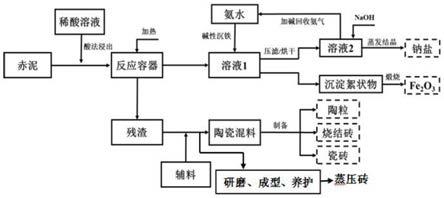
1.本发明属于赤泥资源化技术流域,具体涉及一种拜耳法赤泥综合利用方法,特别适合于al2o3 sio2 tio2 cao mgo含量在48.0~68.0%、fe2o3含量25.0~42.0%、na2o含量4.0~10.0%、其它组份含量在1.0~5.0%的拜耳法赤泥的全量化资源利用。
背景技术:
2.赤泥是铝土矿经过高浓度naoh溶液浸出其中的al后产生的大宗工业废渣。具体的流程为:在高温高压的实验条件下,铝土矿中的al2o3会与naoh溶液发生反应,生成铝酸钠。生成铝酸钠的同时,铝土矿中的其他组分,如sio2、fe2o3、tio2氧化物等则并不会与碱发生反应。将上述在naoh溶液中不溶的、仍以固体形式存在的固体物分离出来,即得到了赤泥。在固液分离的过程中,仍然会有一部分naoh溶液会随着固体物分离出来,因此,最终获得到的废弃物通常为呈泥浆状的流体,并且,由于其中含有稍过量的fe2o3,这些废弃物通常呈现出暗红色或砖红色,故称为赤泥。
3.赤泥是综合利用率较低的工业固体废弃物,其资源属性受到广泛关注,但赤泥的回收利用一直是氧化铝行业面临的难题和技术难关。据文献报道,每生产1吨的al2o3时,需要产生1.5~2.0吨左右的赤泥。中国作为世界第一大氧化铝生产国,每年排放的赤泥近亿吨,累积堆存的赤泥已经超过了13亿吨。赤泥中fe2o3等的含量一般较高,此外还含有4
‑
10%的na2o。赤泥的大量堆存不仅占用大量土地,对环境造成严重污染,也造成市场中缺口较大的铝土矿资源的严重浪费;另外,现在国内外铝厂对于赤泥的处理,大多采用的都是输送堆场、筑坝湿法堆存或者干法堆存,而赤泥中的含碱废液会对地表及地下水源造成污染,进而严重地破坏生态自然环境。综上所述,充分且合理地回收赤泥中的fe2o3及na2o,并利用其尾渣制备建筑材料,有效实现赤泥的梯级全量化利用,做到对赤泥的减量化、无害化、资源化利用,具有显著的、深远的环境、社会和经济意义。
4.目前,对赤泥中的铁资源的回收的研究较多。《化工进展》2018年第9期发表的“赤泥中铁的提取与回收利用研究进展”一文系统综述了国内外赤泥中铁提取回收方法与工艺路线的研究进展,提出将从赤泥中提取回收利用铁的方法归纳为直接物理分选法、还原
‑
磁选法和湿法提取法。但采用直接物理分选法得到的铁精矿品位不足50%,且回收率不足55.0%;还原
‑
磁选法的能耗高,生产成本高,对环境的污染严重,而且在还原焙烧的过程中还需要一定量的添加剂,包括镁盐、钙盐、钠盐和复盐,难以在生产实际中推广应用;湿法分离提取铁的能耗虽然比还原
‑
磁选法低,但铁在酸中的溶出时间长、浸出率低,且还需要进行后续与al、ti分离净化操作;最主要的问题是没有实现赤泥的整体综合利用,并产生新的固体废物。
5.为了解决上述问题,长期以来国内外对赤泥的处理与应用进行了大量的研究与探索。赤泥的脱钠较容易实现,但赤泥中fe2o3的回收目前并没有较为合适的办法。现阶段主要的方法有酸法和碱法两种:酸溶法氧化铝的收得率高,能耗不高,但对于后续溶液中离子的处理及尾渣的处理并没有较为合适的思路,这也导致了该法并没有进行成熟的工业化应
用;碱法则主要包括碳酸钠分解法、水热反应法以及压热反应法等,碳酸钠分解法中氧化铝的回收率低,水热法得到的溶液中氧化铝浓度偏低,难以与拜耳法主体溶出工序相配套,压热法在回收氧化铝时能回收其中一部分钠,但是,其温度一般要达到260
‑
280℃以上,并且高温高压操作往往会导致生产能耗高,对设备要求也比较大,这也在一定的程度上限制了该方法的应用。
6.因此,基于上述现状,有必要对赤泥的研究及处理进行更进一步地探索,提出一种可以规模化处理和利用赤泥的新方法。
技术实现要素:
7.本发明的目的就是针对现有赤泥利用技术存在的综合利用率低、成本高、易对环境造成二次污染等难题,而提供一种可综合回收铁、钠资源,且处理工艺简单、成本低、环境友好的梯级回收赤泥中铁钠资源及尾渣全量化利用的方法,通过对尾渣进行全量化的资源利用,可以生产陶粒、瓷砖、烧结砖等建筑陶瓷材料,从而实现赤泥的整体综合利用,能够在赤泥处理工业化生产中广泛地推广应用。
8.为实现本发明的上述目的,本发明拜耳法赤泥分步回收铁、钠及尾渣的全量化整体利用方法,用于al2o3 sio2 tio2 cao mgo含量在48.0~68.0%、fe2o3含量25.0~42.0%、na2o含量4.0~10.0%、其它组份含量在1.0~5.0%的拜耳法赤泥的全量化资源利用,具体采用以下工艺、步骤:
9.1)原料处理
10.将赤泥原料通过粉碎或者球磨制成粒度为
‑
0.074μm粒级的质量百分含量占60~95%的微细赤泥料。一般情况下,微细赤泥料的粒度控制在
‑
0.074μm粒级的质量百分含量占75~90%范围为优,既可以满足赤泥处理工艺要求,又节约磨矿能耗。。
11.2)酸法浸出
12.将上述微细赤泥料在液固比为20~60ml/g、硫酸质量浓度为10~40%的条件下进行fe与na的溶解,浸出时间控制在30~120min,浸出温度控制在25~90℃范围,并通过固液分离获得浸出液、浸出尾渣。本步骤工艺参数液固比、硫酸质量浓度、浸出时间、浸出温度的优化选择的原则是综合考虑fe的浸出率、na的浸出率以及系统处理能力、生产成本,一般情况下液固比为40~60ml/g、硫酸质量浓度为25~40%,通过综合调控液固比、硫酸质量浓度、浸出时间、浸出温度,使fe的浸出率≥85.0%、na的浸出率≥80.0%。
13.3)氨水沉铁-铁资源回收
14.经过上述步骤后的溶液中,fe以fe
3
的形式存在。此时,向步骤2)获得的浸出液中加入过量的氨水进行反应,在溶液中生成絮状沉淀物fe(oh)3;对含有絮状沉淀物fe(oh)3的溶液进行固液分离,获得fe(oh)3固体,对fe(oh)3固体进行煅烧,即可得到fe2o3产品。
15.4)钠资源回收
16.上述采用氨水作为沉淀剂,步骤3)固液分离出fe(oh)3固体的溶液中含有较多的nh
4
、na
及so
42
‑
,向其加入naoh进行化学反应,化学反应产生的氨气返回至步骤3)进行氨水沉铁;对化学反应后的剩余溶液采用蒸发结晶法,即可获得钠盐na2so4。
17.5)浸出尾渣全量化利用
18.对步骤2)获得的浸出尾渣进行压滤,向滤饼中加入辅料-富硅铝原料、富钙镁原
料、石英,经含水率测试及设计不同辅料的添加配比,按照陶瓷原料中物相组成与成分控制混合料各组份质量百分含量,即:浸出尾渣50~85%,石英0~10%,富硅铝原料5~35%,富钙镁原料0~20%;所述富硅铝原料包括粘土、矸石、页岩或长石中的一种或两种及以上的混合物;所述富钙镁原料为白云石、石材加工边角料、大理石、镍铁渣中的一种或两种及以上的混合物;再通过湿法研磨混匀、压制成型和烧结,即可获得不同用途的建筑陶瓷产品,进而实现赤泥中铁钠资源及浸出尾渣的梯级全量化利用。
19.当然,根据市场需求,对步骤2)获得的浸出尾渣进行压滤,向滤饼中加入辅料-粉煤灰、骨料、工业废石膏,按照蒸压砖原料要求控制物相组成与成分,再通过湿法研磨混匀、半干法压制成型、蒸压养护,最终制备成实心或空心蒸压砖,进而实现赤泥中铁钠资源及浸出尾渣的梯级全量化利用。
20.经过试验研究,处理的拜耳法赤泥组份中,(al2o3 sio2)含量35.0~50.0%、(cao mgo)含量15.0~22.0%、fe2o3含量25.0~42.0%、tio2含量3.5~7.0%、na2o含量4.0~10.0%为优。
21.与现有技术相比,本发明拜耳法赤泥分步回收铁、钠及尾渣的全量化整体利用方法具有如下有益效果:
22.(1)本发明方法,利用了稀酸溶液中cao、sio2及al2o3的溶解度较低,主要是因为该几种组分多以矿物相存在。而fe2o3和na2o则能够较好地溶解在酸液中,是因为铁组分主要以易溶于酸液的赤铁矿存在,钠组分本身就是源自于外加的盐,故此本发明可以实现了fe、na资源与其他氧化物的分离,分离效率较高。
23.(2)与目前国内外已报道的大规模应用的方法,如氧化钙烧结法、水热法及高温高压水化学方法相比,本发明方法所提出的方案,在低温、低压的温和条件下进行,实现了fe2o3与na2o的高回收率,使赤泥中的fe2o3与na2o的最终回收率分别达到85.0%、80.0%以上。
24.(3)本发明方法中所提及的方法,实现了赤泥回收利用过程的节能减耗,实现了赤泥中各种资源的梯级回收利用,提高了资源利用率。此外,本发明方法还消除了赤泥夹带碱对环境造成的污染,是一条具有大规模应用前景的赤泥处理工艺。
25.(4)此外,本发明方法所用的液体基本是闭环循环,污染低,无尾气。
26.(5)本发明方法不仅回收了赤泥中的铁、钠资源,还100%利用了浸出尾渣,实现了赤泥的全量化整体利用。
附图说明
27.图1是本发明拜耳法赤泥分步回收铁、钠及尾渣的全量化整体利用方法的技术路线图。
具体实施方式
28.以拜耳法赤泥为原料,采用低温低压水化学法,回收赤泥中的fe2o3与na2o,实现赤泥组分中不同种类资源的梯级回收利用。为描述本发明,下面结合实施例对本发明拜耳法赤泥分步回收铁、钠及尾渣的全量化整体利用方法做进一步详细说明。但本发明并不局限于实施例,根据本发明的实质内容所做出的简单修改,均应涵盖在本发明的保护范围之内。
29.本发明实施例中所用的拜耳法赤泥主要成分组成(wt.%)如下表1:
30.表1拜耳法赤泥主要化学组分(wt.%)
31.成分al2o3sio2fe2o3caotio2na2omgo含量(%)23.3817.5527.7216.654.214.692.62
32.由图1所示的本发明拜耳法赤泥分步回收铁、钠及尾渣的全量化整体利用方法的技术路线图可以看出,本发明方法技术路线为:原料处理(细磨)-酸法浸出-氨水沉铁、铁资源回收-钠资源回收(蒸发结晶)-浸出尾渣全量化利用(陶粒、烧结砖、瓷砖)。
33.具体的处理工艺步骤为:
34.1)取一定量的赤泥加入质量百分浓度为30%及40%的硫酸溶液中,h2so4与赤泥的液固比依此分别为50ml/g及60ml/g,均匀混合后转移至三口烧瓶中,调节搅拌速度,设定控温程序,将水浴锅升温至90℃并反应120min,然后开通冷凝管中的循环水。另外,为了验证浸出温度对fe与na浸出行为的影响,实验在室温下(25℃)、硫酸浓度为25%、液固比为50ml/g、浸出时间为1小时的实验条件下,进行了赤泥中fe与na浸出行为的研究。待反应结束后,将料浆趁热过滤、液固分离,赤泥滤饼备用。随后,称取适量的赤泥滤饼备用。
35.2)通过对反应步骤1)中,不同浸出条件下得到的浸出液进行icp
‑
ms分析可知:当硫酸浓度为30%、h2so4与赤泥的液固比为50ml/g、浸出时间为0.5min、浸出温度为25℃时,fe与na的浓度可以达到72.5mg/l及45.7mg/l;当硫酸浓度为30%、h2so4与赤泥的液固比为50ml/g、浸出时间为120min、浸出温度为90℃时,定容至250ml的溶液中,fe与na的浓度可以达到341mg/l及54.2mg/l;当硫酸浓度为30%、h2so4与赤泥的液固比为60ml/g、浸出时间为120min、浸出温度为90℃时,定容至250ml的溶液中,fe与na的浓度可以达到567mg/l及83.4mg/l;当硫酸浓度为40%、h2so4与赤泥的液固比为60ml/g、浸出时间为120min、浸出温度为90℃时,定容至250ml的溶液中,fe与na的浓度可以达到641mg/l及104mg/l。上述实验数据表明,增加体系中的液固比,能够较为明显地增大浸出液中fe与na的溶度,即增大原矿中fe与na的浸出率。此时,fe与na的浸出率可以达到85.47%及80.14%;
36.3)将步骤2)中得到的滤液移至锥形瓶中,此时的溶液中含有大量的fe
3
。为了能够将溶液中的fe
3
转变成沉淀并加以回收,需要调节溶液中oh
‑
离子的溶度。将ph计的探头掺入溶液中,不断向锥形瓶中加入氨水溶液。至锥形瓶中絮状物的含量不再发生变化时,将该溶液进行过滤,得到fe(oh)3,进而实现赤泥中fe的回收。
37.4)将步骤3)中得到的料浆对分离后得到的滤液加入naoh后,回收氨气,待不再有气体溢出后,在电热板进行加热蒸发结晶,得到na盐,实现赤泥中na资源的回收。
38.5)对步骤1)中得到的赤泥滤饼通过含水率测试,设计不同辅料-富硅铝原料、富钙镁原料的添加配比,通过湿法研磨混匀制备和烧结,可以得到不同类型的陶瓷产品,如陶粒、瓷砖、烧结砖等建筑陶瓷产品等,实现赤泥资源的梯级全量化利用。还可以根据市场需求,向滤饼中加入辅料-粉煤灰、骨料、工业废石膏,按照蒸压砖原料要求控制物相组成与成分,再通过湿法研磨混匀、半干法压制成型、蒸压养护,最终制备成实心或空心蒸压砖
39.本发明提供的从赤泥中分步回收fe与na资源及其浸出尾渣进行大宗高值化利用的方法,处理工艺简单,成本低,没有引入其他的二次污染,并且避免了目前铁回收过程中的气氛控制过程及大量污染性气体的产生,在赤泥的综合利用领域具有较好的应用前景,适宜进行工业化推广。
再多了解一些
本文用于企业家、创业者技术爱好者查询,结果仅供参考。