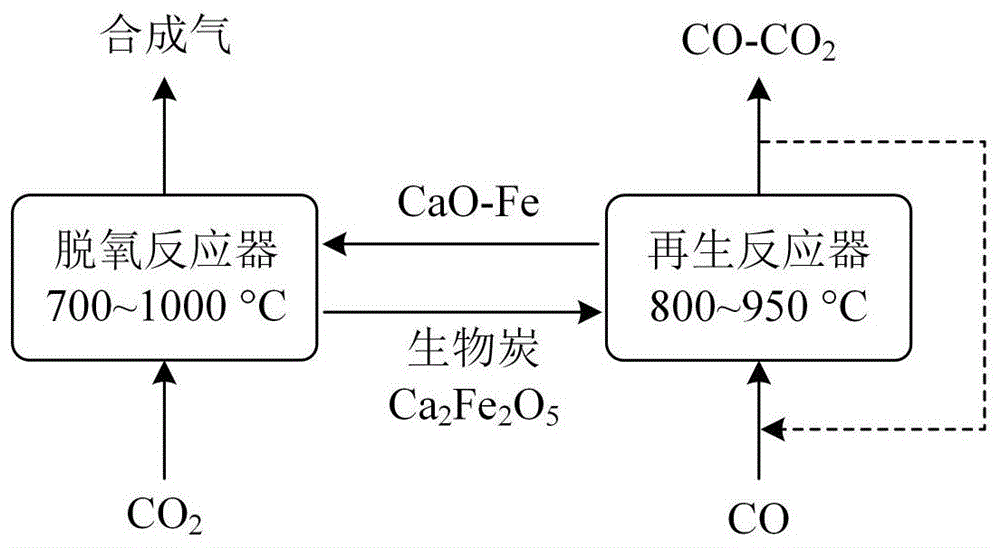
本发明涉及一种功能性复合载氧体化学链脱氧气化协同co2转化方法,属于燃烧化工与材料技术领域。
背景技术:
生物质是仅次于煤炭、石油、天然气的第四大能源,具有分布广、可再生、低污染等特点,合理开发利用生物质能够缓解我国能源环境问题。生物质的利用包括物理转换、热化学转化、生化转化等方式。生物质气化是生物质能高品位利用的重要形式。生物质气化技术是在高温条件下,以空气、蒸汽等为气化剂,将生物质通过热化学反应转化为co、h2和低分子烃类等可燃气体的过程。传统非催化气化技术存在合成气品质低、焦油含量高、积炭、产物含氧量高等不足。
生物质化学链气化是基于化学链燃烧的创新气化技术,以载氧体中的晶格氧代替气态氧化剂参与反应,通过控制载氧体、气化剂与生物质的比例获得以h2和co为主要成分的合成气。与传统非催化气化工艺相比,生物质化学链气化具有以下潜在优势:1)载氧体为气化提供晶格氧,与纯氧气化相比,大大节省了制氧成本;2)与空气气化相比,消除了nox的潜在生成和空气对合成气的稀释作用;3)载氧体还可充当焦油裂解和烃类重整的催化剂,有助于减少气化产物中焦油含量,提高合成气品质;4)合成气具有较高的低位热值,气化效率提高;5)根据合成气组分产率和浓度的不同,可制备不同的化工原料。
载氧体在化学链气化过程中起到至关重要的作用,在已有研究中,铁基载氧体因成本效益和载氧能力而被广泛应用,但其存在烧结与团聚问题。将fe与cao结合能够在原子水平上将其均质化为ca2fe2o5,从而改善载氧体性能,因此,ca2fe2o5作为一种潜在的高性能载氧体受到广泛关注。目前已有的基于ca2fe2o5生物质化学链气化技术主要由燃料反应器(fr)和蒸汽反应器(sr)组成,ca2fe2o5载氧体在fr中与生物质中的挥发分和固定碳发生还原反应并生成目标产物合成气,随后还原态的载氧体(fe cao)被送入sr中,被蒸汽氧化为ca2fe2o5,再次进入fr中气化,形成化学链循环。现有手段化学链反应所需的能耗高,且合成气质量有待提高。
技术实现要素:
针对现有生物质化学链气化技术存在的气化产物中焦油含量较高,含氧性co2和h2o含量高、合成气品质受到限制的问题,本发明提出了一种功能性复合载氧体化学链脱氧气化协同co2转化方法,旨在改善二氧化碳和生物质的协同活化催化,降低二氧化碳排放,此外,还有助于改善合成气的含量和纯度,减少焦油的含氧量,不仅如此,还有利于实现再生化学链循环制备。
一种功能性复合载氧体化学链脱氧气化协同co2转化方法,包括以下步骤:
步骤1):生物质脱氧气化
将生物质和cao、fe的混合物在含有二氧化碳的载气、700℃~1000℃的温度下进行脱氧气化,得到含有h2、co的合成气,以及碳-ca2fe2o5混合物;
所述的cao、fe的摩尔比为1:1~1.1;(cao fe)/b(氧化钙和铁的总重量和生物质的质量比)的质量比大于0,小于或等于0.4;
载气中,二氧化碳的流率大于0,小于或等于80cm/min;
步骤2):铁酸钙载氧体再生
将碳-ca2fe2o5复合物在800℃~950℃的温度下进行再生,得到cao、fe,以及co和co2的再生气;
将再生得到的cao、fe循环至步骤1)中。
本发明首次报道在二氧化碳气氛下,将生物质和cao、fe进行气化反应,进一步基于处理过程中的气化剂(co2)流率、温度以及(cao fe)/b质量比的协同控制,实现cao(111)/fe(110)/ac界面处co2的最稳定吸附,进一步降低二氧化碳的吸附能,有助于改善生物质的气化,提高合成气的还原性气氛的收率以及含量,降低焦油的含氧量,不仅如此,还有助于获得高无序碳(高无定型碳),其能够意外地在低温条件下转化,实现cao-fe的低温再生,产物作为化学链纽带循环至步骤1)中,实现化学链过程。本发明技术方案,具有更优的二氧化碳减排效果,此外,还具有更优的合成气质量,更低的化学链再生条件,具有更优的工业实用价值。
本发明技术方案,生物质和cao、fe在二氧化碳流质介质下进行气化反应,并基于气化反应过程的二氧化碳流率、fe的用量以及温度的协同控制是实现co2的最稳定吸附,制得高无序碳-ca2fe2o5混合物的关键。
本发明步骤1)中,基于fe0→fe3 的机制,实现生物质的气化,其处理机制为:
生物质 co2 fe cao→ca2fe2o5 碳材料 合成气 生物焦油。
本发明中,所述的生物质还可以采用煤、污泥、塑料垃圾、固体废弃物中的至少一种替换。
本发明中,(cao fe)/b指cao和fe的总质量与生物质质量的比。
本发明中,所述的(cao fe)/b的质量比为0.1~0.3:1;进一步优选为0.1~0.2:1。
本发明中,步骤1)中,在流化床中进行;
优选地,载气中,二氧化碳的流率为10~40cm/min;进一步优选为20~30cm/min。
作为优选,步骤1)中,脱氧气化温度为850℃~950℃。
作为优选,步骤1)中,所述的无定型碳的id/ig为0.87~3.25。
本发明中,还可采用能够形成尖晶石型、钙钛矿型、钙铁石型等结构的复合氧化物的金属和氧化物替换所述的铁酸钙。
本发明中,步骤2)中,在含有co的气氛下进行;
优选地,所述的co气氛来源于步骤2)中产气。
作为优选,步骤2)中,再生温度为850℃~950℃。
所述步骤2)中再生反应器采用太阳能供能或工业余热供热。
本发明中,所述步骤2)中在固定床或移动床反应器中进行。
有益效果:
1、本发明首次报道,生物质和fe、cao在二氧化碳气氛下进行气化反应,相较于现有的生物质和载氧体的气化处理工艺,有助于获得更好的合成气产率与品质,更低的焦油含氧量。相较于无cao-fe添加,(cao fe)/b质量比为0.2,合成气产率可增长16.37%,其中co产率增长69.11%。此外,在生物质气化过程,通过cao fe→ca2fe2o5能够实现生物质/生物油的部分脱氧;
2、基于本发明生物质和fe、cao在二氧化碳气氛下进行气化反应,相较于现有的生物质和载氧体的气化处理工艺,该发明通过fe cao co2→ca2fe2o5 co,具有较优的二氧化碳减排能力。相较于无cao-fe添加,(cao fe)/b质量比为0.2,co2减排量从2.25mmol/g·biomass增长至8.73mmol/g·biomass,提高288%;
3、基于本发明步骤1)的处理工艺下,进一步通过fe用量、二氧化碳流率以及处理温度的联合控制,能够产生协同作用,有利于生物质的气化,降低合成气的含氧量,不仅如此,还能够控制碳化得到的碳材料的石墨化程度以及形态,能够获得无定型碳-ca2fe2o5混合物,该混合物具有更温和的反应温度,更利于实现以fe-cao为纽带的化学链过程。实现结果显示:fe添加量达到(cao fe)/b质量比=0.2时,id/ig高达3.25;
4、基于本发明的cao-fe-ac(无定形碳)系统,co2能够实现cao/fe/ac材料上有效吸附、活化与解离。通过密度泛函理论计算获得co2最稳定吸附位点位cao(111)/fe(110)/无定形碳(ac)三相界面处,co2在界面处稳定吸附,并有效的转化为co* o*,其中o*还可以与碳材料结合形成co,该过程的反应能垒为-1.87ev,低于co2在fe(110)及石墨烯表面的吸附能(分别为-1.47ev和-0.188ev),因此,构筑的cao-fe材料更有利于co2的活化与解离。
针对以上分析,可以看到基于铁酸钙载氧体化学链脱氧方法对合成气进行精炼,方法简单易行、操作方便、合成气品质高、碳产物转化温度低,适用于工业化应用,得到高品质原料或能源。
附图说明
图1一种功能性复合载氧体化学链脱氧气化协同co2转化方法流程图摘要附图图2-图15为实验结果,其中,
图2为实施例1((cao fe)/b质量比为0.2)的气化合成气随时间的变化
图3为实施例1生物炭随气化时间的拉曼图谱
图4为实施例1生物炭id/ig(无序化程度)随气化时间的变化
图5为实施例2((cao fe)/b质量比为0.1)气化合成气随气化时间的变化
图6为实施例3(气化温度为950℃)气化合成气随气化时间的变化
图7为实施例4(co2流率为30cm/min)气化合成气随气化时间的变化
图8为实施例5(再生温度为950℃)气化合成气随气化时间的变化
图9为对比例1((cao fe)/b质量比为0)气化合成气随时间的变化
图10为对比例1生物炭随气化时间的拉曼图谱
图11为对比例1生物炭id/ig(无序化程度)随气化时间的变化
图12(cao fe)/b质量比对合成气产率的影响
图13(cao fe)/b质量比对合成气co2浓度的影响
图14(cao fe)/b质量比对co2减排量的影响
图15为对比例2(co2流率为0cm/min)气化合成气随气化时间的变化
图16-图21为量子化学计算结果,其中,
图16cao(111)/fe(110)/ac界面不同吸附位点上的吸附能
图17cao(111)/fe(110)/ac界面co2吸附最稳定位点的侧面图
图18cao(111)/fe(110)/ac界面co2吸附最稳定吸附位点
图19cao(111)/fe(110)/ac界面co2吸附过渡态
图20cao(111)/fe(110)/ac界面co2解离位点
图21cao(111)/fe(110)/ac界面co2吸附、活化与解离的相对能量
具体实施方式
下面结合实施例、对比例和说明书附图对本发明作进一步的说明。
以下案例,除特别声明外,所述的生物质(代号为b)均指松木。
以下案例,所述的ca:fe比例指摩尔比。
实施例1:通过实验测试
1)将1.000g生物质和cao与fe的混合物(0.200g,ca:fe=1:1;(cao fe)/b质量比(cao和fe的总质量与生物质的质量比为0.2)通入脱氧反应器,以170℃/min的升温速率升温至850℃,以n2为载气,其流率为80cm/min,另外,在载气中加入co2,且co2流率为20cm/min。主要产物为生物炭及合成气,含有少量的副产物焦油,反应气中的成分和时间的关系见图2所示。
2)气化完成后,切换升温阶段的气氛100vol.%n2,流率为80cm/min,进入载氧体再生阶段。在高温850℃下,生物炭气化,产物为co与co2的混合物,同时将ca2fe2o5还原为cao、fe。
在脱氧反应器升温与气化阶段持续收集产气,测定各气体组分产率及气体总产率随时间的变化趋势,结果见图2。气化达到42.5min时,总气体产率为83.96mmolg-1·biomass,co产率为47.40mmolg-1·biomass,h2产率为18.15mmolg-1·biomass。
气化产物生物炭随气化时间的拉曼图谱和生物炭id/ig(无序化程度)随气化时间的变化分别见图3和图4。生物炭id/ig随气化时间增加显著变大,从0.87(气化时间=0min)上升到3.25(气化时间=180min)。
实施例2:
与实施例1相比,区别仅在于,在气化过程中(cao fe)/b不同。
1)将1.000g生物质和cao与fe的混合物(0.100g,ca:fe=1:1)通入脱氧反应器,以170℃/min的升温速率升温至850℃,以n2为载气,其流率为80cm/min,在载气中添加co2,其中,co2流率为20cm/min。主要产物为生物炭及合成气,含有少量的副产物焦油。
2)气化完成后,切换升温阶段的气氛100vol.%n2,流率为80cm/min,反应器以170℃/min的升温速率升温至850℃,进入载氧体再生阶段。生物炭气化,产物为co与co2的混合物,同时将ca2fe2o5还原为cao、fe。
在脱氧反应器升温与气化阶段持续收集产气,测定各气体组分产率及气体总产率随时间的变化趋势,结果见图5。气化达到42.5min时,总气体产率为75.38mmolg-1·biomass,co产率为46.01mmolg-1·biomass,h2产率为13.16mmolg-1·biomass。与实施例1相比,气体总产率与co、h2产率均有所下降。
实施例3:
与实施例1相比,区别仅在于,在气化过程中温度不同。
1)将1.000g生物质和cao与fe的混合物(0.200g,ca:fe=1:1)通入脱氧反应器,以170℃/min的升温速率升温至950℃,以n2为载气,其流率为80cm/min,在载气中添加co2,其中,co2流率为20cm/min。主要产物为生物炭及合成气,含有少量的副产物焦油。
2)气化完成后,切换升温阶段的气氛100vol.%n2,流率为80cm/min,反应器以170℃/min的升温速率升温至850℃,进入载氧体再生阶段。生物炭气化,产物为co与co2的混合物,同时将ca2fe2o5还原为cao、fe。
在脱氧反应器升温与气化阶段持续收集产气,测定各气体组分产率及气体总产率随时间的变化趋势,结果见图6。气化达到42.5min时,总气体产率为82.88mmolg-1·biomass,co产率为58.75mmolg-1·biomass,h2产率为15.55mmolg-1·biomass。与实施例1相比,气体总产率与co、h2产率均显著增加,因此,升高气化温度有利于生物质的脱氧气化,但也造成了较大的能源消耗。
实施例4:
与实施例1相比,区别仅在于,在气化过程中co2流率不同。
1)将1.000g生物质和cao与fe的混合物(0.200g,ca:fe=1:1)通入脱氧反应器,以170℃/min的升温速率升温至850℃,以n2为载气,其流率为80cm/min,在载气中添加co2,其中,co2流率为30cm/min。主要产物为生物炭及合成气,含有少量的副产物焦油。
2)切换升温阶段的气氛100vol.%n2,流率为80cm/min,反应器以170℃/min的升温速率升温至850℃,进入载氧体再生阶段。生物炭气化,产物为co与co2的混合物,同时将ca2fe2o5还原为cao、fe。
在脱氧反应器升温与气化阶段持续收集产气,测定各气体组分产率及气体总产率随时间的变化趋势,结果见图7。气化达到42.5min时,总气体产率为79.55mmolg-1·biomass,co产率为51.57mmolg-1·biomass,h2产率为9.00mmolg-1·biomass。
实施例5:
与实施例1相比,区别仅在于,在再生过程中温度不同。
1)将1.000g生物质和cao与fe的混合物(0.200g,ca:fe=1:1)通入脱氧反应器,以170℃/min的升温速率升温至850℃,以n2为载气,其流率为80cm/min,在载气中添加co2,其中,co2流率为20cm/min。主要产物为生物炭及合成气,含有少量的副产物焦油。
2)切换升温阶段的气氛100vol.%n2,流率为80cm/min,反应器以170℃/min的升温速率升温至950℃,进入载氧体再生阶段。生物炭气化,产物为co与co2的混合物,同时将ca2fe2o5还原为cao、fe。
在脱氧反应器升温与气化阶段持续收集产气,测定各气体组分产率及气体总产率随时间的变化趋势,结果见图8。气化达到17.5min时,co产率为12.35mmolg-1·biomass,co2产率为1.19mmolg-1·biomass。
对比例1:
与实施例1相比,区别仅在于,在气化过程不加入cao与fe。
1)将1.000g生物质通入脱氧反应器,以170℃/min的升温速率升温至850℃,以n2为载气,其流率为80cm/min,在载气中补加co2,且co2流率为20cm/min。主要产物为生物炭、焦油及合成气。
2)切换升温阶段的气氛100vol.%n2,流率为80cm/min,反应器以170℃/min的升温速率升温至850℃,生物炭不反应。
在脱氧反应器升温与气化阶段持续收集产气,测定各气体组分产率及气体总产率随时间的变化趋势,结果见图9。气化达到42.5min时,总气体产率为65.97mmolg-1·biomass,co产率为34.32mmolg-1·biomass,h2产率为9.38mmolg-1·biomass。与实施例1相比,气体总产率与co、h2产率均显著下降;气化产物生物炭随气化时间的拉曼图谱和生物炭id/ig(无序化程度)随气化时间的变化分别见图10和图11。生物炭id/ig随气化时间增加无显著变化,保持在0.93~0.83左右。
比较实施例1、实施例2和对比例1的气体产率、co2浓度以及co2减排量,结果见图12~图14。与对实施1的气化结果相比,对比例1的合成气产率降低16.37%,co2浓度升高44.16%,co2减排量从8.73mmol/g·biomass降至2.25mmol/g·biomass,严重影响高合成气品质;比较实施例1和对比例1得到的生物炭id/ig(图4和图11),实施例1得到的生物炭id/ig变化较大(0.87~3.25),对比例1得到的生物炭id/ig无显著变化(0.93~0.83),生物炭无序程度难以调控,且相同气化时间下,实施例1得到的生物炭无序程度更大(id/ig大),其转化温度更为温和。
对比例2:
与实施例1相比,区别仅在于,在气化过程不加入二氧化碳。
1)将1.000g生物质和cao与fe的混合物(0.200g,ca:fe=1:1)通入脱氧反应器,以170℃/min的升温速率升温至850℃,以n2为载气,其流率为80cm/min。主要产物为生物炭、合成气及少量副产物焦油。
2)切换升温阶段的气氛100vol.%n2,流率为80cm/min,反应器以170℃/min的升温速率升温至850℃,进入载氧体再生阶段。生物炭气化,产物为co与co2的混合物,同时将feo还原为fe。
在脱氧反应器升温与气化阶段持续收集产气,测定各气体组分产率及气体总产率随时间的变化趋势,结果见图15。气化达到42.5min时,总气体产率为41.64mmolg-1·biomass,co产率为19.83mmolg-1·biomass,h2产率为13.97mmolg-1·biomass。结合实施例1结果,co2的加入有助于生物质的气化,气体总产率提高了101.63%,co、h2产率分别提高了139.03%和29.92%。
本发明提出一种功能性复合载氧体化学链脱氧气化协同co2转化方法,以cao-fe作催化剂,在脱氧反应器部分,在二氧化碳气流下使生物质在高温下气化,产生生物炭、轻质焦油和h2、co、co2、ch4等气态产物,同时cao、fe在co2气化剂作用下氧化为ca2fe2o5,与生物炭一同进入再生反应器;在再生反应器部分,生物炭在高温下气化,将ca2fe2o5还原为cao、fe,再次返回脱氧反应器,载氧体通过
1)生物质化学链脱氧气化过程中,通过cao-fe体系的催化作用与ca2fe2o5的生成(cao fe co2→ca2fe2o5 co)实现合成气的增产与提质,降低焦油含氧量。(cao fe)/b从0增大至0.2,合成气产率增长16.37%,co2浓度降低44.16%;
2)通过将生物质与fe、cao在co2气化剂中实现气化,对于二氧化碳减排具有积极影响,(cao fe)/b从0增大至0.2,co2减排量从2.25mmol/g·biomass增长至8.73mmol/g·biomass,提高288%;
3)通过控制(cao fe)/b、气化剂流率、温度、气化时间等条件调节产物的组成,定向调控高无序度碳的生成,实现co2在cao/fe/ac材料上有效吸附、活化与解离。获得的无定型碳能够实现更低温度下的ca2fe2o5 c→cao fe co,降低载氧体氧化还原循环的能耗。
本文用于企业家、创业者技术爱好者查询,结果仅供参考。