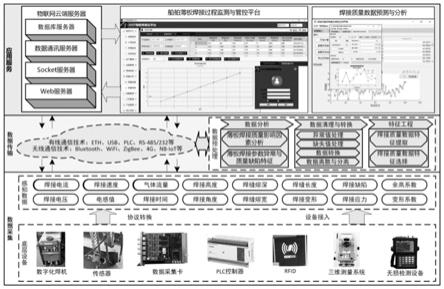
1.本发明属于涉及计算机集成制造技术领域,具体涉及一种大数据驱动的船舶薄板焊接质量预测方法。
背景技术:
2.船舶工业是国家高端装备制造业的重要组成部分,也是推动融合物联网、大数据、云计算等新一代信息技术的重点应用领域。在船舶建造过程中,逐渐呈现出全面推进数字化、网络化、智能化模式转变与传统技术升级趋势。焊接技术作为在船舶建造中最重要的工艺技术之一,其焊接工时一般占据着船体建造总工时的30%~40%。在水面舰艇及多数中小型船舶建造中,考虑到薄板结构本身具备重量轻、工艺性能好的特点,广泛应用板厚小于6mm的薄板结构以减轻船舶自重与提高航速等技术性能。但难以避免的是,在薄板的焊接过程中常发生严重形变和应变现象。然而,在大多数船舶制造企业中,质量管理通常是静态的质量管控,即采取质量计划下达、序后生产检验和质量统计报表等形式,并未能实现焊接过程的实时监测与焊接质量预测,导致质检效率低、质量反馈时效性差与质量控制滞后等问题。因此,针对船舶薄板结构焊接质量的实时监控与预测一直是船舶建造中亟需落地的技术与研究重点。
3.船舶薄板结构焊接是一个高度非线性、有多变量耦合作用和大量不确定因素相互影响的复杂过程,难以建立反映过程输入输出关系的精确数学模型。目前,基于经验知识与数理统计的方法也难以处理综合、复杂的质量问题,不能满足焊接质量的在线监测与精准预测的发展需求。
技术实现要素:
4.发明目的:为了克服现有技术中存在的不能满足焊接质量的在线监测与精准预测的发展需求的问题,提供一种大数据驱动的船舶薄板焊接质量预测方法。
5.技术方案:为实现上述目的,本发明提供一种大数据驱动的船舶薄板焊接质量预测方法,包括如下步骤:
6.s1:确定船舶薄板结构焊接中关键可控的质量指标,并对其影响因素进行了初步分析,基于工业物联网的技术体系,利用建立好的物联网组建框架,进行实时焊接数据的采集与上行传输;
7.s2:对采集的焊接质量影响因素数据进行关键数据特征优选,完成焊接大数据中初始特征集合的数据降维;
8.s3:通过建立好的自适应模拟退火粒子群算法优化的bp神经网络预测模型,根据数据降维后的数据特征,输出船舶薄板焊接质量预测结果。
9.进一步地,所述步骤s1中物联网组建框架建立面向船舶薄板结构焊接质量实时监测与预测,由数据感知、数据传输与预处理和应用服务三个层面组成。物联网组建框架的建模步骤具体包括以下步骤:
10.s1.1:在焊接工艺执行过程中,数据感知层主要实现对各类多源异构数据进行实时与准确地采集,从而为数据集成与分析阶段提供稳定的原始数据源。感知数据类型主要有焊接工艺参数、焊机设备执行状态信息与焊接质量参数等,采集方式可以通过接口与协议转换,或者接入外接智能感知设备进行操作;
11.s1.2:数据传输主要对各类采集到的多源异构数据进行联网聚合与传输,从而实现底层设备、应用服务与各类数据库间的互联互通。随着新一代通讯技术的成熟,针对工业级的信息通讯有很多方式可供选择,如蜂窝网络、5g、工业wi
‑
fi网络、zigbee与工业以太网等,根据实际需求与优势互补也可形成组合通讯方案,以满足远近传输与抗干扰能力、通信速率与稳定性等要求;
12.s1.3:船舶建造车间设备的多样性与应用系统的异构性造成了数据具备多源性与异构性特征,因此数据集成则是为了屏蔽数据之间类型与结构上的差异,以实现对数据进行统一存储、管理与分析。数据集成的关键技术包括数据储存管理与数据的预处理(数据清洗与转换、数据降维)。
13.进一步地,所述步骤s2中采用过滤式特征选择算法,对采集的焊接质量影响因素数据进行关键数据特征优选,根据各属性特征的权重计算结果,将权值大于阈值τ的特征子集作为焊接质量预测算法的输入变量。
14.进一步地,所述过滤式特征选择算法对采集的焊接质量影响因素数据进行关键数据特征优选的具体过程为:
15.a1:选取船舶薄板焊接质量影响因素数据集,并对数据集进行归一化处理;
16.a2:采用在relief算法的功能进行扩展得到的relief
‑
f,在不改变原有数据特征的基础上,采用特征评价准则与权重指标,对原始数据集的各个输入特征进行计算,得到各属性特征的权重计算结果;
17.a3:对初始特征集合进行过滤操作,即指定一个阈值τ,再选择更具有代表性与统一意义的数据特征,去除无关和冗余特征以达到数据降维的目的。
18.进一步地,所述步骤s2中根据算法输入的数据集d,样本抽样次数m,特征权重阈值δ与最近邻样本个数k,其计算过程包括如下步骤:
19.b1:初始化特征权值w(r)=0,特征权重集t为空集;
20.b2:开始迭代,从数据集d中随机选取示例x
i
,;
21.b3:从同类中找到x
i
的k个最近邻样本x
i,l,nh
,记作h
i
(c)(i=1,2,
…
,k,c=class(x
i
)),从不同类中找到x
i
的k个最近邻样本x
i,l,nm
,记作
22.b4:更新特征权值w(r)与t。
23.进一步地,所述步骤s3中bp神经网络预测模型的建立的基本思路为通过自适应模拟退火粒子群优化算法对bp神经网络的权重与阈值进行优化。具体而言,以预测模型的均方误差计算函数作为适应度函数,充分利用自适应模拟退火粒子群优化算法的全局搜索能力,将各神经网络节点的权重与阈值作为飞行粒子以求解适应度函数的最优解,从而改善bp神经网络预测模型的容易陷入局部极小点、收敛速度慢、鲁棒性差等缺陷。
24.具体包括如下步骤:
25.c1:优选焊接质量影响因素数据的关键数据特征并作为输入变量集合,再结合对应的焊接质量数据建立焊接质量预测算法的训练数据集;
26.c2:建立船舶薄板焊接质量的bp神经网络预测模型;
27.c3:以预测模型的均方误差计算函数作为适应度函数,将各神经网络节点的权重与阈值作为飞行粒子,通过粒子的速度与位置更新以求解适应度函数的最优解;
28.c4:将模拟退火算法的metropolis准则引入到粒子群算法的迭代寻优过程中,提高粒子群算法在迭代寻优过程中自身跳出局部最优解的能力。
29.进一步地,所述步骤c3中粒子每一次迭代都通过跟踪粒子本身的个体极值与种群的全局极值以更新粒子的位置,控制速度与位置更新的惯性权重系数w和学习因子表达式为:
[0030][0031][0032][0033]
其中,w
max
,w
min
是惯性权重系数的最大值和最小值;k是当前迭代次数,k
max
是最大迭代次数;c
1max
,c
1min
分别是自我学习因子的最大值和最小值,c
2max
,c
2min
分别是社会学习因子的最大值和最小值。
[0034]
进一步地,所述步骤c4中将模拟退火算法的metropolis准则引入到粒子群算法的迭代寻优过程中的具体表达式为:
[0035][0036][0037]
其中,表示在当前温度t(k)的个体解;p
t(k)
(i)为由产生的新解代替旧解的接受概率;t(k)表示在第k次退火的当前温度;μ表示降温系数。
[0038]
本发明一方面针对当前船舶焊接薄板结构的焊接质量预测难以结合领域大数据进行落地应用,基于工业物联网的技术体系,建立了面向船舶薄板结构焊接质量实时监测与预测的物联网组建框架,然后,在焊接物联网平台的基础上,采用过滤式特征选择算法,对采集到的焊接质量影响因素数据进行了关键数据特征优选,以完善焊接大数据的采集、传输与预处理;另一方面针对当前船舶焊接薄板结构焊接质量预测算法的泛化性能不足和无法平衡全局与局部搜索能力,本发明提出了一种自适应模拟退火粒子群算法优化的bp神经网络预测模型(sapso_bp),使其预测误差与算法性能在原有算法的基础上得到显著地优化,以满足船舶薄板结构的焊接质量实时监控与预测需求,并对焊接工艺的优化决策提供可靠性高的参考价值。
[0039]
随着新一代信息技术在船舶制造业中的广泛应用,焊接过程中会产生大规模监测数据,这些数据蕴含着丰富的焊接设备和焊接过程运行状态信息。因此,本发明利用大数据思维,在船舶建造车间的焊接过程中,能够对产生的海量数据中进行利用与挖掘,包括数据
融合处理、关联分析、性能预测与优化决策等,以实现焊接过程的在线监测与焊接质量的精准预测,并指导科学与合理的焊接工艺改进。
[0040]
有益效果:本发明与现有技术相比,具备如下优点:
[0041]
1、针对当前船舶焊接薄板结构的焊接质量预测难以结合领域大数据进行落地应用,本发明基于工业物联网的技术体系,建立了面向船舶薄板结构焊接质量实时监测与预测的物联网组建框架,有利于船舶焊接薄板结构的焊接过程中数据采集与传输,从而为实现实时大数据驱动的智能化服务提供支持。
[0042]
2、本发明在焊接物联网平台的基础上,采用过滤式特征选择算法,对采集的焊接质量影响因素数据进行了关键数据特征优选,以实现焊接大数据的初始特征集合过滤操作,即达到数据降维的目的。
[0043]
3、本发明针对当前船舶焊接薄板结构焊接质量预测存在缺陷,如算法的泛化性能不足和无法平衡全局与局部搜索能力,建立了一种sapso_bp预测模型,改善了bp神经网络预测模型的容易陷入局部极小点、收敛速度慢、鲁棒性差等缺陷,从而实现了对于船舶薄板焊接过程的在线监测与焊接质量的精准预测,提升了预测结果精度,为焊接工艺的优化决策提供可靠性高的参考价值。
附图说明
[0044]
图1是本发明的大数据驱动的船舶薄板焊接质量预测方法流程图;
[0045]
图2是本发明的基于工业物联网的船舶薄板结构焊接数据采集框架图;
[0046]
图3是本发明的sapso_bp算法流程图;
[0047]
图4是本发明的船舶薄板结构的焊接过程数据采集系统示意图。
具体实施方式
[0048]
下面结合附图和具体实施例,进一步阐明本发明,应理解这些实施例仅用于说明本发明而不用于限制本发明的范围,在阅读了本发明之后,本领域技术人员对本发明的各种等价形式的修改均落于本技术所附权利要求所限定的范围。
[0049]
本发明提供一种大数据驱动的船舶薄板焊接质量预测系统,其主要包括面向船舶薄板结构焊接质量实时监测与预测的物联网组建框架、焊接质量影响因素数据的特征选择方法、一种sapso_bp预测模型的构建方法、与船舶薄板结构的焊接过程数据采集系统。
[0050]
如图1所示,本实施例中应用该预测系统对船舶薄板焊接质量进行在线监测与预测,其具体的预测流程包括如下步骤:
[0051]
s1:确定船舶薄板结构焊接中关键可控的质量指标,并对其影响因素进行了初步分析,基于工业物联网的技术体系,利用建立好的物联网组建框架,进行实时焊接数据的采集与上行传输;
[0052]
s2:对采集的焊接质量影响因素数据进行关键数据特征优选,完成焊接大数据中初始特征集合的数据降维;
[0053]
s3:通过建立好的自适应模拟退火粒子群算法优化的bp神经网络预测模型,也叫作sapso_bp预测模型,根据数据降维后的数据特征集,输出船舶薄板焊接质量预测结果。
[0054]
基于上述方案,本实施例步骤s1中采用如图2所示的焊接数据采集框架(物联网组
建框架)进行实时焊接数据的采集与上行传输,该采集框架主要分为数据感知、数据传输与预处理和应用服务三个层面。
[0055]
在焊接工艺执行过程中,数据感知层主要实现对各类多源异构数据进行实时与准确地采集,从而为数据集成与分析阶段提供稳定的原始数据源。感知数据类型主要有焊接工艺参数、焊机设备执行状态信息与焊接质量参数等,采集方式可以通过接口与协议转换,或者接入外接智能感知设备进行操作。例如,对于一些非数字化智能设备的数据采集,可以通过电气电路的模拟信号进行采集,并通过布置智能传感设备的方式获取焊接设备的电流、电压、焊接速度与脉冲信号等,最终可由数据采集板,如pcl
‑
818l,进行模数转换、汇总融合与数据传送;对于大部分数字化智能设备的数据采集,则可以采用各类通讯接口或串口,plc的网络或者通信接口等多种方式对设备的执行参数与运行状态进行集中采集与汇总,并通过相应的通讯协议,如opc
‑
ua、mqtt等,实现应用程序、服务器与plc之间的数据读写操作。
[0056]
数据传输层主要对各类采集到的多源异构数据进行联网聚合与传输,从而实现底层设备、应用服务与各类数据库间的互联互通。随着新一代通讯技术的成熟,针对工业级的信息通讯有很多方式可供选择,如蜂窝网络、5g、工业wi
‑
fi网络、zigbee与工业以太网等,根据实际需求与优势互补也可形成组合通讯方案,以满足远近传输与抗干扰能力、通信速率与稳定性等要求。
[0057]
船舶建造车间设备的多样性与应用系统的异构性造成了数据具备多源性与异构性特征,因此,数据集成则是为了屏蔽数据之间类型与结构上的差异,以实现对数据进行统一存储、管理与分析。数据集成的关键技术包括数据储存管理与数据的预处理(数据清洗与转换、数据降维)。其中,数据存储管理是使数据价值最大化与数据预处理的基础,常见的数据库技术包括sql数据库,如mysql、oracle等,redis、hbase等类型的nosql数据库及其newsql数据库,以上几类数据库均有其特定的优势及其应用场景,具体部署可根据实际需求与应用场景混合使用,达到优势互补与效益最大化。
[0058]
数据的预处理是操作数据分析与挖掘的前提,不仅能够保证实测数据集的质量与格式,也可以有效避免数据分析过程中维数灾难问题。对于感知数据中缺失的、不规范的等一类数据,则需要采用数据筛选、数据修复、数据转换等手段,以提高数据的质量与统一数据格式,如采用etl与kettle等工具即可有效解决数据清洗与转换等问题。对于感知数据中无关联或冗杂等一些数据,则需要对其进行数据降维,从而从原始数据中提取更加可靠、价值更大的数据信息。数据降维可以通过数据特征提取或者数据特征选择来实现。其中,数据特征提取是将高维的特征向量变换为低维的数据特征向量,以获取具备具体物理意义或者统计意义的数据特征,如线性主成分分析方法等。数据特征选择则是,在不改变原有数据特征的基础上,根据特征评价准则或者量化权重等指标,从原始数据特征集合中选择更具有代表性与统一意义的数据特征,去除无关和冗余特征以达到数据降维的目的。
[0059]
本实施例的步骤s2中采用过滤式特征选择算法,对采集的焊接质量影响因素数据进行关键数据特征优选,具体过程为:
[0060]
a1:选取船舶薄板焊接质量影响因素数据集,并对数据集进行归一化处理;
[0061]
a2:采用在relief算法的功能进行扩展得到的relief
‑
f,在不改变原有数据特征的基础上,采用特征评价准则与权重指标,对原始数据集的各个输入特征进行计算,得到各
属性特征的权重计算结果;
[0062]
a3:对初始特征集合进行过滤操作,即指定一个阈值τ,再选择更具有代表性与统一意义的数据特征,去除无关和冗余特征以达到数据降维的目的。
[0063]
本实施例中采用relief算法的功能进行扩展得到的relief
‑
f。对于多分类问题,设单标签训练数据集d={(x1,y1),(x2,y2),...,(x
n
,y
n
)}可划分为|c|个类别,relief
‑
f可对属于第k
j
类(k
j
∈{1,2,
…
,|c|})的示例x
i
,分别在其第k
j
类与其他每个类的样本集中寻找x
i
的最近邻示例,作为示例x
i
的猜中近邻x
i,l,nh
与猜错近邻x
i,l,nm
(l=1,2,...,|c|;l≠k
j
),然后迭代更新属性特征r的特征权值w(r)。根据算法输入的数据集d,样本抽样次数m,特征权重阈值δ与最近邻样本个数k,其相应计算描述为:
[0064]
b1:初始化特征权值w(r)=0,特征权重集t为空集;
[0065]
b2:开始迭代,从数据集d中随机选取示例x
i
;
[0066]
b3:从同类中找到x
i
的k个最近邻样本x
i,nh
,记作h
i
(c)(i=1,2,...,k,c=class(x
i
)),从不同类中找到x
i
的k个最近邻样本x
i,l,nm
,记作
[0067]
b4:更新特征权值w(r)与t。计算公式为:
[0068][0069][0070]
式中diff(r,x1,x2)表示样本x1与x2在特征r上的距离,class(x
i
)表示样本x
i
包含的类标签,p(c)表示第c类结果标签的先验概率。
[0071]
根据各属性特征的权重计算结果,再对初始特征集合进行过滤操作,即指定一个阈值τ,设置原则符合切比雪夫不等式(a为接受无关特征的概率,m为样本数目),最后将权值大于阈值的特征子集作为焊接质量预测算法的输入变量。
[0072]
本实施例步骤s3中sapso_bp预测模型的建立的基本思路为通过自适应模拟退火粒子群优化算法对bp神经网络的权重与阈值进行优化。具体而言,以预测模型的均方误差计算函数作为适应度函数,充分利用自适应模拟退火粒子群优化算法的全局搜索能力,将各神经网络节点的权重与阈值作为飞行粒子以求解适应度函数的最优解,从而改善bp神经网络预测模型的容易陷入局部极小点、收敛速度慢、鲁棒性差等缺陷。
[0073]
bp神经网络是以误差逆传播算法作为训练算法的多层前馈神经网络,具有优良的多维函数映射能力、自学习和自适应与较好的泛化性能,其网络结构一般分别由若干个输入神经元、输出神经元与隐层神经元组成,而网络各层神经元之间的输入信号由连接权值进行传递,其中输出层与隐含层的神经元具有阈值与激活函数以控制着神经元的输出。传统的bp神经网络模型是比较成功的预测模型与应用最广泛的神经网络,但同时也存在着明显的缺陷。由于bp神经网络算法采用的是误差梯度下降策略,实质上是单点搜索算法,对于解决复杂非线性化问题,网络对初始网络权重与阈值非常敏感,而且网络的权值与阈值是通过沿局部改善的方向逐渐进行调整的,导致算法容易陷入局部极小点、收敛速度慢、鲁棒
性不好与网络性能低等问题。
[0074]
如图3所示,本实施例提供的sapso_bp预测模型的预测流程具体包括如下步骤:
[0075]
c1:优选焊接质量影响因素数据的关键数据特征并作为输入变量集合,再结合对应的焊接质量数据建立焊接质量预测算法的训练数据集;
[0076]
c2:建立船舶薄板焊接质量的bp神经网络预测模型;
[0077]
c3:以预测模型的均方误差计算函数作为适应度函数,将各神经网络节点的权重与阈值作为飞行粒子,通过粒子的速度与位置更新以求解适应度函数的最优解;
[0078]
c4:将模拟退火算法的metropolis准则引入到粒子群算法的迭代寻优过程中,提高粒子群算法在迭代寻优过程中自身跳出局部最优解的能力。
[0079]
步骤c3中在自适应模拟退火粒子群优化算法的迭代寻优过程中,粒子每一次迭代都通过跟踪粒子本身的个体极值与种群的全局极值以更新粒子的位置,移动方式由3个部分组成,分别反映维持先前速度的趋势,逼近历史最佳位置的趋势与群体合作与信息共享,其速度与位置更新的表达式为:
[0080]
v
i
(k 1)=w*v
i
(k) c1r1(p
best.i
(k)
‑
x
i
(k)) c2r2(g
best
‑
x
i
(k))
[0081]
x
i
(k 1)=x
i
(k) v
i
(k 1)
[0082]
其中各部分的关键参数为:w为惯性权重系数;c1、c2分别是自身认知因子和社会认知因子;v
i
(k)与x
i
(k)分别表示第i个粒子在第k次迭代时的速度与位置;r1、r2为[0,1]范围内的均匀随机数;p
best,i
(k)与g
best
分别表示第i个粒子在第k次迭代时的个体最优解与全局最优解。
[0083]
w与c1、c2是控制粒子群算法迭代的重要参数,惯性权重系数w控制着粒子飞行的惯性与算法搜索能力的强弱,c1、c2直接影响着粒子向个体最优或者群体最优的运动偏向,因此,为实现粒子群算法的自适应性,进行动态调整w与c1、c2以控制局部与全局的寻优搜索策略与协同共享能力,本实施例选取负的双曲正切曲线的非线性控制策略,以控制惯性权重系数w的变化,而c1、c2的取值随粒子的迭代次数k变化,其参数设置如下:
[0084][0085][0086][0087]
其中:w
max
,w
min
是惯性权重系数的最大值和最小值;k是当前迭代次数,k
max
是最大迭代次数;c
1max
,c
1min
是自我学习因子的最大值和最小值,c
2max
,c
2min
分别社会学习因子的最大值和最小值;
[0088]
此外,为有效降低粒子群算法陷入局部最优解的概率,步骤c4将模拟退火算法的metropolis准则引入到粒子群算法的迭代寻优过程中,使每次迭代后模拟初始温度t(0)线性衰减过程,不仅能够接受优解,也能以根据以概率p
t
接受较差的解,从而提高粒子群算法在迭代寻优过程中自身跳出局部最优解的能力,具体操作如下:
[0089][0090][0091]
其中,表示在当前温度t(k)的个体解;p
t(k)
(i)为由产生的新解代替旧解的接受概率;t(k)表示在第k次退火的当前温度;μ表示降温系数。
[0092]
如图4所示,本实施例还提供一种采集系统,用于采集本实施例中船舶薄板结构的焊接过程数据,实验采用的船舶薄板材料为一般强度船体结构用钢
‑
q235b船用普碳钢,具体尺寸为500mm
×
500mm
×
5mm,其焊接工艺选择的是船舶薄板中心堆焊。数字化焊机选择的是panasonic公司的全数字熔化极气体保护焊机,型号为gp5系列的yd
‑
350gs5,标准内置iot模块和模拟通讯接口。自动化焊接机器人采用的是panasonic公司的tawers焊接机器人,可实现薄板的极低飞溅焊接。为了采集关键的焊接过程参数,实验搭载与配置一些智能传感器与精密测量仪器。实验中使用了ccd摄像头对熔池图像进行高速抓取,并将采集到的数据与图像,通过图像采集卡传输到了计算机中。焊丝干伸长传感器可以对焊接过程中焊丝的伸长长度进行监测。电感测量仪器采用的是th2810,可以对焊接过程中的电感量进行测量。此外,实验中还采用了保护气体质量流量控制器与x射线残余应力分析仪器,能够分别对焊接工艺中的焊接气流量与焊缝残余应力进行测量。
[0093]
数据的传输采用的设备有通讯接口装置与串口联网模组。对于数字化焊接与焊接机器人,plc提供了模拟量输入模块,可接收由变送器转换后的标准电压或电流信号,通过plc的计算和分析发出指令,将分析后的数值通过通讯接口装置与通讯协议显示在焊接现场人机界面(hmi)上。实验中配置的智能传感器本身具备通讯接口,如rs232或者rs485,因此,采用串口联网模组能够与各传感器建立连接与协议转换,通过射频天线与wan/lan转换组件,实现wifi无线传输与组建ethernet,从而支持焊接现场与上位机之间的焊接数据读写操作。案例中采用了mysql数据库,实现了对焊接数据的储存、管理与共享。
再多了解一些
本文用于企业家、创业者技术爱好者查询,结果仅供参考。