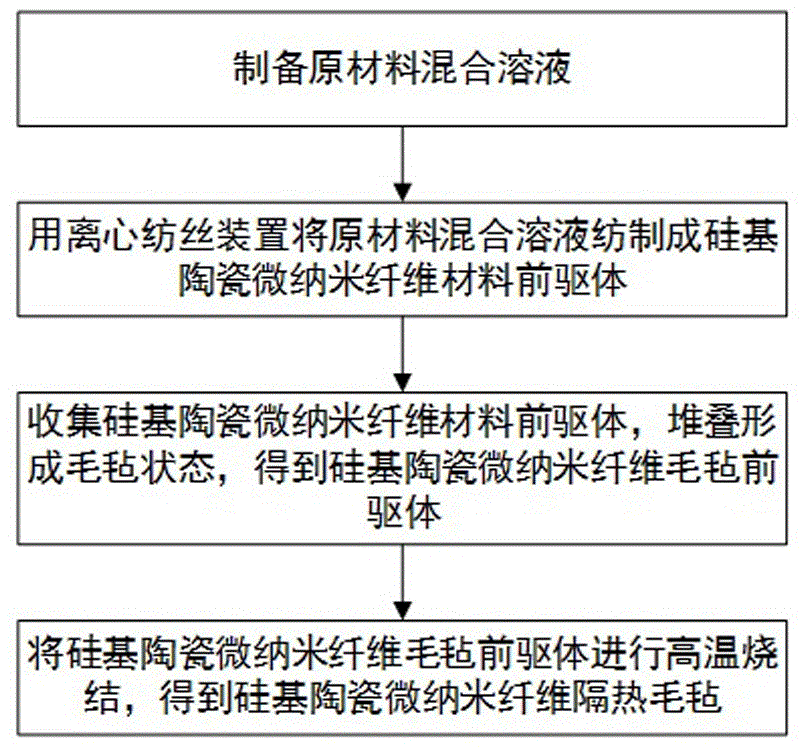
本发明涉及材料科学与工程领域,主要涉及一种硅基陶瓷微纳米纤维隔热毛毡及其制备方法。
背景技术:
用于建筑领域的隔热材料可分为无机绝热材料和有机绝热材料。有机绝热材料的耐高热性能差,遇明火后会分解,释放出大量的热和有毒气体,而且在应用过程中还会散发出甲醛等有害气体。相对于有机绝热材料,无机绝热材料的耐高温性能强,热化学性能相对稳定。出于安全生产生活以及环保考虑,有机绝热材料正逐步被无机绝热材料替代。目前市场常见的无机绝热材料,如岩棉、玻璃棉、硅酸铝纤维、石棉等短纤维材料,纤维横截面直径都只是微米级,都需要添加酚醛树脂类或脲醛树脂等有机粘结剂,再通过热定型制备。
目前市场中的无机绝热材料普遍存在以下问题:1、短纤维材料必须添加有机粘结剂,再通过热定型来增强其机械强度;2、材料中含有的树脂类有机粘结剂会释放出甲醛等气体,危害人体健康;3、材料中含有的有机粘结剂在遇高温或明火(火灾等情况)后分解,同时释放出大量的热和有毒气体;4、材料中粘结剂分解后,材料会变得松散,易脱落,不利于安全生产生活;5、目前生产制备出来的短纤维隔热材料,必须经过短切弹松工艺处理,制作工艺繁琐;6、横截面直径微米级的纤维隔热材料密度大、孔隙率低,导致材料导热系数高,隔热效果差。
因此,现有技术还有待于改进和发展。
技术实现要素:
鉴于上述现有技术的不足,本发明的目的在于提供一种硅基陶瓷微纳米纤维隔热毛毡及其制备方法,旨在解决现有现有无机绝热材料需要粘结剂的问题。
本发明的技术方案如下:
一种硅基陶瓷微纳米纤维隔热毛毡的制备方法,其中,包括以下步骤:
步骤一:制备原材料混合溶液,所述原材料混合溶液中包括有机盐、高分子聚合物以及溶剂;
步骤二:用离心纺丝装置将原材料混合溶液纺制成硅基陶瓷微纳米纤维材料前驱体;
步骤三:收集硅基陶瓷微纳米纤维材料前驱体,堆叠形成毛毡状态,得到硅基陶瓷微纳米纤维毛毡前驱体;
步骤四:将硅基陶瓷微纳米纤维毛毡前驱体进行高温烧结,得到硅基陶瓷微纳米纤维隔热毛毡。
所述的硅基陶瓷微纳米纤维隔热毛毡的制备方法,其中,所述有机盐为硅酸四乙酯加上四氯化锡或钛酸四丁酯中的至少一种,硅酸四乙酯与四氯化锡或钛酸四丁酯的质量比为1:0.2~0.5。
所述的硅基陶瓷微纳米纤维隔热毛毡的制备方法,其中,原材料混合溶液中有机盐与溶剂的质量比为1.2~3:5~11;高分子聚合物占原材料混合溶液总重量的6~30%。
所述的硅基陶瓷微纳米纤维隔热毛毡的制备方法,其中,所述原材料混合溶液中,还包括纳米氧化石墨烯片和液态硅酸钠;所述纳米氧化石墨烯片占有机盐重量的3~5%,液态硅酸钠占有机盐重量的2~3%。
所述的硅基陶瓷微纳米纤维隔热毛毡的制备方法,其中,所述原材料混合溶液中,还包括醋酸,有机盐与醋酸的质量比为1.2~3:0.01。
所述的硅基陶瓷微纳米纤维隔热毛毡的制备方法,其中,所述高分子聚合物采用peo、pva、pan中的至少一种;溶剂采用水、无水乙醇、乙腈、丙酮、二甲基酰胺中的至少一种。
所述的硅基陶瓷微纳米纤维隔热毛毡的制备方法,其中,离心纺丝装置的纺制过程中,机电转速设置为4000-10000rpm,细孔针头的孔径为0.1-0.4mm,收集装置的收集距离为30-50cm。
所述的硅基陶瓷微纳米纤维隔热毛毡的制备方法,其中,所述堆叠的方式可以为卷绕堆叠或之字形堆叠。
所述的硅基陶瓷微纳米纤维隔热毛毡的制备方法,其中,所述烧结过程为,温度以2℃/min的升温速率,从50上℃升至1000℃,并在1000℃环境保持烧结1h,然后以5℃/min的降温速率,从1000℃降至50℃。
一种硅基陶瓷微纳米纤维隔热毛毡,其中,采用如上所述的硅基陶瓷微纳米纤维隔热毛毡的制备方法制备得到。
有益效果:本发明所提供的硅基陶瓷微纳米纤维隔热毛毡的制备方法,具有快速高效、绿色节能、成本低廉、易于大批量工业化生产等特点,克服了现有技术中制备困难、产量低、能耗大、原材料需求量大等缺点。而且,采用本发明方法制备得到的硅基陶瓷微纳米纤维隔热毛毡具有密度低,耐高温等特点,可以用于保温隔热领域。
附图说明
图1是本发明中硅基陶瓷微纳米纤维毛毡的制备方法流程示意图。
图2是本发明中的通过硅基陶瓷微纳米纤维毛毡原材料溶液制备硅基陶瓷微纳米纤维毛毡前驱体的过程示意图。
图3是本发明实施例的单层硅基陶瓷微纳米纤维的实物图。
图4是本发明实施例1的硅基陶瓷微纳米纤维前驱体的sem图。
图5是本发明实施例1的硅基陶瓷微纳米纤维毛毡前驱体的实物图。
图6是本发明实施例1的硅基陶瓷微纳米纤维毛毡的实物图。
图7是本发明实施例1的硅基陶瓷微纳米纤维的sem图。
具体实施方式
本发明提供一种硅基陶瓷微纳米纤维隔热毛毡及其制备方法,为使本发明的目的、技术方案及效果更加清楚、明确,以下对本发明进一步详细说明。应当理解,此处所描述的具体实施例仅仅用以解释本发明,并不用于限定本发明。
下文的公开提供了许多不同的实施方式或例子用来实现本发明的不同结构。为了简化本发明的公开,下文中对特定例子的部件和设置进行描述。当然,它们仅仅为示例,并且目的不在于限制本发明。此外,本发明可以在不同例子中重复参考数字和/或参考字母,这种重复是为了简化和清楚的目的,其本身不指示所讨论各种实施方式和/或设置之间的关系。此外,本发明提供了的各种特定的工艺和材料的例子,但是本领域普通技术人员可以意识到其他工艺的应用和/或其他材料的使用。
离心纺丝法作为一种制备微纳米纤维的方法,具有高产量、低能耗、低成本、适用范围广泛等优势,很容易实现工业化生产。目前离心纺丝法制备微纳米纤维的原材料主要集中在高分子聚合物、金属材料以及碳材料等方面,主要用于生物医药、纳米传感器以及环境污染处理等领域。离心纺丝法制备出来的微纳米纤维材料具有蓬松、多孔、超轻等特性,天然符合超级隔热材料的物理结构特性。基于离心纺丝法制备的微纳米纤维材料的这种结构特性,发明人通过深入研究,发现利用离心纺丝技术可以制备硅基陶瓷微纳米纤维材料前驱体,将该前驱体进行堆叠,形成毛毡状态的硅基陶瓷微纳米纤维前驱体材料,再经过高温煅烧获得由硅基陶瓷微纳米纤维组成的三维弹性毛毡,具有耐高温、弹性好、毛毡纤维结构牢固稳定、不易碎、不掉粉等特点。
具体地,如图1所示,本发明提供一种硅基陶瓷微纳米纤维隔热毛毡的制备方法,包括以下步骤:
步骤一:制备原材料混合溶液,所述原材料混合溶液中包括有机盐、高分子聚合物以及溶剂。
在该步骤中,需要将硅基陶瓷微纳米纤维隔热毛毡对应的有机盐配制成具有可纺性的混合溶液。在制备溶液过程中,需要选择合适的溶剂将有机盐进行溶解;同时,需要加入高分子聚合物,增加混合溶液的粘度,使得溶液具备可纺性;另外,根据需要,还需要增加表面活性剂等溶剂用于改善混合溶液的内置属性。在本发明优选实施例方案中,所述原材料混合溶液中,还包括醋酸,有机盐与醋酸的质量比为1.2~3:0.01,醋酸用作有机盐催化剂和胶体稳定剂,使原料混合溶液中的液态有机盐能够充分水解,并与高分子聚合物溶液均匀混合,从而提高溶液可纺性。
其中,所述有机盐可以为硅酸四乙酯加上四氯化锡或钛酸四丁酯中的至少一种。在本发明优选实施例方案中,硅酸四乙酯与四氯化锡或钛酸四丁酯的质量比为1:0.2~0.5。采用硅酸四乙酯加上四氯化锡,或,硅酸四乙酯加上钛酸四丁酯的有机盐的混合溶液经过离心纺丝,堆叠成毛毡后进行煅烧,得到的硅基陶瓷微纳米纤维毛毡是三维结构,具有耐高温、弹性好、毛毡纤维结构牢固稳定、不易碎、不掉粉等特点。
在本发明中,硅基陶瓷微纳米纤维毛毡原材料混合溶液必须具有良好的可纺性才能利用离心纺丝设备将溶液纺制成纤维,因此原材料混合溶液中需要添加高分子聚合物,使其具备可纺性。在本发明实施例方案中,采用的高分子聚合物不受限制,只要能够使原材料混合溶液具有可纺性即可。在本发明的一些具体实例中,所述高分子聚合物可以采用peo、pva和pan中的至少一种。添加高分子聚合物后,原材料混合溶液具有一定的粘度和可纺性,有利于后续步骤得以进行,并收集到性能优异的硅基陶瓷微纳米纤维。
在本发明中,原材料混合溶液中需要选择合适的溶剂溶解有机盐和高分子聚合物,以此能够获得充分溶解的、具有可纺性的原材料混合溶液。根据本发明的实施例,采用的溶剂种类不受具体限制,本领域技术人员可以根据实际需要进行选择和调配。在本发明实施例方案中,溶剂可采用水、无水乙醇、乙腈、丙酮和二甲基酰胺(dmf)中的至少一种作为溶剂,来促使不同的溶质完全溶解在混合溶液中。在本发明中,原材料混合溶液中溶剂的含量和种类不受具体限制,只要能够满足可纺性要求即可。本发明的实施例中所用的溶剂优选为具有一定的挥发性,使得混合溶液在经过离心纺丝制备纤维的过程中能够迅速的挥发,从而得到固体纤维。
在本发明方案中,原材料混合溶液中溶质的浓度不受具体限制,只要能够满足可纺性要求即可,本领域技术人员可以根据实际需求灵活选择。在本发明实施例方案中,原材料混合溶液中的有机盐的质量百分比一般不超过40%,高分子聚合物的质量百分比一般不超过35%。
优选地,原材料混合溶液中有机盐与溶剂的质量比为1.2~3:5~11;高分子聚合物占原材料混合溶液总重量的6~30%。
更进一步地,所述原材料混合溶液中,还包括纳米氧化石墨烯片和液态硅酸钠;所述纳米氧化石墨烯片占有机盐重量的3~5%,液态硅酸钠占有机盐重量的2~3%。通过原材料混合溶液中添加纳米氧化石墨烯片,经过纺制和烧结后纳米氧化石墨烯片会成为石墨烯纤维分布在毛毡纤维结构中,大大提高了隔热毛毡的韧性和强度,进一步改善其脆性和提高其稳定性,使得毛毡纤维网络完整,具有柔性,不掉粉。
在本发明方案中,可以通过机械搅拌、磁力搅拌和超声等方式将加入的溶剂和溶质搅拌均匀即可获得原材料混合溶液,原材料混合溶液的制备和加料不受特别限制。
步骤二:利用离心纺丝装置将原材料混合溶液纺制成硅基陶瓷微纳米纤维材料前驱体。
在该步骤中,将原材料混合溶液倒入离心纺丝装置的储液罐1中,利用电机驱动储液罐高速旋转产生巨大的离心力,混合溶液在离心力的驱动下通过安装在储液罐上的细孔针头2喷出溶液丝3并拉伸形成纤维4并被收集器5收集,如图2所示。相比较于现有的静电纺丝法、化学液相法、气流纺丝法、模板法等纤维制备方法,本发明中使用的离心纺丝法具有生产效率高、溶剂使用率高、能源消耗低、安全性好等优势,很容易实现工业化生产。
在本发明方案中,利用离心纺丝装置将原材料混合溶液纺制成硅基陶瓷微纳米纤维材料前驱体的过程可以具体的分为三个阶段:阶段一,溶液丝形成的初始阶段;阶段二,溶液丝拉伸阶段;阶段三,溶剂挥发阶段。阶段一,在离心力的驱动下,溶液从储液罐中心位置朝着法向力方向流动,迅速进入细孔针头,在细孔针头里同时受到离心力、溶液黏力和溶液表面张力等共同力的作用下从针头的喷丝口喷出。阶段二,喷出的溶液丝会随着高速旋转的储液罐共同旋转,对溶液丝形成巨大的拉伸力。溶液丝在拉伸力,惯性力,空气阻力以及弹性黏力的共同力作用下超法向力方向继续飞出,并被该共同力迅速拉伸,使得溶液丝迅速变细。阶段三,溶液丝被拉伸并迅速变细后,溶液丝的比表面积大大增加,使得溶剂的挥发速率迅速提高,溶剂挥发后,最终形成固态的微纳米纤维,参考图3和图4。
在本发明方案中,离心纺丝装置所用的电机具体类型不受具体的限制,只要能够提供足够的转速来驱动储液罐高速旋转即可,在此不再赘述。机电转速的范围一般在4000-10000rpm,为了能够获得纤维直径分布均匀且连续的硅基陶瓷微纳米纤维材料前驱体,电机的转速需要持续稳定在转速范围内的某个固定值。控制电机的转速值的大小可以与溶液粘度、针头形态等相配合,使得溶液丝能够均匀稳定的喷出,形成微纳米纤维。
在本发明方案中,储液罐上装有的细孔针头的类型、长短、孔径大小、截面形状不受具体限制,只要能够使得溶液丝能够从针头的喷丝口喷出即可。在本发明方案中,细孔针头可以是尖口针头、扁口针头、平口针头或弯管针头等,本领域技术人员可以根据实际条件进行选择。在本发明实施例方案中,所述细孔针头的孔径为0.1-0.4mm,以确保可纺性溶液被喷射出来的初始弹性溶液丝的截面直径足够小,最终能够得到微纳米级别的超细纤维。
所述收集装置的收集距离为30-50cm。所述收集距离是指细孔针头与收集器之间的距离,采用此收集距离的好处是有足够的时间使得喷出的弹性溶液丝中的溶剂挥发,收集得到干燥的固体微纳米纤维材料。如果溶剂没有来得及完全挥发,收集到的将还是溶液,最后形成的是一层膜,而不是固体微纳米纤维。
在本发明方案中,原材料混合溶液注入储液罐后,溶液的供给速率受电机转速、溶液粘度、细孔针头孔径大小等因素的共同影响。一般情况下,溶液的供给速率基本可以达到1ml/min以上,本领域的技术人员可以由此判断出,离心纺丝法的溶液供给速率相比于静电纺丝法和气流纺丝法的溶液供给速率要高很多,因此离心纺丝法制备微纳米纤维的生产效率要高,更容易实现工业化生产。
在本发明方案中,收集硅基陶瓷微纳米纤维材料前驱体的收集器的形状不受特别限制,本领域技术人员可根据实际需求对收集器的形状结构进行选择。
步骤三:将收集得到的硅基陶瓷微纳米纤维材料前驱体进行堆叠,形成毛毡状态,得到硅基陶瓷微纳米纤维毛毡前驱体。
在该步骤中,将收集得到的如图3所示的单层硅基陶瓷微纳米纤维材料前驱体进行堆叠,形成毛毡状态(如图5所示),得到硅基陶瓷微纳米纤维毛毡前驱体。
所述堆叠的方式可以为卷绕堆叠或之字形堆叠等等。优选地,在本发明方案中,采用卷绕堆叠的方式,可以提高毛毡的整体结构稳定性,且可以通过控制卷绕的速度来得到不同密度的毛毡,免去按压定型工艺流程。
在本发明方案中,在烧结前对单层的硅基陶瓷微纳米纤维材料前驱体进行堆叠加工处理,有助于得到的硅基陶瓷微纳米纤维毛毡前驱体的整体结构,相对于烧结后再堆叠形成毛毡的整体结构更加稳定,不易出现整层纤维脱落的现象。
步骤四:将硅基陶瓷微纳米纤维毛毡前驱体进行高温烧结,得到硅基陶瓷微纳米纤维隔热毛毡。
在该步骤中,硅基陶瓷微纳米纤维毛毡前驱体移动到管式炉中进行烧结,烧结过程中,高分子聚合物被去除,有机盐经过高温煅烧发生氧化反应,转化成为硅基氧化物,获得硅基陶瓷微纳米纤维材料毛毡,参考图6和图7。
在本发明方案中,烧结温度、时间、升温速率和降温速率不受特别限制,针对不同有机盐和高分子聚合物的质量百分比,本领域技术人员可以根据实际情况进行调整,只要能够将高分子聚合物完全去除,并将有机盐完全转化为硅基陶瓷纤维材料即可。本发明实施例方案中,烧结的温度可以以2℃/min的升温速率,从50上℃升至1000℃,并在1000℃环境保持烧结1h,然后以5℃/min的降温速率,从1000℃降至50℃,最终获得具有弹性性能的超轻硅基陶瓷微纳米纤维隔热毛毡。
本发明中还提供一种硅基陶瓷微纳米纤维隔热毛毡,所述硅基陶瓷微纳米纤维隔热毛毡采用如上所述的制备方法制备得到。
综上所述,第一方面,本发明提出了一种硅基陶瓷微纳米纤维隔热毛毡的制备方法,该方法能够批量生产出可回弹的、超轻的、耐高温的、不易碎的、低成本的硅基陶瓷微纳米纤维隔热材料。该制备方法具有效率高、能耗低、操作简单等特点,具有工业化批量生产的潜力。第二方面,本发明提出了一种硅基陶瓷微纳米纤维隔热毛毡。该硅基陶瓷微纳米纤维隔热毛毡是由上述方法制备的。所述硅基陶瓷微纳米纤维隔热毛毡具有低密度、耐高温、可回弹等性能的三维结构,适用于包括建筑隔热在内的多个领域。
下面详细描述本发明的实施例,实施例中未注明具体技术或条件的,按照本领域内的文献所描述的技术条件或者按照产品说明书进行。实施例中所用的材料和仪器没注明生产厂家,均为可以通过市场购买的常规产品。
实施例1
在该实施例中,具体的制备方法为:首先制备原材料混合溶液,先将硅酸四乙酯、钛酸四丁酯、水、醋酸按照质量比为1:0.5:9:0.01的比例在密封瓶中混合均匀,再将peo粉末颗粒加入到混合均匀的溶液中继续密封搅拌8小时,原材料混合溶液中的peo的质量百分比为6%,再加入纳米氧化石墨烯片和液态硅酸钠,所述纳米氧化石墨烯片占有机盐重量的3%,液态硅酸钠占有机盐重量的2%。抽取一定量的均匀的原材料混合溶液注入储液罐中,控制电机驱动的转速至4000rpm,利用储液罐高速的转动产生的离心力将溶液从储液罐上装有的细小针头喷出,被喷出的溶液在空中被迅速拉伸形成粘稠的溶液丝,溶液丝中的溶剂迅速挥发后形成微纳米纤维,并收集在距离针头喷嘴35cm处的收集柱上,微纳米纤维相互缠绕堆叠组成层状的毛毡前驱体,如图3和图4所示。最后,将收集得到的硅基有机盐/peo微纳米纤维毛毡前驱体放入管式炉中烧结,以5℃/min的升温速率至1000℃,并在1000℃的条件下保持1小时,然后以10℃/min的降温速率至50℃。经过烧结后得到的材料为硅基陶瓷微纳米纤维毛毡,如图6和图7所示。
最终得到的硅基陶瓷微纳米纤维毛毡材料的热导率:0.026-0.036(w/m·k),密度:21-116mg/cm3,压缩形变最大值90%。
实施例2
在该实施例中,具体的制备方法为:首先制备原材料混合溶液,先将硅酸四乙酯、四氯化锡、水、醋酸按照质量比为1:0.3:11:0.01的比例在密封瓶中混合均匀,再将peo粉末颗粒加入到混合均匀的溶液中继续密封搅拌8小时,原材料混合溶液中的peo的质量百分比为8%,再加入纳米氧化石墨烯片和液态硅酸钠,所述纳米氧化石墨烯片占有机盐重量的4%,液态硅酸钠占有机盐重量的3%。抽取一定量的均匀的原材料混合溶液注入储液罐中,控制电机驱动的转速至8000rpm,利用储液罐高速的转动产生的离心力将溶液从储液罐上装有的细小针头喷出,被喷出的溶液在空中被迅速拉伸形成粘稠的溶液丝,溶液丝中的溶剂迅速挥发后形成微纳米纤维,并收集在距离针头喷嘴50cm处的收集柱上,微纳米纤维相互缠绕堆叠组成层状的毛毡前驱体。最后,将收集得到的硅基有机盐/peo微纳米纤维毛毡前驱体放入管式炉中烧结,以5℃/min的升温速率至1000℃,并在1000℃的条件下保持1小时,然后以10℃/min的降温速率至50℃。经过烧结后得到的材料为硅基陶瓷微纳米纤维毛毡。
最终得到的硅基陶瓷微纳米纤维毛毡材料的热导率:0.026-0.036(w/m·k),密度:21-116mg/cm3,压缩形变最大值90%。
实施例3
在该实施例中,具体的制备方法为:首先制备原材料混合溶液,先将硅酸四乙酯、水、乙醇、醋酸按照质量比为1:0.2:11:1:0.01的比例在密封瓶中混合均匀,再将pva粉末颗粒加入到混合均匀的溶液中,在80℃的水浴条件下,继续密封搅拌2小时,原材料混合溶液中的pva的质量百分比为30%,再加入纳米氧化石墨烯片和液态硅酸钠,所述纳米氧化石墨烯片占有机盐重量的4%,液态硅酸钠占有机盐重量的5%。抽取一定量的均匀的原材料混合溶液注入储液罐中,控制电机驱动的转速至8000rpm,利用储液罐高速的转动产生的离心力将溶液从储液罐上装有的细小针头喷出,被喷出的溶液在空中被迅速拉伸形成粘稠的溶液丝,溶液丝中的溶剂迅速挥发后形成微纳米纤维,并收集在距离针头喷嘴50cm处的收集柱上,微纳米纤维相互缠绕堆叠组成层状的毛毡前驱体。最后,将收集得到的硅基有机盐/pva微纳米纤维毛毡前驱体放入管式炉中烧结,以4℃/min的升温速率至1000℃,并在1000℃的条件下保持1小时,然后以10℃/min的降温速率至室温。经过烧结后得到的材料为硅基陶瓷微纳米纤维毛毡。
最终得到的硅基陶瓷微纳米纤维毛毡材料的热导率:0.026-0.036(w/m·k),密度:21-116mg/cm3,压缩形变最大值90%。
应当理解的是,本发明的应用不限于上述的举例,对本领域普通技术人员来说,可以根据上述说明加以改进或变换,所有这些改进和变换都应属于本发明所附权利要求的保护范围。
本文用于企业家、创业者技术爱好者查询,结果仅供参考。