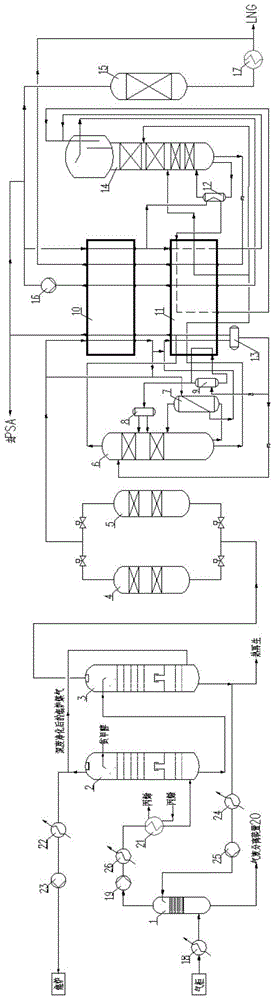
本发明涉及焦炉煤气净化技术领域,尤其涉及一种焦炉煤气深度净化制lng联产氢气的系统及方法。
背景技术:
焦炉煤气是炼焦过程中得到的重要副产品,近些年对焦炉煤气的组成成分的研究已经相当成熟。焦炉煤气属于中热值然气,氢气含量50%~60%,甲烷22%~24%,其中包含巨大的利用价值。在生产焦炭的同时会产生大量焦炉煤气,如果按照生产1吨焦炭产生430立方米的焦炉煤气计算,我国全年焦炉煤气发生量基本维持在1800亿立方米,其中45-50%左右的焦炉煤气返回焦炉,剩余的焦炉煤气相当可观。因此,如何回收利用好焦炉煤气对实现资源的循环利用和经济的可持续发展具有重要意义。在焦炉煤气综合利用之前焦炉煤气的净化就成了重中之重。
焦炉煤气中氢气含量大约占到55%~60%。氢气以热值高、品质纯洁等优点赢得人们的青睐。作为最有发展潜力的清洁能源,氢气具有广阔的发展和应用前景,氢能可广泛应用于能源、工业、交通运输、建筑等领域。为炼化、钢铁、冶金等行业提供原料、还原剂和高品质热源,能有效减少碳排放;也可以通过燃料电池技术应用于汽车、轨道交通、船舶等领域,降低交通运输对石油和天然气的依赖;还可应用于分布式发电,为家庭住宅、商业建筑等供电供暖。因此,作为多能源传输和融合交互的纽带,氢能被誉为21世纪最具发展前景的二次能源,是未来清洁低碳能源系统的核心之一。
液化天然气(lng)的主要成分为甲烷,大约占80~99%,无色、无味且无腐蚀性,具有热值高(>31mj/nm3)和方便储运的特点,一般用于电厂、热能、供暖、空调等工业企业的主要燃料,餐饮业和民用燃料,化工原料等。氢气作为燃料,是所有化石燃料、化工原料和生物燃料中最高的,为142351kj/kg,是汽油发热量的3倍,它的燃烧产物是水,没有灰渣和废气,不会污染环境。近些年,随着氢能产业的不断发展,市场需求量也在不断增加,有着广阔的市场。
焦炉煤气中高含量的氢气,使其作为制氢的理想原料,已逐步成为国家促进焦化行业产业升级、开发氢能源的重要途径。同时,焦炉煤气中还有丰富的制备lng的原料。因此,如何综合利用焦炉煤气受到广泛关注。然而,由于焦炉煤气中含有苯、萘、氨、焦油、灰尘和硫等杂质,使得在综合利用焦炉煤气过程净化面临重大考验。主要表现在以下几个方面:
(1)焦炉煤气含硫、氨超标,影响后续净化及合成的正常运行。
一般焦炉煤气只是作为燃料气来使用时,要求h2s低于500mg/nm3,氨含量低于100mg/nm3,但实际运行中酸气和氨时有超标现象,影响后系统稳定运行。随着焦化规模扩大,产业集聚化,焦炉煤气成为重要的化工原料气来使用,焦炉煤气用途的改变,就造成了原焦炉煤气深度净化的设计指标远不能满足现使用指标要求。
(2)焦炉煤气含焦油和萘严重影响压缩机正常运行,主要原因是焦炉煤气夹带焦油、萘含量高,压缩时气温升高焦油气化结焦;以及萘冷凝结晶,造成压缩机萘堵,使压缩机无法正常运行,被迫停修,有时仅开1-2天就要停车抢修,使生产十分被动,往往都是1开2备或1开3备的局面。
(3)由于粗脱硫不正常造成精脱硫的脱硫剂提前失效,影响生产操作,主要是硫穿透,被迫提前更换脱硫剂,由此发生的脱硫剂更换频繁,运行费用增加。
(4)返炉焦炉煤气中硫含量高,需要建设烟气脱硫装置脱除烟道气中氧化硫,同时脱硫过程会产生难处理的脱硫废液。
(5)传统制氢时的脱碳工艺采用甲烷化工艺,在脱碳过程中消耗一定量的氢气,减少了氢气的收率。
技术实现要素:
为解决目前综合利用焦炉煤气时存在会影响后系统稳定运行、会造成压缩机堵塞、会造成精脱硫的脱硫剂提前失效而增加运行费用、返回焦炉的焦炉煤气中硫含量高及会使得氢气的收率比较低的技术问题,本发明提供一种焦炉煤气深度净化制lng联产氢气的系统及方法。
为解决上述技术问题,本发明采用的技术方案是:
一种焦炉煤气深度净化制lng联产氢气的系统,其包括预洗塔、脱硫塔、脱碳塔、第一吸附塔、第二吸附塔、汽提塔、第一再沸器、第一气液分离器、第二气液分离器、第一冷箱、第二冷箱、第二再沸器、第三气液分离器、分离塔和甲烷化塔,其中:所述预洗塔为超重力旋转装置,其中:气柜经第一换热器与预洗塔下部的气相进口连接,预洗塔底部的液相出口与气液分离装置连接,预洗塔顶部的气体出口经第一压缩机、第二换热器和第三换热器与脱硫塔下部的进气口连接,脱硫塔顶部的出气口经第四换热器和第二压缩机与焦炉连接,脱硫塔顶部的出气口还与脱碳塔下部的进气口连接,脱硫塔底部的出液口与脱碳塔上部的进液口连接,脱碳塔底部的出液口经第五换热器和第三压缩机与预洗塔上部的液相进口连接,脱碳塔顶部的出气口与第一吸附塔的进气口和第二吸附塔的进气口均连接,第一吸附塔的出气口和第二吸附塔的出气口均与第一再沸器上部的进气口连接,第一吸附塔的出气口和第二吸附塔的出气口还均与第一冷箱顶部的进气口连接,第一冷箱底部的出气口也与第一再沸器上部的进气口连接,第一再沸器下部的出气口和第一冷箱底部的出气口均与第二冷箱顶部的进气口连接,第二冷箱底部的物料出口与第三气液分离器顶部的物料进口连接,第三气液分离器顶部的富氢气出口与第二冷箱底部的富氢气进口连接,第二冷箱顶部的富氢气出口与第一冷箱底部的富氢气进口连接,第一冷箱顶部的富氢气出口与psa氢气提纯系统连接,第一冷箱顶部的富氢气出口还与甲烷化塔的进气口连接,第三气液分离器底部的出液口与第二气液分离器下部的物料进口连接,第二气液分离器底部的出液口与第二冷箱侧面的进液口连接,第二冷箱侧面的出气口和第二气液分离器顶部的出气口均与第一气液分离器的物料进口连接,第一气液分离器的出液口和出气口分别与汽提塔中部的进液口和进气口连接,第三气液分离器底部的出液口还与汽提塔上部的进液口连接,汽提塔顶部的富氢气出口与第二冷箱侧面的富氢气进口连接,汽提塔底部的出液口与第二冷箱侧面的进液口连接,第二冷箱底部的出液口与分离塔的上部填料中部连接,第二冷箱底部的出液口还与第二冷箱底部的进液口连接,第二冷箱侧面的出气口与分离塔中部的进气口连接,分离塔底部的富ch液出口与第二冷箱底部的富ch液进口连接,第二冷箱顶部的富ch液出口与第一冷箱底部的富ch液进口连接,第一冷箱顶部的富ch液出口为lng出口,分离塔顶部的co出口与第二冷箱底部的co进口连接,第二冷箱顶部的co出口与第一冷箱底部的co进口连接,第一冷箱顶部的co出口经第四压缩机与甲烷化塔的进气口连接,第四压缩机的co出口与第一冷箱顶部的co进口连接,第一冷箱底部的co出口与第二冷箱顶部的co进口连接,第二冷箱底部的co出口与分离塔顶部的co进口连接,第一冷箱底部的co出口还与第二再沸器上部的co进口连接,第二再沸器顶部的co出口与分离塔下部的co进口连接,分离塔底部的出液口与第二再沸器底部的进液口连接,第二再沸器下部的出液口与第二冷箱侧面的进液口连接,甲烷化塔的出液口与第六换热器连接,第六换热器的出液口为lng出口。
可选地,所述预洗塔包括传动装置、转轴和预洗壳体,传动装置与转轴一端连接,转轴另一端连接有转子,转子设于预洗壳体内腔的中下部,预洗壳体的顶部中间连接有气体出口,预洗壳体的底部连接有液相出口,预洗壳体的一侧底部连接有气相进口,预洗壳体的另一侧中上部连接有液相进口,液相进口连接有l形液体管道,l形液体管道的竖直管延伸至转子中部,l形液体管道的竖直管上安装有若干个液相喷嘴,预洗壳体内腔的顶部设有除沫器,除沫器底部与转子顶部之间安装有分隔板,转子顶部中间与分隔板之间通过第一密封垫密封,转子底部中间两侧与转轴之间分别通过第二密封垫和第三密封垫密封,转子内部填充有填料层。
一种焦炉煤气深度净化制lng联产氢气的方法,所述焦炉煤气深度净化制lng联产氢气的方法采用上述焦炉煤气深度净化制lng联产氢气的系统,其包括如下步骤:
s1,洗脱苯后的焦炉煤气经第一换热器换热到20-25℃后从预洗塔下部送入预洗塔中,同时来自脱碳塔底部的煤气洗涤剂经第五换热器换热和第三压缩机加压后从预洗塔上部送入预洗塔;其中,预洗塔为超重力旋转装置;
s2,换热后的焦炉煤气与煤气洗涤剂在预洗塔内逆流或错流接触进行预处理,预处理后的煤气洗涤剂在预洗塔的超重力作用下在预洗塔内壁聚集后排出至气液分离装置;
s3,预处理后的焦炉煤气经第一压缩机加压到0.3-1.0mpa后经过第二换热器换热、第三换热器深冷至-22~-28℃后进入脱硫塔,在脱硫塔内与脱硫塔通入的贫甲醇进行低温甲醇洗操作脱出焦炉煤气中的杂质,得到深度净化后的焦炉煤气,42-50%的深度净化后的焦炉煤气经过第四换热器复热并经第二压缩机减压到8-10kpa后作为返炉煤气用于焦炉加热,其余深度净化后的焦炉煤气进入脱碳塔进行脱碳;
s4,脱碳塔脱碳后的焦炉煤气进入第一吸附塔或第二吸附塔中吸附残留的甲醇和co2,使它们含量小于0.1ml/m3;
s5,吸附后的焦炉煤气经第一冷箱换热至-130~-140℃后分为两股,其中一股与吸附后的焦炉煤气混合后进入第一再沸器进行汽化而作为汽提塔的热源;从第一再沸器出来的焦炉煤气与从第一冷箱出来的另一股吸附后的焦炉煤气混合后进入第二冷箱,在第二冷箱中进一步冷却至-180~-185℃;
s6,从第二冷箱出来物料进入第三气液分离器,并在第三气液分离器中进行气液分离,其中大部分co和ch4已冷凝,第三气液分离器分离出的气相富氢气经过第一冷箱和第二冷箱复温至常温后,一部分去psa氢气提纯系统进行提氢,另一部分与co混合进入甲烷化塔进行甲烷的合成;
s7,第三气液分离器分离出的液相物料分为两股物料,其中:一股物料经过减压膨胀后温度降至-180~-185,压力变为1.0~1.5mpa,该股物料进入第二气液分离器进行气液分离,第二气液分离器分离的液相进入第二冷箱换热后与第二气液分离器分离的气相物料混合,使其温度升至-170~-175℃后,该股物料进入第一气液分离器进行气液分离,第一气液分离器分离得到的气相和液相进入汽提塔的两层填料之间进行提氢;第三气液分离器分离出的液相物料中的另一股物料经减压膨胀后温度降至-180~-185,压力变为1.0~1.5mpa,该股物料由汽提塔上部进入汽提塔进行提氢;经过汽提塔汽提后富氢气由汽提塔顶部解析出来,并经过第一冷箱和第二冷箱复温至35~45℃去往psa氢气提纯系统进行提氢;
s8,汽提塔底部液相经过第二冷箱换热至-180~-185℃,压力变为0.25~0.50mpa,分为两部分:其中一部分直接进入分离塔上部填料中部;另一部分在第二冷箱中汽化为气相,温度升至-170~-175℃,压力保持0.25~0.50mpa后作为热源进入分离塔;
s9,进入分离塔中的物料经过分离塔分离后,底部富ch4液的温度为-170~-180℃,压力为0.3~0.4mpa,底部富ch4液经过减压膨胀后经过第一冷箱和第二冷箱换热至常温后获得lng;
s10,分离塔顶部的气体co经过第一冷箱和第二冷箱换热至常温后,进入第四压缩机进行压缩后分为两部分,压缩后的co压力为0.7~0.8mpa,其中:一部分进入分离塔顶部作为分离塔的回流液,该股回流液经过第一冷箱换热至-150~-155℃后分流一股物料至第二再沸器进行汽化而作为分离塔的热源,在分离塔中冷却后的物料进入第二冷箱换热至180~-185℃后进入分离塔顶部作为回流液;另一部分与富氢气混合后进入甲烷化塔进行甲烷的合成,甲烷化塔合成的甲烷在第六换热器作用下得到lng。
可选地,所述煤气洗涤剂的用量为0.20~0.32kg/m3焦炉煤气,脱硫塔中贫甲醇的用量为1.30~1.50kg/m3焦炉煤气。
可选地,所述低温甲醇洗操作的温度为-20℃~-40℃,压力为0.3-1.5mpa。
可选地,所述第一吸附塔或第二吸附塔的吸附操作温度为-60~-50℃,操作压力5~6mpa;脱附操作温度为180~350℃,操作压力为50~200kpa,脱附采用氮气。
可选地,所述汽提塔的操作压力为1.0~1.5mpa,温度为-196~40℃。
可选地,所述分离塔的操作压力为0.1~0.5mpa,温度为-196~40℃。
可选地,所述甲烷化塔的甲烷化温度为230℃~650℃,压力为3.0~6.0mpa,氢碳比为2.90~3.10,催化剂采用镍基催化剂。
本发明的有益效果是:
通过设置预洗塔,并设置预洗塔为超重力旋转装置,使得脱苯后的焦炉煤气可以在预洗塔内通过超重力旋转技术进行杂质的初步脱除,通过预洗塔的预处理,可以深度脱除脱苯后的焦炉气内的尘、苯、焦油、萘、氨和硫等有害物质,解决了焦炉煤气中的硫、氨超标会影响后系统的稳定运行的问题,能够提高系统运行的稳定性;还解决了焦炉煤气中的焦油、萘会造成压缩系统堵塞的问题,避免在后续工段可能造成的堵塞异常;还解决了粗脱硫不正常造成精脱硫的脱硫吸附剂提前失效而增加运行成本的问题,使得后续生产化工产品精脱硫催化及使用寿命至少延长一年以上。另外,通过预处理,使得焦炉煤气返回焦炉后无需再脱硫,从而能够减少烟道气脱硫装置的投资和脱硫废液的产生。进一步地,通过低温甲醇洗操作进行脱硫和脱碳操作,进一步深度净化了焦炉煤气中的杂质,提高了焦炉煤气的洁净度,不仅避免传统工艺中脱硫液的消耗和脱硫废液的处理成本,进一步降低净化成本,同时脱硫废气送制酸,制酸浓度高且品质好,而且提高了脱碳精度,脱碳过程不消耗氢气因而能够提高氢气的收率,进而能够提高副产品氢气的产量。通过采用低温甲醇洗结合psa吸附的工艺流程,充分净化焦炉煤气中的硫等杂质,同时减少了焦炉煤气脱碳过程中氢气的消耗,提高了氢气纯度和利用率。
本发明通过焦炉煤气深冷分离分离出ch4、co、h2,甲烷直接作为产品输出,而co和h2作为原料通过甲烷化制备lng,同时可以联产氢气,提高了焦炉煤气的综合利用效益。本发明所述系统和方法实现了对焦炉煤气的深度净化,并通过深冷分离和甲烷化制备lng,副产高品质氢气,实现了对焦炉煤气的梯级利用,提高了经济效益。通过本发明实施例提供的系统和方法,既满足了焦炉煤气增压输送以及后续的深度净化需求,达到了生产化学品合成系统净化需要的目的,又制备得到lng,同时提高了副产氢气的产量。本发明具有投资少,设备体积和占地面积小,脱除焦炉煤气中焦油尘、萘等杂质效率高、能耗低、洗涤效率高等优点。
附图说明
图1是本发明的系统组成示意图。
图2是图1中预洗塔的结构示意图。
图3是本发明中所使用的气液分离器的结构示意图。
具体实施方式
下面将结合附图和实施例对本发明作进一步地详细描述。
如图1所示,本发明实施例提供了一种焦炉煤气深度净化制lng联产氢气的系统,其包括预洗塔1、脱硫塔2、脱碳塔3、第一吸附塔4、第二吸附塔5、汽提塔6、第一再沸器7、第一气液分离器8、第二气液分离器9、第一冷箱10、第二冷箱11、第二再沸器12、第三气液分离器13、分离塔14和甲烷化塔15,其中:所述预洗塔1为超重力旋转装置,其中:气柜经第一换热器18与预洗塔1下部的气相进口103连接,预洗塔1底部的液相出口102与气液分离装置20连接,预洗塔1顶部的气体出口107经第一压缩机19、第二换热器26和第三换热器21与脱硫塔2下部的进气口连接,脱硫塔2顶部的出气口经第四换热器22和第二压缩机23与焦炉连接,脱硫塔2顶部的出气口还与脱碳塔3下部的进气口连接,脱硫塔2底部的出液口与脱碳塔3上部的进液口连接,脱碳塔3底部的出液口经第五换热器24和第三压缩机25与预洗塔1上部的液相进口109连接,脱碳塔3顶部的出气口与第一吸附塔4的进气口和第二吸附塔5的进气口均连接,第一吸附塔4的出气口和第二吸附塔5的出气口均与第一再沸器7上部的进气口连接,第一吸附塔4的出气口和第二吸附塔5的出气口还均与第一冷箱10顶部的进气口连接,第一冷箱10底部的出气口也与第一再沸器7上部的进气口连接,第一再沸器7下部的出气口和第一冷箱10底部的出气口均与第二冷箱11顶部的进气口连接,第二冷箱11底部的物料出口与第三气液分离器13顶部的物料进口连接,第三气液分离器13顶部的富氢气出口与第二冷箱11底部的富氢气进口连接,第二冷箱11顶部的富氢气出口与第一冷箱10底部的富氢气进口连接,第一冷箱10顶部的富氢气出口与psa氢气提纯系统连接,第一冷箱10顶部的富氢气出口还与甲烷化塔15的进气口连接,第三气液分离器13底部的出液口与第二气液分离器9下部的物料进口连接,第二气液分离器9底部的出液口与第二冷箱11侧面的进液口连接,第二冷箱11侧面的出气口和第二气液分离器9顶部的出气口均与第一气液分离器8的物料进口连接,第一气液分离器8的出液口和出气口分别与汽提塔6中部的进液口和进气口连接,第三气液分离器13底部的出液口还与汽提塔6上部的进液口连接,汽提塔6顶部的富氢气出口与第二冷箱11侧面的富氢气进口连接,汽提塔6底部的出液口与第二冷箱11侧面的进液口连接,第二冷箱11底部的出液口与分离塔14的上部填料中部连接,第二冷箱11底部的出液口还与第二冷箱11底部的进液口连接,第二冷箱11侧面的出气口与分离塔14中部的进气口连接,分离塔14底部的富ch4液出口与第二冷箱11底部的富ch4液进口连接,第二冷箱11顶部的富ch4液出口与第一冷箱10底部的富ch4液进口连接,第一冷箱10顶部的富ch4液出口为lng出口,分离塔14顶部的co出口与第二冷箱11底部的co进口连接,第二冷箱11顶部的co出口与第一冷箱10底部的co进口连接,第一冷箱10顶部的co出口经第四压缩机16与甲烷化塔15的进气口连接,第四压缩机16的co出口与第一冷箱10顶部的co进口连接,第一冷箱10底部的co出口与第二冷箱11顶部的co进口连接,第二冷箱11底部的co出口与分离塔14顶部的co进口连接,第一冷箱10底部的co出口还与第二再沸器12上部的co进口连接,第二再沸器12顶部的co出口与分离塔14下部的co进口连接,分离塔14底部的出液口与第二再沸器12底部的进液口连接,第二再沸器12下部的出液口与第二冷箱11侧面的进液口连接,甲烷化塔15的出液口与第六换热器17连接,第六换热器17的出液口为lng出口。
本发明实施例的系统应用在焦炉煤气初冷、电捕焦油、预冷、中间冷却、除氨、终冷和洗脱苯后,用来脱除焦炉煤气内含的尘、苯、焦油、萘、氨以及各种形态硫等杂质,并进行lng和氢气的制备。该焦炉煤气深度净化制lng联产氢气的系统涉及的处理工序包括预洗、脱硫、脱碳、深冷分离、psa氢气提纯和甲烷化。
可选地,如图2所示,所述预洗塔1包括传动装置101、转轴115和预洗壳体108,传动装置101与转轴115一端连接,转轴115另一端连接有转子104,转子104设于预洗壳体108内腔的中下部,预洗壳体108的顶部中间连接有气体出口107,预洗壳体108的底部连接有液相出口102,预洗壳体108的一侧底部连接有气相进口103,预洗壳体108的另一侧中上部连接有液相进口109,液相进口109连接有l形液体管道,l形液体管道的竖直管延伸至转子104中部,l形液体管道的竖直管上安装有若干个液相喷嘴111,预洗壳体108内腔的顶部设有除沫器106,除沫器106底部与转子104顶部之间安装有分隔板105,转子104顶部中间与分隔板105之间通过第一密封垫110密封,转子104底部中间两侧与转轴115之间分别通过第二密封垫112和第三密封垫113密封,转子104内部填充有填料层114。
可选地,所述填料层114的孔隙率80%~99%;填料层114的填料采用大波纹丝网填料和小波纹丝网填料。在靠近转轴115处设置长度占预洗壳体108半径5%~10%长度的小波纹填料,优选为5%~8%。大波纹丝网填料的平均孔径为5~10mm,优选为4~8mm;小波纹丝网填料的平均孔径为1~5mm,优选为2~4mm。这种填料方式有利于液相洗涤液的均匀雾化,提高对杂质的捕集效果,大波纹填料可以减小气液相阻力,提高填料的抗堵塞能力。
可选地,如图3所示,所述气液分离装置20为卧式三堰型气-液-液-液四相分离器,四相分离器包括分离壳体218,分离壳体218内腔从左至右分为入口段ⅰ、沉降分离段ⅱ和采集段ⅲ;所述入口段ⅰ设置有气液分离器206、挡板207和镇静板208,进料口201设于分离壳体218外部并与分离壳体218顶部连接,气液分离器206安装于进料口201下面,镇静板208底端与分离壳体218底部连接,挡板207顶端与分离壳体218顶部连接并位于气液分离器206和镇静板208之间;所述沉降分离段ⅱ安装有聚结器209;所述采集段ⅲ设置有重相流体溢流堰217、重相流体收集槽219、轻相流体收集槽220和中间相流体溢流堰216,重相流体溢流堰217设置于聚结器209一侧并与分离壳体218底部连接,重相流体收集槽219顶端与分离壳体218底部连接并位于聚结器209与重相流体溢流堰217之间,重相流体收集槽219侧壁的顶部和底部各安装有一个第一液位计213,重相流体收集槽219底部连接有重相流体出口203,重相流体收集槽219上方的分离壳体218顶部和底部各安装有一个第二液位计212,轻相流体收集槽220设置于重相流体溢流堰217一侧,轻相流体收集槽220的前墙为轻相流体溢流堰214,轻相流体溢流堰214的高度低于轻相流体收集槽220的后墙215的高度,轻相流体收集槽220内的顶部和底部各设有一个第三液位计210,轻相流体收集槽220底部连接有轻相流体出口204,轻相流体出口204位于分离壳体218外部,轻相流体收集槽220上方设置有除雾器222,气相出口202设于分离壳体218外面并与除雾器222连接,中间相流体溢流堰216设置于轻相流体收集槽220一侧并与分离壳体218底部连接,中间相流体溢流堰216与分离壳体218尾部的空间形成中间相流体收集槽221,中间相流体溢流堰216一侧的顶部和底部各设有一个第四液位计211,中间相流体溢流堰216一侧的分离壳体218底部连接有中间相流体出口205。
其中,气液分离器206和镇静板208是入口段ⅰ的常规部件,其中气液分离器206的主要功能是实现气-液预分离,实际应用中可有多种形式,其作用是把液体在填料顶部或某一高度上进行均匀的初始分布或再分布,用来提高传质、传热的有效表面,改善相间接触,从而提高塔的分离效率。镇静板208的主要作用是减缓入口段ⅰ液相区的两相波动,也兼有液-液-液预分离的功能,但主要是抑制波动为沉降分离段ⅱ提供稳定的操作条件。聚结器209主要是通过促进轻相(比如油滴)在板面的聚结来提高分离效率,同时也具有抑制沉降分离段ⅱ液相区波动的功能。
可选地,所述入口段ⅰ、沉降分离段ⅱ和采集段ⅲ的长度比例为1:3.2-4.2:2。
可选地,所述镇静板208顶端与位于分离壳体218顶部的第二液位计212处于同一水平面;所述挡板207底端高于镇静板208顶端400-500mm,挡板207底端低于气液分离器206底端不小于200mm。
可选地,所述聚结器209的高度与轻相流体溢流堰214的高度(h1)相同,所述重相流体溢流堰217的高度高出轻相流体收集槽220底端200-500mm,轻相流体溢流堰214高度为四相分离器直径的1/2-3/4,轻相流体收集槽220的后墙215高度(h2)高出除雾器222底端200mm,中间相流体溢流堰216的高度(h3)比轻相流体溢流堰214的高度低20-100mm。
通过在采集段ⅲ设置了重相流体溢流堰217、轻相流体溢流堰214和中间相流体溢流堰216三块溢流堰板和重相流体收集槽219、轻相流体收集槽220和中间相流体收集槽221三个液相收集槽,因此四相分离器采集段ⅲ的长度大于普通分离器,但也因为如此设置,使得操作过程中的液-液界面得到较好的控制,从而保证分离过程的稳定进行,从而减小或避免了工况波动对沉降分离段ⅱ过程的影响。本发明实施例中四相分离器的液-液界面的控制源于两个方面:一是三块溢流堰板和三个液相收集槽结构使液-液界面同时受到轻相/中间相和重相流体静压的控制,因而比较稳定;二是轻相流体收集槽220和中间相流体收集槽221为操作过程中上、下游(进、出口)流量的波动提供了缓冲空间,从而减小或避免了工况波动对沉降段分离过程的影响。通过设置镇静板208及聚结器209等部件,确保较低的横向流速使得液相区流体有足够的停留时间实现液-液-液沉降分离,同时有利于分散相的沉降或浮升,还减少液相区的波动,缩短分离时间,减小设备尺寸。
本发明实施例之所有采用图3所示的四相分离器进行气液的分离,是综合考虑实际分离工况下沉降分离段ⅱ末端的压力分布的影响因素包括:轻相流体溢流堰214高度和三堰板的高差、溢流堰顶的液层厚度和溢流堰顶的液层流速和轻相收集槽220底部的流动阻力而作出的。
本发明实施例中预洗塔1预处理后的煤气洗涤液进入四相分离器,预洗塔1预处理后的煤气洗涤剂中含有焦油、尘、粗苯、萘、氨、有机硫等杂质,本发明实施例通过四相分离器对其中残留的气体、重油、轻油和中间相液体进行回收处理。四相分离器分离得到的气体从其气相出口202排出,四相分离器分离得到的重油从其重相流体出口203排出,四相分离器分离得到的轻油从其轻相流体出口204排出,四相分离器分离得到的中间相液体从其中间相流体出口205排出。
本发明实施例还提供了一种焦炉煤气深度净化制lng联产氢气的方法,所述焦炉煤气深度净化制lng联产氢气的方法采用上述焦炉煤气深度净化制lng联产氢气的系统,其包括如下步骤:
s1,洗脱苯后的焦炉煤气经第一换热器18换热到20-25℃后从预洗塔1下部送入预洗塔1中,同时来自脱碳塔3底部的煤气洗涤剂经第五换热器24换热和第三压缩机25加压后从预洗塔1上部送入预洗塔1;其中,预洗塔1为超重力旋转装置。
洗脱苯后的焦炉煤气中含有尘、苯、焦油、萘、氨以及各种形态硫等杂质。通常,洗脱苯后的焦炉煤气中含有焦油尘5-15mg/m3,萘10-200mg/m3,氨15-100mg/m3,硫小于500mg/m3及其它微量杂质。
s2,换热后的焦炉煤气与煤气洗涤剂在预洗塔1内逆流或错流接触进行预处理,预处理后的煤气洗涤剂在预洗塔1的超重力作用下在预洗塔1内壁聚集后排出至气液分离装置20。
可选地,所述预洗塔1的操作条件为:操作温度15~20℃、操作压力3~6kpa、填料比表面积500~4000m2/m3,填料旋转频率为30~60hz,气液比1000~6000。所述煤气洗涤剂的用量为0.20~0.32kg/m3焦炉煤气。
由于洗脱苯后的焦炉煤气中包括尘、苯、焦油、萘、氨以及各种形态硫等杂质,因此,本发明实施例先通过采用超重力旋转技术的预洗塔1对洗脱苯后的焦炉煤气进行预处理,以初步脱除洗脱苯后的焦炉煤气中的尘、苯、焦油、萘、氨以及各种形态硫等杂质。
具体地,在预洗塔1内,煤气洗涤剂经预洗塔1的液相喷嘴111均匀分布后进入填料层114,在传动装置101、转轴115和转子104作用下,煤气洗涤剂被分裂成液体微元(液膜、液丝和液滴)并与洗脱苯后的焦炉煤气逆流接触来脱除洗脱苯后的焦炉煤气中的杂质。由于预洗塔1为超重力旋转装置,使得本发明实施例是利用超重力旋转技术来进行杂质的脱除的。超重力旋转技术的切割粒径达到10-8m的数量级,煤气洗涤剂经过填料层114后的粒径几乎达到分子级别,再在超重力旋转装置中聚集后与杂质一并脱出。本发明实施例利用超重力旋转技术对洗脱苯后的焦炉煤气进行预处理,可以强化洗涤效果,降低洗涤的粒径切割尺寸,同时通过液相喷雾和超重力作用下,使液滴分布更加均匀,与焦炉煤气中杂质接触面更大,从而提升对杂质的洗脱效果。超重力旋转装置具有良好的粒子捕集效果、气相压降小,旋转填料不易堵塞等特点,以此来达到深度脱除焦炉气内的尘、苯、焦油、萘、氨和硫等有害物质,从而满足焦炉煤气增压输送以及后续的深度净化,达到生产化学品合成系统净化需要的目的。脱除杂质后的焦炉煤气经过除沫器106除沫后得到预处理后的焦炉煤气,脱除杂质后的煤气洗涤剂被甩至预洗壳体108内壁并由液相出口102流入气液分离装置20。
进一步地,本发明实施例通过试验确定最佳的预处理焦炉煤气的最合适温度在20-25℃,煤气洗涤剂至少包括甲醇和粗苯,煤气洗涤剂还可以包括脱盐水、乙醇、洗油和焦油中的一种或两种及两种以上的组合,煤气洗涤剂温度小于20℃时具有很好的预处理效果。
焦炉煤气预处理是在不同温度、压力、洗涤剂下试验发现焦炉煤气中的萘在<20℃时易结晶析出。为避免低温下萘结晶造成设备、管道的堵塞,本发明实施例通过新增预洗塔1,并利用预洗甲醇来脱除焦炉煤气中的萘。由于预洗甲醇中含有粗苯,苯与萘均属于芳香类化合物,根据相似相容原理,萘基本溶解到煤气洗涤剂中。在这些条件下对洗脱苯后的焦炉煤气进行预处理后,实践证明,对焦油灰尘的捕集效率达到99%以上,能够完全除去3μm以上的颗粒;对萘的脱除率80%以上;对焦油和尘的脱除率达到60%以上;对有机硫脱除率达到85%以上;对氨的脱除率达到50%以上;对苯的脱除率达到50%以上;这种脱除率使得预处理后的焦炉煤气满足了后续压缩以及深度净化的要求。
s3,预处理后的焦炉煤气经第一压缩机19加压到0.3-1.0mpa后经过第二换热器26换热、第三换热器21深冷至-22~-28℃后进入脱硫塔2,在脱硫塔2内与脱硫塔2通入的贫甲醇进行低温甲醇洗操作脱出焦炉煤气中的杂质,得到深度净化后的焦炉煤气,42-50%的深度净化后的焦炉煤气经过第四换热器22复热并经第二压缩机23减压到8-10kpa后作为返炉煤气用于焦炉加热,其余深度净化后的焦炉煤气进入脱碳塔3进行脱碳。
可选地,脱硫塔2中贫甲醇的用量为1.30~1.50kg/m3焦炉煤气。所述低温甲醇洗操作的温度为-20℃~-40℃,压力为0.3-1.5mpa。
脱硫塔2中的甲醇在吸收酸性气体的同时还吸收了工艺气中的nh3,这会对低温甲醇洗系统(脱硫塔2和脱碳塔3)造成一定的影响。低温下nh3在甲醇中的溶解度远高于co2和h2s等酸性气体在甲醇中的溶解度,因此,很容易在甲醇洗系统中累积。co2和h2s等酸性气体溶解到甲醇中后会使得甲醇的ph值降低,造成低温甲醇洗系统设备的腐蚀。为了减少设备的腐蚀、延长设备的使用年限和运行周期,现低温甲醇洗工艺都会允许系统中存在一定含量的nh3,但是必须要严格控制nh3在低温甲醇洗系统中的含量,如果nh3含量低会造成设备腐蚀的加剧;当nh3含量高到一定程度就会造成工艺气中硫含量超标。所以必须要控制好低温甲醇洗系统中的nh3含量,因而本发明实施例需要在净化时将氨气浓度控制在一定范围,即维持循环使用的贫甲醇(在脱硫塔2、脱碳塔3和预洗塔1中循环的)中nh3含量小于20×10-6ppm,ph值在8-10。
依据焦炉煤气中h2s浓度的不同,在0.3-1.0mpa、温度-20~-40℃甲醇中的溶解度为0.9~6nm3h2s/m3,co2在0.3-1.0mpa、温度-20~-40℃在甲醇中的溶解度为0.8~5nm3co2/m3,可以确定脱硫塔2中贫甲醇的用量(即进入脱硫塔2中的贫甲醇用量)为1.30-1.50kg/m3焦炉煤气。
焦炉煤气成分复杂,杂质众多,其气体组分包括co、h2、co2、ch4、h2s、有机硫、c2h4、c2h6、c3h8、c4h10、hcn、n2、ar以及焦油、脂肪酸、单酚、复酚、石脑油、蒽油、萘油、飞灰等。在这些组分中除co、h2有效组分和ch4、n2、ar以及烃类属惰性气体外,其余所有组分包括co2和硫化物都是需要脱除的有害杂质,可见其净化任务的艰巨。随伴随着焦化企业退城入园、升级改造等政策的实施,规模化、高端化成为焦化行业的发展方向,对焦炉煤气脱硫的要求也随之提高,采用低温甲醇洗净化方法可以干净地脱除焦炉煤气中的各种有害成分,诸如co2、h2s、cos、c4h4s、hcn、nh3、h2o、c2以上烃类(包括轻油、芳香烃、石脑油、烯烃及胶质物等)以及其他羰基化合物等,而其它任何净化工艺都无法做到。另外,采用低温甲醇洗脱除焦炉煤气中成分复杂的硫杂质,既可以保证净化气指标,又可通过甲醇再生循环利用解决焦化脱硫废液无法根治处理的难题。
经过低温甲醇洗操作,使得深度净化后的焦炉煤气中的有机硫杂质几乎全部被脱除焦炉煤气中总硫含量小于10ppm。深度净化后的焦炉煤气中返回焦炉作燃料气,能够减少烟道气脱硫装置的投资和脱硫废液的产生。
低温甲醇洗净化脱碳后的焦炉煤气进行深冷分离,分离出ch4、co,纯度均大于99.5%,以下步骤即为焦炉煤气深冷分离的具体实现过程。
s4,脱碳塔3脱碳后的焦炉煤气进入第一吸附塔4或第二吸附塔5中吸附残留的甲醇和co2,使它们含量小于0.1ml/m3。
其中,第一吸附塔4和第二吸附塔5在吸附残留的甲醇和co2时,是通过它们的控制阀切换使用的,第一吸附塔4进行吸附时,第二吸附塔5进行脱附;第一吸附塔4进行脱附时,第二吸附塔5进行吸附。
可选地,所述第一吸附塔4或第二吸附塔5的吸附操作温度为-60~-50℃,操作压力5~6mpa;脱附操作温度为180~350℃,操作压力为50~200kpa,脱附采用氮气。
s5,吸附后的焦炉煤气经第一冷箱10换热至-130~-140℃后分为两股,其中一股与吸附后的焦炉煤气混合后进入第一再沸器7进行汽化而作为汽提塔6的热源;从第一再沸器7出来的焦炉煤气与从第一冷箱10出来的另一股吸附后的焦炉煤气混合后进入第二冷箱11,在第二冷箱11中进一步冷却至-180~-185℃。
s6,从第二冷箱11出来物料进入第三气液分离器13,并在第三气液分离器13中进行气液分离,其中大部分co和ch4已冷凝,第三气液分离器13分离出的气相富氢气经过第一冷箱10和第二冷箱11复温至常温后,一部分去psa氢气提纯系统进行提氢,另一部分与co混合进入甲烷化塔15进行甲烷的合成。
s7,第三气液分离器13分离出的液相物料分为两股物料,其中:一股物料经过减压膨胀后温度降至-180~-185,压力变为1.0~1.5mpa,该股物料进入第二气液分离器9进行气液分离,第二气液分离器9分离的液相进入第二冷箱11换热后与第二气液分离器9分离的气相物料混合,使其温度升至-170~-175℃后,该股物料进入第一气液分离器8进行气液分离,第一气液分离器8分离得到的气相和液相进入汽提塔6的两层填料之间进行提氢;第三气液分离器13分离出的液相物料中的另一股物料经减压膨胀后温度降至-180~-185,压力变为1.0~1.5mpa,该股物料由汽提塔6上部进入汽提塔6进行提氢;经过汽提塔6汽提后富氢气由汽提塔6顶部解析出来,并经过第一冷箱10和第二冷箱11复温至35~45℃去往psa氢气提纯系统进行提氢。
其中,通过psa氢气提纯工艺进行提氢的流程包括升压、吸附、均压、顺放、逆放和冲洗等,具体过程可以参见现有的psa氢气提纯工艺,本发明实施例对此不作详细解释说明。
可选地,所述汽提塔6的操作压力为1.0~1.5mpa,温度为-196~40℃。
s8,汽提塔6底部液相经过第二冷箱11换热至-180~-185℃,压力变为0.25~0.50mpa,分为两部分:其中一部分直接进入分离塔14上部填料中部;另一部分在第二冷箱11中汽化为气相,温度升至-170~-175℃,压力保持0.25~0.50mpa后作为热源进入分离塔14。
s9,进入分离塔14中的物料经过分离塔14分离后,底部富ch4液的温度为-170~-180℃,压力为0.3~0.4mpa,底部富ch4液经过减压膨胀后经过第一冷箱10和第二冷箱11换热至常温后获得lng。
可选地,所述分离塔14的操作压力为0.1~0.5mpa,温度为-196~40℃。
s10,分离塔14顶部的气体co经过第一冷箱10和第二冷箱11换热至常温后,进入第四压缩机16进行压缩后分为两部分,压缩后的co压力为0.7~0.8mpa,其中:一部分进入分离塔14顶部作为分离塔14的回流液,该股回流液经过第一冷箱10换热至-150~-155℃后分流一股物料至第二再沸器12进行汽化而作为分离塔14的热源,在分离塔14中冷却后的物料进入第二冷箱11换热至180~-185℃后进入分离塔14顶部作为回流液;另一部分与富氢气混合后进入甲烷化塔15进行甲烷的合成,甲烷化塔15合成的甲烷在第六换热器17作用下得到lng。
甲烷化原料为co和氢气的混合气体,其中的硫含量<0.1ppm。可选地,所述甲烷化塔15的甲烷化温度230℃~650℃,压力3.0~6.0mpa,氢碳比2.90~3.10,催化剂采用镍基催化剂。
本发明实施例通过深冷分离分理出焦炉煤气中的ch4、co、h2,通过氢气与一氧化碳甲烷化反应制备lng,同时可以副产高纯的氢气产品。本发明提供的系统和方法实现了对焦炉煤气的深度净化,并通过深冷分离和甲烷化制备lng,副产高品质氢气,实现了对焦炉煤气的梯级利用,提高了经济效益。
可以理解的是,以上实施方式仅仅是为了说明本发明的原理而采用的示例性实施方式,然而本发明并不局限于此。对于本领域内的普通技术人员而言,在不脱离本发明的精神和实质的情况下,可以做出各种变型和改进,这些变型和改进也视为本发明的保护范围。
本文用于企业家、创业者技术爱好者查询,结果仅供参考。