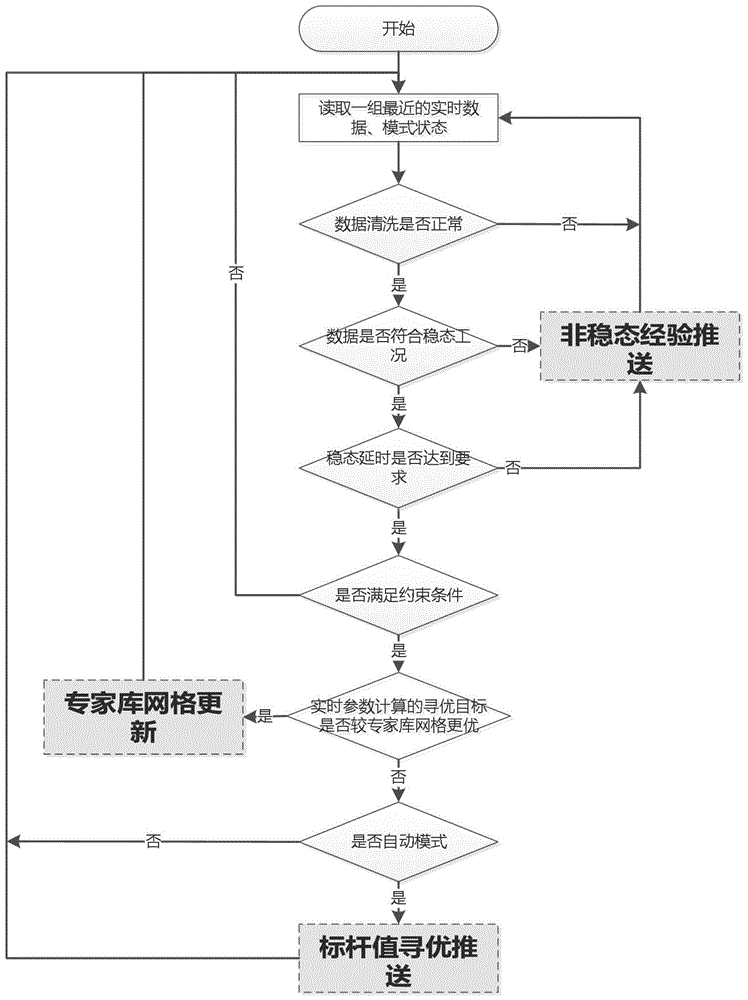
本发明涉及一种火力发电厂燃煤锅炉控制技术,尤其是涉及一种燃煤锅炉开环燃烧优化控制方法。
背景技术
随着发电企业配煤掺烧的要求及深度调峰的形势发展,锅炉的燃烧安全经济运行面临严峻考验,锅炉的运行调整主要通过运行人员依据经验在进行调整,由于监测设备不足、运行人员水平参差不齐、调整不及时等原因,无法保障锅炉始终具有较高的经济性、环保性和安全性。
燃煤锅炉的燃烧效率的提高、污染物排放的降低以及发电成本的减少,对于节约能源和环境保护具有重要意义。提高锅炉燃烧热效率与降低氮氧化物等污染物排放二者是矛盾的,提高燃烧热效率的同时往往伴随着氮氧化物排放量的增多,需要实现锅炉热效率和氮氧化物排放相互协调最优,来满足发电厂的经济效益和社会效益。
电站锅炉燃烧过程控制系统是一个复杂的多变量、强耦合系统,需要根据压力、流量、温度等诸多物理量的测量结果施以相应的控制手段,其控制效果的好坏很大程度上依赖于测量结果的准确度与控制优化算法的设计合理性。
近年来神经网络、遗传算法等智能算法在火电厂热工过程控制优化中的应用研究不断增加,使用机组海量运行数据为样本进行学习训练,以期实现对燃烧热效率和污染物排放量的预测,不同的模型产生的结果往往会有较大差异,且由于推荐调整方案的预测性会带来未知的安全风险。
基于历史方案进行数据挖掘的燃烧寻优,能够有机融合燃烧学原理、自学习技术和全局寻优算法,寻优后推荐的运行调整方式也是历史方案,兼顾燃烧优化与机组运行安全。
技术实现要素:
本发明针对现有技术不足,提出一种燃煤锅炉开环燃烧控制优化方法,获得锅炉的历史最佳燃烧工况及对应的各燃烧参数最佳设定值,推送至DCS开环指导运行人员燃烧调整。目的是随着机组不断运行调整,实现自主寻优更新,强化巩固已有成果,最终实现锅炉燃烧、氮氧化物排放相互协调,愈来愈优。
本发明采用的技术方案:
为了实现上述目的,本发明提供了一种燃煤锅炉开环燃烧控制优化方法,包括如下步骤:
步骤1:根据超低负荷、低负荷、中负荷和高负荷工况划分不同负荷段,分级建立专家库,采用机组负荷、燃煤低位发热量、环境温度和不同磨煤机组合方式来表征锅炉燃烧基础状态并作为聚类因子建立专家库网格,采用机组历史数据进行专家库初始化;对于各个表征锅炉燃烧基础状态的聚类因子,分别设定步长,划分成若干区间,组成多维网格。
步骤2:读取锅炉燃烧的实时运行数据及人工干预/自动模式状态,转至步骤3;
步骤3:对采集实时数据进行数据清洗,若不正常则转至步骤2,若正常则转至步骤4;数据清洗指:判断数据是否存在缺值、突增突减和超出上下限值;
步骤4:分析处理锅炉运行实时数据,判断当前锅炉燃烧是否符合稳态工况,若不符合稳态工况,则执行步骤4.1非稳态经验推送,若符合则转至步骤5;
步骤4.1:采用机组负荷和不同磨煤机组合方式2个聚类因子表征非稳态工况时,对应专家库若干网格。对这些网格内的各标杆值参数分别取平均作为经验值,将其推送至DCS后转至步骤2;
步骤5:在判定第1个稳态工况后开始进行稳态累计时间的计时,达到预定时间后方可进入步骤6,否则转至步骤4.1,期间因数据异常或判断为非稳态工况均重置计时;
步骤6:分析处理锅炉运行数据,判断当前锅炉燃烧是否满足约束条件,若不满足约束条件,则转至步骤2,若满足则转至步骤7;
步骤7:采用实时参数计算寻优目标,并与专家库网格内寻优目标值比较,若前者更优则转至步骤7.1,否则转至步骤8;寻优目标采用归一化方法,综合考虑脱硝入口氮氧化物浓度和锅炉热效率;
步骤7.1:执行专家库网格更新,将原专家库网格内的标杆值更新为当前实时参数,转至步骤2;
步骤8:判断当前人工干预/自动模式状态,若为人工干预模式则转至步骤2,否则转至步骤9。
步骤9:执行标杆值寻优推送,将专家库网格内的标杆值推送至DCS,转至步骤2。
根据本申请提供的燃煤锅炉开环燃烧控制优化方法,步骤2中,人工干预/自动模式可人为选择切换,两者区别在于处于人工干预模式下,不会推送运行调整方式给予操作指导,而是由机组运行人员自行燃烧调整,此时满足条件后仍会执行专家库网格更新。
根据本申请提供的燃煤锅炉开环燃烧控制优化方法,专家库网格更新只有在保证同一网格的情况下,由实时数据计算得到的寻优目标在设定时间范围内持续优于网格值方可执行。
根据本申请提供的燃煤锅炉开环燃烧控制优化方法,步骤4中,稳态工况的判断方法为在选取表征机组运行的一系列关键参数包括燃煤低位发热量、机组负荷、主汽压力、主汽温度、再热汽温、烟气含氧量、各层二次风门开度和炉膛负压后,求取设定时间范围内各参数的平均值,若实时参数与各平均值比较后在波动误差范围内,即可认为稳态。
根据本申请提供的燃煤锅炉开环燃烧控制优化方法,步骤6中,约束条件为换热器壁温不报警、主汽压力与滑压曲线的差值在设定范围、主/再热汽温与设计值偏差在设定范围、脱硝入口氮氧化物浓度不过高、再热器减温水流量在设定范围内和给水温度与设计值偏差在设定范围。
本发明的有益效果:
1、本发明锅炉开环燃烧控制优化方法,基于锅炉燃烧基础状态作为聚类因子结合分级负荷段建立了专家库网格,相比全负荷段明显减少了网格数量,可以吸取历史工况优秀方案以及更新采纳未来运行中可能出现的更优方案,实现自主寻优更新,强化巩固已有成果。在机组运行后,可全时段(含稳态/非稳态工况)推送优化调整方案,平滑过渡工况变化阶段,在安全的前提下,实现锅炉燃烧、氮氧化物排放相互协调,愈来愈优。
2、本发明锅炉开环燃烧控制优化方法,基于不同负荷进行了一级分类,且具有更高维度的工况划分依据(机组负荷、燃煤低位发热量、环境温度和不同磨煤机组合方式)作为二级分类。根据压力、流量、温度等诸多物理量的测量结果施以相应的控制手段,实现锅炉热效率和氮氧化物排放相互协调最优,来满足发电厂的经济效益和社会效益。
3、本发明锅炉开环燃烧控制优化方法,采用基于专家库系统的大数据挖掘算法,具有并详细阐明了数据清洗功能、稳态工况判断和约束条件判断,而且针对稳态/非稳态各提供一套指导策略。锅炉燃烧控制效果的好坏很大程度上依赖于测量结果的准确度与控制优化算法的设计合理性,本发明基于历史方案进行数据挖掘的燃烧寻优,有机融合燃烧学原理、自学习技术和全局寻优算法,寻优后推荐的运行调整方式也是历史方案,兼顾燃烧优化与机组运行安全。
附图说明
图1本发明锅炉开环燃烧控制优化方法流程图;
图2本发明锅炉开环燃烧控制优化方法专家库网格框架实例。
具体实施方式
为了使发明创造实现其发明目的的技术构思及优点更加清楚,下面结合附图对本发明的技术方案作进一步详细描述。应当理解的是,以下各实施例仅用以解释和说明本发明的优选实施方式,不应当构成对本发明专利保护范围的限定。
实施例1
参见图1,本发明一种燃煤锅炉开环燃烧控制优化方法,包括如下步骤:
S1,根据超低负荷、低负荷、中负荷和高负荷工况划分不同负荷段,分级建立专家库,采用机组负荷、燃煤低位发热量、环境温度和不同磨煤机组合方式来表征锅炉燃烧基础状态并作为聚类因子建立专家库网格,采用机组历史数据进行专家库初始化;其中,对于各个表征锅炉燃烧基础状态的聚类因子,分别设定步长,划分成若干区间,组成多维网格;
S2,设计人工干预/自动模式,实时读取锅炉燃烧的机组运行参数和模式状态,执行数据清洗、稳态判定、约束判定,依据聚类因子查询专家库对应网格,使用实时参数计算寻优目标并且和对应网格参数进行比较,根据不同的模式状态、判定结果、计算结果决定是否进行非稳态经验推送、专家库网格更新和标杆值寻优推送;其中,标杆值指的是专家库网格内存储的较为优秀的机组运行参数;寻优目标采用归一化方法,综合考虑脱硝入口氮氧化物浓度和锅炉热效率;
S3,设计延时策略解决非稳态/稳态推送方案切换的扰动,在分析实时机组运行数据后推送一组包括烟气含氧量、各层二次风门开度的运行调整方式至分布式控制系统(DCS),开环指导运行人员燃烧调整,保证优化控制系统稳定。
本发明燃煤锅炉开环燃烧控制优化方法,人工干预/自动模式可人为选择切换,两者区别在于处于人工干预模式下,不会推送运行调整方式给予操作指导,而是由机组运行人员自行燃烧调整,此时满足条件后仍会执行专家库网格更新;专家库网格更新只有在保证同一网格的情况下,由实时数据计算得到的寻优目标在设定时间范围内持续优于网格值方可执行。
实施例2
本实施例的燃煤锅炉开环燃烧控制优化方法,和实施例1的不同之处在于:步骤S2中,实时读取锅炉燃烧的运行数据及人工干预/自动模式状态,对采集实时数据进行数据清洗,即判断数据是否存在缺值、突增突减和超出上下限值,若正常则转至步骤S2-1;若不正常则返回至读取锅炉燃烧的机组运行参数和模式状态,执行数据清洗;
步骤S2-1:分析处理锅炉运行实时数据,判断当前锅炉燃烧是否符合稳态工况,若不符合稳态工况,则执行步骤S2-2,进行非稳态经验推送,若符合则转至步骤S2-3;
步骤S2-2:采用机组负荷和不同磨煤机组合方式2个聚类因子表征非稳态工况时,对应专家库若干网格。对这些网格内的各标杆值参数分别取平均作为经验值,将其推送至DCS,然后返回至读取锅炉燃烧的机组运行参数和模式状态,执行数据清洗;
步骤S2-3:在判定第1个稳态工况后开始进行稳态累计时间的计时,达到预定时间后方可进入步骤S2-4,否则转至步骤S2-2,期间因数据异常或判断为非稳态工况均重置计时;
步骤S2-4:分析处理锅炉运行数据,判断当前锅炉燃烧是否满足约束条件,若不满足约束条件,则返回至读取锅炉燃烧的机组运行参数和模式状态,执行数据清洗;若满足则转至步骤S2-5;
步骤S2-5:采用实时参数计算寻优目标,并与专家库网格内寻优目标值比较,若前者更优则转至步骤S2-6,否则转至步骤S2-7;
步骤S2-6:执行专家库网格更新,将原专家库网格内的标杆值更新为当前实时参数,返回至读取锅炉燃烧的机组运行参数和模式状态,执行数据清洗;
步骤S2-7:判断当前人工干预/自动模式状态,若为人工干预模式则返回至读取锅炉燃烧的机组运行参数和模式状态,执行数据清洗;否则转至步骤S2-8;
步骤S2-8:执行标杆值寻优推送,将专家库网格内的标杆值推送至DCS,返回至读取锅炉燃烧的机组运行参数和模式状态,执行数据清洗。
本发明燃煤锅炉开环燃烧控制优化方法,步骤S2-1中,稳态工况的判断方法为在选取表征机组运行的一系列关键参数包括燃煤低位发热量、机组负荷、主汽压力、主汽温度、再热汽温、烟气含氧量、各层二次风门开度和炉膛负压后,求取设定时间范围内各参数的平均值,若实时参数与各平均值比较后在波动误差范围内,即可认为稳态。
本发明燃煤锅炉开环燃烧控制优化方法,步骤S2-4中,约束条件为换热器壁温不报警、主汽压力与滑压曲线的差值在设定范围、主/再热汽温与设计值偏差在设定范围、脱硝入口氮氧化物浓度不过高、再热器减温水流量在设定范围内和给水温度与设计值偏差在设定范围。
实施例3
本实施例以某1000MW燃煤机组锅炉燃烧系统为例,具体说明本发明燃煤锅炉开环燃烧控制优化方法的具体实现过程,如图1所示,其流程包括:
步骤1:根据超低负荷、低负荷、中负荷和高负荷工况划分不同负荷段,分级建立专家库,采用机组负荷、燃煤低位发热量、环境温度和不同磨煤机组合方式来表征锅炉燃烧基础状态并作为聚类因子建立专家库网格,共计网格数量67815个,采集相关机组历史数据进行专家库初始化,如图2所示。根据上述专家库网格框架,可选取数据库管理系统,例如MySQL、Oracle和Sybase等进行搭建,进行数据的存储与调用。
步骤2:读取锅炉燃烧的实时运行数据及人工干预/自动模式状态,转至步骤3;
在DCS组态中写入人工干预/自动模式,供机组运行人员选择切换,人工干预/自动模式两者区别在于处于人工干预模式下,将不会推送运行调整方式给予操作指导,由机组运行人员自行燃烧调整,处于自动模式下,将执行非稳态经验推送和标杆值寻优推送。
步骤3:对采集实时数据进行数据清洗,当数据存在缺值、突增突减和超出上下限值的情况时转至步骤2,否则转至步骤4。
步骤4:分析处理锅炉运行实时数据,判断当前锅炉燃烧是否符合稳态工况,条件如下:
a.读取燃煤低位发热量近10分钟的数据,求平均值,当前值与平均值的差值,在范围±1000kJ/kg之间,为正常;否则为异常;
b.读取机组负荷近10分钟的数据,求平均值,当前值与平均值的差值,在范围±1%额定负荷值之间,为正常;否则为异常;
c.读取主汽压力近10分钟的数据,求平均值,当前值与平均值的差值,在范围±2%额定主汽压力值之间,为正常;否则为异常;
d.读取主汽温度近10分钟的数据,求平均值,当前值与平均值的差值,在范围±3℃之间,为正常;否则为异常;
e.读取再热汽温近10分钟的数据,求平均值,当前值与平均值的差值,在范围±4℃之间,为正常;否则为异常;
f.读取氧量近10分钟的数据,求平均值,当前值与平均值的差值,在范围±0.5%之间,为正常;否则为异常;
g.读取二次风门各层操近10分钟的数据,求每个层操的平均值,每个层操的当前值与平均值的差值,全部在范围±2%之间,为正常;否则为异常;
h.当前炉膛负压近3秒的数据,求平均值,当前值与平均值的差值,在范围±100Pa之间,为正常;否则为异常。
若不符合稳态工况,则执行步骤4.1非稳态经验推送,若符合则转至步骤5;
步骤4.1:采用机组负荷和不同磨煤机组合方式2个聚类因子表征非稳态工况时,对应专家库若干网格;
采用全局搜索算法调取数据库网格中存储的标杆值数据,对各参数分别取平均作为经验值,将其推送至DCS后转至步骤2。
步骤5:在判定第1个稳态工况后开始进行稳态累计时间的计时,达到预定时间后方可进入步骤6,否则转至步骤4.1,期间因数据异常或判断为非稳态工况均重置计时。
步骤6:分析处理锅炉运行数据,判断当前锅炉燃烧是否满足约束条件,条件如下:
a.各段水冷壁、各级过热器和各级再热器的壁温全部不超过报警值,为正常;否则为异常;
b.主汽压力与滑压曲线的差值在范围±1MPa之间,为正常;否则为异常;
c.主汽温度与设计值的差值在范围±10℃之间,为正常;否则为异常;
d.再热汽温与设计值的差值在范围±10℃之间,为正常;否则为异常;
e.脱硝装置入口氮氧化物浓度不高于历史稳态工况下的最大值,为正常;否则为异常;
f.再热器减温水流量不高于历史稳态工况下的允许值,为正常;否则为异常;
g.读取给水温度的实时数据,实时数据与设计值的差值在±10℃之间,为正常;否则异常。
若不满足约束条件,则转至步骤2,若满足则转至步骤7。
步骤7:采用实时参数计算寻优目标值,并与专家库网格内寻优目标值比较,寻优目标公式如下:
φ:寻优目标值;
fNOx(x):实时脱硝入口氮氧化物浓度;
fη(x):实时锅炉热效率;
fNOx(xmax):历史稳态工况下脱硝入口氮氧化物浓度的最大值;
fNOx(xmin):历史稳态工况下脱硝入口氮氧化物浓度的最小值;
α:脱硝入口氮氧化物浓度权值;
β:锅炉热效率权值,α β=1;
fη(xmax):历史稳态工况下锅炉热效率的最大值;
fη(xmin):历史稳态工况下锅炉热效率的最小值;
若前者更优则转至步骤7.1,否则转至步骤8;
步骤7.1:执行专家库网格更新,将原有专家库网格内的标杆值更新为当前实时参数,转至步骤2。
步骤8:判断当前人工干预/自动模式状态,若为人工干预模式则转至步骤2,否则转至步骤9;
在人工干预模式下,允许运行人员不依托该方法推送的运行调整方式,自行燃烧调整,主动探索燃烧优化方案,在找寻到一套更优方案时将更新对应专家库网格。
步骤9:执行标杆值寻优推送,读取专家库网格内的标杆值包括烟气含氧量、各层二次风门开度并推送至DCS,开环指导运行人员燃烧调整,转至步骤2。
以上所述仅为本发明的优选实施方式,并不构成对本发明的限定。本领域技术人员在现有技术的指引下,无需进行创造性劳动即可对本发明的实施情况进行其他修改,凡在本发明的精神和原则之内所作的任何修改或者采用本领域惯用技术手段进行的简单置换或等同替换,均应包含在本发明的保护范围之内。
本文用于企业家、创业者技术爱好者查询,结果仅供参考。