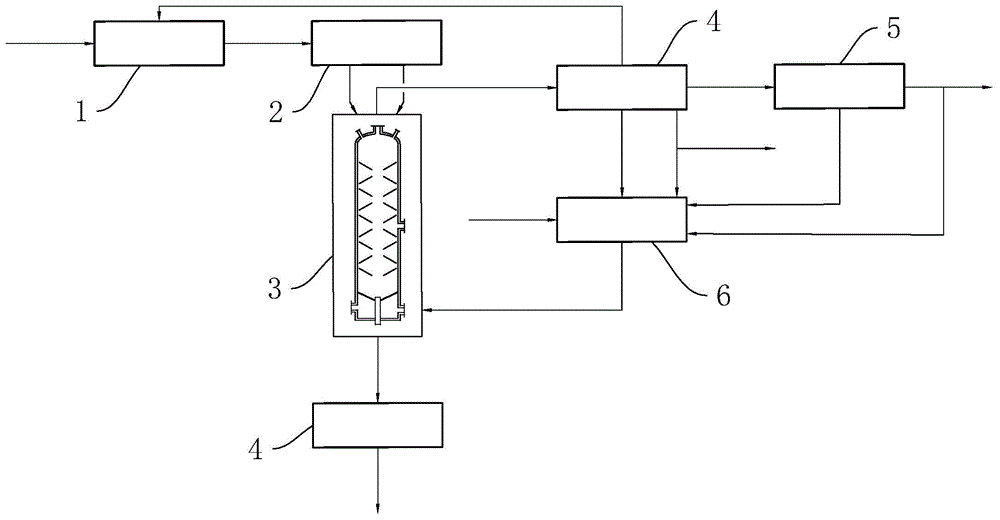
本申请涉及有机固体废弃物的环保技术的领域,尤其是涉及一种热载体式有机固体废弃物的处理工艺以及系统。
背景技术:
:目前,我国的固体废弃物存量大,如何对其进行有效的处理或者利用已经成为国家环保领域关注的重点。国家推行的垃圾分类,主要的对象便是针对固体废弃物。其中,有机固体废弃物因含有有机成分,处理难度高,对环境的破坏性大,处理过程容易发生二次污染。从另一角度讲,若是能将有机固体废弃物中的有机组分进行回收和利用,则可以在解决环保问题的同时,实现资源化转化,降低环保处理的成本,甚至产生一定的经济效益。当前针对有机固体废弃物的处理方法主要包括堆肥、填埋、焚烧、气化、热解等技术。其中,堆肥和填埋的处理周期非常长,并且需要占用大量的土地资源,效率低下,处理过程中产生的残液容易对土壤造成二次污染;焚烧处理效率高,并可以回收其中的部分能量,但是焚烧属于有氧化学反应,且燃烧温度难以超过1000℃,无法避免二噁英等污染物的产生;气化利用部分氧化反应,反应温度可以达到1200℃以上,且整个反应环境为还原性氛围,可以解决二噁英的问题,但是,气化要求的反应温度较高,若有机组分的含量有限,需要大量的外部燃料来保证气化温度,因此,在原料适应性方面有较高的要求。与上述几种技术相比,热解处理技术为无氧惰性反应环境,通过热量输入将有机质进行提取或者分解,获得相应的气态、液态和固态产品,原料适应性强,且环境友好。当前发展的有机固体废弃物热解技术均以间接给热方式为主,存在传热效率不高、吸热效率低导致热量利用效率低、热解反应速度慢、反应时间较长、能耗高等问题。技术实现要素:为了实现有机固体废弃物的快速资源化转化和无害化处理以及提高热解技术能量利用效率,本申请提供一种热载体式有机固体废弃物的处理工艺以及系统。第一方面,本申请提供的一种热载体式有机固体废弃物的处理工艺,采用如下的技术方案:一种热载体式有机固体废弃物的处理工艺,其特征在于,包括以下处理步骤:s1、预处理有机固体废弃物进入预处理装置对有机固体废弃物进行预处理以满足进料装置的输送需求;s2、固废输送预处理后的有机固体废弃物,通过进料装置进入热解反应装置;s3、热解反应在热解反应装置内,有机固体废弃物与热载体通过逆流方式直接接触换热并发生化学反应,转化为气相产物和固相产物;s4、热量回收气相产物和固相产物进入热量回收装置,通过直接或者间接热交换的方式将气相产物和固相产物所含有的热量进行回收,并得到气相产物、固相产品、液相产品和液相热载体,根据所选热载体种类从s4中回收液相热载体,或从s5中回收气相热载体,如从s4中回收液相热载体,则s5中不再回收热载体;s5、净化回收气相产物进入净化装置,除去有害组分,得到净化的气相产品和气相热载体;净化的气相产品部分或全部输送至热载体发生装置作为热载体发生装置的燃料;气相热载体输送至热载体发生装置;s6、热载体发生热载体发生装置产出热载体输入热解反应装置。通过采用上述方案:有机固体废弃物在无氧或者缺氧条件下,与热载体直接接触,受热转化为气相和固相产物。该系统提高了热解反应和提馏反应速度、缩短了热解提馏反应时间、提高了有机固体废弃物中的有机质转化回收产率;提高了有机固体废弃物热解提馏过程的给热效率与吸热效率,提高了热量利用效率、有效降低了能耗。热量回收装置可回收热解反应装置的余热,并将余热应用于热载体发生装置、净化装置和热解反应装置,进一步提高能源利用率。净化装置可用于净化分离产物和热载体,使热载体回收利用。优选的,所述热载体反应装置的操作温度为200℃~1300℃,操作压力为-0.10~13mpa。通过采用上述方案:具有较高的提溜反应效率以及热量利用率,进一步降低能耗。优选的,s1中预处理为破碎、干燥、分离、挤压、萃取、热处理、化学吸收、干化中的一种或多种的组合方法。通过采用上述方案:物理和化学的组合方法可对有机固体废弃物进行充分的预处理,提高后续的反应效率,且可保护工艺后续的各个设备。优选的,s2中进料装置为气力输送、螺旋输送、泵输送、其他机械输送中的一种或多种的组合方式。优选的,热载体与s2中预处理后的有机固体废弃物的质量比例为0.1:1~10:1。通过采用上述方案:使整体工艺具有较高的提溜反应效率以及热量利用率,进一步降低能耗。第二方面,本申请提供的热载体式有机固体废弃物的处理系统,采用如下的技术方案:一种应用于上述热载体式有机固体废弃物的处理工艺的系统,包括用于热解有机固体废弃物的热解反应装置、用于提供热载体的热载体发生装置;有机固体废弃物自上而下进入热解反应装置内,热载体自下而上进入热解反应装置内,且有机固体废弃物与热载体在热解反应装置内直接接触给热。优选的,所述热解反应装置和所述热载体发生装置组成一体式的热解反应-热载体发生耦合装置。通过采用上述方案:将热解反应装置和热载体发生装置集成在一起,降低了工程造价费用,减小了占地面积。优选的,还包括预处理装置和用于输送有机固体废弃物的进料装置,所述进料装置连接于所述预处理装置和热解反应装置之间。通过采用上述方案:有机固体废弃物经预处理装置预处理后再通过进料装置进入热解反应装置,使有机固体废弃物更适应热解反应,从而进一步提升热解效率。优选的,还包括净化装置,所述净化装置与热量回收装置、热载体发生装置连接。优选的,还包括热量回收装置,所述热量回收装置同时与预处理装置、热解反应装置、净化装置、热载体发生装置连接。综上所述,本申请包括以下至少一种有益技术效果:1.利用热载体直接传热的方式,提高了能量利用效率,也避免了二次污染;对工艺流程进行能量和物质集成优化,进一步提高了物质和能量利用效率。本技术通过将有机固体废弃物中的有机组分进行提取,实现有机固体废弃物的资源化利用,获得的产品一部分可作为燃料返回系统并为系统运行提供能量,一部分外售产生经济效益;2.有机固体废弃物在无氧或者缺氧条件下,与热载体直接接触,受热转化为气相和固相产物。该系统提高了热解反应和提馏反应速度、缩短了热解提馏反应时间、提高了有机固体废弃物中的有机质转化回收产率;提高了有机固体废弃物热解提馏过程的给热效率与吸热效率,提高了热量利用效率、有效降低了能耗;3.当热载体采用蒸汽等可以降温液化的介质时,热载体将在热量回收装置进行回收,实现循环利用;当热载体为不凝气、有机气体、氢气、氮气、二氧化碳其他难以液化的气体时,热载体将在净化装置进行分离,并循环利用;4.本工艺处理得到的油泥含油量<3‰,达到农用污泥标准;处理生物质得到的生物炭可应用于农业用途以及碳收集及储存使用;5.将热解反应装置和热载体发生装置集成在一起,降低了工程造价费用,减小了占地面积。附图说明图1是本申请有热载体式有机固体废弃物处理系统的示意图;图2是本申请热解反应装置的结构示意图;图3是本申请实施例1热载体式有机固体废弃物处理工艺的流程示意图;图4是本申请实施例2热载体式有机固体废弃物处理工艺的流程示意图;图5是本申请热载体式有机固体废弃物处理系统的示意图;图6是本申请热解反应-热载体发生耦合装置的结构示意图;图7是本申请实施例3热载体式有机固体废弃物处理工艺的流程示意图,采用热解反应-热载体发生耦合装置;图8是本申请实施例4热载体式有机固体废弃物处理工艺的流程示意图,热解反应-热载体发生耦合装置。附图标记说明:1、预处理装置;2、进料装置;3、热解反应装置;4、热量回收装置;5、净化装置;6、热载体发生装置;7、热解反应-热载体发生耦合装置;31、壳体;32、耐火隔热衬里;33、反应上段;34、反应中段;35、反应下段;36、有机固体废弃物进口;37、产物出口;38、人孔;39、物料分配板;341、缺口一;342、环隙一;343、湍动微反应床;344、二次热载体进口;351、导渣板;3211、主反应区;3212、副反应区;3214、上导流板;3215、下导流板;32141、缺口二;32142、环隙二;32151、缺口三;32152、环隙三;3241、缺口四;3242、环隙四;331、热载体进口;332、热载体分布板;334、残渣出口;101、流股aa;102、流股ab;103、流股ac;104、流股ad;105、流股ae;106、流股af;107、流股ag;108、流股ah;109、流股ai;110、流股aj;111、流股ak;112、流股al;113、流股am;114、流股an;201、流股ba;202、流股bb;203、流股bc;204、流股bd;205、流股be;206、流股bf;207、流股bg;208、流股bh;209、流股bi;210、流股bj;211、流股bk;212、流股bl;213、流股bm;214、流股bn;215、流股bo;43、上段炉;44、中段炉;45、下段炉;46、炉壳体;431、有机固体废弃物物料进口;432、气态混合物出口;433、物料进口分配板;442、出口导流板;443、二次给热口;447、二次燃料燃烧器;451、燃料燃烧器;452、气体分布板;453、排渣口;454、压温气体进口;455、二次给热高温烟气出口;301、流股ca;302、流股cb;303、流股cc;304、流股cd;305、流股ce;306、流股cf;307、流股cg;308、流股ch;309、流股ci;310、流股cj;311、流股ck;312、流股cl;314、流股cn;401、流股da;402、流股db;403、流股dc;404、流股dd;405、流股de;406、流股df;407、流股dg;408、流股dh;409、流股di;410、流股dj;411、流股dk;412、流股dl;414、流股dn。具体实施方式以下结合附图1-8对本申请作进一步详细说明。本申请实施例公开了一种热载体式有机固体废弃物的处理系统,参照图1,一种热载体式有机固体废弃物的处理系统,包括预处理装置1、进料装置2、热解反应装置3、热量回收装置4、净化装置5、热载体发生装置6。预处理装置1可通过破碎、干燥、分离、挤压、萃取等物理方法或者热处理、化学吸收等化学方法或者物理、化学二者结合等方法,改变有机固体废弃物的外形(处理后的外形可以为棒状、球状、片状、粒状等规则形态、不规则形态以及多种形态的组合)、规格、组成(所含组分有一定量的变化或者有新的组分加入或者生成)及状态(可以为固态、气态、液态、浆态或者两种及以上状态的组合),使有机固体废弃物满足进料装置2的要求。进料装置2根据有机固体废弃物的形态,可以是螺旋、皮带、泵等机械输送或者气力输送,也可以是几种输送方式的组合,并将有机固体废弃物输送至热解反应装置3。有机固体废弃物与热载体在热解反应装置3内逆流,并在无氧或者缺氧条件下,有机固体废弃物与热载体直接接触,受热转化为气相产物和固相产物。热解反应装置3的操作温度为200℃~1300℃,操作压力为-0.10~13mpa。特别的,以蒸汽为热载体时,蒸汽与预处理后的有机固体废弃物反应的质量比例为0.1:1~10:1。热量回收装置4通过直接或者间接热交换的方式将气相产物和固相产物所含有的热量进行回收。经过热量回收后,固相产物成为可以对外出售的产品、燃料或者不再具有环境危害特性而直接排放;气相产物经过冷却、分离后分为气相和液相产品,热交换的对象可以为燃料、空气、导热油、热载体、水、蒸汽、不凝气、有机气体、氢气、氮气、二氧化碳等工艺介质。回收的热量可以通过气体或者液体媒介(媒介不限于上文所述的热交换的对象),用于预处理装置1、热解反应装置3、热载体发生装置6以及系统伴热等辅助需求。所获得的液相产品可以作为燃料或者产品外售。净化装置5将气相产物通过物理或者化学方法,除去气相产物中含有的有害组分后,部分或者全部送至热载体发生装置6,通过燃烧或者部分氧化反应,直接或间接为热载体发生装置6提供热量。热载体发生装置6产出热载体进入热解反应装置3。热载体可以为燃烧尾气、部分氧化反应的产物、氮气、二氧化碳、蒸汽、炼厂干气等气体介质。当热载体采用蒸汽等可以降温液化的介质时,热载体将在热量回收装置4进行回收,实现循环利用;当热载体为不凝气、有机气体、氢气、氮气、二氧化碳其他难以液化的气体时,热载体将在净化装置5进行分离,并循环利用。热载体加热的燃料可以为有机固体废弃物转化获得的气相、液相、固相产品,也可以来自于外部的其他气态、液态或者固态燃料。另外,本申请具体公开了一种热解反应装置3,参照图2,其包括壳体31,壳体31的内壁与外壁之间具有耐火隔热衬里32,且壳体31由上至下分布有相互连通的反应上段33、反应中段34和反应下段35三个区域。高温热载体由反应下段35上升至反应上段33;有机固体废弃物由反应上段33下行至反应下段35;在反应中段34时,下行的有机固体废弃物与上行的高温热载体直接接触换热,有机固体废弃物吸收高温热载体携带的热量发生有机质的裂解反应和提馏反应而产生低分子量的气态烃类物质及/或气相油品、高温热载体组成气态混合物自下而上流动。需要说明的是,反应上段33、反应中段34和反应下段35可以是同轴同直径连通,也可以不同轴不同直径连通;反应上段33、反应中段34和反应下段35的截面形状可以是圆筒形或椭圆形,也可以是矩形或多边形;反应上段33、反应中段34和反应下段35的截面形状可以是同一种截面结构,也可以是不同截面形状及其不同结构的组合;反应上段33、反应中段34和反应下段35的截面面积可以相等,也可以不同;反应上段33、反应中段34和反应下段35可以是整体结构,也可以是分段连接结构。另外,壳体31可以是多层耐火隔热浇注料结构,也可以是多层的耐火隔热砖结构,也可以是耐火隔热浇注料与耐火隔热砖的组合结构,也可以是列管式或盘管式的膜式水冷壁结构,也可以是冷却夹套结构,也可以是这几种结构形式的不同组合。反应上段33具有有机固体废弃物进口311、产物出口312、人孔38以及设置于壳体31内的物料分配板314。具体地,有机固体废弃物进口311开设于反应上段33的顶部侧面,本申请中设置有4个有机固体废弃物进口311并以壳体31中轴线为轴均匀分布;产物出口312开设有1个并位于壳体31顶部中心处,且与壳体31中轴线同轴;人孔38开设于壳体31侧面,便于工作人员检修。物料分配板314的上表面或下表面可以是齐平面也可以是弯折面,上表面形状可以是平直的,也可以是波纹状,也可以是开设导流槽结构,也可以是这几种结构的不同组合。为了便于说明,定义物料分配板314上表面与壳体31中心线的夹角为α,夹角α可以为0-180°的任一值;当夹角0°<α≤90°时,物料分配板314的聚点在底部,当夹角90°<α<180°时,物料分配板314的聚点在顶部。物料分配板314在其中心区域的底部(0°<α≤90°时)或顶部(90°<α<180°时)开设宽度或直径为a0(a0≥0)的缺口一3141,对应地,在其底部(0°<β1<90°时)或顶部(90°<β2≤180°时)与壳体31的内壁面之间开设有宽度为b01和b02(b01≥0、b02≥0)的环隙一3142,均为有机固体废弃物物料下行和气态物料上行的通道。在一实施例中物料分配板314开设有缺口一3141,但并未开设环隙一3142。在另一实施例中,物料分配板314开设有环隙一3142,但并未开设缺口一3141。在又一实施例中,物料分配板314既开设有缺口一3141,又开设有环隙一3142。另外,环隙一3142的宽度可以是相同的,也可以是不同的,可以是部分不同也可以是全部不同。反应中段34具有若干组串联的湍动微反应床321、二次热载体进口323以及导渣板324。湍动微反应床321内具有主反应区3211,相邻湍动微反应床321之间形成有副反应区3212。具体地,湍动微反应床321包括至少一块上导流板3214和至少一块下导流板3215,上导流板3214和下导流板3215之间形成有主反应区3211,上导流板3214和壳体31内壁之间、下导流板3215和壳体31内壁之间均形成有副反应区3212。本实施例中,湍动微反应床321包括一块上导流板3214和一块下导流板3215,且以壳体31中心线为中心轴双向对称布置或双向非对称布置。本实施例中,以双向对称为例说明。另外,为了便于说明,定义上导流板3214的上表面与反应器壳体31中心线的夹角β1,夹角β1为0-180°之间的任一角度;下导流板3215的上表面与反应器壳体31中心线的夹角β2,夹角β2为0-180°之间的任一角度;且当90°≤β1<180°时0°<β2≤90°,相应地当0°<β1≤90°时90°≤β1<180°。与物料分配板314相同的是,当上导流板3214的夹角0°<β1≤90°时,上导流板3214的聚点在底部,当夹角90°<β1<180°时,上导流板3214的聚点在顶部;当下导流板3215的夹角0°<β1≤90°时,下导流板3215的聚点在底部,当夹角90°<β1<180°时,下导流板3215的聚点在顶部。另外,不同上导流板3214和下导流板3215与反应器壳体31中心线的夹角β1与β2可以是相同数值,也可以是相互不同数值。上导流板3214中心区域顶部(90°≤β1<180°时)或底部(0°<β1<90°时)开有宽度或直径为a1(a1≥0)的缺口二32141,对应地,在上导流板3214底部(90°≤β1<180°时)或顶部(0°<β1≤90°时)与壳体31内壁面之间开有宽度为b11和b12(b11≥0、b12≥0)的环隙二32142,均为固态物料下行和气态物料上行的通道,且a1和b11及b12不同时为0。即为,在一实施例中上导流板3214开设有缺口二32141,但并未开设环隙二32142。在另一实施例中,上导流板3214开设有环隙二32142,但并未开设缺口二32141。在又一实施例中,上导流板3214既开设有缺口二32141,又开设有环隙二32142。另外,每相邻两组湍动微反应床321上导流板3214的a1和b11及b12可以是相同数值,也可以是相互不同数值。下导流板3215中心区域底部(0°<β2≤90°时)或顶部(90°<β2<180°时)开设宽度或直径为a2(a2≥0mm)的缺口三32151,对应地,在下导流板3215顶部(0°<β2≤90°时)或底部(90°<β2<180°时)与壳体31内壁面之间开有宽度为b21和b22(b21≥0、b22≥0)的环隙三32152,均为固态物料下行和气态物料上行的通道,且a2和b21及b22不同时为0。即为,在一实施例中下导流板3215开设有缺口三32151,但并未开设环隙三32152。在另一实施例中,下导流板3215开设有环隙三32152,但并未开设缺口三32151。在又一实施例中,下导流板3215既开设有缺口三32151,又开设有环隙三32152。另外,每相邻两组湍动微反应床321下导流板3215的a2和b21及b22可以是相同数值,也可以是相互不同数值。至此,每一组湍动微反应床321内,即为上导流板3214与下导流板3215之间构成的空间区域为主反应区3211,相邻两组湍动微反应床321之间,即为上一组微反应床的下导流板3215与下一组微反应床的上导流板3214之间构成的两侧两个空间区域为副反应区3212。有机固体废弃物经过在湍动微反应床321的提馏反应后,有机固体废弃物残渣物料下行汇集于导渣板324。导渣板324的上表面或下表面可以是齐平面也可以是弯折面,上表面形状可以是平直的,也可以是波纹状,也可以是开设导流槽结构,也可以是这几种结构的不同组合。为了便于说明,定义导渣板324板上表面与壳体31中心线的夹角为β3,夹角β3可以为0-180°的任一值;当夹角0°<β3≤90°时,物料分配板314的聚点在底部,当夹角90°<β3<180°时,物料分配板314的聚点在顶部。导渣板324底部(0°<β3≤90°时)或顶部(90°<β3<180°时)开设宽度或直径为a3(a3≥0)的缺口四3241,对应地,在其顶部(0°<β1<90°时)或底部(90°<β2≤180°时)与壳体31内壁面之间开设宽度为b31和b32(b31≥0、b32≥0)的环隙四3242,均为热解固态残渣出口334和热载体上行的通道,且a3和b31及b32不同时为0。即为,在一实施例中导渣板324开设有缺口四3241,但并未开设环隙四3242。在另一实施例中,导渣板324开设有环隙四3242,但并未开设缺口四3241。在又一实施例中,导渣板324既开设有缺口四3241,又开设有环隙四3242。二次热载体进口323开设于壳体31侧面,且位于相邻两组的湍动微反应床321之间。另外,需要说明的是,在实际生产过程中,二次热载体进口323的开设数量根据有机固体废弃物物料组成、处理规模、气态有机质热解提馏产物出口312温度和热解固态残渣出口334组成确定,其数量可以是0个,也可以是1个也可以是多个。反应下段35具有热载体进口331、热载体分布板332、残渣出口334。具体地,热载体进口331对称开设有两个,且设置在壳体31的侧面;残渣出口334开设有1个并位于壳体31底部中心处,且与壳体31中轴线同轴;热载体分布板332设置有一个且其形状与壳体31下端的截面形状相匹配,为了便于说明,定义热载体分布板332上表面与壳体31中心线的夹角为γ,夹角γ可以为0~90°之间的任一值。具体地,高温热载体自热载体进口331进入反应下段35,通过热载体分布板332分配均匀后从反应中段34底部进入串联的湍动微反应床321的最底部,自下而上流动为湍动微反应床321进行的热解提馏反应提供热量,高温热载体的压力为0.01~10mpag,温度为300~1000℃。本申请采用的热载体为单一组分气体(氧气除外)或贫氧或无氧的多组分气体混合物。如n2、氩气等惰性气体、co2气体、过热蒸汽或燃料燃烧后的烟气、热解尾气、合成气、炼厂干气或石化废气或弛放尾气等单一组分气体或此类气体的多组分气体混合物,均具有易获得性、安全性和可实现废气的再利用的优势。同时,有机固体废弃物自反应上段33的有机固体废弃物进口311进入壳体31内,靠重力下行,与上行的气态热解提馏产物与热载体的混合物直接接触换热,并经过吸热预热下行流入物料分配板314,汇集后进入反应中段34的顶部。经预热的有机固体废弃物从反应中段34顶部自上而下流动依次进入每一组湍动微反应床321,并与自下而上流动的高温热载体与热解提馏气态产物两者的混合物直接接触进行热解提馏反应;具体地,热解反应装置3的热解提馏反应压力为-0.1~10mpag,反应温度为300~1000℃。下行的有机固体废弃物与上行的高温热载体和热解提馏气态产物两者的混合物在主反应区3211和副反应区3212内部呈现气固两相湍动悬浮的充分混合状态直接接触换热,有机固体废弃物吸收高温热载体携带的热量发生有机质的裂解反应和提馏反应而产生低分子量的气态烃类物质及/或气相油品,并与梯级放热降温的高温热载体组成气态混合物自下而上流动。在反应中段34完成热解提馏反应的有机固体废弃物残渣物料下行经导渣板324汇集后流进反应下段35。有机固体废弃物固体残渣物料进一步经热载体分布板332汇集形成一定厚度的物料移动态床层,与经热载体分布板332分配均匀后上行的高温热载体直接接触换热并继续进行裂解反应和提馏反应,壳体31内的热解提馏反应压力为-0.1~10mpag,反应温度为300~1000℃;产生的气态反应产物随高温热载体一起上行,最终热解固态残留物自热解固态残渣出口334流出壳体31,进入后续残渣冷却与余热回收工序。另外,根据气态有机质热解提馏产物出口312温度和热解固态残渣出口334组成分析,如发现热解固态残渣中残余有机质含量超标则说明有机固体废弃物热解反应进行不完全,或气态有机质热解提馏产物出口312温度偏低时,则可以从反应下段35的热载体进口331加大热载体的流量,也可以在二次热载体进口323加入一定流量的热载体,也可以同时从反应下段35的热载体进口331加大热载体的流量及从二次热载体进口323的其中一个或多个同时加入一定流量的热载体。气态烃类和气相油品与梯级放热降温的热载体组成的混合物最后经反应器上段的气态有机质热解提馏产物和热载体混合物出口流出反应器,进入后续热解提馏产物余热回收利用与有机质分离回收工序。参照图3,根据上述热载体式有机固体废弃物的处理系统,具体地公开了一种有机固体废弃物的热载体处工艺,包括以下步骤:s1、预处理含水量约90%的油泥首先进入预处理装置1,通过干化工艺,将油泥中的含水量降至40%以下,含水油泥转化为干化油泥;s2、固废输送干化油泥进入进料装置2,利用皮带或者螺旋输送机送至料仓,料仓设置惰性气体吹扫装置,控制油泥中的氧气含量。干化油泥利用料仓底部设置的给料机,结合称重或者料位探测仪表实现进料速度控制;s3、热解反应干化油泥由进料装置2进入热解反应装置3,与热载体通过逆流方式进行直接换热并发生化学反应,转化为气相产物和固相产物,热载体的温度300~800℃,反应压力0~10mpa;s4、热量回收固相产物和气相产物进入热量回收装置4,通过直接或者间接热交换的方式将气相产物和固相产物所含有的热量进行回收,并得到气相产物、固相产品、液相产品和液相热载体;具体地,热量回收装置4可以是冷渣器,固相产物通过冷渣器与脱盐水换热降温后排出,油含量降低至3‰;热量回收装置4可以是余热锅炉,气相产物进入余热锅炉产生蒸汽,通过换热器加热氮气、二氧化碳、导热油等媒介,吸收热量后的介质送至预处理装置1,用于油泥的干化;气相产物在冷却过程中,会出现不凝气和液相产物,热量回收装置4可以是包括油水分离器,液相产物送至油水分离器,分离出的水经过净化后进入余热锅炉发生蒸汽重新通过换热器加热氮气、二氧化碳、导热油等媒介,吸收热量后的介质送至预处理装置1;分离出的油品则可作为产品出售,或者进入热载体发生装置6;s5、净化回收不凝气经过加压后进入净化装置5,除去其中的硫、氯等有害组分,一方面得到净化的不凝气,作为燃料补充至热载体发生装置6;s6、热载体发生热载体在热载体发生装置6中,再次吸收燃料燃烧放出的热量后,再进入热解反应装置3。具体地,各流股参数见表1。实施例1各流股参数根据已有运行数据,油泥直接热解固相产物的比例约为30%~50%,气相产物比例为5%~10%,液相产物比例为40%~65%,固相中的含油量可降至3‰以下,燃料油的能量利用效率为92%。实施例2参照图4,根据上述热载体式有机固体废弃物的处理系统,还具体地公开了另一种有机固体废弃物的热载体处理工艺,包括以下步骤:s1、预处理生物质进入预处理装置1,经过破碎、筛分及干燥后,其含水量降至20%以下,粒径为0~6mm。生物质可以是各种农林废弃物,本申请实施例中采用秸秆作为生物质。s2、固废输送在进料装置2中,以气力输送或者螺旋输送的方式送至热解料仓。当采用气力输送时,输送气体可以为净化装置5分离出的不凝气或者氮气、二氧化碳、氢气等气体;当采用螺旋输送时,应采用氮气、二氧化碳等惰性气体进行除氧。料仓设置惰性气体吹扫装置,控制油泥中的氧气含量。利用料仓底部设置的给料机,结合称重或者料位探测仪表实现进料速度控制;s3、热解反应生物质由进料装置2进入热解反应装置3,与热载体蒸汽通过逆流方式进行直接换热发生化学反应,转化为气相产物和固相产物,热载体的温度300~1300℃,反应压力0~10mpa;s4、热量回收气相产物和固相产物进入热量回收装置4,通过直接或者间接热交换的方式将气相产物和固相产物所含有的热量进行回收,并得到气相产物、固相产品和液相产品;热量回收装置4可以是冷渣器,固相产物通过冷渣器与脱盐水换热降温后排出,产品为生物炭,可以用作土壤改良产品,部分也可加入热载体发生装置6作为燃料;热量回收装置4可以是余热锅炉,气相产物进入余热锅炉产生蒸汽,通过换热器加热氮气、二氧化碳、导热油等媒介,吸收热量后的介质送至预处理装置1,用于生物质的干燥;气相产物在冷却过程中,会出现不凝气和液相产品。热量回收装置4可以包括油水分离器,液相产品送至油水分离器,分离出的水经过净化进入余热锅炉发生蒸汽重新通过换热器加热氮气、二氧化碳、导热油等媒介,吸收热量后的介质送至预处理装置1;油品则可作为产品出售,或者进入热载体发生装置6;s5、净化回收不凝气经过加压后进入净化装置5,净化装置5可以是脱硫脱氯设备,一方面除去其中的硫、氯等有害组分,得到净化的不凝气作为燃料补充至热载体发生装置6;另一方面分离出其中的热载体返回至热载体发生装置6;s6、热载体在热载体发生装置6中,再次吸收燃料燃烧放出的热量后,再进入热解反应装置3。具体地,各流股参数见表2。实施例2各流股参数根据已有运行数据,生物质热解后固相产物的比例为10%~30%,气相产物比例为20%~40%,液相产物比例为35%~65%,固相中的含油量可降至3‰以下,燃料油的能量利用效率为91%。实施例3参照图5,具体地公开了另一种热载体耦合式有机固体废弃物的处理系统,与实施例1的区别在于,将热解反应装置3和热载体发生装置6集合组成一体式的热解反应-热载体发生耦合装置7,大大降低工程造价费用,减小占地面积。具体地,参照图6,热解反应-热载体发生耦合装置7包括炉壳体46,炉壳体46包括由上至下依次相互连通的上段炉43、中段炉44、下段炉45,炉壳体46设置有耐火隔热衬里32。上段炉43的顶部或侧面上部设置n(n≥1)个有机固体废弃物物料进口431、n(n≥1)个气态有机质热解提馏产物和高温烟气的气态混合物出口432、物料进口分配板433及人孔38。物料进口分配板433的上表面与炉壳体46中心线的夹角α为0-180°之间的任一角度,并在其中心区域的底部(0°<α≤90°时)或顶部(90°<α<180°时)开设宽度或直径为a0(a0≥0)的缺口,对应地,在其底部(0°<β1<90°时)或顶部(90°<β2≤180°时)与耐火隔热衬里32内壁面之间开有宽度为b01和b02(b01≥0、b02≥0)的缺口或环隙,均为有机固体废弃物物料下行和气态物料上行的通道,且a0和b01及b02不同时为0。物料进口分配板433在0°<α<90°设置时,其顶部可以不开设缺口或环隙(b01和b02均为0),但其底部需开设缺口作为固态物料下行和气态物料上行的通道,且a0>0。物料进口分配板433在90°<α<180°设置时,在其顶部可以不开设缺口(即a0为0),但其两侧底部需开设宽度或环隙为b01和b02的缺口(b01和b02均>0)作为固态物料下行和气态物料上行的通道。物料进口分配板433的上表面形状是以有利于物料流动的结构,可以是平直的,也可以是波纹状,也可以是开设导流槽结构,也可以是这几种结构的不同组合。中段炉44作为有机固体废弃物物料热解提馏段,设置有n(n≥1)组串联的湍动微反应床343、出口导流板442和n(n≥0)个二次给热口443。每一组湍动微反应床343包括一块上导流板3214和一块下导流板3215,且以炉壳体46中心线为中心轴双向对称布置或双向非对称布置;每一组湍动微反应床343内具有主反应区,具体为上导流板3214与下导流板3215之间构成的空间区域;相邻两组湍动微反应床343之间具有副反应区,具体为上一组微反应床的下导流板3215与下一组微反应床的上导流板3214之间构成的两侧两个空间区域或环隙区域;上导流板3214的上表面与炉壳体46中心线的夹角β1为0-180°之间的任一角度;下导流板3215的上表面与炉壳体46中心线的夹角β2为0-180°之间的任一角度,且当90°≤β1<180°时0°<β2≤90°,相应地当0°<β1≤90°时90°≤β1<180°。每相邻两组湍动微反应床343的上导流板3214和下导流板3215与炉壳体46中心线的夹角β1与β2可以是相同数值,也可以是相互不同数值。每一组湍动微反应床343的上导流板3214中心区域顶部(90°≤β1<180°时)或底部(0°<β1<90°时)开有宽度或直径为a1(a1≥0)的缺口,对应地,在其底部(90°≤β1<180°时)或顶部(0°<β1≤90°时)与耐火隔热衬里32内壁面之间开有宽度为b11和b12(b11≥0、b12≥0)的缺口或环隙,均为固态物料下行和气态物料上行的通道,且a1和b11及b12不同时为0,且每相邻两组湍动微反应床343的上导流板3214的a1和b11及b12可以是相同数值,也可以是相互不同数值。每一组湍动微反应床343的下导流板3215中心区域底部(0°<β2≤90°时)或顶部(90°<β2<180°时)开设宽度或直径为a2(a2≥0mm)的缺口,对应地,在其顶部(0°<β2≤90°时)或底部(90°<β2<180°时)与耐火隔热衬里32内壁面之间开有宽度为b21和b22(b21≥0、b22≥0)的缺口或环隙,均为固态物料下行和气态物料上行的通道,且a2和b21及b22不同时为0,且每相邻两组湍动微反应床343的下导流板3215的a2和b21及b22可以是相同数值,也可以是相互不同数值。另外,上导流板3214和下导流板3215的上表面形状是以有利于物料流动的结构,可以是平直的,也可以是波纹状,也可以是开设导流槽结构,也可以是这几种结构的不同组合。中段炉44的n(n≥0)个二次给热口443设置在任何相邻两组湍动微反应床343之间位置,根据有机固体废弃物物料组成、处理规模、气态混合物出口432和排渣口453组成确定其数量为0个或n个。中段炉44的n(n≠0)个二次给热口443可以设置二次燃料燃烧器447,该二次燃料燃烧器447为气体燃料或液体燃料燃烧器或气液联合燃烧器;也可以从设置在中段炉44侧面位置的n(n≠0)个二次给热高温烟气出口455直接引入高温烟气进入对应的n(n≠0)个二次给热口443。每一组湍动微反应床343由m1(m1≥1,且m1≤n/2且取整数)块上导流板3214和m2(m2≥1,且m2≤n/2且取整数)块下导流板3215构成,其每相邻两组或若干组湍动微反应床343以炉壳体46中心线为中心轴分别以双向导流板和单向导流板两种形状交错布置。出口导流板442的上表面形状是以有利于物料流动的结构,可以是平直的,也可以是波纹状,也可以是开设导流槽结构,也可以是这几种结构的不同组合。出口导流板442的上表面与炉壳体46中心线的夹角β3为0-180°之间的任一角度,其中心区域底部(0°<β3≤90°时)或顶部(90°<β3<180°时)开设宽度或直径为a3(a3≥0)的缺口,对应地,在其顶部(0°<β1<90°时)或底部(90°<β2≤180°时)与耐火隔热衬里32内壁面之间开设宽度为b31和b32(b31≥0、b32≥0)的缺口或环隙,均为热解固态残渣下行和高温烟气上行的通道,且a3和b31及b32不同时为0。出口导流板442的形状与炉壳体46及其耐火隔热衬里32的截面形状相匹配。出口导流板442的形状也可以与上导流板3214或下导流板3215的设置方法相同或类似。物料进口分配板433、上导流板3214、下导流板3215、出口导流板442上可以开设n(n≥0)个通气孔,总开孔数量和总开孔面积根据有机固体废弃物物料粒径分布、处理规模和多级串联的湍动微反应床343的气相流速和压降确定,也可以不开设通气孔(n=0)。下段炉45设置有燃料燃烧器451、气体分布板452、排渣口453、人孔38、n(n≥0)个压温气体进口454、n(n≥0)个二次给热高温烟气出口455。燃料燃烧器451、排渣口453和人孔38设置在下段炉45的底部或侧面,数量可以分别是n(n≥1)个设置在不同位置;在下段炉45的底部或侧面气体分布板452下部位置设置数量为n(n≥1)个压温气体进口454;可以在下段炉45侧面气体分布板452上方设置n(n≥0)个二次给热高温烟气出口455或不设置(n=0);可以在下段炉45侧面且位于气体分布板452上方设置数量为n(n≥0)个压温气体进口454或不设置(n=0)。燃料燃烧器451为气体燃料或液体燃料燃烧器或气液联合燃烧器用于燃料在下段炉45内燃烧产生高温烟气作为热载体为有机固体废弃物热解提馏反应提供热量。气体分布板452主要起到通过通入压温气体来调节燃料燃烧产生高温烟气进入中段炉44温度的作用,同时也起到防止热解固态残渣下行流动不畅而附着架桥使其流入残渣出口353的作用,该压温温气体为具有易经济获得性、安全性、且不对热解反应及其热解产物产生不良影响的单一组分气体(氧气除外)或贫氧或无氧的多组分气体混合物。如n2、氩气等惰性气体、co2气体、蒸汽或燃料燃烧后的低温排放烟气、热解尾气、炼厂干气或石化废气或弛放尾气等单一组分气体或此类气体的多组分气体混合物。气体分布板452的形状与下段炉45的炉壳体46及其耐火隔热衬里32的截面形状相匹配。气体分布板452上表面与下段炉45的炉壳体46中心线的夹角γ为0-90°之间的任一角度,并开设有n(n≥1)个通气孔。下段炉45的燃料燃烧器451可以附加设置外通道通入压温气体来调节燃料燃烧产生高温烟气进入中段炉44的温度。下段炉45也可以通过将n(n≥1)个燃料燃烧器451设置在下段炉45的底部,气体分布板452作为布风板,并与炉壳体46及其耐火隔热衬里32的截面形状相匹配构建流化床,此时,气体分布板452需调整设置为流化床的常规布风板结构,n(n≥1)个压温气体进口454需设置在下段炉45所构建的流化床区域的侧面上部位置。下段炉45构建成流化床时,可以将部分有机固体废弃物物料从下段炉45加入炉内,与热解固态残渣共同在此流化床进行燃烧反应或高温热解反应。另外,上段炉43、中段炉44和下段炉45的炉壳体46及其耐火隔热衬里32的截面形状可以是圆筒形或椭圆形,也可以是矩形(正方形或长方形)或多边形,上段炉43、中段炉44和下段炉45的炉壳体46及其耐火隔热衬里32的截面形状可以是同一种截面结构,也可以是不同截面形状及其不同结构的组合;上段炉43、中段炉44和下段炉45的炉壳体46及其耐火隔热衬里32的截面面积可以相等,也可以不同。耐火隔热衬里32可以是n(n≥1)层耐火隔热浇注料结构,也可以是n(n≥1)层的耐火隔热砖结构,也可以是耐火隔热浇注料与耐火隔热砖的组合结构,也可以是列管式或盘管式的膜式水冷壁结构,也可以是冷却夹套结构,也可以是这几种结构形式的不同组合。上段炉43、中段炉44、下段炉45及其炉壳体46和耐火隔热衬里32可以是整体结构,也可以是分段连接结构。参照图7,根据上述热解反应-热载体发生耦合装置7,具体地公开了另一种热载体式有机固体废弃物的处理工艺,包括以下步骤:s1、预处理含水量约90%的油泥进入预处理系统,通过干化工艺,将油泥中的含水量降至40%以下,含水油泥转化为干化油泥;s2、固废输送干化油泥进入进料系统2,利用皮带或者螺旋输送机送至料仓,料仓设置惰性气体吹扫装置,控制油泥中的氧气含量。干化油泥利用料仓底部设置的给料机,结合称重或者料位探测仪表实现进料速度控制;s3、热解反应干化油泥由进料装置2进入热解反应-热载体发生耦合装置,干化油泥与热载体通过逆流方式在热解反应子装置31内进行直接换热并发生化学反应,转化为气相产物和固相产物,热载体的温度300~800℃,反应压力0~10mpa;s4、热量回收固相产物和气相产物进入热量回收装置4,通过直接或者间接热交换的方式将气相产物和固相产物所含有的热量进行回收,并得到气相产物、固相产品、液相产品和液相热载体;具体地,热量回收装置4可以是冷渣器,固相产物通过冷渣器与脱盐水换热降温后排出系统,固相产物的油含量降低至3‰以下;热量回收装置4可以是余热锅炉,气相产物进入余热锅炉产生蒸汽,通过换热器加热氮气、二氧化碳、导热油等媒介,吸收热量后的媒介送至预处理装置1,用于油泥的干化;分离出的热载体返回至热载体发生装置6;气相产物在冷却过程中,会出现不凝气和液相产物以及热载体。热量回收装置4可以包括油水分离器,液相产物送至油水分离器,分离出的水经过净化后进入余热锅炉发生蒸汽重新通过换热器加热氮气、二氧化碳、导热油等媒介,吸收热量后的介质送至预处理装置1;分离出的油品则可作为产品出售,或者进入热载体发生装置6;s5、净化回收不凝气经过加压后进入净化装置5,除去其中的硫、氯等有害组分,得到净化的不凝气,并作为燃料补充至热载体发生装置6;s6、热载体发生热载体在热载体发生装置6中,再次吸收燃料燃烧放出的热量后,直接进入热解反应装置3;具体地,各流股参数见表1。实施例3各流股参数流股号介质名称温度(℃)压力(mpag)流量(kg/h)ca(301)油泥2502255cb(302)干化油泥12001041cc(303)热解油泥5500425cd(304)热解油泥600425ce(305)油气3500.033316cf(306)不凝气600.0248cg(307)不凝气600.0148ch(308)油水混合物60-0.01568ci(309)水400.3272cj(310)热载体600.32700ck(311)燃料油2002.5246cl(312)油品2002.550cn(314)蒸汽1440.3272根据已有运行数据,油泥直接热解固相产物的比例约为30%~50%,气相产物比例为5%~10%,液相产物比例为40%~65%,固相中的含油量可降至3‰,燃料油的能量利用效率为92.3%。实施例4参照图8,还具体地公开了一种有机固体废弃物的热载体处理工艺,包括以下步骤:s1、预处理生物质进入预处理装置1,经过破碎、筛分及干燥后,其含水量降至20%以下,粒径为0~6mm。s2、固废输送在进料装置2中,以气力输送或者螺旋输送的方式送至热解料仓。当采用气力输送时,输送气体可以为净化装置5分离出的不凝气或者氮气、二氧化碳、氢气等气体;当采用螺旋输送时,应采用氮气、二氧化碳等惰性气体进行除氧。料仓设置惰性气体吹扫装置,控制油泥中的氧气含量。利用料仓底部设置的给料机,结合称重或者料位探测仪表实现进料速度控制。s3、热解反应生物质由进料装置2进入热解反应装置3,与热载体蒸汽通过逆流方式进行直接换热发生化学反应,转化为气相产物和固相产物,热载体的温度300~1300℃,反应压力0~10mpa;s4、热量回收气相产物和固相产物进入热量回收装置4,通过直接或者间接热交换的方式将气相产物和固相产物所含有的热量进行回收,并得到气相产物、固相产品和液相产品。热量回收装置4可以是冷渣器,固相产物通过冷渣器与脱盐水换热降温后排出,产品为生物炭,可以用作土壤改良产品,部分也可加入热载体发生装置6作为燃料;热量回收装置4可以是余热锅炉,气相产物进入余热锅炉产生蒸汽,通过换热器加热氮气、二氧化碳、导热油等媒介,吸收热量后的介质送至预处理装置1,用于生物质的干燥;气相产物在冷却过程中,会出现不凝气和液相产品。热量回收装置4可以包括油水分离器,液相产品送至油水分离器,分离出的水经过净化进入余热锅炉发生蒸汽加热氮气、二氧化碳、导热油等媒介,吸收热量后的介质送至预处理装置1,用于生物质的干燥;油品则可作为产品出售,或者进入热载体发生装置6;s5、净化回收不凝气经过加压后进入净化装置5,净化装置5可以是脱硫脱氯设备,一方面除去其中的硫、氯等有害组分,作为燃料补充至热载体发生装置6;另一方面分离出其中的热载体,返回补充至热载体发生装置6;s6、热载体发生热载体在热载体发生装置6中,再次吸收燃料燃烧放出的热量后,再进入热解反应装置3;具体地,各流股参数见表2。实施例4各流股参数流股号介质名称温度(℃)压力(mpag)流量(kg/h)da(401)生物质2501000db(402)干化油泥1100450dc(403)生物炭500090dd(404)生物炭25090de(405)油气3500.034310df(406)不凝气600.023975dg(407)不凝气800.0125dh(408)油水混合物60-0.01335di(409)水400.3150dj(410)热载体800.33950dk(411)燃料油2002.5120dl(412)燃料油2002.565dn(414)蒸汽1440.3150根据已有运行数据,生物质热解后固相产物的比例为10%~30%,气相产物比例为20%~40%,液相产物比例为35%~65%,固相中的含油量可降至3‰以下,燃料油的能量利用效率为91.2%。本申请一种热载体耦合式有机固体废弃物的处理工艺以及系统的实施原理为:利用热载体直接传热的方式,提高了能量利用效率,也避免了二次污染;对工艺流程进行能量和物质集成优化,进一步提高了物质和能量利用效率。本技术通过将有机固体废弃物中的有机组分进行提取,实现有机固体废弃物的资源化利用,获得的产品一部分循环利用为系统运行提供能量,一部分外售产生经济效益。有机固体废弃物在无氧或者缺氧条件下,与热载体直接接触,受热转化为气相和固相产物。该系统提高了热解反应和提馏反应速度、缩短了热解提馏反应时间、提高了有机固体废弃物中的有机质转化回收产率;提高了有机固体废弃物热解提馏过程的给热效率与吸热效率,提高了热量利用效率、有效降低了能耗。将热解反应装置3和热载体发生装置6集成在一起,降低了工程造价费用,减小了占地面积。本工艺处理得到的油泥含油量<3‰,达到农用污泥标准;处理生物质得到的生物炭可应用于农业用途以及碳收集及储存使用。本工艺的燃料油的能量利用效率大于91%,从而大大提高了热解技术的能量利用率。以上均为本申请的较佳实施例,并非依此限制本申请的保护范围,故:凡依本申请的结构、形状、原理所做的等效变化,均应涵盖于本申请的保护范围之内。当前第1页12
再多了解一些
本文用于企业家、创业者技术爱好者查询,结果仅供参考。