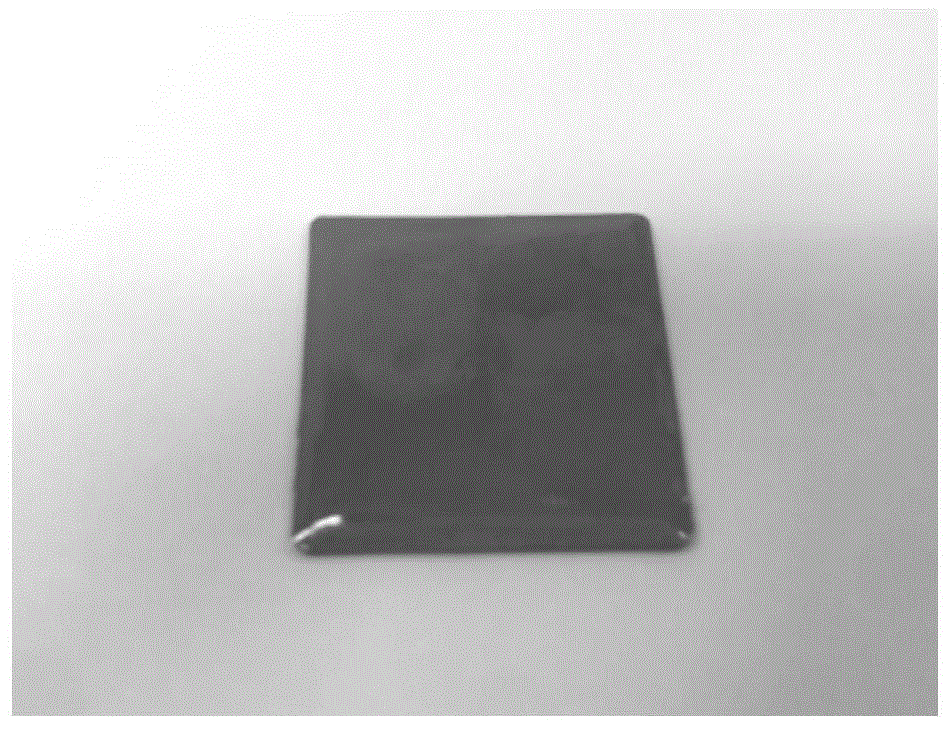
本发明属于热界面材料技术领域,涉及一种高分子复合热界面材料及其制备方法。
背景技术:
随着计算机芯片、大功率电子设备及光电器件等电子产品,空调、电视、冰箱、led照明等家用和工业用电器,汽车、飞机、轮船、高铁等现代化交通设备向轻量化、小型化、高功率方向发展,其单位面积产生的热量愈来愈高,对热控系统提出了更高的要求。因此,如何快速、安全的带走发热元件上的热量成为了制约很多工业领域发展的一个重要课题。
热界面材料广泛应用于电子器件的散热管理,主要用于填充电子器件与散热器之间空隙,降低电子器件与散热器之间接触热阻,直接影响电子器件的性能和使用寿命。在大功率芯片(cpu或gpu)封装结构中,热界面材料主要用于填补芯片与均热板、均热板与热沉接触时产生的微空隙。且由于均热板和热沉分别选用高导热的铜(导热系数400w/mk)和铝(导热系数237w/mk),材质比较硬容易碰撞产生磨损,因此选择导热性能好、柔顺性好的热界面材料不仅能起到增强散热效果的功能,还能起到保护的作用。
现有的热界面材料主要包括导热膏体、导热凝胶、相变热界面材料、高分子基复合热界面材料和金属热界面材料等几类。其中,尤其以铝、氧化铝、氮化硼或氮化铝作为导热填料的热界面材料被广泛研究与发展。
当前大部分研究往往关注于如何提高热界面材料的导热系数,忽视了柔性的重要性。所谓良好的柔顺性是指材料具有低的弹性模量和高的柔顺性。低的弹性模量能在较低的安装压力下便能使热界面材料充分的填充空袭,降低热界面材料与接触面的接触热阻。高的弹性形变可以减轻芯片、均热板和热沉由于热膨胀系数不匹配导致的应力集中带来的翘曲失效问题。然而在热界面材料中“高导热“往往与”柔顺性“相抵触。高的导热填料填充量会提高材料的导热性能,但也会使材料的力学性能急剧恶化,且随着使用会在其表面或内部产生裂缝而让其散热效能急剧下降,降低其使用寿命。在实际应用过程中,热界面材料不仅要求高的导热系数,还要求高的柔性(低的弹性模量且高的弹性形变量),并且具有一定的自修复能力提高热界面材料的使用寿命。因此研发出一种具有高导热、高柔顺、自修复的热界面材料具有重大意义。
技术实现要素:
为了解决传统热界面材料导热填料升高导致柔顺性下降,使用过程中产生的裂缝缺陷使得散热效能降低的问题,本发明的目的在于提供一种高分子复合热界面材料及其制备方法。该热界面材料是一种可自愈、可回收的热界面材料,其具有优异的导热性能和柔顺性,可以紧密贴合于各种需散热的表面,使发热元件与散热器表面间的间隙中完全没有空气流通,提高系统的散热能力。
为了达到上述目的,本发明所采用的技术方案为:一方面,本发明提供了一种高分子复合热界面材料,包括以下原料制成:
硫辛酸和/或其衍生物、交联剂、铝盐、导热填料;
所述硫辛酸的结构式为:
所述硫辛酸衍生物的结构式为:
其中n选自10-100。
进一步地,所述硫辛酸和/或其衍生物、交联剂、铝盐和导热填料的质量比为1:(0.1-1):(0.001-0.01):(0.1-5)。
进一步地,所述交联剂为不饱和烯烃化合物,所述不饱和烯烃化合物包括1,4-二异丙烯基苯、1,3-二异丙烯基苯、对苯二甲酸二烯丙酯、间苯二甲酸二烯丙酯、2-甲基-1-苯基丙烯、4-甲基苯乙烯、4-异丙烯基甲苯中的至少一种。
进一步地,所述铝盐包括氯化铝、硝酸铝、硫酸铝、硬脂酸铝中的一种或多种。
进一步地,所述导热填料包括铝粉、氮化硼、碳纳米管、氧化铝、石墨烯、纳米银粉。
进一步地,所述铝粉为表面活化的铝粉;
优选地,所述表面活化的铝粉是将铝粉置于去离子水、无水乙醇、过氧化氢的混合溶液中50-70℃加热搅拌2-10h后,离心洗涤得到;
优选地,所述去离子水、无水乙醇、过氧化氢的混合溶液中去离子水、无水乙醇、过氧化氢的质量比为(1-5):1:1;
优选地,所述铝粉与混合溶液的质量比为1:(5-100)。
另一方面,本发明提供了一种上述任一所述的高分子复合热界面材料的制备方法,包括以下步骤:
(1)将硫辛酸和/或其衍生物置于容器中,搅拌并加热,直到硫辛酸和/或其衍生物融化为低粘度黄色透明液体;
(2)在硫辛酸和/或其衍生物融化为低粘度黄色透明液体时,加入交联剂,继续加热搅拌一段时间,之后再加入铝盐溶液,继续加热搅拌一段时间制备得到聚硫辛酸基超分子弹性体;
(3)维持在加热状态下,加入导热填料,在真空下搅拌均匀,冷却至室温得到所述高分子复合热界面材料。
进一步地,步骤(1)中所述加热的温度为100-180℃。
进一步地,步骤(2)中所述加入交联剂后加热的温度为100-180℃,加热搅拌的时间为2-10min;
优选地,步骤(2)中加入铝盐溶液后加热的温度为100-180℃,加热搅拌的时间为1-10min。
进一步地,所述铝盐溶液所用溶剂包括甲醇、乙醇、四氢呋喃、丙酮中的一种或多种。
进一步地,步骤(3)中所述加热的温度为100-180℃。
本发明高分子复合热界面材料中聚硫辛酸基超分子弹性体具有动态的二硫键,在高温加热的情况下二硫键会断裂打开,冷却时又能重新键合,这使得材料具有制备便捷、能熔融再塑的特点。且超分子弹性体里面具有大量的非共价牺牲键-氢键,在材料受到拉伸时,氢键能够断裂提供能量消散的作用,防止界面材料变形时应力过大,对芯片等重要器件造成损坏,同时也大大提高了材料的拉伸性能,并且大量的氢键赋予了其优异的自修复性能。导热填料的加入构建了良好的导热网络,导热填料表面的官能团如羟基、羧基等也能和聚硫辛酸弹性体中大量的羧基形成氢键,提高了两者之间的结合,从而整体提高了复合材料的机械性能和导热性能,具有良好柔顺性的高导热材料得以制备出来。
本发明的有益效果是:1)本发明所用的原料对人体无害,生物相容,来源广泛,价廉易得,具有工业可行性。2)本发明采用直接加热熔化原料的方法,无溶剂,反应迅速,过程简单安全,反应条件温和,不产生废水、废渣等工业污染;整个制备工艺简单,生产成本低廉,无副产物产生,经济效益好,符合绿色化学的要求。3)本发明高分子复合热界面材料具有室温自愈性,高度拉伸性(伸长率可达3000%)以及优异的热响应性(能在热刺激下,熔融再塑)。4)本发明高分子复合热界面材料具有较高的导热系数(导热系数可达2.028w/(m·k)),在热界面材料领域具有广泛的应用前景。5)本发明高分子复合热界面材料具有自修复、可回收的特点。
附图说明
图1为本发明实施例1制备得到的高分子复合热界面材料—l的外观图。
图2为本发明实施例2制备得到的高分子复合热界面材料—2的拉伸性能曲线。
图3为本发明实施例3制备得到的高分子复合热界面材料—3的结构表征图,其中a为高分子复合热界面材料—3的结构示意图,b为高分子复合热界面材料—3的红外光谱图,c为高分子复合热界面材料—3的扫面电镜图。
图4为本发明实施例4制备得到的高分子复合热界面材料的自愈性能图,其中a为高分子复合热界面材料的自愈光学图像,b为高分子复合热界面材料初始和自愈后的拉伸曲线。
图5为本发明实施例5制备得到的高分子复合热界面材料的熔融再塑性能图,其中a为剪碎的高分子复合热界面材料,b为熔融再塑的高分子复合热界面材料。
图6为本发明实施例6制备得到的高分子复合热界面材料的拉伸及回弹性能图,其中a为高分子复合热界面材料的回弹性能测试图,从左到右依次为初始图、拉伸和释放的图,b为高分子复合热界面材料的循环拉伸曲线;
图7为对比例制备得到的硅橡胶/铝复合材料拉伸性能曲线。
具体实施方式
为了更好地理解本发明的内容,下面结合具体实施方法对本发明内容作进一步说明,但本发明的保护内容不局限以下实施例。
实施例1
称取去离子水60g,无水乙醇20g,过氧化氢20g配置铝粉表面活化溶液。称量20g铝粉加入上述表面活化溶液中,50℃油浴加热下搅拌5h后,离心洗涤得到所述表面活化的铝粉。
将10g硫辛酸置于带有搅拌装置的反应容器中,油浴加热搅拌(油浴温度为100℃-180℃)至硫辛酸粉末融化为低粘度黄色透明液体。然后加入5g1,3-二异丙烯基苯至该反应容器中,继续加热搅拌2分钟,再加入含50mg氯化铝的四氢呋喃溶液至该反应器中,继续加热搅拌2分钟,最后加入15g表面活化的铝粉至反应容器中,在真空下再加热搅拌5分钟,停止加热,趁热将复合溶液倾倒至聚四氟乙烯模具中,冷却后得高分子复合热界面材料-1。
实施例2
称取去离子水90g,无水乙醇30g,过氧化氢30g配置铝粉表面活化溶液。称量30g铝粉加入上述表面活化溶液中,50℃油浴加热下搅拌7h后,离心洗涤得到所述表面活化的铝粉。
将10g硫辛酸置于带有搅拌装置的反应容器中,油浴加热搅拌(油浴温度为100℃-180℃)至硫辛酸粉末融化为低粘度黄色透明液体。然后加入2g1-4二异丙稀基苯至该反应容器中,继续加热搅拌2分钟,再加入含50mg氯化铝的四氢呋喃溶液至该反应器中,继续加热搅拌2分钟,最后加入28g表面活化的铝粉至反应容器中,在真空下再加热搅拌5分钟,停止加热,趁热将复合溶液倾倒至聚四氟乙烯模具中,冷却后得高分子复合热界面材料-2。
实施例3
称取去离子水90g,无水乙醇30g,过氧化氢30g配置铝粉表面活化溶液。称量30g铝粉加入上述表面活化溶液中,50℃油浴加热下搅拌7h后,离心洗涤得到所述表面活化的铝粉。
将10g硫辛酸置于带有搅拌装置的反应容器中,油浴加热搅拌(油浴温度为100℃-180℃)至硫辛酸粉末融化为低粘度黄色透明液体。然后加入3g1-4二异丙稀基苯至该反应容器中,继续加热搅拌2分钟,再加入含40mg氯化铝的四氢呋喃溶液至该反应器中,继续加热搅拌2分钟,最后加入30g表面活化的铝粉至反应容器中,在真空下再加热搅拌5分钟,停止加热,趁热将复合溶液倾倒至聚四氟乙烯模具中,冷却后得高分子复合热界面材料-3。
实施例4
称取去离子水60g,无水乙醇20g,过氧化氢20g配置铝粉表面活化溶液。称量20g铝粉加入上述表面活化溶液中,50℃油浴加热下搅拌5h后,离心洗涤得到所述表面活化的铝粉。
将10g硫辛酸置于带有搅拌装置的反应容器中,油浴加热搅拌(油浴温度为100℃-180℃)至硫辛酸粉末融化为低粘度黄色透明液体。然后加入2g1-4二异丙稀基苯至该反应容器中,继续加热搅拌2分钟,再加入含20mg氯化铝的四氢呋喃溶液至该反应器中,继续加热搅拌2分钟,最后加入12g表面活化的铝粉至反应容器中,在真空下再加热搅拌5分钟,停止加热,趁热将复合溶液倾倒至聚四氟乙烯模具中,冷却后得高分子复合热界面材料-4。
实施例5
称取去离子水60g,无水乙醇20g,过氧化氢20g配置铝粉表面活化溶液。称量20g铝粉加入上述表面活化溶液中,50℃油浴加热下搅拌5h后,离心洗涤得到所述表面活化的铝粉。
将5g硫辛酸和5g硫辛酸衍生物(n为50)置于带有搅拌装置的反应容器中,油浴加热搅拌(油浴温度为100℃-180℃)至硫辛酸粉末融化为低粘度黄色透明液体。然后加入2g1-4二异丙稀基苯至该反应容器中,继续加热搅拌2分钟,再加入含20mg氯化铝的四氢呋喃溶液至该反应器中,继续加热搅拌2分钟,最后加入12g表面活化的铝粉至反应容器中,在真空下再加热搅拌5分钟,停止加热,趁热将复合溶液倾倒至聚四氟乙烯模具中,冷却后得高分子复合热界面材料-5。
实施例6
称取去离子水120g,无水乙醇40g,过氧化氢40g配置铝粉表面活化溶液。称量40g铝粉加入上述表面活化溶液中,50℃油浴加热下搅拌10h后,离心洗涤得到所述表面活化的铝粉。
将10g硫辛酸置于带有搅拌装置的反应容器中,油浴加热搅拌(油浴温度为100℃-180℃)至硫辛酸粉末融化为低粘度黄色透明液体。然后加入2.5g对苯二甲酸二烯丙酯至该反应容器中,继续加热搅拌2分钟,再加入含10mg氯化铝的四氢呋喃溶液至该反应器中,继续加热搅拌2分钟,最后加入36g表面活化的铝粉至反应容器中,在真空下再加热搅拌5分钟,停止加热,趁热将复合溶液倾倒至聚四氟乙烯模具中,冷却后得高分子复合热界面材料-6。
实施例7
称取去离子水90g,无水乙醇30g,过氧化氢30g配置铝粉表面活化溶液。称量30g铝粉加入上述表面活化溶液中,50℃油浴加热下搅拌7h后,离心洗涤得到所述表面活化的铝粉。
将10g硫辛酸置于带有搅拌装置的反应容器中,油浴加热搅拌(油浴温度为100℃-180℃)至硫辛酸粉末融化为低粘度黄色透明液体。然后加入2g1-4二异丙稀基苯至该反应容器中,继续加热搅拌2分钟,再加入含20mg氯化铝的四氢呋喃溶液至该反应器中,继续加热搅拌2分钟,最后加入28g表面活化的铝粉至反应容器中,在真空下再加热搅拌5分钟,停止加热,趁热将复合溶液倾倒至聚四氟乙烯模具中,冷却后得高分子复合热界面材料-7。
本发明提供的高分子复合热界面材料的外观(以高分子复合热界面材料—l为例),如图1所示。
本发明所提供的高分子复合热界面材料拉伸性能曲线(以高分子复合热界面材料-2为例)如图2所示,从图2可以看出,高分子复合热界面材料-2具有超过3000%的形变,优异的伸长率有助于材料在热膨胀系数不匹配度更高的两个器件中用作热界面材料。
本发明所提供的高分子复合热界面材料结构表征(以高分子复合热界面材料-3为例),如图3所示,从图3a可以看出,体系内具有大量的动态共价键-二硫键,在室温时提供材料足够的机械性能,在高温时能断裂以起到自修复、熔融再塑的作用。同时体系内还具有大量的氢键和金属配位键。可以增强链之间的作用力,起到增强机械性能、室温自修复的作用。经过表面活化的铝粉带有大量的羟基,可以和基体中的羧基形成氢键,增强了填料与基体之间的接触作用,降低了填料和基体之间的界面热阻,从图3b可以看出,2500-3500cm-1出现了宽而大的氢键峰,证明了体系内含有大量的氢键,从图3c可以看出,导热填料铝粉在体系内分散均匀,无团聚的现象,这是实现良好机械性能和导热性能的必要条件。
高分子复合热界面材料自愈性能、回弹性能和导热性能测试。
1、自愈性能测试
(1)取一骨头棒状的本发明所述的高分子复合热界面材料(以高分子复合热界面材料-4为例),用剪刀将其切割成两段并紧靠放在一起,放置在离型纸上,用光学相机记录受损聚合物自修复的图像。图4a1所示为切断成两部分将进行自修复的复合材料;图4a2为正在进行室温自修复的复合材料;图4a3为经过5min自修复后可进行拉伸的样品,表明复合材料具有良好的室温快速自修复能力。
为精确获取复合材料室温自修复的效率,取一段条状的本发明所述的高分子复合热界面材料(以高分子复合热界面材料-4为例),用剪刀将其切割成两段并紧靠放在一起,室温下放置60min,将高分子复合热界面材料原始样品和自修复样品分别放置于材料万能试验机上,用20mm/min的速度进行拉伸,观察其拉伸性能,结果如图4b所示,从图4b可以看出,经过室温60min的自修复,复合材料可恢复其原伸长率的94%,具有十分优异的自修复性能。
取一段条状的本发明所述的高分子复合热界面材料(以高分子复合热界面材料-5为例),剪碎后置于试样瓶中在油浴150摄氏度的条件下加热5min,待熔融后再倒至聚四氟乙烯模中塑形,待冷却至室温后便得整块复合材料,剪碎的高分子复合热界面材料如图5a所示,熔融再塑的高分子复合热界面材料如图5b所示。说明高分子复合热界面材料-5能轻易熔融再塑。
上述实验表明,高分子复合热界面材料具有优良的自修复、熔融再塑性能。
2、回弹性能测试
取一骨头棒状的本发明所述的高分子复合热界面材料(以高分子复合热界面材料-6为例),用手握住聚合物的两端,聚合物材料中间棒状初始长度为30mm,缓慢拉伸至中间棒状部分为180mm(即型变量600%)后释放。观察其回弹性能,结果如图6a所示,可以看出仅发生了20mm的塑性形变,回弹率高达89%,显示出复合材料具有优良的回弹性能
取一骨头棒状的本发明所述的高分子复合热界面材料(以高分子复合热界面材料-6为例),在万能试验机上以100mm/min的速度进行循环拉伸,观察其回弹性能,结果如图6b所示。由图6b可以看出高分子复合热界面材料-6可在150%拉伸下多次循环,五次循环过后塑性形变低于30%。
以上实验表面高分子复合热界面材料具有优良的回弹性能。
3、导热性能测试
取一段块状的本发明所述的高分子复合热界面材料(以高分子复合热界面材料-7为例),制备样品尺寸为10*10*1mm的样品使用激光导热仪器测试其热扩散系数,测得热扩散系数为1.043m2/s。取适量样品(以高分子复合热界面材料-7为例)利用dsc测试其比热容,比热容为:1.116j/(k·g)。取适量样品(以高分子复合热界面材料-7为例),利用真密度仪器测试其密度,密度为:1.7424g/cm3,利用公式λ(t)=α(t)*cp(t)*ρ(t)(其中λ为导热系数,α为热扩散系数,cp为比热容,ρ为密度)计算得其导热系数,计算的导热系数为:2.028w/(m·k)。
对比例1
以70wt%填充量下的硅橡胶/铝复合材料与实施例2进行对比。
称取去离子水900g,无水乙醇300g,过氧化氢300g配置铝粉表面活化溶液。称量300g铝粉加入上述表面活化溶液中,50℃油浴加热下搅拌7h后,离心洗涤得到所述表面活化的铝粉。
采用溶液共混法通过加成反应合成70wt%填料含量的硅橡胶复合材料。具体而言,首先将75g乙烯基硅油基质和卡斯特催化剂以质量比为2000:1的比例在25℃下混合15min。然后将将233g的上述表面活化铝粉加入混合物当中并在25℃下搅拌120min。之后,加入25g固化剂含氢硅油并将产物在25℃下混合搅拌10min。最后,将所得混合物均匀地倒入模具中并在150℃下放置一定时间以使复合产物硫化成形。之后可将其切割成一定形状的试样以供进一步测试。对比例制备得到的硅橡胶/铝复合材料拉伸性能曲线结果如图7所示,在质量分数为70的填充量下,本发明的复合材料的伸长率(3058%)约为对比例制备得到的硅橡胶/铝复合材料伸长率(301%)的10倍以上,本申请显示出更为优秀的机械性能。
以上所述仅为本发明的具体实施方式,不是全部的实施方式,本领域普通技术人员通过阅读本发明说明书而对本发明技术方案采取的任何等效的变换,均为本发明的权利要求所涵盖。
本文用于企业家、创业者技术爱好者查询,结果仅供参考。