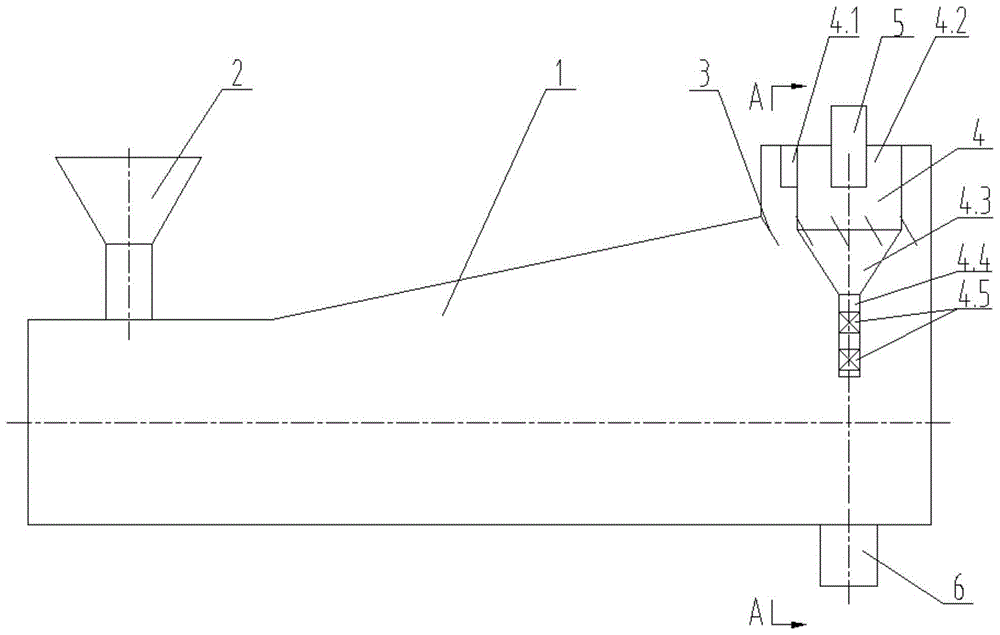
本发明属于垃圾热解技术领域,具体涉及一种降低油气含尘量的高温热解反应器。
背景技术:
在对垃圾进行热解处理时,所产热解气中含尘量较高,且含尘热解气具有温度高(>500℃)、易相变、易粘结、粘附性强等特性,在热解气净化系统中,极易造成管道堵塞和急冷设备失效,系统被迫紧急停车;又或者粘附在换热管壁上,造成换热效率降低,影响系统热效率;同时热解气经急冷后产生的含尘焦油也极难处理,造成热解油流动性差,降低热解油品质,并增加油的处理难度。目前,热解气除尘是热解装置中,影响系统稳定、连续运行的一大难点。
基于此,国内关于热解气除尘开发了很多技术,多采用在热解反应器后增设多级除尘或与多种除尘设备组合模式,以降低热解气含尘量。但多级或组合配置模式,都会导致系统的复杂性,增大系统阻力、增加系统控制、投资成本;并增加热解气管程长度,增大管道中冷凝、堵塞风险。
由此,本发明开发出一种降低油气含尘量的高温热解反应器,目的是降低热解气出口含尘量,简化热解气后续除尘处理系统。
技术实现要素:
本发明的目的在于提供一种降低油气含尘量的高温热解反应器,利用热解反应器自身结构,在热解反应器内部对热解气进行气相干式除尘,以降低热解气出口含尘量,简化热解气后续除尘工艺配置,且降低热解油处理难度。
为达到上述目的,本发明所采取的技术方案为:
一种降低油气含尘量的高温热解反应器,包括热解反应器壳体、反应器物料入口、百叶挡板、旋流装置、热解气出口和热解固体产物出口;热解反应器壳体采用前小后大的阶梯结构,前端设置反应器物料入口,尾部设置热解固体产物出口;反应器壳体中后部为壳体放大段,放大段上部凸起空腔作为热解气出口区域,此区域气相入口处设置百叶挡板,内部设置旋流装置,气相出口处设置热解气出口,热解气出口即为旋流装置出口,旋流装置和热解气出口位置置于热解固体产物出口上方。
所述的旋流装置采用旋风分离器型式:在热解反应器壳体内部热解气出口区域,设置水平进口段,水平进口段与旋流筒体连接,旋流筒体下部与锥段连接,锥段下部与排灰料腿连接;排灰料腿底部根据捕集粉尘量多少,可采用单料腿型式,或连接双锁气重力排灰阀;双锁气重力排灰阀对应热解固体产物出口。
所述的旋风分离器型式的排灰料腿上设置惰性气体孔,运行时通入微量惰性气体,利用气固流化原理,以保证此处粉尘顺畅下落。
所述的旋流装置采用旋流叶片,位于热解气出口内部。
所述的旋流叶片可采用螺旋结构,也可以采用沿圆周交错单片型式。
所述的旋流叶片沿气流流动方向翘起一定角度,角度范围为0~60°。
所述的旋流叶片端部加防磨套板,套板可拆卸。
所述的旋流叶片螺距为0~2d,叶片宽度为0.2d~0.8d,d为热解气出口内径。
所述的百叶挡板设置2~3圈或更多,采用上下交错布置型式,百叶间距离使气体流速控制在20m/s左右。
所述的热解气出口筒体下部采用扩口结构。
本发明所取得的有益效果为:
1)本发明热解反应器具备降低油气出口含尘量功能,通过在壳体1上设置阶梯放大结构,避免气体流动过程中对灰尘的二次夹带;且此结构利用了粉尘重力沉降原理,使50μm以上颗粒在反应器内自动沉降。
2)本发明热解反应器在中后端设置凸起空腔作为热解气出口区域,在此区域设置百叶挡板3,旋流装置4,使热解气出口含尘粒径降低至10μm以下,使热解反应器排出的热解气产生的热解焦油具有流动性,可直接泵入燃烧器燃烧,简化热解油后处理难度。
3)本发明热解反应器根据捕集粉尘流动性差特性,提出在排灰料腿4.4中设置惰性气体孔,运行时通入微量惰性气体,利用气固流化原理,保证粉尘下落顺畅;且针对捕集粉尘量少时工况,在料腿4.4上设置双锁气重力排灰阀4.5,此结构有效防止串气,既对料腿起到密封作用,又可保证除尘效率。
附图说明
图1为热解反应器除尘装置主视图;
图2为热解反应器除尘装置a-a视图;
图3为热解反应器除尘装置俯视图;
图4为旋流装置局部图;
图5为旋流叶片俯视放大图;
图中:1热解反应器壳体;2反应器物料入口;3百叶挡板;4旋流装置;4.1水平进口段;4.2旋流筒体;4.3锥段;4.4排灰料腿;4.5双锁气重力排灰阀;5热解气出口;4.6旋流叶片;6热解固体产物出口。
具体实施方式
下面结合附图和具体实施例对本发明进行详细说明。
本发明提供一种降低油气含尘量的高温热解反应器,主要通过热解反应器自身结构,对热解气进行气相干式除尘,使其具备自除尘功能,以降低热解气出口含尘量,简化热解气后续除尘工艺系统,降低热解油处理难度。
如图1-5所示,本发明所述一种降低油气含尘量的高温热解反应器,包括热解反应器壳体1,反应器物料入口2,百叶挡板3,旋流装置4,热解气出口5,热解固体产物出口6。其中,旋流装置4分两种结构,一种采用旋风分离器型式,水平进口段4.1、旋流筒体4.2、锥段4.3、排灰料腿4.4、双锁气重力排灰阀4.5;另一种采用旋流叶片型式,旋流叶片4.6。
所述热解反应器壳体1采用前小后大阶梯结构,中后部为壳体放大段。根据热解反应进程及产气量,通过逐级增大气相流通面积,使热解气在反应器内流速始终<1m/s,以此降低气体流动过程中对灰尘的二次夹带;同时,通过壳体放大结构,利用粉尘重力沉降原理,使50μm以上颗粒在热解反应器内自动沉降。
所述热解反应器壳体1前端设置反应器物料入口2,尾部设置热解固体产物出口6。
所述反应器壳体1放大段中后端上部设置凸起空腔作为热解气出口区域,此区域内部设置旋流装置4,出口处设置热解气出口5,热解气出口5即为旋流装置4出口,旋流装置4和热解气出口5位置置于热解固体产物出口6上方。此方位设置方式可以使被捕集的粉尘直接随热解固体产物经出口6排出,以防出现部分粉尘重新落入热解反应器内后,再次进入热解气中,导致除尘效率降低。
所述热解反应器壳体1放大段中后端上部热解气出口区域,入口处设置百叶挡板3,百叶挡板设置2~3圈或更多,采用上下交错布置型式。此结构实现局部热解气流向改变,且增大气流速度至20m/s左右,利用粉尘粒子沿原气流方向前进的惯性,通过百叶挡板3捕集20μm以上粒径的粉尘。
所述百叶挡板3,可以使用平板、角钢或u型槽钢,根据热解反应器内温度,材质选择奥氏体不锈钢。
所述热解反应器壳体1中热解气出口区域中设置旋流装置4,进一步降低热解气出口含尘量。旋流装置4可采用旋风分离器结构,也可以采用旋流叶片4.6。所述旋风分离器结构,在热解反应器壳体1内部热解气出口区域,设置水平进口段4.1,水平进口段4.1与旋流筒体4.2水平连接,旋流筒体4.2下部与锥段4.3连接,锥段4.3下部与排灰料腿4.4连接。其中,锥段4.3顶角角度,考虑粉尘安息角较小、易结块、流动性差特性,角度小于安息角(<30℃),保证捕集粉尘顺利流入排灰料腿4.4;排灰料腿4.4上设置惰性气体孔,运行时通入微量惰性气体,利用气固流化原理,以保证此处粉尘顺畅下落。
水平进口段4.1引导气流进入旋风分离器入口并加速,在旋流筒体4.2中高速旋转,利用离心力将微细颗粒分离,通过锥段4.3进入排灰料腿4.4,排灰料腿4.4底部根据捕集粉尘量多少,可采用单料腿型式,或采用连接双锁气重力排灰阀4.5型式。当灰尘量较多可在料腿中形成料封时,采用单料腿型式;但若气体中含粉尘相对少,捕集粉尘在料腿中无法形成料封时,以防料腿串气进入旋流筒体4.2,造成分离效率大幅下降,采取在排灰料腿4.4上设置双锁气重力排灰阀4.5方案。当粉尘达到一定重量时,阀门上、下交错打开,此结构既可自动卸料,又可在卸料的同时对料腿起到密封作用。
双锁气重力排灰阀4.5对应热解固体产物出口6,使从热解气中收集的粉尘随热解后固体产物一起进入下游设备,以防再次落入反应器内,产生二次扬尘,导致除尘效率降低。此除尘方案可使热解气出口含尘粒径降低至10μm以下。经此除尘后,从热解反应器排出的热解气经急冷净化后,产生的热解焦油具有流动性(垃圾产热解焦油不含尘时有一定流动性),可直接泵入燃油燃烧器燃烧。
所述热解气流程中要求在热解反应器内部阻力消耗小,或反应器总高度受限制时,在反应器壳体1尾部,热解气出口5内部增设旋流叶片4.6,叶片可采用螺旋结构,也可以是交错单片型式,为防止磨损,叶片沿气流流动方向翘起一定角度,角度范围为0~60°,叶片端部加防磨套板,所述套板可拆卸。叶片采用螺旋结构时,螺距一般为0~2d(d为热解气出口内径),叶片宽度0.2d~0.8d,叶片布置高度与热解气出口5筒体总高度配合,叶片分层布置,使气流在出口筒体内呈s型绕行,将气体中粉尘通过惯性力去除。
所述热解气出口5筒体下部采用扩口结构,此结构可降低下落粉尘被气流二次夹带的几率。
本文用于企业家、创业者技术爱好者查询,结果仅供参考。