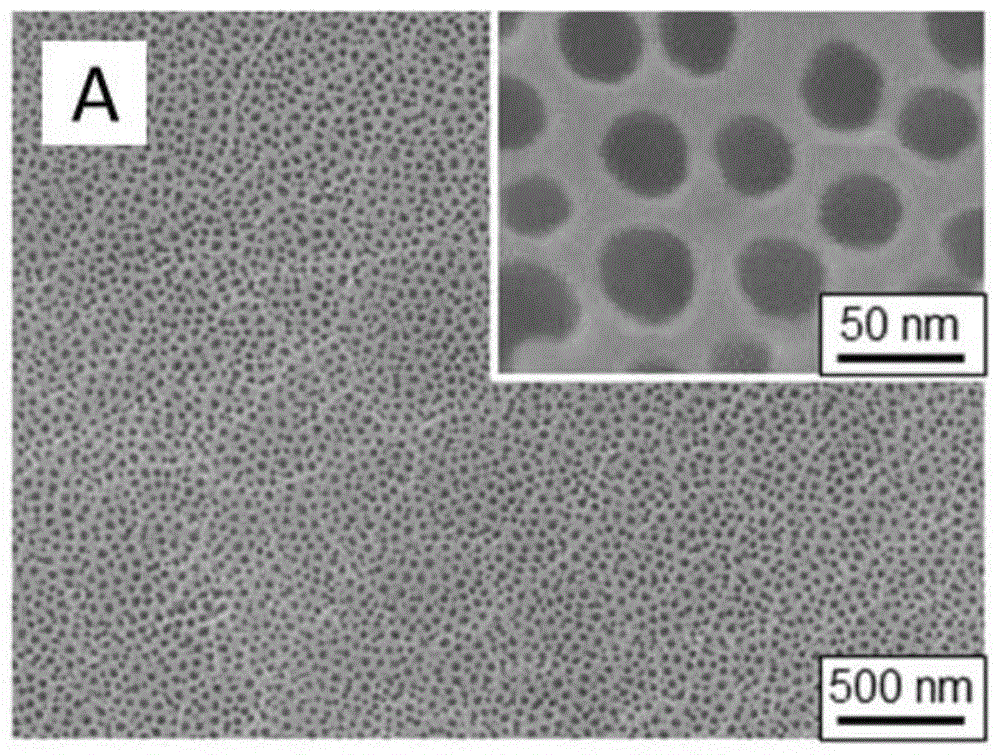
本公开内容涉及金属构件。
背景技术:
工业上需要具有斥液性表面的金属构件。
作为斥液性的表面,已知被称为注液光滑多孔表面(slipperyliquid-infusedporoussurface,slips)的液体易滑性表面,所述液体易滑性表面为包含表面自由能低并且具有微细凹凸结构的粗糙表面和涂布在该粗糙表面上的润滑油膜的斥液性表面。
表面自由能低的粗糙表面提高了润滑油的湿润并且防止了液体牢固地附着在固体表面上,因此附着在润滑油膜上的液滴得到高的移动性,在微小的倾斜下即容易滑落。
认为由于slips具有这样的特征,因此不仅能够用作斥液性、防污性和耐腐蚀性表面,而且防止冰附着的难附冰性表面、防止血液等源自生物的液体的附着的耐生物污损表面、以及利用了润滑油膜上液滴的高凝聚性的集水技术等利用以往的超斥水、超斥油性表面难以实现的应用展开也变得可能。
需要说明的是,作为表面自由能低的物质的代表例,可以列举聚四氟乙烯(ptfe;临界界面张力γc=18mnm-1)等氟类树脂,但它们的用途是受局限的。
另一方面,工业上有很多需求的是各种金属氧化物表面上的斥液化。已知金属氧化物的表面自由能与其它物质相比具有非常高的值,但可以通过利用自组装有机单分子膜(sam)将表面进行改性而大幅降低表面自由能,所述自组装有机单分子膜(sam)包含在末端具有-cf3(γc=6mnm-1)的长链全氟烷基、具有-ch3(γc=24mnm-1)的长链烷基。其中,近年来广泛使用的膦酸衍生物其自身是非常稳定的化合物,密度比以前已知的硅烷偶联剂高,形成稳定的sam。
另外,如专利文献1所公开的那样,已知对于汽车发动机部件等钢铁材料,利用钢铁材料的表面处理方法能够提高钢铁材料的耐冲击性、耐磨损性和耐腐蚀性,在所述钢铁材料的表面处理方法中,对钢铁材料进行等离子体氮化,然后注入氮离子,使钢铁材料表面的氮浓度为30原子%以上。
现有技术文献
专利文献
专利文献1:日本特开2003-073800号公报
技术实现要素:
发明所要解决的课题
用于形成上述sam的化学物质价格昂贵,另外,在用液相法进行利用sam的涂布的情况下要求严格的溶液管理,在用气相法进行的情况下需要昂贵的设备。
因此,若能够在不需要利用sam等的表面处理的情况下制造具有斥液性表面的金属构件,则可以期待在大规模产业化时实现处理工序的简化、大幅的成本削减。
但是,迄今为止认为,为了使附着的液体滑落,用于降低金属氧化物表面的表面自由能的利用sam等的表面处理是必不可少的。
实际上,本发明人得到了如下见解:即使使用作为slips的润滑油而广为人知的包含氟类高分子的润滑油、硅油,若不进行利用sam等的表面处理,则连水的附着也无法防止。
本发明的目的在于,提供一种在不需要利用sam等的表面处理的情况下具有斥水性和耐腐蚀性的表面的金属构件。
用于解决课题的手段
本发明人发现,通过以下手段能够实现上述课题:
《方案1》
一种金属构件,其中,所述金属构件具有多孔表面,所述多孔表面被含有二烷基二硫代磷酸锌(zndtp)的烃类油直接覆盖。
《方案2》
如方案1所述的金属构件,其中,所述多孔表面为氧化表面。
《方案3》
如方案2所述的金属构件,其中,所述多孔表面为阳极氧化表面。
《方案4》
如方案1~3中任一项所述的金属构件,其中,所述金属构件为al、ti、fe或mg的构件或者这些金属中的任一者的合金的构件或者不锈钢的构件。
《方案5》
如方案1~4中任一项所述的金属构件,其中,所述二烷基二硫代磷酸锌(zndtp)的浓度相对于所述烃类油为0.1质量%~30.0质量%。
《方案6》
如方案1~5中任一项所述的金属构件,其中,所述烃类油为机油。
《方案7》
如方案1~6中任一项所述的金属构件,其中,所述金属构件为汽车用构件。
《方案8》
如方案7所述的金属构件,其中,所述金属构件用于被供给了机油的部分。
《方案9》
如方案7或8所述的金属构件,其中,所述金属构件为中间冷却器用构件。
发明效果
根据本公开内容,能够提供一种在不需要利用sam等的表面处理的情况下具有斥水性和耐腐蚀性的表面的金属构件。
附图说明
[图1a]图1a为具有多孔表面的铝板表面的扫描型电子显微镜(sem)图像。
[图1b]图1b为具有经过层次结构化(階層構造化)的多孔表面的铝板表面的扫描型电子显微镜(sem)图像。
[图1c]图1c为表示水滴或汽车用机油滴相对于参考例1~4的铝板各自的表面的接触角的图。
[图2a]图2a为表示实施例1和2以及比较例5的铝板各自的铝板转速与汽车用机油的残留量的关系(旋转时间:60秒)的图。
[图2b]图2b为表示实施例1和2以及比较例5的铝板各自的铝板转速与10μl的水滴的滚落角(転落角)的关系(旋转时间:60秒)的图。
[图2c]图2c为表示实施例1和2以及比较例5的铝板各自的汽车用机油的残留量与10μl的水滴的滚落角的关系(旋转时间:10、60、300秒)的图。
[图3]图3为表示实施例1和2、比较例5和7的铝板在混合液中的浸渍时间与10μl水滴的滚落角的关系的图。
[图4]图4为表示实施例1和2以及比较例1~6的铝板在耐腐蚀试验后的重量变化的图。
[图5a]图5a为未进行层次结构化而进行了阳极氧化的铝板表面在耐腐蚀试验前的扫描型显微镜(sem)图像。
[图5b]图5b为比较例5的铝板表面在耐腐蚀试验后的扫描型显微镜(sem)图像。
[图5c]图5c为比较例3的铝板表面在耐腐蚀试验后的扫描型显微镜(sem)图像。
[图5d]图5d为实施例1的铝板表面在耐腐蚀试验后的扫描型显微镜(sem)图像。
[图5e]图5e为比较例1的铝板表面在耐腐蚀试验后的扫描型显微镜(sem)图像。
[图6a]图6a为进行了层次结构化并且进行了阳极氧化的铝板表面在耐腐蚀试验前的扫描型显微镜(sem)图像。
[图6b]图6b为比较例6的铝板表面在耐腐蚀试验后的扫描型显微镜(sem)图像。
[图6c]图6c为比较例4的铝板表面在耐腐蚀试验后的扫描型显微镜(sem)图像。
[图6d]图6d为实施例2的铝板表面在耐腐蚀试验后的扫描型显微镜(sem)图像。
[图6e]图6e为比较例2的铝板表面在耐腐蚀试验后的扫描型显微镜(sem)图像。
[图7]图7为表示参考例5的铝板的制作方法的图。
[图8a]图8a为表示参考例5的铝板表面的状态和放置有10μl的水滴时的接触角的图。
[图8b]图8b为表示参考例6的铝板表面的状态和放置有10μl的水滴时的接触角的图。
[图9a]图9a为表示参考例5的铝板在利用汽车用机油浸渍、洗涤后的表面的x射线光电子能谱法(xps)分析结果的图。
[图9b]图9b为表示参考例5的铝板在利用汽车用机油浸渍、洗涤后的表面的x射线光电子能谱法(xps)分析结果的图。
[图9c]图9c为表示参考例5的铝板在利用汽车用机油浸渍、洗涤后的表面的x射线光电子能谱法(xps)分析结果的图。
[图10]图10为表示实施例3~5和比较例8的铝板的电化学测定结果的图。
[图11]图11为表示实施例3和比较例8~10的铝板的电化学测定结果的图。
具体实施方式
以下,对本公开内容的实施方式详细说明。需要说明的是,本公开内容不限于以下的实施方式,可以在公开的主旨的范围内进行各种变形来实施。
本公开内容的金属构件具有多孔表面,所述多孔表面被含有二烷基二硫代磷酸锌(zndtp)的烃类油直接覆盖。
《金属构件》
在本公开内容中,金属构件具有多孔表面。
在此,多孔表面是指形成在金属构件的表面上的多孔覆膜,例如可以为具有与金属构件同种金属的氧化物的氧化表面。更具体而言,多孔表面可以为阳极氧化表面。
需要说明的是,阳极氧化表面可以通过将金属构件进行阳极氧化而得到,例如,在金属构件为al构件的情况下,可以通过氧化铝膜(アルマイト)处理、更具体而言通过将al作为阳极( 极)进行电解处理而生成氧化膜(al2o3)的表面处理来得到。需要说明的是,氧化铝膜处理例如可以基于jish8601或jish8603等进行,但也可以为其它方法。
多孔表面的厚度和孔径没有特别限定。
多孔表面的厚度可以根据金属构件的用途适当调节。
多孔表面只要是液体易滑性表面(slips),则其形状就没有限定。多孔表面的各孔的孔径(直径)可以为1nm以上且5μm以下。多孔表面可以具有微米级凹凸结构、纳米级凹凸结构或它们混杂存在的结构,还可以具有它们的层次结构。
例如,在多孔表面具有微米级凹凸结构情况下,多孔表面的各孔的孔径(直径)可以为0.1μm以上且5μm以下、优选为0.1μm以上且0.5μm以下。
另外,在多孔表面具有纳米级的凹凸结构的情况下,多孔表面的各孔的孔径(直径)可以为1nm以上且100nm以下、优选为30nm以上且100nm以下。
金属构件的材料可以为能够形成多孔表面的任意金属,例如,金属构件可以为al、ti、fe或mg的构件或者这些金属中的任一者(いずれか,即“任意者”)的合金的构件或者不锈钢的构件。
金属构件可以为用于任意用途的构件,例如可以为车辆用构件、更具体而言为汽车用构件。
在金属构件为汽车用构件的情况下,优选用于被供给了机油的部分。这是因为,在将本公开内容的金属构件应用于这样的部分的情况下,即使作为烃类油的机油从金属构件的表面脱离,也能够始终向金属构件供给机油。
在金属构件为汽车用构件的情况下,金属构件可以为中间冷却器用构件。中间冷却器为高温空气流入的装置,根据汽车的构成,废气也会流入,因此在设置于汽车中的装置中也有容易腐蚀的构件。作为这样的构件,例如可以列举热交换器等。因此,通过将本公开内容的金属构件应用于这样的构件,能够提高中间冷却器的耐腐蚀性。
《烃类油》
烃类油至少含有二烷基二硫代磷酸锌(zndtp)。烃类油可以为链烷烃类油或聚α-烯烃。另外,烃类油例如可以为润滑油、具体而言为机油、更具体而言为汽车用机油。
二烷基二硫代磷酸锌(zndtp)在包含在烃类油中的状态下,对金属构件的表面赋予斥水性。更具体而言,认为通过将含有二烷基二硫代磷酸锌(zndtp)的烃类油涂布在金属构件上,二烷基二硫代磷酸锌(zndtp)化学吸附至金属构件的表面等而形成斥液性的覆膜。
二烷基二硫代磷酸锌(zndtp)的浓度相对于烃类油可以为0.1质量%~30.0质量%。二烷基二硫代磷酸锌(zndtp)的浓度可以为0.1质量%以上、1.0质量%以上、2.0质量%以上或5.0质量%以上,并且可以为30.0质量%以下、20.0质量%以下、10.0质量%以下或5.0质量%以下。
[实施例]
《参考例1~4》
以如下的方式制作参考例1~4的金属构件,评价各例中的斥液性。
<参考例1>
将99.5%铝(al)板切成20mm×50mm的大小,通过超声波洗涤进行10分钟的丙酮脱脂。接着,为了除去氧化膜而在1.0m的naoh水溶液(60℃)中浸渍120秒钟,进一步为了除去在前一个过程中产生的污物而在1.0m的hno3水溶液(60℃)中浸渍180秒钟。
接着,利用0.3m的h2so4水溶液(15℃)以25v的极板间电压进行180秒钟的阳极氧化,形成具有纳米级的孔的阳极氧化膜。这是在以上述基板作为工作电极、以另外的al板作为对电极的双电极系统中进行的。
然后,通过在5重量%的h3po4水溶液(30℃)中浸渍15分钟来进行孔径的扩张。
最后,实施4分钟氧等离子体处理,将表面净化,由此得到具有多孔的阳极氧化表面的铝板。
<参考例2>
除了在阳极氧化前进行化学蚀刻而形成微米级的蚀刻坑以外,与参考例1同样地操作而得到具有层次结构的铝板。
<参考例3>
对参考例1的铝板进行氧等离子体处理,然后在1mm的cf3(cf2)7po(oh)2(全氟辛基膦酸;fopa)的乙醇溶液中浸渍2天,最后在大气气氛(100℃)下进行1小时热处理,由此在参考例1的铝板表面上形成自组装有机单分子膜(sam)。
<参考例4>
除了使用参考例2的铝板代替参考例1的铝板以外,与参考例3同样地操作而在具有层次结构的参考例2的铝板的表面上形成自组装有机单分子膜(sam)。
<斥液性的测定>
(测量方法)
对参考例1~4的铝板分别测定水滴或汽车用机油滴的接触角。
对不具有层次结构的参考例1和3的铝板测定静态接触角,对具有层次结构的参考例2和4的铝板测定作为动态接触角的前进接触角和接触角滞后。
(结果)
将参考例1~4的构成和评价结果示于表1和图1a~图c。需要说明的是,在表中,接触角栏的括号()的内部表示接触角滞后。
表1
图1a为参考例1的铝板的扫描型显微镜(sem)图像。如图1a所示,通过阳极氧化在参考例1的铝板表面上形成有多孔的al2o3覆膜。另外,如图1b所示,在参考例2的铝板表面上形成有由蚀刻形成的微米级的坑和由多孔的al2o3覆膜形成的层次结构。
如表1和图1c所示,未形成自组装有机单分子膜(sam)的参考例1和参考例2的铝板相对于水滴的接触角分别为4.6±1.2和~0,为超亲水性。与此相对,形成有自组装有机单分子膜(sam)的参考例3和参考例4的铝板相对于水滴的接触角分别为129.1±0.8和161.7±1.0,具有高斥水性。
另外,在具有层次结构并且在表面形成有自组装有机单分子膜(sam)的参考例4的铝板中,接触角显示出158.2±1.5的大值,相对于汽车用机油滴具有高斥液性,与此相对,在参考例1~3中,接触角为90°以下,具有低斥液性。
这显示出,至少关于参考例1~3的铝板,能够将汽车用机油形成为油膜。
《实施例1和2以及比较例5~7》
以如下的方式制作实施例1和2以及比较例5~7的铝板,评价其性能。
<实施例1和2以及比较例5和6>
量取100μl汽车用机油,涂布在参考例1~4的铝板各自的表面上,静置10分钟以上,由此得到实施例1和2以及比较例5和6的铝板。
需要说明的是,如在上述关于参考例4的汽车用机油的斥液性的评价中所示,由于在具有层次结构并且实施了sam涂布的参考例4的铝板表面上,汽车用机油没有充分地润湿扩展,因此预先在机油中浸渍48小时而使斥油性劣化,然后涂布汽车用机油。
<比较例7>
在利用蚀刻的层次结构化、利用阳极氧化的多孔化以及sam涂布均未实施的铝板上与实施例1同样地涂布汽车用机油,除此以外,得到比较例7的铝板。
<在对汽车用机油施加剪切力的环境下slips的稳定性的评价>
(评价方法)
对实施例1和2以及比较例5的铝板评价在对汽车用机油施加剪切力的环境下汽车用机油的保持性和液体滑落特性。其目的在于模拟在因重力、风等而丧失润滑油的环境下slips的劣化。
作为评价方法,首先,对实施例1和2以及比较例5的铝板分别使用旋涂机,在转速为500rpm~7000rpm、旋转时间为10秒~300秒的条件下旋转。然后,测定残留的汽车用机油的重量和10μl的水滴的滚落角。
(结果)
将测定结果示于图2a~图c。需要说明的是,图2a为表示实施例1和2以及比较例5的铝板各自的铝板转速与汽车用机油的残留量的关系(旋转时间:60秒)的图,图2b为表示实施例1和2以及比较例5铝板各自的铝板转速与10μl的水滴的滚落角的关系(旋转时间:60秒)的图,并且图2c为表示实施例1和2以及比较例5的铝板各自的汽车用机油的残留量与10μl的水滴的滚落角的关系(旋转时间:10、60、300秒)的图。
如图2a所示,在任一铝板中,当转速增加而对汽车用机油施加的离心力增大时,汽车用机油的残留量相应地减少。
该残留量在具有层次结构的实施例2的铝板中特别多。认为这是由于具有层次结构的铝板具有微米级的凹凸,在所述凹凸中保持了汽车用机油。
另外,在将不具有层次结构的实施例1和比较例5的铝板进行比较时,汽车用机油的残留量没有大的差别。
如图2b所示确认到,关于水滴滚落角,即使在不具有层次结构并且未实施sam涂布的实施例1的铝板中,通过在多孔表面上涂布汽车用机油,所附着的水滴以一定滚落角滑落。认为,由于实施例1的铝板自身的表面如图1c所示的那样显示出亲水性,因此不能单独成为slips。
在将实施例1和2以及比较例5铝板进行比较时,水滴滚落角随着转速增加而增大、即斥水性逐渐降低,最容易降低的是具有层次结构并且未实施sam涂布的实施例2的铝板,相反,保持最小的水滴滚落角、即保持斥水性的是不具有层次结构并且未实施sam涂布的实施例1的铝板。
作为在实施例2的铝板中水滴滚落角特别容易增大的理由,认为原本平滑的润滑油膜随着润滑油的丧失而反映出粗糙表面的粗糙度,润滑油膜表面粗糙化而与水滴的接触面积增大。
即使观察汽车用机油的残留量与10μl的水滴的滚落角的关系,在润滑油的残留量相同的情况下,显示出最小的水滴滚落角(良好的斥水性)的是不具有层次结构并且未实施sam涂布的实施例1的铝板。
由此,如图2c所示,如实施例1和2那样在未实施sam涂布的铝板上直接涂布汽车用机油而形成的表面与如比较例5那样在铝板上实施sam涂布而形成的表面同样地,不仅能够使水滴容易地滑落,而且显示出在对润滑油施加剪切力的环境下也保持最高的稳定性。
<水中的slips的稳定性的评价>
(评价方法)
将乙酸和10g/l的nacl水溶液(ph=3)以1000rpm搅拌,制备混合液。将实施例1和2、比较例3和7的铝板分别浸渍在该混合液中,经过预定的时间,然后取出。然后,测定各例的铝板上的10μl水滴的滚落角。需要说明的是,各例的铝板上的汽车用机油的涂布量为3.75μl/cm2。
(结果)
图3为表示实施例1和2、比较例5和7的铝板在混合液中的浸渍时间与10μl的水滴的滚落角的关系的图。
如图3所示,水滴滚落角无论在哪个例子中均在数日以内超过了作为测定界限的20°,但最长时间保持小的水滴滚落角(即保持高斥水性)的是未实施sam涂布的实施例1的铝板。另一方面,在具有层次结构并且未实施sam涂布的实施例2的铝板中,水滴滚落角最容易增大(即斥水性降低),与在比较例7的铝板、即既没有层次结构化也没有多孔化的平滑的铝板上涂布汽车用机油的情况相比,在短时间内超过20°。
由此可以说,在未实施sam涂布的铝板上直接涂布汽车用机油而形成slips的情况下,不进行层次结构化的方式能够得到更高的水中稳定性。
<耐腐蚀试验>
对于实施例1和2以及比较例1~6的铝板,以如下的方式评价耐腐蚀性。
(试验方法)
将各例的铝板在上述混合液中浸渍5天,然后观察基板的重量变化和表面形态的变化等。
(结果)
将结果示于表1以及图4、图5a~e和图6a~e中。
[表2]
表2
在表1中,“〇”表示耐腐蚀性良好,“×”表示没有耐腐蚀性。
图4为表示实施例1和2以及比较例1~6的铝板在耐腐蚀试验后的重量变化的图。
如图4所示,在未涂布汽车用机油的比较例1、比较例2、比较例3和比较例4的铝板中,重量均减少约0.5mg/cm2~约1.5mg/cm2。这是由腐蚀引起的铝的溶解导致的。
另一方面,在涂布有汽车用机油的实施例1和实施例2以及比较例5和6的铝板中,重量变化均为0.1mg/cm2以下,能够抑制由腐蚀引起的重量减少。需要说明的是,在实施例2、比较例5和比较例6的铝板中,在耐腐蚀试验后重量稍微增加。这是因为,即使在腐蚀试验后用丙酮等有机溶剂洗涤这些铝板,也会残留少量的白色产物。需要说明的是,认为该白色产物是作为汽车用机油的添加剂而含有的中和剂与混合溶液的反应产物。
这些结果显示,通过在进行了多孔化的铝板上涂布汽车用机油,能够得到与在多孔化的铝板上实施sam涂布的情况同等的耐腐蚀性。
通过扫描型显微镜观察实施例1、实施例2、比较例5和比较例6的铝板在耐腐蚀试验后的表面状态。
图5a为未进行层次结构化而进行了阳极氧化的铝板表面在耐腐蚀试验前的扫描型显微镜(sem)图像,图5b~图5e依次分别为比较例5、比较例3、实施例1、比较例1的铝板表面在耐腐蚀试验后的扫描型显微镜(sem)图像。
参照图5a、图5b和图5d,将进行了多孔化并且在表面上涂布有汽车用机油的比较例5和实施例1的铝板进行比较,则不论有无sam涂布,在耐腐蚀试验后也残留有与试验前同样的多孔膜,可以说保持了孔结构。
与此相对,如图5c所示,在仅进行sam涂布而未在表面上涂布汽车用机油的比较例3中,阳极氧化表面溶解,孔结构消失。另外,在未实施sam涂布并且也未涂布汽车用机油的比较例1中,不仅阳极氧化表面、连作为基底的铝板也大幅溶解。
另外,图6a为进行了层次结构化并且进行了阳极氧化的铝板表面在耐腐蚀试验前的扫描型显微镜(sem)图像,图6b~图6e依次分别为比较例6、比较例4、实施例2、比较例2的铝板表面在耐腐蚀试验后的扫描型显微镜(sem)图像。
参照图6a、图6b和图6d,将具有层次结构、进行了多孔化并且在表面上涂布有汽车用机油的比较例6和实施例2的铝板进行比较,则不论有无sam涂布,在耐腐蚀试验后也残留有与试验前同样的多孔膜,可以说保持了孔结构。
与此相对,如图6c所示,在仅进行sam涂布而未在表面上涂布汽车用机油的比较例4中,阳极氧化表面溶解,孔结构消失。另外,在未实施sam涂布并且也未涂布汽车用机油的比较例2中,不仅阳极氧化表面、连作为基底的铝板也大幅溶解。
由这些结果可以说,在具有层次结构的情况和不具有层次结构的情况这两个情况下,通过在进行了多孔化的铝板表面上直接涂布汽车用机油,能够得到与在进行了多孔化的铝板表面上实施sam涂布的情况同等的耐腐蚀性。
《参考例5和参考例6》
为了查明通过在进行了多孔化的铝板表面上直接涂布汽车用机油而得到与在进行了多孔化的铝板表面上实施sam涂布的情况同等的耐腐蚀性的理由,在涂布汽车用机油后,用有机溶剂洗涤,然后进行静态接触角测定和利用x射线光电子能谱法(xps)的表面分析。
<参考例5>
如图7所示,在具有多孔表面的铝板上涂布汽车用机油(12.5μl/cm2),静置24小时。然后,在庚烷中将该铝板进行超声波洗涤,使其干燥,由此得到参考例5的铝板。
<参考例6>
除了不涂布汽车用机油以外,与参考例5同样地操作而得到参考例6的铝板。
<铝板的表面状态的评价>
(评价方法等)
用扫描型显微镜(sem)观察参考例5和参考例6的铝板的表面状态。另外,在这些铝板上放置10μl的水滴,测定其接触角。另外,对于参考例5的铝板,利用x射线光电子能谱法(xps)将汽车用机油浸渍、洗涤后的表面进行分析。
(结果)
图8a和8b分别为表示参考例5和参考例6的铝板的表面状态和放置有10μl水滴时的接触角的图。
如图8a所示,在参考例5中,即使在汽车用机油浸渍后,也清楚地观察到多孔表面的纳米孔,因此可知汽车用机油通过洗涤而被除去,孔径也看不出变化。
但是,如图8b所示明确了,未涂布机油的参考例6中的水滴接触角为20°以下,为亲水性表面,与此相对,如图8a所示,在参考例5中,在机油浸渍、洗涤后接触角成为110°以上,斥水性表面变化。
推测这可能是汽车用机油中的添加物化学吸附至表面而引起表面改性。
图9a~图9c为表示参考例5的铝板在利用汽车用机油浸渍、洗涤后的表面的x射线光电子能谱法(xps)分析结果的图。
在汽车用机油浸渍、洗涤后残留有在汽车用机油浸渍前不存在的zn。从图9b所示的s2p光谱中,在171ev附近可以看到源自硫酸中的阳极氧化的硫酸根离子的峰,此外,被认为源自作为添加剂的二烷基二硫代磷酸锌(zndtp)的164ev的峰也在机油浸渍、洗涤后出现。
由以上结果可知,汽车用机油中的二烷基二硫代磷酸锌(zndtp)吸附至参考例5的铝板表面而进行表面改性,由此表面自由能降低,即使没有sam也成为稳定的slips状态,导致了耐腐蚀性的大幅改善。
《实施例3~5以及比较例8~10》
以如下的方式制作实施例3~5以及比较例8~10的铝板,评价其耐腐蚀性。
<实施例3>
与参考例1同样地操作,制作具有多孔的阳极氧化表面的铝板。通过在该铝板上涂布在基础油中添加二烷基二硫代磷酸锌(zndtp)而得的油,制作了实施例3的铝板。需要说明的是,油中的二烷基二硫代磷酸锌(zndtp)的量相对于油整体为2质量%。
<实施例4和5>
除了使油中的二烷基二硫代磷酸锌(zndtp)的量分别为10质量%和20质量%以外,与实施例3同样地操作而制作了实施例4和5的铝板。
<比较例8>
与参考例1同样地操作,制作具有多孔的阳极氧化表面的铝板。通过在该铝板上涂布基础油,制作了比较例8的铝板。
<比较例9>
除了使用在基础油中添加了磺酸钙代替二烷基二硫代磷酸锌(zndtp)而得的油以外,与实施例3同样地操作而制作比较例9的铝板。需要说明的是,油中磺酸钙的量相对于油整体为1质量%。
<比较例10>
除了将油中磺酸钙的量设为10质量%以外,与比较例9同样地操作而制作比较例10的铝板。
<耐腐蚀性的评价>
(评价方法)
对于实施例3~5以及比较例8~10的铝板,通过电化学测定评价其耐腐蚀性。作为腐蚀液,使用将乙酸和10g/l的nacl水溶液以1000rpm搅拌而制备的混合液(ph=3)。
(结果)
图10为表示实施例3~5以及比较例8的铝板的电化学测定结果的图。
如图10所示,在涂布了未添加二烷基二硫代磷酸锌(zndtp)的基础油的比较例8的铝板中,阳极电流密度大,得不到充分的腐蚀抑制效果。与此相对,在涂布了在基础油中添加二烷基二硫代磷酸锌(zndtp)而得的油的实施例3~5的铝板中,电流密度与比较例8的铝板相比降低了4位数以上,即表现出优异的耐腐蚀性。
另外,图11为表示实施例3以及比较例8~10的铝板的电化学测定结果的图。
如图11所示,在涂布了基础油的比较例8以及添加了磺酸钙代替二烷基二硫代磷酸锌(zndtp)的比较例9和10的铝板中,阳极电流密度大,得不到充分的腐蚀抑制效果。
本文用于企业家、创业者技术爱好者查询,结果仅供参考。