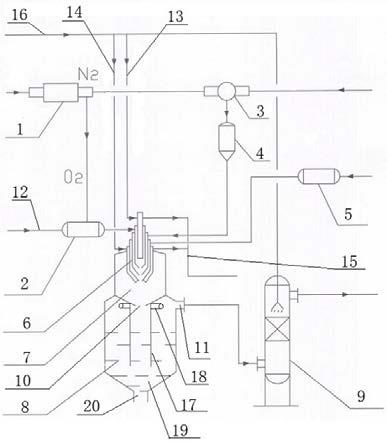
一种粉煤
‑
天然气共混加压气化制备合成气的方法及设备
技术领域
1.本发明涉及氮肥厂合成气制备技术领域,具体地涉及一种粉煤
‑
天然气共混加压气化制备合成气的方法及设备。
背景技术:
2.我国有400多家氮肥厂,合成氨产量7000万吨,在国民经济中占有十分重要的地位。合成气的制备主要有煤气化和天然气转化两种工艺,近十年来,国内外积极研发和推广粉煤气化技术,逐步淘汰了传统的固定床气化工艺,煤的转化率提高了36%以上。但仍存在如下的缺陷,气化反应产生的热量利用率低,合成气中h2/co小于0.8,需要进行co的变换co h2o
→
co2 h2,耗大量水蒸气,还要经低温甲醇洗或液氮洗等工艺脱除co2,增加大量动力消耗。与其相反天然气转化工艺需燃烧部分天然气为转化反应提供热量,生成的合成气h2/co高达2.0以上,用于生产尿素和甲醇等还必须另外补充碳元素。因此,如何设计一种不仅能使产生的合成气既符合生产尿素或甲醇所适宜的h2/co,又能减少co的变换量和co2的排放量,以达到节能减排的目的的工艺,是十分必要的。
技术实现要素:
3.本发明的发明目的在于克服现有技术存在的缺点,提出设计一种粉煤
‑
天然气共混加压气化制备合成气的方法,实现加压粉煤气化工艺和天然气转化工艺的有机耦合,达到元素互补、能量充分利用、co2超低排放的目的。
4.本发明解决其技术问题所采取的技术方案是:一种粉煤
‑
天然气共混加压气化制备合成气的方法,包括以下工艺步骤:(1)制备反应物料粉煤、天然气、气化剂;(2)物料输送:将制备的气化剂输送至气化炉上部的喷射器内部的气化剂通道,粉煤由氮气输送至所述喷射器内部的粉煤通道,天然气加压后经天然气储罐送至所述喷射器内部的天然气通道;(3)气化反应:将粉煤、气化剂、天然气由所述喷射器按设定的比例同时从喷射器底部的喷出口以雾状喷入气化炉中部的气化室,发生气化反应,生成粗合成气和熔渣;(4)粗合成气和熔渣水浴激冷:粗合成气和熔渣通过气化室底部渣口进入气化炉下部的激冷室,粗合成气经水浴激冷洗涤后,从激冷室上部气体出口排入洗涤塔,进一步洗涤净化后进入氨合成系统,熔渣经水浴激冷洗涤后从激冷室底部排入废渣处理系统。
5.进一步的,在步骤(1)中,所述气化剂和粉煤的制备过程为:利用空分装置从空气中分离出氧气和氮气,氧气进入气化剂混合器按比例与水蒸汽混合成气化剂;氮气加压后送至磨煤机,原料煤输送至磨煤机在氮气保护下研磨成粉煤。
6.具体的,所述空分装置分离出来的氧气加压至1
‑
8.5mpa,进入气化剂混合器,同时向气化剂混合器送入1.5
‑
9.81mpa压力的水蒸汽,所述氧气与水蒸气的体积比为3
‑
10。
7.具体的,所述空分装置分离出来的氮气加压至0.004
‑
0.01mpa,送至磨煤机;原料
煤在氮气保护下研磨成细度为9
‑
20μm的粉煤。
8.进一步的,在步骤(3)中,所述粉煤、天然气和气化剂的体积比为0.75
‑
2:1:5.5
‑
7。
9.进一步的,在步骤(3)中,所述粗合成气主要成分为h2和co。
10.进一步的,在步骤(4)中,所述粗合成气和熔渣沿激冷室内的中心下降管排入激冷室的水浴池,粗合成气经水浴激冷和洗涤后逸出水面,再经设置在渣口周围喷淋水管的进一步洗涤,从激冷室上部气体出口排入洗涤塔。
11.进一步的,所述激冷室排出的粗合成气从洗涤塔下部侧向进入,与洗涤塔上部喷淋而下的冷水逆流接触,进一步降温洗涤,使固体微粒含量降至0.1
‑
1mg/m3,检测合格后进入变换
‑
脱碳等净化系统。
12.进一步的,所述喷射器采用自动控制的多通道喷射器,用于自动控制调节各种物料的压力与流量,即按设定的程序进行自动控制调节各种物料的压力与流量,有效控制粉煤、天然气和气化剂(氧、水蒸气)的流量,即物料的合理配比,达到生产尿素或甲等最适宜的h2/co。
13.本发明还提供另一种技术方案:一种基于所述粉煤
‑
天然气共混加压气化制备合成气的方法的设备,包括空分装置、气化剂混合器、磨煤机、煤锁斗、天然气储罐、气化炉、洗涤塔;所述汽化炉包括自上而下依次连接的喷射器、气化室、激冷室;所述喷射器为自动控制的多通道喷射器,各通道分别与气化剂混合器、磨煤机、天然气储罐连接;所述喷射器底部喷出口置入气化室内,粉煤、天然气、气化剂均以雾状喷入气化室;气化室底部设有渣口,渣口置入激冷室内,激冷室上部设置气体出口,气体出口通过管路与洗涤塔下部侧向连接;所述空分装置用于分离空气中的氧气和氮气,其中,氧气输出端与气化剂混合器连接,氮气输出端与磨煤机连接;气化剂混合器与蒸汽管网连接;磨煤机与喷射器之间设有煤锁斗。本发明采用多通道喷射的方式,按一定比例同时喷射粉煤、天然气和气化剂,能够充分利用粉煤气化高温反应的热量为天然气转化提供反应能量,节约天然气并提高天然气转化的速率,反过来用天然气转化高h2/co富余的氢气补充粉煤气化低h2/co缺乏的氢气,达到元素互补、热能充分利用的效果。
14.进一步的,所述喷射器由钢材制作而成,内部通过套管分割为五个螺旋状通道,自内向外依次为内套冷却水通道、气化剂通道、粉煤通道、天然气通道、外套冷却水通道;所述内套冷却水通道和外套冷却水通道底部均封闭;内套冷却水通道顶部设有内套冷却水进口和内套冷却水出口,内套冷却水进口与内套冷却水管连接;气化剂通道上部侧向设有气化剂进口,底部为气化剂喷出口,气化剂进口与气化剂混合器连接;粉煤通道上部侧向设有粉煤进口,底部为粉煤喷出口,粉煤进口与煤锁斗连接;天然气通道上部侧向设有天然气进口,底部为天然气喷出口,天然气进口与天然气储罐连接;外套冷却水通道上部侧向分别设有外套冷却水进口和外套冷却水出口,外套冷却水进口与外套冷却水管连接。内、外套冷却水通道内,通入循环冷却水,控制喷射器内部和外部温度在900℃以下,粉煤在高压n2驱动下,通过喷射器内部的煤粉通道以雾状喷入气化室,气化剂通过喷射器内部的气化剂通道以雾状喷入气化室,同时加压后的天然气通过天然气通道以雾状喷入气化室,进行气化反应。
15.进一步的,所述喷射器各通道的进出口均设有电磁阀,电磁阀通过光缆与dcs自控系统连接,按设定的程序进行自动控制调节各种物料的压力与流量,采用自动控制的多通
道喷射器,有效控制粉煤、天然气和气化剂(氧、水蒸气)的流量,即物料的合理配比,达到生产尿素或甲等最适宜的h2/co。
16.进一步的,所述内套冷却水出口与外套冷却水出口均与汇合管连接;所述内套冷却水管和外套冷却水管均与循环水管网连接;所述循环水管网还与洗涤塔连接,为洗涤塔提供洗涤水。
17.进一步的,所述渣口下方与中心下降管连接,渣口周围位于中心下降管外侧设置喷淋水管;中心下降管底部延伸至激冷室内侧底部的水浴池内;粗合成气经水浴激冷和洗涤后逸出水面,再经喷淋水管进一步洗涤,从激冷室上部侧向气体出口排入洗涤塔。
18.进一步的,所述激冷室底部开设有渣排出口。
19.本发明与现有技术相比,具有以下优点:(1)本发明的一种粉煤
‑
天然气共混加压气化制备合成气的方法,充分利用粉煤气化高温反应的热量为天然气转化提供反应能量,节约天然气并提高天然气转化的速率,反过来用天然气转化高h2/co富余的氢气补充粉煤气化低h2/co缺乏的氢气,达到元素互补、热能充分利用的效果,对于生产尿素或甲醇而言,通过优化工艺,调节粉煤和天然气的配比,严格控制工艺参数,co的变换量可由68%降至36%,吨氨节约蒸汽0.3
‑
0.6吨,co2的排放量可大幅度减少,是节能减排技术的一项重大突破;(2)本发明的自动控制多通道物料喷射器,有效控制粉煤、天然气和气化剂(氧、水蒸气)的流量,即物料的合理配比,达到生产尿素或甲醇最适宜的h/co;所设置的内套水冷却通道和外水冷却通道,能够迅速移走反应热量,保证伸入气化室的喷嘴温度不超过900℃,安全可靠,寿命长,是实现粉煤和天然气共混加压气化的关键。
附图说明
20.图1为本发明主体结构原理示意图;图2为本发明多通道物料喷射器的结构原理示意图。
21.图中,空分装置1、气化剂混合器2、磨煤机3、煤锁斗4、天然气储罐5、喷射器6、气化室7、激冷室8、洗涤塔9、渣口10、气体出口11、蒸汽管网12、内套冷却水管13、外套冷却水管14、汇合管15、循环水管网16、中心下降管17、喷淋水管18、水浴池19、渣排出口20、内套冷却水进口61、内套冷却水出口62、气化剂进口63、气化剂喷出口64、粉煤进口65、粉煤喷出口66、天然气进口67、天然气喷出口68、外套冷却水进口69、外套冷却水出口610。
具体实施方式
22.为使本发明实施例的目的、技术方案和优点更加清楚,下面结合说明书附图,对本发明实施例中的技术方案进行清楚、完整地描述。
23.实施例1:本实施例涉及的一种粉煤
‑
天然气共混加压气化制备合成气的设备,包括空分装置1、气化剂混合器2、磨煤机3、煤锁斗4、天然气储罐5、气化炉、洗涤塔9;所述汽化炉包括自上而下依次连接的喷射器6、气化室7、激冷室8;所述喷射器6为自动控制的多通道喷射器,各通道分别与气化剂混合器2、磨煤机3、天然气储罐5连接;所述喷射器6底部喷出口置入气化室7内,粉煤、天然气、气化剂均以雾状喷入气化室7;气化室7底部设有渣口10,渣口10置
入激冷室8内,激冷室8上部侧向设置气体出口11,气体出口11通过管路与洗涤塔9下部侧向连接;所述空分装置1用于分离空气中的氧气和氮气,其中,氧气输出端与气化剂混合器2连接,氮气输出端与磨煤机3连接;气化剂混合器2与蒸汽管网12连接;磨煤机3与喷射器6之间设有煤锁斗4。本发明采用多通道喷射的方式,按一定比例同时喷射粉煤、天然气和气化剂,能够充分利用粉煤气化高温反应的热量为天然气转化提供反应能量,节约天然气并提高天然气转化的速率,反过来用天然气转化高h2/co富余的氢气补充粉煤气化低h2/co缺乏的氢气,达到元素互补、热能充分利用的效果。
24.所述喷射器6由钢材制作而成,内部通过套管分割为五个螺旋状通道,自内向外依次为内套冷却水通道、气化剂通道、粉煤通道、天然气通道、外套冷却水通道;所述内套冷却水通道和外套冷却水通道底部均封闭;内套冷却水通道顶部设有内套冷却水进口61和内套冷却水出口62,内套冷却水进口61与内套冷却水管13连接;气化剂通道上部侧向设有气化剂进口63,底部为气化剂喷出口64,气化剂进口63与气化剂混合器2连接;粉煤通道上部侧向设有粉煤进口65,底部为粉煤喷出口66,粉煤进口65与煤锁斗4连接;天然气通道上部侧向设有天然气进口67,底部为天然气喷出口68,天然气进口67与天然气储罐5连接;外套冷却水通道上部侧向分别设有外套冷却水进口69和外套冷却水出口610,外套冷却水进口69与外套冷却水管14连接。内、外套冷却水通道内,通入循环冷却水,控制喷射器6内部和外部温度在900℃以下,粉煤在高压n2驱动下,通过喷射器6内部的煤粉通道以雾状喷入气化室7,气化剂通过喷射器6内部的气化剂通道以雾状喷入气化室7,同时加压后的天然气通过天然气通道以雾状喷入气化室7,进行气化反应。
25.所述喷射器6各通道的进出口均设有电磁阀,电磁阀通过光缆与dcs自控系统连接,按设定的程序进行自动控制调节各种物料的压力与流量,采用自动控制的多通道喷射器,有效控制粉煤、天然气和气化剂(氧、水蒸气)的流量,即物料的合理配比,达到生产尿素或甲等最适宜的h/co。
26.所述内套冷却水出口62与外套冷却水出口610均与汇合管15连接;所述内套冷却水管13和外套冷却水管14均与循环水管网16连接;所述循环水管网16还与洗涤塔9连接,为洗涤塔9提供洗涤水。
27.所述渣口10下方与中心下降管17连接,渣口10周围位于中心下降管17外侧设置喷淋水管18;中心下降管17底部延伸至激冷室8内侧底部的水浴池19内;粗合成气经水浴激冷和洗涤后逸出水面,再经喷淋水管18进一步洗涤,从激冷室上部侧向气体出口11排入洗涤塔。
28.所述激冷室8底部开设有渣排出口20。
29.实施例2:本实施例基于实施例1所述的粉煤
‑
天然气共混加压气化制备合成气的设备,实现制备生产尿素的合成气的方法,包括:(1)由空分装置1从空气中分离出氧气和氮气,分离出的氧气加压5.5mpa,送进气化剂混合器2,与来自蒸汽管网12的压力为9.81mpa的水蒸气混合,按照o2/h2o体积比为5的比例配制成气化剂;分离出的氮气加压0.004mpa,送入磨煤机3,在氮气的保护下,原料煤研磨成粒度为9
‑
20μm的粉煤,在密闭的管道内,由氮气保护输送至煤锁斗4;管道天然气由增压机加压后,储于天然气储罐5;
(2)对生产尿素而言,根据物料衡算,适宜的h2/co为1.87,由实测得知粉煤加压气化的合成气h2/co为0.8,天然气转化的合成气h2/co为2.0,由此推算出粉煤:粉煤:天然气:气化剂的体积比应为0.75:1:5.5。
30.由自动控制的多通道喷射器将粉煤、天然气、气化剂按上述比例从其内部设置的粉煤通道、天然气通道、气化剂通道输送到伸入气化室7上部的喷出口,通过高压喷嘴均以雾状喷入气化室7,在高压高温下发生复杂的气化反应,生成以co、h2为主要成分的粗合成气和熔渣;其中,粗合成气中h2/co为1.08,则co的变换量较单项加压粉煤气化工艺由64%下降至48%,co2排放量 3
‑
5%;(3)气化反应生成的粗合成气和熔渣从气化室7底部的渣口10进入激冷室8的中心下降管17,直接排入激冷室8下部的水浴池19中,粗合成气经过水浴激冷和洗涤逸出水面,再经喷淋水管18的冲刷,进一步除去细灰,从激冷室8上部侧向气体出口11排出;熔渣和细灰及黑水则从激冷室8底部的渣排出口20排出,去废渣处理系统;(4)从激冷室8上部气体出口11排出的粗合成气,从洗涤塔9底部进入,塔内装有筛板、填料、上部连续喷淋冷水、粗合成气从底部进入,与上部喷淋而下的冷水逆流接触,进一步降温并除去细灰,从塔顶上部气体出口排出,进入变换等净化系统。
31.实施例3:本实施例基于实施例1所述的粉煤
‑
天然气共混加压气化制备合成气的设备,实现制备生产甲醇的合成气的方法,包括:(1)由空分装置1从空气中分离出氧气和氮气,分离出的氧气加压5.5mpa,送进气化剂混合器2,与来自蒸汽管网12的压力为9.81mpa的水蒸气混合,按照o2/h2o体积比为6的比例配制成气化剂;分离出的氮气加压0.004mpa,送入磨煤机3,在氮气的保护下,原料煤研磨成粒度为9
‑
20μm的粉煤,在密闭的管道内,由氮气保护输送至煤锁斗4;管道天然气由增压机加压后,储于天然气储罐5;(2)对生产甲醇而言,根据物料衡算,适宜的h2/co为2,则对应的粉煤、天然气、气化剂的配比为每吨粉煤配天然气740 m3和3885 m3气化剂。
32.由自动控制的多通道喷射器将粉煤、天然气、气化剂按上述比例从其内部设置的粉煤通道、天然气通道、气化剂通道输送到伸入气化室7上部的喷出口,通过高压喷嘴均以雾状喷入气化室7,在高压高温下发生复杂的气化反应,生成以co、h2为主要成分的粗合成气和熔渣;其中,粗合成气中h2/co为1.08,则co的变换量较单项加压粉煤气化工艺由64%下降至48%,co2排放量 3
‑
5%;(3)气化反应生成的粗合成气和熔渣从气化室7底部的渣口10进入激冷室8的中心下降管17,直接排入激冷室8下部的水浴池19中,粗合成气经过水浴激冷和洗涤逸出水面,再经喷淋水管18的冲刷,进一步除去细灰,从激冷室8上部侧向气体出口11排出;熔渣和细灰及黑水则从激冷室8底部的渣排出口20排出,去废渣处理系统;(4)从激冷室8上部排气口排出的粗合成气,从洗涤塔9底部进入,塔内装有筛板、填料、上部连续喷淋冷水、粗合成气从底部进入,与上部喷淋而下的冷水逆流接触,进一步降温并除去细灰,从塔顶上部气体出口排出,进入变换等净化系统。
33.上述具体实施方式仅是本发明的具体个案,本发明的专利保护范围包括但不限于上述具体实施方式的产品形态和式样,任何符合本发明权利要求书且任何所属技术领域的
普通技术人员对其所做的适当变化或修饰,皆应落入本发明的专利保护范围。
再多了解一些
本文用于企业家、创业者技术爱好者查询,结果仅供参考。