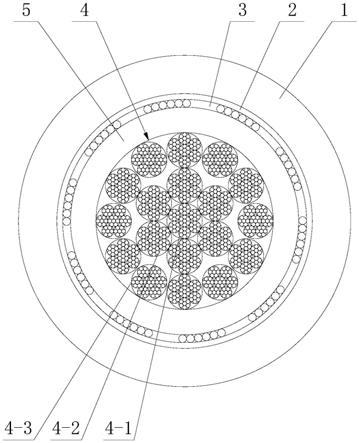
1.本实用新型属于电缆技术领域,尤其涉及一种新能源车内用耐振动柔性高压电缆。
背景技术:
2.随着新能源电动汽车技术的不断发展与成熟,目前,新能源电动汽车因其节能环保、方便快捷的优点逐渐被大众所接受,成为消费者购车的首选。电力驱动系统以及控制系统是新能源电动汽车的核心。电能通过车内的高压电缆传输,高压电缆作为车内的能量传输管道,起着至关重要的作用。与传统的燃油车不同,用于新能源汽车车内传输能量的高压电缆,需要连接不同的组件,不同的组件之间存在着相对的振动,所以提高电缆的耐振性能和柔软性非常的重要。
3.普通的车内电缆结构简单,没有特殊的耐振动设计及柔性优化,连接于车内不同组件之间的电缆容易出现导体断丝,绝缘开裂、绝缘电阻降低等问题。
技术实现要素:
4.针对现有技术存在的问题,本实用新型提供了一种解决目前用于车内的电缆耐振性能差、柔性差的问题的新能源车内用耐振动柔性高压电缆。
5.本实用新型是这样实现的,一种新能源车内用耐振动柔性高压电缆,其特征在于:所述电缆自外向内依次为护套层、复合屏蔽层、编织屏蔽层和至少一导体单元,所述导体单元包括导体线芯和设于导体线芯外侧的绝缘层,所述导体线芯包括直径为0.142mm~0.158mm导体单丝,7根导体单丝束绞成为股线,股线的节径比为27
‑
29倍,股线外侧依次绞合第一导体层、第二导体层和第三导体层,所述第一导体层由6根股线绞合而成,所述第一导体层的绞合节径比为17
‑
20倍,所述束绞的7根股线构成复绞导体,所述第二导体层由6根复绞导体绞合而成,所述第二导体层的绞合节径比为15
‑
18倍,所述第三导体层由12根复绞导体绞合而成,所述第三导体层的绞合节径比为11
‑
14倍,相邻导体层之间的绞合方向相反。
6.本实用新型具有以下优点:
7.1.导体结构稳定,在正弦复合振动的条件下,导体单元的结构设计可以满足导体单元在相对运动时有足够的空间和长度在往复运动,正弦复合振动的位移不足以破坏导体单元的机构稳定性和拉断导体单丝。本实用新型所述电缆柔软,按iso19642
‑
2:2019的柔性测试,力值小于55n。
8.在上述技术方案中,所述编织屏蔽层为镀锡铜丝编织而成,所述复合屏蔽层为铝塑复合薄膜。
9.在上述技术方案中,所述编织屏蔽层内设有三条导体单元,所述三条导体单元之间填充设置内衬层。
附图说明
10.图1是本实用新型中实施一的结构示意图;
11.图2是本实用新型中实施例二的结构示意图。
12.图中、1、护套层;2、复合屏蔽层;3、编织屏蔽层;4、导体线芯;4
‑
1、第一导体层;4
‑
2、第二导体层;4
‑
3、第三导体层;5、绝缘层;6、内衬层。
具体实施方式
13.为了使本实用新型的目的、技术方案及优点更加清楚明白,以下结合实施例,对本实用新型进行进一步详细说明。应当理解,此处所描述的具体实施例仅仅用以解释本实用新型,并不用于限定本实用新型。
14.为解决目前用于车内的电缆耐振性能差、柔性差的问题,本实用新型特提供一种新能源车内用耐振动柔性高压电缆,本电缆柔软,耐振性能强,从结构上解决了不同组件之间的相对振动对电缆带来的破坏。为了进一步说明本实用新型的结构,结合附图详细说明书如下:
15.实施例一
16.请参阅图1,一种新能源车内用耐振动柔性高压电缆,电缆自外向内依次为护套层1、复合屏蔽层2、编织屏蔽层3和导体单元。导体单元包括导体线芯4和设于导体线芯外侧的绝缘层5。
17.导体线芯4包括直径为0.142mm~0.158mm导体单丝,7根导体单丝束绞成为股线,股线的节径比为27
‑
29倍,股线外侧依次绞合第一导体层4
‑
1、第二导体层4
‑
2和第三导体层4
‑
3,所述第一导体层4
‑
1由6根股线绞合而成,第一导体层4
‑
1的绞合节径比为17
‑
20倍,束绞的7根股线构成复绞导体,第二导体层4
‑
2由6根复绞导体绞合而成,第二导体层4
‑
2的绞合节径比为15
‑
18倍,第三导体层4
‑
3由12根复绞导体绞合而成,第三导体层4
‑
2的绞合节径比为11
‑
14倍,相邻导体层之间的绞合方向相反。
18.具体的,导体单丝采用镀锡软铜导体,采用24头多头拉丝机生产制得,并丝张力均匀一致,股线采用φ630高速双绞绞线机束合而成。导体单丝张力均匀稳定可控,避免因张力不均匀导致的单体断丝。导体的总绞合采用退扭的37盘笼绞生产,笼绞张力采用电磁分盘独立控制,张力可调可控。
19.电缆在高低温环境下(
‑
40℃~85℃)周期性变化,电缆做正弦复合振动(x轴振动幅度
±
15mm22万次;x轴振动幅度
±
8mm140万次,y轴振动幅度
±
10mm22万次)后测试电缆的绝缘电阻、耐电压测、耐压测试的漏电流、电线表面状态、单丝断裂等性能优异。
20.绝缘层5和护套层1采用高性能聚合物挤包绝缘经电子加速器辐照交联,分子结构网状固化,其是基于聚乙烯的聚烯烃化合物,包含一种基于溴化化合物的阻燃系统,该系统在着火时具有自熄性,并显着降低了释放出的烟气密度,阻燃系统适用于在工作温度下不分解的情况。绝缘层5的材料的硬度优良,邵氏硬度shore d25
±
3,抗张强度≥13mpa,断裂伸长率≥300%,材料密度1.19
±
0.03g/cm3。材料密度低,电缆轻量化效果明显。绝缘层5的绝缘电阻不受高温、低温、高湿等外界环境的影响,在经受高温、低温、高湿等试验测试后仍有优异的电性能和耐压性能。
21.绝缘层5和护套层1采用挤出一次成型。绝缘层5和护套层1的材料耐低温
‑
40℃,工
作温度可达125℃和150℃两个级别。
22.编织屏蔽层3由镀锡铜丝0.15mm
±
0.008mm编织而成,采用24或32锭高速编织机。外层绕包0.025
‑
0.036的铝塑复合薄膜作为复合屏蔽层2,编织角度控制在40
°‑
60
°
之间,绕包的重叠率控制在20%
‑
30%之间。编织和绕包铝塑复合膜一次完成。
23.实施例二
24.请参阅图2,一种新能源车内用耐振动柔性高压电缆,电缆自外向内依次为护套层1、复合屏蔽层2、编织屏蔽层3和三个导体单元。本实施例中导体单元与实施例一相同。
25.三个导体单元的绝缘层采用不同颜色区分,成缆采用退扭设备,成缆后不绕包。采用挤出的内衬层6,内衬层6的材料强度低小于等于6mpa,内衬层6的材料与绝缘层5的绝缘材料兼容不粘连且易剥离。
26.本新型通过导体的结构设计和工艺参数的匹配,确保产品的振动过程中,导体的基本单元有足够的长度和空间进行伸缩,振动过程不会造成因导体的位移而产生断裂。高性能聚合物的应用,确保了产品的柔软性能,在振动过程中,向导体施加的内力减小。同时绝缘和护套材料的耐环境性能优异,可以保证在高温、低温、湿度等条件下具有优异的电学和机械性能。内衬层的采用兼容不粘连且易剥离材料,起到了保护屏蔽层在振动过程中损伤绝缘,同时在线束加工中,不影响后续的加工。
27.以上所述仅为本实用新型的较佳实施例而已,并不用以限制本实用新型,凡在本实用新型的精神和原则之内所作的任何修改、等同替换和改进等,均应包含在本实用新型的保护范围之内。
再多了解一些
本文用于企业家、创业者技术爱好者查询,结果仅供参考。