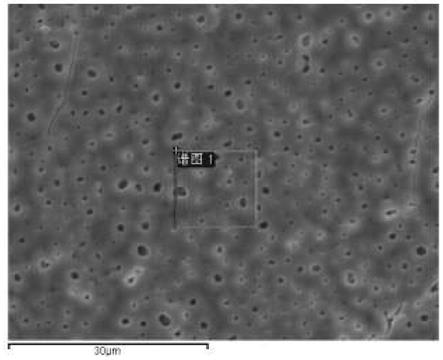
1.本发明涉及镁合金阳极微弧氧化电解液及利用该电解液对镁合金阳极微弧氧化的方法,属于金属表面处理技术领域。
背景技术:
2.镁合金具有质轻密度小(1.8g/cm3左右),强度高,弹性模量大,散热好,消震性好,承受冲击载荷能力比铝合金大,耐有机物和碱的腐蚀性能高的导热和导电性能、无磁性、屏蔽性好和无毒等优点,在汽车、航空航天、电子、军事、通讯、光学仪器、计算机等多个领域具有广阔的应用前景,被誉为“21世纪最具发展潜力和前途的绿色工程材料”。但镁合金的化学活性很大,应用于各种环境均易发生腐蚀,这在很大程度上阻碍了镁合金的应用。近年来出现的微弧氧化技术,利用镁合金在电解液中表面放电作用,在镁合金表面形成以氧化镁为主的陶瓷层。但是,由于镁合金本身存在许多缺陷,如固溶析出物、第二相及差排等会使镁合金表面阳极微弧氧化后形成的氧化镁陶瓷层产生缺陷。因此,制备一种成膜效果好、耐腐蚀等级高、绿色长效环保稳定的电解液及其应用成为相关业界探索的重要课题。
技术实现要素:
3.为解决上述问题,本发明提供一种镁合金阳极微弧氧化电解液。采用该电解液可在镁合金表面生成氧化膜,且氧化膜的微孔分布均匀、紧实性好、耐蚀性好。
4.本发明还提供利用上述电解液对镁合金阳极微弧氧化的方法。
5.为实现上述目的,本发明提供如下技术方案:
6.镁合金阳极微弧氧化电解液,所述电解液中各成分的浓度为:
7.10
‑
60g/l的氢氧化物、10
‑
60g/l的硅酸盐、10
‑
30g/l的碳酸盐、 5
‑
30g/l的硼酸盐、0.5
‑
10ml/l的edta、5
‑
30ml/l的乙二醇、 1
‑
15ml/l的丙三醇、3
‑
20ml/l的三乙醇胺、0.5
‑
10ml/l的8羟基喹啉。
8.进一步的,所述氢氧化物为氢氧化钠、氢氧化钾中的一种或两者的混合物。
9.所述硅酸盐是硅酸钾、硅酸钠中的一种或两者的混合物。
10.所述碳酸盐为碳酸钠、碳酸钾中的一种或两者的混合物。
11.所述硼酸盐为硼酸钠、硼酸钾中的一种或两者的混合物。
12.利用镁合金阳极微弧镁氧化电解液对镁合金阳极微弧氧化的方法,包括如下步骤:
13.s1:取10
‑
60g/l的氢氧化物、10
‑
60g/l的硅酸盐、10
‑
30g/l 的碳酸盐、5
‑
30g/l的硼酸盐、0.5
‑
10ml/l的edta、5
‑
30ml/l的乙二醇、1
‑
15ml/l的丙三醇、3
‑
20ml/l的三乙醇胺、0.5
‑
10ml/l的8 羟基喹啉,依次加入去离子水中,搅拌使其完全溶解,制得镁合金阳极微弧镁氧化电解液;
14.s2:制备镁合金样品,用碱溶液及柠檬酸清洗镁合金样品表面以去除油质及表面
氧化物,然后用水清洗干净并烘干;
15.s3:将s2制备的镁合金样品放入含s1所配制的电解液的电解槽中,以镁合金作为电解阳极,电解槽作为电解阴极;设定电流参数终电压为300v,电流密度为40
‑
50ma/cm2,氧化时间5min;
16.s4:氧化后使用去离子水清洗并烘干。
17.与现有技术相比,本发明的有益效果是:
18.本发明的镁合金阳极微弧氧化电解液,与现有的电解液的成分相比,增加了edta、乙二醇、丙三醇、三乙醇胺及8羟基喹啉,其中edta可以增加膜的均匀性及成膜稳定性,抑制氧化膜快速生成;乙二醇可以起到提高孔隙均匀性的作用;丙三醇能有效抑制成膜速度,增加单位面积负离子吸收能力,降低火花尺寸,三乙醇胺作为ph 值缓冲溶液,可以增加成膜厚度;8羟基喹啉能降低电解液导电度起到快速起弧作用增加膜厚并且能降低孔洞尺寸,进而改变成膜颜色。
附图说明
19.图1是本发明实施例4微弧氧化后镁合金表面的扫描电镜形貌图;
20.图2是本发明实施例5微弧氧化后镁合金表面的扫描电镜形貌图;
21.图3是本发明比较例1微弧氧化后镁合金表面的扫描电镜形貌图。
具体实施方式
22.下面采用具体实施例进一步说明本发明的内容。
23.实施例1:
24.镁合金阳极微弧氧化电解液,所述电解液中各成分的浓度为:
25.30g/l的氢氧化钠、30g/l的硅酸钾、30g/l的碳酸钾、5g/l 的硼酸钠、5ml/l的edta、20ml/l的乙二醇、3ml/l的丙三醇、10ml/l 的三乙醇胺、5ml/l的8羟基喹啉。
26.利用镁合金阳极微弧镁氧化电解液对镁合金阳极微弧氧化的方法,包括如下步骤:
27.s1:取30g/l的氢氧化钠、30g/l的硅酸钾、30g/l的碳酸钾、 5g/l的硼酸钠、5ml/l的edta、20ml/l的乙二醇、3ml/l的丙三醇、 10ml/l的三乙醇胺、5ml/l的8羟基喹啉,依次加入去离子水中,搅拌使其完全溶解,制得镁合金阳极微弧镁氧化电解液;
28.s2:制备镁合金样品,用碱溶液及柠檬酸清洗镁合金样品表面以去除油质及表面氧化物,然后用水清洗干净并烘干;
29.s3:将s2制备的镁合金样品放入含s1所配制的电解液的电解槽中,以镁合金作为电解阳极,电解槽作为电解阴极;设定电流参数终电压为300v,电流密度为40
‑
50ma/cm2,氧化时间5min;
30.s4:氧化后使用去离子水清洗并烘干。
31.实施例2:
32.镁合金阳极微弧氧化电解液,所述电解液中各成分的浓度为:
33.10g/l的氢氧化钾、10g/l的硅酸钠、10g/l的碳酸钠、18g/l 的硼酸钾、0.5ml/l的edta、5ml/l的乙二醇、3ml/l的丙三醇、3ml/l 的三乙醇胺、0.5ml/l的8羟基喹啉。
34.利用镁合金阳极微弧镁氧化电解液对镁合金阳极微弧氧化的方法,包括如下步骤:
35.s1:取10g/l的氢氧化钾、10g/l的硅酸钠、10g/l的碳酸钠、 18g/l的硼酸钾、0.5ml/l的edta、5ml/l的乙二醇、3ml/l的丙三醇、3ml/l的三乙醇胺、0.5ml/l的8羟基喹啉,依次加入去离子水中,搅拌使其完全溶解,制得镁合金阳极微弧镁氧化电解液;
36.s2:制备镁合金样品,用碱溶液及柠檬酸清洗镁合金样品表面以去除油质及表面氧化物,然后用水清洗干净并烘干;
37.s3:将s2制备的镁合金样品放入含s1所配制的电解液的电解槽中,以镁合金作为电解阳极,电解槽作为电解阴极;设定电流参数终电压为300v,电流密度为40
‑
50ma/cm2,氧化时间5min;
38.s4:氧化后使用去离子水清洗并烘干。
39.实施例3:
40.镁合金阳极微弧氧化电解液,所述电解液中各成分的浓度为:
41.60g/l的氢氧化钾和氢氧化钠的混合物、60g/l的硅酸钠和硅酸钾的混合物、20g/l的碳酸钠和碳酸钾的混合物、30g/l的硼酸钾、 10ml/l的edta、30ml/l的乙二醇、15ml/l的丙三醇、20ml/l的三乙醇胺、10ml/l的8羟基喹啉。
42.利用镁合金阳极微弧镁氧化电解液对镁合金阳极微弧氧化的方法,包括如下步骤:
43.s1:取60g/l的氢氧化钾和氢氧化钠的混合物、60g/l的硅酸钠和硅酸钾的混合物、20g/l的碳酸钠和碳酸钾的混合物、30g/l的硼酸钾、10ml/l的edta、30ml/l的乙二醇、15ml/l的丙三醇、20ml/l 的三乙醇胺、10ml/l的8羟基喹啉,依次加入去离子水中,搅拌使其完全溶解,制得镁合金阳极微弧镁氧化电解液;
44.s2:制备镁合金样品,用碱溶液及柠檬酸清洗镁合金样品表面以去除油质及表面氧化物,然后用水清洗干净并烘干;
45.s3:将s2制备的镁合金样品放入含s1所配制的电解液的电解槽中,以镁合金作为电解阳极,电解槽作为电解阴极;设定电流参数终电压为300v,电流密度为40
‑
50ma/cm2,氧化时间5min;
46.s4:氧化后使用去离子水清洗并烘干;
47.实施例4:
48.镁合金阳极微弧氧化电解液,所述电解液中各成分的浓度为:
49.30g/l的氢氧化钠、30g/l的硅酸钠、20g/l的碳酸钠、10g/l 的硼酸钠、5ml/l的edta、15ml/l的乙二醇、10ml/l的丙三醇、10ml/l 的三乙醇胺、2ml/l的8羟基喹啉。
50.利用镁合金阳极微弧镁氧化电解液对镁合金阳极微弧氧化的方法,包括如下步骤:
51.s1:取30g/l的氢氧化钠、30g/l的硅酸钠、20g/l的碳酸钠、 10g/l的硼酸钠、5ml/l的edta、15ml/l的乙二醇、10ml/l的丙三醇、10ml/l的三乙醇胺、2ml/l的8羟基喹啉,依次加入去离子水中,搅拌使其完全溶解,制得镁合金阳极微弧镁氧化电解液;
52.s2:制备镁合金样品,用碱溶液及柠檬酸清洗镁合金样品表面以去除油质及表面氧化物,然后用水清洗干净并烘干;
53.s3:将s2制备的镁合金样品放入含s1所配制的电解液的电解槽中,以镁合金作为电解阳极,电解槽作为电解阴极;设定电流参数终电压为300v,电流密度为40
‑
50ma/cm2,氧化时间5min;
54.s4:氧化后使用去离子水清洗并烘干。
55.实施例5:
56.镁合金阳极微弧氧化电解液,所述电解液中各成分的浓度为:
57.30g/l的氢氧化钠、30g/l的硅酸钠、20g/l的碳酸钠、10g/l 的硼酸钠、5ml/l的edta、15ml/l的乙二醇、10ml/l的丙三醇、10ml/l 的三乙醇胺、5ml/l的8羟基喹啉。
58.利用镁合金阳极微弧镁氧化电解液对镁合金阳极微弧氧化的方法,包括如下步骤:
59.s1:取30g/l的氢氧化钠、30g/l的硅酸钠、20g/l的碳酸钠、 10g/l的硼酸钠、5ml/l的edta、15ml/l的乙二醇、10ml/l的丙三醇、10ml/l的三乙醇胺、5ml/l的8羟基喹啉,依次加入去离子水中,搅拌使其完全溶解,制得镁合金阳极微弧镁氧化电解液;
60.s2:制备镁合金样品,用碱溶液及柠檬酸清洗镁合金样品表面以去除油质及表面氧化物,然后用水清洗干净并烘干;
61.s3:将s2制备的镁合金样品放入含s1所配制的电解液的电解槽中,以镁合金作为电解阳极,电解槽作为电解阴极;设定电流参数终电压为300v,电流密度为40
‑
50ma/cm2,氧化时间5min;
62.s4:氧化后使用去离子水清洗并烘干。
63.本发明的镁合金阳极微弧氧化电解液,配比的氢氧化物可以确保镁合金在溶液中稳定存在,且对环境友好,配比的硅酸盐在镁合金的阳极氧化时,参与了成膜过程,得到的阳极氧化膜中含有性能稳定、耐蚀性较好的镁硅氧化物,能够提高膜层的耐蚀性;配比的碳酸盐在于提供碳元素,使氧化膜中含有一定碳元素,进而提高氧化膜的耐蚀性能;配比的硼酸盐在于提供硼元素,使氧化膜中含有一定硼元素,进而提高氧化膜的耐蚀性能减少氧化膜应力;同时增加了edta、乙二醇、丙三醇、三乙醇胺及8羟基喹啉,其中edta 可以增加膜的均匀性及成膜稳定性,抑制氧化膜快速生成;乙二醇可以起到提高孔隙均匀性的作用;丙三醇能有效抑制成膜速度,增加单位面积负离子吸收能力,降低火花尺寸,三乙醇胺作为ph值缓冲溶液,可以增加成膜厚度;8羟基喹啉能降低电解液导电度起到快速起弧作用增加膜厚并且能降低孔洞尺寸,进而改变成膜颜色。
64.下面结合对比实施例1制备的镁合金阳极微弧氧化电解液与本发明实施例4
‑
5制备的镁合金阳极微弧氧化电解液进行比较说明。对比实施例1:
65.镁合金阳极微弧氧化电解液,所述电解液中各成分的浓度为: 30g/l的氢氧化钠、30g/l的硅酸钠、20g/l的碳酸钠、10g/l的硼酸钠、5ml/l的edta、15ml/l的乙二醇、10ml/l的丙三醇、10ml/l 的三乙醇胺。
66.利用镁合金阳极微弧镁氧化电解液对镁合金阳极微弧氧化的方法,包括如下步骤:
67.s1:取30g/l的氢氧化钠、30g/l的硅酸钠、20g/l的碳酸钠、 10g/l的硼酸钠、5ml/l的edta、15ml/l的乙二醇、10ml/l的丙三醇、10ml/l的三乙醇胺,依次加入去离子水中,搅拌使其完全溶解, 制得镁合金阳极微弧镁氧化电解液;
68.s2:制备镁合金样品,用碱溶液及柠檬酸清洗镁合金样品表面以去除油质及表面氧化物,然后用水清洗干净并烘干;
69.s3:将s2制备的镁合金样品放入含s1所配制的电解液的电解槽中,以镁合金作为电解阳极,电解槽作为电解阴极;设定电流参数终电压为300v,电流密度为40
‑
50ma/cm2,氧化时间5min;
70.s4:氧化后使用去离子水清洗并烘干。
71.将经过实施例4、5和对比实施例1的电解液阳极微弧氧化后的 3份镁合金样品的表面经sem扫描电镜及edx分析后,膜层成分及表面孔隙度结果如下:
72.1、edx分析后,3份样品的膜层各成分含量结果如表1(单位:
73.百分比)。
74.表1:
[0075][0076]
2、3份样品的膜层扫描电镜结果如图1
‑
3。其中:图1是本发明实施例4,微弧氧化后镁合金表面的扫描电镜形貌图;图2是本发明实施例5,微弧氧化后镁合金表面的扫描电镜形貌图;图3是本发明对比实施例1,微弧氧化后镁合金表面的扫描电镜形貌图。
[0077]
分析表1及图1
‑
3,结论如下:
[0078]
1、由扫描电镜结果得知未添加8羟基喹啉,微弧氧化后的镁合金表面存在非常多的开孔且存在很多大孔洞,随着8羟基喹啉的量增加,孔径变小且多为闭孔结构。使形成的氧化膜应力减少进而膜的裂纹也减少;
[0079]
2、由edx成分分析得知随着8羟基喹啉的量增加,碳含量也随着增加,驱使开孔质渐变成闭孔;由于碳进入氧化膜内,降低了成膜应力,也驱使表面膜层的孔洞变小。
[0080]
对于本领域技术人员而言,显然本发明不限于上述示范性实施例的细节,而且在不背离本发明的精神或基本特征的情况下,能够以其他的具体形式实现本发明。因此,无论从哪一点来看,均应将实施例看作是示范性的,而且是非限制性的,本发明的范围由所附权利要求而不是上述说明限定,因此旨在将落在权利要求的等同要件的含义和范围内的所有变化囊括在本发明内。
再多了解一些
本文用于企业家、创业者技术爱好者查询,结果仅供参考。