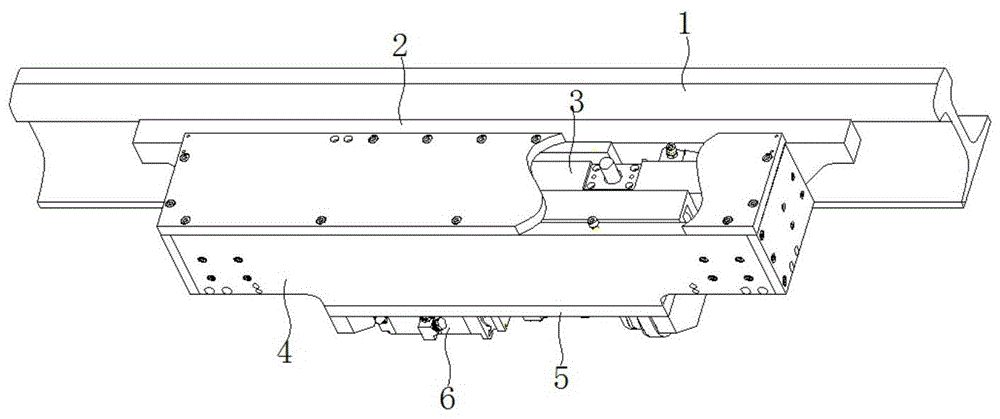
本实用新型属于轨道交通技术领域,更具体地说,涉及一种用于精确检测车轮踏面擦伤及不圆度的系统。
背景技术:
列车在运行的过程中会出现不同程度的磨耗,磨耗对车轮安全运行会产生影响,而其中磨耗不均匀导致的车轮踏面擦伤及径向跳动均会导致车轮踏面失圆,车轮踏面失圆对列车的运行安全性构成严重威胁,使列车车辆对线路和自身的动力作用大大加大,同时还会带来附加的振动和冲击,降低列车的临界速度,使得列车的平稳性和舒适性变差。因此对车轮踏面的不圆度测量对列车安全运行有着重要意义。
车轮不圆度的检测方法主要分为静态检测和动态监测,静态检测需要在列车停止或车轮拆卸的情况下进行,不仅占用列车的周转时间,且速度慢,劳动强度大。动态监测不仅可以实现对轮对的在线监测,而且自动化程度高,不占用车辆周转时间,便于存储信息资料,目前采用的动态监测不圆度方法有振动加速度检测法和接触测量法。其中,振动加速度检测法通过分析采集的整列列车经过检测点时轨道的振动情况,提取车轮的不圆度信息,但是该方法受传感器安装夹具、枕木振动衰减的影响,测量精确度不高。
接触测量法典型的为平行四边形法,如申请号为200720082608.9,实用新型明创造名称为:升降式车轮踏面插伤及不圆度在线动态检测装置,以及申请号为201210307496.8,实用新型创造名称为:一种车轮踏面插伤和不圆度在线检测装置的申请案均公开了平行四边形结构的在线测量方法及其改进,上述申请案中位移传感器与固定在构成平行四边形机构一边的钢轨上的支座相连,传感器可直接测量出车轮踏面与轮缘的相对高度的变化量,位移传感器记录整个踏面圆周的直径情况,当踏面不圆时传感器即输出曲线,从而得出不圆度,但是上述方法均不适合于列车高速通过的情况下进行检测,且其检测精度有待进一步提高。
技术实现要素:
1.实用新型要解决的技术问题
本实用新型的目的在于克服现有列车车轮踏面径向跳动检测存在的以上问题,提供了一种用于精确检测车轮踏面擦伤及不圆度的系统。采用本实用新型的技术方案可以实现列车车轮踏面径向跳动的实时动态检测,且其检测精度及检测装置的结构稳定性相对于现有检测机构均得到有效提高。
2.技术方案
为达到上述目的,本实用新型提供的技术方案为:
本实用新型的一种用于精确检测车轮踏面擦伤及不圆度的系统,包括沿列车入库方向依次安装于轨道内侧的前置机构和检测机构,其中前置机构用于对待检测车轮的轮缘高进行检测,检测机构用于对车轮径向跳动进行检测,该检测机构包括安装于轨道内侧且相互平行的踏板、滑动板及固定板总成,滑动板与踏板及固定板总成之间均通过滑轨机构相连,且滑动板与踏板之间连接有弹性元件;所述滑动板还通过摆杆传动机构与驱动机构相连。
更进一步的,所述的摆杆传动机构包括上滑块固定板、摆杆和下滑块固定板,其中摆杆的两端分别与上滑块固定板、下滑块固定板转动相连并形成平行四边形机构,所述上滑块固定板与滑动板固定相连,下滑块固定板与驱动机构驱动相连,通过驱动机构驱动下滑块固定板沿水平方向进行运动。
更进一步的,所述摆杆传动机构通过滑轨机构与底板总成可滑动连接,该底板总成固定安装于轨道底部;所述固定板总成及驱动机构均安装于底板总成上。
更进一步的,所述的检测机构对称安装于双侧轨道内侧,且同一侧检测机构的数量≥2;所述前置机构的前方还设有触发机构,该触发机构包括沿单侧轨道内侧间隔设置的第一磁钢和第二磁钢。
更进一步的,所述的驱动机构采用电机或伺服电动缸作为驱动源。
更进一步的,所述的驱动机构包括驱动电机、丝杠和丝杠螺母,其中驱动电机的输出轴与丝杠一端固定相连,丝杠另一端穿过丝杠螺母并与丝杠螺母螺纹相连,且丝杠螺母与摆杆传动机构固定相连。
更进一步的,所述丝杠的端部还与电磁制动器固定相连。
更进一步的,所述的固定板总成包括主固定板、位于主固定板两端的端固定板以及位于主固定板顶部的上封板,主固定板、端固定板及上封板共同围绕形成箱式结构;更进一步的,所述踏板与滑动板之间还设有中间固定板。
更进一步的,所述滑动板与踏板之间的滑轨机构相对于滑动板倾斜安装,滑动板与固定板总成之间的滑轨机构相对于滑动板垂直安装;所述踏板上固定有位移感应板,位移感应板的上方或下方对应设有固定安装的位移传感器。
更进一步的,所述的弹性元件采用拉簧或压簧;更进一步的,所述的弹性元件通过弹性元件支座固定安装于滑动板上,所述踏板上对应设有与弹性元件的活塞杆端部作用的弹性元件支撑板,且滑动板上还固定有弹性元件调节板,弹性元件调节板上设有顶丝和螺母,顶丝正对弹性元件支撑板的顶面进行安装。
更进一步的,所述前置机构的结构同检测机构,且其踏板的上表面沿列车入库方向依次包括上坡段、水平段和下坡段。
3.有益效果
采用本实用新型提供的技术方案,与现有技术相比,具有如下显著效果:
(1)本实用新型的一种用于精确检测车轮踏面擦伤及不圆度的系统,包括沿列车入库方向依次安装于轨道内侧的前置机构和检测机构,通过前置机构对待检测列车车轮的轮缘高进行检测并反馈给控制系统,通过控制系统控制对检测机构的初始高度进行调节,从而能够满足不同轮缘高车轮的检测要求,防止车轮快速冲击检测机构时对检测机构造成较大的冲击,延长了机构的使用寿命,并降低了冲击振动对检测精度的影响,有利于保证测量精度。
(2)本实用新型的一种用于精确检测车轮踏面擦伤及不圆度的系统,其检测机构包括安装于轨道内侧且相互平行的踏板、滑动板及固定板总成,其中滑动板通过摆杆传动机构与驱动机构相连,当车轮压过踏板表面时,踏板沿滑轨机构相对于滑动板产生向下位移,此时滑动板与固定板总成之间保持相对静止,通过对列车车轮行驶整个周长范围内踏板相对于滑动板下压位移的变化,即可以对列车车轮踏面的径向跳动进行在线动态测量,大大提高了测量效率,且其测量精度及整个测量装置的结构稳定性相对于现有平行四边形测量机构均得到明显提高。
(3)本实用新型的一种用于精确检测车轮踏面擦伤及不圆度的系统,所述滑动板与踏板之间连接有弹性元件,在弹性元件的回复力作用下可以使车轮离开时踏板自动回复至初始位置。同时,所述滑动板通过摆杆传动机构与驱动机构相连,在列车到达前,通过驱动机构驱动滑动板进行升降运动,从而可以在弹性元件的作用下使踏板与滑动板进行同步升降,进而可以对踏板的初始高度进行调节,以满足不同轮缘高车轮的测量要求,防止车轮对踏板造成较大的冲击,并有利于保证测量精度。
(4)本实用新型的一种用于精确检测车轮踏面擦伤及不圆度的系统,所述的摆杆传动机构包括上滑块固定板、摆杆和下滑块固定板,本实用新型通过摆杆传动机构的设置,利用驱动机构驱动下滑块固定板沿水平方向左右运动,即可以实现滑动板沿竖直方向的升降运动,从而一方面有利于保证滑动板升降运动的平稳性,并有效防止车轮压过踏板时滑动板发生倾斜,另一方面还可以有效节省驱动机构的安装空间,直接将驱动机构输出端的水平运动转化为滑动板的升降运动。
(5)本实用新型的一种用于精确检测车轮踏面擦伤及不圆度的系统,所述轨道内侧位于前置机构前端还设有触发机构,该触发机构包括沿轨道内侧间隔设置的第一磁钢和第二磁钢,根据第一磁钢和第二磁钢的触发顺序可以判断列车的入库与出库,从而便于决定前置机构和检测机构的启动与否。另外,通过第一磁钢和第二磁钢的设置还可以对列车的行驶速度进行测量。
(6)本实用新型的一种用于精确检测车轮踏面擦伤及不圆度的系统,所述的检测机构对称安装于双侧轨道内侧,且同一侧检测机构的数量≥2,具体以满足车轮整个踏面周长的检测为准,采用该种设计可以满足对前后不同车轮检测的需求,防止前一车轮未离开检测机构而后一车轮已进入检测机构对检测结果的影响。
(7)本实用新型的一种用于精确检测车轮踏面擦伤及不圆度的系统,所述的驱动机构包括驱动电机、丝杠和丝杠螺母,通过电机驱动丝杠发生转动,使丝杠螺母沿丝杠轴线进行水平移动,从而带动摆杆传动机构的运动,借助于摆杆传动机构的摆动即可以实现滑动板的升降调节。
(8)本实用新型的一种用于精确检测车轮踏面擦伤及不圆度的系统,所述丝杠的端部还与电磁制动器固定相连,当电机驱动时,电磁制动器打开制动,电机能够顺利将滑动板实现上下运动;而当车轮压上踏板时,电机保持不动,电磁制动器工作,保持制动,从而可以保证丝杠螺母不产生水平的移动,进而能够防止在车轮的滚压作用下滑动板产生上下的位移而影响测量结果得准确性。
(9)本实用新型的一种用于精确检测车轮踏面擦伤及不圆度的系统,所述的固定板总成包括主固定板、位于主固定板两端的端固定板以及位于主固定板顶部的上封板,主固定板、端固定板及上封板共同围绕形成箱式结构,从而可以进一步提高整个检测装置的结构强度和稳定性以及滑动板与踏板、固定板总成之间相对运动的平稳性。所述滑动板与踏板之间还设有中间固定板,从而进一步提高了装置的结构稳定性。
(10)本实用新型的一种用于精确检测车轮踏面擦伤及不圆度的系统,所述滑动板与踏板之间的滑轨机构相对于滑动板倾斜安装,滑动板与固定板总成之间的滑轨机构相对于滑动板垂直安装,从而有利于进一步提高整个测量装置结构与运行的稳定性,并有效降低车轮对检测装置的冲击,保证了测量结果的准确性。本实用新型的踏板上固定有位移感应板,位移感应板的上方或下方对应设有固定安装的位移传感器,通过对位移传感器所测与位移感应板之间距离的变化数据进行处理即可直接得到车轮的径向跳动情况。
附图说明
图1为本实用新型的检测机构的整体结构示意图;
图2为本实用新型的固定板总成的安装结构示意图;
图3为本实用新型的检测机构的拆分结构示意图(一);
图4为本实用新型的检测机构的拆分结构示意图(二);
图5为本实用新型的滑动板升降驱动及传动机构的结构示意图;
图6为本实用新型的底板总成的结构示意图;
图7为本实用新型的升降驱动机构的结构示意图;
图8为本实用新型的螺旋拉簧的结构示意图;
图9为本实用新型的弹簧销的结构示意图;
图10为本实用新型的用于精确检测车轮踏面擦伤及不圆度的系统的平面安装示意图;
图11为本实用新型的用于精确检测车轮踏面擦伤及不圆度的方法的控制原理图;
图12为本实用新型的前置机构踏板的结构示意图。
示意图中的标号说明:
1、轨道;2、踏板;201、上坡段;202、水平段;203、下坡段;3、滑动板;4、固定板总成;401、主固定板;402、端固定板;403、上封板;404、中间固定板;5、底板总成;501、底部支撑板;502、第一轨道压板;503、压板螺栓;504、压板螺母;505、拉杆螺栓;506、固定耳;507、加强筋;508、第二轨道压板;6、驱动机构;601、驱动电机;602、电机安装座;603、丝杠;604、丝杠螺母;605、丝杠固定座;701、第一滑轨;702、第二滑轨;703、第三滑轨;704、第四滑轨;8、弹性元件;801、弹性元件支座;802、弹性元件调节板;803、弹性元件支撑板;804、弹簧销;805、勾槽;901、位移传感器;902、传感器安装座;903、位移感应板;10、摆杆传动机构;1001、上滑块固定板;1002、摆杆;1003、下滑块固定板;1004、滑块;1005、导轨;1006;螺母连杆;11、电磁制动器;1201、第一磁钢;1202、第二磁钢;13、前置机构;1401、第一检测机构;1402、第二检测机构;1403、第三检测机构;1404、第四检测机构。
具体实施方式
为进一步了解本实用新型的内容,现结合附图和具体实施例对本实用新型作详细描述。
实施例1
如图10所示,本实施例的一种用于精确检测车轮踏面擦伤及不圆度的系统,包括沿列车入库方向依次安装于轨道内侧的前置机构13和检测机构,其中前置机构13用于对待检测车轮的轮缘高进行检测,检测机构用于对车轮径向跳动进行检测。检测机构及前置机构13均与控制系统控制相连,通过控制系统控制前置机构13和检测机构的启停。
本实施例在检测机构前方(列车入库来车方向)增加前置机构,通过前置机构13对待检测车轮的轮缘高进行测量,并根据所测轮缘高以及检测机构的当前位置,通过控制系统控制升降驱动机构6运行,从而对检测机构的初始高度进行调节,以保证检测机构的预压量属于设定范围,进而能够减小车轮快速冲击检测机构时对检测机构的冲击力,延长了机构的使用寿命,降低了冲击振动对检测精度的影响。此处所谓预压量,是指车轮压上检测机构的踏板时,踏板产生的垂直方向的位移大小。本实施例对前置机构的结构不做要求,可以直接采用现有任意车轮轮缘高在线检测装置,只要可以对车轮的轮缘高进行检测即可。
结合图1-图5,本实施例的检测机构包括安装于轨道1内侧且相互平行的踏板2、滑动板3及固定板总成4,滑动板3与踏板2及固定板总成4之间均通过滑轨机构相连,且滑动板3与踏板2之间连接有弹性元件8;所述滑动板3还通过摆杆传动机构10与驱动机构6相连。
列车车轮包括踏面部分和轮缘部分,踏面长期与轨道接触磨损造成踏面失圆,而轮缘不与其他物体接触,仍为一标准圆。因此,当车轮踏面不同位置与钢轨接触时,轮缘顶点到钢轨顶面的距离均不相同。本实施例通过在轨安装一踏板2,在车轮经过时,踏板2顶面始终保持与轮缘顶点接触,踏板2在车轮轮缘的压下作用下产生向下的位移量,且该位移量随着踏面与轨道接触点的不同而变化,采集车轮通过踏板2过程中踏板2位移的变化,即可以描绘出车轮踏面失圆情况。
因在实际使用中,一列车上所有车轮的轮缘高会有不同,测量时踏板2会高出车轮轮缘一定的值来作为预压量,该预压量值不能太大,否则车轮会严重撞击踏板2,造成踏板2的损坏而降低测量精度;该预压量同样也不能太小,不然车轮轮缘会压不到踏板2,造成检测不到数据。本实施例中通过踏板2、滑动板3与固定板总成4的分体式结构设计,同时配合驱动机构6的作用,从而既可以实现车轮踏面缺陷的测量,同时又可以对踏板2的初始高度进行调节,从而满足不同轮缘高车轮的测量要求,减小车轮对踏板2造成较大的冲击,并保证测量精度。具体的,在列车到达前,根据待测列车车轮的轮缘高,通过驱动机构6驱动摆杆传动机构10摆动,从而带动滑动板3相对于固定板总成4进行升降,在弹性元件8的作用下,踏板2与滑动板3进行同步升降,从而实现踏板2初始高度的调节。当踏板2的高度达到设定值后,驱动机构6即停止工作。
而当列车车轮压上踏板2后,在车轮的滚压作用下,踏板2沿滑轨机构相对于滑动板3向下移动,此时在驱动机构6的支撑作用下滑动板3相对于固定板总成4不产生相对滑动;而当列车车轮离开踏板2时,在弹性元件8的回复力作用下踏板2沿滑轨机构相对于滑动板3逐渐自动向上进行回复运动,通过对踏板2的下压位移数据进行处理,即可得到列车车轮踏面的径向跳动、踏面擦伤及磨损数据,实现了列车车轮缺陷的在线动态测量,大大提高了测量效率。本实施例通过对检测装置的结构进行优化设计,借助于滑轨机构对踏板2的移动进行导向,并通过弹性元件8的作用使其进行回复运动,从而相对于现有平行四边形测量机构,测量装置的结构稳定性及测量精度均得到了有效提高。
具体的,若此车轮踏面不存在擦伤,则整个踏面周长内相对钢轨的垂直位置不变,踏板2的下压位移保持不变;反之若此车轮踏面存在擦伤或磨损不均,踏面到轮缘顶部的相对高度发生了变化,则踏板2与钢轨的垂直位置也发生了相对变化,此时踏板2垂直高度的变化量即为擦伤量的大小。同时将此时踏板2的下压位移量与无磨损的新车轮相比较,即可得出车轮踏面的磨损量。本实施例中所述踏板2上固定有位移感应板903,位移感应板903的上方或下方对应设有固定安装的位移传感器901,当车轮压上踏板2后,位移感应板903随踏板2同步升降,而位移传感器901保持固定,则通过车轮滚压过程中位移传感器901所测与位移感应板903之间的位移变化即可直接得到车轮踏面的径向跳动。
实施例2
本实施例的一种用于精确检测车轮踏面擦伤及不圆度的系统,其结构基本同实施例1,其区别主要在于:如图3、图5所示,本实施例的摆杆传动机构10包括上滑块固定板1001、摆杆1002和下滑块固定板1003,其中若干个平行摆杆1002的两端分别与上滑块固定板1001、下滑块固定板1003转动相连并形成平行四边形机构(本实施例中摆杆1002的两端分别安装有轴承,上滑块固定板1001、下滑块固定板1003上分别对应固定有与上述轴承匹配的轴承销,从而实现摆杆1002与上滑块固定板1001、下滑块固定板1003之间的转动相连)。所述上滑块固定板1001与滑动板3固定相连,下滑块固定板1003与驱动机构6驱动相连,通过驱动机构6驱动下滑块固定板1003沿水平方向进行运动,在摆杆1002的作用下上滑块固定板1001就会进行上下运动,从而带动滑动板3与踏板2同步进行升降运动。本实施例通过摆杆传动机构的设置,并对其结构进行优化设计,从而一方面有利于保证滑动板3升降运动的平稳性,并有效防止车轮压过踏板2时滑动板3发生倾斜,另一方面还可以有效节省驱动机构6的安装空间,直接将驱动机构6输出端的水平运动转化为滑动板3的升降运动。
实施例3
本实施例的一种用于精确检测车轮踏面擦伤及不圆度的系统,其结构基本同实施例2,其区别主要在于:本实施例的摆杆传动机构10通过滑轨机构与底板总成5可滑动连接,该底板总成5固定安装于轨道1底部,所述固定板总成4及驱动机构6均安装于底板总成5上。具体的,所述滑轨机构包括滑块1004和导轨1005,其中导轨1005固定安装于底板总成5上,滑块间隔固定安装于下滑块固定板1003的底部,当驱动机构6工作时,驱动下滑块固定板1003沿直线导轨1005进行水平运动,从而有利于保证摆杆传动机构10运动的平稳性。
实施例4
本实施例的一种用于精确检测车轮踏面擦伤及不圆度的系统,其结构基本同实施例3,其区别主要在于:本实施例的检测机构对称安装于双侧轨道内侧,且同一侧检测机构的数量≥2,且每一侧检测机构的长度总和大于车轮的周长,这样既可以保证检测出大于车轮周长的车轮踏面周向数据,同时又能够满足对前后不同车轮检测的需求,防止前一车轮未离开检测机构而后一车轮已进入检测机构对检测结果的影响。其中,第一个检测机构与前置机构13保持一定的距离,车轮行经该距离所用的时间能够满足检测机构调整预压量所用的时间。
本实施例中所述前置机构13的前方还设有触发机构,该触发机构包括沿单侧轨道内侧间隔设置的第一磁钢1201和第二磁钢1202。根据第一磁钢1201和第二磁钢1202的触发顺序可以判断列车的入库与出库,从而便于决定前置机构13和检测机构的启动与否。具体的,当磁钢的触发顺序为第一磁钢1201-第二磁钢1202时,列车为入库,前置机构和检测机构启动,准备进行车轮检测;当磁钢的触发顺序为第二磁钢1202-第一磁钢1201时,列车为出库,所有检测机构不启动,列车出库时,设备不启动,检测机构呈避让状态,车轮与机构不接触,消除了列车出库时车轮与检测机构之间的冲击力与摩擦力,既保护了机构,又实现了设备的自动检测。因此,通过安装在设备前端的磁钢作为外部触发信号,可以控制设备的启动。同时,通过第一磁钢1201和第二磁钢1202的安装还可以用来测车速,当安装距离已知时,记录两个磁钢被触发的时间间隔,就可以计算得到列车速度。
实施例5
本实施例的一种用于精确检测车轮踏面擦伤及不圆度的系统,其结构基本同实施例4,其区别主要在于:结合图2、图4、图6和图7,本实施例的底板总成5包括底部支撑板501,底部支撑板501上设有第一轨道压板502和第二轨道压板508,第一轨道压板502通过压板螺栓503与底部支撑板501固定相连,所述轨道1底部两侧分别压紧固定于第一轨道压板502、第二轨道压板508与底部支撑板501之间;所述底部支撑板501上还设有压板螺母504,压板螺母504上加工有与轨道1底部侧边仿形的咬口,且压板螺母504通过拉杆螺栓505与底部支撑板501底部的固定耳506固定相连。拉杆螺栓505通过固定耳506紧固压板螺母504时,压板螺母504与第二轨道压板508之间的咬口距离缩小,使得底板总成5与钢轨紧紧地固定在一起;然后再通过压板螺栓503和第一轨道压板502进一步将底部支撑板501与钢轨连接紧固。本实施例中底部支撑板501的两侧还设有加强筋507,底部支撑板501与加强筋507是一体式,可采用铸造或焊接的形式,以保证机构整体的刚性,以满足整个机构的测量精度需要。
实施例6
本实施例的一种用于精确检测车轮踏面擦伤及不圆度的系统,其结构基本同实施例5,其区别主要在于:如图3、4所示,所述滑动板3与踏板2及固定板总成4之间的滑轨机构均包括相互配合的滑块与导轨,本实施例中踏板2与固定板总成4上分别固定安装有滑块,滑动板3上对应设有与上述滑块滑动配合的导轨,其中滑动板3与固定板总成4之间的滑轨机构相对于滑动板3垂直安装,滑动板3与踏板2之间的滑轨机构相对于滑动板3倾斜安装,从而有利于提高整个装置的结构稳固性,并有效降低车轮对测量装置的冲击作用。
实施例7
本实施例的一种用于精确检测车轮踏面擦伤及不圆度的系统,其结构基本同实施例6,其区别主要在于:所述的驱动机构6采用电机驱动,具体的,如图5、图7所示,本实施例的驱动机构6包括驱动电机601、丝杠603和丝杠螺母604,其中驱动电机601通过电机安装座602固定安装于底部支撑板501底部,其输出轴通过联轴器与丝杠603一端固定相连,丝杠603另一端穿过丝杠螺母604并与丝杠螺母604螺纹相连,且底部支撑板501上还固定有丝杠固定座605,丝杠603穿过丝杠固定座605与电机输出轴相连。所述丝杠螺母604通过螺母连杆1006与摆杆传动机构10的下滑块固定板1003固定相连,本实施例中螺母连杆1006的下端套装固定于丝杠螺母604表面,其上端穿过底部支撑板501与下滑块固定板1003固定相连。电机转动时驱动丝杠603转动,丝杠螺母604会带着螺母连杆1006和下滑块固定板1003一起沿着水平方向来回移动,从而实现滑动板3的上下运动。同时需要说明的是,所述的驱动机构6并不限于本实施例的具体结构,只要能实现下滑块固定板1003水平运动的驱动即可,比如采用伺服电动缸直接代替本实施例的驱动电机601,并使伺服电动缸的缸杆与螺母连杆1006固定相连。
实施例8
本实施例的一种用于精确检测车轮踏面擦伤及不圆度的系统,其结构基本同实施例7,其区别主要在于:本实施例中丝杠603的端部还与电磁制动器11固定相连,且电磁制动器11固定安装于底部支撑板501底部。
因系统的需要,当车轮在压上踏板2时,此时踏板2承受的力会通过弹性元件8传递给滑动板3,如果滑动板3产生了位移,则测量就会受影响,甚至位移传感器测量不到数据。此时滑动板3要保持位置不动尤为重要。本实施例通过在丝杠603的端部安装一个电磁制动器11,当电机驱动时,电磁制动器11打开制动,电机能够顺利将滑动板3实现上下运动。当车轮压上踏板2时,电机保持不动,电磁制动器11则保持制动,从而保证丝杠螺母604不会产生水平的移动,滑动板3则不会产生上下的位移,进而保证了测量精度。
如图11所示,本实施例的用于精确检测车轮踏面擦伤及不圆度的方法,其过程如下:
步骤一、列车出入库判断
通过触发单元的触发顺序判断列车的入库与出库,若列车为入库,则通过控制系统控制前置机构13和检测机构启动,准备进行车轮检测;若列车为出库,则前置机构13和检测机构均不启动;
步骤二、列车车轮的轮缘高检测
当列车为入库,且行经前置机构13时,通过前置机构13对列车车轮的轮缘高进行检测,并反馈给控制系统;
步骤三、检测机构踏板的预压量调节
根据前置机构13的检测结果,通过控制系统控制升降驱动机构6运行,从而对检测机构中踏板2的初始高度进行调节,当踏板2的预压量处于设定范围时升降驱动机构6停止运行。
踏板预压量的控制方式为:系统启动时,当前置机构检测出车轮轮缘高为sh1时,系统判断此轮缘高是否达到预压量为1.5-2mm,如果预压量在此范围,则检测机构不需要动作,如果不在此范围,检测机构的伺服电机控制踏板升降至w2位置,使轮缘高sh1达到1.5-2mm的预压量。当前置机构13检测出后一车轮的轮缘高为sh2,并且前一车轮已经通过检测机构时,检测机构判断当前w2位置是否处于轮缘高sh2预压量为1.5-2mm的范围,并作相应的升降调整,直至检测完整列车的车轮。当前置机构13在一段时间内不再产生新的轮缘高时,认为列车已经通过检测系统,前置机构13和检测机构归于零位,系统停止工作。在调节检测机构预压量的过程中,前置机构13始终位于w1位置不变,而且每侧钢轨的多套检测机构每次均升降到同一位置。
步骤四、列车车轮的踏面径向跳动检测
当列车车轮行经检测机构时,通过该检测机构对列车车轮的踏面径向跳动进行检测。
实施例9
本实施例的一种用于精确检测车轮踏面擦伤及不圆度的系统,其结构基本同实施例8,其区别主要在于:结合图2,本实施例的固定板总成4包括主固定板401、位于主固定板401两端的端固定板402以及位于主固定板401顶部的上封板403,主固定板401、端固定板402及上封板403共同围绕形成箱式结构。其中滑动板3通过第一滑轨701与踏板2滑动相连,通过第二滑轨702与主固定板401滑动相连,并通过第三滑轨703与端固定板402滑动相连,从而可以进一步提高整个装置结构的稳定性及滑动板上下运动时的平稳性,有利于保证测量精度。更进一步的,所述踏板2与滑动板3之间还设有中间固定板404,且滑动板3与中间固定板404通过第四滑轨704滑动相连,主固定板401、端固定板402、上封板403及中间固定板404共同围绕形成相对封闭的箱式结构,滑动板3即安装于箱式固定板总成内部。本实施例中位移传感器901通过传感器安装座902固定安装于上封板403上,所述传感器安装座902加工为c型结构。
实施例10
本实施例的一种用于精确检测车轮踏面擦伤及不圆度的系统,其结构基本同实施例9,其区别主要在于:所述的弹性元件8可采用弹簧,具体的,如图4所示,本实施例的弹性元件8采用压簧结构,其通过弹性元件支座801固定安装于滑动板3上(弹性元件支座801上加工有与弹性元件直径相同的安装孔),所述踏板2上对应设有与弹性元件8的活塞杆端部作用的弹性元件支撑板803,本实施例的弹性元件支撑板803加工为z字型。本实施例中滑动板3上还固定有弹性元件调节板802,该弹性元件调节板802为l型,用螺栓固定在滑动板3上,弹性元件调节板802上加工有螺纹孔,顶丝穿过该螺纹孔顶在踏板的弹性元件支撑板803上,即用顶丝来实现弹簧预压力的调节,调节到预定位置后,再使用一个螺母将顶丝并紧。
需要说明的是,上述弹性元件8具体包括但不限于螺旋弹簧、气体弹簧、液体弹簧、片簧、橡胶弹簧等等,其安装支座可根据元件的外形及使用要求制作不同的支座,只要能实现踏板2与滑动板3之间的随动弹性相连即可。比如,当采用图8中的螺旋拉簧作为弹性元件时,在踏板2及滑动板3上均固定有弹簧销804,如图9所示,螺旋拉簧的两端均设有弹簧勾,且弹簧销804上对应加工有与弹簧勾对应的勾槽805,螺旋拉簧的两端即通过弹簧勾分别固定安装于踏板2与滑动板3上。
采用本实施例的检测机构进行检测的具体过程为:
步骤一、踏板高度调节:根据待检测列车车轮的轮缘高,通过驱动机构6驱动摆杆传动机构10进行摆动,从而带动滑动板3进行升降,此时踏板2与滑动板3之间无相对运动,踏板2随滑动板3同步升降,当踏板2升降到指定位置时,驱动机构6停止工作;
步骤二、车轮径向跳动检测:当车轮压上踏板2时,踏板2被车轮轮缘压下,产生沿滑轨方向向下的位移,在踏板2下降的过程中,在驱动机构6的作用下滑动板3相对于固定板总成4保持不动,此时位移传感器901即相对于位移感应板903产生相对位移,通过转化即求得车轮经过时踏板2被车轮轮缘压下的位移;通过对整个车轮踏面周长内位移传感器901所采集到的数据进行处理,即可得到列车车轮踏面径向跳动情况;
步骤三、当车轮离开时,踏板2在弹性元件8的作用下恢复到初始位置;此时驱动机构6继续启动工作,驱动踏板2下降到指定位置,该位置不论经过的车轮的轮缘高是多少,车轮轮缘均不能压到踏板2。
具体的,当踏板2长度大于车轮周长时,可以检测到车轮踏面一周的周向数据,进一步描绘出车轮踏面失圆情况。通过对每个检测机构踏板2的位移曲线进行截取、拼接,得到一条从第一个检测机构至最后一个检测机构的踏板2位移曲线,并从中得到最大值和最小值,最大值与最小值的差值就是该车轮的径向跳动值。
其中,系统控制检测机构踏板2升降至合适预压量的方法有两种,查表法与追踪法。查表法是将最小轮缘高到最大轮缘高等分成n个区间,每个区间对应不同的检测机构踏板2位置wn,当前置机构13检测出待测车轮的轮缘高sh时,判断此轮缘缘高属于哪个区间,再把检测机构踏板2升降至该区间对应的位置w。追踪法是利用位移传感器作为反馈信号,不断调节检测机构踏板2的位置,直至位移传感器的示值达到所需预压量下的示值为止。例如位移传感器当前示值为z1,当前置机构检测出待测车轮的轮缘高sh时,系统根据预压量计算位移传感器需要达到的示值z2,然后开启伺服电机进行升降,电机升降的过程中,位移传感器的示值不断变化,并作为反馈信号传递给伺服电机,直至位移传感器的示值达到z2时,认为检测机构踏板2已升降至所需位置,然后关闭电机。
实施例11
本实施例的一种用于精确检测车轮踏面擦伤及不圆度的系统,其结构基本同实施例10,其区别主要在于:本实施例的前置机构13的结构同检测机构,如图12所示,其中前置机构13的踏板上表面沿列车入库方向依次包括上坡段201、水平段202和下坡段203,车轮经过前置机构13时,会在踏板总成2的水平段202产生一个位移最大值,根据该最大值可以测量出车轮的轮缘高,具体方法为:当已知轮缘高为sh1的车轮经过前置机构13时,前置机构13踏板的最大位移为h1,当未知轮缘高的车轮经过前置机构时,前置机构踏板的最大位移为h2,则未知车轮的轮缘高sh2=sh1 (h2-h1)。
实施例12
本实施例的一种用于精确检测车轮踏面擦伤及不圆度的系统,其结构基本同实施例11,其区别主要在于:本实施例中每侧轨道内侧的检测机构包括第一检测机构1401、第二检测机构1402、第三检测机构1403和第四检测机构1404。
当磁钢检测出列车为入库时,检测系统启动,前置机构和四套检测机构上升到指定位置,该过程在列车到达前置机构之前完成。当前置机构检测出第一个车轮的轮缘高时,四套检测机构结合当前位置判断此轮缘高是否满足预压量为1.5-2mm的要求,若不满足,则plc控制伺服电机升降至满足条件的位置,此过程在待检测车轮到达第一检测机构1401前完成。当第四检测机构1404动作完成后,启动log数据记录,记录车轮经过各个检测机构时踏板的垂向位移,当车轮离开第四检测机构1404时,停止log数据记录。当前置机构检测出第二个车轮的轮缘高时,第一个车轮尚未通过检测机构,此时各个检测机构先判断第一个车轮是否已经离开,如果第一个车轮已经离开,则检测机构根据当前位置和第二个车轮的轮缘高升降到合适的位置,如果第一个车轮尚未离开,或者尚示到达该检测机构,则等到第一个车轮离开后检测机构才开始升降。每当第一检测机构1401升降结束,系统便会启动一个log数据记录,同样,每当第四检测机构1404检测出车轮离开,便会停止前一个log数据记录。直至前置机构无新值检测出时,系统认为列车已通过检测机构,前置机构和检测机构返回到初始位置。
将四套检测机构的位移传感器采集到的数据均传送给上位机,该数据的大小反映的是车轮踏面不同周向位置轮缘高的相对值的大小,当踏板长度大于车轮周长时,可以检测到车轮踏面一周的周向数据,进一步描绘出车轮踏面失圆情况。上位机对每个检测机构踏板的位移曲线进行截取、拼接,得到一条从第一检测机构1401至第四检测机构1404的踏板位移曲线,并从中的到最大值和最小值,最大值与最小值的差值就是该车轮的径向跳动值。
以上示意性的对本实用新型及其实施方式进行了描述,该描述没有限制性,附图中所示的也只是本实用新型的实施方式之一,实际的结构并不局限于此。所以,如果本领域的普通技术人员受其启示,在不脱离本实用新型创造宗旨的情况下,不经创造性的设计出与该技术方案相似的结构方式及实施例,均应属于本实用新型的保护范围。
本文用于企业家、创业者技术爱好者查询,结果仅供参考。