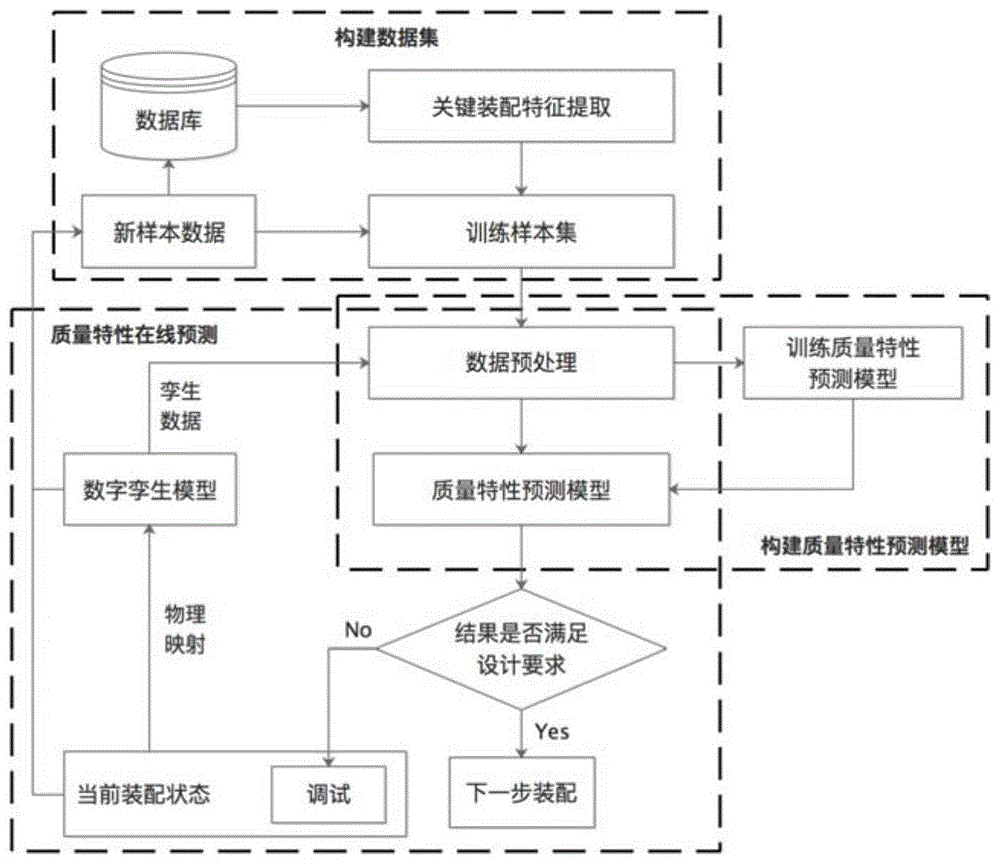
本发明涉及高精密产品装配技术领域,尤其涉及面向装配质量预测的高精密产品数字孪生可计算性方法。
背景技术
像电液伺服阀、机器人传动机构等高精密产品广泛应用于航天、船舶、化工等领域。高精密产品装配工艺复杂、装配精度要求较高。在装调过程中,为了获取质量特性数据通常需要反复采用试验台进行测试,从而指导实际调试操作。采用试验台测试的方法不仅效率较低,影响整个装配周期,同时耗费大量的如人力、物力等资源。为此,在装调过程中采用智能算法对质量特性进行预测是十分有意义的。采用智能算法进行质量特性预测最为关键的是数据的获取。当前部分学者对高精密产品质量特性进行预测是在装配完成后,通过采集的装配过程数据进行预测,这种方式通常需要大幅度拆装,不利于提高装配效率。
近年来,随着机器学习、大数据、云计算和IoT等技术的快速发展,使产品装配技术由数字化模型仿真为主的虚拟装配逐渐向虚实深度融合的智能化装配方向发展。数字孪生通过集成新一代信息技术实现了虚拟空间与物理空间的信息交互与融合,通过构建产品高保真数字孪生模型可以真实刻画产品模型随装配过程的动态演变。鉴于此,本发明提出了一种面向装配质量预测的高精密产品数字孪生可计算性方法。
技术实现要素:
本发明的目的是通过数字孪生的演变规律,在高精密产品装调过程中获取关键装配特征孪生数据,实现质量特性在线预测,有效减少装调过程的逆向操作。
为了实现上述目的,本发明采用了如下技术方案:
面向装配质量预测的高精密产品数字孪生可计算性方法,包括以下步骤:
S1、构建数据集模块:根据历史数据对影响质量特性的关键装配特征进行提取,形成训练样本集;
S2、构建质量特性预测模型模块:对S1中形成的训练样本集进行预处理,用以训练智能预测模型;
S3、构建质量特性在线预测模块:根据当前物理装配状态向数字孪生模型进行映射,作为扰动数据使数字孪生模型演化获取孪生数据,实现装调质量特性在线预测。
优选地,所述S1采用基于信息熵的关键特征提取方法,在综合考虑相关性、互补性和冗余性的基础上,设计关键装配特征参数的入选测度fE。在已知某质量特性Pi和当前关键装配特征集G的情况下,对装配特征与质量特性的关联关系进行度量。通过综合考虑三种关联关系来筛选具备最大相关性、最大互补性和最小冗余性的参数作为关键装配特征参数:
式中,表示候选装配特征xi和质量特性Pi之间的相关性;表示候选装配特征xi与关键装配特征集G之间的冗余性;Com(xi,pi,G)表示候选装配特征xi对于当前关键装配特征集G的互补性;α和β是权值变量,其由试验结果分析确定,且α,β,(α β)∈[0,1]。
优选地,所述S2中提到的质量特性预测模型模块中采用的智能算法可以根据不同数据量进行选择,且通过不断装配累计的数据进行自我训练。
优选地,所述S3中提到的质量特性在线预测模块的具体操作步骤如下:
A1、获取当前物理装配装配状态数据,映射至数字孪生模型,其映射数据为零件空间位姿:
式中,d为位置矢量,s为方向矢量;
A2、将映射数据作为扰动因素使数字孪生模型进行演化,获取孪生数据,其中演化方法采用状态空间模型:
式中,i表示第i个装配工序,i∈(1,2,...,m);A(i)为系统矩阵,表示系统内部状态变量之间的联系;B(i)为转换矩阵,表示物理空间设备、夹具等位姿相对于孪生空间位姿的变换;E(i)也为转换矩阵,表示将装配过程中第i个装配工序中物理零件空间位姿相对于孪生空间位姿的变换;x(i)表示第i个装配工序下的状态向量;u(i)表示第i个装配工序下的设备、夹具等误差因素;φ(i)表示第i个装配工序下的零件加工误差因素;F(i)为转换矩阵;δ(i)为已孪数据影响因素;y(i)表示第i个装配工序下的装配特征向量;C(i)为观测矩阵,表示输出变量反应状态向量;表示装配环境(主要为温度)引起的误差,由于高精密产品的装配车间温度恒定,这里默认为零矩阵;
A3、在获取的孪生数据中提取关键装配特征数据作为质量特性在线预测模型的输入;
A4、质量特性在线预测模型输出预测结果;
A5、当预测结果不满足设计要求,则进行物理调试,否则执行下一步装配。
与现有技术相比,本发明提供了面向装配质量预测的高精密产品数字孪生可计算性方法,具备以下有益效果:
本发明针对现有的高精密产品装调过程质量特性需要经过反复测试而导致的装调效率低和资源浪费问题,提出了一种面向装配质量预测的高精密产品数字孪生可计算性方法,通过数字孪生的演变规律,在高精密产品装调过程中获取关键装配特征孪生数据,实现质量特性在线预测,有效减少装调过程的逆向操作;具体来说:
(1)通过构建高精密产品数字孪生模型,真实刻画了产品模型随物理装调过程的动态演变,形成的孪生数据作为质量特性预测模型的输入。
(2)通过采用信息熵的关键装配特征提取方法,实现了装配特征与质量特性之间关系的可解释性。
(3)通过构建智能化质量特性预测模型,实现了装调过程质量特性在线预测。
附图说明
图1为本发明提出的面向装配质量预测的高精密产品数字孪生可计算性方法的孪生数据驱动的高精密产品装调质量特性预测流程示意图;
图2为本发明提出的面向装配质量预测的高精密产品数字孪生可计算性方法的高精密产品数字孪生模型组成示意图。
具体实施方式
下面将结合本发明实施例中的附图,对本发明实施例中的技术方案进行清楚、完整地描述,显然,所描述的实施例仅仅是本发明一部分实施例,而不是全部的实施例。
实施例1:
请参阅图1-2;
面向装配质量预测的高精密产品数字孪生可计算性方法,包括以下步骤:
S1、构建数据集模块:根据历史数据对影响质量特性的关键装配特征进行提取,形成训练样本集;
S2、构建质量特性预测模型模块:对S1中形成的训练样本集进行预处理,用以训练智能预测模型;
S3、构建质量特性在线预测模块:根据当前物理装配状态向数字孪生模型进行映射,作为扰动数据使数字孪生模型演化获取孪生数据,实现装调质量特性在线预测。
S1采用基于信息熵的关键特征提取方法,在综合考虑相关性、互补性和冗余性的基础上,设计关键装配特征参数的入选测度fE。在已知某质量特性Pi和当前关键装配特征集G的情况下,对装配特征与质量特性的关联关系进行度量。通过综合考虑三种关联关系来筛选具备最大相关性、最大互补性和最小冗余性的参数作为关键装配特征参数:
式中,表示候选装配特征xi和质量特性Pi之间的相关性;表示候选装配特征xi与关键装配特征集G之间的冗余性;Com(xi,pi,G)表示候选装配特征xi对于当前关键装配特征集G的互补性;α和β是权值变量,其由试验结果分析确定,且α,β,(α β)∈[0,1]。
S2中提到的质量特性预测模型模块中采用的智能算法可以根据不同数据量进行选择,且通过不断装配累计的数据进行自我训练。
S3中提到的质量特性在线预测模块的具体操作步骤如下:
A1、获取当前物理装配装配状态数据,映射至数字孪生模型,其映射数据为零件空间位姿:
式中,d为位置矢量,s为方向矢量;
A2、将映射数据作为扰动因素使数字孪生模型进行演化,获取孪生数据,其中演化方法采用状态空间模型:
式中,i表示第i个装配工序,i∈(1,2,...,m);A(i)为系统矩阵,表示系统内部状态变量之间的联系;B(i)为转换矩阵,表示物理空间设备、夹具等位姿相对于孪生空间位姿的变换;E(i)也为转换矩阵,表示将装配过程中第i个装配工序中物理零件空间位姿相对于孪生空间位姿的变换;x(i)表示第i个装配工序下的状态向量;u(i)表示第i个装配工序下的设备、夹具等误差因素;φ(i)表示第i个装配工序下的零件加工误差因素;F(i)为转换矩阵;δ(i)为已孪数据影响因素;y(i)表示第i个装配工序下的装配特征向量;C(i)为观测矩阵,表示输出变量反应状态向量;表示装配环境(主要为温度)引起的误差,由于高精密产品的装配车间温度恒定,这里默认为零矩阵;
A3、在获取的孪生数据中提取关键装配特征数据作为质量特性在线预测模型的输入;
A4、质量特性在线预测模型输出预测结果;
A5、当预测结果不满足设计要求,则进行物理调试,否则执行下一步装配。
本发明针对现有的高精密产品装调过程质量特性需要经过反复测试而导致的装调效率低和资源浪费问题,提出了一种面向装配质量预测的高精密产品数字孪生可计算性方法,通过数字孪生的演变规律,在高精密产品装调过程中获取关键装配特征孪生数据,实现质量特性在线预测,有效减少装调过程的逆向操作;具体来说:通过构建高精密产品数字孪生模型,真实刻画了产品模型随物理装调过程的动态演变,形成的孪生数据作为质量特性预测模型的输入;通过采用信息熵的关键装配特征提取方法,实现了装配特征与质量特性之间关系的可解释性;通过构建智能化质量特性预测模型,实现了装调过程质量特性在线预测。
实施例2:
请参阅图1-2,基于实施例1但有所不同之处在于,
面向装配质量预测的高精密产品数字孪生可计算性方法,如图1所示,主要包括有构建数据集模块、构建质量特性预测模型模块和质量特性在线预测模块三个模块,具体实施方式如下:
(1)在构建数据集模块中,最重要的一步是关键装配特征提取,本发明采用了基于信息熵的关键特征提取方法,在综合考虑相关性、互补性和冗余性的基础上,设计关键装配特征参数的入选测度fE。在已知某质量特性Pi和当前关键装配特征集G的情况下,对装配特征与质量特性的关联关系进行度量。通过综合考虑三种关联关系来筛选具备最大相关性、最大互补性和最小冗余性的参数作为关键装配特征参数:
式中,表示候选装配特征xi和质量特性Pi之间的相关性;表示候选装配特征xi与关键装配特征集G之间的冗余性;
Com(xi,pi,G)表示候选装配特征xi对于当前关键装配特征集G的互补性;α和β是权值变量,由试验结果分析确定,且α,β,(α β)∈[0,1]。
通过提取的关键装配特征和对应的质量特性形成预测模型的训练集。
(2)在构建质量特性预测模型模块,首先采用归一化处理方法对训练集数据进行预处理。然后选择质量预测模型进行训练。其中,具有大数据量的高精密产品可选择人工神经网络(ANN)等算法;对于少量数据的高精密产品可选择支持向量回归(SVR)等算法做回归获取预测结果。
(3)质量特性在线预测模块具体操作步骤如下:
1)获取当前物理装配状态数据,映射至数字孪生模型,其映射数据为零件空间位姿:
式中,d为位置矢量;s为方向矢量;
其中,高精密产品数字孪生模型包含了装调工艺信息、模型几何信息、产品特性信息和物理属性信息,如图2所示。
2)将映射数据作为扰动因素使数字孪生模型进行演化,获取孪生数据,其中演化方法采用状态空间模型:
式中,i表示第i个装配工序,i∈(1,2,...,m);A(i)为系统矩阵,表示系统内部状态变量之间的联系;B(i)为转换矩阵,表示物理空间设备、夹具等位姿相对于孪生空间位姿的变换;E(i)也为转换矩阵,表示将装配过程中第i个装配工序中物理零件空间位姿相对于孪生空间位姿的变换;x(i)表示第i个装配工序下的状态向量;u(i)表示第i个装配工序下的设备、夹具等误差因素;φ(i)表示第i个装配工序下的零件加工误差因素;F(i)为转换矩阵;δ(i)为已孪数据影响因素;y(i)表示第i个装配工序下的装配特征向量;C(i)为观测矩阵,表示输出变量反应状态向量;表示装配环境(主要为温度)引起的误差,由于高精密产品的装配车间温度恒定,这里默认为零矩阵。
A、B、C、E矩阵可由最小二乘法获得。若第i个装配工序中包含a个位姿向量,则该装配工序下的状态向量为:
若第i个装配工序中包含b个设备误差位姿向量Pie、c个夹具误差位姿向量Pif,则该装配工序下的第一个输出向量为:
若第i个装配工序中包含d个设备误差位姿向量Pim,则该装配工序下的第二个输出向量为:
若第i个装配工序中包含e个设备误差位姿向量PiU,则该装配工序下的第三个输入向量为:
3)在获取的孪生数据中提取关键装配特征数据作为质量特性在线预测模型的输入;
4)质量特性在线预测模型输出预测结果;
5)当预测结果不满足设计要求,则进行物理调试,否则执行下一步装配。
以上所述,仅为本发明较佳的具体实施方式,但本发明的保护范围并不局限于此,任何熟悉本技术领域的技术人员在本发明揭露的技术范围内,根据本发明的技术方案及其发明构思加以等同替换或改变,都应涵盖在本发明的保护范围之内。
本文用于企业家、创业者技术爱好者查询,结果仅供参考。