发电机旋转驱动。
之后,在气体净化设备74中从废热回收锅炉20排出的废气气体的有害物质被去除,净化后的废气气体从烟囱75向大气放出。
以下,关于本实施方式的气化炉,参照附图进行说明。图5中,示出本实施方式的气化炉的概略结构图。本实施方式的燃烧器设置于图5所示的气化炉101等。
气化炉101在铅垂方向上延伸而形成,向铅垂方向的下方侧供给煤粉及氧,部分燃烧而气化后的生成气体从铅垂方向的下方侧朝向上方侧流通。气化炉101具有压力容器110和设置于压力容器110的内部的气化炉壁(冷却壁)111。并且,气化炉101在压力容器110与气化炉壁111之间的空间形成有环形部115。另外,气化炉101在气化炉壁111的内部的空间,从铅垂方向的下方侧(即,生成气体的流通方向的上游侧)起依次形成有燃烧室部116、扩散器部117、减压器部118。
压力容器110形成为内部成为中空空间的筒形状,在上端部形成有气体排出口121,另一方面,在下端部(底部)形成有炉渣料斗122。气化炉壁111形成为内部成为中空空间的筒形状,其壁面与压力容器110的内面对向而设置。在本实施方式中,压力容器110为圆筒形状,气化炉壁111的扩散器部117也形成为圆筒形状。并且,气化炉壁111通过未图示的支承构件连结于压力容器110内面。
气化炉壁111将压力容器110的内部分离为内部空间154和外部空间156。虽然后述,但气化炉壁111为横截面形状在燃烧室部116与减压器部118之间的扩散器部117变化的形状。气化炉壁111中,成为铅垂上方侧的其上端部连接于压力容器110的气体排出口121,成为铅垂下方侧的其下端部与压力容器110的底部空开间隙而设置。并且,在形成于压力容器110的底部的炉渣料斗122,积存有储存水,通过气化炉壁111的下端部浸入储存水,将气化炉壁111的内外密封。在气化炉壁111插入有燃烧器126、127,在内部空间154配置有合成气体冷却器102。关于气化炉壁111的构造后述。
环形部115是形成于压力容器110的内侧和气化炉壁111的外侧的空间,即,是外部空间156,在空气分离设备分离出的作为非活性气体的氮通过未图示的氮供给线而被供给。因而,环形部115成为充满氮的空间。此外,在该环形部115的铅垂方向的上部附近,设置有用于使气化炉101内均压的未图示的炉壁内均压管。炉壁内均压管将气化炉壁111的内外连通而设置,以气化炉壁111的内部(燃烧室部116、扩散器部117及减压器部118)与外部(环形部115)的压力差成为规定压力以内的方式形成大致均压。
燃烧室部116成为使煤粉及焦炭和空气局部燃烧的空间,在燃烧室部116中的气化炉壁111配置有由多个燃烧器126构成的燃烧装置。在燃烧室部116中使煤粉及焦炭的一部分燃烧所得到的高温的燃烧气体,通过扩散器部117而向减压器部118流入。
减压器部118成为如下的空间:被维持为气化反应所需的高温状态,向来自燃烧室部116的燃烧气体供给煤粉并使其部分燃烧,将煤粉分解成挥发成分(一氧化碳、氢、低级烃等)并气化而生成生成气体,在减压器部118中的气化炉壁111配置有由多个燃烧器127构成的燃烧装置。
合成气体冷却器102设置于气化炉壁111的内部,并且设置于减压器部118的燃烧器127的铅垂方向的上方侧。合成气体冷却器102是热交换器,从气化炉壁111的铅垂方向的下方侧(生成气体的流通方向的上游侧)起依次配置有蒸发器(evaporator)131、过热器(superheater)132、节煤器(economizer)134。这些合成气体冷却器102通过与在减压器部118中生成的生成气体进行热交换,将生成气体冷却。另外,蒸发器(evaporator)131、过热器(superheater)132、节煤器(economizer)134不限定图中记载的其数量。
在此,对上述的气化炉101的动作进行说明。
在气化炉101中,通过减压器部118的燃烧器127投入氮和煤粉并点火,并且通过燃烧室部116的燃烧器126投入煤粉及焦炭和压缩空气(氧)并点火。于是,在燃烧室部116中,通过煤粉与焦炭的燃烧而产生高温燃烧气体。另外,在燃烧室部116中,通过煤粉与焦炭的燃烧而在高温气体中生成熔融炉渣,该熔融炉渣向气化炉壁111附着,并且向炉底落下,最终向炉渣料斗122内的积水排出。并且,在燃烧室部116产生的高温燃烧气体通过扩散器部117而向减压器部118上升。在该减压器部118中,被维持为气化反应所需的高温状态,煤粉与高温燃烧气体混合,在高温的还原气氛下使煤粉部分燃烧而进行气化反应,生成生成气体。气化了的生成气体从铅垂方向的下方侧朝向上方侧流通。
燃烧器126在燃烧室部116的周围设置有多个,在图1~图3中示出了其中的1个燃烧器126。气化炉壁111构成为多个炉壁管9排列而成为筒状,将多个炉壁管9的直线形状部分的中心轴在周向上排列配置的位置设为壁面111s。燃烧器126插通设置于在气化炉壁111形成的开口部11。气化炉壁111由在上下方向上延伸且平行设置的多个炉壁管(冷却管)9和将相邻的炉壁管9彼此连接的翅片10构成。冷却水在炉壁管9内流动。形成于气化炉壁111的开口部11通过使炉壁管9的一部分弯曲而形成。
具体地说,以不在相当于开口部11的区域配置炉壁管9的方式,将作为炉壁管9的一部分的第一炉壁管9a向燃烧器126的径向外侧方向以沿着壁面111s的位置的方式弯曲而形成。通过相邻的第一炉壁管9a也依次弯曲而形成,形成图3所示那样的开口部11。
燃烧器126具备从炉壁外到炉壁内配置的燃烧器主体5、和卷绕于该燃烧器主体5的周围的燃烧器用冷却管7。
在燃烧器主体5内,流通有煤粉等燃料粉、空气(一次空气、二次空气),通过从燃烧器主体5供给的燃料粉及空气,在炉壁内形成火炎而产生燃烧气体。
燃烧器用冷却管7在内部流通有冷却水(冷却介质)。燃烧器用冷却管7为了获得传热性而以沿着燃烧器主体5的外周面包围燃烧器主体5的方式配置。燃烧器用冷却管7的设置区域从燃烧器主体5的顶端5a到气化炉壁111侧而设置,更具体地说,从燃烧器主体5的顶端5a到在开口部11近旁且进入比开口部11靠炉壁外侧的位置而设置。
基于上述结构的燃烧器126如以下这样使用。
从未图示的供给源向燃烧器主体5内供给燃料粉及空气,在燃烧器主体5内以规定的空气比调整而混合后的混合气被从燃烧器主体5的顶端5a喷出。从燃烧器主体5喷出的混合气在炉壁内投入到已经形成的燃料区域,维持所希望的燃烧状态。
为了保护燃烧器主体5免受由形成于炉壁内的火炎产生的燃烧热的影响,使冷却水流动于燃烧器用冷却管7内。冷却水从未图示的冷却水源向燃烧器用冷却管7供给,从燃烧器主体5的顶端5a侧向基端5b侧流通。
接着,对本实施方式的气化炉壁111的开口部构造进行说明。
形成于气化炉壁111的开口部11如上所述,通过使炉壁管9的一部分弯曲而形成。具体地说,使相当于开口部11的位置的炉壁管9的一部分向燃烧器126的侧方弯曲而形成。通过使相邻的炉壁管9也依次弯曲而形成,形成图3所示那样的开口部11。
多个炉壁管9在气化炉壁111的筒状的内径恒定的区域,以直线状部分彼此成为平行的方式配置于铅垂上下方向上,构成气化炉壁111。气化炉壁111的在相对于铅垂上下方向垂直的方向上切断后的横截面例如为圆环形状。
在构成气化炉壁111的多个炉壁管9中的、开口部11附近的多个炉壁管9,存在直线形状部分和弯曲形状部分。关于该弯曲形状部分,存在直线形状部分在轴向上延长的假想轴(第一假想轴)重叠于开口部11的第一炉壁管(第一冷却管)9a。这些第一炉壁管9a,为了形成能够供燃烧器126插入设置的开口部11,第一炉壁管9a成为相对于直线形状部分的轴向弯曲了的弯曲形状。开口部11以沿着多个弯曲形状部分的第一炉壁管9a的外周面依次弯曲并被包围的方式形成。
在直线形状部分的轴向上延长的假想轴重叠于开口部11的第一炉壁管9a的数量根据开口部11的大小、炉壁管9的直径、间距等而不同。多根第一炉壁管9a的弯曲形状部分配置于沿着炉壁管9的壁面内。第一炉壁管9a由平面弯曲构造形成。由此,不会使第一炉壁管9a的弯曲形状成为复杂的形状,以多个炉壁管9包围的方式简易地形成开口部11。
在多个第一炉壁管9a中,存在在直线形状部分的轴向上延长的第一假想轴与离开口部11的中心轴最近的位置重叠的第一炉壁管9a-1。该第一炉壁管9a-1的弯曲形状部分,在离燃烧器126的外周面最近的位置,以沿着燃烧器126的最外周面设置的方式形成开口部11。在直线形状部分的轴向上延长的假想轴在离开口部11的中心轴第二近的位置处重叠的第一炉壁管9a-2,弯曲形状部分与上述的在离燃烧器126的外周面最近的位置形成开口部11的第一炉壁管9a-1相比,从燃烧器126中心轴向径向外侧分隔,与沿着燃烧器126的最外周面设置的第一炉壁管9a-1相邻地设置。
在直线形状部分的轴向上延长的假想轴通过相当于开口部11的区域的第一炉壁管9a(例如第一炉壁管9a-3、9a-4)依次在燃烧器126的径向外侧,与中心侧的第一炉壁管9a-2、9a-3相邻地配置。这些第一炉壁管9a均沿着燃烧器126的最外周面的形状设置,例如,也可以设置成与第一炉壁管9a的弯曲形状部分的一部分相符的假想圆的中心成为与接触于燃烧器126的最外周面的假想圆相同的中心。
而且,第一炉壁管9a的弯曲形状部分配置于沿着壁面111s的面内,该壁面111s为多个炉壁管9的直线形状部分的中心轴排列配置的位置。因而,燃烧器126以沿着壁面111s配置的第一炉壁管9a为界,配置于炉内侧和炉外侧。并且,燃烧器126的从燃烧器主体5的顶端5a到燃烧器126与壁面111s交叉的位置之间的区域配置于炉的内部空间。因此,与炉壁管9的弯曲形状部分从壁面111s向炉外侧突出而呈大致圆台状配置的以往的结构相比,配置于气化炉101的内部空间的燃烧器主体5暴露于高温的燃烧气体的部分减低。
此外,如图6所示,第一炉壁管9a的弯曲形状部分不限定于沿着气化炉壁111的壁面111s配置的情况,也可以以从壁面111s以规定距离以下分隔并在筒状的气化炉壁111的径向上扩张的方式,配置于径向外侧。在该情况下,规定距离作为壁面111s与弯曲形状部分之间的间距,为与第一炉壁管9a的直径同一长度以下。即,第一炉壁管9a的弯曲形状部分也可以是,以与第一炉壁管9a的直径同一长度的间距量以下作为规定距离,从壁面111s分隔而配置于径向外侧。
在上述的变形例中,第一炉壁管9a的弯曲形状部分以从壁面111s分隔并在筒状的气化炉壁111的径向上扩张的方式,配置于径向外侧。由此,不会将设置于多个第一炉壁管9a之间的翅片10之间扩大到规定间隔以上,能够容易配置第一炉壁管9a,所以能够抑制第一炉壁管9a的传热量的减少。
在构成气化炉壁111的多个炉壁管9中,存在在直线形状部分的轴向上延长的假想轴在比相当于开口部11的区域的外周靠外径侧(在径向上靠外侧)重叠的炉壁管。这些炉壁管9中的在开口部11的近旁重叠的第二炉壁管9b,若想要仅通过使直线形状部分延长来配置,则会与上述的第一炉壁管9a干涉。因此,第二炉壁管9b具有相对于直线形状部分的轴向向开口部11的外径侧弯曲的弯曲形状。第一炉壁管9a的弯曲形状部分沿着壁面111s配置,第二炉壁管9b的弯曲形状部分配置于比第一炉壁管9a靠炉外侧,第一炉壁管9a与第二炉壁管9b的干涉得以避免。
第二炉壁管9b的数量根据第一炉壁管9a的数量、弯曲形状等而不同。多根第二炉壁管9b的弯曲形状部分相对于第一炉壁管9a的弯曲形状部分配置于壁面111s的外径侧(炉外侧)的面内。第二炉壁管9b由平面弯曲构造形成。由此,不会使第二炉壁管9b的弯曲形状成为复杂的形状,而简易地形成开口部11。
第二炉壁管9b的弯曲形状部分相对于气化炉壁111的壁面111s在比第一炉壁管9a靠炉外侧,沿着第一炉壁管9a配置。由此,第二炉壁管9b能够避免与第一炉壁管9a的干涉。
在弯曲形状部分,在2根第一炉壁管9a之间或2根第二炉壁管9b之间,配置利用金属板实现的翅片10。在直线形状部分,关于2根炉壁管9之间,同样配置翅片10。另一方面,在该直线形状部分的延长上的弯曲形状部分,关于1根第一炉壁管9a与同该第一炉壁管9a相邻的1根第二炉壁管9b之间,也可以无需设置翅片10。
在开口部11的周围的壁面111s的炉内侧,配置利用耐火材料实现的密闭部16。由此,在开口部11的周围,能够使气化炉壁111中的热传递降低。因而,来自设置于炉壁管9、第一炉壁管9a及第二炉壁管9b之间的翅片10宽度的传热特性的制约减低,在沿着壁面111s的面内配置炉壁管9,简易地形成开口部11。
另外,利用耐火材料实现的密闭部16,即便是存在不配置翅片10的部分的情况下,也能够防止气体从内部空间泄漏。作为耐火材料,例如优选使用氧化铝系、sic系。
利用耐火材料实现的密闭部16不限于开口部11的周围,例如也可以遍及燃烧室部116的壁面111s的炉内侧整周面,设置利用耐火材料实现的密闭部16。
在炉壁外侧,以覆盖由炉壁管9形成的开口部11的方式设置有密封盒(密闭容器)13。密封盒13例如是不锈钢制。在密封盒13内填充有耐火材料15。作为耐火材料15,例如优选使用氧化铝系、sic系。
由此,在开口部11的周围,能够防止气体从内部空间泄漏,使朝向气化炉壁111的外侧的热传递量降低。另外,通过这些密封盒13及耐火材料15,维持被加压了的炉壁内的压力,并且,使得将要从燃烧器126与开口部11的间隙向气化炉壁111外漏出的辐射热、炉渣类不会进一步向外部漏出。
填充于密封盒13内部的耐火材料15,优选不与设置于燃烧器主体5的周围的燃烧器用冷却管7紧贴,从燃烧器用冷却管7分隔并设置间隙而配置。由此,将从耐火材料15拆下燃烧器用冷却管7时的仅燃烧器用冷却管7设为能够装卸,能够容易地进行更换。
上述的本实施方式的开口部11如以下这样形成。
首先,对第一炉壁管9a及第二炉壁管9b以具有规定的形状的方式进行平面弯曲加工而形成弯曲形状部分。在本实施方式中,无需将用于形成炉壁管9的配管弯曲加工成立体形状。
如图3所示,多个炉壁管9在气化炉壁111的筒状的内径恒定的区域,以直线状部分彼此成为平行的方式配置。在气化炉壁111在相对于铅垂上下方向垂直的方向上切断后的横截面例如为圆环形状的情况下,多个炉壁管9的直线形状部分呈圆环形状配置。
多个炉壁管9中的、在直线形状部分的轴向上延长的假想轴与相当于开口部11的区域重叠的第一炉壁管9a,以弯曲形状部分包围燃烧器126的最外周面的方式,形成能够供燃烧器126插通设置的开口部11。第一炉壁管9a中的、在直线形状部分的轴向上延长的假想轴在离开口部11的中心轴最近的位置配置的第一炉壁管9a-1在离燃烧器126的最外周面最近的位置处沿着燃烧器126的外周面设置。
此时,第一炉壁管9a-1的弯曲形状部分配置于沿着由多个炉壁管9的直线形状部分构成的壁面111s的面内。此外,如图6所示,第一炉壁管9a的弯曲形状部分有时也以从壁面111s以与第一炉壁管9a的直径同一长度的间距量以下分隔并向筒状的气化炉壁111的径向外侧扩张的方式配置。
接着,在直线形状部分的轴向上延长的假想轴通过离重叠于开口部11的区域的中心轴第二近的位置的第一炉壁管9a-2,与上述的配置于离燃烧器126的外周面最近的位置的第一炉壁管9a-1相比,在开口部11的径向外侧,沿着第一炉壁管9a-1设置。另外,关于该第一炉壁管9a-2也是在沿着由多个炉壁管9的直线形状部分构成的壁面111s的面内,或者以从壁面111s以与第一炉壁管9a的直径同一长度的间距量以下分隔并向筒状的气化炉壁111的径向外侧扩张的方式配置。
这样一来,在直线形状部分的轴向上延长的假想轴与相当于开口部11的区域重叠的第一炉壁管9a,依次在燃烧器126的外周面的径向外侧,与中心轴侧的第一炉壁管9a相邻地配置。这些第一炉壁管9a也可以均沿着燃烧器126的外周面,例如设置成与第一炉壁管9a的弯曲形状部分的一部分相符的假想圆的中心成为与接触于燃烧器126的外周面的假想圆相同的中心。
另外,配置多个炉壁管9中的、在直线形状部分的轴向上延长的假想轴与比相当于开口部11的区域靠径向外侧处重叠的第二炉壁管9b。这些炉壁管9中的通过开口部11的近旁的第二炉壁管9b以在弯曲形状部分的炉内侧沿着壁面111s配置有第一炉壁管9a的方式设置,从而不会与第一炉壁管9a干涉。此时,第二炉壁管9b的弯曲形状部分相对于气化炉壁111的壁面111s在比第一炉壁管9a靠炉外侧沿着第一炉壁管9a配置。由此,避免第一炉壁管9a与第二炉壁管9b干涉。
另外,在多个第一炉壁管9a之间、多个第二炉壁管9b之间,翅片10通过焊接而相对于第一炉壁管9a或第二炉壁管9b接合。
如上所述,通过配置第一炉壁管9a和第二炉壁管9b,形成开口部11。在开口部11,使得能够之后将燃烧器主体5和燃烧器用冷却管7设置于开口部11内。燃烧器用冷却管7在与气化炉壁111的设置现场不同的场所制作成圆筒形状,在气化炉壁111的设置现场,进行安装作业。
接着,在开口部11的周围的壁面111s的炉内侧,设置利用耐火材料实现的密闭部16。另外,在开口部11的周围的壁面111s的外侧设置密封盒13。在密封盒13设置于规定的位置后,在密封盒13的内部设置燃烧器用冷却管7,填充耐火材料15。密闭部16的耐火材料、密封盒13的耐火材料15例如通过在现场向模具框、密封盒13内流入而填充、固化。然而,燃烧器主体5被插入燃烧器用冷却管7的内部,燃烧器126设置于气化炉壁111。
以上,根据本实施方式,与以往的结构不同,在开口部11的周围炉壁管9的弯曲形状部分未被配置成大致圆台状,在沿着由直线形状部分构成的壁面111s的面上,配置第一炉壁管9a的弯曲形状部分。其结果,在向气化炉壁111的内部空间突出的燃烧器126的周围配置第一炉壁管9a,所以,与以往的大致圆台状的配置相比较,暴露于火炎的范围变窄。因而,沿着燃烧器主体5的外周面设置的圆筒状的燃烧器用冷却管7的长度也能够减低。若燃烧器用冷却管7的长度能够变短,则配管的卷数也减低。燃烧器主体5与燃烧器用冷却管7之间,要求紧贴性的管理,需要形成精度高的燃烧器用冷却管7。通过螺旋状的配管的卷数少,燃烧器用冷却管7的制作所需的作业被简化,工时减低。
另外,如上所述,在向气化炉壁111的内部空间突出的燃烧器主体5及燃烧器用冷却管7,暴露于火炎的范围变窄,所以,与以往的结构相比,燃烧器用冷却管7的金属表面温度降低。而且,由于燃烧器用冷却管7的长度变短,所以冷却水的压力损失也减低而燃烧器用冷却管7的使用寿命提高。
此外,在上述实施方式中,将具备从煤粉生成可燃性气体的煤气化炉的igcc作为一例进行了说明,但本公开的气化炉设备也可适用于例如将间伐材、废木、浮木、草类、废弃物、淤泥、轮胎等生物质燃料等其他含碳固体燃料气化。另外,本公开的气化炉设备不限于发电用,也可适用于获得所希望的化学物质的化工厂用气化炉。
而且,本公开的冷却壁,也可作为一般的锅炉的火炉壁而适用。
另外,在上述的实施方式中,作为燃料使用了煤,但即便是高档煤、低档煤等其他含碳固体燃料,也可适用,另外,不限于煤,既可以是作为能够再生的生物来源的有机资源而使用的生物质,也可以使用例如间伐材、废木、浮木、草类、废弃物、淤泥、轮胎及将它们作为原料的再循环燃料(颗粒、片)等。
此外,本实施方式,作为气化炉101,对塔型气化炉进行了说明,但即使气化炉101是交叉型气化炉,通过将气化炉101内的各器械的铅垂上下方向以与生成气体的气体流动方向相匹配的方式置换,也同样能够实施。
标号说明
1:煤气化复合发电设备(气化复合发电设备)
5:燃烧器主体
5a:顶端
5b:基端
7:燃烧器用冷却管
9:炉壁管(冷却管)
9a、9a-1、9a-2、9a-3:第一炉壁管(第一冷却管)
9b:第二炉壁管(第二冷却管)
10:翅片
11:开口部
13:密封盒
14:气化炉设备
15:耐火材料
16:密闭部
17:燃气涡轮
18:蒸气涡轮
19:发电机
20:废热回收锅炉
21:供煤设备
21a:供煤线
25:焦炭回收设备
26:气体精制设备
42:空气分离设备
48:异物去除设备
51:集尘设备
52:供给料斗
61:压缩机
62:燃烧器
63:涡轮
64:旋转轴
68:升压机
69:涡轮
73:复水器
74:气体净化设备
75:烟囱
101:气化炉
102:合成气体冷却器(热交换器)
110:压力容器
111:气化炉壁(冷却壁)
111s:壁面
115:环形部
116:燃烧室部
117:扩散器部
118:减压器部
121:气体排出口
122:炉渣料斗
126、127:燃烧器
本文用于企业家、创业者技术爱好者查询,结果仅供参考。