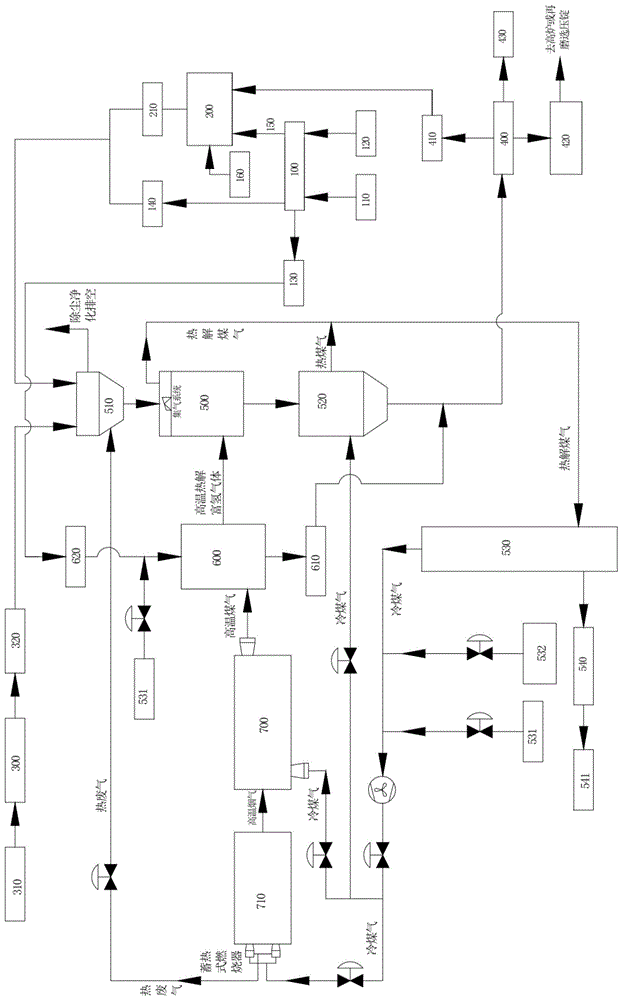
本发明涉及冶金还原技术领域,特别涉及一种富氢气体冶金还原共低价末煤热解工艺及系统。
背景技术:
全球钢铁生产中75%采用高炉工艺,在传统的“长流程”生产方式中,都是用焦炭还原铁矿石,虽然高炉炼铁在世界上广泛应用,但高炉炼铁的存在极大的弊端如:高炉的焦炭用量相当大而炼焦煤越来越少焦炭价格上涨,环境污染严重,炼铁流程长投资大等等。所以为了克服以上缺点,以氢代碳已经成为低碳冶金的新路线。氢冶金的主要矛盾在于氢能的成本较高,如何找到低成本可用的“氢能”,才是氢能冶金的关键。
目前我国的氢气主要来源是天然气为原料制取,是当今世界上制取氢气主要的方法。该方法在我国已经具有成熟的工艺。但与煤炭资源储备不同,我国有限的天然气资源储备较低,依赖大量进口,难以满足工业快速增长的消费需求。所以利用天然气生产还原气体炼铁已无法满足我国对还原铁的需求,如何打破天然气生产氢气的技术,寻求其他代替品制取氢气,已成为我国急需解决的一大问题。但我国低阶煤蕴藏量占比较高,低阶煤被视作一种劣质煤炭资源。所以如何高效转化利用低阶煤就成了煤炭利用的一个重要问题。
技术实现要素:
本发明的目的克服现有技术存在的不足,为实现以上目的,采用一种富氢气体冶金还原共低价末煤热解工艺及系统,以解决上述背景技术中提出的问题。
一种富氢气体冶金还原共低价末煤热解工艺,具体步骤包括:
s1、通过煤原料获取末煤、小粒煤、半焦粉及焦煤,利用小粒煤及经过处理的半焦粉、焦煤作为炭化还原系统的第一路原料进入烘干系统;
s2、矿石、铁精粉经过筛分成型车间后形成块矿和矿团,并进入烘干系统进行烘干和预加热后,作为炭化还原系统的第二路原料;
s3、将第一路原料与第二路原料在烘干系统中均匀混合并送入炭化还原系统,第一路原料经过高温炭化和析炭反应得到热解煤气和高温热解富氢气体,同时第二路原料在高温热解富氢气体的作用下进行高温还原;
s4、将得到的热解煤气送入荒煤气洗涤净化系统进行焦油回收、煤气脱硫及净化处理,形成冷煤气,再利用煤气鼓风机将冷煤气送回系统自用;
s5、将冷煤气分为三个部分进行系统自用,第一部分冷煤气作为燃料进入燃烧室充分燃烧,得到的高温烟气进入煤气加热重整系统,与第二部分冷煤气在煤气加热重整系统中与高温烟气进行热交换得到高温煤气,并在煤气加热重整系统中对热解煤气的主要成分进行高温裂解,得到裂解重整后的高温煤气;
s6、在末煤流化热解系统中将末煤进行流化热解,并对得到的高温煤气进行析炭反应,得到高温热解富氢气体和半焦粉,且半焦粉经过冷却排料装置后进入筛分磁选车间循环筛选;
s7、将得到高温热解富氢气体作为热载体和还原剂进入炭化还原系统,并循环送入的第一路原料进行高温炭化和析炭反应生成热解煤气,同时对部分热解煤气进行再反应,生成高温热解富氢气体,该高温热解富氢气体对第二路原料进行高温还原;
s8、将炭化还原系统内还原后得到的还原铁或者预还原矿团,以及剩余的半焦粉、型煤和型焦进入物料冷却排料系统520,同时利用第三部分的冷煤气对还原铁进行保护冷却后再进入筛分磁选车间。
作为本发明的进一步的方案:所述通过煤原料获取末煤、小粒煤、半焦粉及焦煤,利用小粒煤及经过处理的半焦粉、焦煤作为炭化还原系统的第一路原料进入烘干系统的具体步骤包括:
s11、获取煤原料并送入洗选车间经过洗选后,产出末煤、小粒煤、半焦粉及焦煤;
s12、将步骤s11的半焦粉、焦煤添加粘合剂并送入型煤型焦成型车间加工处理后,生成型煤和型焦,其中型煤、型焦及小粒煤作为作为炭化还原系统的第一路原料进入烘干系统。
作为本发明的进一步的方案:所述步骤s11中末煤经过上料系统送入末煤流化热解系统进行流化热解。
作为本发明的进一步的方案:所述步骤s5中的第一部分的冷媒气在燃烧室中燃烧产生热废气,并将热废气送入烘干系统进行烘干处理后净化除尘排入大气。
作为本发明的进一步的方案:所述步骤s8的炭化还原系统剩余的小粒煤、型煤和型焦进行干馏,在干馏过程中产生热解煤气。
一种富氢气体冶金还原共低价末煤热解系统,包括:
筛选成型系统,所述筛选成型系统包括洗选车间、型煤型焦成型车间、筛分成型车间,以及筛分磁选车间;
主产系统,所述主产系统包括烘干系统、设置于烘干系统出料口的炭化还原系统,以及设置于炭化还原系统出料口的物料冷却排料系统520;
热交换系统,所述热交换系统包括洗涤净化系统、燃烧室,以及煤气加热重整系统;
末煤系统,所述末煤系统包括末煤流化热解系统,以及设置于末煤流化热解系统的出料口的冷却排料装置;
所述洗选车间设置有三个出料口,第一出料口与型煤型焦成型车间的入料口相连,第二出料口与型煤型焦成型车间的出料口合并后连接于烘干系统的入料口,第三出料口通过上料系统与末煤流化热解系统的入料口相连;
所述末煤流化热解系统的进气口与煤气加热重整系统的出气口相连,且末煤流化热解系统的出气口与炭化还原系统的进气口相连;
所述洗涤净化系统设置有三个出气口,第一出气口与燃烧室的进气口相连,第二出气口和燃烧室均与煤气加热重整系统的进气口相连,第三出气口与物料冷却排料系统520的进气口相连;
所述筛分磁选车间的入料口与冷却排料装置和物料冷却排料系统520的出料口均相连,且筛分磁选车间的半焦粉出口与洗选车间的入料口相连。
作为本发明的进一步的方案:所述洗涤净化系统的出料口设置有回收系统。
作为本发明的进一步的方案:所述燃烧室的热废气出口连接于烘干系统的进气口。
与现有技术相比,本发明存在以下技术效果:
通过采用上述的技术方案,利用末煤进行热解产生的热解煤气作为产生高温热解富氢气体的原料,能够提高热解煤气的利用率。同时还可以通过煤气加热重整系统进行热交换,使得冷煤气转换为高温煤气,再进一步将高温煤气进行裂解重整,利用低阶煤的高温炭化及热解煤气中甲烷和一氧化碳的析炭反应,使裂解重整的高温煤气组合成高温热解富氢气体。并且在炭化还原系统中第一路原料在高温炭化过程中对部分热解煤气再次进行裂解重整和析炭反应,生成高温热解富氢气体。该高温热解富氢气体对矿石快进行均质还原,同时利用高温热解富氢气体的热量对小粒煤和型煤进行中温热解,即利用了煤气的热效率又提高热解煤气和焦油的生产率。最后利用热解产生的高温热解富氢气体作为冶金还原工序的还原剂,还原剂成本低。生产过程中,根据实际情况可以调节低阶煤的投入量,从而使其保持浓郁的还原气氛中。上述工艺过程中,实现了热解煤气的高效利用,突破了以往冶金还原段还原气体稀薄的限制。能够对大规模的廉价末煤等低价煤进行开发利用。
附图说明
下面结合附图,对本发明的具体实施方式进行详细描述:
图1为本申请公开的一些实施例的富氢气体冶金还原共低价末煤热解工艺的流程框图;
图2为本申请公开的一些实施例的富氢气体冶金还原共低价末煤热解系统示意图。
图中:100、洗选车间;110、焦煤;120、低价煤;130、末煤;140、小粒煤;150、半焦粉及焦煤;160、粘合剂;200、型煤型焦成型车间;210、型煤型焦;300、筛分成型车间;310、矿石、铁精粉;320、块矿和矿团;400、筛分磁选车间;410、半焦粉;420、还原铁或者预还原矿团;430、型焦;500、炭化还原系统;510、烘干系统;520、物料冷却排料系统520;530、洗涤净化系统;531、氮气;532、启动用液化气;540、回收系统;541、煤焦油;600、末煤流化热解系统;610、冷却排料装置;620、上料系统;700、煤气加热重整系统;710、燃烧室。
具体实施方式
下面将结合本发明实施例中的附图,对本发明实施例中的技术方案进行清楚、完整地描述,显然,所描述的实施例仅仅是本发明一部分实施例,而不是全部的实施例。基于本发明中的实施例,本领域普通技术人员在没有做出创造性劳动前提下所获得的所有其他实施例,都属于本发明保护的范围。
请参考图1和图2,本发明实施例中,一种富氢气体冶金还原共低价末煤热解系统,包括:
筛选成型系统,所述筛选成型系统包括用于焦煤110、低阶煤120的洗选车间100、用于半焦粉、型煤成型的型煤型焦成型车间200、用于矿石、铁精粉310的筛分成型车间300,以及用于半焦粉、型焦、还原铁或预还原矿团筛分磁选的筛分磁选车间400;
主产系统,所述主产系统包括用于块矿和矿团320、小粒煤140、型煤型焦210进行烘干预热的烘干系统510、设置于烘干系统510出料口用于小粒煤140、型煤型焦炭化还原的炭化还原系统500,以及设置于炭化还原系统500出料口用于半焦粉410、型焦430、还原铁或预还原矿团冷却排料的物料冷却排料系统;
热交换系统,所述热交换系统包括用于荒煤气洗涤净化的洗涤净化系统530、用于冷煤气燃烧产生热烟气的燃烧室710,以及用于冷煤气换热和裂解的煤气加热重整系统700;
末煤系统,所述末煤系统包括末煤流化热解系统600,以及设置于末煤130流化热解系统的出料口用于半焦粉冷却排料的冷却排料装置610;
所述洗选车间100设置有三个出料口,第一出料口与型煤型焦成型车间200的入料口相连,第二出料口与型煤型焦成型车间200的出料口合并后连接于烘干系统510的入料口,第三出料口通过用于末煤130上料的上料系统620与末煤流化热解系统600的入料口相连;
所述末煤流化热解系统600的进气口与煤气加热重整系统700的出气口相连,且末煤流化热解系统600的出气口与炭化还原系统500的进气口相连;
所述洗涤净化系统530设置有三个出气口,第一出气口与燃烧室710的进气口相连,第二出气口和燃烧室710均与煤气加热重整系统700的进气口相连,第三出气口与物料冷却排料系统的进气口相连;具体的,炭化还原系统500中产生的热解煤气在洗涤净化系统530中洗涤净化后的回收利用,并进行裂解重整生成高温热解富氢气体。
所述筛分磁选车间400的入料口与冷却排料装置610和物料冷却排料系统的出料口均相连,且筛分磁选车间400的半焦粉出口与洗选车间100的入料口相连。
所述洗涤净化系统530的出料口设置有用于煤焦油541回收的回收系统540。
所述燃烧室710的热废气出口连接于烘干系统510的进气口。该热废气通过除尘净化过程后排空。
一种富氢气体冶金还原共低价末煤热解工艺,具体步骤包括:
s1、通过煤原料获取末煤130、小粒煤140、半焦粉及焦煤150,利用小粒煤140及经过处理的半焦粉及焦煤150作为炭化还原系统500的第一路原料进入烘干系统510,具体步骤包括:
s11、获取煤原料并送入洗选车间100经过洗选后,产出末煤130、小粒煤140、半焦粉及焦煤150;
s12、将步骤s11的半焦粉及焦煤150添加粘合剂160并送入型煤型焦成型车间200加工处理后,生成型煤型焦210,其中型煤型焦210及小粒煤140作为作为炭化还原系统500的第一路原料进入烘干系统510。其中末煤130经过上料系统620送入末煤流化热解系统600进行流化热解。具体的,煤原料包括焦煤110、低阶煤120,以及筛分磁选车间400送出的半焦粉。
s2、矿石、铁精粉310经过筛分成型车间300后形成块矿和矿团320,并进入烘干系统510进行烘干和预加热后,作为炭化还原系统500的第二路原料;
s3、将第一路原料与第二路原料在烘干系统510中均匀混合并送入炭化还原系统500,第一路原料经过高温炭化和析炭反应得到热解煤气和高温热解富氢气体,同时第二路原料在高温热解富氢气体的作用下进行高温还原;
s4、将得到的热解煤气送入荒煤气洗涤净化系统530进行焦油回收、煤气脱硫及净化处理,形成冷煤气,再利用煤气鼓风机将冷煤气送回系统自用;
s5、将冷煤气分为三个部分进行系统自用,第一部分冷煤气作为燃料进入燃烧室710充分燃烧,得到的高温烟气进入煤气加热重整系统700,与第二部分冷煤气在煤气加热重整系统700中与燃烧室710充分燃烧得到的高温烟气进行热交换得到高温煤气,并在煤气加热重整系统700中对热解煤气的主要成分进行高温裂解,得到裂解重整后的高温煤气;具体的,该热解煤气的主要成分为甲烷和一氧化碳;
具体的,所述步骤s5中的第一部分的冷媒气在燃烧室710中燃烧产生热废气,并将热废气送入烘干系统510进行烘干处理后净化除尘排入大气。
s6、在末煤流化热解系统600中将末煤130进行流化热解,并对得到的高温煤气进行析炭反应,得到大量的高温热解富氢气体和半焦粉,其中半焦粉经过冷却排料装置610后进入筛分磁选车间400循环筛选;
s7、将得到高温热解富氢气体作为热载体和还原剂进入炭化还原系统500,并循环送入的第一路原料进行高温炭化和析炭反应生成热解煤气,同时对部分热解煤气进行再反应,生成高温热解富氢气体,该高温热解富氢气体对第二路原料进行高温还原;
s8、将炭化还原系统500内还原后得到的还原铁或者预还原矿团420,以及剩余的半焦粉、型煤和型焦进入物料冷却排料系统,同时利用第三部分的冷煤气对还原铁进行保护冷却后再进入筛分磁选车间400。具体的,物料冷却排料系统的冷媒气出气口添加氮气531,以及用于启动的启动用液化气532。
所述步骤s8的炭化还原系统500剩余的小粒煤140、型煤和型焦进行干馏,在干馏过程中产生热解煤气。
具体的,在筛分磁选车间400磁选筛分出的型焦、还原铁或预还原矿团可作为产品销售。
尽管已经示出和描述了本发明的实施例,对于本领域的普通技术人员而言,可以理解在不脱离本发明的原理和精神的情况下可以对这些实施例进行多种变化、修改、替换和变型,本发明的范围由所附权利要求及其等同物限定,均应包含在本发明的保护范围之内。
本文用于企业家、创业者技术爱好者查询,结果仅供参考。