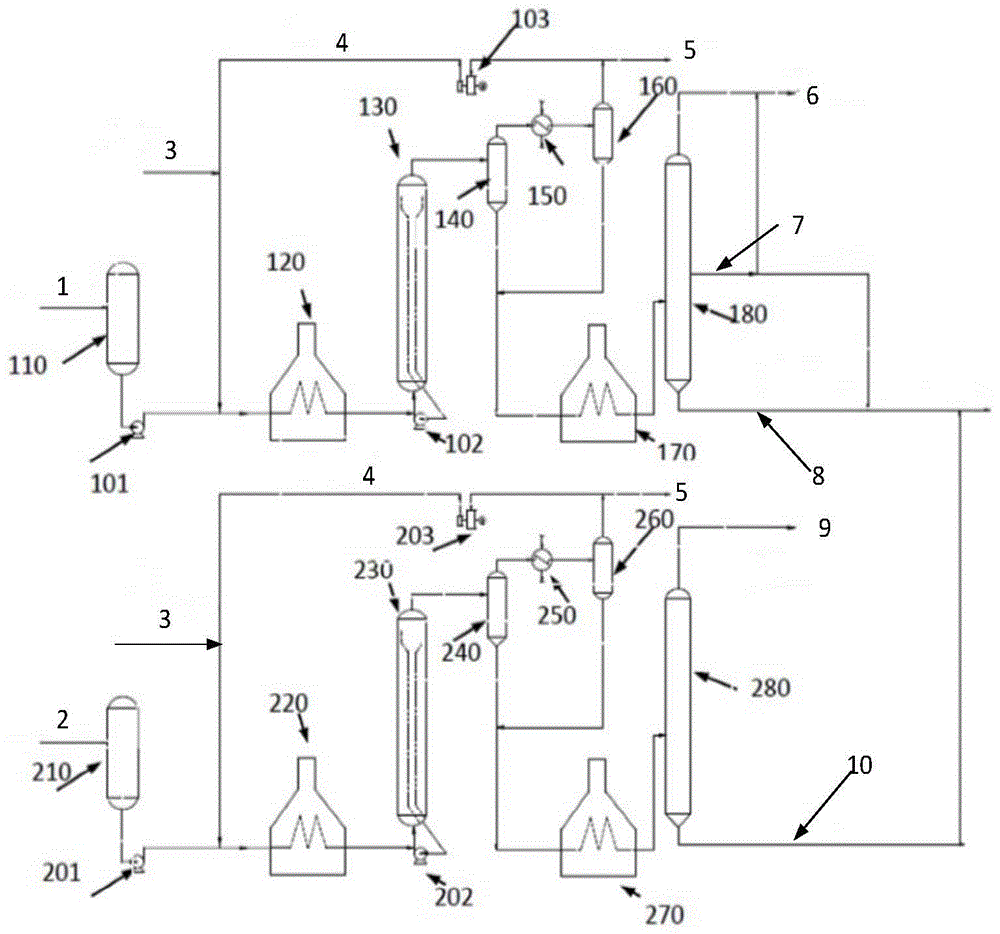
本发明涉及煤直接液化,具体涉及煤直接液化循环溶剂及其制备方法和系统。
背景技术:
煤直接液化技术是指煤在氢气和催化剂作用下,通过加氢裂化转变为液体燃料的过程。溶剂是煤液化反应过程中重要的介质,溶剂的主要作用主要可归纳为以下几种:溶解和溶胀作用、分散作用、提供活性氢、传递转移活性氢、溶解气相氢、稀释液化产物,其中,提供活性氢即供氢作用是指在煤直接液化反应过程中能够向煤热自由基碎片直接供氢或传递氢,使自由基及时得到稳定,转化小分子的油,因此溶剂的供氢性能直接关系煤的液化转化率和油收率。
当前煤直接液化供氢溶剂来自煤的液化自身产物,并采用加氢方式获得。对煤直接液化获得煤液化粗油进行加氢处理,并再次循环回煤浆制备部分,溶剂加氢的主要作用包括三个部分:一是通过加氢使芳烃部分饱和,提高溶剂的氢能能力;二是可以降低油煤浆黏度,便于输送;三是脱除煤直液化油中杂原子,为煤液化油进一步加工生产合格燃料及其它化工产品提供合格原料。溶剂供氢能力直接关系煤直接液化油收率和转化率,如何保持循环溶剂的高活性以及循环溶剂性质的稳定性,使煤在液化反应过程中可以始终转化率和油收率,是当前煤直接液化领域重点研究方向。
煤直接液化过程中由于溶剂来自于自身反应产物且在系统中不断循环,易造成溶剂性质发生变化,一些不利于煤液化反应的物质会发生聚集,如链烷烃及环烷烃;另外,煤直接液化过程中出现波动,也会对循环溶剂性质造成影响,比如低负荷运行时二次裂化严重以及反应深度不足,溶剂循环量加氢深度过高,造成芳烃加氢过饱和,循环溶剂量略有不足等不利现象。这些均会造成煤的转化率和油收率降低,且是一种恶性循环,直接影响煤直接液化的影响效益。
cn105925304a公开了一种煤直接液化循环溶剂及其制备方法。该方法通过对煤直接液化油先进行分馏,切割为重质油馏分、中质馏分、轻质馏分,将重质馏分单独加氢,然后再与中质馏分混合作为循环溶剂,虽然提高重质馏分加氢效果,但由于中质馏分没有得到加氢且其含量较高,因此溶剂供氢性能未能得到有效改善;另外,油煤浆黏度也会提高,对输送提出了更高也要求,同样也会对下游产品加工装置造成不利影响。
cn103468315a公开了一种煤直接液化循环溶剂及其制备方法。该方法将煤焦油中的蒽油与煤直接液化油共同加氢,经分馏后得到煤直接液化得到循环溶剂,虽然可以将蒽油加工为合格产品,提高装置目标产物产量,但由于蒽油与煤直接液化油共同加氢时,蒽油馏程范围与煤液化目标产物高度重合,很大一部分蒽油加氢产物经分馏后进入到目标产物中,因而对循环溶剂性能改善有限。
综上,现有的煤直接液化循环溶剂加工方法存在循环氢溶剂供氢能力较差、工艺路线复杂、装置建设投资成本高、操作难度大等不足,且没有彻底解决循环溶剂能供氢能性质恶化、保持溶剂高活性的难题,因此,仍需要对现有的循环溶剂的加工方法进行改进。
技术实现要素:
本发明的目的是为了克服现有技术存在的煤直接液化循环溶剂的供氢能力较差、液化活性稳定差问题,提供一种煤直接液化循环溶剂及其制备方法和系统。
为了实现上述目的,本发明第一方面提供一种制备煤直接液化循环溶剂的方法,包括以下步骤:
s1、在含氢气体和第一加氢催化剂存在下,将煤直接液化油进行第一加氢反应,得到第一加氢产物,所述第一加氢产物经第一分离得到煤液化加氢稳定油;以及
在含氢气体和第二加氢催化剂存在下,将煤焦油进行第二加氢反应,得到第二加氢产物,所述第二加氢产物经第二分离得到煤焦油加氢稳定油;
s2、将所述煤液化加氢稳定油进行第一分馏,得到轻质馏分油a、中质馏分油b和重质馏分油c;以及
将所述煤焦油加氢稳定油进行第二分馏,得到轻质馏分油d和重质馏分油e;
s3、将所述重质馏分油c、所述重质馏分油e和可选的部分所述中质馏分油b混合,得到煤液化循环溶剂。
本发明第二方面提供一种根据上述方法制备得到的煤直接液化循环溶剂。
本发明第三方面提供一种制备煤直接液化循环溶剂的系统,包括分别与混料系统连通的煤直接液化油处理系统和煤焦油处理系统;
所述煤直接液化油处理系统包括:
煤直接液化油罐,用于储存煤直接液化油;
第一加氢反应器,用于将来自煤直接液化油罐的煤直接液化油进行第一加氢反应,得到第一加氢产物;
第一分离系统,用于将所述第一加氢产物进行分离,得到煤液化加氢稳定油;
第一分馏塔,用于将所述煤液化加氢稳定油进行分馏,得到轻质馏分油a、中质馏分油b和重质馏分油c;
所述煤焦油处理系统包括:
煤焦油罐,用于储存煤直接液化油;
第二加氢反应器,用于将来自煤焦油罐的煤直接液化油进行第二加氢反应,得到第二加氢产物;
第二分离系统,用于将所述第二加氢产物进行分离,得到煤焦油加氢稳定油;
第二分馏塔,用于将所述煤焦油加氢稳定油进行分馏,得到轻质馏分油d和重质馏分油e;
混料系统,用于对所述重质馏分油c、所述重质馏分油e和可选的部分所述中质馏分油b混合,得到煤直接液化循环溶剂。
通过上述技术方案,本发明的煤焦油来自煤热解过程,其组成与煤相似,主要以芳烃为主,且芳烃含量高于煤直接液化循环溶剂,在煤直接液化过程中引入经单独加氢的煤焦油,有利于提高煤液化循环溶剂的供氢能力;
其次,通过引入加氢煤焦油置换部分煤直接液化自产循环溶剂,在改善循环溶剂性能的同时也可保证循环溶剂性质的稳定,且保持较高供氢性能,从而有利于促进煤的液化转化,并获取较高的油收率;
此外,在煤液化过程中,引入煤焦油作为溶剂,实现了煤与煤焦油共炼,拓宽了煤焦油的加工方式和加工难度,可以置换更多的目标产品,有利于提高煤直接液化经济效益。
附图说明
图1是根据本发明一实施方式的煤直接液化循环溶剂的制备工艺流程图。
附图标记说明
1、煤直接液化油2、煤焦油
3、含氢气体4、循环氢
5、尾气6、轻质馏分油a
7、中质馏分油b8、重质馏分油c
9、轻质馏分油d10、重质馏分油e
110、煤直接液化油罐120、第一加热炉
130、第一加氢反应器140、第一热高压分离器
150、第一高压换热器160、第一冷高压分离器
170、第三加热炉180、第一分馏塔
101、第一高压原料泵102、第一循环泵
103、第一循环氢压缩机210、煤焦油罐
220、第二加热炉230、第二加氢反应器
240、第二热高压分离器250、第二高压换热器
260、第二冷高压分离器270、第四加热炉
280、第二分馏塔201、第二高压原料泵
202、第二循环泵203、第二循环氢压缩机
具体实施方式
在本文中所披露的范围的端点和任何值都不限于该精确的范围或值,这些范围或值应当理解为包含接近这些范围或值的值。对于数值范围来说,各个范围的端点值之间、各个范围的端点值和单独的点值之间,以及单独的点值之间可以彼此组合而得到一个或多个新的数值范围,这些数值范围应被视为在本文中具体公开。
本发明提供一种制备煤直接液化循环溶剂的方法,包括以下步骤:
s1、在含氢气体和第一加氢催化剂存在下,将煤直接液化油进行第一加氢反应,得到第一加氢产物,所述第一加氢产物经第一分离得到煤液化加氢稳定油;以及
在含氢气体和第二加氢催化剂存在下,将煤焦油进行第二加氢反应,得到第二加氢产物,所述第二加氢产物经第二分离得到煤焦油加氢稳定油;
s2、将所述煤液化加氢稳定油进行第一分馏,得到轻质馏分油a、中质馏分油b和重质馏分油c;以及
将所述煤焦油加氢稳定油进行第二分馏,得到轻质馏分油d和重质馏分油e;
s3、将所述重质馏分油c、所述重质馏分油e和可选的部分所述中质馏分油b混合,得到煤液化循环溶剂。
本发明中,分别将煤直接液化油和煤焦油进行加氢反应,实现煤直接液化油和煤焦油中芳烃的部分饱和,提高循环溶剂的供氢性能,同时也为下游产品加工提供合格原料。煤液化加氢稳定油经分馏得到轻质馏分油a、中质馏分油b、重质馏分油c,煤焦油加氢稳定油经分馏得到轻质馏分油d和重质馏分油e;将两者重质馏分(重质馏分油c、重质馏分油e)及部分中质馏分(中质馏分油b)混后作为循环供氢溶剂,由于煤焦油来自煤热解过程,其组成与煤相似,主要以芳烃为主,且芳烃含量较高,芳烃含量高于煤直接液化循环溶剂,经加氢后,其供氢性能优于煤直接液化循环溶剂,因此在煤直接液化过程中引入经单独加氢的煤焦油置换部分循环溶剂,有利于提高煤液化循环溶剂的供氢能力。
其次,由于煤直接液化过程,煤液化自产溶剂在不断循环过程,循环溶剂中的不利组分饱和烃会产生聚集,造成循环溶剂性质恶化,同时煤直接液化反应过程出现波动也会造成循环溶剂无法回收,导致循环溶剂性变差,这些均不利于煤的液化反应,通过引入煤焦油加氢稳定油置换部分煤直接液化自产循环溶剂,在改善循环溶剂性能的同时也可保证循环溶剂性质的稳定,且保持较高供氢性能,从而有利于促进煤的液化转化,并可获取较高的油收率。
此外,在煤液化过程中,引入煤焦油作为溶剂,能够实现煤与煤焦油共炼,拓宽了煤焦油的加工方式和加工难度,可以置换更多的目标产品,有利于提高煤直接液化经济效益。
本发明中,为了提高循环溶剂的供氢能力,所述煤直接液化油为煤直接液化全馏分油或馏程>200℃的煤直接液化馏分油;优选地,所述煤直接液化油的馏程为220-500℃,馏程为220-500℃的煤直接液化馏分油中,饱和烃含量低,不饱和芳烃含量较高,通过催化加氢、分馏后,能够得到供氢能力更强的循环溶剂。
本发明中,为了提高循环溶剂的供氢能力,所述煤焦油的馏程<500℃;优选地,所述煤焦油的馏程为220-500℃,更优选为220-400℃,馏程为220-500℃的煤焦油馏分油中饱和烃含量低、不饱和芳烃含量较高且不含沥青质,通过催化加氢、分馏后,能够得到供氢能力更强的循环溶剂,而馏程为220-400℃的煤焦油馏分油中饱和烃含量更低、不饱和芳烃含量更高,更易发生加氢饱和反应,且可以提高煤焦油添加量,通过催化加氢、分馏后,得到具有更好供氢性能的循环溶剂,生产更多的目标产品。
本发明中,为了进一步提高所述循环溶剂的供氢能力,优选条件下,以所述煤焦油的总量计,所述煤焦油中芳烃的重量含量>70wt%,优选>85wt%。
在本发明的一个优选实施方式中,为了得到具有更好供氢性能的循环溶剂,所述煤焦油的馏程为220-500℃,且以所述煤焦油的总量计,所述煤焦油中芳烃的重量含量>70wt%,更优选的,所述煤焦油的馏程为220-400℃,所述煤焦油中芳烃的重量含量>85wt%。
洗油和蒽油的馏程范围窄,且小于400℃,芳烃含量高达90wt%以上、不含沥青质,优选条件下,为了进一步提高所述循环溶剂的供氢性能,所述煤焦油选自洗油和/或蒽油。
本发明中,为了得到更加优良的煤直接液化循环溶剂,优选条件下,所述轻质馏分油a的馏程<220℃,更优选为<200℃;优选条件下,所述中质馏分油b的馏程为200-350℃,更优选为220-350℃;优选条件下,所述重质馏分油c的馏程>200℃;优选条件下,所述重质馏分油e的馏程>220℃,更优选为>350℃。按照上述方式对煤液化加氢稳定油和煤焦油加氢稳定油进行分馏,能够更充分地分离煤直接液化油加氢产物中的供氢组分与非供氢组分(或弱供氢组分),使最终煤直接液化循环溶剂中具有更高含量的芳烃,从而使煤直接液化循环溶剂具有更好的供氢性能。
本发明中,为了进一步提高循环溶剂中芳烃的含量,提高循环溶剂的供氢性能,优选条件下,以所述重质馏分油e的总量计,所述重质馏分油e中芳烃的重量含量大于80wt%。
本发明中,为了提高循环溶剂中的芳烃含量,提高循环溶剂的供氢性能和稳定性,生产更多的目标产品,以所述煤直接液化循环溶剂的总量计,所述重质馏分油c的重量含量为20-35wt%、所述重质馏分油e的重量含量不高于80wt%,所述中质馏分油b的重量含量为0-80wt%;进一步优选地,所述重质馏分油c的重量含量为25-35wt%、所述重质馏分油e的重量含量为30-65wt%,所述中质馏分油b的重量含量为0-45wt%。
本发明中,所述第一加氢催化剂和所述第二加氢催化剂可以为所属领域技术人员所知。在本发明的一个优选实施方式中,为了使催化剂具有更好的加氢饱和活性和加氢脱氮、氧、硫活性,利于加氢反应的进行,提高加氢反应中部分饱和芳烃的生成量,增加煤液化循环溶剂中活性氢的含量,进而提高循环供氢溶剂的供氢能力。优选条件下,所述第一加氢催化剂包括第一载体和负载在所述第一载体上的第一活性组分,所述第二加氢催化剂包括第二载体和负载在所述第二载体上的第二活性组分;所述第一活性组分和第二活性组分各自独立地选自vib族金属和/或viii族金属中的至少一种;进一步优选地,所述vib族金属选自钼和/或钨;所述viii族金属选自钴和/或镍。
优选条件下,所述第一载体和所述第二载体各自独立的选自无定形氧化物和硅酸盐中的至少一种。
优选地,以所述第一加氢催化剂的总量计,所述第一活性组分以氧化物计的重量含量为10-40wt%;以所述第二加氢催化剂的总量计,所述第二活性组分以氧化物计的重量含量为10-40wt%。
在本发明的一个优选实施方式中,所述第一加氢催化剂和第二加氢催化剂相同,其载体为硅酸铝,活性组分为mo和ni。
煤直接液化油以及煤焦油的加氢反应主要为芳烃饱和反应,芳烃加氢是可逆反应,受反应动力学和热力学影响。本发明中,为了提高加氢反应中部分饱和芳烃的含量,增加活性氢的含量,以进一步提高循环供氢溶剂的供氢能力,优选条件下,所述第一加氢反应的条件至少满足:反应温度为320-400℃,优选为350-390℃;反应压力为8-22mpa,优选为12-19mpa;氢油比为300-1000,体积空速为0.5-2.0h-1;进一步优选的,所述第二加氢反应的条件至少满足:反应温度为320-400℃,优选为350-390℃;反应压力为8-22mpa,优选为12-19mpa;氢油比为300-1000,体积空速为0.5-2.0h-1。
为了提高循环溶剂的供氢能力和稳定性,优选条件下,在步骤s1中,所述第一分离包括:将所述第一加氢产物进行第一热高分离,得到第一热高分离气和第一热高分离液,接着对所述第一热高分离气进行第一冷高分离,得到第一含氢气体和第一冷低分离液;将所述第一热高分离液与所述第一冷低分离液混合得到煤液化加氢稳定油。进一步优选的,所述第一热高分离的条件至少满足:温度为230-270℃,压力为8-22mpa,优选地,所述第一热高分离的条件至少满足:温度为230-350℃,压力为12-19mpa;优选条件下,所述第一冷高分离的条件至少满足:温度为45-54℃,压力为8-22mpa,更优选为压力为12-19mpa。
为了提高循环溶剂的供氢能力和稳定性,优选条件下,在步骤s1中,所述第二分离包括:将所述第二加氢产物进行第二热高分离,得到第二热高分离气和第二热高分离液,接着对所述第二热高分离气进行第二冷高分离,得到第二含氢气体和第二冷低分离液;将所述第二热高分离液与所述第二冷低分离液混合得到煤焦油加氢稳定油;进一步优选的,所述第二热高分离的条件至少满足:温度为230-270℃,压力为8-22mpa,更优选为温度为230-350℃,压力为12-19mpa;优选条件下,所述第二冷高分离的条件至少满足:温度为45-54℃,压力为8-22mpa,更优选为压力为12-19mpa。
本发明中,为了得到加氢性能更优的煤直接液化循环溶剂,优选条件下,所述第一分馏的条件至少满足:压力为0.1-0.2mpa,温度为300-350℃;所述第二分馏的条件至少满足:压力为0.1-0.2mpa,温度为300-350℃。
本发明中,采用上述具体步骤和工艺参数就可以得到供氢能力较强的溶剂,保证循环溶剂性质的稳定性。在本发明的一个优选实施方式中,将剩余的中质馏分油b和全部轻质馏分油d混合形成煤液化产品。上述工艺步骤,在制备出循环供氢溶剂的同时,还得到了煤液化产品。这有利于扩宽煤焦油加氢途径,降低煤焦油加工难度,提高煤液化装置的经济性,为下游煤液化产品进一步加工提供了合格原料。上述煤液化产品经过下游加工后,可以用于生产液体燃料或作为化工产品原料。
本发明还提供一种所述的方法制备得到的煤直接液化循环溶剂,所述煤直接液化循环溶剂中饱和芳烃的重量含量为80-90wt%;链烷烃烃的重量含量小于5wt%;环烷烃的含量小于15wt%;进一步优选地,所述煤直接液化循环溶剂中饱和芳烃的重量含量为81-89wt%;链烷烃烃的重量含量为2-3wt%;环烷烃的含量为10.8-13wt%。
图1是根据本发明一实施方式的煤直接液化循环溶剂的制备工艺流程图,如图1所示,本发明还提供一种制备煤直接液化循环溶剂的系统,包括:混料系统,以及分别与混料系统连通的煤直接液化油处理系统和煤焦油处理系统;
所述煤直接液化油处理系统包括:
煤直接液化油罐110,用于储存煤直接液化油;
第一加氢反应器130,用于将来自煤直接液化油罐的煤直接液化油进行第一加氢反应,得到第一加氢产物;
第一分离系统,用于将所述第一加氢产物进行分离,得到煤液化加氢稳定油;
第一分馏塔180,用于将所述煤液化加氢稳定油进行分馏,得到轻质馏分油a、中质馏分油b和重质馏分油c;
所述煤焦油处理系统包括:
煤焦油罐210,用于储存煤直接液化油;
第二加氢反应器230,用于将来自煤焦油罐的煤直接液化油进行第二加氢反应,得到第二加氢产物;
第二分离系统,用于将所述第二加氢产物进行分离,得到煤焦油加氢稳定油;
第二分馏塔280,用于将所述煤焦油加氢稳定油进行分馏,得到轻质馏分油d和重质馏分油e;
混料系统,用于将所述重质馏分油c、所述重质馏分油e和可选的部分所述中质馏分油b混合,得到煤直接液化循环溶剂。
为了提高循环溶剂的供氢能力和稳定性,优选条件下,所述第一分离系统包括:第一热高分离器140,用于对所述第一加氢产物进行第一热高分离,得到第一热高分离气和第一热高分离液;
第一冷高分离器160,用于对所述第一热高分离气进行第一冷高分离,得到第一含氢气体和第一冷低分离液。
优选条件下,所述第二分离系统包括:
第二热高分离器240,用于对所述第二加氢产物进行第二热高分离,得到第二热高分离气和第二热高分离液;
第二冷高分离器260,用于对所述第二热高分离气进行第二冷高分离,得到第二含氢气体和第二冷低分离液。
本发明中,在加氢反应过程主要发生芳烃部分饱和、脱杂原子反应,尽量避免加氢裂化反应,同时要防止出现加氢过饱和及加氢深度不足的情况,加氢过饱和会导致循环溶剂中饱和烃含量过度增加;加氢深度不足,芳烃没有得到充分部分饱和,活性氢含量低;两者均会导致循环溶剂供氢能力不足。优选的,所述第一加氢反应器和第二加氢反应器各自独立的选自固定床反应器、膨胀床反应器、浆态床反应器或强制内循环沸腾床反应器,更优选的,所述第一加氢反应器和第二加氢反应器均为强制内循环沸腾床反应器,强制内循环沸腾床反应器对原料适应性强,可实现催化剂在线更换,且催化剂活性稳定,反应温度控制更加均匀,加氢后生成油的性质也比较稳定,循环溶剂性质也更稳定。
本发明中对混料系统的种类没有特殊的要求,只要能够实现重质馏分油c、所述重质馏分油e和所述中质馏分油b的混合即可,可以为所属领域技术人员所知,例如可以为管路。
以下将通过实施例对本发明进行详细描述。
以下实施例中,原料油的物性如表1所示,原料油的馏程根据astmd1160-2015测定得到。
加氢催化剂a的载体为硅酸铝,活性成分为mo和ni,以氧化物计,mo2o3的重量含量为20.6wt%,nio的重量含量为4.6wt%;
加氢催化剂b的载体为硅酸铝,活性成分为mo和co,以氧化物计,mo2o3的重量含量为20.6wt%,co2o3的重量含量为4.6wt%;
加氢催化剂c的载体为硅酸铝,活性成分为mo、co和ni,以氧化物计,mo2o3的重量含量为20wt%,nio的重量含量为3wt%,co2o3的重量含量为2wt%。
表1
实施例1
一种制备煤直接液化循环溶剂的方法,步骤如下:
s1、将煤直接液化全馏分油1引入煤直接液化油罐110中,经过第一高压原料泵101升压后与氢气3混合,得到混合物流,混合物流经第一加热炉120加热后引入含有加氢催化剂a的第一加氢反应器130中(沸腾床反应器)进行第一加氢反应,实现芳烃部分饱和以及杂原子脱除反应,得到第一加氢产物,第一加氢反应器130中的底部设置有第一强制循环泵102。
第一加氢产物经过换热冷却后进入第一热高压分离器140进行第一热高分离,得到第一热高分离气和第一热高分离液,第一热高分离的条件为:温度为250℃,压力为15mpa;第一热高分离气经第一高压换热器150冷却后进入第一冷高压分离器160进行第一冷高分离,得到第一含氢气体和第一冷低分离液,第一冷高分离的条件为:温度为54℃,压力为15mpa;
部分第一含氢气体作为循环氢4经过第一循环氢压缩机103升压后循环至第一加热炉120入口与煤直接液化油1进行混合,剩余部分第一含氢气体作为尾气5进行排放;第一热高分离液经过减压后与第一冷低分离液混合得到煤液化加氢稳定油。
将煤焦油2(馏程小于500℃)引入煤焦油罐210中,经过第二高压原料泵201升压后与氢气3混合,得到混合物流;混合物流经第二加热炉220加热后引入含有加氢催化剂a的第二加氢反应器230中(沸腾床反应器)进行第二加氢反应,实现芳烃部分饱和以及杂原子脱除反应,得到第二加氢产物,第二加氢反应器230中的底部设置有第二强制循环泵202。
第二加氢产物经过换热冷却后进入第二热高压分离器240进行第二热高分离,得到第二热高分离气和第二热高分离液,第二热高分离的条件为:温度为250℃,压力为15mpa;第二热高分离气经第二高压换热器250冷却后进入第二冷高压分离器260进行第二冷高分离,得到第二含氢气体和第二冷低分离液,第二冷高分离的条件为:温度为54℃,压力为15mpa;
部分第二含氢气体作为循环氢4经过第二循环氢压缩机203升压后循环至第二加热炉220入口与煤焦油2进行混合,剩余部分第二含氢气体作为尾气5进行排放;第二热高分离液经过减压后与第二冷低分离液混合得到煤焦油加氢稳定油。
s2、将煤液化加氢稳定油经第三加热炉170加热后引入第一分馏塔180中进行第一分馏,第一分馏条件为300℃,0.1mpa,得到馏程小于200℃的轻质馏分油a6、馏程为200-350℃的中质馏分油b7和馏程为大于350℃的重质馏分油c8;
将所述煤焦油加氢稳定油经第四加热炉270加热后引入第二分馏塔280中进行第二分馏,第二分馏条件为300℃,0.1mpa,得到馏程小于200℃的轻质馏分油d9和馏程大于200℃的重质馏分油e10;
s3、将所述重质馏分油c、所述重质馏分油e和部分所述中质馏分油b混合在管路中混合,得到煤液化循环溶剂,所述重质馏分油e占循环溶剂量的30wt%。
本实施例中制备煤液化循环溶剂的原料种类以及煤液化循环溶剂的组成如表2所示。
本实施例中各步骤的工艺参数如表3所示,得到的煤液化循环溶剂的基本性质如表4所示。
实施例2
按照实施例1的方法,不同的是,重质馏分油e占循环溶剂总量的65wt%。
本实施例中制备煤液化循环溶剂的原料种类以及煤液化循环溶剂的组成如表2所示。
本实施例中各步骤的工艺参数如表3所示,得到的煤液化循环溶剂的基本性质如表4所示。
实施例3
按照实施例1的方法,不同的是,煤直接液化油原料油为馏程大于200℃的煤液化油b。
本实施例中制备煤液化循环溶剂的原料种类以及煤液化循环溶剂的组成如表2所示。
本实施例中各步骤的工艺参数如表3所示,得到的煤液化循环溶剂的基本性质如表4所示。
实施例4
按照实施例1的方法,不同的是,煤直接液化油原料油为馏程220-500℃的煤液化油c。
本实施例中制备煤液化循环溶剂的原料种类以及煤液化循环溶剂的组成如表2所示。
本实施例中各步骤的工艺参数如表3所示,得到的煤液化循环溶剂的基本性质如表4所示。
实施例5
按照实施例1的方法,不同的是,煤焦油原料油为馏程220-500℃的煤焦油b;
本实施例中制备煤液化循环溶剂的原料种类以及煤液化循环溶剂的组成如表2所示。
本实施例中各步骤的工艺参数如表3所示,得到的煤液化循环溶剂的基本性质如表4所示。
实施例6
按照实施例1的方法,不同的是,煤焦油原料油为馏程220-400℃的煤焦油c,且重质馏分油e占循环溶剂量的45wt%。
本实施例中制备煤液化循环溶剂的原料种类以及煤液化循环溶剂的组成如表2所示。
本实施例中各步骤的工艺参数如表3所示,得到的煤液化循环溶剂的基本性质如表4所示。
实施例7
按照实施例1的方法,不同的是,煤焦油原料油为洗油,且重质馏分油e占循环溶剂量的45wt%。
本实施例中制备煤液化循环溶剂的原料种类以及煤液化循环溶剂的组成如表2所示。
本实施例中各步骤的工艺参数如表3所示,得到的煤液化循环溶剂的基本性质如表4所示。
实施例8
按照实施例1的方法,不同的是,煤焦油原料油为蒽油,且重质馏分油e占循环溶剂量的45wt%。
本实施例中制备煤液化循环溶剂的原料种类以及煤液化循环溶剂的组成如表2所示。
本实施例中各步骤的工艺参数如表3所示,得到的煤液化循环溶剂的基本性质如表4所示。
实施例9
按照实施例1的方法,不同的是,第一加氢反应器和第二加氢反应器均为固定床反应器,且第一分馏与第二分馏的条件均与实施例1不同,具体如下:
s1、将煤直接液化全馏分油1引入煤直接液化油罐110中,经过第一高压原料泵101升压后与氢气3混合,得到混合物流,混合物流经第一加热炉120加热后引入含有加氢催化剂a的第一加氢反应器130中(固定床反应器)进行第一加氢反应,实现芳烃部分饱和以及杂原子脱除反应,得到第一加氢产物,第一加氢反应器130中的底部设置有第一强制循环泵102。
第一加氢产物经过换热冷却后进入第一热高压分离器140进行第一热高分离,得到第一热高分离气和第一热高分离液,第一热高分离的条件为:温度为250℃,压力为15mpa;第一热高分离气经第一高压换热器150冷却后进入第一冷高压分离器160进行第一冷高分离,得到第一含氢气体和第一冷低分离液,第一冷高分离的条件为:温度为54℃,压力为15mpa;
部分第一含氢气体作为循环氢4经过第一循环氢压缩机103升压后循环至第一加热炉120入口与煤直接液化油1进行混合,剩余部分第一含氢气体作为尾气5进行排放;第一热高分离液经过减压后与第一冷低分离液混合得到煤液化加氢稳定油。
将煤焦油2(馏程小于500℃)引入煤焦油罐210中,经过第二高压原料泵201升压后与氢气3混合,得到混合物流;混合物流经第二加热炉220加热后引入含有加氢催化剂a的第二加氢反应器230中(固定床反应器)进行第二加氢反应,实现芳烃部分饱和以及杂原子脱除反应,得到第二加氢产物,第二加氢反应器230中的底部设置有第二强制循环泵202。
第二加氢产物经过换热冷却后进入第二热高压分离器240进行第二热高分离,得到第二热高分离气和第二热高分离液,第二热高分离的条件为:温度为250℃,压力为15mpa;第二热高分离气经第二高压换热器250冷却后进入第二冷高压分离器260进行第二冷高分离,得到第二含氢气体和第二冷低分离液,第二冷高分离的条件为:温度为54℃,压力为15mpa;
部分第二含氢气体作为循环氢4经过第二循环氢压缩机203升压后循环至第二加热炉220入口与煤焦油2进行混合,剩余部分第二含氢气体作为尾气5进行排放;第二热高分离液经过减压后与第二冷低分离液混合得到煤焦油加氢稳定油。
s2、将煤液化加氢稳定油经第三加热炉170加热后引入第一分馏塔180中进行第一分馏,第一分馏条件为300℃,0.1mpa,得到馏程小于220℃的轻质馏分油a6、馏程为220-350℃的中质馏分油b7和馏程为大于350℃的重质馏分油c8;
将所述煤焦油加氢稳定油经第四加热炉270加热后引入第二分馏塔280中进行第二分馏,第二分馏条件为300℃,0.1mpa,得到馏程小于220℃的轻质馏分油d9和馏程大于220℃的重质馏分油e10;
s3、将所述重质馏分油c、所述重质馏分油e和部分所述中质馏分油b混合在管路中混合,得到煤液化循环溶剂,所述重质馏分油e占循环溶剂量的30wt%。
本实施例中制备煤液化循环溶剂的原料种类以及煤液化循环溶剂的组成如表2所示。
本实施例中各步骤的工艺参数如表3所示,得到的煤液化循环溶剂的基本性质如表4所示。
实施例10
按照实施例9的方法,不同的是,第一加氢催化剂和第二加氢催化剂均为加氢催化剂b。
本实施例中制备煤液化循环溶剂的原料种类以及煤液化循环溶剂的组成如表2所示。
本实施例中各步骤的工艺参数如表3所示,得到的煤液化循环溶剂的基本性质如表4所示。
实施例11
按照实施例9的方法,不同的是,第一加氢催化剂和第二加氢催化剂均为加氢催化剂c。
本实施例中制备煤液化循环溶剂的原料种类以及煤液化循环溶剂的组成如表2所示。
本实施例中各步骤的工艺参数如表3所示,得到的煤液化循环溶剂的基本性质如表4所示。
对比例1
按照实施例1的方法,不同的是:煤液化循环溶剂为煤直接液化自产溶剂,其组成为:75wt%中质馏分油b(馏程为220-350℃)和25wt%重质馏分油c(馏程大于350℃)混合作为循环溶剂。
本实施例中制备煤液化循环溶剂的原料种类以及煤液化循环溶剂的组成如表2所示。
本实施例中各步骤的工艺参数如表3所示,得到的煤液化循环溶剂的基本性质如表4所示。
表2
表3
表4
表4-续
实验例
循环溶剂的煤液化性能评价:
采用0.2t/d煤直接液化实验装置进行煤直接液化反应,考察实施例1至11和对比例1中的得到的循环溶剂煤直接液化的性能。
实验条件为:反应温度455℃,反应压力19mpa;实验采用的煤样分析数据如表5所示,液化反应结果如表6所示。
表5
表6
从表4和表6中可以看出,将煤焦油加氢产物与煤直接液化自产溶剂混合,可以提高煤直接液化循环溶剂中部分饱和芳烃含量,降低饱和链烃含量,从而提高了煤直接液化循环溶剂的供氢能力。
通过提高优化煤直接液化循环溶剂的组成,在煤直接液化反应过程中有利于煤的转化率,提高了煤的液化油收率。
通过实施例1和实施例2的数据对比可知,虽然实施例2的循环溶剂中不含有中质馏分油b,但是通过优化第一加氢反应和第二加氢反应的条件,也能够提高循环溶剂的煤直接液化的性能。
通过实施例1和实施例10-11的数据对比可知,通过同时优化加氢催化剂的种类、加氢反应条件和循环溶剂的组成,能够提高循环溶剂的煤直接液化的性能。
此外,在确保循环溶剂供氢效果的同时,在煤液化过程中,引入煤焦油作为溶剂,实现煤与煤焦油共炼,拓宽了煤焦油的加工方式和加工难度,可以生产更多的目标产品,有利于提高煤直接液化经济效益。
以上详细描述了本发明的优选实施方式,但是,本发明并不限于此。在本发明的技术构思范围内,可以对本发明的技术方案进行多种简单变型,包括各个技术特征以任何其它的合适方式进行组合,这些简单变型和组合同样应当视为本发明所公开的内容,均属于本发明的保护范围。
本文用于企业家、创业者技术爱好者查询,结果仅供参考。