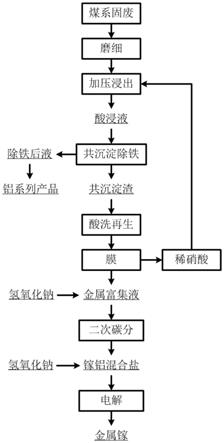
1.本发明属于冶金技术领域,尤其涉及一种从煤系固体废弃物中提取金属镓的方法。
背景技术:
2.镓是一种对高科技产业发展极其重要的金属元素,广泛应用于半导体、太阳能电池、合金、医学、玻璃制造、化工等领域,具有良好的市场前景。镓在自然界多与铝、锌等共生于矿物中,锌的硫化物矿和铝矾土矿是提取镓的重要原料。目前,世界上90%的镓都是从以铝土矿为主要原料的氧化铝工业的副产物中得到的。
3.煤系固体废弃物包括粉煤灰和煤矸石,来自煤的开采、加工和利用过程。我国是煤炭生产和消费大国,每年产生大量的煤系固体废物,不仅占用了大量的土地资源,而且还严重污染着环境。因此,煤系固体废弃物的处置及高值化综合利用具有重要的研究意义。然而目前关于粉煤灰和煤矸石的利用方法主要考虑的是其主要成分氧化铝的经济价值,而其他成分往往作为杂质处理掉。而实际上,粉煤灰和煤矸石中还赋存了大量珍贵的稀有金属,如镓、锗等。因此,从煤系固体废弃物中有效回收稀有金属具有良好的经济效益。
4.现有技术中稼的提取方法主要包括溶剂萃取法、萃淋树脂法、石灰乳碳酸化法。其中,溶剂萃取法所采用的最为有效的萃取剂是kelex l00,但其合成难度大,价格昂贵,导致应用受限。萃淋树脂法的主要工序包括吸附、淋洗、贫树脂转型和电解,目前已有投入工业生产的报道,然而该工艺中所采用的鳌合型树脂或离子交换树脂价格偏高,如果循环母液中稼的浓度较低,则会造成较高的生产成本,影响进一步推广。石灰乳碳酸化法是在氧化铝碳分母液中通入二氧化碳,进行彻底碳酸化分解,再加石灰乳脱铝,达到稼的富集,此法工艺复杂,形成铝酸钙同时有大量稼损失。此外,电解法因其产品纯度高、生产成本和能耗低、三废污染少等优势已成为目前生产镓的主要方法,所得到纯度大于99.99%的镓在后续的拉晶提纯法中有着良好的可行性。
5.中国专利申请cn101255504a公开了一种从粉煤灰和煤矸石中提取镓的生产工艺,采用吸附柱吸附的方法从含镓氯化铝溶液中提取镓,其使用的含镓氯化铝溶液是将粉煤灰与碳酸钠混合煅烧,经水浸、碳分,再与盐酸反应制得的。cn85100163a公开了一种从氧化铝生产的分解液中提取稼的方法,该方法是向碳酸化分解分离出氢氧化铝以后的母液中通入co2,进行彻底碳酸化分解,稼及铝以无定形水化物的形态进入沉淀,分离沉淀,去除大部分na2o,向沉淀中加入石灰乳脱铝,得到富稼的溶液,再通入co2,生成富稼的沉淀,用氢氧化钠溶解富稼沉淀,并同时加入硫化钠除重金属,制得含稼3.9g/l的电解液;用不锈钢作阴阳极的电解槽电解,在阴极上得到稼,再用盐酸处理,即可生产出纯度为99.99
‑
99.999%的金属稼。cn101284668a公开了一种从高铝粉煤灰中提取二氧化硅、氧化铝及氧化镓的方法,该方法是将粉煤灰提取氧化硅后得到的残渣经处理后得到含镓偏铝酸钠溶液,以此作为分离富集镓的母液,然后采用分步碳分
‑
氢氧化钠溶解法和树脂吸附法进行镓的富集。cn101130835a公开了一种提取镓的生产方法,以粉煤灰生产氧化铝过程中得到的中间产物
碳分母液为原料,经与碳酸氢钠反应和彻底碳酸化后,得到镓精矿。此外,赵毅等报道了“从粉煤灰中分离镓的实验研究”(华北电力技术,1998年,no.1,35
‑
37页),研究表明,将粉煤灰与石灰石烧结、经碳酸钠溶液浸出后得到的含镓偏铝酸钠溶液,可以作为分离富集镓的母液,通过分步碳酸化
‑
氢氧化钠溶解的方法实现镓的提取。
6.上述现有技术的报道均采用煤系固体废弃物提取氧化铝过程中得到的碳分或种分母液为原料进行镓的分离富集,即提取镓的母液均是碱性的含镓偏铝酸钠溶液,这些方法存在工序复杂,镓损失较高等问题。
技术实现要素:
7.针对现有技术中存在的缺陷与不足,本发明提供了一种从煤系固体废弃物中提取金属镓的方法,包括酸溶、共沉淀吸附与富集、碱溶除铁钙镁杂质、分步碳酸化除铝、碱溶以富集镓、电解等工序,最终镓的总回收率高于70%。该方法具有能耗小、设备要求低、除杂效果好且溶剂可循环利用等优点。
8.为了实现上述目的,本发明采用的技术方案为:
9.一种从煤系固体废弃物中提取金属镓的方法,包括以下步骤:
10.(1)将待处理的煤系固体废弃物进行粉碎,采用硝酸加压浸出法得到酸浸液;
11.(2)向所述酸浸液中加入偏锡酸进行共沉淀反应,充分反应后过滤得到除铁后液和含铁、镓的共沉淀渣,对所述共沉淀渣先进行水洗除去大部分铝、钙、镁,再用硝酸酸洗回收铁、镓,得到含铁、镓的吸收液;
12.(3)对所述吸收液进行纳滤膜分离,得到稀硝酸和含铁、镓的富集液,所述稀硝酸返回共沉淀渣酸洗工序;
13.(4)向所述富集液中加入氢氧化钠溶液,除去铁及溶液中少量残留的钙、镁元素,得到含镓的偏铝酸钠溶液;
14.(5)向上述含镓的偏铝酸钠溶液中通入二氧化碳,控制溶液ph值让溶液中的铝、镓分步沉淀,得到粗制氢氧化铝和粗制氢氧化镓;
15.(6)将上述粗制氢氧化镓加入氢氧化钠溶液,得到含镓碱溶液,对所述含镓碱溶液进行电解,得金属镓。
16.进一步的,步骤(1)中将所述煤系固体废弃物粉碎至粒度为0.02
‑
0.1mm。
17.进一步的,步骤(1)中所述硝酸加压浸出法中硝酸溶液的质量浓度为10%
‑
50%,保温温度为150℃以上,保温时间为0.5
‑
5h,搅拌转速为300
‑
700r/min。
18.进一步的,步骤(1)中所述酸浸液的化学元素组成包括:fe为0.1
‑
0.6g/l;al为45.6
‑
78.9g/l;si为0.01
‑
0.15g/l;ca为0.15
‑
2.46g/l;mg为0.01
‑
0.6g/l;ga为0.01
‑
0.2g/l。
19.进一步的,步骤(2)中所述共沉淀反应的ph值为0.5
‑
3.0,温度为20℃
‑
80℃,偏锡酸用量为所述酸浸液质量的1%
‑
10%,保温时间为0.5
‑
3h。需要说明的是,偏锡酸共沉淀吸附铁、镓后,可通过酸洗再生重复利用。
20.进一步的,步骤(2)中偏锡酸共沉淀反应中铁的吸附率为90
‑
99%,镓的吸附率为70
‑
80%;对所述共沉淀渣水洗时铝、钙、镁的洗出率大于90%,铁、镓的洗出率小于5%;对所述共沉淀渣酸洗时铁、镓洗出率大于95%。
21.进一步的,步骤(2)中对所述共沉淀渣水洗的液固比为3
‑
10:1;所述共沉淀渣酸洗的液固比为3
‑
10:1,所用到的硝酸质量浓度为20
‑
60%。
22.进一步的,步骤(3)中所述富集液中镓的质量百分含量为0.05
‑
0.5%。
23.进一步的,步骤(4)中向所述富集液中加入氢氧化钠溶液,控制溶液的ph为13
‑
14,所述氢氧化钠溶液的质量浓度为30%。需要说明的是,该步骤在搅拌下向富集液中加入氢氧化钠溶液,通过控制溶液ph值,让使富集液中的硝酸铝、硝酸镓与氢氧化钠反应生成偏铝酸钠、偏镓酸钠,而溶液中的铁、钙、镁等则以氢氧化物的形式形成沉淀,再经过滤分离、洗涤得到含镓的偏铝酸钠溶液。
24.进一步的,步骤(5)具体包括:
25.一次碳分化:向所述含镓的偏铝酸钠母液中直接通入二氧化碳气体进行碳分化,气体流速为100
‑
200ml/min,确保反应的均匀性,控制反应温度为60
‑
80℃,碳酸化时间为1
‑
5h,反应终点ph为9.5
‑
11.3,反应后绝大部分铝生成氢氧化铝沉淀,镓则留在溶液中,分离出氢氧化铝沉淀后的滤液中镓和铝的质量比大于1:90;
26.二次碳分化:对上述滤液继续通入二氧化碳气体,气体流速为150
‑
250ml/min,控制反应温度为60
‑
80℃,碳分化时间2
‑
5h,反应终点ph为8.5
‑
8.9,使氢氧化铝全部沉淀,镓大部分沉淀,过滤获得铝镓混合盐沉淀,所得滤液进行蒸发、结晶析出碳酸钠晶体,分离碳酸钠后的含镓液返回步骤(4),所述铝镓混合盐中镓和铝的质量比大于1∶50。
27.进一步的,步骤(6)中所述氢氧化钠溶液的质量浓度为15
‑
30%。
28.与现有技术相比,本发明技术方案具有如下技术优势或积极效果:
29.(1)本发明所公开的镓的提取方法适用于各种含镓煤系固体废弃物,原料适用性广泛;
30.(2)本发明采用硝酸加压浸出法直接从原料中浸出镓,保证了镓的浸出率高达90%以上;
31.(3)本发明中镓的总回收率高于70%,最终经电解得到的镓纯度高达99.9%以上;
32.(4)本发明的工艺还具有能耗小、设备要求低、除杂效果好且溶剂可循环利用等优点。
附图说明
33.图1为本发明所述一种从煤系固体废弃物中提取金属镓的方法的工艺流程图。
具体实施方式
34.为使本发明的目的、技术方案和优点更加清楚,下面将对本发明实施方式作进一步地详细描述。
35.【实施例1】
36.将待处理的煤系固体废弃物粉碎至粒度为0.02mm,采用质量浓度为10%的硝酸溶液对原料进行浸出,浸出反应的温度为160℃,保温时间为5h,搅拌转速为300r/min。
37.将得到的酸浸液用偏锡酸共沉淀吸附铁、镓,ph=2、温度20℃、偏锡酸用量2%、保温1h,过滤,得共沉淀渣和除铁后液。
38.对共沉淀前后溶液中铁、铝、钙、镁、镓的含量进行测试,测试结果如表1所示。
39.表1偏锡酸共沉淀前后物质含量测试结果
[0040] 铁(g/l)铝(g/l)镁(g/l)钙(g/l)镓(g/l)酸浸液0.2756.654.050.380.0062除铁后液0.01254.363.810.340.0019
[0041]
将得到的共沉淀渣先水洗后酸洗洗脱再生,水洗液固比10:1,常温搅洗1h,过滤,得水洗渣和水洗液;将水洗渣在液固比10:1,硝酸质量浓度30%,常温搅洗1h,过滤,得酸洗渣和酸洗液。
[0042]
对水洗液和酸洗液中铁、铝、钙、镁、镓的含量进行测试,测试结果如表2所示。
[0043]
表2共沉淀渣洗液中物质含量测试结果
[0044] 铁(g/l)铝(g/l)镁(g/l)钙(g/l)镓(g/l)水洗液0.0477.810.920.560.001酸洗液2.580.720.080.0470.021
[0045]
对酸洗液进行膜过滤,此处采用纳滤膜,膜过滤后溶液成分见表3。
[0046]
表3纳滤膜处理酸洗水后的物质含量测试结果
[0047] 铁(g/l)铝(g/l)镁(g/l)钙(g/l)镓(g/l)硝酸(%)淡水0.00430.790.0780.0410.000215浓缩液26.58.20.940.460.484.1
[0048]
在65℃下,以100ml/min的速度向100ml偏铝酸钠母液中通入二氧化碳气体,控制反应终点ph为9.5,过滤完成一次碳酸化。对经过一次碳酸化分离出氢氧化铝沉淀后的溶液进行二次碳酸化,在50℃下以120ml/min的速度继续通入二氧化碳气体,控制反应终点ph为8.5,过滤得铝镓混合盐沉淀。经测定,此时铝镓混合盐中的镓和铝质量比为1:45。
[0049]
将上述粗制氢氧化镓加入氢氧化钠溶液,得到含镓碱溶液,对所述含镓碱溶液进行电解,得金属镓。经计算,镓的总回收率为75.6%。
[0050]
【实施例2】
[0051]
将待处理的煤系固体废弃物粉碎至粒度为0.05mm,采用质量浓度为20%的硝酸溶液对原料进行浸出,浸出反应的温度为170℃,保温时间为1.5h,搅拌转速为400r/min。
[0052]
将得到的酸浸液用偏锡酸共沉淀吸附铁、镓,ph=2、温度30℃、偏锡酸用量3%、保温1h,过滤,得共沉淀渣和除铁后液。
[0053]
对共沉淀前后溶液中铁、铝、钙、镁、镓的含量进行测试,测试结果如表1所示。
[0054]
表1偏锡酸共沉淀前后物质含量测试结果
[0055] 铁(g/l)铝(g/l)镁(g/l)钙(g/l)镓(g/l)酸浸液0.2558.654.070.350.0068除铁后液0.00858.363.410.300.0014
[0056]
将得到的共沉淀渣先水洗后酸洗洗脱再生,水洗液固比7:1,常温搅洗1h,过滤,得水洗渣和水洗液;将水洗渣在液固比7:1,硝酸质量浓度35%,常温搅洗1h,过滤,得酸洗渣和酸洗液。
[0057]
对水洗液和酸洗液中铁、铝、钙、镁、镓的含量进行测试,测试结果如表2所示。
[0058]
表2共沉淀渣洗液中物质含量测试结果
[0059] 铁(g/l)铝(g/l)镁(g/l)钙(g/l)镓(g/l)水洗液0.0427.910.980.580.001酸洗液2.650.820.0850.0490.021
[0060]
对酸洗液进行膜过滤,此处采用纳滤膜,膜过滤后溶液成分见表3。
[0061]
表3纳滤膜处理酸洗水后的物质含量测试结果
[0062] 铁(g/l)铝(g/l)镁(g/l)钙(g/l)镓(g/l)硝酸(%)淡水0.00460.780.0880.0480.000312浓缩液24.58.50.950.430.284
[0063]
在65℃下,以100ml/min的速度向100ml偏铝酸钠母液中通入二氧化碳气体,控制反应终点ph为9.5,过滤完成一次碳酸化。对经过一次碳酸化分离出氢氧化铝沉淀后的溶液进行二次碳酸化,在50℃下以120ml/min的速度继续通入二氧化碳气体,控制反应终点ph为8.5,过滤得铝镓混合盐沉淀。经测定,此时铝镓混合盐中的镓和铝质量比为1:50。
[0064]
将上述粗制氢氧化镓加入氢氧化钠溶液,得到含镓碱溶液,对所述含镓碱溶液进行电解,得金属镓。经计算,镓的总回收率为76.6%。
[0065]
【实施例3】
[0066]
将待处理的煤系固体废弃物粉碎至粒度为0.07mm,采用质量浓度为30%的硝酸溶液对原料进行浸出,浸出反应的温度为200℃,保温时间为2.0h,搅拌转速为450r/min。
[0067]
将得到的酸浸液用偏锡酸共沉淀吸附铁、镓,ph=3、温度60℃、偏锡酸用量10%、保温1h,过滤,得共沉淀渣和除铁后液。
[0068]
对共沉淀前后溶液中铁、铝、钙、镁、镓的含量进行测试,测试结果如表1所示。
[0069]
表1偏锡酸共沉淀前后物质含量测试结果
[0070] 铁(g/l)铝(g/l)镁(g/l)钙(g/l)镓(g/l)酸浸液0.2558.654.070.350.0068除铁后液0.00858.363.410.300.0014
[0071]
将得到的共沉淀渣先水洗后酸洗洗脱再生,水洗液固比5:1,常温搅洗1h,过滤,得水洗渣和水洗液;将水洗渣在液固比5:1,硝酸质量浓度40%,常温搅洗1h,过滤,得酸洗渣和酸洗液。
[0072]
对水洗液和酸洗液中铁、铝、钙、镁、镓的含量进行测试,测试结果如表2所示。
[0073]
表2共沉淀渣洗液中物质含量测试结果
[0074]
ꢀꢀ
铁(g/l)铝(g/l)镁(g/l)钙(g/l)镓(g/l)水洗液0.0728.610.990.780.003酸洗液2.650.820.0950.0490.041
[0075]
对酸洗液进行膜过滤,此处采用纳滤膜,膜过滤后溶液成分见表3。
[0076]
表3纳滤膜处理酸洗水后的物质含量测试结果
[0077] 铁(g/l)铝(g/l)镁(g/l)钙(g/l)镓(g/l)硝酸(%)淡水0.00660.950.0980.0680.000618浓缩液27.58.50.930.480.585
[0078]
在65℃下,以100ml/min的速度向100ml偏铝酸钠母液中通入二氧化碳气体,控制
反应终点ph为9.5,过滤完成一次碳酸化。对经过一次碳酸化分离出氢氧化铝沉淀后的溶液进行二次碳酸化,在60℃下以120ml/min的速度继续通入二氧化碳气体,控制反应终点ph为8.5,过滤得铝镓混合盐沉淀。经测定,此时铝镓混合盐中的镓和铝质量比为1:53。
[0079]
将上述粗制氢氧化镓加入氢氧化钠溶液,得到含镓碱溶液,对所述含镓碱溶液进行电解,得金属镓。经计算,镓的总回收率为77.6%。
[0080]
【实施例4】
[0081]
将待处理的煤系固体废弃物粉碎至粒度为0.1mm,采用质量浓度为50%的硝酸溶液对原料进行浸出,浸出反应的温度为210℃,保温时间为0.5h,搅拌转速为700r/min。
[0082]
将得到的酸浸液用偏锡酸共沉淀吸附铁、镓,ph=1、温度80℃、偏锡酸用量10%、保温1h,过滤,得共沉淀渣和除铁后液。
[0083]
对共沉淀前后溶液中铁、铝、钙、镁、镓的含量进行测试,测试结果如表1所示。
[0084]
表1偏锡酸共沉淀前后物质含量测试结果
[0085] 铁(g/l)铝(g/l)镁(g/l)钙(g/l)镓(g/l)酸浸液0.4563.654.970.660.0083除铁后液0.01462.673.830.560.0018
[0086]
将得到的共沉淀渣先水洗后酸洗洗脱再生,水洗液固比5:1,常温搅洗1h,过滤,得水洗渣和水洗液;将水洗渣在液固比5:1,硝酸质量浓度60%,常温搅洗1h,过滤,得酸洗渣和酸洗液。
[0087]
对水洗液和酸洗液中铁、铝、钙、镁、镓的含量进行测试,测试结果如表2所示。
[0088]
表2共沉淀渣洗液中物质含量测试结果
[0089] 铁(g/l)铝(g/l)镁(g/l)钙(g/l)镓(g/l)水洗液0.0728.610.990.780.003酸洗液2.650.820.0950.0490.041
[0090]
对酸洗液进行膜过滤,此处采用纳滤膜,膜过滤后溶液成分见表3。
[0091]
表3纳滤膜处理酸洗水后的物质含量测试结果
[0092] 铁(g/l)铝(g/l)镁(g/l)钙(g/l)镓(g/l)硝酸(%)淡水0.00660.950.0980.0680.000628浓缩液27.58.50.930.480.584.2
[0093]
在65℃下,以100ml/min的速度向100ml偏铝酸钠母液中通入二氧化碳气体,控制反应终点ph为9.5,过滤完成一次碳酸化。对经过一次碳酸化分离出氢氧化铝沉淀后的溶液进行二次碳酸化,在50℃下以120ml/min的速度继续通入二氧化碳气体,控制反应终点ph为8.5,过滤得铝镓混合盐沉淀。经测定,此时铝镓混合盐中的镓和铝质量比为1:56。
[0094]
将上述粗制氢氧化镓加入氢氧化钠溶液,得到含镓碱溶液,对所述含镓碱溶液进行电解,得金属镓。经计算,镓的总回收率为77.9%。
[0095]
以上所述仅为本发明的较佳实施例,并不用以限制本发明,凡在本发明的精神和原则之内,所作的任何修改、等同替换、改进等,均应包含在本发明的保护范围之内。
再多了解一些
本文用于企业家、创业者技术爱好者查询,结果仅供参考。