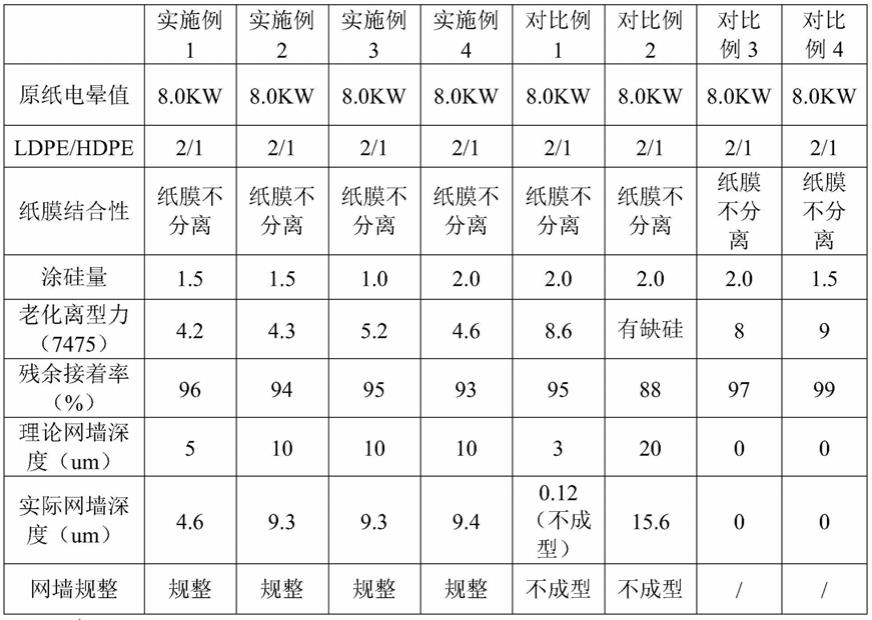
1.本发明属于离型纸技术领域,更具体地,涉及一种微网格离型纸及其制备方法。
背景技术:
2.网格离型纸目前在原纸淋膜时将网格通过网纹辊将网格负载到淋膜层,再淋膜层上涂覆溶剂硅油,固化得到网格离型纸。因为pe网墙的耐热温度有限,往往只能使用低温硅油或者uv固化硅油。低温硅油的离型产品的固化较差,sa会低,对后续的胶黏制品的粘性影响较大,硅转移较多;uv固化硅油往往会堵塞网墙,网格排气性能较差。
3.随着环保要求增高,大规模的溶剂型硅油的使用越来越受到限制,无溶剂硅油的使用成必然趋势,网格离型纸也将迎来新的工艺要求。
技术实现要素:
4.本发明的目的是针对以上不足,提供一种微网格离型纸,不含溶剂型硅油,网墙规整;还提供了该离型纸的制备方法,固化程度高,残余接着率高,生产过程中不产生溶剂排放,对环境友好。
5.为实现上述目的,本发明是通过以下技术方案实现的:
6.一种微网格离型纸,包括原纸层,淋塑在原纸层上的淋膜层,涂布在淋膜层上的有机硅离型层,所述淋膜层和有机硅离型层上均设有网格,所述网格的网强深度为5~10μm,所述有机硅离型层为不含溶剂硅油的有机硅离型剂。
7.优选的,所述网格是通过微波加热的同时使用网纹辊压花的方式得到。
8.优选的,所述原纸层采用平滑度在200
‑
300s的原纸。
9.优选的,所述淋膜层为hdpe,lldpe或ldpe的一种或者多种,进一步优选的,采用ldpe和hdpe质量比为2:1的混合物。
10.优选的,所述有机硅离型层由如下组分制备而成的:乙烯基封端的聚二甲基硅氧烷(无溶剂硅油),甲基氢硅油和珀金催化剂,其质量比为100:2~6:0.6~3,优选为100:2~3:1~1.5。
11.本发明还提供了一种上述微网格离型纸的制备方法,包括以下步骤:
12.将原纸烘烤后,对原纸表面进行电晕预处理;
13.将淋膜层原料加热后淋膜至预处理后的原纸的两面,冷却后得淋膜纸;
14.将有机硅离型剂涂布于淋膜纸的一面或两面,在110~130℃范围内分段烘干,然后熟成,得到平纹离型纸;
15.使用微波对平纹离型纸的离型面进行照射,同时使用网纹辊压合,压制网墙深度为5~10μm,得到微网格离型纸。
16.优选的,所述原纸烘烤的温度为90~120℃,电晕值为8.0~8.5kw。
17.优选的,所述淋膜层原料经过250~280℃加热架桥,淋膜时膜头温度为280~310℃,淋膜挤出压力为5.8~8.3mpa,冷却温度为35~40℃。
18.优选的,所述淋膜时淋膜量不小于25g/m2。
19.优选的,所述有机硅离型剂的烘干过程分为8段,温度依次设置为80,90,100,115,128,130,110,90。涂布离型剂后的烘箱是由多节组成的,一般长度都是5m,宽度是2m,每一片离型纸均经过这8节烘箱,前段的低温期主要是为了加热烘干涂布液中溶剂和无用小分子;128~130为主要反应温度区间。
20.优选的,所述有机硅离型剂固含量为100%,涂硅量不小于1.0g/m2。
21.与现有技术相比,本发明的有益效果为:
22.(1)本发明所述微网格离型纸,采用不含溶剂硅油的有机硅离型层,网墙深度低且规整,纸膜结合性好,美观且环保。
23.(2)本发明所述微网格离型纸的制备方法,固化程度高,残余接着率高,生产过程中不产生溶剂排放,对环境友好。
具体实施方式
24.下面将结合具体实施例更详细地描述本发明的优选实施方式。
25.实施例1
26.一种微网格离型纸,其制备方法包括以下步骤:
27.(1)采用平滑度为200s的原纸,通过90℃的前置烤箱,然后使用8.0kw的电晕对原纸表面进行电晕;
28.(2)将ldpe和hdpe按照质量比例2:1充分混合,经过250℃加热架桥,淋膜时膜头温度为280℃,淋膜至预处理后的原纸的双面,挤出压力为5.8mpa,淋膜量为25g/m2,冷却后得到淋膜纸,冷却辊的温度为35℃;
29.(3)将乙烯基封端的聚二甲基硅氧烷、甲基氢硅油和珀金催化剂按质量比为100:2.6:1.2混合制得固含为100%的有机硅离型剂,将该离型剂涂布在pe淋膜纸的一面,涂硅量为1.5g/m2,经过烘箱烘干,烘箱温度依次设置为80,90,100,115,128,130,110,90,50℃熟成2天,得到平纹离型纸;
30.(4)使用微波对离型面进行照射,同时使用网纹辊进行压合,最终得到微网格离型纸,网墙深度为5μm。
31.实施例2
32.一种微网格离型纸,其制备方法包括以下步骤:
33.(1)采用平滑度为200s的原纸,通过90℃的前置烤箱,然后使用8.0kw的电晕对原纸表面进行电晕;
34.(2)将ldpe和hdpe缩按照质量比例2:1充分混合,经过250℃加热架桥,淋膜时膜头温度为280℃,淋膜至预处理后的原纸的双面,挤出压力为5.8mpa,淋膜量为25g/m2,冷却后得到淋膜纸,冷却辊的温度为35℃;
35.(3)将乙烯基封端的聚二甲基硅氧烷、甲基氢硅油和珀金催化剂按质量比为100:2.6:1.2混合制得固含为100%的有机硅离型剂,将该离型剂涂布在pe淋膜纸的一面,涂硅量为1.5g/m2,经过烘箱烘干,烘箱温度依次设置为80,90,100,115,128,130,110,90,50℃熟成2天,得到平纹离型纸;
36.(4)使用微波对离型面进行照射,同时使用网纹辊进行压合,最终得到微网格离型
纸,网墙深度为10μm。
37.实施例3
38.一种微网格离型纸,其制备方法包括以下步骤:
39.(1)采用平滑度为250s的原纸,通过100℃的前置烤箱,然后使用8.0kw的电晕对原纸表面进行电晕;
40.(2)将ldpe和hdpe缩按照质量比例2:1充分混合,经过260℃加热架桥,淋膜时膜头温度为300℃,淋膜至预处理后的原纸的双面,挤出压力为6.5mpa,淋膜量为28g/m2,冷却后得到淋膜纸,冷却辊的温度为38℃;
41.(3)将乙烯基封端的聚二甲基硅氧烷、甲基氢硅油和珀金催化剂按质量比为100:2.6:1.2混合制得固含为100%的有机硅离型剂,将该离型剂涂布在pe淋膜纸的一面,涂硅量在1.0g/m2,经过烘箱烘干,烘箱温度依次设置为80,90,100,115,128,130,110,90,50℃熟成2天,最终得到平纹离型纸;
42.(4)使用微波对离型面进行照射,同时使用网纹辊进行压合,最终得到微网格离型纸,网墙深度10μm。
43.实施例4
44.一种微网格离型纸,其制备方法包括以下步骤:
45.(1)采用平滑度为300s的原纸,通过120℃的前置烤箱,然后使用8.0kw的电晕对原纸表面进行电晕;
46.(2)将ldpe和hdpe缩按照质量比例2:1充分混合,经过280℃加热架桥,淋膜时膜头温度为310℃,淋膜至预处理后的原纸的双面,挤出压力为7.5mpa,淋膜量为30g/m2,冷却后得到淋膜纸,冷却辊的温度为40℃;
47.(3)将乙烯基封端的聚二甲基硅氧烷、甲基氢硅油和珀金催化剂按质量比为100:2.6:1.2混合制得固含为100%的有机硅离型剂,将该离型剂涂布在pe淋膜纸的一面,涂硅量在2.0g/m2,经过烘箱烘干,烘箱温度依次设置为80,90,100,115,128,130,110,90,50℃熟成2天,最终得到平纹离型纸;
48.(4)使用微波对离型面进行照射,同时使用网纹辊进行压合,最终得到微网格离型纸,网墙深度10μm。
49.对比例1
50.一种微网格离型纸,其制备方法包括以下步骤:
51.(1)采用平滑度为300s的原纸,通过120℃的前置烤箱,然后使用8.0kw的电晕对原纸表面进行电晕;
52.(2)将ldpe和hdpe缩按照质量比例2:1充分混合,经过280℃加热架桥,淋膜时膜头温度为310℃,淋膜至预处理后的原纸的双面,挤出压力为7.5mpa,淋膜量为30g/m2,冷却后得到淋膜纸,冷却辊的温度为40℃;
53.(3)将乙烯基封端的聚二甲基硅氧烷、甲基氢硅油和珀金催化剂按质量比为100:2.6:1.2混合制得固含为100%的有机硅离型剂,将该离型剂涂布在pe淋膜纸的一面,涂硅量在2.0g/m2,经过烘箱烘干,烘箱温度依次设置为80,90,100,115,128,130,110,90,50℃熟成2天,最终得到平纹离型纸;
54.(4)使用微波对离型面进行照射,同时使用网纹辊进行压合,最终得到微网格离型
纸,网墙深度3μm。
55.对比例2
56.一种微网格离型纸,其制备方法包括以下步骤:
57.(1)采用平滑度为300s的原纸,通过120℃的前置烤箱,然后使用8.0kw的电晕对原纸表面进行电晕;
58.(2)将ldpe和hdpe缩按照质量比例2:1充分混合,经过280℃加热架桥,淋膜时膜头温度为310℃,淋膜至预处理后的原纸的双面,挤出压力为7.5mpa,淋膜量为30g/m2,冷却后得到淋膜纸,冷却辊的温度为40℃;
59.(3)将乙烯基封端的聚二甲基硅氧烷、甲基氢硅油和珀金催化剂按质量比为100:2.6:1.2混合制得固含为100%的有机硅离型剂,将该离型剂涂布在pe淋膜纸的一面,涂硅量在2.0g/m2,经过烘箱烘干,烘箱温度依次设置为80,90,100,115,128,130,110,90,50℃熟成2天,最终得到平纹离型纸;
60.(4)使用微波对离型面进行照射,同时使用网纹辊进行压合,最终得到微网格离型纸,网墙深度20μm。
61.对比例3
62.一种平纹离型纸,其制备方法包括以下步骤:
63.(1)采用平滑度为300s的原纸,通过120℃的前置烤箱,然后使用8.0kw的电晕对原纸表面进行电晕;
64.(2)将ldpe和hdpe缩按照质量比例2:1充分混合,经过280℃加热架桥,淋膜时膜头温度为310℃,淋膜至预处理后的原纸的双面,挤出压力为7.5mpa,淋膜量为30g/m2,冷却后得到淋膜纸,冷却辊的温度为40℃;
65.(3)将乙烯基封端的聚二甲基硅氧烷、甲基氢硅油和珀金催化剂按质量比为100:2.6:1.2混合制得固含为100%的有机硅离型剂,将该离型剂涂布在pe淋膜纸的一面,涂硅量在2.0g/m2,经过烘箱烘干,烘箱温度依次设置为80,90,100,115,128,130,110,90,50℃熟成2天,最终得到平纹离型纸。
66.对比例4
67.一种平纹离型纸,其制备方法包括以下步骤:
68.(1)采用平滑度为200s的原纸,通过90℃的前置烤箱,然后使用8.0kw的电晕对原纸表面进行电晕;
69.(2)将ldpe和hdpe缩按照质量比例2:1充分混合,经过250℃加热架桥,淋膜时膜头温度为280℃,淋膜至预处理后的原纸的双面,挤出压力为5.8mpa,淋膜量为25g/m2,冷却后得到淋膜纸,冷却辊的温度为35℃;
70.(3)将乙烯基封端的聚二甲基硅氧烷、甲基氢硅油和珀金催化剂按质量比为100:2.6:1.2混合制得固含为100%的有机硅离型剂,将该离型剂涂布在pe淋膜纸的一面,涂硅量为1.5g/m2,经过烘箱烘干,烘箱温度依次设置为80,90,100,115,128,130,110,90,50℃熟成2天,得到平纹离型纸。
71.以上实施例及对比例所制备的离型纸性能对比见表1。
72.表1实施例及对比例所制备的离型纸的性能对比
[0073][0074]
注:表中所述老化离型力7475是指测试老化离型力的标准胶带德萨7475胶带,测试方法为ftm
‑
10。
[0075]
从表1中可以看出,对比例1的网墙太浅,而纸张本身的厚度就存在公差,无法呈现完整的网格,故网墙不成型;对比例2因为网墙过高,2.0g/m2的硅油的伸缩能力无法覆盖压出来的20μm的深度,故而有缺硅,且20μm的网格有部分已经坍塌。
[0076]
目前市面的网格离型纸因为是先有网格,在涂硅,为了保证网格的规整性,硅油固化温度都是很高,因而残余比较低;本发明所述微网格离型纸先使硅油固化,再压出网格,残余不受硅油固化的影响,因此,相对于对比例3和4的平纹面,残余接着率下降的不多。另,测试离型力时,使用标准胶带德萨7475胶带,贴合离型面,网格的深浅会直接将标准胶带的胶面压出网格形状,从而影响离型力;残余接着率也是同理。
[0077]
以上已经描述了本发明的各实施例,上述说明是示例性的,并非穷尽性的,并且也不限于所披露的各实施例。在不偏离所说明的各实施例的范围和技术原理的情况下,对于本技术领域的普通技术人员来说许多修改和变更都是显而易见的,这些修改和变更也应视为本发明的保护范围。
再多了解一些
本文用于企业家、创业者技术爱好者查询,结果仅供参考。