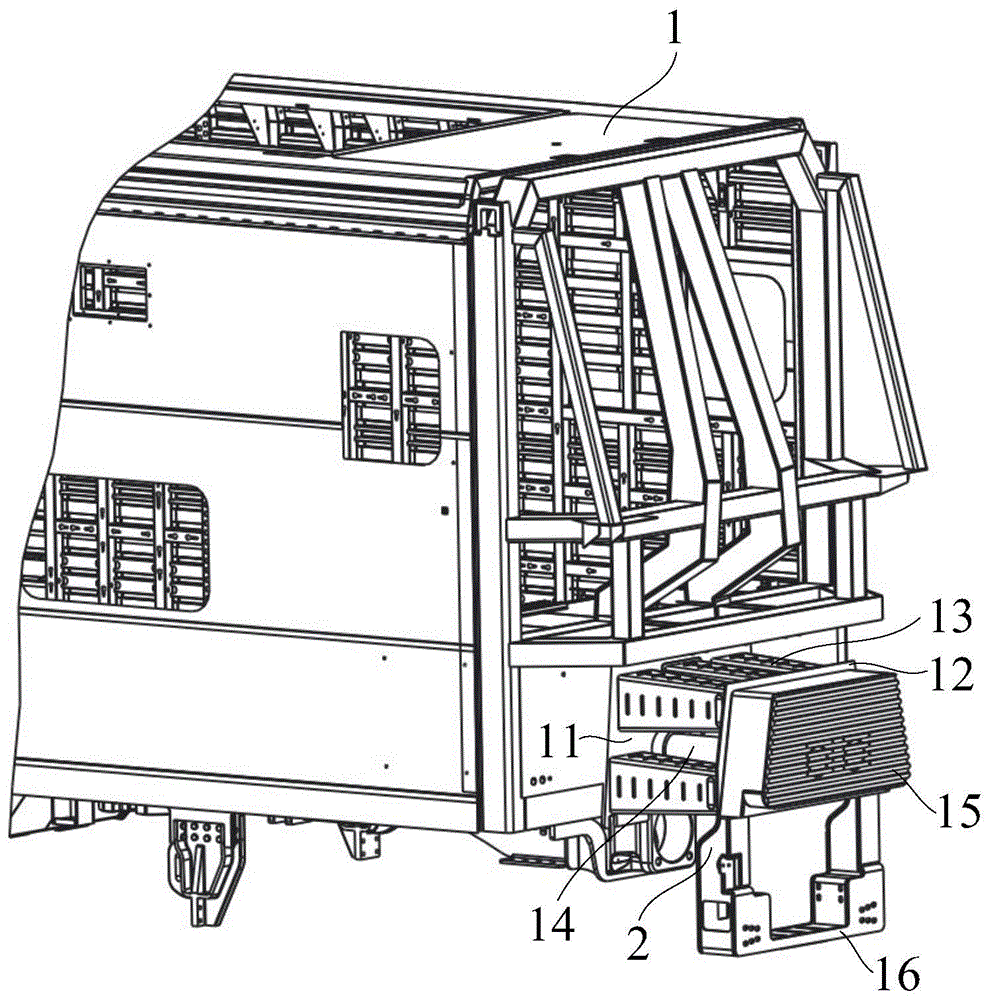
本申请涉及轨道车辆技术领域,具体地,涉及一种轨道车辆及其车端吸能结构。
背景技术:
随着轨道交通行业的快速发展,动车组、城市轨道列车等轨道车辆已成为人们日常出行的重要交通工具,轨道车辆的运行安全性极其重要。当轨道车辆的主动安全防护失效时,被动安全将成为保护乘客生命、财产安全的最重要的保障。因此,轨道车辆结构的耐撞性设计至关重要,尤其是作为碰撞第一接触面的车端吸能结构。为了保证轨道车辆在发生碰撞事故时的安全性,需要设计一种能够稳定、有序、可控变形的车端吸能结构,实现轨道车辆的被动安全防护功能,提高轨道车辆的运行安全性。
技术实现要素:
本申请实施例中提供了一种轨道车辆及其车端吸能结构,该车端吸能结构能够在碰撞发生时进行稳定、有序、可控变形,实现轨道车辆的被动安全防护功能,并能提高轨道车辆的运行安全性。
根据本申请实施例的第一个方面,提供了一种用于轨道车辆的车端吸能结构,该车端吸能结构包括安装面板、固定板、吸能机构、导向机构以及防爬器;
所述吸能机构包括多个吸能盒,每个吸能盒的一端固定安装于所述安装面板、且另一端固定安装于所述固定板;
所述防爬器固定安装于所述固定板背离所述安装面板的一端,所述防爬器在背离所述安装面板的一端设置有多个防爬齿;
所述导向机构与所述安装面板和所述固定板均固定连接,并且背离所述安装面板的一端穿过所述固定板后与所述防爬器固定连接,背离所述固定板的另一端穿过所述安装面板,用于与所述轨道车辆的车体固定连接。
优选地,所述吸能盒包括:
前端板,固定安装于所述固定板;
后端板,固定安装于所述安装面板;
筒体,固定安装于所述前端板和所述后端板之间,并在朝向所述前端板的一端设置有用于诱导变形的诱导结构;
多个隔板,沿从所述前端板到所述后端板的方向间隔固定安装于所述筒体内。
优选地,所述诱导结构为开设于所述筒体上的压痕。
优选地,所述筒体由相对设置的两个u型板焊接而成。
优选地,所述筒体的横截面为矩形,在所述筒体的每个侧面上设置有与所述隔板一一相对应的开口;
所述隔板的四周均设置有凸缘,所述凸缘插入对应的所述开口内。
优选地,所述筒体为四棱台形结构,所述筒体朝向所述前端板的横截面面积小于所述筒体朝向所述后端板的横截面面积。
优选地,所述筒体中相对的两个侧面形成的夹角为2°~10°。
优选地,所述隔板的数量为4~8。
优选地,所述吸能盒的数量为4~8。
优选地,所述吸能盒分布成上、下两排。
优选地,所述导向机构设置于下排的两个所述吸能盒之间。
优选地,所述隔板为矩形环状结构或十字形结构。
优选地,所述导向机构包括:
后套筒安装板,固定连接于所述车体;
前套筒安装板,固定连接于所述固定板;
两个平行设置的导向柱,所述导向柱的一端固定安装于所述后套筒安装板、且另一端穿过所述前套筒安装板后固定安装于所述防爬器。
优选地,
所述导向柱在朝向所述后套筒安装板的一端套设有后套筒,所述后套筒固定连接于所述后套筒安装板和所述安装面板;
所述导向柱的另一端焊接有端盖;
在所述导向柱穿设所述前套筒安装部的部分套设有前套筒,所述前套筒固定连接于所述前套筒安装板。
优选地,还包括固定安装于所述防爬器底部的车钩托梁,所述车钩托梁为u形结构。
根据本申请实施例的第二个方面,还提供了一种轨道车辆,包括车体,还包括上述技术方案提供的任意一种车端吸能结构,所述车端吸能结构的安装面板和导向机构固定安装于所述车体的端部。
采用本申请实施例中提供的轨道车辆及其车端吸能结构,具有以下有益效果:
上述车端吸能结构通过安装面板和导向机构固定安装于车体的端部,在轨道车辆的车体端部发生碰撞时,通过防爬器防止轨道车辆产生爬车现象,并通过吸能机构吸收碰撞能量,在碰撞吸能过程中通过导向机构保证吸能结构不受偏载的影响,发生稳定、有序、可控的变形来吸收碰撞能量,实现轨道车辆的被动安全防护功能,并能提高轨道车辆的运行安全性。
附图说明
此处所说明的附图用来提供对本申请的进一步理解,构成本申请的一部分,本申请的示意性实施例及其说明用于解释本申请,并不构成对本申请的不当限定。在附图中:
图1为本申请实施例提供的车端吸能结构在安装于车体时的装配结构示意图;
图2为本申请实施例提供的车端吸能结构的立体结构示意图;
图3为图2中提供的车端吸能结构的仰视图;
图4为图2中提供的车端吸能结构的一种吸能盒的立体结构示意图;
图5为图4中提供的吸能盒的侧视结构示意图;
图6为图4中提供的吸能盒的内部结构示意图;
图7为图2中提供的车端吸能结构的另一种吸能盒的结构示意图;
图8为图6中提供的吸能盒中隔板的结构示意图;
图9为图4中提供的吸能盒的另一种隔板的结构示意图;
图10为图2中提供的车端吸能结构的导向机构的结构示意图。
附图标记:
1-车体;2-车端吸能结构;11-安装面板;12-固定板;13-吸能机构;14-导向机构;15-防爬器;16-车钩托梁;131-吸能盒;132-前端板;133-后端板;134-筒体;135-隔板;136-诱导结构;1341-u型板;1351-凸缘;141-后套筒安装板;142-前套筒安装板;143-导向柱;144-后套筒;145-端盖;146-前套筒;151-防爬齿;152-顶镐位。
具体实施方式
为了使本申请实施例中的技术方案及优点更加清楚明白,以下结合附图对本申请的示例性实施例进行进一步详细的说明,显然,所描述的实施例仅是本申请的一部分实施例,而不是所有实施例的穷举。需要说明的是,在不冲突的情况下,本申请中的实施例及实施例中的特征可以相互组合。
本申请实施例提供了一种轨道车辆,该轨道车辆包括车体以及安装于车体端部的车端吸能结构,车端吸能结构包括安装面板、固定板、吸能机构、导向机构以及防爬器,并且车端吸能结构通过安装面板和导向机构固定安装于车体的端部。该车端吸能结构可以安装于带有司机室的车体的端部,也可以安装于普通车厢的端部。如图1结构所示,车端吸能结构安装于司机室前端的底部端墙上。安装于车体端部的车端吸能结构能够在轨道车辆发生碰撞时进行稳定、有序、可控变形,实现轨道车辆的被动安全防护功能,并能提高轨道车辆的运行安全性。
本申请实施例提供的车端吸能结构主要用于满足北美标准apta(theamericanpublictransportationassociation,美国公共运输协会)pr-cs-s-034-99,rev.2《standardforthedesignandconstructionofpassengerrailroadrollingstock》的要求。该车端吸能结构主要特点是压溃距离短、平均压溃力大(大于4mn)、吸能量大(大于2.5mj),可以同时满足与相同列车碰撞和与机车牵引列车碰撞的要求。
上述车端吸能结构2可以采用以下具体结构来实现:
如图2和图3结构所示,用于轨道车辆的车端吸能结构2包括安装面板11、固定板12、吸能机构13、导向机构14、防爬器15以及车钩托梁16;其中:如图1结构所示,安装面板11可以通过焊接或者螺栓等紧固件固定连接到司机室前端的端墙上;当将该车端吸能结构2用于其它车厢时,同样通过安装面板11固定安装于车厢端部的端墙上;
吸能机构13包括多个吸能盒131,每个吸能盒131的一端固定安装于安装面板11、且另一端固定安装于固定板12;吸能盒131的长度方向与轨道车辆的长度方向相一致,并且各吸能盒131之间平行设置,在轨道车辆发生碰撞时,吸能盒131沿其长度方向被挤压变形,从而通过变形吸收碰撞能量实现碰撞能量的消耗,以保护轨道车辆和乘客的安全;吸能盒131可以分布成上、下两排,其中,上排的吸能盒131与下排的吸能盒131之间可以上下对齐设置,也可以交错设置;沿轨道车辆的车宽方向,导向机构14设置于下排的两个吸能盒131之间;如图2和图3结构中,吸能机构13由固定连接于安装面板11和固定板12之间的五个吸能盒131构成,吸能盒131分为上、下两排设置,上排间隔设置有三个吸能盒131,在下排设置有两个吸能盒131;并在下排的两个吸能盒131之间设置有导向机构14;吸能盒131的数量可以为4~8个,即,在车端吸能结构2中可以设置有4、5、6、7、8个吸能盒131,同时,在吸能盒131的结构尺寸较小时,还可以设置更多个吸能盒131;吸能盒131可以设置为上、下两排,也可以设置为一排、三排或多排,一排可以设置两个吸能盒131、三个吸能盒131或多个吸能盒131,所需设置的吸能盒131数量与需要吸收的碰撞能量大小相关。
防爬器15固定安装于固定板12背离安装面板11的一端,防爬器15在背离安装面板11的一端设置有多个防爬齿151;如图1和图2结构所示,防爬器15位于车体1和车端吸能结构2的最前端,用于在轨道车辆发生碰撞时,通过防爬齿151进行咬合,防止轨道车辆发生爬车现象;
导向机构14与安装面板11和固定板12均固定连接,并且背离安装面板11的一端穿过固定板12后与防爬器15固定连接,背离固定板12的另一端穿过安装面板11,用于与轨道车辆的车体1固定连接;如图3结构所示,导向机构14朝向车体1的一端突出于安装面板11,并与车体1的端部固定连接;导向机构14背离车体1的一端固定安装于固定板12和防爬器15,用于在碰撞过程中,如果轨道车辆发生正向碰撞,没有发生偏载则导向机构14不发生作用,吸能机构13发生有序、可控的变形以吸收碰撞能量;如果轨道车辆发生碰撞时发生偏载则导向机构14发挥作用,保证吸能机构13不受偏载的影响,依然可以发生有序、可控、稳定的变形以吸收碰撞能量,保证轨道车辆的安全;
车钩托梁16为u形结构,固定安装于防爬器15的底部。如图1和图2结构所示,在防爬器15的底部固定安装有车钩托梁16,车钩托梁16为u形结构,用于使回退式车钩能够顺利穿过,同时对回退式车钩进行固定和支承。如图3结构所示,车钩托梁16的底面设置有顶镐位152,用于对轨道车辆进行顶升操作。
轨道车辆在发生碰撞时,首先,车体1端部的两个车钩接触,车钩缓冲器进行压缩,紧接着是车钩压溃管变形吸能,最后车钩自由运动,退出整个碰撞系统;其次,车端吸能结构2通过防爬器15上的防爬齿151进行咬合,通过防爬齿151可以有效防止爬车;然后,吸能机构13开始发生变形吸能,吸能机构13中的吸能盒131通过发生有序、可控的变形吸收碰撞能量;如果发生碰撞时轨道车辆是正向碰撞,没有发生偏载则导向机构14不发生作用,吸能机构13发生进行变形吸能;如果发生碰撞时轨道车辆发生偏载则导向机构14发挥作用,保证吸能机构13不受偏载的影响,依然可以发生有序、可控、稳定的变形以吸收碰撞能量。
上述车端吸能结构2通过安装面板11和导向机构14固定安装于车体1的端部,在轨道车辆的车体1端部发生碰撞时,通过防爬器15防止轨道车辆产生爬车现象,并通过吸能机构13吸收碰撞能量,在碰撞吸能过程中通过导向机构14保证吸能结构不受偏载的影响,发生稳定、有序、可控的变形来吸收碰撞能量,实现轨道车辆的被动安全防护功能,并能提高轨道车辆的运行安全性。
如图4、图5和图7结构所示,吸能盒131包括前端板132、后端板133、筒体134和多个隔板135;前端板132固定安装于固定板12;后端板133固定安装于安装面板11;筒体134固定安装于前端板132和后端板133之间,并在朝向前端板132的一端设置有用于诱导变形的诱导结构136;多个隔板135沿从前端板132到后端板133的方向间隔固定安装于筒体134内。如图4和图5结构所示,诱导结构136可以为开设于筒体134上的压痕和/或通孔,压痕或通孔可以对称设置,即在筒体134的相对位置上均设置有压痕,或在筒体134的相对位置上均设置有通孔,以使筒体134能够在诱导结构136的诱导下发生均匀变形。诱导结构136还可以为压痕、凹槽、裂缝等结构。在筒体134内设置的隔板135的数量可以为4~8,即,在筒体134内可以间隔设置有4、5、6、7、8个隔板135,如在图4、图5、图6和图7中的吸能盒131中均设置有6个隔板135,即,在本申请实施例中以设置有6个隔板135的吸能盒131为例进行说明。如图8结构所示,隔板135为矩形环状结构,在隔板135的四周均设置有凸缘1351;如图9结构所示,隔板135为十字形结构,在隔板135的四周均设置有凸缘1351,并且在图9中所示的隔板135中还设置有通孔。
当吸能盒131发生碰撞被压溃时,首先通过诱导结构136发生诱导变形,吸收能量;接着通过诱导变形和隔板135的控制作用使吸能盒131的各个胞体依次发生压溃,最终实现吸能盒131发生有序变形,吸收能量,保证车辆和人员的生命财产安全。
如图6结构所示,筒体134可以由相对设置的两个u型板1341焊接而成,并将隔板135固定安装于两个u型板1341之间,隔板135可以焊接于u型板1341上,也可以插接在u型板1341上。
如图6结构所示,筒体134的横截面为矩形,在筒体134的每个侧面上设置有与隔板135一一相对应的开口;隔板135的四周均设置有凸缘1351,凸缘1351插入对应的开口内。隔板135通过四周的凸缘1351插接于筒体134周向的开口中,通过开口既可以实现对隔板135的定位和安装,同时还可以实现筒体134的诱导变形,使筒体134在碰撞压溃过程中能够稳定、有序地变形。
如图4结构所示,筒体134为四棱台形结构,筒体134朝向前端板132的横截面面积小于筒体134朝向后端板133的横截面面积。筒体134中相对的两个侧面形成的夹角可以为2°~10°,如:2°、3°、4°、5°、6°、7°、8°、9°、10°。
由于筒体134为四棱台形结构,并且从远离车体1的一端朝向靠近车体1一端横截面面积逐渐变大,从而能够在碰撞发生过程时,随着吸能盒131的压缩变形量越大而吸收的碰撞能量越多,使得在开始碰撞时能够通过横截面面积较小的端部进行诱导变形,并且通过靠近车体1一侧的较大的横截面面积能够适应较大的碰撞能量,使车辆在碰撞过程中能够保证车辆和乘客的安全。
如图3和图10结构所示,导向机构14包括后套筒安装板141、前套筒安装板142以及两个平行设置的导向柱143;后套筒安装板141固定连接于车体1;前套筒安装板142固定连接于固定板12;导向柱143的一端固定安装于后套筒安装板141、且另一端穿过前套筒安装板142后固定安装于防爬器15。在本申请实施例中,导向机构14以设置有两个导向柱143为例进行说明,但是在实际设计过程中,也可以根据实际需要增加或减少导向柱143的数量。导向柱143的长度方向,即,导向柱143的轴向沿轨道车辆的长度方向设置,在轨道车辆发生碰撞时,导向柱143支承于两个车体之间。导向机构14可以包括两个平行设置的导向柱143,也可以仅包括一个导向柱143、三个导向柱143或多个导向柱143,当设置有两个或多个导向柱143时,导向柱143可以分布为一排或一列,也可以分布成其它形状,还可以与吸能盒131之间间隔分布。
导向柱143在朝向后套筒安装板141的一端套设有后套筒144,后套筒144固定连接于后套筒安装板141和安装面板11;导向柱143的另一端焊接有端盖145;在导向柱143穿设前套筒146安装部的部分套设有前套筒146,前套筒146固定连接于前套筒安装板142。
导向机构14的工作原理为:两个导向柱143平行设置,并与车体1垂直设置;导向柱143上套设有前套筒146和后套筒144,并在导向柱143靠近车体1的一端部焊接有后套筒安装板141,后套筒安装板141和后套筒144可以通过焊接或栓接等方式进行固定连接,并将后套筒安装板141和导向管焊接或栓接在车体1上或安装面板11上;前套筒安装板142和前套筒146焊接或栓接,并将前套筒安装板142焊接或栓接到固定板12上,导向柱143朝向防爬器15的端部焊接有端盖145,并将导向柱143的端部焊接或栓接到防爬器15的前面板上。当轨道车辆发生碰撞时,防爬器15首先啮合,然后吸能盒131开始压溃,随着吸能盒131的压溃,导向机构14可以承载垂向载荷,并沿着前套筒146和后套筒144向后滑动,对吸能机构13起到导向作用,以保证在发生偏置碰撞时吸能机构13依然保持顺序变形。
由于导向柱143的一端部直接固定在车体1上,并且导向柱143与车体1的端部垂直设置,因此,在碰撞过程中,能够通过导向柱143对吸能机构13进行导向,从而保证吸能机构13中的吸能盒131在碰撞过程中始终能够稳定、有序、可控的变形以吸收碰撞能量,从而保证轨道车辆及其乘客的安全,提高轨道车辆运行的安全性。
尽管已描述了本申请的优选实施例,但本领域内的技术人员一旦得知了基本创造性概念,则可对这些实施例作出另外的变更和修改。所以,所附权利要求意欲解释为包括优选实施例以及落入本申请范围的所有变更和修改。
显然,本领域的技术人员可以对本申请进行各种改动和变型而不脱离本申请的精神和范围。这样,倘若本申请的这些修改和变型属于本申请权利要求及其等同技术的范围之内,则本申请也意图包含这些改动和变型在内。
本文用于企业家、创业者技术爱好者查询,结果仅供参考。