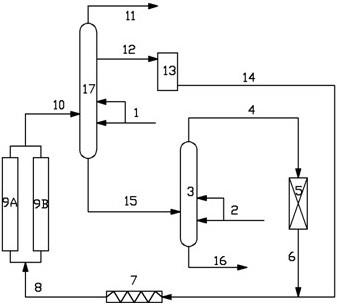
1.本发明属于石油焦制备技术领域,特别是涉及一种低硫石油焦的生产方法和生产系统。
背景技术:
2.近年来,随着石墨电极和锂离子电池等行业的发展,硫含量低于0.5wt%的低硫石油焦备受关注。石油焦主要来源于炼油企业延迟焦化装置,而延迟焦化装置加工的原料通常为减压渣油、脱油沥青、焦油等劣质油品,硫含量普遍较高,很难得到低硫石油焦。cn 102153070a、cn1349955a公开了以石油焦为原料,直接对其进行脱硫的方法;cn108998060a、cn1468939a公开了制备低硫石油焦的方法,通常是在反应阶段,向渣油原料中添加氧化剂或者驱硫剂,从而达到脱硫的目的。
3.催化油浆裂化性能相对较差,其含有的大量稠环芳烃经过热反应更容易缩聚形成焦炭,是生产针状焦的优质原料,而针状焦是低硫石油焦的一种。cn103789028a公开了一种催化油浆生产针状焦原料的方法,催化油浆分别经过吸附脱固、加氢脱硫后得到合格的针状焦原料。但是,并非所有的催化油浆都适合作为生产针状焦的原料。由于针状焦对于催化油浆的性质要求较为苛刻,如芳烃含量、沥青质含量、密度、馏程分布等,而且针状焦生产工艺复杂,因此针状焦产量低,通常用来生产高端石墨电极。一般情况下,低端电极和锂离子负极材料等都以普通低硫石油焦为原材料。
技术实现要素:
4.针对现有技术的不足,本发明目的是提供一种低硫石油焦的生产方法和系统,所述生产方法可以在得到低硫石油焦产品的同时,尽可能提高原料转化率和焦炭收率,减少馏分油产出。
5.本发明第一方面提供一种低硫石油焦的生产方法,所述生产方法包括如下内容:(1)催化油浆与焦化反应流出物在焦化分馏塔内接触,分离后得到气体、轻馏分和重馏分;(2)步骤(1)得到的轻馏分进入聚合反应器进行聚合反应,得到聚合物不凝气;(3)步骤(1)得到的重馏分进行脱固处理,处理后得到净化油和尾油;(4)步骤(2)分离后得到的净化油与氢气混合后进入加氢处理系统,在催化剂作用下进行加氢处理,加氢反应流出物经分离后得到气体、石脑油和精制油;(5)步骤(2)得到的聚合物和步骤(4)得到的精制油混合并经加热后进入延迟焦化装置进行反应,反应流出物进入焦化分馏塔与催化油浆接触进行处理。
6.上述低硫石油焦的生产方法中,步骤(1)中所述轻馏分95%馏出温度为250℃~380℃,优选270℃~330℃。所述的气体主要成分为干气、c3~c4烃类。所述的重馏分包括焦化蜡油和催化油浆。
7.上述低硫石油焦的生产方法中,步骤(2)中所述聚合反应条件为:反应温度为380
℃~550℃,优选400℃~450℃,反应压力为0.01 mpa~10 mpa,优选1mpa~4mpa,停留时间为0.1h~20h,优选2h~5h。所述聚合反应器可以采用固定床反应器,反应器内部装填有催化剂,所述催化剂包括载体和活性组分,以高岭土、蒙脱土、氧化铝、含硅氧化铝中的一种或几种为载体,活性组分为第ivb族和/或第vib族金属的氧化物中的一种或几种组合,如zr、w、mo中的一种或几种。所述的催化剂金属含量为0.1wt%~40wt%,优选3wt%~25wt%。所述的催化剂形状可以是球形、圆柱、三叶草、四叶草、拉西环等中的一种或者几种。
8.上述低硫石油焦的生产方法中,步骤(3)中所述脱固处理可以是过滤分离、离心沉降、减压蒸馏处理等方式中的任一种或几种,优选采用减压蒸馏处理;进一步优选采用减压蒸馏进行脱固处理时,掺入减压渣油与重馏分一起进行脱固处理,所述的减压渣油5%馏出温度为480~550℃,优选500~540℃;催化油浆与减压渣油质量比为0.1:1~10:1,优选2:1~5:1。
9.上述低硫石油焦的生产方法中,步骤(3)中所述净化油95%馏出温度为470℃~540℃,优选470℃~520℃。所述净化油的固含量<0.01wt%。
10.上述低硫石油焦的生产方法中,步骤(4)中所述加氢处理系统设置一个以上的加氢反应器,所述加氢反应器可以为固定床反应器、沸腾床反应器、悬浮床反应器中的一种或几种;优选为固定床反应器。所述加氢反应器中装填加氢催化剂,所述加氢催化剂包括载体和活性组分,其中载体为氧化铝或含硅氧化铝,活性组分为第
ⅵ
b族和/或第
ⅷ
族金属的氧化物,具体可以为mo、w、co和ni中的一种或几种。也可以采用本领域现有重油加氢处理催化剂,如中国石化催化剂分公司生产的fzc系列加氢处理催化剂。加氢处理催化剂可以采用单一催化剂或者多种催化剂配套使用。
11.上述低硫石油焦的生产方法中,步骤(4)中所述的加氢处理系统的操作条件:反应温度为300℃~480℃,优选为330℃~420℃,反应压力为3mpa~20mpa,优选为5mpa~10mpa,氢油体积比为100~2700,优选为500~1500,其中氢油体积比为氢气与拔出油体积比,液时体积空速为0.1h-1
~2.0h-1
,优选0.3h-1
~1.0h-1
。
12.上述低硫石油焦的生产方法中,步骤(5)中所述的延迟焦化装置包含至少一个加热炉、一个分馏系统和两个焦炭塔,始终保持至少一个焦炭塔处于反应阶段,至少一个焦炭塔处于除焦阶段。所述的加热炉出口温度为470℃~550℃,优选490℃~505℃;焦炭塔塔顶压力为0.01mpa~2.5mpa,优选0.5mpa~1.0mpa,可以恒压操作或者变压操作,当采用变压操作时,压力变化速率为0.01mpa/h~50mpa/h,优选0.2mpa/h~5mpa/h;反应周期为10h~35h,优选18h~26h。
13.本发明第二方面提供一种低硫石油焦生产系统,所述生产系统包括:焦化分馏塔:其用于接收催化油浆和来自延迟焦化装置的反应产物,处理后得到气体、轻馏分、重馏分;聚合反应器,其用于接收来自焦化分馏塔的轻馏分,处理后得到聚合物和不凝气;脱固单元:其用于接收来自焦化分馏塔的重馏分,处理后得到净化油和尾油;加氢处理系统:其用于接收氢气和来自脱固单元的净化油,处理后得到气体、石脑油和精制油;延迟焦化反应单元:其用于接收来自聚合反应器的聚合物和来自加氢处理系统的精制油,反应流出物经管线进入焦化分馏塔。
14.上述低硫石油焦的生产系统中,所述加氢处理系统设置一个以上的加氢反应器,所述加氢反应器可以为固定床反应器、沸腾床反应器、悬浮床反应器中的一种或几种;优选为固定床反应器。
15.上述低硫石油焦的生产系统中,所述的延迟焦化反应单元包含至少一个加热炉和两个焦炭塔,始终保持至少一个焦炭塔处于反应阶段,至少一个焦炭塔处于除焦阶段。
16.上述低硫石油焦的生产系统中,所述的脱固单元可以采用的设备包括过滤器、离心沉降器、减压蒸馏塔中的任一种或几种,优选采用减压蒸馏塔。
17.上述低硫石油焦的生产系统中,所述的聚合反应器可以采用固定床反应器。
18.与现有技术相比,本发明提供的低硫石油焦生产方法和系统具有以下优点:1、现有的催化油浆生产低硫石油焦或者针状焦的方法,是原料先经过脱固、加氢脱硫,然后进入焦化分馏塔与焦化反应生成物接触,携带焦化蜡油后进入延迟焦化装置生产焦。本发明方法中,催化油浆首先直接进入焦化分馏塔与焦化反应生成物接触,携带焦化蜡油后再经过脱固、加氢脱硫处理,将催化油浆和焦化蜡油混合油的硫降至一定值后,再进行延迟焦化反应。重质油浅度加氢,原料中硫含量会降低,但是当加氢至一定深度时,虽然原料中硫含量进一步降低,但是同时会伴有芳烃饱和等反应,会导致焦炭收率降低,因此原料脱硫和焦炭产率是相互有冲突的,需要找到一个合理的方案既能是原料中的硫满足要求,又能保证目的产品焦炭收率较高。本发明方法中,通过将焦化蜡油加氢脱硫对降低焦炭硫含量做出较大贡献,大大缓解了催化油浆原料的脱硫压力,即催化油浆和焦化蜡油可以在相对缓和的加氢条件下脱硫,降低芳烃开环率,从而提高低硫石油焦的收率。
19.2、催化油浆延迟焦化反应生成的轻馏分油中硫含量相对较少,但是芳烃含量高、稳定性差,后处理困难。本发明方法中将轻馏分油经过聚合反应重质化后再次作为焦化进料,不仅解决富芳焦化生成油加工困难的问题,还有利于提高低硫石油焦的收率。
20.3、催化油浆中的催化剂粉末直接影响石油焦的灰分含量,而焦化油气携带的焦粉不利于加氢处理装置正常运行。将催化油浆和焦化蜡油馏分的混合物送至减压蒸馏装置与减压渣油接触,减压渣油携带大部分催化剂粉末和焦粉从塔底外甩,可以作为常规延迟焦化进料,而塔顶排出净化油的固含量会降到很低。
21.4、本发明提供的低硫石油焦方法,在获得高收率低硫石油焦的同时,还可以副产气体(干气和液化气)和少量石脑油,大大提高了催化油浆的利用率。
附图说明
22.图1为本发明所述低硫石油焦生产方法和系统示意图。
具体实施方式
23.下面结合实施例进一步说明本发明方法的过程及效果,但以下实施例不构成对本发明方法的限制。
24.如图1所示,本发明所述低硫石油焦生产方法包括如下内容:催化油浆1与焦化反应流出物10在焦化分馏塔17内接触,分离出气体11、轻馏分12和重馏分15。其中,重馏分15送至减压蒸馏系统3与减压渣油2接触,分离后得到净化油4和尾油16;尾油16外甩,净化油4与氢气混合后送至加氢处理系统5,得到的加氢精制油6经过加热炉7加热至一定温度后经
由管线8进入延迟焦化塔9a/b,焦化反应流出物10从塔顶排出。焦化分馏塔17分离出的轻馏分12送至聚合反应器13,生成的聚合物14也经过加热炉7加热至一定温度后经由管线8进入延迟焦化塔9a/b。
25.本发明所述实施例、对比例中所用的催化油浆和减压渣油性质见表1。
26.实施例1实施例1采用本发明方法,催化油浆与焦化反应流出物在分馏塔内接触,分离出气体、轻馏分和重馏分,其中轻馏分的95%馏出温度为310℃。重馏分与减压渣油以质量比3:1在减压蒸馏塔塔低接触,分离出净化油和尾油,其中净化油的95%馏出温度为502℃。净化油与氢气混合油送至加氢处理系统,得到的精制油送至延迟焦化反应系统,延迟焦化反应采用恒温、恒压操作工艺,具体反应条件见表2。焦化分馏塔分离出的轻组分送至聚合反应器,生成的聚合物也送至延迟焦化反应系统,具体反应条件也见表2。产品分布和焦炭硫含量分析结果见表3。
27.实施例2实施例2采用本发明方法,与实施例1不同之处在于延迟焦化反应条件采用恒温、变压操作工艺,当进料时间达到反应周期60%时,焦炭塔压力以0.8mpa/h的速率泄压。具体反应条件见表2。产品分布和焦炭硫含量分析结果见表3。
28.对比例1对比例1中,采用现有技术处理催化油浆生产低硫石油焦,即焦化蜡油不经过加氢处理直接循环回延迟焦化装置,焦化轻馏分外排。催化油浆与减压渣油以质量比3:1在减压蒸馏塔塔低接触,分离出净化油和尾油,其中净化油的95%馏出温度为502℃。净化油与氢气混合油送至加氢处理系统,得到的精制油送至焦化分馏塔与焦化反应流出物接触,分离出气体和轻馏分外排,蜡油随着精制油一起进入延迟焦化反应系统。焦化反应流出物送至分馏塔分离出气体、轻馏分和重馏分,其中轻馏分的95%馏出温度为313℃。具体反应条件见表2。产品分布和焦炭硫含量分析结果见表3。
29.对比例2对比例2与对比例1的操作流程相同,不同之处在于焦化蜡油并非全循环,而是部分循环,控制延迟焦化装置循环比为0.5,具体反应条件的设置,见表2。产品分布和焦炭硫含量分析结果见表3。
30.对比例3对比例3与对比例1操作条件基本相同,不同之处在于加氢精制油不进入分馏塔与焦化反应流出物接触,而是直接送至延迟焦化装置,即焦化蜡油不循环回延迟焦化装置,而是作为产品输出,具体反应条件见表2。产品分布和焦炭硫含量分析结果见表3。
31.表1 催化油浆和减压渣油性质
表2 加氢反应和延迟焦化反应条件 表3 以精制油计产品分布和焦炭硫含量
从表3中数据分析后可以看出,实施例1和实施例2焦炭收率分别为78.7wt%和74.2wt%,焦炭硫含量均低于0.5%,符合低硫石油焦对硫含量的要求。对比例1焦炭硫含量高于0.5%,不符合要求。对比例2和对比例3焦炭硫含量符合要求,但是焦炭收率偏低,经济型较差,不具有工业推广价值。
再多了解一些
本文用于企业家、创业者技术爱好者查询,结果仅供参考。