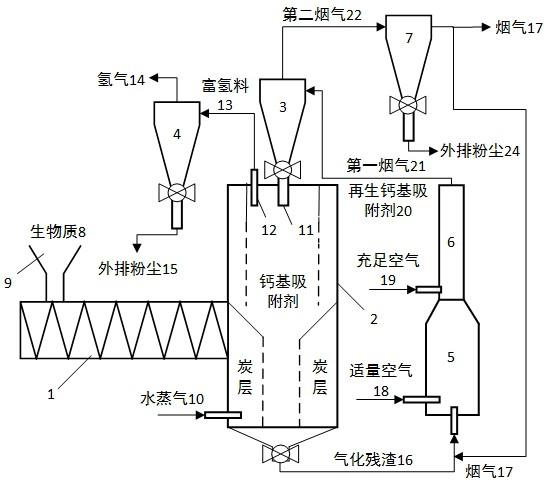
1.本发明属于生物质利用技术领域,涉及一种生物质热转化制氢方法及系统。
背景技术:
2.氢气是一种重要的清洁能源,被公认为是最有希望部分替代传统化石燃料的能源载体。2017年全球氢气市场规模约为1292.5亿美元,国际氢能理事会预计,到2050年,氢的年需求量可能增加10倍。目前96%氢气来源于天然气和煤,加剧能源危机和环境污染,利用生物质制取氢气整体费用约为25元/公斤,高于甲烷制氢的13-18元/公斤,但低于电解水制氢的40元/公斤,具有很强的市场竞争力。目前国外生物质制氢技术已从中试进入商业化阶段,较为成熟的串行鼓泡流化床和循环流化床技术上可获得氢气浓度40-60%,产率60-80g/kg生物质,相比之下,国内在该领域的研究仍处于小试到中试阶段。在具体的实践应用中仍存在产氢浓度低、夹带焦油脱净困难、工艺复杂等共性问题。
3.针对产氢浓度低的问题,cn107142128a提供了一种生物质炉内喷钙循环流化床燃烧气化h2原位吸附强化水汽变换制氢的工艺,即生物质在空气-水蒸气作用下在炉内进行水蒸气气化,同时炉内喷入生石灰催化增效,生成的合成气进入移动床反应器进行h2原位吸附强化水汽变换反应制氢,同时制取的氢气吸附储存在吸氢材料,分离吸氢材料进行再生释放得到高纯氢气产品。但该发明采用流化床产氢会存在气体携带焦油的问题,势必影响后续的富氢分离过程,而且h2原位吸附强化水汽变换反应制氢工艺在250~350℃下进行,水蒸气转化率极低,产物气中氢气浓度仅占5%左右,水蒸气耗大;另外,整个工艺涉及频繁的变温换热操作,工艺较复杂以及能损过高。
4.为了进一步解决氢气夹带焦油难以脱净的问题,cn104129754a公开了一种热解气化装置和旋转化学链膜制氢装置耦合的装置,利用蜂窝状孔道结构的旋转氧载体转子代替传统的床料循环,一方面利用氧载体高温下对热解气和焦油的催化裂解作用,使氧载体还原并降低产物中焦油含量,另一方面蜂窝状孔道结构的旋转氧载体转子通过绕中轴旋转操作实现氧载体的氧化再生产生富氢气体,通过上述方法制备的氢气纯度高且不含焦油。但该发明忽视了气体产物中携带的细微颗粒,这些细微颗粒不仅堵塞化学链膜孔道,而且也会与氧载体发生反应,使化学链反应活性显著降低。
技术实现要素:
5.针对现有技术中存在的不足,本发明提供一种生物质热转化制氢方法及系统,能够在得到高纯度氢气的同时实现氢气产率最大化和工艺流程最简化,得到的氢气能够满足工业用氢要求,解决了现有技术中以生物质为原料制备氢气工艺中存在的氢气品质差、工艺流程繁杂和能耗高等问题,工艺经济性得到显著提高,具有良好应用前景。
6.本发明第一方面提供一种生物质热转化制氢方法,所述方法包括如下内容:(1)生物质原料进入微波热解反应器进行反应,反应后得到含氢热解挥发性组分和热解固相物料;
(2)步骤(1)得到的含氢热解挥发性组分和热解固相物料进入气化反应器与水蒸气接触进行气化反应,得到粗合成气和固相残渣;(3)步骤(2)得到的粗合成气与经过活化的钙基吸附剂接触进行裂解、重整、水气变换以及碳酸化反应,经气固分离得到高纯氢气和碳酸化的钙基吸附剂;(4)步骤(3)中碳酸化的钙基吸附剂与步骤(2)中固相残渣进入吸附剂再生器进行再生处理,得到再生钙基吸附剂返回到气化反应器中循环使用。
7.上述生物质热转化制氢方法中,步骤(3)中所述的钙基吸附剂包括活性组分a、助剂b和组分c;以钙基吸附剂的总重量为基准,所述活性组分a含量为50~80%,助剂b含量为5~10%,组分c含量为 10~40%;所述活性组分a为氧化钙、氢氧化钙、碳酸钙、碳酸氢钙、草酸钙、乙酸钙、白云石、贝壳中的一种或几种,优选为碳酸钙;所述助剂b为硫酸钙、亚硫酸钙、硫酸氢钙、亚硫酸氢钙、硫化钙中的一种或几种,优选为硫酸钙;所述组分c包括ca和cb,其中ca选自莫来石、氧化铝、zsm分子筛(所述zsm分子筛可以是zsm-5、zsm-8、zsm-11、zsm-21、zsm-35、zsm-38分子筛中的一种或几种)、β-分子筛、钛硅分子筛ts-1、锆硅分子筛、堇青石、碳化硅中的一种或几种;cb选自硅酸三钙、硅酸二钙、铝酸一钙、铝酸三钙、二铝酸一钙、七铝酸是二钙、铁铝酸四钙铝酸钡、铝酸钡锆、氟铝酸钙、钙铝黄长石、钙矾石中的一种或几种,优选为碳化硅和二铝酸一钙,碳化硅与二铝酸一钙的质量比为1:0.1~1。
8.上述的生物质热转化制氢方法中,步骤(3)中所述钙基吸附剂制备方法如下:将活性组分a、助剂b、组分c和造孔剂混合后进行研磨,研磨后添加适量水搅拌形成均匀湿料并经成型、养护和高温处理后得到钙基吸附剂。
9.上述钙基吸附剂制备方法中,所述造孔剂为炭化料,选自生物质及其废弃物、工业有机废弃物、城镇有机垃圾等有机物质的炭化料,包括但不限于生物焦炭、塑料制品焦炭、橡胶制品焦炭、餐厨垃圾焦炭、纤维制品焦炭中的一种或几种,优选为生物焦炭。
10.上述钙基吸附剂制备方法中,所述造孔剂中碳与助剂b中钙的摩尔比为2~10:1。
11.上述钙基吸附剂制备方法中,所述成型包括但不限于挤压成型法、旋转成型法、挤压滚圆法中的任一种,优选采用挤压滚圆法,其中挤压滚圆法的挤压温度为15~60℃、压力为0.5~5mpa、挤压时间5~30分钟、滚圆盘转速150~500转/分,可获得直径为0.5~5mm球形粒子。
12.上述钙基吸附剂制备方法中,所述养护为在湿度不低于90%,温度15~60℃下养护处理1~10天。
13.上述钙基吸附剂制备方法中,所述高温处理包括绝氧还原处理和有氧焙烧处理,其中绝氧还原处理温度为850~1000℃、处理时间0.5~5h,有氧焙烧处理温度为900~1100℃、处理时间0.5~5h。
14.上述的生物质热转化制氢方法中,步骤(1)中所述生物质原料可以来源于玉米秸秆、稻壳、麦秆、木块、树叶或树枝等任何含有木质纤维素的物质,原料粒度为1~10mm。
15.上述的生物质热转化制氢方法中,步骤(1)中所述微波热解反应器中反应条件为:热解温度为400~600℃,热解时间为10~60分钟,微波功率密度为0.5
×
105~5
×
105w/m3。经过此工序,生物质的热解产物以热解挥发性组分和热解固相物料,其中热解固相物料为生物半焦,其中热解挥发性组分占65~85wt%,生物半焦为15~35wt%;热解挥发性组分中不可冷凝的气体含量达到80%以上。
16.上述的生物质热转化制氢方法中,步骤(2)和(3)中所述气化反应器中的反应条件为:气化温度为600~800℃,反应时间10~30分钟,水蒸气流量为0.2~2m3/h。
17.上述的生物质热转化制氢方法中,步骤(2)中所述气化反应器采用微波加热,微波功率密度0.1
×
105~1
×
105w/m3,主要是生物半焦对热解挥发性组分中焦油进行裂解、生物半焦的水蒸气气化以及水汽变换反应等,获得更高碳氢比的粗合成气。
18.上述的生物质热转化制氢方法中,步骤(3)中所述气化反应器利用高温钙基吸附剂的自身热量维持气化温度,主要发生钙基吸附剂增强粗合成气制氢反应,得到纯度接近95%的氢气产品,所述的生物质与钙基吸附剂质量比为1:1~10。
19.上述的生物质热转化制氢方法中,步骤(4)中所述再生包括第一段预再生处理和第二段再生处理,所述第一段预再生处理为在预再生气存在条件下进行处理,所述处理条件为:反应温度为850~1000℃,反应时间为2~10秒,预再生气流量2~5m3/h;所述预再生气为空气与烟气混合气、空气与氮气混合气、空气、氮气和烟气混合气中的一种,其中所述烟气可以是来自钙基吸附剂再生过程产生的烟气;所述第二段再生处理为在空气气氛下进行处理,所述处理条件为:反应温度为900~1100℃,反应时间为1~5秒,空气流量1~5m3/h。
20.上述的生物质热转化制氢方法中,所述的气固分离基于重力沉降、离心分离、滤网分离、静电分离、吸附分离等手段,但不限于上述方式,具体包括旋风分离、布袋过滤、静电除尘、吸附分离中的一种或几种。
21.本发明第二方面提供一种生物质热转化制氢系统,所述系统包括:微波热解反应器,其用于接收生物质原料,反应后得到热解挥发性组分和热解固相物料;气化反应器,其用于接收来自微波热解反应器的热解挥发性组分和热解固相物料与来自水蒸气进料管线的水蒸气,在钙基吸附剂存在下接触反应后得到气相物料和含钙基吸附剂的气化残渣;第一气固分离器,其用于接收来自气化反应器的气相物料,分离后得到氢气产品和粉尘;吸附剂再生装置,其用于接收来自气化反应器的含钙基吸附剂的气化残渣,在空气和烟气的作用下进行再生处理;第二气固分离器,其用于接收来自吸附剂再生装置的反应后物料,分离后得到再生吸附剂和气相物料,所述再生吸附剂返回气化反应器循环使用;第三气固分离器,其用于接收来自第二气固分离器的分离后的气相物料,分离后得到烟气和粉尘,其中部分或全部烟气经管线与吸附剂再生装置入口连通,用于输送来自气化反应器的含钙基吸附剂的气化残渣。
22.上述生物质热转化制氢系统中,所述气化反应器下部设置有套筒结构,所述套筒结构由向下收口的锥形无孔套筒和圆柱形多孔套筒构成,锥形无孔套筒的斜面与圆柱形多孔套筒的竖直面之间钝角b为120
˚
~170
˚
,圆柱形多孔套筒的开孔尺寸介于ф0.5mm~ф5mm,开孔间距2mm~20mm;圆柱形多孔套筒外径占气化反应器内径的1/8~1/2,圆柱形多孔套筒的开孔方向与圆柱形多孔套筒竖直面之间钝角c为100
˚
~160
˚
。
23.上述生物质热转化制氢系统中,进一步优选所述气化反应器上部设置有圆柱形套
筒结构,圆柱形套筒的筒壁下部开有孔,所述开有孔的筒壁长度为整个套筒筒壁长度的1/2~5/6,开孔尺寸ф1mm~ф10mm,开孔间距2mm~20mm;开孔方向与筒体竖直面的锐角a为15
˚
~75
˚
,上述圆柱形套筒外壁与气化反应器内壁间的缝隙为2mm~20mm。
24.上述生物质热转化制氢系统中,所述气化反应器上部设置有圆柱形套筒结构下端与反应器下部套筒结构的斜面上端在竖直方向的间距d为5mm~50mm。
25.上述生物质热转化制氢系统中,所述的微波热解反应器为卧式移动床反应器,反应器内部设有螺旋部件,所述螺旋部件不仅起到推料和挤料作用,也具有分散和混和作用,螺旋部件的类型可以为实体螺旋、带式螺旋和叶片螺旋等形式中的一种或几种;本发明采用的内部设有螺旋部件的卧式移动床反应器保证了物料的连续稳定移动,避免了粘壁和堵料现象发生。
26.上述生物质热转化制氢系统中,所述的微波热解反应器、气化反应器微波部分的内胆材质都采用微波专用陶瓷材料,外套采用能够屏蔽微波泄漏的不锈钢材料,而不锈钢器壁设置相应的微波传输窗口,每个窗口对应一个微波发生器,单个微波发生器的功率为1000~2000w,根据反应器的容积等情况设置具体的窗口数量,微波热解反应器、气化反应器微波部分的微波发生器一般设置4~40个,保证反应器内的功率密度为0.1
×
105~5
×
105w/m3。
27.上述生物质热转化制氢系统中,吸附剂再生装置包括预再生区和再生区,所述预再生区和再生区可以为一体结构;也可以分别独立设置,彼此之间通过管线连通;优选为一体结构,当为一体结构时,预再生区与再生区通过变径单元连通,再生区的外径为预再生区外径的1/3~4/5,预再生区与再生区的高度比为1:1~5;变径单元斜面与预再生区竖直面的钝角e为100
˚
~160
˚
。
28.上述生物质热转化制氢系统中,所述的第一气固分离器、第二气固分离器和第三气固分离器是基于重力沉降、离心分离、滤网分离、静电、吸附等手段中的一种或几种,但不限于上述方式,所述气固分离器具体可以为旋风分离器、布袋过滤器、静电除尘器、吸附分离器中的一种或几种。
29.与现有技术相比,本发明所述生物质热转化制氢方法及系统具有以下优点:1、本发明所述生物质热转化制氢方法及系统中,首创生物质双反应器制氢技术方法及系统,首先利用微波热解生物质获得富氢燃气,再将富氢燃气通过副产生物半焦形成的高温炭层获得少焦油低碳烃的富氢燃气,进一步将少焦油低碳烃的富氢燃气与钙基吸附剂进行燃气重整、水汽变换以及二氧化碳吸附反应获得高品质氢气。
30.2、本发明所述生物质热转化制氢方法及系统中,钙基吸附剂包括活性组分a、助剂b和组分c,尤其助剂b起到维持钙基吸附剂活性稳定的作用,防止活性组分a聚集,保证钙基吸附剂多次循环使用。采用钙的硫化物和(亚)硫酸盐作为助剂b,主要利用钙的硫化物和(亚)硫酸盐比氧化钙(ρ=3.35g/cm3)和碳酸钙(ρ=2.93g/cm3)具有更低密度的特点,具体体现在生物质热转化过程中钙基吸附剂发生碳酸化反应时吸附剂体积发生急剧膨胀(见反应1),而较低密度的硫酸钙(ρ=2.32g/cm3)因具有较高的自由空间能够部分抵消钙基吸附剂的膨胀,有效减缓钙基吸附剂的崩裂和破碎;当碳酸化的钙基吸附剂进行再生时吸附剂会发生明显聚集形成致密化结构(见反应2),从而降低吸附剂的作用,而引入硫酸钙后,较低密度硫酸钙在再生前期(预再生)虽然会部分形成较高密度硫化钙(见反应3),但硫化钙密
度(ρ=2.6g/cm3)低于氧化钙,仍然能起到减缓氧化钙的聚集和致密化,在再生中后期,生成的硫化钙会再次转化为硫酸钙(见反应4),强化了对氧化钙的聚集和致密化的抑制作用,从而为钙基吸附剂结构稳定、活性维持和机械性能提供了保障。
31.体积急剧膨胀反应:cao co2→
caco
3 (反应1,温度低于825℃)体积急剧收缩反应:caco3→
cao co
2 (反应2,温度高于825℃)体积适度收缩反应:caso4 c
→
cas co
2 (反应3,温度高于850℃)体积适度膨胀反应:cas o2→
caso
4 (反应4,温度低于1200℃)3、本发明所述生物质热转化制氢方法及系统中,利用颗粒状钙基吸附剂的重力作用,在气化反应器中形成了颗粒移动床,通过内嵌的多孔筒体设计,强化了富氢热解气体的径向移动,进一步提高富氢气体杂质以及携带灰尘的脱除效率。另外,颗粒移动床富集的粉尘通过多级气固分离装置进行外排,实现了产品的多级分层次回收和利用。
附图说明
32.图1为本发明的生物质热转化制氢系统示意图。
33.图2为本发明的生物质气化反应器示意图。
34.图3为本发明的钙基吸附剂再生器示意图。
具体实施方式
35.以下对本发明的具体实施方式进行详细说明。应当理解的是,此处所描述的具体实施方式仅用于说明和解释本发明,并不用于限制本发明。下述非限制性实施例可以使本领域的普通技术人员更全面地理解本发明,但不以任何方式限制本发明。以下实施例和对比例中,如无特别说明,所用的原料均可通过商购获得。
36.如图1-图3所示,本发明提供一种生物质热转化制氢系统,所述系统包括微波热解反应器1、气化反应器2、第一气固分离器3、第二气固分离器4、吸附剂再生装置(包括预再生区5和再生区6)、第三气固分离器7;其中生物质原料8经进料设备9输送进入微波热解反应器1,反应后得到热解挥发性组分和热解固相物料直接进入气化反应器2,在水蒸气10的作用下,热解挥发性组分依次与热解固相物料和来自第一气固分离器3底部出口11的钙基吸附剂发生反应,其中与热解固相物料发生焦油裂解、燃气重整以及生物焦水蒸气气化反应,与钙基吸附剂发生焦油深度裂解、燃气深度重整、水汽变换反应以及二氧化碳吸附反应,生成的富氢料13通过气化反应器2顶部气体出口12进入第二气固分离器4,经气固分离后从第二气固分离器4气体出口得到高品质氢气产品,而外排粉尘15通过第二气固分离器4底部出口进行收集。气化反应的残渣(含碳酸化的钙基吸附剂)16从气化反应器2底部排出并通过烟气17送入预再生区5,在适量空气18的作用下,碳酸化的钙基吸附剂进行预再生,经过预再生的钙基吸附剂进一步进入再生区6,并在充分空气19的作用下完全反应,得到的再生钙基吸附剂20和第一烟气21,进入第一气固分离器3进行气固分离,得到再生钙基吸附20进入气化反应器2循环使用,第二烟气22进入第三气固分离器7进行再分离得到烟气17和粉尘24,烟气17中的部分烟气作为载气回用于吸附剂再生。
37.本发明实施例1-9和比较例1中采用的气化反应器中下部设置有套筒结构,上部设置有圆柱形套筒结构。实施例10中采用的气化反应器仅下部设置有套筒结构。
38.实施例1按照质量分数,将60%碳酸钙、6%硫酸钙、24%碳化硅和10%二铝酸一钙与适量生物焦炭混合后进行球磨,其中生物焦炭中碳与硫酸钙中钙的摩尔比例6:1,球磨后添加适量水搅拌形成均匀湿料并采用挤压滚圆法进行成型处理,挤压温度为60℃、压力为2mpa、挤压时间10分钟、滚圆盘转速300转/分,获得3mm球形粒子。将成型料取出放入容器中养护,湿度不低于90%,温度15℃,养护10天后置于马弗炉中进行高温处理,先于温度950℃下绝氧处理时间5h,再于温度1000℃下有氧焙烧处理5h,得到钙基吸附剂ca1。
39.实施例2按照质量分数,将50%氧化钙、10%亚硫酸钙、26%分子筛zsm-5和14%氟铝酸钙与适量生物焦炭混合后进行球磨,其中生物焦炭中碳与亚硫酸钙中钙的摩尔比例10:1,球磨后添加适量水搅拌形成均匀湿料并采用挤压滚圆法进行成型处理,挤压温度为15℃、压力为0.5mpa、挤压时间30分钟、滚圆盘转速150转/分,获得5mm球形粒子。将成型料取出放入容器中养护,湿度不低于90%,温度60℃,养护1天后置于马弗炉中进行高温处理,先于温度850℃下绝氧处理时间5h,再于温度900℃下有氧焙烧处理5h,得到钙基吸附剂ca2。
40.实施例3按照质量分数,将70%草酸钙、10%硫化钙、10%钛硅分子筛ts-1和10%七铝酸二钙与适量生物焦炭混合后进行球磨,其中生物焦炭中碳与硫化钙中钙的摩尔比例2:1,球磨后添加适量水搅拌形成均匀湿料并采用挤压滚圆法进行成型处理,挤压温度为60℃、压力为5mpa、挤压时间5分钟、滚圆盘转速300转/分,获得0.5mm球形粒子。将成型料取出放入容器中养护,湿度不低于90%,温度15℃,养护10天后置于马弗炉中进行高温处理,先于温度1000℃下绝氧处理时间0.5h,再于温度1100℃下有氧焙烧处理0.5h,得到钙基吸附剂ca3。
41.实施例4按照质量分数,将65%白云石、5%硫酸氢钙、10%莫来石和20%铁铝酸四钙与适量生物焦炭混合后进行球磨,其中生物焦炭中碳与硫酸氢钙中钙的摩尔比例6:1,球磨后添加适量水搅拌形成均匀湿料并采用挤压滚圆法进行成型处理,挤压温度为60℃、压力为2mpa、挤压时间10分钟、滚圆盘转速300转/分,获得3mm球形粒子。将成型料取出放入容器中养护,湿度不低于90%,温度15℃,养护10天后置于马弗炉中进行高温处理,先于温度950℃下绝氧处理时间5h,再于温度1000℃下有氧焙烧处理5h,得到钙基吸附剂ca4。
42.实施例5按照质量分数,将64%碳酸钙、25.5%碳化硅和10.5%二铝酸一钙与适量生物焦炭混合后进行球磨,球磨后添加适量水搅拌形成均匀湿料并采用挤压滚圆法进行成型处理,挤压温度为60℃、压力为2mpa、挤压时间10分钟、滚圆盘转速300转/分,获得3mm球形粒子。将成型料取出放入容器中养护,湿度不低于90%,温度15℃,养护10天后置于马弗炉中进行高温处理,先于温度950℃下绝氧处理时间5h,再于温度1000℃下有氧焙烧处理5h,得到钙基吸附剂ca-5。
43.实施例6按照质量比1:10取生物质原料和钙基吸附剂ca1,其中钙基吸附剂ca1从气化反应器送入,而生物质原料处理至5mm进入微波热解反应器,在热解温度600℃、热解时间为10分钟、微波功率密度为2
×
105w/m3条件下,得到气态热解挥发分和热解固相物料,其中热解挥发性
组分占85%,生物半焦为15%;将上述气态热解挥发分和热解固相物料直接送入气化反应器,在气化温度为800℃、反应时间10分钟、水蒸气流量为2m3/h、微波功率密度1
×
105w/m3条件下,依次与热解固相物料和钙基吸附剂ca1发生反应,生成的气相产物经气固分离得到纯度为94%氢气产品,气相残渣从气化反应器依次送入吸附剂预再生器和再生器,预再生条件:反应温度为900℃、反应时间为6秒、烟气流量3.6m3/h、空气流量0.4m3/h,再生条件:反应温度为1000℃、反应时间为3秒、空气流量3m3/h,经过上述再生处理的钙基吸附剂ca1经过气固分离回用到气化反应器,烟气经过两级气固分离后部分回用与钙基吸附剂ca1的预再生过程。
44.实施例7按照质量比1:1取生物质原料和钙基吸附剂ca2,其中钙基吸附剂ca2从气化反应器送入,而生物质原料处理至10mm进入微波热解反应器,在热解温度600℃、热解时间为10分钟、微波功率密度为5
×
105w/m3条件下,得到气态热解挥发分和热解固相物料,其中热解挥发性组分占80%,生物半焦为20%;将上述气态热解挥发分和热解固相物料直接送入气化反应器,在气化温度为600℃、反应时间30分钟、水蒸气流量为0.2m3/h、微波功率密度0.1
×
105w/m3条件下,依次与热解固相物料和钙基吸附剂ca2发生反应,生成的气相产物经气固分离得到纯度为75%氢气产品,气相残渣从气化反应器依次送入吸附剂预再生器和再生器,预再生条件:反应温度为850℃、反应时间为10秒、烟气流量1.9 m3/h、空气流量0.1m3/h,再生条件:反应温度为900℃、反应时间为5秒、空气流量1m3/h,经过上述再生处理的钙基吸附剂ca2经过气固分离回用到气化反应器,烟气经过两级气固分离后部分回用与钙基吸附剂ca2的预再生过程。
45.实施例8按照质量比1:10取生物质原料和钙基吸附剂ca3,其中钙基吸附剂ca3从气化反应器送入,而生物质原料处理至1mm进入微波热解反应器,在热解温度400℃、热解时间为60分钟、微波功率密度为0.5
×
105w/m3条件下,得到气态热解挥发分和热解固相物料,其中热解挥发性组分占65%,生物半焦为35%;将上述气态热解挥发分和热解固相物料直接送入气化反应器,在气化温度为800℃、反应时间10分钟、水蒸气流量为2m3/h、微波功率密度1
×
105w/m3条件下,依次与热解固相物料和钙基吸附剂ca3发生反应,生成的气相产物经气固分离得到纯度为88%氢气产品,气相残渣从气化反应器依次送入吸附剂预再生器和再生器,预再生条件:反应温度为1000℃、反应时间为2秒、烟气流量4m3/h、空气流量1m3/h,再生条件:反应温度为1100℃、反应时间为1秒、空气流量5m3/h,经过上述再生处理的钙基吸附剂ca3经过气固分离回用到气化反应器,烟气经过两级气固分离后部分回用与钙基吸附剂ca3的预再生过程。其中预再生区反应条件为:反应温度为850~1000℃,反应时间为2~10秒,预再生气流量2~5m3/h,所述预再生气可为空气与氮气、空气与烟气、空气与氮气和烟气中的一种,空气在预再生气的体积含量为5~20%,优选空气与烟气的组合;再生区反应条件为:反应温度为900~1100℃,反应时间为1~5秒,空气流量1~5m3/h。
46.实施例9按照质量比1:5取生物质原料和钙基吸附剂ca4,其中钙基吸附剂ca4从气化反应器送入,而生物质原料处理至5mm进入微波热解反应器,在热解温度600℃、热解时间为10分钟、微波功率密度为2
×
105w/m3条件下,得到气态热解挥发分和热解固相物料,其中热解挥发性
组分占83%,生物半焦为17%;将上述气态热解挥发分和热解固相物料直接送入气化反应器,在气化温度为800℃、反应时间10分钟、水蒸气流量为2m3/h、微波功率密度1
×
105w/m3条件下,依次与热解固相物料和钙基吸附剂ca4发生反应,生成的气相产物经气固分离得到纯度为82%氢气产品,气相残渣从气化反应器依次送入吸附剂预再生器和再生器,预再生条件:反应温度为900℃、反应时间为6秒、烟气流量3.6m3/h、空气流量0.4m3/h,再生条件:反应温度为1000℃、反应时间为3秒、空气流量3m3/h,经过上述再生处理的钙基吸附剂ca4经过气固分离回用到气化反应器,烟气经过两级气固分离后部分回用与钙基吸附剂ca4的预再生过程。
47.实施例10按照质量比1:10取生物质原料和钙基吸附剂ca1,其中钙基吸附剂ca1从气化反应器送入,而生物质原料处理至5mm进入微波热解反应器,在热解温度600℃、热解时间为10分钟、微波功率密度为2
×
105w/m3条件下,得到气态热解挥发分和热解固相物料,其中热解挥发性组分占85%,生物半焦为15%;将上述气态热解挥发分和热解固相物料直接送入气化反应器,在气化温度为800℃、反应时间10分钟、水蒸气流量为2m3/h、微波功率密度1
×
105w/m3条件下,依次与热解固相物料和钙基吸附剂ca1发生反应,生成的气相产物经气固分离得到纯度为92%氢气产品,气相残渣从气化反应器依次送入吸附剂预再生器和再生器,预再生条件:反应温度为900℃、反应时间为6秒、烟气流量3.6m3/h、空气流量0.4m3/h,再生条件:反应温度为1000℃、反应时间为3秒、空气流量3m3/h,经过上述再生处理的钙基吸附剂ca1经过气固分离回用到气化反应器,烟气经过两级气固分离后部分回用与钙基吸附剂ca1的预再生过程。
48.比较例1按照质量比1:10取生物质原料和钙基吸附剂ca5,其中钙基吸附剂ca5从气化反应器送入,而生物质原料处理至5mm进入微波热解反应器,在热解温度600℃、热解时间为10分钟、微波功率密度为2
×
105w/m3条件下,得到气态热解挥发分和热解固相物料,其中热解挥发性组分占86%,生物半焦为14%;将上述气态热解挥发分和热解固相物料直接送入气化反应器,在气化温度为800℃、反应时间10分钟、水蒸气流量为2m3/h、微波功率密度1
×
105w/m3条件下,依次与热解固相物料和钙基吸附剂ca5发生反应,生成的气相产物经气固分离得到纯度为86%氢气产品,气相残渣从气化反应器依次送入吸附剂预再生器和再生器,预再生条件:反应温度为900℃、反应时间为6秒、烟气流量3.6m3/h、空气流量0.4m3/h,再生条件:反应温度为1000℃、反应时间为3秒、空气流量3m3/h,经过上述再生处理的钙基吸附剂ca5经过气固分离回用到气化反应器,烟气经过两级气固分离后部分回用与钙基吸附剂ca5的预再生过程。
再多了解一些
本文用于企业家、创业者技术爱好者查询,结果仅供参考。