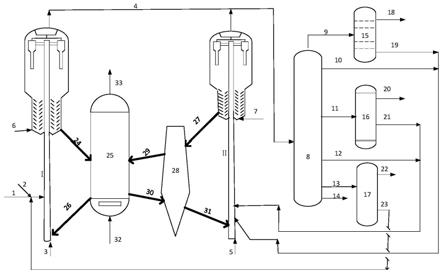
1.本发明涉及石油化工领域,具体地,涉及一种石油烃类生产低碳烯烃与多种芳烃的方法。
背景技术:
2.低碳烯烃和btxn(c6~c8单环芳烃与萘、烷基萘双环芳烃的简称)是重要的化工原料,其主要通过催化裂化和热裂化进行生产。
3.催化裂化的流程主要包括三个部分:原料油催化裂化;催化剂再生;产物分离。原料喷入提升管反应器下部,在此处与高温催化剂混合、气化并发生反应。反应油气与催化剂在沉降器和旋风分离器离后,进入分馏塔分出汽油、柴油和重质回炼油。裂化气经压缩后去气体分离系统。结焦的催化剂在再生器用空气烧去焦炭后循环使用。
4.热裂化是在热的作用下(不用催化剂)使重质油发生裂化反应,转变为裂化气、汽油、柴油的过程。热裂化原料通常为原油蒸馏过程得到的重质馏分油或渣油,或其他石油炼制过程副产的重质油。热裂化过程广泛应用于石油炼制过程,用于将大分子裂化为小分子。
5.但是已有的催化裂化和热裂化方法中,低碳烯烃与c6~c8芳烃和萘油(btxn)产品收率较低且焦炭产率较高,难以满足日益增长的低碳烯烃和芳烃等化工原料的需求。
技术实现要素:
6.本发明的目的是提供一种石油烃类生产低碳烯烃与多种芳烃的方法,该方法能够显著提高低碳烯烃与c6~c8芳烃和萘油(btxn)产品收率并降低焦炭产率,能够转化出更多的低碳烯烃和芳烃。
7.本发明的发明人出乎意料地发现:在催化裂化过程中通过加入临氢催化裂解来处理催化裂化循环油lco,能够使得lco中分子量较高的单环芳烃和双环芳烃转化为btxn,由此得到了本发明。
8.为了实现上述目的,本发明提供一种生产低碳烯烃和芳烃的方法,该方法包括:(1)将重质石油烃送入第一提升管反应器,进行催化裂化;(2)将含有fcc轻循环油馏分的轻质石油烃送入第二提升管反应器,进行临氢催化裂解;(3)将所述第一提升管反应器导出的物料进行第一油剂分离,得到第一油气产物和第一待生催化剂;(4)将所述第二提升管反应器导出的物料进行第二油剂分离,得到第二油气产物和待生催化剂;(5)将所述第一待生催化剂和所述第二待生催化剂合并后进行再生;(6)将所述第一油气产物和所述第二油气产物合并后进行精馏分离、气分分离和芳烃抽提分离。
9.通过上述技术方案,低碳烯烃与c6~c8芳烃和萘油(btxn)产品收率得到了显著的提高,并且并焦炭产率得到了显著地降低。
10.本发明的其他特征和优点将在随后的具体实施方式部分予以详细说明。
附图说明
11.附图是用来提供对本发明的进一步理解,并且构成说明书的一部分,与下面的具体实施方式一起用于解释本发明,但并不构成对本发明的限制。在附图中:
12.图1是本发明的一种实施方式的示意图。
13.附图标记说明
14.1重质石油烃
ꢀꢀꢀꢀꢀꢀꢀꢀ
2雾化介质
ⅰꢀꢀꢀꢀꢀꢀꢀꢀꢀ
3流化介质ⅰ15.4反应油气管线
ꢀꢀꢀꢀꢀꢀ
5流化介质
ⅱꢀꢀꢀꢀꢀꢀꢀꢀ
6汽提介质ⅰ16.7汽提介质
ⅱꢀꢀꢀꢀꢀꢀꢀꢀ
8精确分馏塔
ꢀꢀꢀꢀꢀꢀꢀꢀ
9裂化气
17.10轻石脑油
ꢀꢀꢀꢀꢀꢀꢀꢀꢀ
11轻质芳烃馏分
ꢀꢀꢀꢀꢀ
12轻循环油
18.13重质芳烃馏分
ꢀꢀꢀꢀꢀ
14油浆
ꢀꢀꢀꢀꢀꢀꢀꢀꢀꢀꢀꢀꢀ
15气分系统
19.16芳烃抽提系统
ⅰꢀꢀꢀ
17芳烃抽提系统
ⅱꢀꢀꢀ
18低碳烯烃
20.19 c1~c4烷烃气体
ꢀꢀ
20轻质芳烃
ꢀꢀꢀꢀꢀꢀꢀꢀꢀ
21轻质芳烃抽余油
21.22重质芳烃
ꢀꢀꢀꢀꢀꢀꢀꢀꢀ
23重质芳烃抽余油
ꢀꢀꢀ
24待生管线ⅰ22.25再生器
ꢀꢀꢀꢀꢀꢀꢀꢀꢀꢀꢀ
26再生管线
ⅰꢀꢀꢀꢀꢀꢀꢀ
27待生管线ⅱ23.28催化剂闭锁料斗
ꢀꢀꢀ
29待生管线
ⅲꢀꢀꢀꢀꢀꢀꢀ
30再生剂管线ⅱ24.31再生管线
ⅲꢀꢀꢀꢀꢀꢀꢀ
32含氧再生气体
ꢀꢀꢀꢀꢀ
33烟气
[0025]ⅰ第一提升管反应器
ꢀⅱ
第二提升管反应器
具体实施方式
[0026]
以下结合附图对本发明的具体实施方式进行详细说明。应当理解的是,此处所描述的具体实施方式仅用于说明和解释本发明,并不用于限制本发明。
[0027]
本发明提供一种生产低碳烯烃和芳烃的方法,该方法包括:(1)将重质石油烃送入第一提升管反应器,进行催化裂化;(2)将含有fcc轻循环油馏分的轻质石油烃送入第二提升管反应器,进行临氢催化裂解;(3)将所述第一提升管反应器导出的物料进行第一油剂分离,得到第一油气产物和第一待生催化剂;(4)将所述第二提升管反应器导出的物料进行第二油剂分离,得到第二油气产物和待生催化剂;(5)将所述第一待生催化剂和所述第二待生催化剂合并后进行再生;(6)将所述第一油气产物和所述第二油气产物合并后进行精馏分离、气分分离和芳烃抽提分离。
[0028]
所述第一提升管反应器和所述第二提升管反应器可以各自为上行式提升管反应器或下行式提升管反应器。
[0029]
本发明中所述第一提升管反应器和所述第二提升管反应器,可以各自是选自等直径提升管、等线速提升管、变直径提升管、变线速提升管中之一,也可以各自是由等直径提升管或变直径提升管构成的复合反应器,优选变直径提升管反应器和提升管构成的复合反应器。
[0030]
可选地,所述第一提升管反应器中的所述催化裂化的条件包括:温度为500-750℃,剂油重量比为5-20:1,反应压力为0.1-1.0mpa,反应时间为1-15秒;
[0031]
可选地,所述第二提升管反应器中的所述临氢催化裂解的条件包括:温度为500-750℃,剂油重量比为1.0-10:1,反应压力为0.1-10.0mpa,反应时间为0.1-20秒,氢油体积比为100-1000:1,油气表观平均线速为0.5-5.0米/秒。
[0032]
优选地,所述第一提升管反应器中的所述催化裂化的条件包括:温度为520-700℃,剂油重量比为6-9:1,反应压力为0.2-0.9mpa,反应时间为0.5-15秒。
[0033]
优选地,所述第二提升管反应器中的所述临氢催化裂解的条件包括:温度为520-700℃,剂油重量比为3.0-9.0:1,反应压力为0.2-0.9mpa,反应时间为0.5-15秒,氢油体积比为150-800:1,油气表观平均线速为1.0-4.0米/秒。
[0034]
其中,所述第一提升管反应器中的催化裂化可以为非临氢催化裂化。
[0035]
其中,所述第一提升管反应器和所述第二提升管反应器中的温度各自可以为反应区出口温度。
[0036]
可选地,所述轻质石油烃还含有石脑油和加氢fcc循环油馏分中的至少一种;所述轻质石油烃还可选地包括干气、液化气和天然气中的至少一种。
[0037]
所述重质石油烃包括蜡油、常压渣油和加氢渣油中的至少一种。
[0038]
可选地,所述轻质石油烃的碳原子数为1-20,密度为600~920千克/立方米,残炭值<1.0重%,终馏点为不大于360℃。
[0039]
可选地,所述重质石油烃的碳原子数大于20,密度为800~1100千克/立方米,硫含量<1.5重%,氮含量<0.5重%,残炭值<8.0重%,金属ni v<50μg/g,初馏点为不小于360℃。
[0040]
可选地,所述精馏分离将所述油气产物进行分离,得到裂化气、轻石脑油馏分、轻质芳烃馏分、轻循环油馏分和重质芳烃馏分以及油浆。
[0041]
可选地,所述轻石脑油馏分的初馏点为25-35℃,终馏点为75-85℃。
[0042]
可选地,轻质芳烃馏分的初馏点为75-85℃,终馏点为155-175℃。
[0043]
可选地,轻循环油馏分的初馏点为155-175℃,终馏点为230-250℃。
[0044]
可选地,重质芳烃馏分的初馏点为230-250℃,终馏点为355-385℃。
[0045]
其中,本发明中提到的“初馏点”和“终馏点”对一个确定的馏分而言是点值,本领域技术人员可以在上述温度范围内选择馏分的“初馏点”和“终馏点”,并通过精馏装置和条件的改变得到所需的馏分。
[0046]
可选地,所述气分分离将所述裂化气进行分离,得到低碳烯烃和气分系统剩余物料。
[0047]
可选地,所述芳烃抽提包括轻质芳烃抽提和重质芳烃抽提。
[0048]
可选地,通过所述轻质芳烃抽提将所述轻质芳烃馏分分离,得到轻质芳烃和轻质芳烃抽余油。
[0049]
可选地,通过所述重质芳烃抽提将所述轻质芳烃馏分分离,得到重质芳烃和重质芳烃抽余油。
[0050]
可选地,所述低碳烯烃包括乙烯、丙烯和c4烯烃中的至少一种;所述轻质芳烃包括苯、甲苯和二甲苯中的至少一种;所述重质芳烃包括萘、菲、蒽、烷基萘、烷基菲、和烷基蒽中的至少一种。
[0051]
可选地,可以将分离后的馏分进行回炼。例如,该方法还包括:将所述轻石脑油馏分、所述轻质芳烃抽余油和所述轻循环油馏分中的至少一者中的部分或全部掺入所述轻质石油烃中进行回炼;该方法还可选地包括:将所述重质芳烃抽余油的部分或全部掺入所述重质石油烃中进行回炼;该方法还可选地包括:将所述气分系统剩余物料的部分或全部掺入所述轻质石油烃和/或所述第二提升管反应器的预提升介质中进行回炼。又例如,所述第
二提升管反应器包括烷烃裂解区和芳烃裂解区,所述芳烃裂解区设置在所述烷烃裂解区裂化区的下游;该方法还包括:将所述轻质芳烃抽余油和所述轻循环油馏分中的至少一者中的部分或全部掺入所述轻质石油烃中导入所述第二提升管中的芳烃裂解区进行回炼;该方法还可选地包括:将所述重质芳烃抽余油的部分或全部掺入所述重质石油烃中导入所述第一提升管反应器中进行回炼;该方法还可选地包括:将所述气分系统剩余物料的部分或全部与所述轻石脑油馏分的部分或全部导入所述第二提升管中的烷烃裂解区进行回炼。
[0052]
其中,所述轻质石油烃的部分或全部可以全部来源于所述方法中回炼的物料,例如在所述方法的正常运行期间,所述轻质石油烃的50%-100%来源于所述方法中回炼的物料。优选地,在所述方法的正常运行期间,所述轻质石油烃的全部来源于所述方法中回炼的物料,例如所述轻质石油烃的全部来源于所述轻石脑油馏分、所述轻质芳烃抽余油和所述轻循环油馏分中的至少一者,或者,所述轻质石油烃的全部来源于所述轻石脑油馏分、所述轻质芳烃抽余油和所述轻循环油馏分中的至少一者,或者,所述轻质石油烃的全部来源于所述轻质芳烃抽余油和所述轻循环油馏分中的至少一者;由此,整个方法在正常运行期间可以仅以重质石油烃为净输入原料,充分利用重质石油烃来生产低碳烯烃与c6~c8芳烃和萘油(btxn)产品,提高其产率。
[0053]
优选地,为了减少催化剂的活性的下降,所述方法还可选地包括:在将所述重质芳烃抽余油的部分或全部掺入所述重质石油烃中进行回炼前,还进行吸附处理和/或选择性加氢处理,以脱除氮化物、硫化物、胶质和/或重金属。
[0054]
可选地,所述第一提升管反应器和所述第一提升管反应器中的催化剂为含有中孔沸石和/或任选的大孔沸石、无机氧化物和任选的粘土的具有芳构化功能催化裂化催化剂。可以采用金属、非金属等对中孔沸石和大孔沸石改性。优选为采用fe、co、ni、cu、zn和稀土等过渡金属和/或p等非金属改性的中孔沸石和大孔沸石共同作为活性组分的具有芳构化功能的催化裂化催化剂。
[0055]
可选地,其中,催化裂化催化剂含有:沸石1-50重%、无机氧化物5-95重%、粘土0-70重%以及改性金属组分和改性非金属组分。其中,所述沸石可以为任选的大孔沸石和中孔沸石,大孔沸石占沸石总重量的50-100重%,优选60重%-90重%;中孔沸石占沸石总重量的0-50重%,优选10重%-40重%。所述大孔沸石可以选自y系列沸石,包括稀土y(rey)、稀土氢y(rehy)、不同方法得到的超稳y、高硅y。所述中孔沸石选自zsm系列沸石和/或zrp沸石,也可对上述中孔沸石用p等非金属元素进行改性;zsm系列沸石可以选自zsm-5、zsm-11、zsm-12、zsm-23、zsm-35、zsm-38、zsm-48和其它类似结构的沸石之中的一种或两种以上的混合物。此外,沸石还包括兼具大孔结构与中孔结构的beta型分子筛。
[0056]
所述无机氧化物作为粘接剂,可以选自二氧化硅(sio2)和/或三氧化二铝(al2o3),以干重基计,无机氧化物中二氧化硅可以占50重-90重%,三氧化二铝可以占10重-50重%。
[0057]
所述粘土作为基质(即载体),可以选自二氧化硅、高岭土和/或多水高岭土、蒙脱土、硅藻土、埃洛石、皂石、累托土、海泡石、凹凸棒石、水滑石和膨润土中的一种或几种。
[0058]
所述改性金属组分具有脱氢作用的过渡金属,主要是过渡金属的第四、五周期的金属元素,优选fe、co、ni、cu、zn和稀土等过渡金属中的任意一种或任意两种、三种或多种金属的氧化物或氢氧化物。改性金属组分按照金属氧化物计,占催化剂总重量的0~15重%,优选1.0-10重%。
[0059]
优选情况下,催化剂为采用cu、p等金属、非金属改性的中孔沸石和大孔沸石共同作为活性组分的具有芳构化功能的催化裂化催化剂。
[0060]
可选地,作为本发明一种优选的实施方式,所述第一提升管反应器和所述第一提升管反应器中的催化剂含有15-22重%dasy沸石、10-14重%mfi结构中孔沸石、1.5-2.5重%的氧化铜、0.5-1.2重%的五氧化二磷、20-25重%的拟薄水铝石和5-7重%铝溶胶和余量的高岭土。
[0061]
根据本发明,将所述待生催化剂进行再生;在所述再生过程中,再生气体可以为空气、氧气和含氧气体中的一种与多种,再生温度可以为500-800℃,优选为550-750℃。再生后催化剂的换热可以采用本领域普通技术人员所熟知的方法进行,从而控制焦炭生成量和油剂接触温度。
[0062]
例如,图1为本发明一种实施方式的工艺流程示意图,在该实施方式中,使用双提升管反应器,渣油等重质石油烃类在第一提升管反应器非临氢催化裂化,fcc轻循环油等轻质烃在第二升管反应器进行高温临氢催化裂解反应,反应后的油气进入精确分离系统进行产品分离、芳烃抽提。其工艺流程如下:
[0063]
重质石油烃1经不含氢雾化介质2雾化进入第一提升管反应器ⅰ催化裂化生产低碳烯烃与芳烃,反应产物和反应后带炭的待生催化剂进行气固分离,分离后的待生催化剂经不含氢汽提介质6汽提后由再生管线24直接输送到再生器25;轻石脑油馏分、fcc轻循环油馏分、加氢fcc循环油馏分和/或干气、液化气、天然气等轻质烃注入双提升管催化裂化装置的第二提升管反应器ⅱ,在含氢的流化介质5反应氛围下进行临氢催化裂解反应,其中轻石脑油馏分、fcc轻循环油馏分、加氢fcc循环油馏分和/或干气、液化气、天然气等可以在第二提升管反应器ⅱ的同一位置进料也可以在不同位置分区进料,优选轻石脑油馏分和/或干气、液化气、天然气等轻质烃注入第二提升管反应器ⅱ的下部而fcc轻循环油馏分、加氢fcc循环油馏分等轻质烃注入第二提升管反应器ⅱ的上部,从而实现轻质烃分区临氢催化裂解反应;第二提升管反应器的反应产物和反应后带炭的待生催化剂气固分离后经含氢或不含氢汽提介质7汽提,汽提后的待生催化剂经待生管线27直接进入再生器,和/或经待生管线27进入催化剂闭锁料斗28脱氢降压,脱氢降压后的待生催化剂经29进入再生器25;含氧再生气体32注入再生器底部,来自两个反应器的待生催化剂在同一再生器25含氧氛围内500-800℃烧焦再生,部分热的再生催化剂直接返回第一提升管反应器ⅰ循环使用,部分热的再生催化剂经再生管线30直接和/或经催化剂闭锁料斗28脱氧升压后经再生管线31返回到第二提升管反应器ⅱ循环使用;两个提升管反应器油剂分离后的反应油气,经反应油气管线4进入油气分离系统8,精确分离得到裂解气体9、轻石脑油10、轻质芳烃馏分11、轻循环油12和重质芳烃馏分13以及油浆14等;裂解气体9经气分系统15分离,得到低碳烯烃18与c1~c4烷烃气体19;轻质芳烃馏分11经芳烃抽提系统ⅰ16进行芳烃抽提,得到苯、甲苯、二甲苯等轻质芳烃20与轻质芳烃抽余油21;重质芳烃馏分13经芳烃抽提系统ⅱ17进行芳烃抽提,得到萘、甲基萘等重质芳烃22与重质芳烃抽余油22。轻石脑油10、c1~c4烷烃气体19根据需要选择部分循环回反应器作为含氢流化介质或者预提升介质回炼;轻循环油12、轻质芳烃抽余油21根据需要回炼或不回炼,优先选择在第二提升管反应器ⅱ回炼多产低碳烯烃与芳烃;重质芳烃抽余油根据需要回炼或不回炼,优先选择在第一提升管反应器ⅰ与重油混合回炼多产芳烃。
[0064]
在该实施方式中,所述催化剂闭锁料斗与所述反应器装置的所述催化剂进口和催化剂出口相连接,且与所述再生装置的催化剂进口和催化剂出口相连接,使得来自所述反应器装置的待生催化剂经所述催化剂料斗系统后进入所述再生装置中再生,并使得来自所述再生装置的再生催化剂经所述催化剂料斗系统后循环回所述反应器装置中。
[0065]
下面的实施例将对本方法予以进一步的说明,但并不因此限制本方法。
[0066]
实施例中所用的原料重质石油烃性质,如表1所示。
[0067]
催化剂制备实施例
[0068]
实施例中所用的催化剂的制备方法如下:
[0069]
1)、将20kg氯化铵溶于1000kg水中,向此溶液中加入100kg(干基)晶化产品dasy沸石(齐鲁石化公司催化剂厂生产,2.445-2.448nm,稀土含量re2o3=2.0重%),在90℃交换0.5h后,过滤得滤饼;加入39.3kgcu(no3)2·
6h2o溶于203kg水中,与滤饼混合浸渍烘干;接着在550℃温度下焙烧处理2小时得到含铜的大孔沸石,其元素分析化学组成为0.1na2o
·
5.1al2o3·
18.2cuo
·
3.8re2o3·
88.1sio2。
[0070]
2)、将20kg磷酸铵溶于500kg水中,搅拌均匀,向此溶液中加入50kg mfi结构中孔zrp-1沸石(齐鲁石化公司催化剂厂工业产品,sio2/al2o3=30),60℃浸渍搅拌3h,过滤得滤饼;分子筛滤饼在120℃烘干,接着在550℃温度下焙烧处理1小时得到含磷的中孔沸石,其中五氧化二磷含量6.8%。
[0071]
3)、用250kg脱阳离子水将75.4kg多水高岭土(苏州瓷土公司工业产品,固含量71.6m%)打浆,再加入54.8kg拟薄水铝石(山东铝厂工业产品,固含量63m%),用盐酸将其ph调至2-4,搅拌均匀,在60-70℃下静置老化1小时,保持ph值为2-4,将温度降至60℃以下,加入41.5kg铝溶胶(齐鲁石化公司催化剂厂产品,al2o3含量为21.7m%),搅拌40分钟,得到混合浆液。
[0072]
4)、将步骤1)制备的含铜的大孔沸石(干基为33.8kg)以及步骤2制备的含磷mfi结构中孔zrp-1沸石干基为15.0kg)加入到步骤3)得到的混合浆液中,搅拌均匀,并加入商业三氧化二铝粘接剂4g,混合后并放于粘合机中,加入适量水,充分搅拌均匀,在空气中放置4小时,在空气中放置4小时,喷雾干燥成型,于干燥箱中120℃烘干3小时后,用磷酸二氢铵溶液(磷含量为1重%)洗涤,洗去游离na
,洗涤除去游离na
,再次干燥即得催化剂记为cat-2。该催化剂的组成为18.9重%dasy沸石、12.0重%mfi结构中孔沸石、氧化铜1.9重%、五氧化二磷0.8重%、22.8重%拟薄水铝石、6.0重%铝溶胶和余量高岭土。其性质列于表2。
[0073]
实施例1
[0074]
该实施例按照图1的装置和流程进行试验,使用表1中加氢渣油a作为重质原料油,在小型双提升管反应器装置上进行试验,采用cat-2催化剂,催化剂mat为62。该小型双提升管反应器,催化剂的藏量为20公斤。与常规双提升管反应器装置不同的是,其中第二提升管反应器催化剂处于湍动流化状态,表观平均线速为1.0-3.0米/秒,并采用氢气流化,反应压力操作范围为0.1-10.0mpa。
[0075]
重质石油烃a经280℃预热后进入双提升管反应器装置的第一提升管,在反应压力0.4mpa下随着不含氢流化介质水蒸气由下向上流动,在反应温度680~515℃、催化剂与原料油的重量比6.8、反应时间为3.5秒、雾化水蒸气与总原料的重量比0.10条件下进行催化裂化反应,反应后的待生催化剂进入再生器再生;反应后的油气进入精馏分馏塔分离,精馏
分馏塔分离塔板数为50层塔板,精确分离得到裂解气体、轻石脑油(37~80℃)、轻质芳烃馏分(78~170℃)、轻循环油(170~245℃)和重质芳烃馏分(240~380℃)以及油浆等;裂解气体经气分系统分离,得到低碳烯烃与气分系统剩余物料(c1~c4烷烃气体);轻质芳烃馏分经芳烃抽提系统进行芳烃抽提,得到苯、甲苯、二甲苯等轻质芳烃与轻质芳烃抽余油,而重质芳烃馏分经芳烃抽提系统进行芳烃抽提得到萘、甲基萘等重质芳烃与重质芳烃抽余油;轻石脑油、轻循环油、芳烃抽余油以及气分系统剩余物料(c1~c4烷烃气体)等轻质烃产品在第二提升管100%回炼,其中轻石脑油与气分系统剩余物料(c1~c4烷烃气体)在第二提升管的下部回炼,而轻循环油和芳烃抽余油在第二提升管的上部回炼,在反应压力3.0mpa下,氢分压2.4mpa下接触热再生剂,随着含氢流化介质由下向上流动,在反应温度680~560℃、催化剂与原料油的重量比4.5、反应时间为6.0秒下反应,反应后的油气进入精馏分馏塔分离,待生催化剂汽提后经催化剂闭锁料斗脱氢降压进入再生器再生;再生器采用空气作为再生气体,在再生温度680~720℃、再生器压力0.5mpa下与待生剂接触进行再生;再生后的再生剂循环使用。操作条件和产品分布列于表3。
[0076]
从表3可以看出,实施例1中,重质石油烃在双提升管反应器装置的一个提升管反应器中非临氢催化裂化,而轻石脑油、轻循环油、芳烃抽余油以及c1~c4烷烃气体等轻质烃在双提升管反应器装置的另一个提升管反应器中回炼进行临氢催化裂解,裂化气收率为25.2重%,btx收率为33.3重%,重质芳烃收率24.3重%,三烯(乙烯 丙烯 丁烯)收率21.4重%;油浆产率为4.1重%,焦炭产率为8.1重%。
[0077]
对比例1
[0078]
通过与实施例1相同的装置和方法进行催化裂化,不同在于对比例1中:第二提升管回炼气分系统剩余物料(c1~c4烷烃气体)、轻石脑油与轻循环油,在第二提升管中进行非临氢催化裂解。
[0079]
该对比例的催化剂与工艺条件与实施例1相同,采用cat-2催化剂,催化剂mat为62,重质石油烃a在反应压力0.4mpa下,随着非含氢流化介质由下向上流动,在反应温度680~515℃、催化剂与原料油的重量比6.8、反应时间为3.5秒、水蒸气与总原料的重量比0.10条件下进行催化裂化反应,反应后的待生催化剂与反应油气分离;油剂分离后油气,精确分离得到低碳烯烃与气分系统剩余物料(c1~c4烷烃气体)、轻石脑油(37~80℃)、轻质芳烃馏分(78~170℃)、轻循环油(170~245℃)和重质芳烃馏分(240~380℃)以及油浆等;轻质芳烃馏分与重质芳烃馏分分别进行芳烃抽提,得到轻质芳烃与重质芳烃以及芳烃抽余油;气分系统剩余物料(c1~c4烷烃气体)、轻石脑油与芳烃抽余油等轻质烃在第二提升管回炼,回炼比例100%,在反应压力0.4mpa、反应温度680~560℃、催化剂与原料油的重量比4.5、反应时间为6.0秒下反应;两个提升管油剂分离后的待生催化剂,水蒸气汽提后,在再生温度680~720℃、再生器压力0.6mpa下空气再生,再生后的再生剂循环使用。操作条件和产品分布列于表3。
[0080]
从表3可以看出,实施例1(轻质烃临氢催化裂解)与对比例1(轻质烃非临氢催化裂解)相比,btx收率和重质芳烃收率以及三烯收率高,而且焦炭产率低;btx收率和重质芳烃收率以及三烯收率分别提高9.7、4.6和2.9个百分点,焦炭产率降低1.5个百分点。
[0081]
实施例2
[0082]
该实施例按照图1的装置和流程进行试验,使用表1中常压渣油b作为重质原料油,
加氢lco作为轻质原料之一,在小型双提升管反应器装置上进行试验,采用cat-2催化剂,催化剂mat为58。该小型双提升管反应器,催化剂的藏量为20公斤。与常规双提升管反应器装置不同的是,其中第二提升管反应器催化剂处于湍动流化状态,表观平均线速为1.0-3.0米/秒,并采用氢气流化,反应压力操作范围为0.1-10.0mpa。
[0083]
重质石油烃b经240℃预热后进入双提升管反应器装置的第一提升管,在反应压力0.2mpa下随着水蒸气流化介质由下向上流动,在反应温度700~550℃、催化剂与原料油的重量比8.2、反应时间为5.5秒、雾化水蒸气与总原料的重量比0.15条件下进行催化裂化反应,反应后的待生催化剂进入再生器再生;反应后的油气进入精馏分馏塔分离,精馏分馏塔分离塔板数为50层塔板,精确分离得到裂解气体、轻石脑油(37~80℃)、轻质芳烃馏分(78~170℃)、轻循环油(170~245℃)和重质芳烃馏分(240~380℃)以及油浆等;裂解气体经气分系统分离,得到低碳烯烃与气分系统剩余物料(c1~c4烷烃气体);轻质芳烃馏分经芳烃抽提系统进行芳烃抽提,得到苯、甲苯、二甲苯等轻质芳烃与轻质芳烃抽余油,而重质芳烃馏分经芳烃抽提系统进行芳烃抽提得到萘、甲基萘等重质芳烃与重质芳烃抽余油;轻石脑油、轻循环油、芳烃抽余油以及气分系统剩余物料(c1~c4烷烃气体)等轻质烃产品在第二提升管70%回炼,其中轻石脑油与气分系统剩余物料(c1~c4烷烃气体)在第二提升管的下部回炼,而轻循环油和芳烃抽余油以及外来加氢lco在第二提升管的上部回炼,在反应压力1.0mpa下,氢分压0.8mpa下接触热再生剂,随着含氢流化介质由下向上流动,在反应温度700~580℃、催化剂与原料油的重量比6.4、反应时间为2.0秒下反应,反应后的油气进入精馏分馏塔分离,待生催化剂汽提后经催化剂闭锁料斗脱氢降压进入再生器再生;再生器采用空气作为再生气体,在再生温度680~720℃、再生器压力0.4mpa下与待生剂接触进行再生;再生后的再生剂循环使用。操作条件和产品分布列于表4。
[0084]
从表4可以看出,实施例2中,重质石油烃在双提升管反应器装置的一个提升管反应器中非临氢催化裂解,而轻石脑油、轻循环油、芳烃抽余油以及c1~c4烷烃气体等轻质烃在双提升管反应器装置的另一个提升管反应器中回炼进行临氢催化裂解,裂化气收率为41.2重%,三烯(乙烯 丙烯 丁烯)收率35.0重%,btx收率为22.7重%,重质芳烃收率23.0重%;焦炭产率为6.4重%。
[0085]
对比例2
[0086]
通过与实施例2相同的装置和方法进行催化裂化,不同在于对比例2中:第二提升管回炼c1~c4烷烃气体、轻石脑油与轻循环油以及加氢lco,在第二提升管中进行非临氢催化裂解。
[0087]
该对比例的催化剂与工艺条件与实施例1相同,采用cat-2催化剂,催化剂mat为62,重质石油烃b在反应压力0.3mpa下,随着非含氢流化介质由下向上流动,在反应温度680~515℃、催化剂与原料油的重量比6.8、反应时间为3.5秒、水蒸气与总原料的重量比0.10条件下进行催化裂化反应,反应后的待生催化剂与反应油气分离;油剂分离后油气,精确分离得到低碳烯烃与c1~c4烷烃气体、轻石脑油(37~80℃)、轻质芳烃馏分(78~170℃)、轻循环油(170~245℃)和重质芳烃馏分(240~380℃)以及油浆等;轻质芳烃馏分与重质芳烃馏分分别进行芳烃抽提,得到轻质芳烃与重质芳烃以及芳烃抽余油;c1~c4烷烃气体、轻石脑油轻质烃与芳烃抽余油等轻质烃在第二提升管最大量回炼,回炼比例100%,在反应压力0.3mpa、反应温度680~560℃、催化剂与原料油的重量比6.4、反应时间为2.0秒下反应;两
个提升管油剂分离后的待生催化剂,水蒸气汽提后,在再生温度680~720℃、再生器压力0.5mpa下空气再生,再生后的再生剂循环使用。操作条件和产品分布列于表4。
[0088]
从表4可以看出,实施例2(轻质烃临氢催化裂解)与对比例2(轻质烃非临氢催化裂解)相比,btx收率和重质芳烃收率以及三烯收率高,而且焦炭产率低;btx收率和重质芳烃收率以及三烯收率分别提高7.7、9.2和7.4个百分点,焦炭产率降低0.7个百分点。
[0089]
本发明与现有技术相比还具有下列技术效果:(1)原料适应性强,不仅适用于优质催化裂解原料,还适用于高密度低氢含量的劣重质原料的深度催化裂解生产化工料;(2)通过fcc轻循环油馏分、加氢fcc循环油馏分和/或轻石脑油馏分、干气、液化气、天然气等在专有提升管反应器分区临氢催化裂解,实现了fcc轻循环油中烷基芳烃的临氢催化裂解脱烷基反应,而且相对非临氢催化裂解低碳烯烃与芳烃料产率高,生焦低,氢气依赖度低;(3)产品方案灵活,精确分离系统不仅可以分离裂化油气生产裂化气、汽油、柴油和油浆以及重循环油,而且可以精确分离生产低碳烯烃、btx、萘、二甲基萘等双环芳烃以及菲、蒽等三环芳烃等化工料,从而满足催化裂化装置生产芳烃的需求;(4)在一套装置中实现了轻质烃临氢催化裂解和重质油的深度催化裂化,工艺集成度高,装置效率高,并且可以利用提升管反应器催化裂化装置进行改造。
[0090]
表1
0~40微米18.840~80微米58.6>80微米22.6
[0094]
表3
[0095] 实施例1对比例1原料油aa反应方式轻质烃临氢催化裂解轻质烃非临氢催化裂解催化剂名称cat-2cat-2催化剂活性(mat)6262轻质烃的回炼比1.01.0反应操作条件
ꢀꢀ
第一提升管反应器
ꢀꢀ
反应压力,mpa0.40.4反应器入口温度,℃680680反应器出口温度,℃515515催化剂/原料油的重量比6.86.8油气停留时间,s3.53.5雾化蒸气/总原料的重量比0.100.10第二提升管反应器
ꢀꢀ
反应压力,mpa3.00.4氢分压,mpa2.4~反应器入口温度,℃680680反应器出口温度,℃560560催化剂/原料油的重量比4.54.5油气停留时间,s6.06.0h2/油的体积比800~雾化蒸气/总原料的重量比~0.05产品收率,重%
ꢀꢀ
裂化气25.226.4其中乙烯2.11.8丙烯12.911.1丁烯6.45.5轻质芳烃(78~170℃)38.333.7其中btx33.323.6重质芳烃(240~380℃)24.326.4其中萘4.92.6甲基萘10.97.9菲、蒽7.37.9油浆4.13.9
焦炭8.19.6合计100.00100.0
[0096]
表4
[0097][0098]
以上结合附图详细描述了本发明的优选实施方式,但是,本发明并不限于上述实施方式中的具体细节,在本发明的技术构思范围内,可以对本发明的技术方案进行多种简
单变型,这些简单变型均属于本发明的保护范围。
[0099]
另外需要说明的是,在上述具体实施方式中所描述的各个具体技术特征,在不矛盾的情况下,可以通过任何合适的方式进行组合,为了避免不必要的重复,本发明对各种可能的组合方式不再另行说明。
[0100]
此外,本发明的各种不同的实施方式之间也可以进行任意组合,只要其不违背本发明的思想,其同样应当视为本发明所公开的内容。
再多了解一些
本文用于企业家、创业者技术爱好者查询,结果仅供参考。