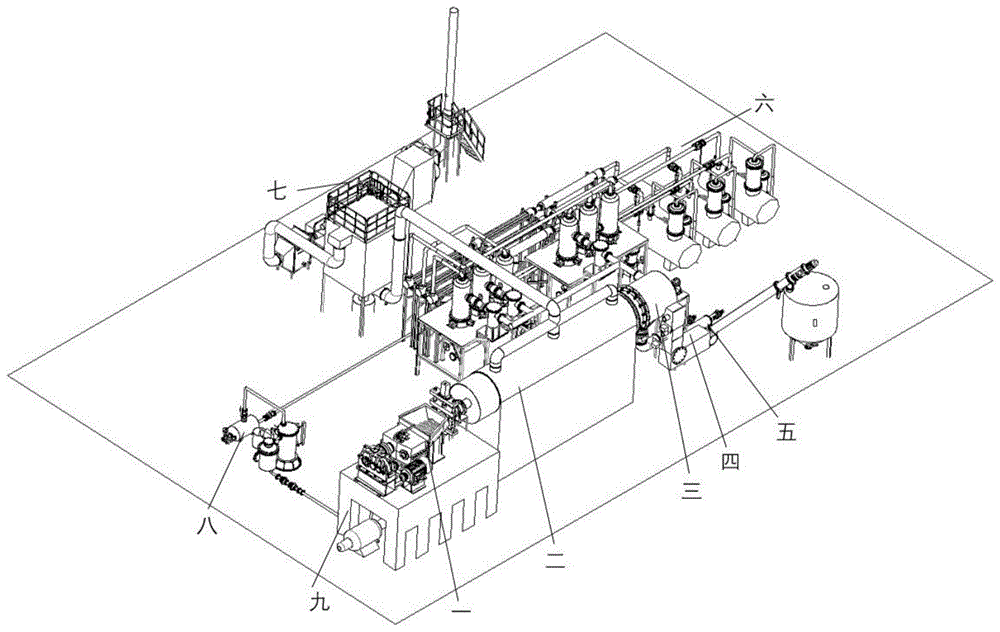
本发明属于固体废弃物循环利用技术领域,面向废轮胎资源化利用行业,尤其是废轮胎整胎工业连续化裂解,主要是用于废轮胎整胎裂解固相产物自动分离方法及装置,主要指裂解钢丝与裂解炭黑的分离、输送方法及装置,从而实现废轮胎工业连续化整胎裂解,节约裂解过程的能源消耗。
背景技术:
橡胶是事关国计民生和国防安全的重要战略物资,与煤炭、钢铁、石油并称为四大基础工业原料,广泛应用于工业、农业、国防、航天、运输、日常生产等各个领域。在国家政策的大力支持下,橡胶工业已成为国民经济的主要支撑产业,国内年产值已过万亿元,轮胎约占70%。中国轮胎产量约占世界的40%,其中40%用于出口,成为名副其实的橡胶工业大国。与此同时,也产生了大量的废橡胶,据估计,2019年废橡胶达到1600万吨左右,其中废轮胎3亿多条接近1400万吨。
轮胎是安全性能要求极高的产品,为了保证人身安全,轮胎朝着高强度、耐磨、稳定和耐老化的方向发展,导致轮胎废弃后长期(几百甚至上千年的时间)不能自然降解,如何处理这种“黑色污染”已成为世界性难题。
我国废旧轮胎处理方法主要有循环利用(翻新再制造、再生橡胶、胶粉)和最终处理(堆积、填埋、焚烧、裂解等)两种方式。现阶段废旧轮胎的循环利用主要以载重胎、工程胎为主,废旧乘用胎由于配方和结构的原因循环利用率极低,而其产量约占废旧轮胎的一半;同时,经过2-3次循坏利用后的轮胎等橡胶制品,从安全角度而言已不能再循环使用,故每年也会产生大量的废旧轮胎。这些不能循环利用的废旧轮胎只能通过堆积、填埋、焚烧、裂解等方式进行处理。
裂解技术能够将废轮胎转换成为富含芳烃的油、高燃值的气、可回用的炭黑及钢丝,与其他处理方法相比具有处理量大、经济效益高、污染小等众多的优点,能够实现资源的回收再利用,是目前废轮胎资源化处理最有效的方式。废旧轮胎裂解工艺技术装备的发展问题也引起了国家的高度重视,国家发改委2017年第一号公告明确将“废旧轮胎分解制油和炭黑装置”列入《战略性新兴产业重点产品和服务指导目录(2016版)》,国家多部门也联合印发《关于加快推进再生资源产业发展的指导意见》,把废轮胎热裂解生产技术与装备列入重点领域,引起了研究学者的广泛关注。
近年来关于废轮胎裂解的专利众多,如cn201710526465.4一种废旧轮胎裂解炉,它包括保温炉体,保温炉体的左右端面上分别旋转的连接有转轴a和转轴b,转轴a和转轴b旋转的设置在支架上,保温炉体内设置有裂解炉膛,裂解炉膛的左端面固定在转轴a的右端,转轴b采用中空结构,裂解炉膛内的转轴b上设置有排气孔,裂解炉膛内的转轴b的外表面设置有搅拌叶片,转轴b的右端通过旋转接头与灰尘沉降室相连,灰尘沉降室的上方设置有排气口,排气口通过连接管与油水分离器相连,油水分离器的底端和顶端分别设置有排水口和排油口,排油口通过连接管与冷凝装置顶端的进气口相连,冷凝装置的顶端和底端分别设置有排气管和排液管;总的,本发明具有结构设计合理、裂解充分、工作效率高的特点。专利cn201510429619.9废旧轮胎裂解炉及其分段裂解工艺,废旧轮胎裂解炉包括裂解炉主体(1)、裂解室(2)、入料口(3)、炉盖(4),所述废旧轮胎裂解炉的内壁上设置有若干条热辐射管(5),沿着所述裂解炉主体(1)的长度方向上设置有若干个分段阀(6),所述若干个分段阀(6)均与所述裂解室(2)相连通。所述废旧轮胎裂解炉的分段裂解工艺包括如下步骤:a、进料;b、预加热;c、分段裂解;d、冷却;e、清炉。本发明应用于废旧轮胎处理的技术领域。专利cn2013106831038一种废旧轮胎裂解进料工艺及设备,采用特定的进料设备保证废旧轮胎在密封状态下被整胎送入裂解仓进行裂解,该设备包括固定的圆桶状外壳,外壳内设置有内筒体,所述的内筒体中心设置有转轴,内筒体筒壁与转轴之间通过辐条连接,内筒体筒壁上设置有至少一个开口,每个开口内侧的内筒体内连接有料仓,所述外壳左右两侧筒壁上各设置有一个与内筒体开口对应的窗口i和窗口ii。采用本发明,简化了现有的废旧轮胎裂解工艺步骤,真正实现了废旧轮胎整胎连续化裂解。专利cn2015104295425废旧轮胎真空热反射裂解系统及处理工艺,所述废旧轮胎真空热反射裂解系统包括废旧轮胎裂解炉、燃烧炉和有机热气冷却装置,所述废旧轮胎裂解炉上设置有抽气管路(1),所述抽气管路(1)与所述有机热气冷却装置相连通,所述有机热气冷却装置上还设置有出气管(2);所述废旧轮胎裂解炉的内壁上设置有若干条热辐射管(5a)。所述处理工艺包括如下步骤:a、进料;b、预加热;c、裂解;d、冷却、分离;e、清理所述废旧轮胎裂解炉,打包分离出来的钢丝和碳素并进行入库处理。
上述提及的发明专利分别是针对废轮胎裂解装备的反应釜主体结构、裂解方法、进料结构、加热系统等方面进行了发明创造,实现了废旧轮胎裂解工艺装备的进一步优化。从关于废旧轮胎裂解专利的检索理资料表明,目前废轮胎裂解主要以间歇式裂解和废旧轮胎破碎式裂解为主,其中间歇式裂解存在裂解效率较低,工作劳动强度较大,智能化水平较低等问题,行业并不鼓励发展间隙式裂解工艺;废旧轮胎破碎式裂解,需要额外提供轮胎破碎机,额外增加了废轮胎裂解的工序和能源的消耗;因此,废轮胎整胎裂解已成为行业发展的趋势,但却一直未见工业化应用,这主要是由于废旧轮胎破碎式连续化裂解的固相产物中钢丝大小较少,能够与裂解炭黑一起通过炭黑输出装置输送出裂解反应器,后经过磁选工序便可相互分离;而废轮胎整胎连续化裂解过程中轮胎带束层、胎体中的钢丝保持完整,传统的分离、输送方法及装置无法完成钢丝与裂解炭黑的分离及输送,这也是导致目前行业内一直未出现整胎连续化裂解装备面临的主要问题之一。
针对上述难题,本发明主要以废轮胎整胎工业连续化裂解为目标,研发出一种裂解炭黑与钢丝自动分离、连续输送的方法及装置,实现废轮胎整胎裂解过程中炭黑与钢丝的自动分离和连续输出,从而实现废轮胎整胎工业连续化裂解,降低裂解过程轮胎破碎的能源消耗,实现裂解过程无害化及裂解产物的最大经济收益。
技术实现要素:
有鉴于此,本发明针对上述问题,提出一种废轮胎整胎工业连续化裂解固相产物自动分离方法及装备,实现废轮胎整胎裂解过程中裂解固相产物的自动分离和连续输出,从而达到废轮胎工业连续化裂解的目的。
为了实现上述目的,本发明采用如下技术方案实现:
一种废轮胎整胎工业连续化裂解固相产物自动分离装备,包括通过连接部件相连的异型双锥连续进料系统一、裂解反应器主体系统二、裂解固相产物分离系统三、钢丝输送系统四、裂解炭黑连续输出系统五、裂解油品等级自动收集系统六,模块化分布式智能尾气综合处理系统七、裂解不凝可燃气回用系统八、燃烧供热系统九以及催化裂解智能控制系统,能够实现废轮胎整胎裂解过程中裂解固相产物的分离。
优选的,所述裂解固相产物分离系统三包括固相产物分离叶片5及钢丝输送叶片8,固相产物分离叶片5与钢丝输送叶片8中间有高度为50~65mm挡板,从而使裂解钢丝在输送过程中必须跨过中间的挡板1;
挡板为介划分为固相产物分离区域ⅰ和钢丝输送区域ⅱ。
优选的,固相产物分离叶片5结构的具体特征为:分离叶片沿横向中心线扭转15~20°,沿着纵向扭转35~45°,分离叶片右侧底部上翘3~8°。
优选的,具体分离叶片方程如下所述:
1)在直角坐标系形成平面结构:
f(x,y,z)=ax by cz
2)平面沿着
3)上述曲面结构沿着
4)上述平面沿x0y平面向z轴正方向扭转角度
优选的,其中,a值范围与钢丝由固相产物分离区域ⅰ长度l有关,b值的范围需要根据反应釜直径d尺寸来确定,其中,a=1.1~1.3l,b=0.6~0.7d,
优选的,固相产物分离叶片5呈半圆形设计,底部上翘,对称安装在固相分离系统的传动轴11上,随着传动轴11的转动而运动,并且在转动过程中通过上翘部分将裂解钢丝从固相产物分离区域ⅰ输送到钢丝输送区域ⅱ中,在输送过程中会使裂解钢丝团一直处于滚动过程中,从而使夹杂在裂解钢丝中的裂解炭黑逐渐漏出,实现了夹杂在钢丝团中的炭黑与钢丝分离。
优选的,在固相产物分离叶片5底部开设矩形槽;使钢丝在运动过程中漏出的裂解炭黑通过固相产物分离叶片5底下的槽空间漏出,在通过底部的筛网进入裂解炭黑连续输出系统五中;
在固相产物分离叶片5的作用下,裂解钢丝从固相产物分离区域ⅰ输送到钢丝输送区域ⅱ中实现了夹杂在钢丝团中的裂解炭黑与钢丝的分离;
在钢丝输送区域ⅱ底部仍然设有孔道,并且与固相产物分离区域ⅰ的孔道相连,并且通过钢丝输送叶片8在带动钢丝团运动过程中实现内部裂解炭黑的进一步漏出,并通过底部的筛网结构进入裂解炭黑连续输出系统五中。
优选的,钢丝输送叶片8沿横向弯曲25~35°,弯曲的凸起方向为钢丝分离叶片的工作面,通过其凸起推动裂解钢丝运动,并且钢丝输送叶片底部开设矩形槽,给漏出的裂解炭黑留有移动通道;
钢丝输送叶片8对称安装在固相分离系统的传动轴11上,随着传动轴的转动而运动,其中钢丝输送叶片8与固相产物分离叶片5呈90°角度安装,其中钢丝输送叶片8与固相产物分离叶片5都是通过夹板式螺栓连接在传动轴11上。
优选的,传动轴11的动力源来自于裂解反应釜(裂解反应器主体系统二下的裂解反应釜二-2)的回转运动,无需外接动力源,裂解反应釜二-2通过链条二-4与电机二-5减速器相连,实现了外部电机在带动裂解反应釜二-2运动的同时也带动了固相产物分离叶片5的运动,
电机二-5减速器将动力源通过链条二-4传递到从动轮二-3上,从动轮二-3与裂解反应釜二-2焊接固定,从而实现裂解反应釜二-2的回转运动,裂解反应釜二-2通过内部结构在将动力源传递到分离叶片上;
固相分离轴系结构通过焊接板4与裂解反应釜二-2焊接固定,轴系末端通过轴承组件13支撑,并通过密封组件12实现轴系结构与裂解反应釜二-2的密封;
中空固定支撑柱3与焊接板4焊接到一起,将焊接板4设计成u字型开口结构,通过焊接板4的背面与裂解反应釜焊接固定;中空固定支撑柱3另一侧与传动轴承组件9的外壳9-1焊接固定,为了便于安装和焊接,外壳9-1的焊接位置设计成槽型结构,在安装过程中先将中空固定支撑柱3与外壳9-1焊接,然后再将中空固定支撑柱3与焊接板4焊接,最后再将焊接板4与裂解反应釜二-2焊接;
传动轴承组件9是由外壳9-1,滑动轴套9-2上下两部分组成,其安装关系为:外壳9-1、滑动轴套9-2与传动轴11通过定位销定位后,用4个螺钉从外壳9-1外部将滑动轴套9-2紧固,然后与传动轴承组件9的下部分配合固定在传动轴11的相应位置。
优选的,通过5固相产物分离叶片及8钢丝输送叶片实现裂解固相产物中裂解炭黑与钢丝的分离。
裂解钢丝由于成团的特性,增加了其输送难度,为此研发了裂解钢丝输送方法,具体如下:
裂解钢丝进入(四、钢丝输送系统中)后先落入四-3.钢丝出料门a上方,待一段时间后(根据裂解工艺具体确定,一般为2~5min最为适宜),打开四-3.钢丝出料门a使裂解钢丝落入四-5.钢丝出料门b,并关闭四-3.钢丝出料门a,使该部分区域形成密闭空间;
进一步的,此时抽真空装置开始工作,裂解气体经过四-4.真空泵出气口,进入四-1.真空泵入气口后重新进入裂解反应器内,防止了裂解气体外泄引发的环境污染和安全事故,该封闭区域的裂解气体取完毕后,打开四-5.钢丝出料门b,使裂解钢丝进入四-7.钢丝运输输送带,在输送带的运动下将裂解钢丝输送到指定位置。
优选的,由于裂解钢丝的刚性,增加了运输过程的难度,使其在输送过程中极易发生堵塞,为了及时解决钢丝堵塞问题;在该部分开设了四-2.裂解钢丝输送检修口,四-6.钢丝输送检修口,便于及时检修装备,从而实现裂解钢丝的输送。
经过固相产物分离系统后裂解炭黑经五-1蝶阀落入五-2裂解炭黑一级输送机构中,经过五-3裂解炭黑二级输送机构及后续的输送系统进入裂解炭黑收集仓,该部分的具体结构已申请相关专利,具体见(cn201820668702.0一种废橡胶或废塑料的裂解残渣连续输出装置,cn201810427508.8一种废橡胶或废塑料的裂解残渣连续输出装置和方法)此部分不在详细讲述。
本发明涉及一种废轮胎整胎工业连续化裂解固相产物自动分离方法,包括以下步骤:
1)废旧轮胎经过烘烤,即在100℃环境下停留3~5分钟后由输送带将其连续运输到一、异型双锥连续进料系统通过异型双锥螺杆结构实现废轮胎的整胎吃入,持续进入裂解反应器主体系统二;
2)裂解反应器主体系统二在燃烧供热系统九的作用下维持温度在450℃~500℃之间,进入裂解反应器主体系统二的废轮胎整体在该温度下持续分解,产生的气体组分在风机的作用下,通过裂解油品等级自动收集系统六冷凝收集;
3)未能冷凝的不凝可燃气体通过裂解不凝可燃气回用系统八处理后重新作为燃料提供给燃烧供热系统九为系统供热;
4)废轮胎进入裂解反应釜后在裂解反应器主体系统二下的裂解反应釜内的螺旋结构的作用下向前运动,直至运动到裂解固相产物分离系统三处,此时废轮胎已经全部分解完毕,只剩下裂解炭黑和钢丝;
5)在裂解固相产物分离系统三的作用下分离,裂解钢丝经过钢丝输送系统四输送到钢丝收集装置中;
6)裂解炭黑经过裂解炭黑连续输出系统五收集到裂解炭黑收集仓中;
7)燃烧供热系统九产生的尾气经过模块化分布式智能尾气综合处理系统七处理后排放。
本发明的技术方案至少具有如下优点和有益效果:
1.本发明能实现废轮胎整胎裂解过程中裂解炭黑与钢丝的自动分离和连续输出,从而解决废轮胎整胎工业连续化裂解时裂解固相产物无法连续输出的难题,实现了废轮胎整胎工业连续化裂解,降低裂解过程轮胎破碎的能源消耗,实现废轮胎整胎连续、高效、安全裂解。。
2.本发明解决了废轮胎整胎连续化裂解过程中轮胎带束层、胎体中的钢丝保持完整,传统的分离、输送方法及装置无法完成钢丝与裂解炭黑的分离及输送,导致目前行业内一直未出现整胎连续化裂解装备的技术问题。
3.本发明解决了废轮胎裂解主要以间歇式裂解和废旧轮胎破碎式裂解为主,其中间歇式裂解存在裂解效率较低,工作劳动强度较大,智能化水平较低,需要额外提供轮胎破碎机,额外增加了废轮胎裂解的工序和能源的消耗等技术问题。
附图说明
图1为本发明的废轮胎整胎工业连续化裂解固相产物自动分离装备整体视图;
图2本发明方案一固相产物分离系统结构示意图;
图3为本发明方案一固相产物分离系统传动关系图;
图4为本发明方案一固相分离系统轴系结构图;
图5为本发明方案一传动轴承上半部分视图;
图6为本发明方案二废轮胎整胎连续化裂解固相产物分离系统的主体结构视图;
图6(a)为总体标号,图6(b)为分标号。
图7为本发明方案二固相分离部分总体图;
图8为本发明方案二固相分离部分工作区域划分图;
图9为本发明方案二第一分离叶片图;
图10为本发明方案二第二分离输送叶片图;
其中,附图标记对应的零部件名称如下:
一、异型双锥连续进料系统,二、裂解反应器主体系统,三、裂解固相产物分离系统,四、钢丝输送系统,五、裂解炭黑连续输出系统,六、裂解油品等级自动收集系统,七、模块化分布式智能尾气综合处理系统,八、裂解不凝可燃气回用系统,九、燃烧供热系统;
固相产物分离区域ⅰ:第一工作区域;钢丝输送区域ⅱ:第二工作区域;其中ⅰ与ⅱ区域的划分是以挡板为界;
1.挡板,2.筛网;
四-1.真空泵入气口,四-2.裂解钢丝输送检修口,四-3.钢丝出料门a,四-4.真空泵出气口,四-5.钢丝出料门b,四-6.钢丝输送检修口,四-7.钢丝运输输送带;
二-1高温烟气加热腔,二-2裂解反应釜,二-3从动轮,二-4链条,二-5电机减速器,二-6动环密封,12密封组件,13轴承组件,14机架,五-1蝶阀,五-2裂解炭黑一级输送机构,五-3裂解炭黑二级输送机构;
3.中空固定支撑柱,4焊接板,5.固相产物分离叶片,6.固相产物分离叶片夹板,7.钢丝输送叶片夹板,8.钢丝输送叶片,9.传动轴承组件,10.支撑轴承组件,11传动轴;
9-1外壳,9-2滑动轴套;
方案二中:ⅰ固相产物分离部分,ⅱ裂解炭黑分离输送机构,ⅲ钢丝分离输送部件;
1.分离叶片,2.轴承,3.分离部分筒体,4.传动轴,5.挡板,6.筛网,7.闸阀,8.裂解炭黑输送机构,9.真空泵入气口,10.裂解钢丝输送检修口,11.钢丝出料门a,12.真空泵出气口,13.钢丝运输输送带,14.钢丝输送检修口部件,15.钢丝出料门b;
16.传动部分检修口部件,a是六裂解油品等级自动收集系统的接口,b是五裂解炭黑连续输出系统的接口,c是四钢丝输送系统的接口;
ⅰ—1固相分离第一工作区域,ⅰ—2固相分离第二工作区域;
1-1固相分离第一工作区域分离叶片工作面,1-2固相分离第一工作区域分离叶片非工作面;
1-3固相分离第二工作区域分离叶片工作面,1-4固相分离第二工作区域分离叶片非工作面;
具体实施方式
下面结合附图和具体实施例对本发明进行说明。
为使本发明实施例的目的、技术方案和优点更加清楚,下面将结合附图,对本发明实施例中的技术方案进行清楚、完整的描述。显然,所描述的实施例是本发明的一部分实施例,而不是全部的实施例。
因此,以下对本发明的实施例的详细描述并非旨在限制要求保护的本发明的范围,而是仅仅表示本发明的部分实施例。基于本发明中的实施例,本领域普通技术人员在没有作出创造性劳动前提下所获得的所有其他实施例,都属于本发明保护的范围。
应注意到:相似的标号和字母在下面的附图中表示类似项,因此,一旦某一项在一个附图中被定义,则在随后的附图中不需要对其进行进一步定义和解释。
在本发明的描述中,需要说明的是,术语“中心”、“上”、“下”、“左”、“右”、“竖直”、“水平”、“内”、“外”、“背面”等指示的方位或位置关系为基于附图所示的方位或位置关系,或者是该发明产品使用时惯常摆放的方位或位置关系。这类术语仅是为了便于描述本发明和简化描述,而不是指示或暗示所指的装置或元件必须具有特定的方位、以特定的方位构造和操作,因此不能理解为对本发明的限制。
还需要说明的是,在本发明的描述中,除非另有明确的规定和限定,术语“设置”、“安装”、“相连”、“连接”应做广义理解,例如,可以是固定连接,也可以是可拆卸连接,或一体地连接;可以是机械连接,也可以是电连接;可以是直接相连,也可以通过中间媒介间接相连,可以是两个元件内部的连通。对于本领域技术人员而言,可以根据具体情况理解上述术语在本发明中的具体含义。
如图1-5所示,一种废轮胎整胎工业连续化裂解固相产物自动分离装备,包括通过连接部件相连的异型双锥连续进料系统一、裂解反应器主体系统二、裂解固相产物分离系统三、钢丝输送系统四、裂解炭黑连续输出系统五、裂解油品等级自动收集系统;六、模块化分布式智能尾气综合处理系统七、裂解不凝可燃气回用系统八,燃烧供热系统九以及催化裂解智能控制系统等,能够实现废轮胎整胎裂解过程中裂解固相产物的分离。裂解装备整体如图1所示。
作为本发明一个优选的实施例,本发明涉及一种废轮胎整胎工业连续化裂解固相产物自动分离方法,包括以下步骤:
1.废旧轮胎(以轿车轮胎为主)经过烘烤(一般在100℃环境下停留3~5分钟)后由输送带将其连续运输到(一、异型双锥连续进料系统)通过异型双锥螺杆结构实现废轮胎的整胎吃入,持续进入(二、裂解反应器主体系统);
2.(二、裂解反应器主体系统)在(九、燃烧供热系统)的作用下维持温度在450℃~500℃之间,通过(二、裂解反应器主体系统)中的(二-1高温烟气加热腔)为(二-2裂解反应釜)持续供热,废轮胎整体在该温度下持续分解,产生的气体组分在风机的作用下,通过(六、裂解油品等级自动收集系统)冷凝收集;
3.未能冷凝的不凝可燃气体通过(八、裂解不凝可燃气回用系统)处理后重新作为燃料提供给(九、燃烧供热系统)为系统供热;
4.废轮胎进入裂解反应釜后在(二裂解反应器主体系统下的裂解反应釜)内的螺旋结构的作用下向前运动,直至运动到(三、裂解固相产物分离系统)处,此时废轮胎已经全部分解完毕,只剩下裂解炭黑和钢丝;
5.在(三、裂解固相产物分离系统)的作用下分离,裂解钢丝经过(四、钢丝输送系统)输送到钢丝收集装置中;
6.裂解炭黑经过(五、裂解炭黑连续输出系统)收集到裂解炭黑收集仓中;
7.(九、燃烧供热系统)产生的尾气经过(七、模块化分布式智能尾气综合处理系统)处理后排放。
本发明针对废轮胎整胎裂解过程中裂解固相产物(裂解炭黑与钢丝)无法分离,从而发明了(三、裂解固相产物分离系统);
因为废轮胎没有经过破碎,保持了钢丝的完整性,并且裂解钢丝在废轮胎裂解过程中会由于裂解反应炉的转动相互缠结,缠结的过程中又会夹杂很多裂解炭黑,进一步加剧了裂解炭黑和钢丝的分离难度,并且传统的输送机构都无法实现对大块钢丝密闭、连续输送的需求,从而导致废轮胎整胎裂解无法实现连续化,为此,本发明专利研发了废轮胎整胎工业连续化裂解固相产物自动分离方法及装置,目标在于解决废轮胎整胎裂解过程中裂解炭黑与钢丝的分离及固相裂解产物在输送过程中的密封两个问题。
进一步的,具体方法如下:一种废轮胎整胎工业连续化裂解固相产物自动分离方法,包括以下步骤:
废旧轮胎在(二、裂解反应器主体系统下的二-2裂解反应釜)中的螺旋作用下由进料端向反应釜末端移动,在裂解温度的作用下废旧轮胎中的有机高分子材料分解完全;
剩下裂解炭黑与裂解钢丝,待在(二、裂解反应器主体系统下的二-2裂解反应釜)进一步干燥后输送到(三、裂解固相产物分离系统)中,此部分位于(二、裂解反应器主体系统下的二-2裂解反应釜)的末端,内无内螺旋结构,固相产物运动主要是通过(二、裂解反应器主体系统下的二-2裂解反应釜)中部的螺旋结构运输的物料逐渐堆积向前推动固相产物移动;
并且(三、裂解固相产物分离系统)在废轮胎裂解过程中保持静止不动,底部设有异型孔道,在孔道上安装30-60目的筛网,底部与五、裂解炭黑连续输出系统相连,使裂解炭黑通过筛网进入裂解炭黑输送系统中。但由于在裂解过程中钢丝会随着裂解反应釜的回转运动逐渐成团,其中会夹杂大量的裂解炭黑,增加了裂解炭黑与钢丝的分离难度。
本发明为此研发了图4中的5固相产物分离叶片及图4中的8钢丝输送叶片,并且5固相产物分离叶片与8钢丝输送叶片中间有高度为50~65mm挡板(图2中的1),从而使裂解钢丝在输送过程中必须跨过中间的1挡板(以挡板为介划分为固相产物分离区域ⅰ也称第一工作区域,和钢丝输送区域ⅱ也称第二工作区域);
作为本发明一个优选的实施例,为使钢丝由固相产物分离区域ⅰ运动到钢丝输送区域ⅱ中,此过程必须要通过5固相产物分离叶片来实现,此特殊设计的5固相产物分离叶片结构的具体特征为:分离叶片沿横向中心线扭转15~20°,沿着纵向扭转35~45°,分离叶片右侧底部上翘3~8°。
作为本发明一个优选的实施例,具体分离叶片方程如下所述:
第一步:在直角坐标系形成平面结构:
f(x,y,z)=ax by cz
其中,a值范围与钢丝由固相产物分离区域ⅰ长度l有关,b值的范围需要根据反应釜直径d尺寸来确定,其中,a=1.1~1.3l,b=0.6~0.7d
第二步:平面沿着
其中,θ为15~20°最为适宜
第三步:上述曲面结构沿着
其中,σ为35~45°最为适宜
第四步:上述平面沿x0y平面向z轴正方向扭转角度
其中,
作为本发明一个优选的实施例,(5固相产物分离叶片)呈半圆形设计,底部上翘,对称安装在固相分离系统图4中11传动轴上,随着11传动轴的转动而运动,并且在转动过程中通过上翘部分将裂解钢丝从第一工作区域(固相产物分离区域ⅰ)输送到第二工作区域(钢丝输送区域ⅱ)中,在输送过程中会使裂解钢丝团一直处于滚动过程中,从而使夹杂在裂解钢丝中的裂解炭黑逐渐漏出,实现了夹杂在钢丝团中的炭黑与钢丝分离;
进一步的,在5固相产物分离叶片底部开设矩形槽;使钢丝在运动过程中漏出的裂解炭黑通过5固相产物分离叶片底下的槽空间漏出,在通过底部的筛网进入(五、裂解炭黑连续输出系统,在图1中的第五部分)中。
作为本发明一个优选的实施例,在5固相产物分离叶片的作用下,裂解钢丝从第一工作区域(固相产物分离区域ⅰ)输送到第二工作区域(钢丝输送区域ⅱ)中,此时基本上已经实现了夹杂在钢丝团中的裂解炭黑与钢丝的分离;
为了确保裂解炭黑与钢丝的彻底分离,在第二工作区域((钢丝输送区域ⅱ)底部仍然设有孔道,并且与第一工作区域(固相产物分离区域ⅰ)的孔道相连,并且通过8钢丝输送叶片在带动钢丝团运动过程中实现内部裂解炭黑的进一步漏出,并通过底部的筛网结构进入(五、裂解炭黑连续输出系统)中。
作为本发明一个优选的实施例,为了实现裂解钢丝在第二工作区域((钢丝输送区域ⅱ)中的运动,发明了特殊的8钢丝输送叶片,该叶片主要实现钢丝的输送,具体特征为:分离叶片沿横向弯曲25~35°(弯曲角度主要与反应釜直径相关,直径较大的情况下选取小角度弯曲),弯曲的凸起方向为钢丝分离叶片的工作面,通过其凸起推动裂解钢丝运动,并且钢丝输送叶片底部开设矩形槽,给漏出的裂解炭黑留有移动通道。
作为本发明一个优选的实施例,8钢丝输送叶片对称安装在固相分离系统11传动轴上,随着传动轴的转动而运动,其中8钢丝输送叶片与5固相产物分离叶片呈90°角度安装,其中8钢丝输送叶片与5固相产物分离叶片都是通过夹板式螺栓连接在11传动轴上,避免焊接带来的应力集中使分离曲面运动过程中出现扭断的事故。
作为本发明一个优选的实施例,11传动轴的动力源来自于裂解反应釜(二、裂解反应器主体系统下的二-2裂解反应釜)的回转运动,无需外接动力源,二-2裂解反应釜通过二-4链条与二-5电机减速器相连,实现了外部电机在带动二-2裂解反应釜运动的同时也带动了5固相产物分离叶片的运动,具体结构如图3所示;
作为本发明一个优选的实施例,在上述结构中,二-5电机减速器将动力源通过二-4链条传递到二-3从动轮上,二-3从动轮与二-2裂解反应釜焊接固定,从而实现二-2裂解反应釜的回转运动,二-2裂解反应釜通过内部结构在将动力源传递到分离叶片上;
为了实现上述特征,研发了固相分离轴系结构,该结构通过4焊接板与二-2裂解反应釜焊接固定,轴系末端通过13轴承组件支撑,并通过12密封组件实现轴系结构与二-2裂解反应釜的密封,具体的连接关系如下所述:
作为本发明一个优选的实施例,3.中空固定支撑柱与4焊接板焊接到一起,为了便于安装,将4焊接板设计成u字型开口结构,通过4焊接板的背面与裂解反应釜焊接固定;3.中空固定支撑柱另一侧与9.传动轴承组件的9-1外壳焊接固定,为了便于安装和焊接,9-1外壳的焊接位置设计成槽型结构,在安装过程中先将3.中空固定支撑柱与9-1外壳焊接,然后再将3.中空固定支撑柱与4焊接板焊接,最后再将4焊接板与二-2裂解反应釜焊接;
作为本发明一个优选的实施例,9.传动轴承组件是由9-1外壳,9-2滑动轴套上下两部分组成,其安装关系为:9-1外壳、9-2滑动轴套与11传动轴通过定位销定位后,用4个螺钉从9-1外壳外部将9-2滑动轴套紧固,然后与9.传动轴承组件的下部分配合固定在11传动轴的相应位置;
进一步的,与此同时,9-2滑动轴套与11传动轴之间有严格的尺寸要求,其配合间隙在3~5mm之间,在高温的裂解反应条件下,该尺寸会在9-2滑动轴套的热膨胀下消失,并使9-2滑动轴套紧紧的紧固到11传动轴上,在加上上、下两个定位销贯穿9-1外壳、9-2滑动轴套、11传动轴,在两者的作用下使动力源由二-2裂解反应釜经过4焊接板、3.中空固定支撑柱、9.传动轴承组件传递到了11传动轴上,实现了11传动轴无需直连电机的传动。
作为本发明一个优选的实施例,整个固相分离区域较长,为了防止11传动轴在二-2裂解反应釜的带动过程中出现扭转导致11传动轴与12密封组件、13轴承组件不同心,导致无法运动的情况,研发了10.支撑轴承组件。
其连接关系为:3.中空固定支撑柱与10.支撑轴承组件外壳焊接,然后再将3.中空固定支撑柱与4焊接板焊接,最后再将4焊接板与二-2裂解反应釜焊接;
进一步的,10.支撑轴承组件与9.传动轴承组件结构相似,其中10.支撑轴承组件的外壳和9-2滑动轴套通过定位销定位后,用4个螺钉从外壳外部将9-2滑动轴套紧固,在与下部分配合固定在11传动轴的相应位置,与此同时,9-2滑动轴套与11传动轴之间有严格的尺寸要求,其配合间隙在15~20mm之间,避免高温情况下,滑动轴套热膨胀紧固到11传动轴上,同时,此时的定位销只是定位10.支撑轴承组件的外壳和滑动轴套,并没有贯穿11传动轴,从而实现了10.支撑轴承组件知识支撑11传动轴,并未紧固在11传动轴上。
进一步的,为了保障上述传动过程的长久性,11传动轴在9.传动轴承组件和10.支撑轴承组件相配合位置其直径尺寸与其他传动轴位置相比直径较大,并且喷涂硬质合金,其硬质合金厚度在3~5mm,增加其表面硬度,使其在9.传动轴承组件和10.支撑轴承组件位置的磨损以9-2滑动轴套为主。
作为本发明一个优选的实施例,在整个固相产物分离系统中要严格保证密封性,不能使产生的裂解气体外泄,也不能使空气进入裂解反应釜内引发安全事故,因此,通过二-6动环密封内的石墨盘根将二-2裂解反应釜与(三、裂解固相产物分离系统)密封成整体,防止外泄;同时,11传动轴与三、裂解固相产物分离系统的密封主要通过12密封组件内的石墨盘根来达到密封的效果。
进一步的,11传动轴的末端安装13轴承组件,其内安装双列圆锥辊子轴承,保证11传动轴的回转运动,13轴承组件固定在14机架上。
经过三、裂解固相产物分离系统后裂解钢丝在8.钢丝输送叶片的推动作用下进入(四、钢丝输送系统中),该部分主要由四-1.真空泵入气口,四-2.裂解钢丝输送检修口,四-3.钢丝出料门a,四-4.真空泵出气口,四-7.钢丝运输输送带,四-6.钢丝输送检修口,四-5.钢丝出料门b等部件构成。
作为本发明一个优选的实施例,由于裂解钢丝成刚性,并且成团,使其无法连续输送,本发明装置研发“抽屉式裂解钢丝输送方法及装置”:
裂解钢丝进入(四、钢丝输送系统中)后先落入四-3.钢丝出料门a上方,待一段时间后(根据裂解工艺具体确定,一般为2~5min最为适宜),打开四-3.钢丝出料门a使裂解钢丝落入四-5.钢丝出料门b,并关闭四-3.钢丝出料门a,使该部分区域形成密闭空间;
进一步的,此时抽真空装置开始工作,裂解气体经过四-4.真空泵出气口,进入四-1.真空泵入气口后重新进入裂解反应器内,防止了裂解气体外泄引发的环境污染和安全事故,该封闭区域的裂解气体取完毕后,打开四-5.钢丝出料门b,使裂解钢丝进入四-7.钢丝运输输送带,在输送带的运动下将裂解钢丝输送到指定位置。
作为本发明一个优选的实施例,由于裂解钢丝的刚性,增加了运输过程的难度,使其在输送过程中极易发生堵塞,为了及时解决钢丝堵塞问题;在该部分开设了四-2.裂解钢丝输送检修口,四-6.钢丝输送检修口,便于及时检修装备,从而实现裂解钢丝的输送。
经过固相产物分离系统后裂解炭黑经五-1蝶阀落入五-2裂解炭黑一级输送机构中,经过五-3裂解炭黑二级输送机构及后续的输送系统进入裂解炭黑收集仓,该部分的具体结构已申请相关专利,具体见(cn201820668702.0一种废橡胶或废塑料的裂解残渣连续输出装置,cn201810427508.8一种废橡胶或废塑料的裂解残渣连续输出装置和方法)此部分不在详细讲述。
[方案二]
如图6-10所示,由于裂解过程中钢丝成团,犹如一个大“毛线”团,在团中会夹杂大量的裂解炭黑,在分离叶片的不断旋转运动中,成团的钢丝也会不停转动,并且通过该叶片的弧度及叶片与裂解反应器的间隙使夹杂在钢丝中的裂解炭黑流出,通过第一工作区域的6.筛网最终落入8.裂解炭黑输送机构。
本发明的废轮胎整胎工业连续化裂解固相产物自动分离装备的3裂解固相产物分离系统的具体结构如图6所示:
作为本发明一个优选的实施例,所述废轮胎整胎工业连续化裂解固相产物自动分离装备的裂解固相产物分离系统包络固相产物分离部分ⅰ、裂解炭黑分离输送ⅱ、钢丝分离输送部件ⅲ三大部分。
其中,ⅰ固相产物分离部分主要实现裂解炭黑与钢丝的连续高效分离功能,包括1.分离叶片,2.轴承,3.分离部分筒体,4.传动轴,5.挡板,6.筛网,16.传动部分检修口部件;
ⅱ裂解炭黑分离输送部分主要实现裂解炭黑的连续输出,同时保证输出过程中密封,使废旧轮胎裂解过程中外部空气无法通过裂解炭黑输送部分进入裂解反应器;
包括7.闸阀,8.裂解炭黑输送机构;
ⅲ钢丝分离输送部件主要实现裂解钢丝的输送,同时保证裂解钢丝输出过程中密封,使废旧轮胎裂解过程中外部空气无法通过裂解钢丝输送部分进入裂解反应器;
包括9.真空泵入气口,10.裂解钢丝输送检修口,11.钢丝出料门a,12.真空泵出气口,13.钢丝运输输送带,14.钢丝输送检修口部件组成。
各部分的工作原理:
ⅰ固相产物分离部分:
固相产物分离系统的传动轴4与裂解反应器焊接,依靠裂解反应器的回转运动带动ⅰ固相产物分离部分的转动,该部分划分为两个区域(如图2);
ⅰ—1固相分离第一工作区域,ⅰ—2固相分离第二工作区域,两个区域之间通过5.挡板分离,ⅰ—1固相分离第一工作区域主要是通过1.分离叶片实现裂解炭黑与钢丝的分离,该叶片具体结构如图6所示,此时裂解炭黑分离叶片经过特殊的曲面设计,叶片工作面前段呈现一定的曲面,具体曲面方程如方案一所示:
本发明的1分离叶片呈半圆形设计,底部上翘,在转动过程中通过上翘部分将裂解钢丝从ⅰ—1第一工作区域输送到ⅰ—2第二工作区域中,由于裂解过程中钢丝成团,犹如一个大“毛线”团,在团中会夹杂大量的裂解炭黑,在分离叶片的不断旋转运动中,成团的钢丝也会不断转动,并且通过该叶片的弧度及叶片与裂解反应器的间隙使夹杂在钢丝中的裂解炭黑流出,通过第一工作区域的6.筛网最终落入8.裂解炭黑输送机构。
ⅰ—2固相分离第二工作区域主要实现裂解钢丝的输送,及部分残渣炭黑的输送。此部分的叶片设计如图7所示,是将ⅰ—1第一工作区域中的1分离叶片反向安装,其工作面与ⅰ—1第一工作区域刚好相反,通过1分离叶片的背面推动裂解钢丝进入ⅲ钢丝分离输送部件中,并且在5.挡板的作用下,阻止了钢丝向第一工作区域的反向流动,同时在该区域叶片的旋转运动带动下,夹杂在钢丝中的炭黑会进一步漏出,最后经过6.筛网落入8.裂解炭黑输送机构。
ⅱ裂解炭黑分离输送机构:
经过固相产物分离系统后裂解炭黑落入8.裂解炭黑输送机构中,通过该部分实现裂解炭黑的连续化输送,该部分的具体结构已申请相关专利,具体见(cn201820668702.0一种废橡胶或废塑料的裂解残渣连续输出装置,cn201810427508.8一种废橡胶或废塑料的裂解残渣连续输出装置和方法)此部分不在详细讲述。
ⅲ钢丝分离输送部件:
经过固相产物分离系统后裂解钢丝在分离叶片的推动作用下进入ⅲ钢丝分离输送部件中,该部分包括9.真空泵入气口,10.裂解钢丝输送检修口,11.钢丝出料门a,12.真空泵出气口,13.钢丝运输输送带,14.钢丝输送检修口部件,15.钢丝出料门b部件。
由于裂解钢丝成刚性,并且成团,使其无法连续输送,本发明装置研发“抽屉式裂解钢丝输送方法及装置”,裂解钢丝进入ⅲ钢丝分离输送部件后先落入11.钢丝出料门a上方,待一段时间后(根据裂解工艺具体确定,一般为2~5min最为适宜),打开11.钢丝出料门a使裂解钢丝落入15.钢丝出料门b,并关闭11.钢丝出料门a,使该部分区域形成密闭空间,此时抽真空装置开始工作,裂解气体经过12.真空泵出气口,进入9.真空泵入气口后重新进入裂解反应器内,防止了裂解气体外泄引发的环境污染和安全事故;
该封闭区域的裂解气体取完毕后,打开15.钢丝出料门b,使裂解钢丝进入13.钢丝运输输送带,在输送带的运动下将裂解钢丝输送到指定位置,由于裂解钢丝的刚性,增加了运输过程的难度,使其在输送过程中极易发生堵塞,为了及时解决钢丝堵塞问题,在该部分开设了10.裂解钢丝输送检修口,14.钢丝输送检修口部件,便于及时检修装备。从而实现裂解钢丝的输送。
以上实施方案仅用于说明而非限制本发明的技术方案。不脱离本发明精神的任何修改或局部替换,均应涵盖在本发明的权利要求范围当中。
本文用于企业家、创业者技术爱好者查询,结果仅供参考。