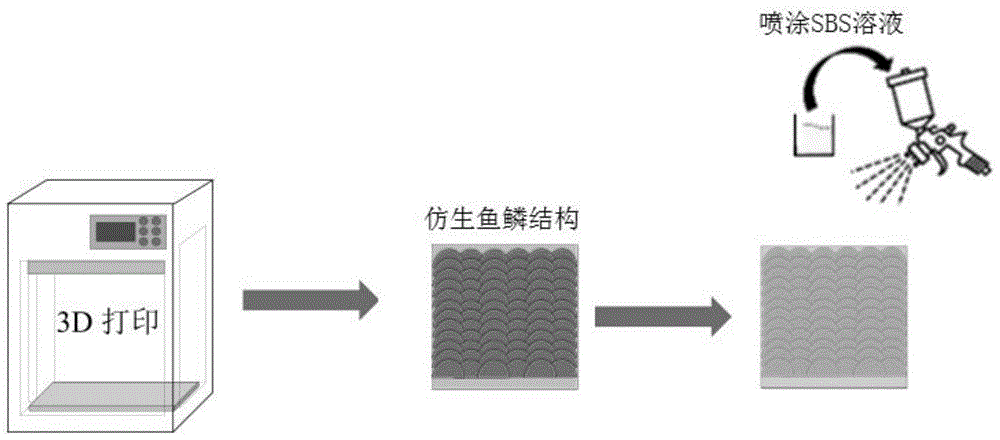
本发明涉及表面工程技术领域,尤其涉及一种减阻降噪多功能结构及其制备方法和应用。
背景技术:
长航程、高航速以及强隐身性是潜艇、舰艇等现代海军装备的重要技术指标。海军装备航行时摩擦阻力占比大,超过50%。而且,舰艇表面在水下污损率高,污损通常会引起摩擦阻力的大幅度增加。例如,污损率为10%时,船舶阻力达到洁净表面时的2倍,燃料消耗增加20%。同时,摩擦阻力的增加会直接增大噪音,损害海军装备声纳信号的发射和接收,增大被敌军探测的机率,显著降低装备的隐身性和作战性能。当潜艇的自噪声降低3db,则声纳探测距离提高近50%。因此,寻找合适的减阻降噪策略对水下航行器具有重要的作用。
但是,现有的减阻降噪技术方法单一,往往不能综合实现减阻降噪效果。
技术实现要素:
本发明的目的在于提供一种减阻降噪多功能结构及其制备方法和应用,本发明提供的结构兼具较好的减阻降噪功能。
为了实现上述发明目的,本发明提供以下技术方案:
本发明提供了一种减阻降噪多功能结构,包括设置在基体表面的仿生减阻微结构以及设置在所述仿生减阻微结构表面的柔性涂层,且所述柔性涂层的表面保留有所述仿生减阻微结构的原始形貌。
优选地,所述仿生减阻微结构包括仿生鱼鳞结构或仿生直沟槽。
优选地,所述仿生鱼鳞结构中的仿生鱼鳞沿顺流方向呈覆瓦式阵列分布,单个所述仿生鱼鳞的纵截面呈直角三角形,所述直角三角形为非等腰直角三角形,且所述直角三角形的长直角边与所述基体表面接触。
优选地,所述直角三角形的斜边与所述基体表面的夹角≤45°,所述直角三角形的长直角边≤3mm。
优选地,所述柔性涂层的厚度为40~650μm。
优选地,所述柔性涂层的制备原料包括弹性体材料和有机溶剂。
本发明提供了上述技术方案所述减阻降噪多功能结构的制备方法,包括以下步骤:
在仿生减阻微结构的表面制备柔性涂层,且使所述柔性涂层的表面保留有所述仿生减阻微结构的原始形貌,得到减阻降噪多功能结构表面;其中,所述仿生减阻微结构设置于基体表面。
优选地,所述仿生减阻微结构的制备方法包括3d打印技术、机械加工技术或光固化成型技术。
优选地,所述柔性涂层的制备方法包括:
将柔性涂层的制备原料混合,得到混合溶液;
将所述混合溶液涂覆在所述仿生减阻微结构的表面,固化后得到柔性涂层。
本发明提供了上述技术方案所述减阻降噪多功能结构或上述技术方案所述制备方法制备得到的减阻降噪多功能结构在水下航行器减阻降噪中的应用。
本发明提供了一种减阻降噪多功能结构,包括设置在基体表面的仿生减阻微结构以及设置在所述仿生减阻微结构表面的柔性涂层,且所述柔性涂层的表面保留有所述仿生减阻微结构的原始形貌。本发明中仿生减阻微结构与柔性涂层耦合,形成的减阻降噪多功能结构并不呈现平滑表面,而是保留了仿生减阻微结构的原始形貌,能够保证最终所得表面兼具较好的减阻降噪功能。
附图说明
图1为实施例1中制备减阻降噪多功能结构的流程图;
图2为实施例1中基体、仿生鱼鳞结构以及减阻降噪多功能结构的示意图;
图3为实施例1中仿生鱼鳞结构与柔性涂层相对关系的示意图;
图4为实施例1以及对比例1制备的功能结构的减阻率效果图;
图5为实施例1以及对比例2制备的功能结构在声监测点处的噪声总声压级对比图。
具体实施方式
本发明提供了一种减阻降噪多功能结构,包括设置在基体表面的仿生减阻微结构以及设置在所述仿生减阻微结构表面的柔性涂层,且所述柔性涂层的表面保留有所述仿生减阻微结构的原始形貌。
本发明提供的减阻降噪多功能结构包括设置在基体表面的仿生减阻微结构。本发明对所述仿生减阻微结构的种类没有特殊限定,采用本领域技术人员熟知的仿生减阻微结构即可,具体可以为仿生鱼鳞结构或仿生直沟槽,优选为仿生鱼鳞结构。具体的,以所述仿生减阻微结构为仿生鱼鳞结构为例,仿生鱼鳞结构可以让流体在近壁面附近产生顺流向涡,从而将固液之间的滑动摩擦变为滚动摩擦,减小固液之间的摩擦系数,降低摩擦力。另外,顺流向涡还可以将近壁面的高速流体推离壁面,从而产生降低速度梯度,达到减阻的目的。在本发明中,当所述仿生减阻微结构为仿生直沟槽时,其作用原理与上述仿生鱼鳞结构类似,不再赘述。
在本发明中,所述仿生鱼鳞结构中的仿生鱼鳞沿顺流方向呈覆瓦式阵列分布,单个所述仿生鱼鳞的纵截面呈直角三角形,所述直角三角形为非等腰直角三角形,且所述直角三角形的长直角边与所述基体表面接触;所述直角三角形的斜边与所述基体表面的夹角优选为≤45°,更优选为5°~25°,进一步优选为10°~15°;所述直角三角形的长直角边优选≤3mm,更优选为1~2.9mm,进一步优选为2~2.8mm。在本发明中,单个仿生鱼鳞的宽度优选≤7mm,更优选为2~6mm,进一步优选为3~5mm;在本发明中,所述仿生鱼鳞的宽度是以展向方向为基准。在本发明中,沿顺流方向,所述仿生鱼鳞结构由多个阵列单元组成,其中单个阵列单元包括相邻的两列仿生鱼鳞,以单个仿生鱼鳞的宽度记为a,阵列节距优选为0.5a~2a,更优选为0.8~1.2a。
在本发明中,所述仿生减阻微结构的制备原料优选为树脂材料或金属材料;所述金属材料优选包括铝合金或钢;所述树脂材料优选包括标准刚性树脂、高精度红蜡树脂、牙科铸造树脂或珠宝铸造树脂,所述标准刚性树脂优选为光固化3d打印刚性光敏树脂。在本发明的实施例中,所述光固化3d打印刚性光敏树脂的型号具体为nova3d,成分具体为齐聚物、光引发剂和稀释剂。本发明优选以标准刚性树脂作为原料制备仿生减阻微结构,其具有较好的力学性能,与金枪鱼表面的鱼鳞力学性能(弹性模量和硬度分别为20.9gpa和1.22gpa)处于同一数量级。
本发明提供的减阻降噪多功能结构包括设置在所述仿生减阻微结构表面的柔性涂层,所述柔性涂层的厚度以保证能够在所述柔性涂层的表面保留有所述仿生减阻微结构的原始形貌为基准,防止柔性涂层厚度过大将仿生减阻微结构埋平;具体的,所述柔性涂层的厚度优选为40~640μm,更优选为100~400μm,进一步优选为140~200μm。在本发明中,仿生减阻微结构表面的柔性涂层可以吸收近壁面的湍流脉动,延迟边界层的转捩,从而达到减阻降噪的效果。
在本发明中,所述柔性涂层的制备原料优选包括弹性体材料和有机溶剂。在本发明中,所述弹性体材料优选包括聚二甲基硅氧烷或苯乙烯-丁二烯-苯乙烯嵌段共聚物(sbs),更优选为sbs。本发明以弹性体材料为原料制备柔性涂层,其能够吸收近壁面的湍流脉动,减小能量耗散,延迟边界层转捩,从而达到减阻降噪的目的。本发明对所述有机溶剂的种类没有特殊限定,能够充分溶解弹性体材料,保证柔性涂层的制备顺利进行即可,具体的,在本发明中,当所述弹性体材料为sbs时,所述有机溶剂优选为二甲苯。本发明对所述弹性体材料和有机溶剂的配比没有特殊限定,能够保证弹性体材料充分溶解即可;具体的,所述sbs与二甲苯的质量比优选为1:(3.5~4.5),更优选为1:4。
本发明提供了上述技术方案所述减阻降噪多功能结构的制备方法,包括以下步骤:
在仿生减阻微结构的表面制备柔性涂层,且使所述柔性涂层的表面保留有所述仿生减阻微结构的原始形貌,得到减阻降噪多功能结构表面;其中,所述仿生减阻微结构设置于基体表面。
在本发明中,所述仿生减阻微结构设置于基体表面,所述仿生减阻微结构的制备方法优选包括3d打印技术、机械加工技术或光固化成型技术;本发明对所述3d打印技术、机械加工技术和光固化成型技术的具体操作方式没有特殊限定,能够得到所需的仿生减阻微结构即可。在本发明的实施例中,具体采用3d打印技术制备仿生减阻微结构,所述3d打印技术的步骤优选包括依次进行的建模、模型切片处理和打印。在本发明的实施例中,所述基体以及仿生减阻微结构具体是采用3d打印技术一体打印得到,所述基体的材质优选与仿生减阻微结构的材质一致,不再赘述。
得到仿生减阻微结构后,本发明在所述仿生减阻微结构的表面制备柔性涂层,且使所述柔性涂层的表面保留有所述仿生减阻微结构的原始形貌,得到减阻降噪多功能结构表面。在本发明中,所述柔性涂层的制备方法优选包括:
将柔性涂层的制备原料混合,得到混合溶液;
将所述混合溶液涂覆在所述仿生减阻微结构的表面,固化后得到柔性涂层。
本发明将柔性涂层的制备原料混合,得到混合溶液。本发明对柔性涂层的制备原料的混合方式没有特殊限定,能够将各组分充分混合均匀即可。
得到混合溶液后,本发明将所述混合溶液涂覆在所述仿生减阻微结构的表面,固化后得到柔性涂层。在本发明中,所述涂覆的方式优选为喷涂,具体是将所述混合溶液置于喷枪中,喷涂至所述仿生减阻微结构的表面;所述喷涂的过程中,混合溶液的喷涂速度优选为130~170ml/min,更优选为140~150ml/min;喷枪与仿生减阻微结构表面之间的距离优选为180~220mm,更优选为190~200mm。在本发明中,所述固化优选在室温条件下进行,即不需要额外的加热或降温;在本发明的实施例中,所述室温具体为25℃。本发明对所述固化的时间没有特殊限定,能够保证充分固化即可。
本发明提供了上述技术方案所述减阻降噪多功能结构或上述技术方案所述制备方法制备得到的减阻降噪多功能结构在水下航行器减阻降噪中的应用。
下面将结合本发明中的实施例,对本发明中的技术方案进行清楚、完整地描述。显然,所描述的实施例仅仅是本发明一部分实施例,而不是全部的实施例。基于本发明中的实施例,本领域普通技术人员在没有做出创造性劳动前提下所获得的所有其他实施例,都属于本发明保护的范围。
实施例1
按照图1所示流程制备减阻降噪多功能结构,步骤如下:
以光固化3d打印刚性光敏树脂(型号具体为nova3d)为原料,通过3d打印技术一体打印得到基体以及仿生鱼鳞结构,且仿生鱼鳞结构设置于基体表面,所述3d打印技术的操作步骤包括依次进行的建模、模型切片处理和打印;所述仿生鱼鳞结构中的仿生鱼鳞沿顺流方向呈覆瓦式阵列分布,单个所述仿生鱼鳞的纵截面呈直角三角形,所述直角三角形为非等腰直角三角形,且所述直角三角形的长直角边与所述基体表面接触,所述直角三角形的斜边与所述基体表面的夹角为10°,所述直角三角形的长直角边为2.8mm;单个仿生鱼鳞的宽度为5mm,所述仿生鱼鳞的宽度是以展向方向为基准;沿顺流方向,所述仿生鱼鳞结构中的阵列单元包括相邻的两列仿生鱼鳞,其中阵列节距为6mm。
将25g苯乙烯-丁二烯-苯乙烯嵌段共聚物(sbs)溶解于100g二甲苯中,得到sbs溶液;将20g所述sbs溶液置于喷枪中,调整喷枪中sbs溶液的喷涂速度为150ml/min,喷枪和仿生鱼鳞结构表面之间的距离为200mm,进行喷涂,喷涂完成后在室温(25℃)条件下进行固化,在仿生鱼鳞结构表面形成柔性涂层,所述柔性涂层的厚度为140μm,得到减阻降噪多功能结构,如图2和图3所示。
对比例1
按照实施例1的方法制备仿生鱼鳞结构。
对比例2
按照实施例1的方法制备减阻降噪多功能结构,不同之处仅在于柔性涂层在所述仿生鱼鳞结构表面形成平滑表面,具体的,以基体表面为基准,所述柔性涂层的最大厚度与仿生鱼鳞结构的最高处之差为140μm。
对实施例1以及对比例1~2制备的功能结构进行性能测试,具体如下:
将实施例1以及对比例1制备的功能结构进行水洞实验,以测试二者的减阻率。图4为实施例1以及对比例1制备的功能结构的减阻率效果图,由图4可知,实施例1制备的功能结构在仿生鱼鳞结构基础上耦合柔性涂层后,减阻效果显著提高。
将实施例1以及对比例2制备的功能结构进行降噪实验,以测试二者的降噪效果。图5为实施例1以及对比例2制备的功能结构在声监测点处的噪声总声压级对比图,由图5可知,随着频率的增加,噪声呈现减少的趋势,而且实施例1的辐射噪声总压级在各个频率下均小于对比例2,在高频段降低较明显。说明本发明提供的功能结构具有更优的降噪效果。
以上所述仅是本发明的优选实施方式,应当指出,对于本技术领域的普通技术人员来说,在不脱离本发明原理的前提下,还可以做出若干改进和润饰,这些改进和润饰也应视为本发明的保护范围。
本文用于企业家、创业者技术爱好者查询,结果仅供参考。