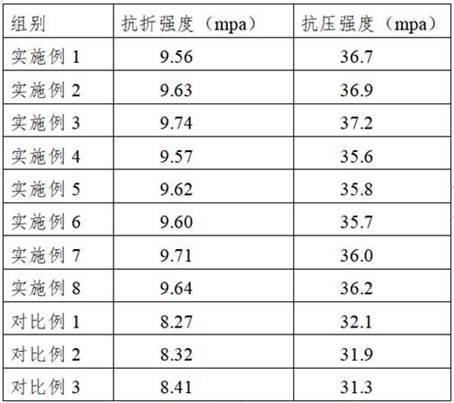
1.本发明涉及路基修建技术领域,具体涉及一种水泥或软土用固化剂及其形成的路基材料。
背景技术:
2.土壤固化剂是一种由多种无机、有机材料合成的用于固化各类土壤的新型节能环保工程材料。它与土壤混合后通过一系列物理化学反应来改变土壤的工程性质,能使土壤颗粒趋于凝聚,易于压实和稳定, 从而形成整体结构,并达到常规所不能达到的压密度。经过土壤固化剂处理过的土壤,其强度、密实度、回弹模量、剪切强度等性能都得到了很大的提高,从而延长了道路的使用寿命,节省了工程维修成本,具有很高的经济环境效益,是当前理想的筑路材料选择。现有的软土固化剂的固化速度较慢,固化强度不高,固化后的路基密实度也受到影响,公路交付完成到后期工程维修的间隔时间较短,维修成本高,且还会影响公路的使用。因此,开发一种效果更优的软土路基处理的土壤固化剂将对公路建设起到非常重要的作用。
技术实现要素:
3.(一)要解决的技术问题鉴于上述技术问题,本发明的技术目的是提供一种水泥或软土用固化剂,其在减少水泥用量的同时,具有固化速度快、固化强度高、固化后的路基密实度高等特点。
4.(二)技术方案为了达到上述目的,本发明采用的主要技术方案包括:第一方面,本发明提供一种水泥或软土用固化剂,按质量百分百计,其包含以下组分:三羟甲基氧化磷1
‑
2%;磺化油25
‑
30%;木质素磺酸钠1
‑
2%;硫酸钠0.3
‑
0.5%;柠檬酸钠0.1
‑
0.15%;三乙醇胺4
‑
5%;硅酸锂0.2
‑
0.8%;二丙二醇甲醚1
‑
1.6%;余量为水。
5.根据本发明的较佳实施例,所述软土用固化剂包含如下组分:三羟甲基氧化磷1.5%;磺化油25%;木质素磺酸钠1.5%;硫酸钠0.4%;柠檬酸钠0.12%;三乙醇胺4.5%;硅酸锂0.5%;二丙二醇甲醚1.4%;余量为水。
6.第二方面,本发明提供一种由上述方案记载的固化剂所形成的路基材料,按质量百分百计,其包括如下成分:上述方案记载的固化剂0.02
‑
0.04%、水泥6
‑
10%;余量为软土和水;其中,水的添加量根据软土的含水率计算确定。
7.根据本发明的较佳实施例,其中,水的添加量的计算方法包括:s1、计算土样含水率:土样含水率=(湿重
‑
土粒重)/土粒重
×
100%;s2、计算加水量:
加水量=(最佳含水率
‑
土样含水率)/(1+土样含水率)
×
土重。
8.根据本发明的较佳实施例,s1中,土样含水率的计算过程包括:从路基修建现场采集土样,称量得到湿重;将土样在微波和负压条件下烘干后,再次称量得到土粒重;利用湿重和土粒重计算得土样含水率。
9.根据本发明的较佳实施例,其中,s2中,最佳含水率按照如下方式得到:从路基修建现场采集已知质量的土样,加水、水泥和固化剂按照比例混合拌匀,得到混合材料;控制混合材料中水泥质量百分比为x,固化剂质量百分比为y;其中x是介于6
‑
10%之间的某确定值,y是介于0.02
‑
0.04%之间的某确定值;改变加水量,按照1%的梯度调节混合材料的湿度,同时将不同湿度的混合材料装入模框中,在振台上振动,使其振实成型为试样;用防水膜多层包裹在试样表面以防止失水,室温放置1d后拆模,测试试样的抗压强度值;做湿度
‑
抗压强度的曲线,从曲线上选择抗压强度最大值对应的湿度,即为对应该土样、水泥质量百分比为x、固化剂质量百分比为y时的最佳含水率。
10.(三)有益效果本发明提供了一种新的软土用固化剂,相比较于现有的软土用固化剂,在其他条件(土样、加压方式和压力、养护)基本相同的情况下,使用本发明的固化剂进行软土路基的固化,具有固化速度快、固化后强度更高、固化后的路基密实度更大等优点,因此可有效延长公路交付使用至维修之间的时间间隔,减少维修施工量,节省维修成本,减少因公路维修带来的不便。此外,固化剂中不含无机酸或碱成分,不影响返耕后土壤的土质和生态环境及当地水质。本发明还涉及由所述固化剂形成的路基材料。
具体实施方式
11.为了更好的解释本发明,以便于理解,下面结合具体实施方式,对本发明作详细描述。
12.本发明提供一种水泥或软土用固化剂,按质量百分百计,其包含以下组分:三羟甲基氧化磷1
‑
2%;磺化油25
‑
30%;木质素磺酸钠1
‑
2%;硫酸钠0.3
‑
0.5%;柠檬酸钠0.1
‑
0.15%;三乙醇胺4
‑
5%;硅酸锂0.2
‑
0.8%;二丙二醇甲醚1
‑
1.6%;余量为水。
13.其中,三羟甲基氧化磷为催化剂及助剂,与水可任意比混溶,耐热稳定性好,耐水解性能优异、无毒,主要用于加快固化速度,增大维护天数较少时的抗压强度。
14.磺化油具有润湿、乳化、分散等作用,与水形成稳定的乳液,磺化油渗透能力强,有良好的填充性,可以密实化土壤。磺化油在水中电离出大量的氢离子和氢氧根离子,离子与土颗粒表面的电荷进行反应,降低土壤颗粒表面双电层厚度,从而减少土壤颗粒对水的吸附能力,使得土壤颗粒表面吸附的结合水膜厚度减小,使土壤颗粒聚集。磺化油的亲水基团与土颗粒结合,而另一端的亲油基则会对外,使土壤颗粒由原本的亲水变为疏水,使得部分的吸附水得以排出,这一反应是不可逆的,因而可以彻底改善土壤的水稳定性,还不会对土壤原本的矿物晶格结构产生解体破坏。配合使用机械或人工进行振实或者挤压密实,使土体压密,提高强度。在形成路基材料时,还加入了一定量水泥(6
‑
10%),水泥在水的作用下产生化学反应生成凝胶状的水化物来固化土壤。磺化油和水泥协同作用,极大提高了软土路基的抗压强度。
15.木质素磺酸钠:填充和黏结物质,易溶于水及碱液,遇酸沉淀,具有良好的分散能力,应用于水泥减水剂可大幅改善其流动性和可塑性,而且可大大降低有害孔隙,明显增强抗压强度,分散剂、絮凝剂和缓蚀阻垢剂,性能优良的阴离子表面活性剂,是高分子材料,能提高材料的稳定性、强度和抗光解等性能。
16.硫酸钠:硫酸钠主要用于与水泥反应生产具有膨胀性的钙钒石晶体,填充水泥土中的孔隙,提高其强度。通常硫酸钠的添加量与水泥土(水泥、固化剂、软土)的抗压强度成正比,但硫酸钠/水泥土=9g/kg时对水泥土强度的增大作用到达极限。这是因为硫酸钠过量时,钙钒石产生的膨胀力大于水泥土的胶结力,会降低水泥土的强度。
17.柠檬酸钠为一种有机螯合剂,在水存在的条件下,可与土壤中的金属离子(对土壤中的ca
2
、mg
2
等有非常强的络合能力)形成螯合物,使土壤颗粒聚集,更加密实。
18.三乙醇胺为助固化剂、早强剂,可使土中富含的二氧化硅被激活,被激活的二氧化硅与硅酸锂(可溶性硅酸盐)在水存在条件下均为一种渗透结晶材料,可迅速渗入土体内部并与游离钙反应,生成不可溶解的非晶态水化硅酸钙,从而实现对土体结构物细孔的封堵,提高密实度和软土固化路基的抗压强度和密实度。
19.二丙二醇甲醚(dpm)是一种具有低毒性;低粘度;低表面张力;适度的蒸发速率;良好的溶解、偶联能力的无色透明液体。dpm可作为偶联剂和凝结剂,粗糙土壤颗粒凝结。
20.为了进一步明确本发明方案及其技术进步性,以下结合具体实施例和技术效果进行说明。
21.实施例1一种固化剂,其组成为(按质量百分比计):三羟甲基氧化磷1%、磺化油28%、木质素磺酸钠1%、硫酸钠0.4%、柠檬酸钠0.1%、三乙醇胺5%、硅酸锂0.6%、二丙二醇甲醚1.2%、余量为水。
22.实施例2一种固化剂,其组成为(按质量百分比计):三羟甲基氧化磷2%、磺化油30%、木质素磺酸钠2%、硫酸钠0.5%、柠檬酸钠0.15%、三乙醇胺5%、硅酸锂0.8%、二丙二醇甲醚1.6%、余量为水。
23.实施例3一种固化剂,其组成为(按质量百分比计):三羟甲基氧化磷1.5%;磺化油25%;木质素磺酸钠1.5%;硫酸钠0.4%;柠檬酸钠0.12%;三乙醇胺4.5%;硅酸锂0.5%;二丙二醇甲醚1.4%;余量为水。
24.实施例4一种固化剂,其组成为(按质量百分比计):三羟甲基氧化磷1%;磺化油30%;木质素磺酸钠1.5%;硫酸钠0.5%;柠檬酸钠0.15%;三乙醇胺4%;硅酸锂0.7%;二丙二醇甲醚1.6%;余量为水。
25.实施例5一种固化剂,其组成为(按质量百分比计):三羟甲基氧化磷2%、磺化油26%、木质素磺酸钠1%、硫酸钠0.4%、柠檬酸钠0.15%、三乙醇胺5%、硅酸锂0.8%、二丙二醇甲醚1.5%、余量为水。
26.实施例6
一种固化剂,其组成为(按质量百分比计):三羟甲基氧化磷1.5%、磺化油30%、木质素磺酸钠2%、硫酸钠0.5%、柠檬酸钠0.15%、三乙醇胺4%、硅酸锂0.5%、二丙二醇甲醚1.2%、余量为水。
27.实施例7一种固化剂,其组成为(按质量百分比计):三羟甲基氧化磷2%、磺化油25%、木质素磺酸钠1%、硫酸钠0.5%、柠檬酸钠0.15%、三乙醇胺4%、硅酸锂0.4%、二丙二醇甲醚1.5%、余量为水。
28.实施例8一种固化剂,其组成为(按质量百分比计):三羟甲基氧化磷2%、磺化油25%、木质素磺酸钠1.8%、硫酸钠0.5%、柠檬酸钠0.15%、三乙醇胺4%、硅酸锂0.5%、二丙二醇甲醚1.2%、余量为水。
29.对比例1本对比例中不添加三羟甲基氧化磷。
30.对比例2本对比例中不添加硅酸锂。
31.对比例3本对比例中将实施例3中的二丙二醇甲醚1.4%换成等量的1,4—二氧六环。
32.实施例9将上述各实施例和对比例的固化剂与混凝土原料按照1:4000的质量比进行配比,然后将固化剂与混凝土原料倒入到搅拌装置内(除了固化剂种类不同外,其余方法步骤均相同),并加入一定量的水充分搅拌混合,形成混合混凝土浆料,将浆料送入砌块成型机模具中振压成型,脱模后在常温常压保湿条件下自然养护7天。然后对制得的混凝土实心砖进行性能检测,具体对比数据如下表1所示:表1
由试验结果可知,实施例1
‑
8的固化剂可使混凝土实心砖快速获得较高的抗压强度,尤其以实施例3组成的固化剂效果最显著。对比例1
‑
3的固化剂制备的混凝土实心砖抗压强度明显不及实施例1
‑
8。
33.实施例10将实施例1
‑
8和对比例1
‑
3的固化剂、软土、普通硅酸盐水泥按照比例混合进行软土固化(修建路基前的小规模试验),软土采集自山东潍坊市郊拟新建公路规划地,现场采集然后封存。固化剂用量为0.02%,硅酸盐水泥用量为10%,控制加水量使固化土样中的含水率约为16%。
34.具体实施时,磺化油要提前溶于水中,充分电离,电离充分后和其余配料充分混合,制得固化剂,一起加入处理好的土样充分搅拌均匀,放入密封袋中闷料24小时,闷料完成后加入普通硅酸盐水泥和剩余的水并搅拌均匀,一个小时后按规范制备试件。本次试验严格按照《公路工程无机结合料稳定材料试验规程》(jtg e51
‑
2009)进行操作。标准养护室养护14天,将7天、14天无侧限抗压强度作为抗压强度指标。抗压强度参照gb/t16925
‑
1997进行测试,对比数据如下表2所示:表2
ꢀ
由试验结果可知,实施例1
‑
8的固化剂可使软土土样在7天,14天时即可获得较高的无侧限抗压强度。反之,对比例1
‑
3的抗压强度则无法达到实施例1
‑
8固化剂的技术效果。一般来说实际施工中,实验室获得的无侧限抗压强度需高于公路实际抗压强度指标值的30%左右,才能保证实际施工修建的公路抗压强度满足要求。根据上述测试结果可知,本发明提供的固化剂完全可以满足公路实际施工的抗压指标要求。
35.实施例11将实施例1的固化剂、软土、普通硅酸盐水泥按照比例混合进行软土固化,软土采集自山东潍坊市郊拟新建公路规划地,现场采集然后封存。固化剂用量为0.02%,硅酸盐水泥用量为4%、6%、8%、10%,控制加水量使固化土样中的含水率约为16%。按照实施例10相同的方法,制备试件。标准养护室养护14天,测7天、14天无侧限抗压强度,具体对比数据如下表3所示:表3由试验结果可知,采用本发明的软土固化剂和水泥制备路基材料时,水泥的添加量最好是不低于6%,优选为10%的水泥用量。
36.实施例12将实施例3的固化剂、软土、普通硅酸盐水泥按照比例混合进行软土固化,软土采
集自山东潍坊市郊拟新建公路规划地,现场采集然后封存。固化剂用量为0.01%、0.02%、0.03%、0.04%、0.05%、0.06%,硅酸盐水泥用量为10%,控制加水量使固化土样中的含水率约为16%。按照实施例10相同的方法,制备试件。标准养护室养护14天,测7天、14天无侧限抗压强度,具体对比数据如下表4所示:表4由试验结果可知,采用本发明的软土固化剂和水泥制备路基材料时,固化剂的添加量最好是不低于0.020%,而高于0.04%后固化软土路基的抗压强度升幅不明显。因此,固化剂用量较佳选择为0.02
‑
0.03%。
37.实施例13由于不同场地所采集的软土本身的含水率不同,软土土质有很大差别,土样中矿物质、含硅酸盐、钙离子、镁离子浓度、酸碱性等均不相同,因此在使用本发明的软土固化剂进行软土固化时,需要考虑最佳用水量,以得到最优的抗压强度,从而保证路基的使用寿命,延长公路交付使用至维修之间的间隔期。在工程实践中,可进行小规模的预试验,以得到最佳含水率。具体可按照如下方式操作:(1)从路基修建现场采集已知质量的土样,加水、水泥和固化剂按照比例混合拌匀,得到混合材料;控制混合材料中水泥质量百分比为x,固化剂质量百分比为y;其中x是介于6
‑
10%之间的某确定值,y是介于0.02
‑
0.04%之间的某确定值。
38.(2)改变加水量,按照1%的梯度调节混合材料的湿度,同时将不同湿度的混合材料装入模框中,在振台上振动,使其振实成型为试样;(3)用防水膜多层包裹在试样表面以防止失水,室温放置1d后拆模,测试试样的抗压强度值;做湿度
‑
抗压强度的曲线,从曲线上选择抗压强度最大值对应的湿度,即为对应该土样、水泥质量百分比为x、固化剂质量百分比为y时的最佳含水率。
39.(4)从路基修建现场采集土样,称量得到湿重;将土样在微波和负压条件下烘干后,再次称量得到土粒重;利用湿重和土粒重计算得土样含水率,土样含水率=(湿重
‑
土粒重)/土粒重
×
100%。
40.(5)根据最佳含水率、土样含水率计算进行软土固化时的加水量:加水量=(最佳含水率
‑
土样含水率)/(1+土样含水率)
×
土重。
41.将上述方法应用在山东潍坊市郊一段路基修建工程中,新建路基路长100米、宽5米、路基土壤厚度0.2米,土密度1.85(吨),则土重为:100
×5×
0.2
×
1.85=185(吨)。
42.经取土样检测,现场实测的土样含水率为10%。
43.取少量施工现场的土样,分成7份。添加硅酸盐水泥和实施例1的固化剂。调节固化施工的加水量,使水泥及土壤混合湿度为10%、11%、12%、13%、14%、15%、16%,加水的同时适当调节水泥和固化剂的加量,保证水泥和固化剂质量百分比保持在一个固定水平(水泥10%、固化剂0.02%)。调配拌匀后,分装到7个底部和顶部均开口的模框中,在振台上振动2min,使其完全振实成型为试样。用保鲜膜包裹试样,室温放置1d后拆掉保鲜膜,测试试样的抗压强度值。测得所采集的软土土样进行高强度固化的最佳含水率为14%。
44.根据加水量=(最佳含水率
‑
土样含水率)/(1+土样含水率)
×
土重,计算加水量为:(14%
‑
10%)/(1+10%)
×
185=6.727≈6.8(吨),并计算出水泥添加量约为21.31吨,固化剂添加量42.62kg。
45.按计算结果准备水泥、水和固化剂。
46.取部分水稀释固化剂100倍,将稀释的固化剂加到路基软土中与软土充分搅拌均匀,覆盖地膜放置隔夜,第二天向软土中加入水泥和剩余的水,再次拌和均匀,用振捣机振捣整平,按照常规的固化剂加固土的工程实施方法施工,最后根据(jtg e51
‑
2009)测定固化土的七天无侧限抗压强度和水稳性指标,7天无侧限抗压强度平均值为7.87mpa,水稳性指标为86%。由此说明,本发明的固化剂和路基固化方法,可以使软土抗压强度和水稳性均达到较高水平,可提高软土路基的强度和耐水性。
47.最后应说明的是:以上各实施例仅用以说明本发明的技术方案,而非对其限制;尽管参照前述各实施例对本发明进行了详细的说明,本领域的普通技术人员应当理解:其依然可以对前述各实施例所记载的技术方案进行修改,或者对其中部分或者全部技术特征进行等同替换;而这些修改或者替换,并不使相应技术方案的本质脱离本发明各实施例技术方案的范围。
再多了解一些
本文用于企业家、创业者技术爱好者查询,结果仅供参考。