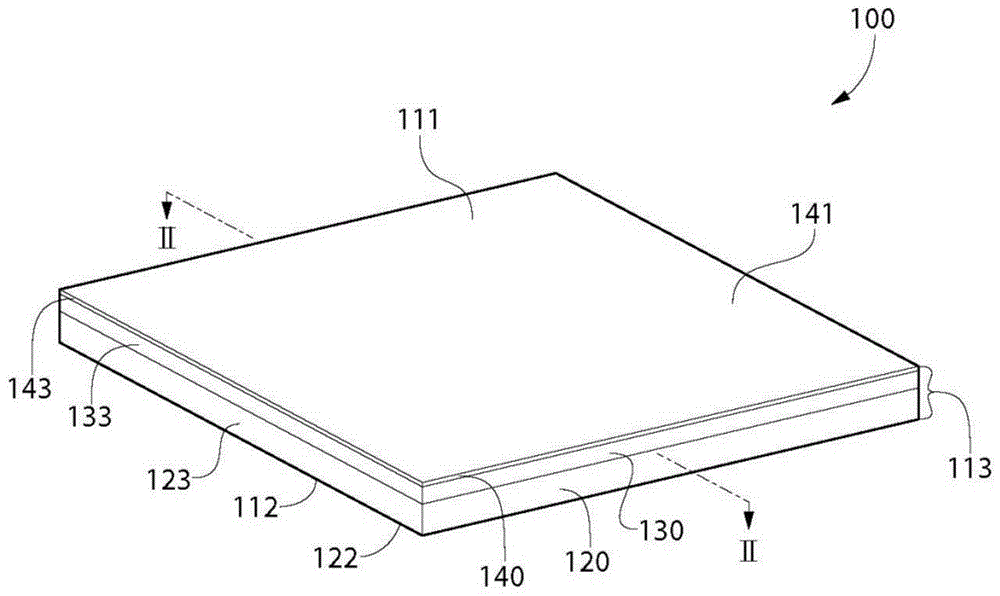
本申请是2017年6月29日提交的申请号为2017800409759、发明名称为“高性能建筑镶板涂层”的中国发明专利申请的分案申请。相关申请的交叉引用本申请要求于2016年6月29日提交的美国临时申请第62/356154号的权益。本申请还要求2017年3月8日提交的美国临时申请第62/468707号的权益。其全部内容结合于此作为参考。
背景技术:
:众所周知,某些含碳氟的聚合物和含硅氧烷的聚合物可能能够为油漆和其它溶剂基涂层增加防污性能。以前,整个配方需要大量这种含碳氟和硅氧烷的聚合物以在所得涂层中获得所需的防污性能。然而,增加这种配方中含碳氟和/或含硅氧烷的聚合物的量会抑制涂层与下面的基材或表面的粘合强度。从而,破坏在涂层的暴露表面的抗污性能和涂层粘附到下面的基材上的能力之间的所得平衡。因此,需要提供防污涂层,特别是能实现所需的暴露表面防护性同时不破坏与下面基材的粘合强度的防污垢和防污涂层。粉末涂层体系可受益于这种防污性能,但与典型的油漆和涂层不同,它具有希望是无溶剂体系的额外的限制。此外,室内和室外表面上的微生物(包括真菌和细菌)生长是当今影响家庭、工作和娱乐环境的主要环境问题。这种微生物生长不仅在暴露的表面上难看,如果不进行处理,它会破坏下面的基材材料,对建筑物和其他结构和设备造成严重损害。在过去几年中,越来越明显的是,暴露于某些细菌和真菌(或其孢子)会严重影响人类、宠物和其他动物的健康。先前对建筑镶板赋予抗菌性能的尝试包括将抗微生物涂层施加到建筑材料的表面。然而,这种先前的抗微生物涂层需要相对大量的抗微生物添加剂以赋予涂层足够的抗微生物活性,从而使这种涂层昂贵并且可能干扰涂层的美学性能。另外,这种涂层需要使用某种类型的溶剂以湿态施加,从而排除了应用于有限数量的基材的可能性。因此,需要一种具有减少量的抗微生物添加剂能够表现出足够的抗微生物性能的涂层。还需要可以在不需要溶剂的情况下施用的这种抗微生物涂层。技术实现要素:本发明涉及一种产品,包括:基材;施加至基材上的聚合物粉末涂层,该聚合物粉末涂层具有与下表面相对的上表面;施加至聚合物粉末涂层的上表面的顶涂层,该顶涂层包括存在于聚合物粉末涂层的上表面的顶上的量为约0.01g/m2至约4g/m2的含氟防护剂组分。本发明的其他实施例包括一种形成防污产品的方法,方法包括:a)提供施加有粉末涂层的基材;b)将液基涂层组合物施加到粉末涂层,液基涂层组合物包括含氟表面活性剂和液体载体;c)干燥液基涂层组合物,从而驱除液体载体以形成防污产品。本发明的其他实施例包括一种产品,产品包括:基材;施加至基材上的粉末涂层,该粉末涂层具有与下表面相对的上表面以及包括第一含氟表面活性剂;施加至粉末涂层的上表面的不同于第一含氟表面活性剂的第二含氟表面活性剂。本发明的其他实施例包括形成防污产品的方法,包括a)共混合包括液体载体、阴离子含氟表面活性剂和聚合物粘合剂的混合物;b)随后干燥混合物以形成基本上不含液体载体的粉末涂层前体混合物;c)然后将粉末涂层前体混合物施加到基材上;d)随后固化粉末涂层前体混合物以形成防污产品,其中,在低于阴离子表面活性剂和聚合物粘合剂的熔融温度的温度下进行步骤a)的混合。本发明的其他实施例包括形成防污产品的方法,包括a)将包括液体载体、阴离子含氟表面活性剂和聚合物粘合剂的混合物共混第一时间段,然后停止共混该混合物第二时间段以完成共混循环;b)重复共混循环;c)干燥混合物以形成基本上不含液体载体的粉末涂层前体混合物,其中第一时间段与第二时间段的比率范围为从约1:1到约1:20。在其他实施例中,本发明包括抗微生物建筑镶板,包括基材、施加到基材上的粉末涂层,粉末涂层包括交联聚合物粘合剂以及包括金属硼酸盐与含硫苯并咪唑化合物的共混物,其中,金属硼酸盐和含硫苯并咪唑化合物的重量比为从约75:1至约10:1。本发明的其他实施例包括抗微生物建筑镶板,包括基材,施加到基材上的粉末涂层,粉末涂层包括交联聚合物粘合剂以及包括金属硼酸盐和含硫苯并咪唑化合物的共混物,其中,基于100重量份的粉末涂层,共混物的含量范围为从约5重量份至约15重量份。本发明的其他实施例包括形成抗微生物建筑镶板的方法,包括a)将粉末涂层前体施加到基材上;b)固化粉末涂层前体以在基材顶上形成交联粉末涂层,其中粉末涂层前体包括聚合物树脂、交联剂、金属硼酸盐和含硫苯并咪唑化合物,以及粉末组合物的固含量为约100%。本发明的其他实施例包括抗微生物涂层组合物,包括聚合物树脂;交联剂;以及金属硼酸盐与含硫苯并咪唑化合物的共混物,其中金属硼酸盐和含硫苯并咪唑化合物的重量比为约75:1至约10:1。本发明的其他实施例包括抗微生物涂层组合物,其包括聚合物树脂,交联剂;和金属硼酸盐和含硫苯并咪唑化合物的共混物,其中,基于100重量份的抗微生物涂层组合物,共混物的含量为约5重量份至约15重量份。在其他实施例中,本发明包括一种产品,包括基材;粉末涂层,粉末涂层具有与下表面相对的上表面,下表面面向基材;施加至粉末涂层的上表面的阳离子含氟表面活性剂;其中粉末涂层由包括聚合物粘合剂、交联剂、阴离子含氟表面活性剂和液体载体的前体形成。本发明的其他实施例包括防污产品,其包括含有粉末涂层和含氟防护剂组分的组合物,其中,粉末涂层由聚合物树脂、交联剂和不同于含氟防护剂组分的阴离子含氟表面活性剂形成。一种产品包括施加至基材的粉末涂层,粉末涂层由包括聚合物树脂、交联剂、液体载体和含氟表面活性剂的共混物的前体形成。根据下文提供的详细描述,本发明的其他应用领域将变得显而易见。应当理解,详细描述和具体实施例虽然表明了本发明的优选实施例,但仅用于说明目的,并不意图限制本发明的范围。附图说明通过详细说明和附图,将更全面地理解本发明,其中:图1是根据本发明的产品的立体图;图2是根据本发明的产品的沿着图1中所示的ii线的剖面图;图3是根据本发明的其他实施例的产品的沿着图1中所示的ii线的剖面图;图4是包括本发明的的产品镶板的建筑系统;以及图5是根据本发明的可选实施例的建筑系统的立体图;以及图6是根据本发明的天花板系统1的部分的侧视轮廓图。具体实施方式以下对优选实施例的描述本质上仅是示例性的,决不是要限制本发明,其应用或用途。如在全文中所使用的,范围用作描述该范围内的每个值的简写。可以选择范围内的任何值作为范围的端点。另外,本文引用的所有参考文献均通过引用整体并入本文。如果本公开中的定义与引用的参考文献中的定义发生冲突,则以本公开为准。除非另有说明,否则本文和说明书中其他地方表述的所有百分比和量应理解为指重量百分比。给出的量基于材料的有效重量。结合附图阅读根据本发明原理的说明性实施例的描述,附图被认为是整个书面描述的一部分。在本文公开的本发明实施例的描述中,对方向或取向的任何提及仅仅是为了便于描述,而不是以任何方式限制本发明的范围。相对的术语,如“向下”、“向上”、“水平”、“垂直”、“上方”、“下方”、“上”、“下”、“顶部”、“底部”及其派生词(例如,“水平地”、“向下地”、“向上地”等应当被解释为指代如所描述的或如所讨论的附图中所示的取向。这些相对的术语仅是为了便于描述,并不要求装置以特定方位构造或操作,除非明确指出。诸如“附接”、“附加”、“连接”、“耦合”、“互连”等术语是指其中结构通过中间结构直接或间接地彼此固定或附接的关系,以及两者除非另有明确说明,否则可移动或刚性附接或关系。此外,通过参考示例性实施例说明了本发明的特征和益处。因此,本发明明确地不应限于这样的示例性实施例,其说明可单独存在或以其他特征组合存在的特征的一些可能的非限制性组合;本发明的范围由所附权利要求限定。除非另有说明,否则本文和说明书中其他地方表述的所有百分比和量应理解为指重量百分比。给出的量基于材料的有效重量。根据本申请,术语“约”表示参考值的 /-5%。根据本申请,术语“基本上不含”是小于基于参考值的总和的约0.1重量%。本发明涉及一种产品,具有存在于三维物体上的一个或多个防污和/或抗微生物表面,该产品是通过将一个或多个涂层施加到三维基材的表面上而形成。形成本发明产品的基材,除了它是能够在高达约210℃的温度下保持其形状至少5分钟的三维物体外,不受任何限制。该产品的非限制性实施例包括建筑镶板、通风口、门、窗帘(例如百叶窗)以及汽车、火车或家庭的其他表面等。尽管不限于此,但本申请将该产品称为建筑镶板。当然,本申请的产品不限于作为三维物体的建筑镶板。参照图1,本发明的建筑镶板100可包括与第二主表面112相对的第一主表面111。建筑镶板100还可包括在第一主表面111和第二主表面112之间延伸的侧表面113,由此限定建筑面板100的周边。参照图4,本发明还可包括天花板系统1,天花板系统1包括安装在内部空间中的一个或多个建筑面板100,由此内部空间包括全体空间3和有效室环境2。全体空间3为建筑物内的机械管线9(例如,hvac、管道等)提供空间。有效空间2在建筑物的正常预期使用期间为建筑物居住者提供空间(例如,在办公楼中,有效空间将被包括计算机、灯等的办公室占用)。在安装状态下,建筑镶板100的第一主表面111面向有效室环境2,并且建筑镶板100的第二主表面112面向全体空间3。现在参照图1至图3,本发明的建筑镶板100可以具有从第一主表面111到第二主表面112测量的板厚度t0。板厚度t0可以在从约5mm至约50mm的范围(包括其间的所有值和子范围)。建筑镶板100可具有范围在从约30cm至约190cm的长度(包括其间的所有值和子范围)。建筑镶板100可以具有范围从约1cm到约121cm的宽度(包括其间的所有值和子范围)。现在参照图2和图3,建筑镶板100可包括基材120,基材120具有与下表面122相对的上表面121,和在上表面121和下表面122之间延伸的基材侧表面123,由此限定基材120的周边。基材120可以具有从基材120的上表面121到下表面122延伸的基材厚度t1。基材厚度t1可以在从约5mm至约50mm的范围内(包括其间所有值和子范围之间)。基材120可以是金属、塑料、陶瓷、复合材料或其组合。在一些实施例中,金属基材可以是铝面板或钢面板(包括镀锌钢)。根据一些实施例,金属基材可选自诸如铁、钢、铝、锡及其合金的材料。基材120可包括适合于建筑镶板应用的任何合适的尺寸。基材可包括适合于建筑镶板应用的任何合适的尺寸。建筑镶板100可以包括第一涂层130,第一涂层130具有与下表面132相对的上表面131,和在上表面131和下表面132之间延伸的第一涂层侧表面133,从而限定第一涂层130的周长。第一涂层130可以具有从第一涂层130的上表面131到下表面132延伸的第一涂层厚度t2。第一涂层厚度t2可以在约50μm到120μm的范围内(包括其间的所有值和子范围)。第一涂层130可以直接施加到基材120的上表面121。具体地言,第一涂层的下表面132可以接触并粘附至基材120的上表面121。在其他实施例中,在基材120和第一涂层130之间可以存在一个或多个中间涂层或层(未示出)。第一涂层130可以是粉末涂层,包括至少一种聚合物粘合剂和任选的一种或多种添加剂,如本文进一步讨论的“聚合物粉末涂层”。第一涂层130在本文中也可以被称为中间涂层。第一涂层130可以包括从第一涂层130的上表面131向下表面132延伸的表面缺陷135,例如凹陷、沟道、孔隙、裂纹、针孔等,从而在第一涂层130上形成空隙。具体地,表面缺陷135可以延伸到从第一涂层130的上表面131到下表面132测量的第一涂层厚度t2的约1%到99%的深度(包括其间的所有百分比和子范围)。建筑镶板100可包括第二涂层140,第二涂层140具有与下表面142相对的上表面141和在上表面141和下表面142之间延伸的第二涂层侧表面143,从而限定第二涂层140的周边。第二涂层140可以作为液基涂层施加,包括至少一种含氟表面活性剂和/或含氟聚合物和液体载体,如本文进一步讨论的。第二涂层140在本文中也可称为“顶涂层”。现在参照图2,第二涂层140可以直接施加到第一涂层130的上表面131,以形成连续的第二涂层140。具体地,第二涂层的下表面142可以接触并且粘附至第一涂层130的上表面131。第一涂层130可以形成第二涂层140和基材120之间的中间涂层。第二涂层140可包括填充部分145,填充部分145向下延伸并超出第二涂层140的下表面142,从而填充由第一涂层130的表面缺陷135产生的空隙,如本文进一步讨论的。第二涂层140可以是基本上连续的,从而在建筑镶板100上形成基本上连续的顶涂层。第一涂层130顶上的第二涂层140可以至少部分地密封存在于第一涂层130上的表面缺陷135以提供比第一涂层130的上表面131相对更加平滑的第一主表面111。根据该实施例,建筑镶板100的第一主表面111包括第二涂层140的上表面141(以及建筑镶板100的第二主表面112可包括基材120的下表面122)。现在参照图3,在可选实施例中,第二涂层140可以直接施加到第一涂层130的上表面131,以形成不连续的第二涂层140。具体地,第二涂层的下表面142可以接触并粘合到第一涂层130的上表面131,并且第一涂层130可以在第二涂层140和基材120之间形成部分中间涂层。术语“部分中间涂层”是指建筑镶板的第一主表面111,包括不连续的第二涂层140的上表面141以及第一涂层130的上表面131的由第二涂层140的不连续部分暴露的部分。建筑镶板100的第二主表面112可以包括基材120的下表面122。关于第一涂层130的组合物,第一涂层130可以由粉末涂层前体形成,粉末涂层前体包括粘合剂组合物和交联剂的高固体混合物(在本文中称为“前体”或“前体混合物”)。如本文所讨论的,前体混合物可在升高的温度下固化以形成完全固化的粉末涂层。根据本发明,术语“固化”和“交联”可互换使用。在一些实施例中,前体混合物具有100%的固含量并且基本上不含溶剂。粘合剂组合物可包括聚合物粘合剂,聚合物粘合剂是能够在固化期间与交联剂反应以形成完全固化的聚合物基质组合物的聚合物树脂。根据一些实施例,本发明的聚合物树脂具有特定的材料性质,包括玻璃化转变温度、分子量、官能度、熔体粘度以及成膜和流平特性。在没有适当考虑上述参考材料性质的情况下,选择不合需要的聚合物树脂可能导致不适合粉末涂层的组合物,因为所得前体混合物在加工过程中可能表现出保质期差和不充分的流动性,并且所得粉末涂层可能表现出使涂层不能操作的不充分的成膜特性。聚合物树脂应该包括至少一种聚合物组合物,其玻璃化转变温度(tg)大于室温,优选至少约20℃。聚合物树脂的tg可以为约45℃至约80℃。聚合物树脂应该包括至少一种聚合物组合物,其玻璃化转变温度(tg)大于室温,优选至少约50℃。聚合物树脂可具有约50℃的tg。聚合物树脂可具有约60℃的tg。聚合物树脂可具有约70℃的tg。聚合物树脂的加工温度可以为约90℃至约150℃。术语“加工温度”是指聚合物树脂的可以加热到不引发聚合物树脂和交联剂之间交联的温度。粘合剂组合物可包括可在固化过程中与交联剂反应的聚合物树脂,如本文所述,从而形成完全固化的基质组合物。本发明的聚合物树脂可具有特定的材料性质,包括玻璃化转变温度、分子量、官能度、熔体粘度以及成膜和流平特性。在没有适当考虑上述参考材料性质的情况下,选择不合需要的聚合物树脂可能导致组合物不适合粉末涂层,因为所得前体混合物在加工过程中可能表现出差的保质期和不充分的流动性,并且所得粉末涂层可能表现出使涂层不能操作的不充分的成膜特性。选择tg过低的聚合物树脂可能导致在混合物的储存和/或运输过程中不能抵抗烧结和附聚的前体混合物,从而降低前体混合物的保质期。相反,由于粉末涂层具有高固含量,选择tg过高的聚合物树脂可能导致没有表现出加工过程中的足够的流动性或没有表现出施加后的流平性的前体混合物,从而导致不均匀施加的粉末涂层组合物。聚合物树脂的tg可以通过选择许多参数来控制,包括但不限于分子量、聚合物主链的类型和结晶度,如本文所讨论的。通过熔体粘度测量聚合物树脂的流动性质。在高固含量(优选100%固体,不含溶剂)下,在加工过程中确保聚合物树脂的最大流量要考虑获得低熔体粘度。当在混合和固化期间加工聚合物树脂时(如本文所讨论的),聚合物树脂开始与固化剂(也称为交联剂)反应,固化剂存在于前体混合物中,随着前体混合物变成完全固化的粉末涂层从而产生前体混合物的粘度的显著增加。因此,使用具有低熔体粘度的聚合物树脂可有助于确保在前体混合物已经反应至接近完全固化的粉末涂层的交联程度之前,前体混合物有足够的时间混合并流过处理单元,如本文所讨论的。聚合物树脂的熔体粘度是许多因素的结果,包括:分子量、官能度和聚合物主链的类型,如本文所讨论的。本文将讨论聚合物树脂和总前体混合物的特定熔体粘度。聚合物树脂可包括至少一种聚合物组份,聚合物组份的重均分子量(mw)的范围为约1,500至15,000(包括其间的所有子范围和分子量)。聚合物树脂的重均分子量(mw)可以为约15,000至30,000(包括其间的所有子范围和分子量)。聚合物树脂的分子量可影响粉末涂层的柔韧性、冲击强度和可加工性(即熔体粘度)。与较低重均分子量(mw)的聚合物树脂相比,具有更高重均分子量(mw)的聚合物树脂可表现出更高的熔体粘度。聚合物树脂的重均分子量(mw)可以为约1,500至约15,000,具有约1的聚合度分布性(包括其间的所有子范围和分子量)。聚合度分布性是聚合物组合物的重均分子量(mw)与数均分子量(mn)的比率。具有约1的聚合度分布性可以确保所得粉末涂层的物理性质(即,柔韧性、冲击强度)最大化,而不牺牲在加工过程中前体混合物的所期望的低熔体粘度。当在高固含量(优选无溶剂)前体混合物下加工时,低熔体粘度是合适的,如根据本发明的一些实施例的粉末涂层所需要的。形成用于形成本发明粉末涂层的三维交联聚合物网络可能要求聚合物树脂包括具有平均至少两个可与交联剂上存在的官能团反应的官能团的聚合物。在一些实施例中,聚合物树脂可具有平均数量的官能团,平均范围为2至10个官能团。在一些实施例中,聚合物树脂可具有直链或支链的主链,并且官能团的位置将取决于聚合物树脂的主链的类型。在一些实施例中,聚合物树脂是具有位于聚合物末端的2~4个官能团的线性聚合物。聚合物树脂的官能团可选自羟基、羧酸基、异氰酸酯基、环氧基、丙烯酸基及其组合。在一些实施例中,聚合物粘合剂的官能团可以如本文所讨论的那样暂时封闭。根据本发明的一些实施例,聚合物树脂可包括具有主链的聚合物,所述主链具有选自酯基、氨基甲酸酯基、碳酸酯基、环氧基及其组合的部分。聚合物树脂和交联剂在固化过程中反应形成具有交联密度的聚合物基质。交联聚合物基质的交联密度可以通过交联聚合物基质的玻璃化转变温度来反映,玻璃化转变温度可以在约150℃至约300℃的范围内(包括其间的所有温度和子范围)。粘合剂组合物可包括选自聚酯树脂、聚氨酯树脂、环氧树脂和聚酯-氨基甲酸酯丙烯酸酯树脂的聚合物树脂。合适的聚酯树脂可以是羟基官能的(oh)或羧基官能的(cooh)。聚酯树脂可以是多元羧酸和多元醇的反应产物。出于本发明的目的,术语多元羧酸包括具有至少两个羧酸基团的化合物。出于本发明的目的,术语多元醇包括具有至少两个羟基的化合物。对于羟基官能聚酯,多元醇相对于多元羧酸以oh:cooh化学计量过量存在,其范围为2:1至6:1。过量的多元醇确保消耗所有游离羧酸基团,同时在酯化反应期间允许过量的羟基保持未消耗。羟基可以存在于聚酯的末端。对于羧基官能聚酯,多元羧酸相对于多元醇以cooh:oh化学计量过量存在,其范围为2:1至6:1。过量的多元羧酸确保消耗所有游离羟基,同时允许过量的羧酸基团在酯化反应过程中保持未消耗。羧酸基团可以存在于聚酯的末端。可通过催化剂促进羟基官能化合物和羧基官能化合物形成聚酯树脂的缩合反应。在一些非限制性实施例中,催化剂可选自n-甲基咪唑、二氮杂双环[2,2,2]辛烷、二氮杂双环[5,4,0]十一碳-7-烯和五甲基二亚乙基三胺及其混合物。合适的酯化催化剂的其他实施例包括4-钛酸四丁酯、辛酸亚锡、对甲苯磺酸及其组合。在非限制性实施例中,多元醇可以是二醇、三醇或具有4-8个羟基的更高官能度的多元醇(例如四醇)。在一些实施例中,多元醇可以是芳族、脂环族、脂族或其组合。在一些实施例中,羧基官能化合物是二羧酸、三羧酸、具有4-8个羧酸基团的更高官能度的多元羧酸或其组合。在一些实施例中,多元羧酸可以是脂族、脂环族、芳族或其组合。多元醇的非限制性实施例可包括选自亚烷基二醇的二醇;例如乙二醇、丙二醇、二甘醇、二丙二醇、三甘醇、三丙二醇、己二醇、聚乙二醇、聚丙二醇和新戊二醇乙二醇;氢化双酚a;环己二醇;丙二醇,包括1,2-丙二醇、1,3-丙二醇、丁基乙基丙二醇、2-甲基-1,3-丙二醇和2-乙基-2-丁基-1,3-丙二醇;丁二醇,包括1,4-丁二醇、1,3-丁二醇和2-乙基-1,4-丁二醇;戊二醇,包括三甲基戊二醇和2-甲基戊二醇;环己烷二甲醇;己二醇,包括1,6-己二醇;羟基烷基化双酚;聚醚二醇,例如,聚(氧四亚甲基)二醇。在一些实施例案中,多元醇可以是选自三羟甲基丙烷、季戊四醇、二季戊四醇、三羟甲基乙烷、三羟甲基丁烷、二羟甲基环己烷、甘油等的三醇或更高级的多元醇。多元羧酸的非限制性实施例可包括选自己二酸、壬二酸、癸二酸、琥珀酸、戊二酸、癸二酸、十二烷二酸、邻苯二甲酸、间苯二甲酸、5-叔丁二酸的二羧酸、丁基间苯二甲酸、四氢邻苯二甲酸、对苯二甲酸、六氢邻苯二甲酸、甲基六氢邻苯二甲酸、对苯二甲酸二甲酯、2,5-呋喃二甲酸、2,3-呋喃二甲酸、2,4-呋喃二甲酸、3,4-呋喃二甲酸、2,3,5-呋喃三甲酸、2,3,4,5-呋喃四羧酸、环己烷二羧酸、1,3-环己烷二羧酸、1,4-环己烷二羧酸及其酸酐以及它们的混合物。在一些实施例中,多元羧酸可选自三羧酸,例如,偏苯三酸及其酸酐。用于粉末涂层组合物的聚氨酯树脂的非限制性实施例公开于例如美国专利第4,404,320号和美国专利第4,246,380号中。合适的聚酯-氨基甲酸酯丙烯酸酯公开在例如美国专利第6,284,321号中。用于粉末涂层组合物的合适的环氧化合物公开于例如美国专利第5,732,052号中。用于产生聚酯树脂的反应物的具体类型和量可以影响聚合物树脂的熔体粘度、结晶度和tg。具体地,芳族和/或脂环族单体产生高tg聚合物,而长链脂族单体产生较低tg聚合物。例如,通过用己二酸代替一定量的对苯二甲酸/间苯二甲酸可以降低在主链中具有大量由对苯二甲酸/间苯二甲酸通过己二酸衍生的酯基的聚酯树脂的tg,从而使聚酯树脂更柔韧以及更能在较低温度下流动。然而,取代过多的己二酸会导致聚酯的tg太低而不能用于粉末涂层配方中。在非限制性实施例中,聚合物树脂可具有100%固含量(即不含溶剂)并且在200℃下具有2,000mpa/s至5,000mpa/s的熔体粘度(包括其间所有子范围和整数)。在非限制性实施例中,聚合物树脂可具有约50℃至约70℃的tg。在一些实施例中,聚合物树脂可以是羟基官能的并且具有约40至约300的羟值。合适的羟基官能聚合物树脂的非限制性实施例包括羟基官能聚酯树脂,例如可商购的polymac3110和/或rucote102。在一些实施例中,聚合物树脂可以是羧基官能的并且具有30至50的酸值。根据本发明的一些实施例,交联剂包括至少一种具有至少两个官能团的低分子量化合物。交联剂可包括2至6个官能团。在一个可选实施例中,交联剂可包括2至4个官能团。交联剂的官能团可选自羟基、羧酸基、异氰酸酯基、环氧基及其组合。在一些非限制性实施例中,合适的交联剂可包括前述多元醇化合物、多元羧酸化合物、以及多异氰酸酯化合物和环氧官能化合物,例如,缩水甘油基官能丙烯酸共聚物。在一些实施例中,如本文所讨论的,交联剂的官能团可以暂时封闭,从而在储存和运输期间提高前体混合物的保质期。具体的官能团取决于所得粉末涂层的所需组成。交联剂的具体选择取决于聚合物树脂的类型和所需的最终基质组合物。例如,羟基官能聚酯可以用多元羧酸交联剂固化,从而得到三维聚酯基质,具有聚酯树脂与交联剂的oh:cooh化学计量比为约1:1,以确保聚合物树脂和交联剂上的所有官能团在酯化交联反应过程中都被消耗。可选的,羟基官能聚酯可以用多异氰酸酯交联剂固化,从而得到聚酯-聚氨酯基质。聚酯树脂与多异氰酸酯交联剂的oh:nco比率基本上为1:1,以确保在聚氨酯形成的交联反应过程中聚合物树脂和交联剂上的所有官能团都被消耗。出于本发明的目的,术语多异氰酸酯是指具有至少两个异氰酸酯官能团的异氰酸酯官能化合物,例如二异氰酸酯、异氰脲酸酯、缩二脲、异氰脲酸酯脲基甲酸酯。在优选的实施例中,聚合物树脂是聚酯-聚氨酯树脂。本发明的多异氰酸酯可选自诸如异佛尔酮二异氰酸酯(ipdi)、4,4'-二环己基甲烷二异氰酸酯和三甲基六亚甲基二异氰酸酯,1,6-六亚甲基二异氰酸酯、2,2,4-三甲基六亚甲基二异氰酸酯、十八烷基二异氰酸酯1,4-亚环己基二异氰酸酯,甲苯二异氰酸酯;亚甲基二苯基二异氰酸酯;四甲基二甲苯二异氰酸酯以及它们的异氰脲酸酯、缩二脲、脲基甲酸酯以及它们的混合物,以及它们的加合物,异氰脲酸酯、缩二脲和它们的脲基甲酸酯等的化合物。在一个实施例中,多异氰酸酯包括ipdi。根据本发明的一些实施例,存在于交联剂上的每个游离异氰酸酯基团可以用封端剂暂时封闭,以确保在最终固化之前不发生羟基和异氰酸酯基团的过早反应从而延长了前体混合物在储存和运输过程中的保质期。合适的封端剂可包括,例如,仲醇或叔醇,如异丙醇或叔丁醇;ch酸性化合物,如丙二酸二烷基酯、乙酰丙酮和乙酰乙酸烷基酯;肟,如甲醛肟、乙醛肟、甲基乙基酮肟、环己酮肟、苯乙酮肟、二苯甲酮肟或二乙基乙二肟;内酰胺,如ε-己内酰胺、δ-戊内酰胺、γ-丁内酰胺;苯酚、邻甲基苯酚等酚类;n-烷基酰胺,如n-甲基乙酰胺、酰亚胺如邻苯二甲酰亚胺、仲胺如二异丙胺;咪唑;吡唑和1,2,4-三唑。在优选的实施例中,交联剂是ε-己内酰胺封端的ipdi。可以相对于游离异氰酸酯基团以约1:1的化学计量比使用封端剂,以确保交联剂上存在的所有游离异氰酸酯基团被暂时封闭。封端剂防止异氰酸酯基团在室温下与水分或交联剂过早反应,但将在不高于170℃的高温下从异氰酸酯基团去封闭,从而使游离异氰酸酯基团与交联剂反应并形成完全固化的基质。在其他实施例中,封端的多异氰酸酯可以是脲二酮改性的多异氰酸酯的形式。脲二酮改性的多异氰酸酯含有两个游离的异氰酸酯基团以及两个内部封端的异氰酸酯基团。异氰酸酯基团的内部封闭发生而不需要外部封端剂,例如ε-己内酰胺。在高温下,在氨基甲酸酯形成反应中,脲二酮环被破坏并且两个内部封闭的异氰酸酯基团可以和异氰酸酯反应性基团(如羟基反应)反应。根据本发明,脲二酮封端的多异氰酸酯可以由例如ipdi的上述多异氰酸酯化合物形成。去封闭后,基于二异氰酸酯的脲二酮将含有四个异氰酸酯基团的等价物。在一些实施例中,可以加入催化剂以帮助羟基和异氰酸酯基团之间的形成氨基甲酸酯的反应。催化剂可选自有机金属催化剂,如二月桂酸二丁基锡或辛酸锡,或如三乙胺的叔胺、吡啶、n,n-二甲基氨基环己烷或1,4-二氮杂双环[2.2.2]辛烷。其他催化剂可选自金属离子二丙烯酸钠盐。催化剂的含量范围可以为基于前体混合物的总重量的约0.001wt%至约1wt%。该范围包括其间的所有特定值和子范围,例如于前体混合物的总重量的0.002wt%、0.005wt%、0.01wt%、0.02wt%、0.05wt%、0.1wt%、0.2wt%、0.5wt%和0.8wt%。聚合物树脂可以是异氰酸酯封端的氨基甲酸酯-聚酯预聚物。预聚物可以是相对于羟基封端的聚酯树脂化学计量过量的多异氰酸酯的反应产物,nco:oh比率为2:1至6:1。过量的异氰酸酯确保在形成聚氨酯预聚物期间消耗所有游离羟基,同时确保游离异氰酸酯基团保留在预聚物上。在形成预聚物后剩余的任何过量多异氰酸酯可以通过低压真空去除。存在于预聚物上的游离异氰酸酯基团可以用先前讨论的异氰酸酯封端剂以与游离异氰酸酯的化学计量比为约1:1的封端剂封闭,以确保预聚物上存在的所有游离异氰酸酯基团被暂时封闭。然后可以将封闭的异氰酸酯封端的聚酯预聚物与多元醇交联剂混合以形成储存稳定的前体混合物。多元醇交联剂包括列出的与聚酯树脂的形成相关的相同的低分子量多元醇化合物。在一些实施例中,羧基官能聚酯树脂可以用多元醇交联剂固化,从而得到聚酯基质。存在于羧基官能聚酯树脂上的游离羧基可以相对于存在于交联剂上的羟基以cooh:oh化学计量比约1:1存在,从而确保聚酯树脂和交联剂上存在的所有官能团在酯化交联反应过程中被消耗。多元醇交联剂包括列出的与聚酯树脂的形成相关的相同的低分子量多元醇化合物。羧基官能聚酯树脂也可以用环氧官能化合物固化。在一些非限制性实施例中,环氧官能化合物可包括饱和的或不饱和的、脂肪族的、脂环族的、芳族的或杂环的环氧树脂。适用于本发明的环氧树脂的实施例包括多羟基化合物的多缩水甘油醚、溴化环氧化物、环氧酚醛清漆或类似的多羟基酚树脂、二醇或聚乙二醇的聚缩水甘油醚和多元羧酸的多缩水甘油酯。优选地,环氧树脂是多元酚的聚缩水甘油醚。多元酚的多缩水甘油醚可以例如通过在碱存在下使表卤代醇与多元酚反应来制备。合适的多元酚的实施例包括:2,2-双(4-羟基苯基)丙烷(双酚-a;2,2-双(4-羟基-叔丁基苯基)丙烷;1,1-双(4-羟基苯基)乙烷;1,1-双(4-羟基苯基)异丁烷;2,2-双(4-羟基叔丁基苯基)丙烷;双(2-羟基萘基)甲烷;1,5-二羟基萘;1,1-双(4-羟基-3)-烷基苯基)乙烷等。粘合剂组合物可以基本上不含挥发性溶剂,不包括水分含量。出于本发明的目的,术语“基本上不含”是指基于引用元素的总重量的小于0.1wt%。在一个非限制性实施例中,包括粘合剂、交联剂和基本上不含溶剂的填料的混合物包括少于基于混合物总重量的0.05wt%的溶剂,优选小于0.01wt%。根据优选的实施例,本发明的粘合剂组合物具有100%固体是不含溶剂(该溶剂包括挥发性有机溶剂)。此外,根据本发明的另外的实施例,粘合剂组合物基本上不含包括氟碳基团的聚合物树脂,例如氟改性的聚氨酯和含氟聚合物,例如pvdf或ptfe。换句话说,构成本发明的粘合剂组合物的聚合物树脂基本上不含氟碳基团。粉末涂层可进一步包括添加剂、填料、涂层性能增强剂。这些填料和添加剂可包括但不限于,惰性填料、抗氧化剂、稳定剂、颜料、增强剂、增强聚合物、润滑剂、抗微生物添加剂(例如杀真菌剂)、脱气剂、表面活性剂、流动添加剂、分散剂、触变剂、粘合促进剂、光稳定剂、阻燃剂、抗腐蚀剂、抑制剂、流平剂、抗缩孔剂以及它们的混合物。在一些实施例中,杀真菌剂的含量可以为基于粉末涂层组合物的总重量的约6wt%至约10wt%。在非限制性实施例中,杀真菌剂可包括硼酸锌、2-(-4-噻唑基)苯并咪唑。根据本发明,包括抗微生物添加剂的粉末涂层可称为抗微生物涂层或抗微生物粉末涂层。术语“抗微生物的”是指对真菌(例如霉菌、霉菌)和/或细菌生长具有抗性的涂层。本发明的抗微生物涂层可以是具有或任选地没有抗污表面活性剂的粉末涂层。抗微生物涂层可以直接施加到基材的一个表面上。具体地,抗微生物涂层可以接触并粘合至基材的暴露表面。在其他实施例中,在基材表面和抗微生物涂层之间可以存在一个或多个中间涂层或层。抗微生物涂层可以以约40μm至约120μm的涂层厚度存在于基材的一个或多个表面上(包括其间的所有厚度和子范围)。抗微生物涂层可以以约130g/m2至约340g/m2的涂层厚度存在于基材的一个或多个表面上(包括其间的所有厚度和子范围)。抗微生物涂层可包括分散在整个交联聚合物中的抗微生物添加剂。抗微生物涂层可进一步包括一种或多种颜料。抗微生物涂层可进一步包括一种或多种其他添加剂和/或填料。交联聚合物可以由粉末涂层前体(也称为“前体”)形成。前体可包括聚合物树脂和交联剂的高固体混合物,如本文进一步讨论的。交联聚合物形成有抗微生物添加剂、颜料、填料和/或其它添加剂分散在其中的三维聚合物基质,如本文进一步讨论的。本发明的抗微生物添加剂包括第一组分和第二组分的共混物。第一组分通常包括金属硼酸盐,第二组分包括苯并咪唑化合物。根据本发明,第一组分的金属硼酸盐是指对应于一元、二元、三元和多元碱式金属硼酸盐的化合物,以及它们的混合物。例如,“硼酸锌”是指由硼酸锌(znb4o7),任何相应的碱式硼酸锌(如结构zn(oh).b4o7的一元碱式硼酸锌、结构2zn(oh)2.b4o7的二元碱式硼酸锌、结构3zn(oh)3.b4o7的三元碱式硼酸锌等)以及它们的混合物组成的一组化合物。作为另一个实施例,“硼酸铜”是指选自由硼酸铜(cub4o7),其任何相应的碱式硼酸铜(如结构为cu(oh).b4o7的一元碱式硼酸铜、结构为2cu(oh)2.b4o7的二元碱式硼酸铜、结构为3cu(oh)3.b4o7的三元碱式硼酸铜等)及它们的混合物组成的组的一组化合物。金属硼酸盐可包括一种或多种金属。在优选的实施例中,金属硼酸盐是硼酸锌。第二组分的苯并咪唑化合物是指具有式i结构的化合物:其中,r1、r3、r4、r5和r6可以选自h、卤素原子(例如br、i、cl)和c1-c6链。r2可以选自含硫杂环化合物,例如噻唑基。苯并咪唑化合物可具有为4-噻唑基的r2基团。苯并咪唑化合物可具有作为氢原子的r1、r3、r4、r5和r6基团。在优选的实施例中,苯并咪唑化合物是具有式ii结构的2-(4-噻唑基)苯并咪唑:在一些实施例中,本发明的苯并咪唑化合物可以基本上不含羰基。第一组分和第二组分可以存在于抗微生物添加剂中,第一组分(金属硼酸盐)和第二组分(苯并咪唑化合物)之间的重量比为约75:1至约10:1(包括其间的所有比率和子范围)。在一些实施例中,第一组分和第二组分的重量比可以为约70:1至约30:1(包括其间的所有比率和子范围)。在一个优选的实施例中,第一组分和第二组分的重量比可以为约70:1至约40:1包括其间的所有比率和子范围。第一组分和第二组分的重量比可以为约70:1。本发明的抗微生物添加剂可以基本上不含包括氨基甲酸酯基团的化合物。在一些实施例中,本发明的抗微生物添加剂可以基本上不含包括卤素原子的化合物。令人惊讶地发现,金属硼酸盐,特别是硼酸锌,与含硫苯并咪唑化合物的组合提供了对所得涂层的抗微生物活性的协同改进。具体地,金属硼酸盐和含硫苯并咪唑的组合在整个涂层中以减少量的抗微生物添加剂为所得涂层提供了足够的抗微生物性能。具体地,抗微生物添加剂可以基于抗微生物涂层的总重量以高达约10wt%的量存在于整个抗微生物涂层中。在一个优选的实施例中,在于整个抗微生物涂层中,抗微生物添加剂的含量可以为基于抗微生物涂层的总重量的从约6wt%至约10wt%(包括其间的所有量和子范围)。在整个涂层中需要较少的抗微生物添加剂,可以以较低的成本制造所得的抗微生物涂层。抗微生物添加剂的含量也可以以重量份表示,由此基于100重量份的总抗微生物涂层组合物,抗微生物添加剂的含量范围为从约6至约10重量份(包括所有重量份数和其间的子范围)。前体组合物可进一步包括增强聚合物,例如进一步包括能够与粘合剂中存在的官能团反应的官能团的丙烯酸共聚物。在非限制性实施例中,增强聚合物可包括缩水甘油基官能的丙烯酸类聚合物。如前所述,缩水甘油基能够与羧酸基团反应。另外的添加剂包括金属和金属氧化物,例如氧化铬、铬、氧化锌、氧化铜、铜、镍、钛、不锈钢、铝、二氧化钛、氧化锡、铁、氧化铁等。例如这些金属可以用作耐磨填料、增容剂或颜料。颜料可进一步包括化合物,例如二氧化钛、硫酸钡、碳酸钙或其组合。在本发明的一些实施例中,颜料的平均粒度可以为180nm至220nm;在优选的实施例中,颜料的平均粒度为约200nm。在一些实施例中,根据本发明,粉末涂层可包括约15wt%至约30wt%的颜料。根据一些实施例,根据本发明,粉末涂层可包括约20wt%的二氧化钛。在本发明的一些实施例中,颜料可具有约0.2微米(μm)至约5μm的平均粒度(包括其间的所有尺寸和子范围)。抗微生物涂层可包括基于抗微生物涂层的总重量的约20wt%至约50wt%的颜料(包括其间的所有量和子范围)。在一些实施例中,在与前体和/或其他添加剂和填料共混之前,可以用抗微生物添加剂预处理颜料。金属硼酸盐和含硫苯并咪唑化合物之间出乎意料的协同作用的另一个好处是抗微生物组合物和前体(以及其它添加剂和填料)可以以约100%的固含量(即,基本上不含溶剂)施加到基材上。不需要溶剂来施加抗微生物涂层,抗微生物涂层可适合作为粉末涂层。本发明的粉末涂层可包括表面活性剂。如本文所讨论的,根据本发明,表面活性剂可以在最终加工和固化之前加入至表面活性剂组合物中的前体混合物中。含氟表面活性剂可以是非离子的或离子的。离子含氟表面活性剂的非限制性实施例包括阳离子含氟表面活性剂和阴离子含氟表面活性剂。在优选的实施例中,粉末涂层料的含氟表面活性剂可以是阴离子的。根据本发明的表面活性剂组合物基本上不含溶剂或液体载体,优选具有100%的固含量并且基本上不含溶剂或液体载体(包括挥发性有机溶剂和/或水)。表面活性剂组合物在室温下呈粉末形式。表面活性剂组合物包括至少一种含氟表面活性剂。在其他实施例中,根据本发明的表面活性剂组合物可以是包括与液体载体混合的阴离子含氟表面活性剂的液基的表面活性剂,如本文更详细讨论的。阴离子含氟表面活性剂可具有约50℃至约70℃的熔融温度。本发明的阴离子含氟表面活性剂具有从约1至约6的低ph值(包括其间的所有值和子范围)。阴离子含氟表面活性剂的阴离子部分可选自硫酸根、磺酸根、磷酸根或羧酸根部分,其中优选的是磷酸根部分。阴离子含氟表面活性剂的非限制性实施例包括下式中的至少一种:式i:(rf1ao)p(o)(o-m )2式ii:(rf1ao)2p(o)(o-m )其中,rf1是可任选地被一个、两个或三个醚氧原子间隔的c1至c16直链或支链全氟烷基。a选自:(ch2cf2)m(ch2)n、(ch2)oso2n(ch3)(ch2)p、o(cf2)q(ch2)r或ochfcf2oe;m是0~4;n、o、p和r的每个均是2至20;q是2e是是可选地被氧、硫或氮原子间隔的c2至c20直链或支链烷基;环状烷基或c6至c10芳基;m是i族金属或铵阳离子(nhx(r2)y) ,r2是c1至c4烷基;x是1至4;y是0至3;以及x y是4。在优选实施例中,含氟表面活性剂可以由下式的阴离子含氟表面活性剂组成:式iii:(rf2ch2ch2o)p(o)(onh4)2其中,rf2是c4至c8的全氟烷基,具有下式:f[cf2-cf2]3-8。在优选的实施例中,含氟表面活性剂是无溶剂的阴离子含氟表面活性剂。合适的阴离子含氟表面活性剂可商购获得。根据一些实施例,含氟表面活性剂的含量可以为基于粉末涂层的总重量的约0.05wt%至约4wt%。在优选的实施例中,含氟表面活性剂的含量可以为基于粉末涂层的总重量的约0.7wt%至3wt%。在一些实施例中,含氟表面活性剂的含量可以为基于粉末涂层的总重量的从约1.5wt%至3wt%,或者,从约0.1wt%至0.3wt%。根据一些实施例,含氟表面活性剂的含量可以为基于颜料的总重量的约10wt%至25wt%(包括其间的所有子范围和整数)。在加入至前体混合物之前,可以用表面活性剂组合物预处理颜料,例如二氧化钛。在优选的实施例中,根据以下步骤用阴离子含氟表面活性剂预处理颜料:可将本发明的阴离子含氟表面活性剂组合物加热至在50℃至70℃的范围内(包括其间的所有整数和子范围)的高温以熔化阴离子含氟表面活性剂,接着加入氧化钛。然后将阴离子含氟表面活性剂和颜料混合,从而产生预处理的二氧化钛颜料。在一些实施例中,高温可以是55℃。可将预处理的颜料冷却至室温,然后与粘合剂和交联剂混合以形成前体混合物,如本文所述。在优选的实施例中,颜料是用式iii的阴离子含氟表面活性剂预处理的二氧化钛。已经发现,在涂层组合物的其它成分加入以制备涂层组合物混合物之前,用含氟表面活性剂预处理颜料可确保含氟表面活性剂在涂层组合物中的均匀分散。可以通过首先将粘合剂、交联剂和添加剂(在抗微生物涂层的情况下包括抗微生物添加剂)和填料混合在一起以形成前体混合物来形成第一涂层130。前体混合物可以在室温下通过干燥混合器轻微混合一段时间,从而在前体混合物中产生均匀分布的粘合剂、交联剂和添加剂/填料。在干燥混合之后,可以根据本文的讨论将前体混合物熔融混合并造粒。然后可以在熔融挤出机中处理前体混合物。熔体挤出机可以是单螺杆或双螺杆挤出机。熔体挤出机可包括三个区域:(1)进料区;(2)熔化区;(3)分散区。进料区可以保持在小于或等于室温的温度下,以防止前体混合物的堵塞。通常将熔融区加热至高于前体混合物的最大tg但低于前体混合物的去封闭和反应温度。在高于tg和低于去封闭/反应温度之间操作允许前体混合物熔化并流动,同时前体混合物不会过早地去封闭并在挤出机内部反应。在分散区中,温度保持在tg以上并且低于去封闭温度,从而使前体混合物变得均匀。在一些实施例中,熔融区和分散区在从约90℃至150℃的范围的温度下操作(包括其间的所有子范围和整数)。在一些实施例中,熔融区和分散区在约90℃至约130℃的范围的温度下操作(包括其间的所有子范围和整数)。在一些实施例中,熔融区和分散区在100℃至110℃的范围的温度下操作。挤出机将包括加热装置和冷却装置以确保各个区域保持在适当的温度范围内。在通过分散区之后,熔融混合的前体混合物通过挤出机出口模具(exitdie)。出口模具可以设置有许多不同构造的多个孔。在一些实施例中,出口模具可以由允许跨越它们的压降的其他装置代替;例如,使用特定的螺杆配置可以实现这种压降。在任何情况下,前体混合物在熔体挤出机中的平均停留时间通常小于5分钟,以及通常在30至120秒的范围内。当熔融前体混合物通过模具时,将其冷却并造粒。研磨粒料,然后收集所得的前体粉末。在一些非限制性实施例中,前体混合物可以通过机器研磨,例如研磨机、低温研磨机等来研磨。所得前体粉末的平均粒度可小于100μm,通常为30μm至50μm。根据本发明的可选实施例,第一涂层130可以根据可选工艺生产。可选工艺包括液基表面活性剂。以前,液基表面活性剂不用于制造粉末涂层。液基表面活性剂可包括与至少一种前述含氟表面活性剂预混合的液体载体。在优选的实施例中,液基表面活性剂可包括与至少一种前述阴离子含氟表面活性剂预混合的液体载体。液体载体的非限制性实施例包括水以及在120℃以下不易燃和/或在120℃以下不释放有毒蒸气的其他液体。液基表面活性剂可包括基于液体载体和干燥状态的表面活性剂的总重量约10wt%至约75wt%的液体载体(包括其间的所有量和子范围)。在一个优选的实施例中,液基表面活性剂可以包括基于液体载体和干燥状态的表面活性剂的总重量的为约30wt%至约75wt%的液体载体(包括其间的所有量和子范围)。可以将液基表面活性剂与粘合剂、交联剂和添加剂和/或填料共混在一起以形成湿前体混合物。液基表面活性剂在湿前体混合物中的含量可以为以基于湿前体混合物的总重量的约0.05wt%至约4wt%(包括其间的所有量和子范围)。可选的,为了确保湿前体混合物中每种组分的适当分布,可以将液基表面活性剂的共混物与粘合剂、交联剂和添加剂和/或填料共混在一起若干个共混循环,共混循环包括混合周期和冷却周期。在非限制性实施例中,共混循环的每个混合周期可以跨越范围从约5秒到约30秒的第一时间段(包括其间的所有时间和子范围)。在非限制性实施例中,共混循环的每个冷却周期可以跨越范围从约5秒到约120秒的第二时间段(包括其间的所有时间和子范围)。单个共混循环的第一时间段和第二时间段之间的比率可以在约1:1至约1:20的范围内(包括其间的所有比率和子范围)。在优选实施例中,第二时间段大于每个共混循环的第一时间段。在优选的实施例中,共混循环可小于约10秒,以避免过多的热量积聚。共混循环的总数可以在约1至约20的范围内(包括所有共混循环数和其间的子范围)。选择每个共混循环的长度和共混循环的总数,使得湿前体混合物完全混合而没有任何结块或湿前体混合物的任何部分没有由于热量积聚而熔化。合适的搅拌器的非限制性实施例包括具有高导热性的侧刮板的搅拌器。在一些实施例中,搅拌器可以是冷却的搅拌器,其有助于在共混期间调节湿前体混合物的温度。可以操作共混循环和/或共混设备,使得湿前体在共混期间不会超过120°f的温度。在其他实施例中,可以操作共混循环和/或共混设备,使得湿前体在共混期间不会超过80°f的温度。在共混期间,液体载体可能被前体混合物的一种或多种组分(例如,颜料)吸收,因此湿前体混合物仍将包括液体载体,这是因为液体载体在共混过程中可能不会蒸发掉。通过将前体混合物在湿态和低于前体混合物中任何组分的熔融温度下共混,蜡质阴离子表面活性剂更好地分布在整个前体混合物中,从而提供最终涂层中的更均匀的抗污性能,即使在相对低量的阴离子表面活性剂下也是如此。一旦共混,湿前体可以根据前面讨论的方法干燥和造粒。在挤出过程中,液体载体可以蒸发掉,得到具有基本100%的固含量的前体。在非限制性实施例中,湿前体可以在高于100℃,优选在105℃和110℃之间,的温度下挤出,以确保液体载体从湿前体混合物中蒸发。然后可以将预定量的前体粉末放入容器中,该容器被放入存储器或运送到另一个位置进行最终处理,如本文所讨论的。在其他实施例中,前体粉末可最终在与熔融混合相同的位置处理。最终处理包括将前体粉末喷涂或静电涂覆到基材120上。可以通过喷枪在静电场中或用摩擦电枪来实施喷涂,其中在摩擦电枪中粉末通过摩擦带电。在将前体粉末喷涂到基材120上之后,通过在烘箱中在高于前体混合物的去封闭和反应温度的固化温度下加热来固化所得的喷涂层。固化温度可以在约160℃至210℃的范围。固化可以进行足以粘合剂和交联剂完全反应的一段时间,从而形成作为第一涂层130的完全固化的粉末涂层。对于从约160℃到190℃的温度范围,固化可以进行15至30分钟的时间段。在其他实施例中,对于约190℃至210℃的温度范围,固化可以进行约6至15分钟的时间段。得到的粉末涂层的厚度范围为40μm至120μm(包括其间的所有子范围和厚度)。涂覆有抗微生物涂层的所得基材适合作为抗微生物产品,例如用于安装在室内环境中的建筑镶板,由此建筑镶板不仅表现出优异的抗细菌、霉菌和真菌生长的能力,并且善于减少预先存在的活微生物的量。在提供涂覆有第一涂层130的基材120(施加有第一涂层130)之后,可以用第二涂层140涂覆第一涂层130的上表面。可以通过涂覆液基涂层组合物至第一涂层130的上表面131,然后干燥液基涂层组合物以在第一涂层130顶上形成第二涂层140来形成第二涂层140。液基涂层组合物可以通过将液体载体与防护组分混合在一起来制备。防护组分可以是含氟防护组分。含氟防护组分可选自含氟聚合物、上述含氟表面活性剂或其组合。在优选的实施例中,含氟防护组分是离子含氟表面活性剂。液体载体可选自水、voc溶剂及其组合。在优选的实施例中,液体载体是水。含氟聚合物可选自氟化丙烯酸共聚物、氟化丙烯酸烷基氨基共聚物及其组合。含氟聚合物的分子量可以为约1,000mn至约10,000,000mn(包括其间的所有重量和子范围)。氟化丙烯酸聚合物的非限制性实施例包括通过聚合含有氟原子的丙烯酸酯官能单体和可选的至少一种不含氟原子的其他丙烯酸酯官能单体而制备的聚合物。含有氟原子的丙烯酸酯官能单体(也称为“氟代丙烯酸酯”)的非限制性实施例包括偏二氟乙烯、氟乙烯、三氟氯乙烯、六氟丙烯、四氟乙烯、全氟甲基乙烯基醚、三氟乙烯及其混合物。不含氟原子的丙烯酸酯官能单体的非限制性实施例包括丙烯酸、甲基丙烯酸以及丙烯酸酯和/或甲基丙烯酸酯。本发明的含氟聚合物可以是离子的。本发明的含氟聚合物可具有从约3至约6的范围的酸性ph(包括其间的所有ph和子范围)。本发明的含氟聚合物可具有从约9至约11的范围的碱性ph(包括其间的所有ph和子范围)。在一些实施例中,含氟聚合物可以是阴离子的并且具有从约9至约11的ph(包括其间的所有ph和子范围)。在一些实施例中,含氟聚合物可以是阳离子的并且具有从约3至约6的ph(包括其间的所有ph和子范围)。如本文进一步讨论的,令人惊讶地发现,非离子含氟聚合物不提供如本文的离子含氟聚合物所提供的防污和防油性。在一个非限制性实施例中,阳离子含氟聚合物可以通过使氟代丙烯酸酯与能够形成盐的单体共聚来制备,由此由单体形成的共价键合基团具有正电荷,例如,诸如n-二甲基氨基乙基甲基丙烯酸,其中氨基与硫酸二乙酯反应形成从含氟聚合物垂饰的阳离子基团。在一个非限制性实施例中,阳离子含氟聚合物可以通过使氟代丙烯酸酯与能够形成盐的单体共聚来制备,由此由该单体形成的共价键合基团具有负电荷,例如,甲基丙烯酸酸,其中羧酸基团与氨反应形成从含氟聚合物垂饰的阴离子基团。液体载体的含量可以为基于液基涂层组合物的总重量的从约80wt%至约99.98wt%(包括其间的所有百分比和子范围)。含氟聚合物的含量可以为基于液基涂层组合物的总重量的约0.02wt%至约20wt%(包括其间的所有百分比和子范围)。可以通过喷涂、辊涂、浸涂或擦拭将液基涂层组合物施加到第一涂层130的上表面131。液基涂层组合物可以以从约80g/m2至约200g/m2的范围的量施加至第一涂层130的上表面131(包括其间的所有子范围和量)。在优选的实施例中,液基涂层组合物可以以从约105g/m2至约122g/m2的量施加至第一涂层130的上表面131(包括其间的所有子范围和量)。在涂覆之后,液基涂层组合物覆盖第一涂层130的上表面131以及渗透并至少部分地填充由第一涂层130上的表面缺陷135产生的空隙。施用后,将液基涂层组合物在温度范围为从约15℃至约40℃下干燥约5分钟至约60分钟的时间段,从而驱除液体载体以及将液基涂层组合物转化为第二涂层140。根据本发明,术语“干燥”或“干燥的”是指从所提及的组合物驱动液体载体。术语“干燥”或“干燥的”不是指使组合物与第二组合物发生化学反应,例如,用交联剂化学固化聚合物粘合剂树脂。因此,包括含氟聚合物的第二涂层140可以施加到第一涂层130,而不需要额外的高温固化(例如在第一涂层130的固化阶段中所使用的)。在干燥之后,所得第二涂层140可基本上不含所有液体载体。得到的建筑镶板100包括施加到第一涂层130的上表面131的含量范围为从约0.02g/m2至约2g/m2的干燥状态下的含氟聚合物(包括其间所有子范围和量),其中含氟聚合物形成建筑镶板100的面漆。在干燥建筑镶板100之后,含氟聚合物不仅保持施加到第一涂层130的上表面131,而且还保持在第一涂层130的表面缺陷135内。具体地,第二涂层140包括填充部分145,填充部分145导致第二涂层140的含氟聚合物的至少一部分存在于第一涂层130的表面缺陷135内,使得第二涂层140的含氟聚合物的至少一部分位于第一涂层130的上表面131和下表面132之间。将包括含氟聚合物的第二涂层140施加到第一涂层130赋予了对耐污渍性(例如,指纹油和汗液)的附加抗性,这导致建筑镶板100能够承受化妆品损坏,否则化妆品损坏通常会在安装过程中发生。可以测量增加的对耐污渍性的附加抗性作为颜色值变化的函数,即,即“变量增量e”(δe)。变量增量e通过以下计算测量:δe=[(l2-l1)2 (a2-a1)2 (b2-b1)2]1/2其中l1、a1和b1各自是建筑镶板100的未沾污的第一主表面111的初始颜色值,其使用来自美能达公司的美能达色度计cr410测量。l2、a2和b2值是在建筑镶板100的每个第一主表面111被污垢组合物(即,手指油、汗液等)沾污之后由美能达色度计cr410测量的颜色值。较小的δe值表示改进的耐污渍性。根据本发明,第一涂层130和第二涂层140的组合可以提供δe值小于2的建筑镶板。另外,第一涂层130和第二涂层140的组合可以导致建筑镶板的第一主表面111具有增强的疏水性。根据本发明,术语“疏水性”或“疏水性的”是指极难润湿并且能够在大气条件下排斥液态水的组合物。因此,如本文所用,术语“疏水性的”是指与参考液体(即水)产生大于90°的接触角的表面。使用液滴在固体基质表面上形成的接触角作为特定固体润湿能力的定量测量的概念也早已被很好地理解。润湿是当液体和固体两者结合在一起时,由分子间相互作用产生的液体与固体表面保持接触的能力。润湿程度(润湿性)由粘合力和内聚力之间的力平衡确定。如果水滴与基材表面的接触角大于90°,则通常认为它是疏水的。根据本发明的建筑镶板100的第一主表面111呈现出至少约115°的水接触角。在优选实施例中,建筑镶板100的第一主表面111呈现出约125°至约135°的水接触角(包括其间的所有子范围和角度)。在该接触角下,大多数普通水和油(例如指纹油)将不会弄湿建筑镶板100的第一主表面111,从而使建筑镶板100在安装期间不会弄脏。现在参照图5和图6,本发明的可选实施例包括内部空间中的天花板系统10,其中内部空间包括全体空间3和有效室环境2。天花板系统10可包括支撑格栅30,其中全体空间3位于支撑格栅30上方并且位于建筑物中上方相邻楼层的屋顶或底层地板4下方。全体空间3为建筑物内的机械线路(例如,hvac、管道等)提供空间。有效空间2在建筑物的正常预期使用期间为建筑物居住者提供空间(例如,在办公楼中,有效空间将被包括计算机、灯等的办公室占用)。支撑格栅30可包括多个第一支撑支柱32和多个第二支撑支柱33。每个第一支撑支柱32可彼此平行。每个第二支撑支柱33可以彼此平行。多个第一支撑支柱32可以与多个第二支撑支柱33正交或垂直,从而形成支柱的交叉图案,该支柱形成支撑格栅30。支撑格栅30可以包括可以接收建筑镶板20的由交叉的第一和第二支撑支柱32、33形成的开口31,从而形成天花板系统10。第一支撑支柱32和第二支撑支柱33中的至少一个可包括具有水平凸缘41和垂直腹板42的倒t形杆。水平凸缘41可包括下表面41a和上表面41b,所示,其中安装状态下下表面41a面向有效室环境2以及上表面41b面向全体空间3。下表面41a在与垂直腹板42从水平凸缘41延伸的方向的对立面。根据该实施例,如前所述,本发明的第一涂层130可以直接施加于第一和/或第二支撑支柱33中的至少一个的水平凸缘41的下表面41a。然后可以将第二涂层140施加到第一涂层130,如前所述。本发明还可以提供一种天花板系统10,其包括涂覆的支撑格栅60,该涂覆的支撑格栅60包括支撑格栅30、第一涂层130和第二涂层140,由此将第一涂层130施加到支撑格栅30的水平凸缘41的上表面41a的至少一部分以及将第二涂层140施加到第一涂层130,并且由此第二涂层140的上表面141面向有效室环境2。根据本发明,本发明的防污产品可以是许多构型之一的结果。根据一些实施例,产品可包括涂覆有第一涂层130的基材120,由此第一涂层130包括液基阴离子含氟表面活性剂。在这样的实施例中,可任选存在第二涂层140。在这样的实施例中,第一涂层130的上表面可以形成产品的主表面。在这样的实施例中,第二涂层140可任选地存在,由此第二涂层140包括含氟防护剂组分,含氟防护剂组分包括含氟聚合物、含氟表面活性剂或其组合。根据其他实施例,防污产品可包括涂有第一涂层130的基材120,由此第一涂层130包括蜡状(即固体)阴离子含氟表面活性剂。在这样的实施例中,可以可选地存在第二涂层140。在这样的实施例中,第一涂层130的上表面可以形成产品的主表面。在这样的实施例中,第二涂层140可任选地存在,由此第二涂层140包括含氟防护剂组分,含氟防护剂组分包括含氟聚合物、含氟表面活性剂或其组合。根据其他实施例,防污产品可包括涂覆有第一涂层130的基材120,由此第一涂层130不包括含氟防护剂组分。在这样的实施例中,产品还包括第二涂层140,由此第二涂层包括含氟防护剂组分,含氟防护剂组分包括含氟聚合物、含氟表面活性剂或其组合。在这样的实施例中,第二涂层140形成产品的主表面。根据本发明制备以下实施例。本发明不限于这里描述的示例。实施例面漆防污测试方案以下实验测量根据本发明的建筑镶板的主表面上的防油和防污性。制备具有由粉末涂层前体形成的聚合物粉末涂层的建筑镶板,其通过将前体组分混合在一起(即,聚合物粘合剂、交联剂和含氟表面活性剂)来制备。含氟表面活性剂具有100%固体并包括具有至少一个磷酸基团的阴离子含氟表面活性剂。阴离子含氟表面活性剂具有50℃至70℃的熔融温度和1至5的ph值。示例性合适的阴离子含氟表面活性剂可以从dupont商购获得,商品名为fs-66。然后将粉末涂层前体通过挤出机在约90℃至约110℃的温度下熔融混合,接着将所得挤出物造粒成粉末。将每种所得粉末喷涂到铝基材的第一主表面上。然后将涂覆的基材在195℃的温度下热固化以形成粉末涂覆的基材。实施例1然后将液基涂层施加到粉末涂层的顶部表面上,其中液基涂层包括80wt%的水和20wt%的第一防护剂组分。第一防护剂组分是阳离子含氟表面活性剂,其ph范围为从约4至约6,密度为1.06g/cm3。将液基涂层以10g/m2的量施加到粉末涂层上。然后将所得的液基涂层在15℃至40℃的温度下干燥,以形成实施例1的建筑镶板。实施例1的所得建筑镶板具有涂覆在粉末涂层顶上的为约2g/m2的量的含氟表面活性剂。实施例2根据与实施例1相同的方法制备第二建筑镶板(实施例2),不同之处在于将液基涂层组合物稀释至第二防护剂组分的浓度为0.2wt%。第二防护剂组分是阴离子含氟表面活性剂,其ph范围为约9至约11,密度为约1.1g/cm3。然后将液基涂层组合物以10g/m2的速率涂覆到含氟表面活性剂的粉末涂层上,并干燥液基涂层组合物。所得到的实施例2的建筑镶板具有涂覆在粉末涂层顶上的约0.02g/m2的量的含氟表面活性剂。对比例1除了使用第一非离子含氟表面活性剂代替第二防护剂组分外,根据与实施例2相同的方法制备第三建筑镶板(对比例1)。非离子含氟表面活性剂的ph范围为从约7至约8.5,密度为约1.4g/cm3,如可从dupont商购获得fs-3100。得到的对比例1的建筑镶板在粉末涂层的顶上涂有0.02g/m2的含氟表面活性剂。对比例2除了将第二非离子含氟表面活性剂施加到粉末涂层上之外,根据与实施例2相同的方法制备第四建筑镶板(对比例2)。第二含氟表面活性剂的ph范围为从约7至约9,密度为约1.1g/cm3,如可从dupont购得fs-65。得到的对比例1的建筑镶板在粉末涂层的顶上涂有0.02g/m2的含氟表面活性剂。然后根据以下方法比较实施例1和2以及对比例1和2的建筑镶板的防油和防污性。制备污垢组合物,包括泥炭苔、硅酸盐水泥、煅烧高岭石和sno-brite粘土。sno-brite粘土包括>95wt%的高岭土以及少量的二氧化硅(石英、方石英)、云母和二氧化钛。将实施例1和比对比例1的每个建筑镶板放置成使得粉末涂覆的表面朝上。然后将一定量(0.2克)表1的污垢组合物放入塑料杯中并保持在粉末涂层的表面上,轻敲塑料杯,使得污垢组合物自然地落在防污镶板的朝上的粉末涂覆的表面上。除了施加到粉末涂覆的表面上的污垢组合物之外,防污镶板仍保持不受影响。然后将弄脏的建筑镶板放置24小时。在24小时之后,将建筑镶板颠倒翻转(180°),使粉末涂覆的表面朝下,使松散的污垢组合物从防污镶板的粉末涂覆的表面上脱落。然后将建筑镶板的与粉末涂覆的表面相对的表面轻敲20次,使得额外的污垢组合物从建筑镶板上脱落。然后将建筑镶板向后半转(90°),使得建筑镶板的粉末涂覆的表面面向侧面,然后轻敲建筑镶板的侧面10次。然后将建筑镶板转回到原始位置,使得粉末涂覆的表面朝上,然后测量该表面的颜色值的变化,即“变量增量e”(δe),如前所述。具体地,l2、a2和b2值是在每个样品被污垢组合物弄脏之后由美能达色度计cr410测量的颜色值,如前所述。每种颜色测试的对照值是相同的颜色和没有施加任何污垢组合物的结构。在样品的三个不同区域拍摄各种颜色读数,并记录平均变量增量e,如表1所示。表1如表1所示,与施加于粉末涂层的包括非离子含氟表面活性剂的其它顶涂层相比,施加于包括阴离子含氟表面活性剂的粉末涂层的顶涂层中的阳离子含氟表面活性剂的组合提供了建筑镶板的防污和防油性的出乎意料的改进,由较小的变量增量e值证明,仅为0.02g/m2的量。粉末涂层中液体含氟表面活性剂的防污测试方案以下实验测量根据本发明的在粉末涂层中使用液基含氟表面活性剂的建筑镶板的主表面上的防油和防污性。在进行该实验时,制备一系列建筑镶板,其上涂覆有粉末涂层。制备第一建筑镶板(对照1),其具有不含含氟表面活性剂的粉末涂层。对照1的建筑面镶板不包括顶涂层。制备第二建筑镶板(实施例3),其中粉末涂层由包括蜡状(即100%固体)阴离子含氟表面活性剂的前体形成。根据与实施例1和2(包括相同的阴离子含氟表面活性剂)的粉末涂层相同的方法制备实施例3的粉末涂层,实施例3的建筑镶板不包括顶涂层。使用由包括液基阴离子含氟表面活性剂的前体形成的粉末涂层制备三个另外的建筑镶板(实施例4-6)。通过在低于120°f的温度下在共混器中将前体组分(即聚合物粘合剂、交联剂和液基阴离子含氟表面活性剂)共混在一起来制备实施例4-6的粉末涂层。共混后,将共混的前体混合物在约90℃至约110℃的温度下通过挤出机,由此存在于液基阴离子含氟表面活性剂中的液体载体从前体蒸发。随后,将所得挤出物造粒成粉末。将每种所得粉末喷涂到铝基材的第一主表面上。然后将涂覆的基材加热至使交联剂和聚合物粘合剂共价键合的温度,从而在基材顶上提供交联的粉末涂层。使用由包括液基非离子含氟表面活性剂的前体形成的粉末涂层制备另外两个建筑镶板(对比例3和4)。根据与实施例4-6相同的方法制备对比例3和4的粉末涂层,不同之处在于液基含氟表面活性剂是非离子的而不是阴离子的。关于实施例3-6和对比例3和4的建筑镶板,选择每种前体混合物中特定量的液基含氟表面活性剂,使得所得粉末涂层在最终粉末涂层中含有相同相对量的固体含氟表面活性剂。因此,尽管实施例3-6和对比例3和4的每种液基含氟表面活性剂的固含量在前体中可以不同,但由于镶板之间的含氟表面活性剂的干燥量(即,固体)是相同的,因此最终的建筑镶板提供了准确的并排比较。然后对所得到的对照1、实施例3-6和对比例3和4的建筑镶板进行如实施例1和2所述的防污和防油性测试。每个建筑镶板的防污和防油的结果试验列于下表2中。表2如表2所示,与使用其他类型的非离子含氟表面活性剂相比,在本发明的粉末涂层中使用液基阴离子含氟表面活性剂在防污和防油性方面提供了意想不到的改善,这反映在与对比例3和4的δe相比实施例4-6的建筑镶板的低δe上。此外,根据本发明的方法掺入液基阴离子含氟表面活性剂避免了含氟表面活性剂在整个前体中的结块和不适当分布的问题,如实施例4-6的建筑镶板的δe所示,如果不低于由固体含氟表面活性剂形成的实施例3的建筑镶板的δe,则与其相同。将液基含氟表面活性剂成功掺入粉末涂层组合物中违背了本领域中的已知常识,即,当形成粉末涂层组合物时避免使用含液体组分。当施加至基材时需要粉末涂层组合物是固体的。抗菌测试方案使用抗菌测试方案来制备和测试实施例7-13、对比例5-11和对照2-8的建筑镶板样品。通过在50mm×50mm金属基材上施加粉末涂层组合物来制备每个建筑镶板样品。粉末涂层组合物的每个均包括聚合物树脂前体、交联剂和颜料的共混物,并具有至少99%的固含量。本发明的粉末涂层组合物(即,实施例7-13)包括基于100份总粉末涂层组合物的7重量份的硼酸锌和0.1重量份的2-(4-噻唑基)苯并咪唑的抗微生物组合物。对比例5-11的粉末涂层组合物不包括本发明的抗微生物组合物,而是包括硝酸银的抗微生物组合物。对照2-8的粉末涂层组合物不包括抗微生物组合物。一旦施加到金属基材上,将每种粉末涂层组合物加热至高于固化温度,使聚合物树脂前体与交联剂反应并形成交联的粉末涂层。进行了若干测试以测量交联粉末涂层的抗菌功效。每个测试包括总共三个培养皿,其中第一培养皿包括本发明的建筑镶板样品中的一个样品(即,实施例7-13中的一个实施例),第二个培养皿包括对比建筑镶板样品中的一个样品(即,对比例5-11中的一个对比例),以及第三培养皿包括对照镶板中的一个镶板(即,对照2-8的一个对照)。每个培养皿接种特定浓度的细菌,然后用无菌塑料覆盖,将接种物均匀地铺在每个样品表面上。将样品在35℃和90%的相对湿度下温育。在每个培养皿中在初始时间(t=0)测量细菌浓度,并在预定的24小时的时间段(t=24)之后再次测量细菌浓度。在24小时的时间段之后,对每个测试样品上的细菌菌落计数并记录。根据下面列出的公式计算每个样品的抗微生物活性值,并记录为对数减小如下:90%减小=1log减小(即,1,000,000降低至100,000是1log减小)99%减小=2log减小(即,1,000,000降低至10,000是2log减小)99.9%减小=3log减小(即,1,000,000降低至1,000是3log减小)99.99%减小=4log减小(即,1,000,000降低至100是4log减小)99.999%减小=5log减小(即,1,000,000降低至10是5log减小)将抗菌涂层的性能标准化为抗菌活性(“r”),其根据以下计算:r=(ut–uo)–(at–uo)=ut–at其中,r:抗菌活性uo:来自对照的活细菌在t=0时的对数平均值。ut:来自对照的活细菌在t=24时的对数平均值。at:来自测试样品的活细菌在t=24时的对数平均值。根据本发明,当抗菌活性为2.0或更高时,抗微生物涂层被认为具有抗菌有效性。本文提供了每种细菌测试的结果。抗金黄色葡萄球菌的抗菌功效在起始细菌浓度为9.7×10cfu/ml时进行测试来测量针对金黄色葡萄球菌细菌的功效。使用金黄色葡萄球菌的第一次测试的结果如下表3所示。表3金黄色葡萄球菌实施例7对比例5对照2在t=24时活细菌的平均对数值-0.203.744.57r值4.770.83-细菌减少99.99%85%-根据本发明的抗微生物涂层(实施例7)显示细菌菌落减少99.99%,导致r值为4.77,远高于针对金黄色葡萄球菌细菌的细菌有效性的2.0阈值。对比抗微生物涂层(对比例5)仅显示出85%的减少,导致r值为0.83,远低于2.0r值阈值。在7.5×105cfu/ml的较低的起始细菌浓度下重复针对金黄色葡萄球菌细菌的功效测试。结果列于表4中。表4金黄色葡萄球菌nctc#10442实施例8对比例6对照3在t=24时活细菌的平均对数值-0.203.775.26r值5.261.49-细菌减少99.99%97%-本发明的抗微生物涂层(实施例8)再次表现出高达99.99%的细菌活性降低,导致对金黄色葡萄球菌细菌的r值为5.26。对比抗微生物涂层(对比例6)仅显示出97%的减少,导致r值为1.49,低于2.0阈值。抗大肠杆菌的抗菌功效在7.2×105cfu/ml的起始细菌浓度下进行测试来测量针对大肠杆菌细菌的有效性。结果列于表5中。表5大肠杆菌atcc#8739实施例9对比例7对照4在t=24时活细菌的平均对数值-0.20-0.202.67r值2.872.87-细菌减少99.8%99.8%-在该浓度下,本发明的抗菌涂层(实施例9)以及对比涂层(对比例7)均显示出细菌菌落减少高达99.8%,导致r值为2.87,高于针对大肠杆菌细菌的细菌有效性的阈值2.0。在7.6×105cfu/ml的较高起始细菌浓度下重复针对大肠杆菌细菌的功效测试。结果列于表6中。表6大肠杆菌nctc#12900实施例10对比例8对照5在t=24时活细菌的平均对数值-0.205.686.06r值6.260.39-细菌减少99.99%58%-本发明的抗微生物涂层(实施例10)表现出高达99.99%的细菌活性降低,导致对大肠杆菌细菌的r值为6.26。然而,对比抗微生物涂层(对比例8)仅显示出58%的降低,导致r值为0.39,远低于2.0的r值阈值。抗蜡状芽孢杆菌的抗菌功效在4.1×105cfu/ml的起始细菌浓度下进行测试以测量针对蜡状芽孢杆菌细菌的有效性。结果如表7所示。表7蜡状芽孢杆菌nctc#11143实施例11对比例9对照6在t=24时活细菌的平均对数值2.644.354.95r值2.310.60-细菌减少99.5%75%-实施例11的抗微生物涂层表现出高达99.5%的细菌活性降低,导致r值为2.31,其高于针对蜡状芽孢杆菌细菌的细菌有效性的阈值2.0。对比抗微生物涂层(对比例9)仅表现出75%的降低,导致r值为0.6,远低于2.0r值阈值。抗鲍氏不动杆菌的抗菌功效在9.2×105cfu/ml的起始细菌浓度下进行测试以测量针对鲍氏不动杆菌的有效性。结果列于表8中。表8鲍氏不动杆菌nctc#12156实施例12对比例10对照7在t=24时活细菌的平均对数值-0.201.625.82r值6.024.20-细菌减少99.99%99.99%-本发明的抗微生物涂层(实施例12)和对比涂层(对比例10)均表现出高达99.99%的细菌菌落减少。然而,在r值为6.02时,本发明的抗微生物涂层再次优于对比抗微生物涂层,对比抗微生物涂层呈现对鲍氏不动杆菌r值为4.2。抗肺炎克雷伯菌的抗菌效力在起始细菌浓度为6.4×105cfu/ml时进行测量针对肺炎克雷伯氏菌的有效性的试验。结果列于表9中。表9本发明的抗微生物涂层(实施例13)和对比涂层(对比例11)均显示出高达99.99%的细菌菌落减少。然而,在r值为4.44时,本发明的抗微生物涂层优于对比抗微生物涂层,对比抗微生物涂层对肺炎克雷伯氏菌表现出r值为4.05。抗菌功效概述每个建筑镶板的抗菌功效总结在表10中表10浓度实施例对比例5-11金黄色葡萄球菌9.7×105有效无效金黄色葡萄球菌7.5×105有效无效大肠杆菌7.2×105有效有效大肠杆菌7.6×105有效无效蜡状芽孢杆菌4.1×105有效无效鲍氏不动杆菌9.2×105有效有效肺炎克雷伯菌6.4×105有效有效如表10所示,本发明的抗微生物添加剂在各种细菌浓度范围内赋予粉末涂层高效的广谱细菌抗性,而对比抗微生物添加剂仅对选定数量的细菌起作用以及对比抗微生物添加剂对有限浓度的选择细菌有效。防霉测试方案使用防霉方案来制备和测试实施例14、15,对比例12和对照实施例9的样品建筑镶板。通过在3”×4”的金属基材上施加粉末涂层组合物来制备每个建筑镶板样品。每种粉末涂层组合物具有至少99%的固含量并且包括聚合物树脂前体、交联剂和颜料的共混物。本发明的粉末涂层组合物(即,实施例14和15)包括基于100份总粉末涂层组合物的7重量份的硼酸锌和0.1重量份的2-(4-噻唑基)苯并咪唑的抗微生物组合物。对比例12的粉末涂层组合物不包括本发明的抗微生物组合物,而是包括硝酸银的抗微生物组合物。对照实施例9的粉末涂层组合物不包括抗微生物组合物。将每个样品置于测试室中,所述测试室包括接种有允许生长的真菌孢子的土壤。具体地,土壤用黑曲霉(atcc#6275);桔青霉(atcc#9849);和出芽短梗霉(atcc#9348)播种。将室保持在室温(32.5±1℃)和95±3%的相对湿度下一周。一段时间后,将每个样品从测试室中取出并观察。观察并测量前后主表面上的由霉菌形成引起的污损量。将污损程度分配到如表11中列出的评定量表:表11等级定义10无污损990%干净(1-10%污损)880%干净(11-20%污损)770%干净(21-30%污损)660%干净(31-40%污损)550%干净(41-50%污损)440%干净(51-60%污损)330%干净(61-70%污损)220%干净(71-80%污损)110%干净(81-90%污损)00%干净(91-100%污损)每周后观察含有施加到基材上的粉末涂层的每个样品以及对照样品的污损,除了粉末涂层不包括抗微生物组合物之外。实验结果列于下表12中。表12周1周2周3周4实施例1410/1010/1010/1010/10实施例1510/1010/1010/1010/10对比例1210/1010/1010/1010/10对照910/1010/1010/1010/10如表12所示,抗微生物涂层组合物在4周的时间内相对于其它粉末涂层表现出充分地防止霉菌生长。当前第1页12
再多了解一些
本文用于企业家、创业者技术爱好者查询,结果仅供参考。