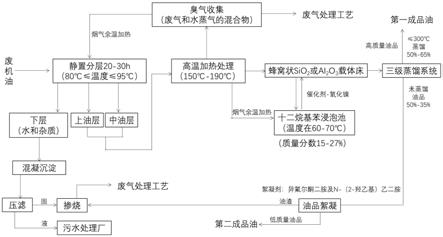
本发明属于废机油纯化技术领域,具体涉及一种废机油的工业纯化方法。
背景技术:
机油在使用的过程中由于受高温及空气的氧化作用,产生多种氧化物,再加上磨擦部件磨下来的金属粉末,呼吸作用及其它原因而进入油中的水分、灰尘,最终导致机油的颜色逐渐变黑,粘度降低,品质下降,且在使用过程中产生的沉淀物、油泥、漆膜和硬漆膜等杂质可能造成油膜的破坏,金属部件的腐蚀,运动器件的磨损,从而造成调速系统卡涩、失灵,造成设备的损坏,因此必须经常更换机油。废机油再生技术的开发对节约资源有重要的意义,同时能产生很好的经济效益。
近年来废机油的再生技术主要有:酸碱精制工艺、溶剂精制工艺、加氢精制工艺、分子蒸馏工艺和膜处理技术,其中硫酸-白土工艺技术最成熟,但该工艺对白土需求量很大,会生成严重的三废问题,对环境有着极大的污染,故该工艺逐渐被溶剂精制和加氢处理所替代;比如在专利cn104004543a中,提供了一种废机油催化提质再生的方法,专利中将废机油进行减压蒸馏,后经硫化物催化剂加氢提质,通过脱硫、脱氮、脱氧、除胶质生产得无异味、品质高的汽柴油和机油混合油,再经蒸馏得到汽、柴油和成品机油馏分油;废机油纯化过程中,不仅处理工艺复杂,增加耗能,污染环境,而且缺少对油渣的处理,使油渣无法得到有效的利用。
技术实现要素:
针对现有技术存在的上述问题,本申请提供了一种废机油的工业纯化方法,通过精准的温度控制和蒸馏技术,结合环节中的蒸馏前催化工艺加速纯化和油品絮凝工序,可快速降低废机油粘度和密度,并通过创新手段减少残碳、提高十六烷值指数,而且处理工艺简单,废油回收率高,能满足大规模工艺生产的需要。
本发明提供如下技术方案:一种废机油的工业纯化方法,包括以下步骤:
1)将废机油置于温度为80℃~95℃恒温油罐中,静置20h~30h,所述废机油分层得到上油层、中油层和下层,所述下层包括水和杂质,通过混凝沉淀和压滤工序,完成固液分离。
2)将所述步骤1)得到的所述上油层和所述中油层进行加热处理,加热温度为150℃~190℃,加热后得到混合油和气体混合物,所述气体混合物包括臭气和水蒸气,所述气体混合物经收集后进入废气处理工艺;
3)将所述步骤2)加热处理后得到的混合油引入催化剂载体床中,经催化剂催化处理得到待纯化油;
4)将所述步骤3)得到的待纯化油引入三级蒸馏塔中,蒸馏出沸点小于300℃的三种馏分混合物,经冷凝分离得到第一成品油,第一成品油的收率为50%~65%;
5)将所述步骤4)蒸馏塔的底油进入絮凝工序,之后静置沉淀2h~4h,分离出第二成品油和油渣,第二成品油的收率为30%~35%。
优选地,所述步骤3)中的催化剂载体床包括载体床和负载在载体床上的氧化镍颗粒,所述氧化镍粒径为1mm~3mm。
优选地,所述载体床按照以下重量份数组成:活性氧化铝30~40份,纳米多孔二氧化硅10~20份,碳化硅8~15份,高岭土5~12份,白云石3~6份,田菁粉2~5份;
所述活性氧化铝的孔容为0.2ml/g~1.2ml/g,孔径为2.0nm~11.0nm,比表面积为200m2/g~380m2/g;
所述纳米多孔二氧化硅的孔容为0.2ml/g~2.5ml/g,孔径为2nm~100nm,比表面积为220m2/g~450m2/g。
优选地,所述载体床的制备方法为:
步骤一:按比例称取各原料后,将原料与占原料总重量20%~30%的水混合,混合均匀后投入混炼机中混炼30min~120min制备得到泥料;
步骤二:将泥料放置于蜂窝钢模具中,设置压力为10mpa~15mpa,通过模压成型制得蜂窝状载体坯体;
步骤三:将蜂窝状载体坯体在110℃~130℃条件下干燥20h~24h,之后将干燥好的蜂窝状载体坯体以30℃/h~40℃/h的升温速率,升温至1200℃~1300℃进行烧成12h~18h,即可制得具有蜂窝状结构的载体床。
优选地,所述步骤3)中的催化剂载体床在使用前需经活性处理,所述活性处理方法为:将催化剂载体置于60℃~70℃的十二烷基苯浸泡池中处理1h~5h,十二烷基苯质量分数为15%~27%,然后经洗涤、分离、干燥即得所需的催化剂载体床,其中十二烷基苯与所述氧化镍催化剂的质量比为1:0.1~0.25。
优选地,所述步骤4)的三级蒸馏塔为常压蒸馏,所述蒸馏塔的温度由上到下依次设置为150℃~175℃、175℃~260℃和260℃~300℃。
优选地,所述步骤5)的絮凝工序为:将体积比为10%~20%的絮凝剂溶液按剂油体积比为1:20~50的比例加入蒸馏塔底油中,温度为60℃~90℃,搅拌8min~20min。
优选地,所述絮凝剂溶液为絮凝剂溶解于甲苯中制得,所述絮凝剂为异佛尔酮二胺、n-(2-羟乙基)乙二胺、n-苯基二乙醇胺和二乙撑三胺中的一种或多种。
优选地,所述步骤2)产生的烟气余温供所述步骤1)中的静置分层工序和催化剂载体床活性处理工序完成余温加热,实现能量回收。
优选地,所述步骤1)固液分离得到的液体被引入进入污水处理工序,固体与所述步骤5)静置沉淀得到的油渣混合掺烧,掺烧产生的废气进入尾气处理工序。
本发明有益的技术效果在于:
(1)本发明通过精准的温度控制和蒸馏技术,结合环节中的蒸馏前催化工艺加速纯化和油品絮凝工序,整个流程达到工艺方法的创新,此工艺流程可快速降低废机油粘度和密度,并通过创新手段减少残碳、提高十六烷值指数,而且处理工艺简单,废油回收率高,不低于80%,能满足大规模工艺生产的需要。
(2)本发明采用脂肪族胺类作为絮凝剂,一方面脂肪族胺类的氨基基团可以和废机油中的氧化基团形成氢键,并中和酸性基团,另一方面,脂肪族胺类的交联性能可吸附胶体微粒,使废机油中的杂质颗粒聚集沉降,从而快速降低蒸馏塔底油的酸值、粘度和密度,加快机械杂质的沉降速度,进而提高第二成品油的质量。
(3)本发明的活性组分为活性氧化铝和纳米多孔二氧化硅,由于活性氧化铝和纳米多孔二氧化硅的多孔结构,使得它们有很大的表面积,其微孔表面具备催化作用所要求的特性,如吸附性能、表面活性、优良的热稳定性等。
(4)本发明的载体床采用蜂窝状结构,蜂窝载体孔隙率大、吸附能力强,能够负载更多的催化活性组分,而且选择活性氧化铝和纳米多孔二氧化硅作为活性组分,使得催化剂载体床同时具有微孔、中孔、大孔或超大孔,增大了催化剂与废机油的接触面积,在相同的空间内具有更高的催化效果。
(5)本发明采用十二烷基苯对催化剂载体床进行活性处理,主要考虑到十二烷基苯作为表面活性剂,可降低水的表面张力,改变固液界面的润湿角,能够促使更多的氧化镍颗粒进入载体床内部孔隙中,从而有效提高催化剂载体床的催化能力。
附图说明
图1为本发明提供的一种废机油工业纯化方法的流程图。
下面结合附图和实施例,对本发明进行具体描述,显然,所描述的实施例仅是本发明一部分实施例,而不是全部的实施例,基于本发明中的实施例,本领域普通技术人员在没有做出创造性劳动前提下所获得的所有其他实施例,都属于本发明保护的范围。
以下结合具体优选实施例对本发明一种废机油工业纯化的方法进行详细阐述。
实施例1:
本实施例提供了一种废机油工业纯化的方法,包括如下步骤:
1)将废机油置于温度为95℃恒温油罐中,静置20h,所述废机油分层得到上油层、中油层和下层,所述下层包括水和杂质,通过混凝沉淀和压滤工序,完成固液分离。
2)将所述步骤1)得到的所述上油层和所述中油层进行加热处理,加热温度为150℃,加热后得到混合油和气体混合物,所述气体混合物包括臭气和水蒸气,所述气体混合物经收集后进入废气处理工艺;
3)将所述步骤2)加热处理后得到的混合油引入催化剂载体床中,经催化剂催化处理得到待纯化油;
4)将所述步骤3)得到的待纯化油引入三级蒸馏塔中,蒸馏出沸点小于300℃的三种馏分混合物,经冷凝分离得到第一成品油,第一成品油的收率为65%;
5)将所述步骤4)蒸馏塔的底油进入絮凝工序,之后静置沉淀2h,分离出第二成品油和油渣,第二成品油的收率为30%。
优选地,所述步骤3)中的催化剂载体床包括载体床和负载在载体床上的氧化镍颗粒,所述氧化镍的粒径为1mm。
优选地,所述载体床按照以下重量份数组成:活性氧化铝40份,纳米多孔二氧化硅20份,碳化硅8份,高岭土5份,白云石6份,田菁粉5份;
所述活性氧化铝的孔容为0.2ml/g,孔径为2.0nm,比表面积为380m2/g;
所述纳米多孔二氧化硅的孔容为0.2ml/g,孔径为2nm,比表面积为450m2/g。
优选地,所述载体床的制备方法为:
步骤一:按比例称取各原料后,将原料与占原料总重量30%的水混合,混合均匀后投入混炼机中混炼120min制备得到泥料;
步骤二:将泥料放置于蜂窝钢模具中,设置压力为10mpa,通过模压成型制得蜂窝状载体坯体;
步骤三:将蜂窝状载体坯体在130℃条件下干燥20h,之后将干燥好的蜂窝状载体坯体以40℃/h的升温速率,升温至1300℃进行烧成12h,即可制得具有蜂窝状结构的载体床。
优选地,所述步骤3)中的催化剂载体床在使用前需经活性处理,所述活性处理方法为:将催化剂载体置于60℃的十二烷基苯浸泡池中处理5h,十二烷基苯的质量分数为15%,然后经洗涤、分离、干燥即得所需的催化剂载体床,其中十二烷基苯与所述氧化镍催化剂的质量比为1:0.25。
优选地,所述步骤4)的三级蒸馏塔为常压蒸馏,所述蒸馏塔的温度由上到下依次设置为150℃、175℃和260℃。
优选地,所述步骤5)的絮凝工序为:先将体积比为10%的异佛尔酮二胺絮凝剂溶液按剂油体积比为1:20的比例加入蒸馏塔底油中,温度为60℃,搅拌20min,再将体积比为20%的n-(2-羟乙基)乙二胺溶液按剂油体积比为1:50的比例加入蒸馏塔底油中,温度为90℃,搅拌8min。
优选地,所述步骤2)产生的烟气余温供所述步骤1)中的静置分层工序和催化剂载体床活性处理工序完成余温加热,实现能量回收。
优选地,所述步骤1)固液分离得到的液体被引入进入污水处理工序,固体与所述步骤5)静置沉淀得到的油渣混合掺烧,掺烧产生的废气进入尾气处理工序。
实施例2:
本实施例提供了一种废机油的工业纯化方法,包括以下步骤:
1)将废机油置于温度为80℃恒温油罐中,静置30h,所述废机油分层得到上油层、中油层和下层,所述下层包括水和杂质,通过混凝沉淀和压滤工序,完成固液分离。
2)将所述步骤1)得到的所述上油层和所述中油层进行加热处理,加热温度为190℃,加热后得到混合油和气体混合物,所述气体混合物包括臭气和水蒸气,所述气体混合物经收集后进入废气处理工艺;
3)将所述步骤2)加热处理后得到的混合油引入催化剂载体床中,经催化剂催化处理得到待纯化油;
4)将所述步骤3)得到的待纯化油引入三级蒸馏塔中,蒸馏出沸点小于300℃的三种馏分混合物,经冷凝分离得到第一成品油,第一成品油的收率为50%;
5)将所述步骤4)蒸馏塔的底油进入絮凝工序,之后静置沉淀2h~4h,分离出第二成品油和油渣,第二成品油的收率为35%。
优选地,所述步骤3)中的催化剂载体床包括载体床和负载在载体床上的氧化镍颗粒,所述氧化镍粒径为3mm。
优选地,所述载体床按照以下重量份数组成:活性氧化铝30份,纳米多孔二氧化硅10份,碳化硅15份,高岭土12份,白云石3份,田菁粉2份;
所述活性氧化铝的孔容为1.2ml/g,孔径为11.0nm,比表面积为200m2/g;
所述纳米多孔二氧化硅的孔容为2.5ml/g,孔径为100nm,比表面积为220m2/g。
优选地,所述载体床的制备方法为:
步骤一:按比例称取各原料后,将原料与占原料总重量20%的水混合,混合均匀后投入混炼机中混炼30min制备得到泥料;
步骤二:将泥料放置于蜂窝钢模具中,设置压力为15mpa,通过模压成型制得蜂窝状载体坯体;
步骤三:将蜂窝状载体坯体在110℃条件下干燥24h,之后将干燥好的蜂窝状载体坯体以30℃/h的升温速率,升温至1200℃进行烧成18h,即可制得具有蜂窝状结构的载体床。
优选地,所述步骤3)中的催化剂载体床在使用前需经活性处理,所述活性处理方法为:将催化剂载体置于70℃的十二烷基苯浸泡池中处理1h,十二烷基苯质量分数为27%,然后经洗涤、分离、干燥即得所需的催化剂载体床,其中十二烷基苯与所述氧化镍催化剂的质量比为1:0.1。
优选地,所述步骤4)的三级蒸馏塔为常压蒸馏,所述蒸馏塔的温度由上到下依次设置为175℃、260℃和300℃。
优选地,所述步骤5)的絮凝工序为:先将体积比为20%的n-(2-羟乙基)乙二胺絮凝剂溶液按剂油体积比为1:50的比例加入蒸馏塔底油中,温度为90℃,搅拌20min,再将体积比为10%的n-苯基二乙醇胺溶液按剂油体积比为1:20的比例加入蒸馏塔底油中,温度为60℃,搅拌8min。
优选地,所述步骤2)产生的烟气余温供所述步骤1)中的静置分层工序和催化剂载体床活性处理工序完成余温加热,实现能量回收。
优选地,所述步骤1)固液分离得到的液体被引入进入污水处理工序,固体与所述步骤5)静置沉淀得到的油渣混合掺烧,掺烧产生的废气进入尾气处理工序。
实施例3:
本实施例提供了一种废机油的工业纯化方法,包括以下步骤:
1)将废机油置于温度为85℃恒温油罐中,静置25h,所述废机油分层得到上油层、中油层和下层,所述下层包括水和杂质,通过混凝沉淀和压滤工序,完成固液分离。
2)将所述步骤1)得到的所述上油层和所述中油层进行加热处理,加热温度为165℃,加热后得到混合油和气体混合物,所述气体混合物包括臭气和水蒸气,所述气体混合物经收集后进入废气处理工艺;
3)将所述步骤2)加热处理后得到的混合油引入催化剂载体床中,经催化剂催化处理得到待纯化油;
4)将所述步骤3)得到的待纯化油引入三级蒸馏塔中,蒸馏出沸点小于300℃的三种馏分混合物,经冷凝分离得到第一成品油,第一成品油的收率为60%;
5)将所述步骤4)蒸馏塔的底油进入絮凝工序,之后静置沉淀3h,分离出第二成品油和油渣,第二成品油的收率为34%。
优选地,所述步骤3)中的催化剂载体床包括载体床和负载在载体床上的氧化镍颗粒,所述氧化镍粒径为2mm。
优选地,所述载体床按照以下重量份数组成:活性氧化铝35份,纳米多孔二氧化硅15份,碳化硅12份,高岭土8份,白云石5份,田菁粉4份;
所述活性氧化铝的孔容为0.8ml/g,孔径为6.0nm,比表面积为280m2/g;
所述纳米多孔二氧化硅的孔容为1.2ml/g,孔径为50nm,比表面积为320m2/g。
优选地,所述载体床的制备方法为:
步骤一:按比例称取各原料后,将原料与占原料总重量25%的水混合,混合均匀后投入混炼机中混炼60min制备得到泥料;
步骤二:将泥料放置于蜂窝钢模具中,设置压力为12mpa,通过模压成型制得蜂窝状载体坯体;
步骤三:将蜂窝状载体坯体在120℃条件下干燥22h,之后将干燥好的蜂窝状载体坯体以35℃/h的升温速率,升温至1250℃进行烧成15h,即可制得具有蜂窝状结构的载体床。
优选地,所述步骤3)中的催化剂载体床在使用前需经活性处理,所述活性处理方法为:将催化剂载体置于65℃的十二烷基苯浸泡池中处理3h,十二烷基苯质量分数为20%,然后经洗涤、分离、干燥即得所需的催化剂载体床,其中十二烷基苯与所述氧化镍催化剂的质量比为1:0.15。
优选地,所述步骤4)的三级蒸馏塔为常压蒸馏,所述蒸馏塔的温度由上到下依次设置为160℃、215℃和280℃。
优选地,所述步骤5)的絮凝工序为:先将体积比为15%的异佛尔酮二胺絮凝剂溶液按剂油体积比为1:20的比例加入蒸馏塔底油中,温度为70℃,搅拌8min,再将体积比为10%的二乙撑三胺溶液按剂油体积比为1:50的比例加入蒸馏塔底油中,温度为60℃,搅拌12min。
优选地,所述步骤2)产生的烟气余温供所述步骤1)中的静置分层工序和催化剂载体床活性处理工序完成余温加热,实现能量回收。
优选地,所述步骤1)固液分离得到的液体被引入进入污水处理工序,固体与所述步骤5)静置沉淀得到的油渣混合掺烧,掺烧产生的废气进入尾气处理工序。
测试例1
将实施例一到实施例三制备得到的第一成品油进行性能测试,对比标准《b5柴油》(gb25199-2017)得到如下性能数据:
测定结果:通过该再生技术得到的第一成品油,粘度、闪点、酸值、十六烷值等物化性质指标都达到了标准《b5柴油》(gb25199-2017)的要求。
测试例2
将实施例一到实施例三制备得到的第二成品油进行性能测试,并且将废机油作为对比例,对比标准《通用润滑油基础油》(qsy44-2009)得到如下性能数据:
测定结果:通过该再生技术得到的第二成品油,色度、外观、酸值、残炭等物化性质指标都达到了《通用润滑油基础油》(qsy44-2009)标准。
尽管本发明的实施方案已公开如上,但其并不仅仅限于说明书和实施方式中所列运用,它完全可以被适用于各种适合本发明的领域,对于熟悉本领域的人员而言,对于本领域的普通技术人员而言,在不脱离本发明的原理的情况下可以对这些实施例进行多种变化、修改、替换和变型,因此在不背离权利要求及等同范围所限定的一般概念下,本发明并不限于特定的细节。
本文用于企业家、创业者技术爱好者查询,结果仅供参考。