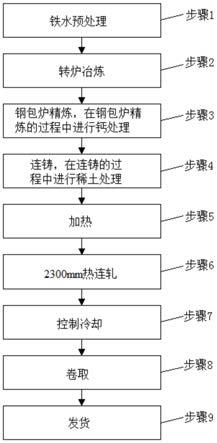
1.本发明涉及耐候钢生产技术领域,尤其涉及一种提高低温冲击韧性的油套管用钢及其制备方法。
背景技术:
2.随着我国石油工业的发展,深井开采所用的油套管对钢材的性能提出了更高的要求,由于特殊的应用领域和使用环境(井下温度一般在
‑
40℃以下,甚至更低),要求钢板具有良好的低温冲击韧性、优良的成形性能、焊接性能和更高的强度等,在钻井过程中油套管起封隔地层和防止井壁坍塌的作用,是一次性消费的钻井管材,油套管因其复杂的使用环境,api spec 5ct对油套管生产及使用有严格的要求。
3.长期以来,国内油套管大部分依赖进口,随着钢的微合金化和控轧控冷技术的发展,高级别的热轧板卷获得了优良的综合性能,九十年代国外开始用热轧板卷制造直缝电阻焊(erw)套管替代传统的无缝钢管,获得了成功,取得了良好的经济效益。据美国石油协会统计,直缝电阻焊套管已占石油套管总量的60%以上,据日本的统计资料,erw 焊接方法生产的套管占70%,其他工业发达国家的直缝电阻焊套管与无缝套管产量比至少为3:7,直缝焊套管的优势主要在于它的几何尺寸精度高、壁厚均匀、在地下服役时其抗挤毁和抗压溃的能力较同钢级无缝套管高10~15%。
4.由于油套管一般在低温环境下使用,用户要求即要具有高强度,又要具有良好的低温冲击韧性、焊接性能和成形性能,随着炼钢工艺技术进步,钢中的氧、氮、氢气和硫、磷含量已经控制到较低的水平,但在钢中仍存在夹杂物超标、成分波动过大现象,这种连铸坯经轧制后会生成连续的、长条状非金属夹杂物缺陷,有的会造成边裂、翘皮等质量问题,这些缺陷对钢的韧性,特别是低温冲击韧性的影响巨大,目前通过消除钢中夹杂物和有害气体的不利影响,改善低温冲击韧性的手段有限。
5.因此,有必要开发一种提高低温冲击韧性的油套管用钢及其制备方法,能够显著提高低温环境下钢的耐冲击韧性。
技术实现要素:
6.本发明旨在解决现有技术或相关技术中存在的技术问题之一。
7.为此本发明提出了一种提高低温冲击韧性的油套管用钢及其制备方法。
8.有鉴于此,本发明的一方面提出了一种提高低温冲击韧性的油套管用钢,所述油套管用钢按质量百分比包括:c:0.03~0.07%,si:0.15~0.30%,mn:1.50~2.0%,s:≤0.005%, p:≤0.010%,al:0.015~0.055%,o:0.0002~0.0010%,n:≤0.0015%,ca:0.0020~0.0040%, nb:0.050~0.10%,ti:0.03~0.06%,cr:0.25~0.45%,ni:0.10~0.30%,cu:0.10~0.50%, nb v ti≤0.15%,re:0.05~0.15%,其余为fe和其他不可避免的杂质,其中,re由ce: 48%,la:32%,pr:5%,nd:5%,pm sm eu gd:8%,其余为fe和其他不可避免的杂质组成。
9.进一步地,所述油套管用钢的厚度为2.0mm至16.0mm。
10.进一步地,所述油套管用钢的抗拉强度700mpa至740mpa,屈服强度640mpa至 670mpa,断后伸长率29%至33%。
11.进一步地,所述制备方法包括如下步骤:铁水预处理
→
转炉冶炼
→
钢包炉精炼
→
连铸
→
加热
→
2300mm热连轧
→
控制冷却
→
卷取
→
发货,其中,在所述钢包炉精炼的过程中进行钙处理,在所述连铸的过程中进行稀土处理。
12.进一步地,所述转炉冶炼采用180吨顶底复吹转炉冶炼,采用滑板挡渣出钢,在出钢过程中脱氧合金化,氧含量严格限制在0.0020%至0.0030%。
13.进一步地,在所述钢包炉精炼包括:钢水到达精炼处理位,底吹氩气搅拌,配加埋弧渣、精炼渣和石灰等,三项电极通电升温10min后,测温、取样,加入合金元素进行调整,根据渣况,配加铝粒和电石造白渣,通电时间大于18min,进行合金成分调整。
14.进一步地,在所述钢包炉精炼处理的过程中进行钙处理包括:对调整后的合金成分进行测温、取样,待所述钢水的成分温度满足目标要求后,喂入钙铁线,所述钙铁线的加入量为400m至500m,喂入所述钙铁线结束后进行软吹氩处理,软吹氩时间≥10min,使夹杂物充分上浮排除。
15.进一步地,所述连铸包括:所述钢水运往板坯连铸机进行浇注,在连铸过程中,根据拉速的不同,设定喂入稀土丝的速度,每吨钢加入所述稀土丝200g至400g,采用结晶器喂入所述稀土丝的方式,保证稀土回收率达到70%以上,过热度控制在10℃至25℃之间,拉速控制在1.0m/min至1.2m/min,所述结晶器二冷水采用中冷模式,气
‑
水喷雾冷却。
16.进一步地,所述加热包括:在步进式加热炉内,将连铸坯加热到1218℃至1242℃,加热时间120min至150min,控制保温时间≥40min。
17.进一步地,所述2300mm热连轧包括粗轧和精轧,其中,中间坯厚度控制在52mm 至58mm,所述粗轧的开轧温度≥1150℃,采用3 5轧制,所述精轧的开轧温度950℃至 990℃,所述精轧的终轧温度840℃至880℃,卷取温度540℃至580℃,压缩比≥5.0以上,所述精轧f1、f2道次压下率≥40%,其余各道次压下率控制在25%至35%。
18.本发明的实施例提供的技术方案可以包括以下有益效果:
19.通过钙处理和稀土处理,使钢中夹杂物充分上浮排除,在钢中起到变质夹杂、冶金控制、细晶强化以及纯净钢水的作用,消除钢中夹杂物有害作用,最终在钢中形成细小、均匀及弥散分布的稀土、钙的硫化物((ca、re)s)、稀土、钙的氧化物((ca、re) o)或稀土、钙的复合氧硫化物((ca、re)(o、s))的复合化合物等,呈球状、点状分布,该分布有效地提高了油套管的低温冲击韧性。
20.应当理解的是,以上的一般描述和后文的细节描述仅是示例性和解释性的,并不能限制本发明。
附图说明
21.此处的附图被并入说明书中并构成本说明书的一部分,示出了符合本发明的实施例,并与说明书一起用于解释本发明的原理。
22.为了更清楚地说明本发明实施例或现有技术中的技术方案,下面将对实施例或现有技术描述中所需要使用的附图作简单地介绍,显而易见地,对于本领域普通技术人员而
言,在不付出创造性劳动的前提下,还可以根据这些附图获得其他的附图。
23.图1示出了根据本发明一个实施例的提高低温冲击韧性的油套管用钢制备方法的流程示意图;
24.图2示出了根据本发明一个实施例的8mm厚钢板的金相组织示意图;
25.图3示出了图2的典型的非金属夹杂物级别;
26.图4示出了现有技术的8mm厚钢板的金相组织示意图;
27.图5示出了图4的非金属夹杂物级别;
28.图6示出了本发明的一个实施例的8.0mm厚钢板在
‑
60℃冲击断口sem形貌;
29.图7示出了本发明的一个实施例的8.0mm厚钢板在
‑
80℃冲击断口sem形貌;
30.图8示出了本发明的一个实施例的8.0mm厚钢板在
‑
100℃冲击断口sem形貌。
具体实施方式
31.这里将详细地对示例性实施例进行说明,其示例表示在附图中。下面的描述涉及附图时,除非另有表示,不同附图中的相同数字表示相同或相似的要素。以下示例性实施例中所描述的实施方式并不代表与本发明相一致的所有实施方式。相反,它们仅是与如所附权利要求书中所详述的、本发明的一些方面相一致的装置和方法的例子。
32.实施例1
33.本实施例提出了一种提高低温冲击韧性的油套管用钢,该油套管用钢按质量百分比包括:c:0.03~0.07%,si:0.15~0.30%,mn:1.50~2.0%,s:≤0.005%,p:≤0.010%, al:0.015~0.055%,o:0.0002~0.0010%,n:≤0.0015%,ca:0.0020~0.0040%,nb: 0.050~0.10%,ti:0.03~0.06%,cr:0.25~0.45%,ni:0.10~0.30%,cu:0.10~0.50%, nb v ti≤0.15%,re:0.05~0.15%,其余为fe和其他不可避免的杂质,其中,re由ce: 48%,la:32%,pr:5%,nd:5%,pm sm eu gd:8%,其余为fe和其他不可避免的杂质组成。
34.通过钙、稀土两次处理,使夹杂物物充分球化,提高钢板的低温冲击韧性。
35.进一步地,油套管用钢的厚度为2.0mm至16.0mm。
36.需要说明的是,根据用户的使用要求生产不同厚度的油套管用钢。
37.进一步地,油套管用钢的抗拉强度700mpa至740mpa,屈服强度640mpa至670mpa,断后伸长率29%至33%。
38.其中,根据本实施例的化学成分生产出的油套管用钢,在保证具有高强度的同时,还具有优良的韧性。
39.实施例2
40.图1示出了根据本发明一个实施例的提高低温冲击韧性的油套管用钢制备方法的流程示意图。
41.如图1所示,本实施例提供了一种提高低温冲击韧性的油套管用钢制备方法,该制备方法包括如下步骤:
42.步骤1,铁水预处理;
43.步骤2,转炉冶炼;
44.步骤3,钢包炉精炼,在钢包炉精炼的过程中进行钙处理;
45.步骤4,连铸,在连铸的过程中进行稀土处理;
46.步骤5,加热;
47.步骤6,2300mm热连轧;
48.步骤7,控制冷却;
49.步骤8,卷取;
50.步骤9,发货。
51.通过钙处理和稀土处理,利用钙处理、稀土处理促使钢中夹杂物上浮排除,在钢中起到变质夹杂、冶金控制、细晶强化以及纯净钢水的作用,消除钢中夹杂物有害作用,最终在钢中形成细小、均匀及弥散分布的钙、稀土的硫化物((ca、re)s)、钙、稀土的氧化物((ca、re)o)或钙、稀土的氧硫化物((ca、re)(o、s))的复合化合物等,呈球状、点状分布,该分布有效地提高了油套管的低温冲击韧性。
52.进一步地,转炉冶炼采用180吨顶底复吹转炉冶炼,采用滑板挡渣出钢,在出钢过程中脱氧合金化,为提高钢板质量、降低钢中气体含量,将氧含量严格限制在0.0020%至 0.0030%。
53.进一步地,在钢包炉精炼包括:钢水到达精炼处理位,底吹氩气搅拌,配加埋弧渣、精炼渣和石灰等,三项电极通电升温10min后,测温、取样,加入合金元素进行调整,根据渣况,配加铝粒和电石造白渣,通电时间大于18min,进行合金成分调整。
54.具体地,为使钢中夹杂物充分上浮排除,底吹氩气搅拌,为进一步脱硫,配加埋弧渣、精炼渣和石灰等根据化学成分内控标准的要求,加入合金元素进行调整;根据渣况,配加铝粒和电石造白渣,通电时间大于18min,进行合金成分调整,使精炼后钢水的化学成分和温度达到工艺标准要求。
55.进一步地,在钢包炉精炼处理的过程中进行钙处理包括:对调整后的合金成分进行测温、取样,待钢水的成分温度满足目标要求后,喂入钙铁线,钙铁线的加入量为400m 至500m,喂入钙铁线结束后进行软吹氩处理,软吹氩时间≥10min,使夹杂物充分上浮排除。
56.经过钙处理后,钢水成分及其质量百分数在下列范围:c:0.03~0.07%、si: 0.15~0.30%、mn:1.50~2.0%、s:≤0.005%、p:≤0.010%、al:0.015~0.055%、o:0.0002~ 0.0010%,n:≤0.0015%,ca:0.0020~0.0040%;nb:0.050~0.10%,ti:0.03~0.06%, cr:0.25~0.45%,ni:0.10~0.30%,cu:0.10~0.50%;nb v ti≤0.15%,其余为fe和其他不可避免的杂质。
57.进一步地,连铸包括:钢水运往板坯连铸机进行浇注,在连铸过程中,根据拉速的不同,设定喂入稀土丝的速度,每吨钢加入稀土丝200g至400g,采用结晶器喂入稀土丝的方式,保证稀土回收率达到70%以上,过热度控制在10℃至25℃之间,拉速控制在 1.0m/min至1.2m/min,结晶器二冷水采用中冷模式,气
‑
水喷雾冷却。
58.经过稀土处理后,最终使油套管用钢中成分按质量百分数为:c:0.03~0.07%、si: 0.15~0.30%、mn:1.50~2.0%、s:≤0.005%、p:≤0.010%、al:0.015~0.055%、o:0.0002~ 0.0010%,n:≤0.0015%,ca:0.0020~0.0040%;nb:0.050~0.10%,ti:0.03~0.06%, cr:0.25~0.45%,ni:0.10~0.30%,cu:0.10~0.50%;nb v ti≤0.15%,re:0.05~0.15%,其中,稀土含有ce:48%,la:32%,pr:5%,nd:5%,pm sm eu gd:8%,其余为 fe和其他不可避免的杂质组成。
59.需要说明的是,稀土丝为稀土包芯线,根据拉速的不同,稀土包芯线的直径可以选择2.5mm、4.0mm或5.0mm。也就是说,当拉速在1.0m/min时,稀土包芯线的直径为 2.5mm;拉速在1.1m/min至1.2m/min时,稀土包芯线的直径为4.0mm;拉速≥1.3m/min 时,选用稀土包芯线的直径为4.5mm,目的是减少烧损、保证稀土的回收率。
60.进一步地,加热包括:在步进式加热炉内,将连铸坯加热到1218℃至1242℃,加热时间120min至150min,控制保温时间≥40min。
61.具体地,采用步进式加热炉,能够做到运料灵活,坯料在炉底或梁上有间隔地摆开,可较快地均匀加热。其中,炉体分为预热段、加热段、均热段,加热段的两面侧墙上设 5置调焰烧嘴,均热段的上加热段设置平焰烧嘴,均热段的下加热段设置调焰烧嘴,调焰烧嘴的煤气和空气的混合气管道上设置电磁阀和调节阀,平焰烧嘴的煤气和空气的混合气管道上设置调节阀,空气总管道和煤气总管道设置在炉顶。
62.为保证合金元素充分溶解,要求加热时间充分,加热温度均匀,以保证最终产品的质量,确定将连铸坯加热到1218℃至1242℃,加热时间120min至150min,控制保温时间≥40min。
63.进一步地,2300mm热连轧包括粗轧和精轧,其中,中间坯厚度控制在52mm至58mm,粗轧的开轧温度≥1150℃,采用3 5轧制,精轧的开轧温度950℃至990℃,精轧的终轧温度840℃至880℃,卷取温度540℃至580℃,压缩比≥5.0以上,精轧f1、f2道次压下率≥40%,其余各道次压下率控制在25%至35%。
64.通过上述热连轧的方式,能够保证油套管用钢的金相组织、力学性能和成形性能,提高产品质量。
65.进一步地,为了获得均匀、细小的金相组织,保证钢板各向同性,保证钢板头、中、尾性能一致性,避免冷速过快,经过热连轧后的钢板卷取后要求在库内热区进行缓冷(远离库门,围冷避免冷风直吹),32小时后才可进行移动,最终获得组织:铁素体加珠光体、少量贝氏体,相应地,ca、re与s、al、mg和o结合形成均匀、细小、弥散、球状复合夹杂物存在,使非金属夹杂物a类、b类、c类和d类小于等于1.0级,并以点状、球状夹杂物存在于钢中,避免长条状夹杂物对钢性能的危害,从而有效地提高油套管专用钢板的低温(
‑
60℃以下)冲击韧性。
66.经过本发明处理的油套管用钢具有良好的低温冲击韧性和冷弯加工性能,满足后续的加工要求,生产过程具有较高的成品质量和成品率,提高经济性,并能够在现有设备的基础上实现油井管专用钢轻量化设计。
67.实施例3
68.根据上述的配比和加工方法,根据表1和表2中三种油套管用钢的多种参数,进行三种油套管用钢的加工。
69.表1三种油套管用钢化学成分质量百分比
[0070][0071]
续表1三种油套管用钢化学成分质量百分比
[0072][0073]
表2三种油套管用钢的加工工艺参数
[0074]
编号厚度/mmf1开轧温度/℃终轧温度/℃卷取温度/℃a5.0960845545b6.0985862561c8.0985880579
[0075]
根据上述方法加工的三种油套管用钢的力学性能、弯曲性能参数如表3所示。
[0076]
表3三种油套管用钢的力学性能、弯曲性能参数
[0077]
编号屈服强度/mpa抗拉强度/mpa延伸率a50(%)180
°
冷弯实验a66573132.5完好b65072230完好c64070129.5完好
[0078]
上述化学成分和加工方法获得的油套管用钢完全符合使用要求。
[0079]
需要说明的是,最终化学成分除稀土外,与前面是一致地,而ce、la、pr、nd、 pm sm eu gd都属于稀土元素。
[0080]
对比例1
[0081]
图2示出了根据本发明一个实施例的8mm厚钢板的金相组织示意图;图3示出了图 2的典型的非金属夹杂物级别。
[0082]
如图2和图3所示,采用实施例2的方法生产的油套管专用钢板的金相组织为铁素体 珠光体 贝氏体,从夹杂物及能谱分析可以看出,钢中b类夹杂物为0.5级,钢中夹杂物以ca、re与s、al、mg和o结合形成均匀、细小、弥散、球状复合夹杂物存在,有效地提高油套罐专用钢的冲击性能。
[0083]
图4示出了现有技术的8mm厚钢板的金相组织示意图;图5示出了图4的非金属夹杂物级别。
[0084]
如图4和图5所示,未经过净化处理的钢板,钢板的金相组织为:铁素体 珠光体,钢中的非金属夹杂物为:a1.5b2.0d0.5,非金属夹杂物严重,对钢板的成形性能、冲击性能造成不利影响。
[0085]
对比例2
[0086]
对钢板性的冲击性能进行测试,在钢板的横、纵向分别取v型缺口冲击试样进行测试,未进行钙处理和稀土处理的与进行钙处理和稀土处理的样品的冲击性能如表4所示。
[0087]
表4横、纵向冲击性能对比表
[0088][0089]
从表4中可以看出,经过两次净化处理后,钢板在
‑
60℃时,横向冲击功的数值是未进行钙、稀土处理的1.7倍,纵向冲击功相当;钢板的温度降低到
‑
80℃时,横向冲击功的数值是未进行钙、稀土处理的1.6倍,而纵向冲击功是1.4倍;钢板的温度进一步降低到
‑
100℃,横向冲击功的数值是未进行钙、稀土处理的3倍,纵向冲击功是2倍。说明经过两次净化处理的钢板,其低温韧性明显好于未经处理的钢板。
[0090]
图6示出了本发明的一个实施例的8.0mm厚钢板在
‑
60℃冲击断口sem形貌;图7 示出了本发明的一个实施例的8.0mm厚钢板在
‑
80℃冲击断口sem形貌;图8示出了本发明的一个实施例的8.0mm厚钢板在
‑
100℃冲击断口sem形貌。
[0091]
通过透射电镜观察,如图6至图8可以看出,冲击试样在
‑
60℃的断口形貌呈现较深的等轴韧窝,说明在断裂前经历了很大的塑性变形;在
‑
80℃时,断口形貌仍为韧窝断口,只是较前者韧窝浅平粗大,说明在此温度下仍是韧性断裂,所以可以判断在
‑
80℃以上为韧性断裂;当温度降低至
‑
100℃时,断口形貌呈现明显的完全解理花样,证明断裂达到完全的脆性断裂,表明深井开采用油套管专用钢的低温韧脆转变温度在
‑
80℃至
‑
100℃之间,可以满足在恶劣的低温条件下的使用要求。
[0092]
本领域技术人员在考虑说明书及实践这里公开的发明后,将容易想到本发明的其它实施方案。本技术旨在涵盖本发明的任何变型、用途或者适应性变化,这些变型、用途或者适应性变化遵循本发明的一般性原理并包括本发明未公开的本技术领域中的公知常识或惯用技术手段。说明书和实施例仅被视为示例性的,本发明的真正范围和精神由下面的权利要求指出。
[0093]
应当理解的是,本发明并不局限于上面已经描述的内容,并且可以在不脱离其范围进行各种修改和改变。本发明的范围仅由所附的权利要求来限制。
再多了解一些
本文用于企业家、创业者技术爱好者查询,结果仅供参考。