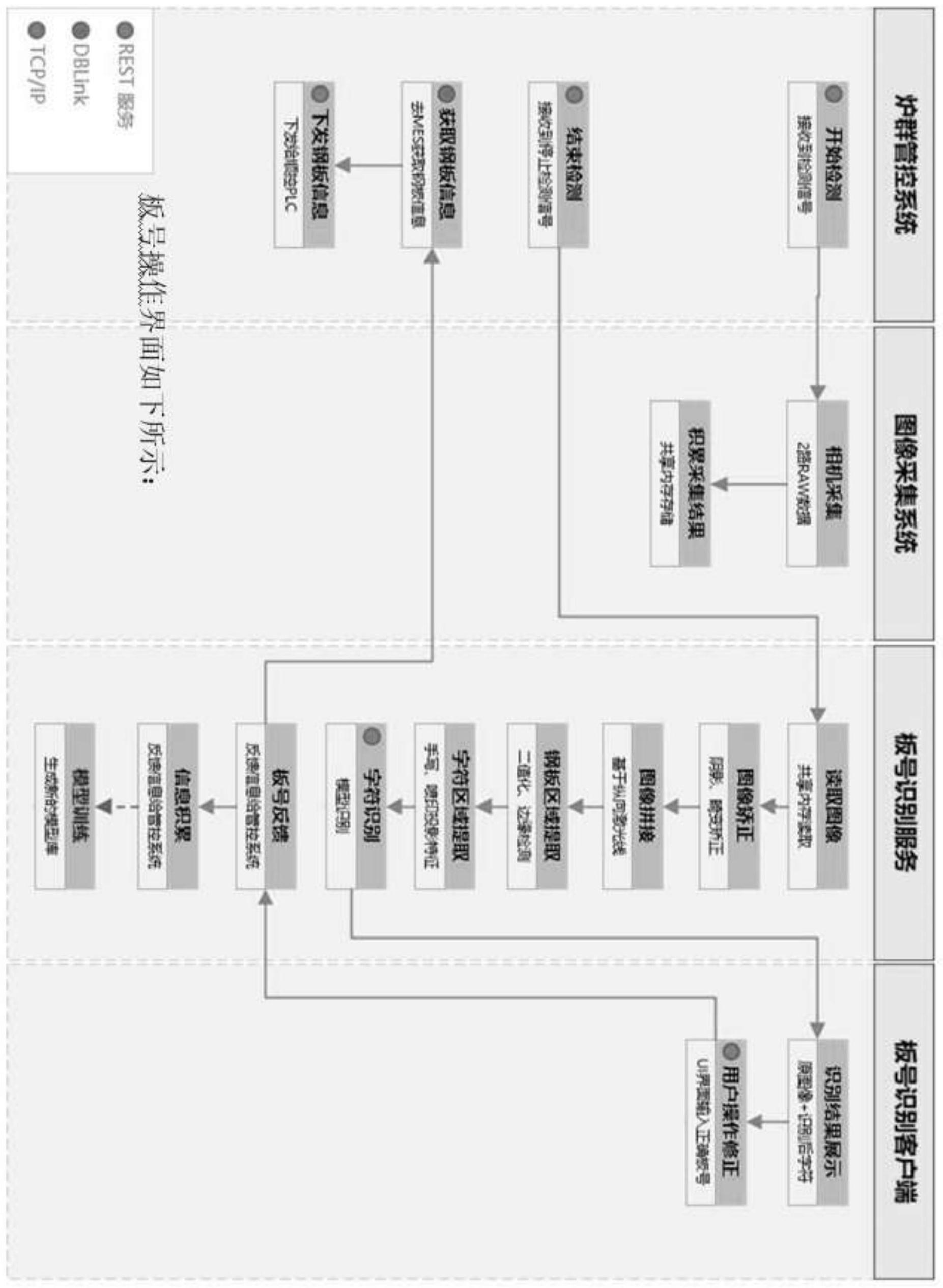
1.本发明涉及钢铁生产技术领域,特别是涉及一种宽厚板全线自动化跟踪方法。
背景技术:
2.随着钢材市场竞争的日益激烈,钢铁应用场景不断增多。目前,宽厚板厂热处理线物料自动跟踪范围从热处理炉上料辊道到淬火机为止,钢板出淬火机后基本上靠人工跟踪,操作上下横移台架、矫直机(矫直机二级模型功能使用效果较差)、冷床、标识和相关辊道,直至产品入库。这种方式容易导致生产计划和实绩匹配性较差,生产效率不高,已经不能满足需要。
技术实现要素:
3.本发明针对上述技术问题,克服现有技术的缺点,提供1.一种宽厚板全线自动化跟踪方法,包括(一)5#热处理炉、淬火机区域1)5#热处理炉入口新增 1 套板号识别设备,自动读取钢板号传输至5#热处理炉二级系统,二级系统自动根据生产计划下达作业指令、热处理工艺,确定好后,系统启动辊道,自动入炉;2)添加钢板实际在炉工艺与技术要求工艺比对功能,工艺不符的有提醒、有报错;3)热处理炉钢板加热趋势曲线自动生成,对应每块钢板,mes 系统中可查询可导出;(二)矫直机区域矫直机机前辊道新增 1 台表喷机,用于淬火后钢板号喷印,用于物料的数据化跟踪;同时新增 1 套板号识别设备,用于钢板上线返矫时,系统自动识别钢板号;(三)标印机区域标印机入口辊道前新增 1 套板号识别设备,自动识别钢板号;(四)新增热处理线物料全自动跟踪系统全线 l21)全线 l2用于物料跟踪,物料跟踪从 5#热处理炉、6#热处理炉前辊道开始覆盖5#热处理炉炉前上料辊道到对中位置、淬火机机后、横移、矫直、冷床及标印区;2)新增全线 l2 与 mes 的通讯接口、全线 l2 与淬火机 l2 接口、全线 l2 与矫直机 l2接口、全线 l2 与标印机 l2 接口、全线 l2 与新增6#热处理炉、新增标印机 l2 接口;3)新增全线 l2 与新增全线 l1 系统的通讯功能;(五)改造热处理全线基础自动化控制系统全线 l11)新增 22 套激光测距仪及电脑操作终端、交换机等基础自动化系统的硬件设施及现场传感设备;2)对原有基础自动化 l1 系统应用软件进行改造,增加自动和半自动功能,完善
与之配套的网络系统及与相关其他系统的接口,即与全线 l2、新增6#热处理炉、新增表喷机、新增6#热处理炉项目的标印机、新增板号识别设备及各设备 l1。
4.本发明进一步限定的技术方案是:前所述的一种宽厚板全线自动化跟踪方法,mes改造如下:钢板作业指示数据抛送全线 l2;钢板流向计划抛送全线 l2;mes 自动接收钢板流向实绩数据;钢板流向实绩收集统计;mes 自动接收矫直实绩、标印结果;报表。
5.前所述的一种宽厚板全线自动化跟踪方法,板号识别系统如下:通过视觉采集设备拍摄辊道上运行中的钢板,抓取文字区域进行内容识别,以视觉检测的方式识别板号,支持手写和喷印两种书写方式的内容识别;板号校验:根据识别信息自动检索生产计划,通过计划数据库信息进行识别板号的二次确认;板号抓图显示:hmi 界面除了显示检测结果外,还显示板号截图,操作人员可通过截图查看原始板号信息进行二次确认;模糊匹配:板号书写质量不佳,出现涂抹、划痕导致板号只能被部分识别时,通过生产计划数据库进行模糊查询,推送显示几种匹配度高的板号信息供操作工选择;声音提示:执行完板号识别工序后,系统发出提示音,提醒操作人员执行板号确认操作。
6.前所述的一种宽厚板全线自动化跟踪方法,表喷系统如下:钢板到达喷印位置停止后,全线 l1 的位置检测器发出钢板到位信号给表喷机,表喷机接到全线 l2/人工输入的钢板喷号信息,表喷机自动投入喷号过程循环,表喷机启动、输送辊道停止运行、表喷机与辊道信号联锁,待所有的字符喷完,辊道与表喷机间的联锁解除,钢板通过矫直机继续下一步物流方向,表喷机等待下一个待喷号的钢板;对热处理后的淬火钢板进行喷号标识,使钢板与热处理前的数据进行一一对应,标识钢板温度 0
‑
100℃,标识完成钢板由磁力运输机吊下线。
7.前所述的一种宽厚板全线自动化跟踪方法,全线 l2系统如下:1)系统功能模块生产计划管理:接收 mes 下发的钢板 pdi、生产计划以及生产工艺信息;物料在线跟踪:生产线区域范围内钢板微跟踪定位;生产实绩管理:从物料上线、装炉、出炉、横移等所有工序实绩记录;生产趋势管理:热处理炉板温变化趋势、炉温变化趋势,高温计检测趋势以及淬火机流量趋势等大数据采集、可视化展示;数据报表管理:生产信息、工艺信息以及跟踪等信息数据支持报表导出,同时支持日报、班报、月报自动生成及推送;hmi 人机操作画面:包括区域正线跟踪、生产计划、上下显示核定、通讯状态维护、生产实绩、趋势数据等界面;
2)系统架构全线 l2 硬件系统主要由服务器1 台、工程师站、 2 台客户端即矫直和标印操作室各配置 1 台、网络设备组成 client/server 体系结构,其中 server 端采用分布式部署,在线跟踪、在线跟踪、数据采集、模型控制等采用独立服务方法发布,彼此之间采用数据总线进行消息交互;客户端采用轻量化设计,支持多终端同时登录运行;3)服务端核心业务服务:负责生产计划、物料跟踪、生产实绩、生产趋势等信息的业务管理,中间结果采用 redis 作为缓存介质,支持内存以及硬盘两种持久化方式;通讯控制模块:负责与 mes、l1 以及其他 l2 过程控制系统的通讯管理;趋势数据管理模块:提供炉温、板温以及其他能耗的趋势数据存取功能,存储方式采用时序数据库;应用服务接口:提供给 client 端的访问接口,用于数据检索,数据录入等hmi 数据交互功能,服务器通过双绞线接入到 l2/l3 中心交换机,通过中心交换机与 mes 主机相连,服务器通过光纤接入到 l1 网络,以便和基础自动化的 hmi 服务器进行通信,在全线 l2 与 mes 之间新增防火墙进行隔离。
8.前所述的一种宽厚板全线自动化跟踪方法,全线 l1系统如下:1)l1 系统的改造范围是从 5#热处理炉炉前输入辊道开始至热处理标印机 p11 辊道的区域,包括在线辊道控制、横移装置、冷床;2)区域范围:5#热处理炉输入辊道、横移装置输入辊道、横移装置、横移装置输出辊道、矫直机入口辊道、矫直机出口辊道、冷床输入辊道、冷床本体、冷床输出辊道、成品标印机入口辊道、成品标印机机后辊道、6#热处理炉输入辊道、6#热处理炉输出辊道、新增成品标印机机后延长辊道、新增冷床输出延长辊道;3)区域线上钢板的跟踪:跟踪区域包括: 热处理区所有的线上辊道、横移装置及冷床;跟踪实现以下功能:将整个热处理区设计为一个连续的坐标系;该区域的钢板具有 x 方向即辊道方向和 y 方向即横移装置方向/冷床方向的跟踪功能;钢板的跟踪信息包括头部位置(x,y)、长度、宽度、钢板号;钢板在横移上料辊道摆动功能;钢板在横移下料辊道摆动功能;新增成品标印机机后延长辊道控制;新增冷床输出延长辊道控制;新增冷床输出延长辊道与6#热处理炉项目新增标印机之间的联锁;6#热处理炉输出辊道与横移下料装置、横移下料辊道之间的联锁;钢板在冷床输出延长辊道摆动功能;4)l1 系统根据全线 l2 指令完成钢板的自动物流控制,主要功能如下:l1 接收全线 l2 系统下发的下一个板区指令,并根据指令完成钢板的自动搬运功能;
l1 接收全线 l2 系统下发的钢板下线指令,并根据指令完成钢板下线;l1 接收全线 l2 系统下发的钢板上线指令,并根据指令完成钢板上线;5)控制系统的组成:plc 控制柜及 hmi:plc 系统利用原全线 l1 级系统,采用 tcp/ip 以太网完成与热处理后道控制系统之间的数据相互传递、信号联络和通讯,拓展现有远程从站et200mi/o模块,用于采集现场新增传感器信号,与控制器之间采用profibusdp网进行数据交换与通讯;hmi 系统采用运行版,在操作室新配置3台hmi操作员站,hmi 系统采用可编程序软件wincc v7.2;hmi 操作员站主要实现功能如下:反映生产线流程作业及控制画面;生产线主画面,反映主要设备工作状态;反映物流信息、设备状态信息;过程数据显示、设定值显示与修正;数据输入、数据存储和调用;设备标定功能;选择类操作,包括操作模式选择;控制类操作,直接控制设备的运行和停止;维护性操作,用于系统的监控、维护;对网络系统的状态显示及故障诊断;plc 模块诊断信息;联锁状态显示;作业事件信息、各类故障及报警信息的显示、记录与打印;pda:用原有 pda 硬件系统,升级原有配置数据,用于热处理区域信号采集以及数据分析;远程io柜,拓展远程io模块;就地操作箱io柜就地操作箱保持不变。
9.前所述的一种宽厚板全线自动化跟踪方法,数据分析系统如下:与原有产线中各个设备的 l1 系统、l2 系统进行数据对接,完善跟踪数据反馈;增加各个仪表设备的大数据采集能力,提供海量数据采集能力,支持小于50ms的数据采集频度,数据高压缩比长久保存;多角度的数据分析功能,针对采集的高频数据进行故障预警、工艺曲线分析、产能分析以及能耗分析等,通过数字看板直观查看;生产过程能力评价功能,统计评价各牌号规格的关键工艺参数,用于保证生产质量;关键工艺参数异常统计功能,用于统计时间范围内加热时间、出炉温度、反红温度等关键工艺参数是否符合工艺设定的上下限,以及统计工艺超限异常;报表导出推送功能,所有显示数据报表均支持导出操作,以及预留接口,支持推送至erp、mes系统。
10.本发明的有益效果是:(1)本发明主要应用于宽厚板热处理线智能生产及管理,从热处理炉装钢开始,到淬火机出口到钢板入库之间所有在线工艺过程的信息自动化控制系统改造,包括淬火机机后、横移、矫直、冷床、标印工序、翻板机及入库辊道的物料自动跟踪、设定数据下发、实际数据的采集及基础自动化的自动和半自动控制等,并对矫直机模型进行改进,提升宽厚板热处理区域生产数据跟踪及流程控制水平,满足宽厚板智能制造管理水平提升的需求;(2)本发明为实现热处理产线全自动物料跟踪,除新增表喷机和板号识别设备外,还补齐该区域实现自动化和信息化所需要的网络及控制设备,在此基础之上对物流控制进行软件开发,最终实现热处理全线物料跟踪全自动控制;(3)本发明中板号识别系统主要用于辊道上运动钢板的在线识别,可大幅度减轻人工抄号、查号的工作量,提升产线运作效率,同时避免错号的现象;(4)本发明中数据平台分析系统负责整合炉群范围内各单体设备,进行集中的数据采集、分析、控制,在原有单体设备自动化控制的基础上,实现整条生产线的自动化控制;(5)本发明改造后,实现自动跟踪标识,间接效益是避免了标识错误,降低了质量异议的风险,提高了对客户的信誉度。
附图说明
11.图1为本发明中板号识别流程。
具体实施方式
12.本实施例提供的一种宽厚板全线自动化跟踪方法,包括(一)5#热处理炉、淬火机区域1)5#热处理炉入口新增 1 套板号识别设备,自动读取钢板号传输至5#热处理炉二级系统,二级系统自动根据生产计划下达作业指令、热处理工艺(加热温度、升温速率、保温时间等),确定好后,系统启动辊道,自动入炉;2)添加钢板实际在炉工艺与技术要求工艺比对功能,工艺不符的有提醒、有报错;3)热处理炉钢板加热趋势曲线自动生成,对应每块钢板,mes 系统中可查询可导出;(二)矫直机区域矫直机机前辊道新增 1 台表喷机,用于淬火后钢板号喷印,用于物料的数据化跟踪;同时新增 1 套板号识别设备,用于钢板上线返矫时,系统自动识别钢板号,避免人工核实错误影响矫直参数调整,造成设备损伤,提高钢板矫直合格率;(三)标印机区域标印机入口辊道前新增 1 套板号识别设备,自动识别钢板号,不再需要人工核对下发,每块钢板标识用时缩短到 2
‑
3 分钟,为后期热处理产能提高到月产 2.9 万吨保驾护航做好准备,也加快了精整转运过来的余材、剖分、返矫板的标识速度;(四)新增热处理线物料全自动跟踪系统全线 l21)全线 l2用于物料跟踪,物料跟踪从 5#热处理炉、6#热处理炉前辊道开始覆盖5#热处理炉炉前上料辊道到对中位置、淬火机机后、横移、矫直、冷床及标印区;
2)新增全线 l2 与 mes 的通讯接口、全线 l2 与淬火机 l2 接口、全线 l2 与矫直机 l2接口、全线 l2 与标印机 l2 接口、全线 l2 与新增6#热处理炉、新增标印机 l2 接口;3)新增全线 l2 与新增全线 l1 系统的通讯功能;(五)改造热处理全线基础自动化控制系统全线 l11)新增 22 套激光测距仪及电脑操作终端、交换机等基础自动化系统的硬件设施及现场传感设备;2)对原有基础自动化 l1 系统应用软件进行改造,增加自动和半自动功能,完善与之配套的网络系统及与相关其他系统的接口,即与全线 l2、新增6#热处理炉、新增表喷机、新增6#热处理炉项目的标印机、新增板号识别设备及各设备 l1。
13.mes改造如下:钢板作业指示数据抛送全线 l2;钢板流向计划抛送全线 l2;mes 自动接收钢板流向实绩数据;钢板流向实绩收集统计;mes 自动接收矫直实绩、标印结果;报表。
14.板号识别系统如下:通过视觉采集设备拍摄辊道上运行中的钢板,抓取文字区域进行内容识别,以视觉检测的方式识别板号,支持手写和喷印两种书写方式的内容识别,识别流程如图1;板号校验:根据识别信息自动检索生产计划,通过计划数据库信息进行识别板号的二次确认,提升检测准确性;板号抓图显示:hmi 界面除了显示检测结果外,还显示板号截图,操作人员可通过截图查看原始板号信息进行二次确认,以此避免误识别时,还需要操作人员去现场查看的操作;模糊匹配:板号书写质量不佳,出现涂抹、划痕导致板号只能被部分识别时,通过生产计划数据库进行模糊查询,推送显示几种匹配度高的板号信息供操作工选择;声音提示:执行完板号识别工序后,系统发出提示音,提醒操作人员执行板号确认操作。
15.表喷系统如下:钢板到达喷印位置停止后,全线 l1 的位置检测器发出钢板到位信号给表喷机,表喷机接到全线 l2/人工输入的钢板喷号信息,表喷机自动投入喷号过程循环,表喷机启动、输送辊道停止运行、表喷机与辊道信号联锁,待所有的字符喷完,辊道与表喷机间的联锁解除,钢板通过矫直机继续下一步物流方向,表喷机等待下一个待喷号的钢板;对热处理后的淬火钢板进行喷号标识,使钢板与热处理前的数据进行一一对应,标识钢板温度 0
‑
100℃,标识完成钢板由磁力运输机吊下线。
16.全线 l2系统如下:1)系统功能模块生产计划管理:接收 mes 下发的钢板 pdi、生产计划以及生产工艺信息;
物料在线跟踪:生产线区域范围内钢板微跟踪定位;生产实绩管理:从物料上线、装炉、出炉、横移等所有工序实绩记录;生产趋势管理:热处理炉板温变化趋势、炉温变化趋势,高温计检测趋势以及淬火机流量趋势等大数据采集、可视化展示;数据报表管理:生产信息、工艺信息以及跟踪等信息数据支持报表导出,同时支持日报、班报、月报自动生成及推送;hmi 人机操作画面:包括区域正线跟踪、生产计划、上下显示核定、通讯状态维护、生产实绩、趋势数据等界面;2)系统架构全线 l2 硬件系统主要由服务器1 台、工程师站、 2 台客户端即矫直和标印操作室各配置 1 台、网络设备组成 client/server 体系结构,其中 server 端采用分布式部署,在线跟踪、在线跟踪、数据采集、模型控制等采用独立服务方法发布,彼此之间采用数据总线进行消息交互;客户端采用轻量化设计,支持多终端同时登录运行;3)服务端核心业务服务:负责生产计划、物料跟踪、生产实绩、生产趋势等信息的业务管理,中间结果采用 redis 作为缓存介质,支持内存以及硬盘两种持久化方式,出现故障时可快速恢复;通讯控制模块:负责与 mes、l1 以及其他 l2 过程控制系统的通讯管理;趋势数据管理模块:提供炉温、板温以及其他能耗的趋势数据存取功能,存储方式采用时序数据库,保证查询速度不随数据量级变化而变化,始终保持较高的查询效率;应用服务接口:提供给 client 端的访问接口,用于数据检索,数据录入等hmi 数据交互功能,服务器通过双绞线接入到 l2/l3 中心交换机,通过中心交换机与 mes 主机相连,服务器通过光纤接入到 l1 网络,以便和基础自动化的 hmi 服务器进行通信,在全线 l2 与 mes 之间新增防火墙进行隔离,本次项目全线 l2 服务器配置360 工业版杀毒软件,其余工程师站及终端配置 360 白名单。
17.全线 l1系统如下:1)l1 系统的改造范围是从 5#热处理炉炉前输入辊道开始至热处理标印机 p11 辊道的区域,包括在线辊道控制、横移装置、冷床;2)区域范围:5#热处理炉输入辊道、横移装置输入辊道、横移装置、横移装置输出辊道、矫直机入口辊道、矫直机出口辊道、冷床输入辊道、冷床本体、冷床输出辊道、成品标印机入口辊道、成品标印机机后辊道、6#热处理炉输入辊道、6#热处理炉输出辊道、新增成品标印机机后延长辊道p10、p11、新增冷床输出延长辊道n13、n14、n15;3)区域线上钢板的跟踪:跟踪区域包括: 热处理区所有的线上辊道、横移装置及冷床;跟踪实现以下功能:将整个热处理区设计为一个连续的坐标系;该区域的钢板具有 x 方向即辊道方向和 y 方向即横移装置方向/冷床方向的跟踪功能;钢板的跟踪信息包括头部位置(x,y)、长度、宽度、钢板号;
钢板在横移上料辊道(n6a、n7a)摆动功能;钢板在横移下料辊道(n6、n7)摆动功能;新增成品标印机机后延长辊道(p10、p11)控制;新增冷床输出延长辊道(n13、n14、n15)控制;新增冷床输出延长辊道与6#热处理炉项目新增标印机之间的联锁;6#热处理炉输出辊道与横移下料装置、横移下料辊道之间的联锁;钢板在冷床输出延长辊道(n13、n14、n15)摆动功能;4)l1 系统根据全线 l2 指令完成钢板的自动物流控制,主要功能如下:l1 接收全线 l2 系统下发的下一个板区指令(next plate zone),并根据指令完成钢板的自动搬运功能;l1 接收全线 l2 系统下发的钢板下线指令,并根据指令完成钢板下线;l1 接收全线 l2 系统下发的钢板上线指令,并根据指令完成钢板上线;5)控制系统的组成:plc 控制柜及 hmi:plc 系统利用原全线 l1 级系统,采用 tcp/ip 以太网完成与热处理后道控制系统之间的数据相互传递、信号联络和通讯,拓展现有远程从站et200mi/o模块,用于采集现场新增传感器信号,与控制器之间采用profibusdp网进行数据交换与通讯;hmi 系统采用运行版,在操作室新配置3台hmi操作员站,hmi 系统采用可编程序软件wincc v7.2;hmi 操作员站主要实现功能如下:反映生产线流程作业及控制画面;生产线主画面,反映主要设备工作状态;反映物流信息、设备状态信息;过程数据显示、设定值显示与修正;数据输入、数据存储和调用;设备标定功能;选择类操作,包括操作模式选择;控制类操作,直接控制设备的运行和停止;维护性操作,用于系统的监控、维护;对网络系统的状态显示及故障诊断;plc 模块诊断信息;联锁状态显示;作业事件信息、各类故障及报警信息的显示、记录与打印;pda:用原有 pda 硬件系统,升级原有配置数据,用于热处理区域信号采集以及数据分析;远程io柜,拓展远程io模块;就地操作箱io柜就地操作箱保持不变。
18.数据分析系统如下:与原有产线中各个设备的 l1 系统、l2 系统进行数据对接,完善跟踪数据反馈;
增加各个仪表设备的大数据采集能力,提供海量数据采集能力,支持小于50ms的数据采集频度,数据高压缩比长久保存;多角度的数据分析功能,针对采集的高频数据进行故障预警、工艺曲线分析、产能分析以及能耗分析等,通过数字看板直观查看;生产过程能力评价功能,统计评价各牌号规格的关键工艺参数,用于保证生产质量;关键工艺参数异常统计功能,用于统计时间范围内加热时间、出炉温度、反红温度等关键工艺参数是否符合工艺设定的上下限,以及统计工艺超限异常;报表导出推送功能,所有显示数据报表均支持导出操作,以及预留接口,支持推送至erp、mes系统。
19.本发明改造后,在钢板入炉前,无需人工读取并输入板号,按平均每次节约24.5秒计算,年节约时间:0.41分钟/张*110张/天*337.7天(设备年作业天数)/60分钟=152.06小时,每小时热处理产量平均约22.2吨,年提高产量:152.06小时*22.2吨/小时=3375.8吨,年增益:3375.8吨*0.05万元/吨=168.79万元。
20.因人工输入错误造成的标印错误每年可减少五次。钢板发运至客户目的地,客户发现后,要派人携带标印工具前往确认处理,若实物错误,需要换货,由此产生的费用平均8000元/次。此项避免质量损失:0.8万元/次*5=4万元。
21.直接效益共计:168.79万元 4万元=172.79万元。
22.除上述实施例外,本发明还可以有其他实施方式。凡采用等同替换或等效变换形成的技术方案,均落在本发明要求的保护范围。
再多了解一些
本文用于企业家、创业者技术爱好者查询,结果仅供参考。