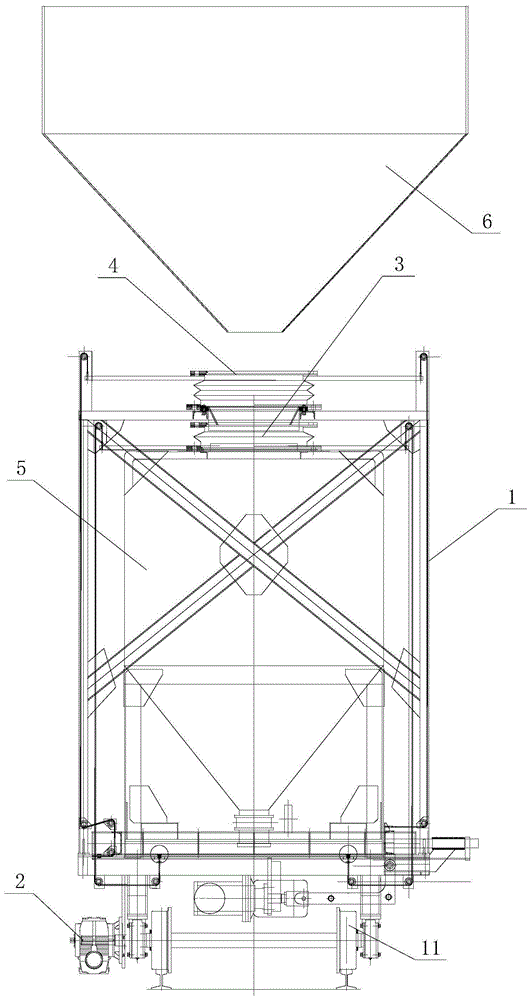
本实用新型涉及钒铁冶金领域,尤其涉及一种钒铁冶炼工艺配料工序用自动对中配料车。
背景技术:
在钒铁冶炼工艺中,一般采用电炉将配置好的钒原料,进行高温冶炼。在钒物料配比时,目前主要使用集成式料仓若干,按照一定配比,通过接近开关粗略控制配料车启停,主要存在的问题是,当物料成分出现波动时,需要进行精细化配料,由于接近开关控制具有一定滞后性,启停车位置出现差错将直接反映在电炉冶炼产成品率波动。并且配料车定位不准确容易出现抛洒,缺斤短两现象,不能达到精准配料的目的。此外,现有配料车没有升降罩、伸缩套导致配料现场环境粉尘大。冶炼工序之间没有相互支撑,配料工序质量难以固化,严重影响生产质量稳定性,生产设备成本增加。
技术实现要素:
为克服现有配料车定位精度差,环境粉尘大等不足,本实用新型所要解决的技术问题是:提供一种定位更加准确,并且能避免扬尘的钒铁冶炼工艺配料工序用自动对中配料车。
本实用新型解决其技术问题所采用的技术方案是:
钒铁冶炼工艺配料工序用自动对中配料车,包括可容纳料罐的车架,所述车架底部设有驱动轮,所述驱动轮的转轴上设有通过电性连接的编码器和驱动器,所述车架顶部中心设有相互连接的升降罩和伸缩套,并分别配有升降机构和伸缩机构,所述升降罩的下端可在升降机构带动下升降并与放置在车架中的料罐的入口对接或脱离,所述伸缩套的上端可在伸缩机构带动下伸缩并与储料罐的卸料口对接或脱离。
进一步的是,所述车架上正对操作人员的一侧为敞开结构,其余三测设有档杆。
进一步的是,所述车架顶部设有支撑板,支撑板中部设有通孔,所述升降罩的上端固定在支撑板底面通孔的周边,所述伸缩套的下端固定在支撑板顶面通孔的周边。
进一步的是,所述升降罩和伸缩套均为波纹管,并且上下两端均设有橡胶密封垫。
进一步的是,所述升降机构和伸缩机构为分别与升降罩下端和伸缩套上端相连的液压推杆。
进一步的是,所述升降机构包括设置在车架底部的压缩弹簧以及与升降罩的下端相连的升降罩控制杆,所述压缩弹簧包括两个,其下端与车架底部固定,上端设有承压板,所述承压板底部设有拉绳,两个压缩弹簧的两根拉绳分别绕过滑轮与升降罩控制杆的两端相连。
进一步的是,所述伸缩机构包括设置在车架底部的电液推杆,以及与伸缩套的上端相连的伸缩套控制杆,所述电液推杆的推杆端部设有推杆横梁,所述推杆横梁上设有拉绳绕过滑轮与伸缩套控制杆的一端相连,所述推杆横梁上还设有同步滑杆,同步滑杆的端部与伸缩套拉杆的一端相连,所述伸缩套拉杆与电液推杆移动方向平行,伸缩套拉杆的另一端穿过车架后与拉绳相连,该拉绳穿过拉杆滑套后绕过滑轮与伸缩套控制杆的另一端相连。
进一步的是,所述电液推杆上还设有滚轮,车架上设有与滚轮配套的滑轨,所述车架底部还设有同步滑杆座,所述同步滑杆穿插在同步滑杆座上滑动。
本实用新型的有益效果是:
1、利用编码器来实现配料车的移动定位,生产过程中通过计算机输入自动对中配料车启停仓位坐标值,可实现配料车往返在不同成分物料仓位进行自动加料,可实现配料车按照预设的线路进行单点加料,解决因配料车不能精确定位导致物料抛洒的问题;
2、升降罩与伸缩套可分别与料罐入口和储料罐卸料口对接,实现全覆盖密封,消除物料泄露,固化单炉冶炼成品的指标,同时避免了配料车在x轴向、y轴向不对中的问题,消除了配料差错率,固化配料参数,改善作业环境,经济效益显著。
附图说明
图1是本实用新型结构示意图。
图2是本实用新型升降罩系统结构示意图。
图3是本实用新型压缩弹簧结构示意图。
图4是本实用新型伸缩套系统结构示意图。
图中标记为,1-车架,2-编码器,3-升降罩,4-伸缩套,5-料罐,6-储料罐,11-驱动轮,12-支撑板,13-滑轨,14-同步滑杆座,31-压缩弹簧,32-升降罩控制杆,33-承压板,34-升降拉绳,35-第一滑轮,41-电液推杆,42-伸缩套控制杆,43-推杆横梁,44-伸缩拉绳,45-第二滑轮,46-同步滑杆,47-伸缩套拉杆,48-拉杆滑套,49-滚轮。
具体实施方式
下面结合附图对本实用新型进一步说明。
如图1所示,本实用新型的钒铁冶炼工艺配料工序用自动对中配料车,包括可容纳料罐5的车架1,所述车架1底部设有驱动轮11,所述驱动轮11的转轴上设有通过电性连接的编码器2和驱动器,所述车架1顶部中心设有相互连接的升降罩3和伸缩套4,并分别配有升降机构和伸缩机构,所述升降罩3的下端可在升降机构带动下升降并与放置在车架1中的料罐5的入口对接或脱离,所述伸缩套4的上端可在伸缩机构带动下伸缩并与储料罐6的卸料口对接或脱离。
本实用新型的工作过程是:首先在轨道起点处将料罐5放置到配料车的车架1中,然后根据设定的程序,驱动器在编码器2的控制下带动车架1到达对应储料罐6的卸料口下方,然后,升降机构带动升降罩3的下端下降,与料罐5的入口对接,同时伸缩机构带动伸缩套4的上端上升与储料罐6的卸料口对接,最后进行下料。完成后按照上述方式循环,完成配料操作。
相对现有采用接近开关定位的方式,本申请的自动对中配料车采用编码器2精准控制x轴向精度,可达0~2毫米范围,y轴向采用升降罩3和伸缩套4对接,可保证料罐5对中精度在0~2毫米范围内,因此定位精度大大提高,消除了配料差错率,固化了配料参数,改善了作业环境,经济效益显著。
为了对料罐5起到良好的固定作用,将所述车架1上正对操作人员的一侧设计为敞开结构,其余三测设有档杆,保证料罐5的定位和稳固。
对于升降罩3和伸缩套4的具体安装结构,本申请在所述车架1顶部设有支撑板12,支撑板12中部设有通孔,所述升降罩3的上端固定在支撑板12底面通孔的周边,所述伸缩套3的下端固定在支撑板12顶面通孔的周边。两者可通过螺栓固定在支撑板12上,通过通孔实现连通。
为了实现稳定的伸缩功能,所述升降罩3和伸缩套4优选波纹管,并且上下两端均设有橡胶密封垫,提高密封性能。
对于升降机构和伸缩机构的具体结构,可以采用分别与升降罩3下端和伸缩套4上端相连的液压推杆。但由于车架1顶部用于安放设备的空间较小,为了制作方便,可以采用如下优选方案:
如图2、图3所示,所述升降机构包括设置在车架1底部的压缩弹簧31以及与升降罩3的下端相连的升降罩控制杆32,所述压缩弹簧31包括两个,其下端与车架1底部固定,上端设有承压板33,所述承压板33底部设有升降拉绳34,两个压缩弹簧31的两根升降拉绳34分别绕过第一滑轮35与升降罩控制杆32的两端相连。其工作原理是:当没有放入料罐5时,压缩弹簧31弹起,向上拉动升降拉绳34,从而使升降罩3的下端上升;当放入料罐5时,压缩弹簧31被压缩,承压板33及升降拉绳34下降,升降罩3在自身重量作用下下降,与料罐5的入口对接。
如图4所示,所述伸缩机构包括设置在车架1底部的电液推杆41,以及与伸缩套4的上端相连的伸缩套控制杆42,所述电液推杆41的推杆端部设有推杆横梁43,所述推杆横梁43上设有伸缩拉绳44绕过第二滑轮45与伸缩套控制杆42的一端相连,所述推杆横梁43上还设有同步滑杆46,同步滑杆46的端部与伸缩套拉杆47的一端相连,所述伸缩套拉杆47与电液推杆41移动方向平行,伸缩套拉杆47的另一端穿过车架1后与伸缩拉绳44相连,该拉绳穿过拉杆滑套48后绕过第二滑轮45与伸缩套控制杆42的另一端相连。其工作原理是:当配料车到达储料罐6下方时,电液推杆41推动推杆横梁43在水平方向上移动,并带动与之相连的伸缩拉绳44一起移动,同时通过同步滑杆46及伸缩套拉杆47带动另一端的伸缩拉绳44同步移动,从而实现伸缩套控制杆42的上下移动,进而实现伸缩套4与储料罐6的对接。
进一步的,为了保证机构运行的平稳性,在所述电液推杆41上还设有滚轮49,车架1上设有与滚轮49配套的滑轨13,所述车架1底部还设有同步滑杆座14,所述同步滑杆46穿插在同步滑杆座14上滑动。
本实用新型利用编码器来实现配料车的移动定位,生产过程中通过计算机输入自动对中配料车启停仓位坐标值,可实现配料车往返在不同成分物料仓位进行自动加料,可实现配料车按照预设的线路进行单点加料,解决因配料车不能精确定位导致物料抛洒的问题;升降罩与伸缩套可分别与料罐入口和储料罐卸料口对接,实现全覆盖密封,消除物料泄露,固化单炉冶炼成品的指标,同时避免了配料车在x轴向、y轴向不对中的问题,消除了配料差错率,固化配料参数,改善作业环境,经济效益显著。
本文用于企业家、创业者技术爱好者查询,结果仅供参考。