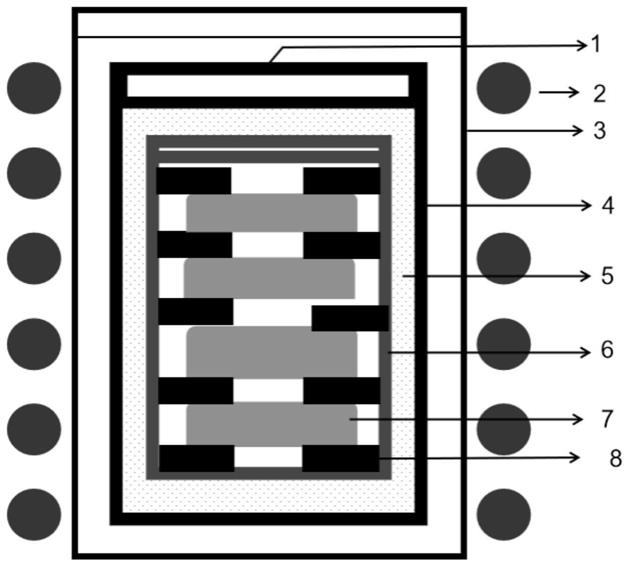
1.本发明属于碳化硅晶体技术领域,尤其涉及一种碳化硅晶体的二次退火方法。
背景技术:
2.目前使用物理气相传输法(pvt)生长的碳化硅晶体,高质量的晶体对坩埚材料,温度,压力,原料,籽晶等都有很高的要求。其中坩埚所处温场对晶体的应力,位错,有着很大的影响。一方面晶体生长依靠温场的温度梯度,根据轴向与径向的温度梯度的不同,晶体各向的生长速度也不同,使得碳化硅晶体内部原子之间相互约束,因不能自由膨胀收缩而产生应力。另一方面通常需要晶体生长面呈微凸状,以减少晶体缺陷,提高晶体质量,并扩大晶体单晶区,这种晶体面型也导致晶体内部应力增大。应力过大会导致晶体容易破裂,缺陷增多,加工成品率降低,也会影响到加工出晶片的面型,进而影响外延片的质量。合适的原位退火与二次退火工艺可以有效的减少晶体内部应力。
3.原位退火,顾名思义是在单晶生长结束后,在不改变原来生长温场结构基础上的退火,虽然可以通过缓慢降温速度,提高退火压力等方式,在一定程度上释放晶体内部的应力,但由于生长温场固有的轴向与径向温度梯度大的特点,原位退火后晶体依旧存在较大的应力;而二次退火可通过改变晶体放置方式、改变温场结构,调整压力和温度工艺曲线等方式来减少退火温度梯度或改变梯度方向,从而有效消除晶体内部应力。
4.目前最常见的晶体退火方式是,使用石墨纸包裹碳化硅晶体水平放入铺满碳化硅原料的坩埚中,可同时放入多块晶体;装配好后将坩埚放入高温退火炉中,在一定的压力下,升温至晶体退火温度,再缓慢降温。现有技术中的方法使用石墨纸和大量碳化硅原料用于防止晶体过度石墨化,但这种方法无法保证晶体径向温度梯度控制在较小范围,无法避免在二次退火中产生新的应力。
技术实现要素:
5.有鉴于此,本发明的目的在于提供一种进一步降低温场轴向与径向温度梯度的碳化硅晶体二次退火方法。
6.本发明提供了一种碳化硅晶体的二次退火方法,包括:
7.将碳化硅晶体放置在坩埚中在退火炉内进行退火处理;
8.所述坩埚包括:
9.大坩埚;
10.设置在所述大坩埚内的小坩埚,小坩埚与大坩埚同轴放置;
11.设置在所述小坩埚内的环形石墨毡;
12.所述碳化硅晶体水平方向放置在环形石墨毡的中心。
13.优选的,所述碳化硅晶体的直径为4~8英寸。
14.优选的,所述环形石墨毡的内径为碳化硅晶体直径的1/3~2/3,外径不小于碳化硅晶体直径,厚度为碳化硅晶体厚度的0.3~2.5倍。
15.优选的,所述小坩埚的内径是碳化硅晶体直径的1.1~2.0倍。
16.优选的,所述大坩埚的内径是小坩埚外径的1.1~3.0倍。
17.优选的,所述小坩埚底部与大坩埚底部之间的距离为20~150mm。
18.优选的,所述大坩埚和小坩埚之间的间隙体积为大坩埚体积的20~40%。
19.优选的,所述大坩埚和小坩埚之间的间隙中填充有保温材料。
20.优选的,所述保温材料选自石墨毡或碳化硅粉料中的一种或两种。
21.优选的,所述退火处理的方法包括:
22.升温至退火温度后保温,然后进行一次降温,最后进行二次降温;
23.所述升温的时间为10~20小时;
24.所述退火温度为2000~2500℃;
25.所述保温时间为20~40小时;
26.所述一次降温为在20~40小时降温至1000~1250℃;
27.所述二次降温为在10~15小时降温至室温。
28.本发明提供了一种“双坩埚”结构和加“环形石墨毡”的退火方法,用于调整晶体径向、轴向温度差,使晶体各处温度基本相同,晶体膨胀收缩时不受内部之间的相互约束。本发明在二次退火阶段使用“双坩埚”模式加“环形石墨毡”,减少径向和轴向温度梯度,使温度梯度保持在2~6℃,使晶体内部应力得到缓慢释放,同时避免晶体在退火过程中产生新的应力。由于晶体边缘相较于晶体中心更易散热,为保持晶体温度一致性,减少后续破损率,将晶体水平放在环形石墨毡上,使边缘的保温效果高于中心,此方法可根据坩埚高度,晶体厚度同时放置多块晶体,增加效率。
附图说明
29.图1为本发明实施例中进行退火过程中使用装置的结构示意图;
30.图2为本发明实施例1退火后得到的晶片的切割片spi面型检测图;
31.图3为本发明比较例2未进行二次退火得到的切割片spi面型检测图。
具体实施方式
32.下面将对本发明实施例中的技术方案进行清楚、完整地描述,显然,所描述的实施例仅仅是本发明一部分实施例,而不是全部的实施例。基于本发明中的实施例,本领域普通技术人员经改进或润饰的所有其它实例,都属于本发明保护的范围。应理解,本发明实施例仅用于说明本发明的技术效果,而非用于限制本发明的保护范围。实施例中,所用方法如无特别说明,均为常规方法。
33.本发明提供了一种碳化硅晶体的二次退火方法,包括:
34.将碳化硅晶体放置在坩埚中在退火炉内进行退火处理;
35.所述坩埚包括:
36.大坩埚;
37.设置在所述大坩埚内的小坩埚,小坩埚与大坩埚同轴放置;
38.设置在所述小坩埚内的环形石墨毡;
39.所述碳化硅晶体水平方向放置在环形石墨毡的中心。
40.在本发明中,所述碳化硅晶体优选为导电晶体和/或半绝缘晶体;所述碳化硅晶体的直径优选为4~8英寸;本发明对所述碳化硅晶体的厚度没有特殊的限制,优选为10~60mm,更优选为20~50mm,最优选为30~40mm。
41.本发明对所述碳化硅晶体的制备方法没有特殊的限制,采用本领域技术人员熟知的物理气相传输法(pvt)制备得到碳化硅晶体再进行一次退火即可。本发明对所述一次退火的方法没有特殊的限制,采用本领域技术人员熟知的原位退火的技术方案即可。在本发明中,所述碳化硅晶体的制备方法优选包括:
42.采用物理气相传输法(pvt)在高压下缓慢升温至碳化硅晶体生长温度,进行碳化硅晶体生长;碳化硅晶体生长结束后进行自然降温至室温的一次退火。
43.在本发明中,所述高压优选为1~10万帕,更优选为2~8万帕,更优选为3~6万帕,最优选为4~5万帕;所述缓慢升温的速度优选为100~200℃/h,更优选为120~180℃/h,最优选为140~160℃/h;所述碳化硅晶体生长温度优选为2200~2400℃,更优选为2250~2350℃,最优选为2300℃;所述碳化硅晶体生长过程中的压力优选为100~1000pa,更优选为200~800pa,更优选为300~600pa,最优选为400~500pa。
44.在本发明中,所述一次退火优选在压力下进行;所述压力优选为1~10万帕,更优选为2~8万帕,更优选为3~6万帕,最优选为4~5万帕;所述一次退火过程中优选增加炉腔压力至1~10万帕。
45.在本发明中,所述小坩埚的内径优选为碳化硅晶体直径的1.1~2.0倍,更优选为1.3~1.7倍,最优选为1.5~1.6倍。在本发明中,所述小坩埚的内径优选为200~350mm,更优选为250~300mm,最优选为260~280mm;所述小坩埚的高度优选为300~500mm,更优选为350~450mm,最优选为400mm;所述小坩埚的壁厚优选为10~100mm,更优选为20~80mm,更优选为20~50mm,更优选为20~30mm,最优选为20mm。在本发明中,所述小坩埚的材质优选为石墨。
46.在本发明中,所述大坩埚的内径优选为小坩埚外径的1.1~3.0倍,更优选为1.5~2.5倍,最优选为2倍。在本发明中,所述大坩埚的内径优选为250~400mm,更优选为300~350mm,最优选为320~330mm;大坩埚的高度优选为400~600mm,更优选为450~550mm,最优选为500mm;所述大坩埚的壁厚优选为10~100mm,更优选为20~80mm,更优选为30~50mm,更优选为30~40mm,最优选为30mm。在本发明中,所述大坩埚的材质优选为石墨。
47.在本发明中,所述小坩埚底部与大坩埚底部之间的距离优选为20~150mm,更优选为50~120mm,更优选为80~100mm,最优选为90mm;所述小坩埚底部与大坩埚底部之间的距离指的是小坩埚的外底部与大坩埚的内底部之间的距离。
48.在本发明中,所大坩埚和小坩埚之间的间隙体积优选为大坩埚体积的20~40%,更优选为25~35%,最优选为30%。
49.在本发明中,所述小坩埚和大坩埚同轴放置,即小坩埚和大坩埚的轴线重合,为同心圆位置。
50.在本发明中,所述大坩埚和小坩埚之间的间隙优选填充有保温材料;所述保温材料优选选自石墨毡或碳化硅粉料中的一种或两种。在本发明中,所述碳化硅粉料的粒度优选为100~3000微米,更优选为200~1500微米,更优选为400~1000微米,最优选为500微米。在本发明中,所述大坩埚和小坩埚的装配方法优选包括:
51.将填充物放入大坩埚中然后将小坩埚放入大坩埚中预设的位置处。
52.在本发明中,所述填充物优选为石墨毡和/或碳化硅粉料。
53.在本发明中,所述大坩埚和小坩埚的装配方法更优选包括:
54.使用石墨毡对小坩埚外表面进行缠绕,在大坩埚底面放入石墨毡至小坩埚的预设位置,将小坩埚放入大坩埚中,使小坩埚与大坩埚处于同轴位置。
55.在本发明中,所述石墨毡的厚度优选为5~20mm,更优选为10~15mm。
56.在本发明中,优选缠绕石墨毡后的小坩埚外径与大坩埚内径一致。
57.在本发明中,优选在大坩埚底面放入一层或多层石墨毡,使石墨毡的厚度达到所需的大坩埚内底部和小坩埚外底部之间的距离。
58.在本发明中,所述大坩埚和小坩埚的装配方法更优选包括:
59.将碳化硅粉料铺在大坩埚底部直至达到小坩埚的预设位置,将小坩埚与大坩埚同轴放入大坩埚内,大坩埚和小坩埚之间的间隙填满碳化硅粉料。
60.本发明采用双坩埚结构,大小坩埚中间填充石墨毡或碳化硅粉料用于保温以减少温度梯度,使晶体的轴向温度梯度优选小于3℃。
61.在本发明中,所述小坩埚内设置有环形石墨毡;所述环形石墨毡的内径优选为碳化硅晶体直径的1/3~2/3,更优选为0.4~0.5;所述环形石墨毡的外径优选不小于碳化硅晶体的直径;所述环形石墨毡的厚度优选为碳化硅晶体厚度的0.3~2.5倍,更优选为0.5~2倍,最优选为1~1.5倍。
62.在本发明中,所述环形石墨毡的外径优选为150~300mm,更优选为180~250mm,最优选为200~230mm;所述环形石墨毡的内径优选为60~150mm,更优选为80~120mm,最优选为100mm;所述环形石墨毡的厚度优选为10~30mm,更优选为15~25mm,最优选为20mm。
63.在本发明中,所述环形石墨毡优选设置在小坩埚的底部,可以根据预进行二次退火的碳化硅晶体的数量在小坩埚底面设置一层或多层石墨毡。
64.在本发明中,所述碳化硅晶体水平方向放置在环形石墨毡的中心;所述碳化硅晶体的水平方向为碳化硅晶体的轴向方向。
65.本发明将碳化硅晶体水平放置在环形石墨毡的中心,以使碳化硅晶体的中心处更好的散热,使碳化硅晶体边缘与中心的温度差优选δt≤3℃。
66.在本发明中,碳化硅晶体装入小坩埚的数量可根据小坩埚的高度进行合理配制。
67.在本发明中,优选将上述装配好的坩埚放入退火炉的炉腔发热筒内进行退火处理。
68.在本发明的实施例中退火过程中采用的装置结构示意图如图1所示,包括:
69.大坩埚顶部留孔1;
70.中频感应加热线圈2;
71.发热筒3;
72.大坩埚4
73.小坩埚6;
74.双坩埚间隙5;
75.碳化硅晶体7;
76.环形石墨毡8。
77.在本发明中,所述中频感应加热线圈设置在发热筒的外部;发热筒内放置有大坩埚;大坩埚内放置小坩埚;大坩埚和小坩埚之间具有双坩埚间隙;小坩埚底面设置有环形石墨毡;环形石墨毡中心位置水平方向放置有碳化硅晶体;大坩埚顶部中心留有一孔洞,直径优选为10~30mm,更优选为15~25mm,最优选为20mm,用于更好的通入惰性气体以及抽出大坩埚内的杂质。
78.在本发明中,所述退火处理过程中退火炉优选采用中频感应加热。
79.在本发明中,所述退火炉的发热筒周边优选环绕设置耐高温石墨毡,以进行保温。
80.在本发明中,所述退火处理过程中优选采用惰性保护气体进行保护;所述惰性保护气体优选包括氦气和/或氩气;所述惰性保护气体的压力优选为3~8万帕,更优选为4~6万帕,最优选为5万帕。
81.在本发明中,所述退火处理的方法优选包括:
82.升温至退火温度后保温,然后进行一次降温,最后进行二次降温。
83.在本发明中,所述升温的时间优选为10~20小时,更优选为12~18小时,最优选为14~16小时;所述升温时间≥10小时;所述退火温度优选为2000~2500℃,更优选为2100~2400℃,最优选为2200~2300℃;所述保温时间优选为20~40小时,更优选为25~35小时,最优选为30小时。
84.在本发明中,所述一次降温优选为缓慢降温,优选在20~40小时降温至1000~1250℃;所述降温的时间优选为25~35小时,更优选为30小时;所述降温的温度优选为1050~1200℃,更优选为1100~1150℃,最优选为1120~1130℃。在本发明中,所述一次缓慢降温过程中的降温速度优选为25~65℃/h,更优选为30~50℃/h,最优选为40℃/h。
85.在本发明中,所述二次降温优选为缓慢降温,优选在10~15小时降温至室温;所述降温时间优选为11~14小时,更优选为12~13小时;所述室温温度优选为20~30℃,更优选为22~28℃,最优选为24~26℃。在本发明中,所述二次降温过程中的降温速度优选为90~110℃/h,更优选为95~105℃/h,最优选为100℃/h。
86.在本发明中,所述一次降温结束后优选立即进行二次降温;所述二次降温的初始温度为一次降温的结束温度。
87.在本发明中,所述退火处理优选包括:
88.将装配好的坩埚放入退火炉炉腔发热筒内,充惰性气体作为保护气体,至压力3~8万帕;在10~20小时内升温至退火温度2000~2500℃,在退火温度恒温保持20~40小时,之后缓慢降温20~40小时至1000~1250℃,然后缓慢降温10~15小时至室温。
89.在本发明中,所述退火处理之前优选进行洗炉处理,所述洗炉处理的方法优选包括:
90.使用机械泵将炉腔抽至腔体内压力在10pa以下,加热至200~500℃,保持抽气1~2小时;随后充入惰性气体,再次抽气至10pa以下完成洗炉。
91.在本发明中,所述加热温度优选为300~400℃,更优选为350℃;所述保持抽气的时间优选为1.5小时;所述惰性气体优选为氩气和/或氦气;所述充入惰性气体的压力优选为1~10万帕,更优选为2~8万帕,更优选为3~6万帕,最优选为4~5万帕。
92.在本发明中,高的退火温度与较长的保温时间有利于碳化硅晶体应力的释放与改善晶体内部缺陷,保持与晶体生长时升温速率升温至退火温度,恒温保持20小时以上;为了
防止碳化硅晶体石墨化,本发明加大了炉内惰性气体压力。本发明使用“双坩埚”加“石墨毡”方式对退火晶体进行二次保温,减少温度梯度;分段式缓慢降温,降温时间大于40小时,保证晶体在退火阶段能缓慢释放内部应力并不再产生新的应力与晶体的安全。通过本发明这种碳化硅晶体二次退火的工艺,能够有效的减少晶体后续加工开裂,通过减少应力改善切割片的面型,进而提高晶片面型质量。
93.在外延中,翘曲度会影响外延层氮浓度的一致性,在封装测试过程中易造成器件失效,降低良率。碳化硅衬底面型的改善可从根源减少晶体应力,改善切割片面型。通过本发明提供的方法获得的退火后的碳化硅晶体,切割加工开裂率有效降低,切割片面型得到有效改善,warp值降至20以下,bow值在5以下。本发明提供的方法获得的切割片经过后续的加工,产品片翘曲度进一步降低。
94.本发明以下实施例中采用的碳化硅晶体为通过pvt物理气相传输法生长的碳化硅晶体经过一次退火后所得:在1~10万帕下缓慢升温(100~200℃/h)至晶体生长温度2200~2400℃,并维持压力在100~1000pa进行晶体生长,晶体生长结束后,增加炉腔压力至1~10万帕,自然降温至室温。
95.实施例1
96.采用图1所示的装置进行退火处理:取6块直径6英寸的4h
‑
sic导电晶体,水平放入双坩埚中的环形石墨毡中心,环形石墨毡厚度为25mm,外径为240mm,内径为80mm;大石墨坩埚内径为300mm,高度为400mm,壁厚为30mm;小石墨坩埚内径为250mm,高度为300mm,壁厚为20mm;大石墨坩埚底部和小石墨坩埚底部之间的距离为50mm;“双坩埚”间隙中放入石墨毡对小石墨坩埚进行保温。
97.将双坩埚装配(在小石墨坩埚外表面缠绕石墨毡,使小石墨坩埚外径与大石墨坩埚内径一致,在大石墨坩埚底面铺50mm厚的石墨毡,将小石墨坩埚放入大石墨坩埚中,使小石墨坩埚和大石墨坩埚为同轴位置)好后放入退火炉中,对退火炉进行洗炉处理,所述洗炉处理的方法为:使用机械泵抽至腔体内压力在10pa以下,加热至300℃,保持抽气1小时;随后充入氩气到3万帕,再次抽气至10pa以下完成洗炉;然后依次按照退火工艺温度、时间要求进行操作:氩气作为保护气体充至6万帕,保持该压力在退火期间不变;采用中频感应加热进行升温,在10个小时升至退火温度2200℃,并保持25个小时;在25小时内,通过调节功率降低温度至1100℃,降温速度为40℃/h;随即以100℃/h的速度在10小时内降至室温。
98.对本发明实施例1退火后的碳化硅晶体进行金刚石多线切割并采用spi面型检测仪测试切割片的面型性能,检测结果如图2所示,图2为切割面进行面扫生成的3d/2d面型图;实施例1提供的方法退火后的6块碳化硅晶体在后续的切割中,切割片面型95%warp值小于20,bow值小于5。
99.实施例2
100.采用图1所示的装置进行退火处理:取7块直径6英寸4h
‑
sic半绝缘晶体,水平放入双坩埚中的环形石墨毡中心,环形石墨毡厚度为20mm,外径为200mm,内径为60mm;大石墨坩埚内径为300mm,高度为400mm,壁厚为30mm;小石墨坩埚内径为250mm,高度为300mm,壁厚为20mm;大石墨坩埚底部和小石墨坩埚底部之间的距离为25mm;“双坩埚”间隙中放入石墨毡对小石墨坩埚进行保温。
101.将双坩埚装配(在小石墨坩埚外表面缠绕石墨毡,使小石墨坩埚外径与大石墨坩
埚内径一致,在大石墨坩埚底面铺25mm厚的石墨毡,将小石墨坩埚与大石墨坩埚同轴位置放入大石墨坩埚中)好后放入退火炉中,对退火炉进行洗炉处理,所述洗炉处理的方法为:使用机械泵抽至腔体内压力在10pa以下,加热至300℃,保持抽气1小时;随后充入氩气到3万帕,再次抽气至10pa以下完成洗炉;依次按照退火工艺温度、时间要求进行操作:氩气作为保护气体充至6万帕,保持该压力在退火期间不变;采用中频感应加热进行升温,在10个小时升至退火温度2100℃,并保持25个小时;在30小时内,通过调节功率降低温度至1000℃,降温速度为35℃/h;随即以100℃/h的速度在10小时内降至室温。
102.按照实施例1的方法对退火后的碳化硅晶体切割后进行面型检测,检测结果为,实施例2提供的方法退火后的7块碳化硅晶体在后续的切割中,切割片面型96%warp值小于20,bow值小于5。
103.比较例1
104.使用石墨纸包裹6块6英寸4h
‑
sic导电晶体,放入填满碳化硅粉料的石墨坩埚中,以相同的退火时间,温度进行退火:氩气作为保护气体充至6万帕,保持该压力在退火期间不变;采用中频感应加热进行升温,在10个小时升至退火温度2200℃,并保持25个小时;在20小时内,通过调节功率降低温度至1100℃;随即以100℃/h的速度在10小时内降至室温。
105.按照实施例1的方法进行检测,本发明比较例1退火后的碳化硅晶体切割加工后,切割片面型中83%warp值小于20,bow值小于5;相比于实施例,面型略差。
106.比较例2
107.取6块直径6英寸4h
‑
sic导电晶体,未经过二次退火。
108.按照实施例1的方法进行检测,碳化硅晶体切割加工未见开裂,追踪其切割片面型结果,65%的切割片warp值小于20,bow值小于5,可看出二次退火使碳化硅晶体应力减少,更有利于改善切割片面型。
109.本发明提供了一种“双坩埚”结构和新的晶体摆放方式的碳化硅二次退火方法,用于调整碳化硅晶体径向、轴向温度差,使碳化硅晶体各处温度基本相同,晶体膨胀收缩时不受内部之间的相互约束。本发明使用“双坩埚”模式加“环形石墨毡”的二次退火方法,减少温度梯度,使温度梯度保持在2~6℃,避免碳化硅晶体在二次退火过程中产生新的应力。由于碳化硅晶体边缘相较于晶体中心更易散热,为保持晶体温度一致性,减少后续破损率,将碳化硅晶体水平放在环形石墨毡上,使边缘的保温效果高于中心,此方法可根据坩埚高度,碳化硅晶体厚度同时放置多块晶体,增加效率。
110.以上所述的仅是本发明的优选实施方式,应当指出,对于本技术领域的普通技术人员来说,在不脱离本发明原理的前提下,还可以做出若干改进和润饰,这些改进和润饰也应视为本发明的保护范围。
再多了解一些
本文用于企业家、创业者技术爱好者查询,结果仅供参考。