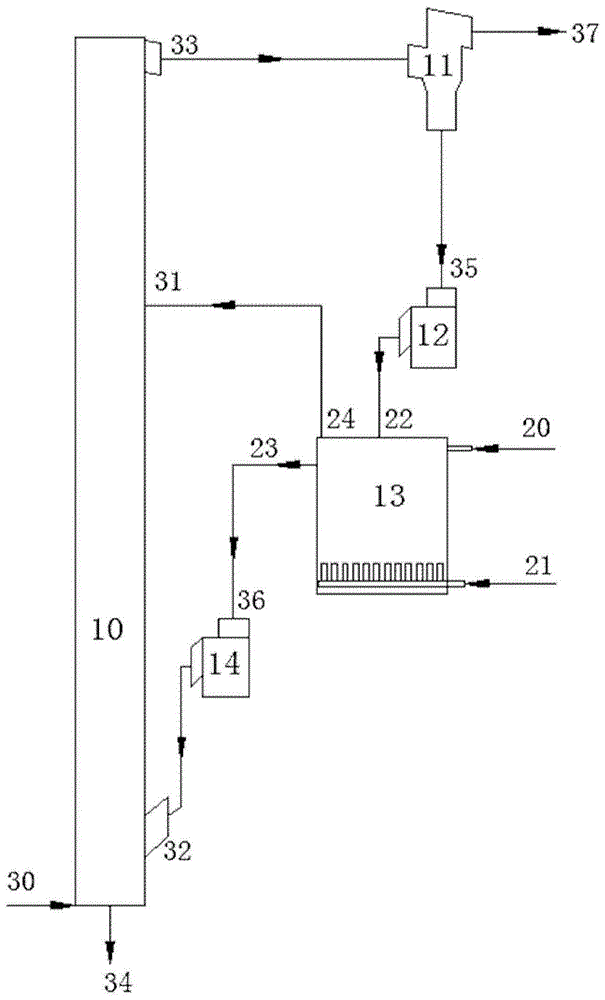
本发明涉及燃料气化技术领域,特别涉及燃料脱碱装置及方法、循环流化床气化装置及方法。
背景技术:
新疆煤炭资源储量丰富,预测储量达290万亿吨,约占中国煤炭资源总量的40%,新疆将成为中国的能源接续区和战略性能源储备区。新疆煤炭资源的大规模开发与利用对中国的能源战略安全及新疆的跨越式发展,起着举足轻重的作用。
在新疆的各大煤田中,准东煤田是中国目前最大的整装煤田,预测储量高达3900亿吨。以中国目前的煤炭年消耗量计算,仅准东煤田就能够全国使用约一百年。由于特殊的成煤条件,该地区的煤质具有低灰、低硫、中高水分、中等发热值、高碱金属含量、易着火、易燃尽、高反应活性、强结渣/沾污、易粉化等特性。与国内其他煤种相比,新疆准东高碱煤灰中的na2o含量在3~15%、cao含量在10~40%、fe2o3含量在7~20%,如此高的碱性金属含量导致新疆准东煤的煤灰熔融温度低在热化学转化过程中表现出强结渣、沾污特性,极大地限制了其大规模开发与利用。
在现役锅炉上,无法实现高碱煤的长周期、满负荷运行。当高负荷下纯烧高碱煤时,锅炉受热面(水冷壁、分隔屏、过热器、再热器等)容易发生严重沾污、结渣、积灰问题,导致部分受热面频繁出现超温、爆管、烟道堵塞、掉焦等现象。目前,电厂通常采用低负荷运行、掺烧其他煤种、或加入添加剂等手段缓解上述问题,但导致高碱煤的利用效率较低。
在现役循环流化床气化炉上,纯烧高碱煤时未出现受热面(空气预热器、余热锅炉、煤气水冷器等)沾污、结渣、积灰问题,体现了循环硫化床气化炉在高碱煤利用方面的优势,但现役循环流化床气化炉的燃料从炉膛中部给入,气化剂从炉膛底部给入,使得炉膛底部温度最高,沿炉膛高度方向温度逐渐降低,灰渣中的碱性金属容易在炉膛底部高温区发生低温共融,导致气化炉炉膛底部出现结渣,是制约循环流化床气化炉长周期稳定运行的瓶颈。再者,循环流化床气化炉的炉膛底部为密相区,煤灰浓度高,导致煤灰中碱金属在该区域富集,增强了结渣风险。综上,解决炉膛底部结渣问题是实现高碱煤循环流化床气化炉长周期稳定运行的关键。
技术实现要素:
有鉴于此,本发明的主要目的在于提供燃料脱碱装置及方法、循环流化床气化装置及方法,以期至少部分地解决上述提及的技术问题中的至少之一。
为了实现上述目的,作为本发明的一个方面,提供了一种燃料脱碱装置,为鼓泡流化床,包括:燃料入口,位于所述燃料脱碱装置的上部,用于向所述燃料脱碱装置输送高碱燃料;辅气化剂入口,位于所述燃料脱碱装置的下部,用于向所述燃料脱碱装置输送辅气化剂,其中所述燃料和辅气化剂在加热下发生脱碱反应;脱碱固体燃料溢流口,位于燃料脱碱装置的上部,用于输出所述脱碱反应产生的脱碱固体燃料;富碱燃料气出口,位于燃料脱碱装置的上部,用于输出所述脱碱反应产生的富碱燃料气。
作为本发明的另一个方面,本发明还提供了一种利用上述燃料脱碱装置进行的燃料脱碱方法,包括:自燃料脱碱装置上部的燃料入口向所述燃料脱碱装置输送燃料;自所述燃料脱碱装置下部的辅气化剂入口向所述燃料脱碱装置输送辅气化剂,使所述燃料和辅气化剂在加热下发生脱碱反应;自所述燃料脱碱装置上部的脱碱固体燃料溢流口输出所述脱碱反应产生的脱碱固体燃料;自所述燃料脱碱装置上部的富碱燃料气出口输出所述脱碱反应产生的富碱燃料气。
作为本发明的再一个方面,还提出一种循环流化床气化装置,包括:主床,自下而上分别包括氧化区和还原区,所述主床的位于氧化区的底部设置有主气化剂入口和返料口,所述主床的位于还原区的位置设置有富碱燃料气入口;下返料器,与所述主床的返料口连通,用于向所述氧化区输送脱碱固体燃料;辅床,为上述的高温脱碱装置,所述辅床的脱碱固体燃料溢流口与所述下返料器连通,用于向所述下返料器输送所述脱碱固体燃料,所述辅床的富碱燃料气出口与所述主床的富碱燃料气入口连通,用于向所述主床的还原区输送富碱燃料气。
作为本发明的又一个方面,还提出一种循环流化床气化方法,包括:将燃料与辅气化剂通入到辅床以进行脱碱反应,产生脱碱固体燃料和富碱燃料气;将所述脱碱固体燃料通入主床的氧化区,与通入到主床的主气化剂发生气化反应,生成气固物料;将所述富碱燃料气通入主床的还原区,在还原性气氛下与所述气固物料相互作用,生成粗燃料气。
从上述技术方案可以看出,本发明的燃料脱碱装置及方法、循环流化床气化装置及方法具有以下有益效果其中之一或其中一部分:
(1)本发明的燃料脱碱装置利用高碱燃料在水蒸气提供的还原气氛下高效脱碱,克服现有技术中水洗脱碱方法的缺陷,简化高碱燃料脱碱工艺流程,实现高温在线脱碱及脱碱后高温半焦的直接利用,从根本上解决现有循环流化床气化炉纯烧高碱燃料存在的炉膛底部结渣瓶颈问题,实现高碱燃料的大规模、长周期稳定运行,同时提高系统的碳转化率和冷燃料气效率。
(2)本发明的循环流化床气化装置与方法,适用于高碱燃料,将高碱燃料直接通入到辅床内,使得高碱燃料中的碱金属在高温及流化作用的条件下充分析出,实现了对高碱燃料中碱金属的高温、高效、在线脱除,从而可以成功将高碱燃料转化为常规低碱含量固体燃料,可有效避免结渣问题。解决了传统水洗法存在的水资源消耗量大、不可溶碱金属去除率低等缺点,避免了水洗法带来的二次污染。
(3)在辅床内,高碱燃料的颗粒停留时间长、反应充分,高碱燃料中30-70%的碱金属在此阶段析出,大幅降低了燃料中碱金属含量。在结构及功能方面,辅床和下返料器的设置及二者的配合是关键,下返料器可将高温脱碱固体物料返回炉膛,同时还具有隔绝碱金属蒸汽进入气化炉底部的功效,以及实现辅床还原区和主床底部氧化区隔离的功效。辅床内为还原性气氛,碳浓度高,布风均匀、不易结渣。
(4)在辅床内生成的高温脱碱固体燃料可输送到主床底部,低碱燃料的燃烧和气化更易控制,从而避免了循环流化床直接燃用高碱燃料时存在的结渣瓶颈问题。解决了高碱燃料因碱金属含量高导致结渣的技术难题,实现了高碱燃料的安全、可靠利用,具有广阔的市场应用前景。
(5)在辅床内生成的富碱燃料气可输送到主床返料口及以上位置,避免了与炉膛底部高温区物料直接接触、反应生成低温共熔体而引发结渣。富碱燃料气中的碱金属可作为气化反应的催化剂,促进由主床底部向上输送的高温物料发生气化反应,促进碳的转化并提升燃料的气化效率。
(6)本发明的适用于高碱燃料的循环流化床气化装置,结构设计简单、操作方便,容易实现规模生产,同时,燃料适应性强,无论对于高碱煤还是生物质等富碱燃料均可使用。
附图说明
图1是本发明实施例的适用于高碱煤(燃料)的循环流化床气化装置示意图;
图2是本发明实施例中用于展示辅床带倾斜角度的高碱燃料循环流化床气化装置示意图;
图3是本发明实施例中用于展示辅床带二次风喷口的高碱煤循环流化床气化装置示意图;
图4是本发明实施例中用于展示辅床的二次风喷口结构示意图。
附图标记说明:
10主床
11气固分离器
12上返料器
13辅床
14下返料器
20燃料入口
21辅气化剂入口
22辅床高温循环半焦入口
23脱碱固体燃料溢流口
24富碱燃料气出口
30主气化剂入口
31富碱燃料气入口
32返料口
33粗燃料气出口
34底渣出口
35上返料器循环半焦入口
36下返料器脱碱固体燃料入口
37气固分离器燃料气出口
40辅床一次风气化剂入口
41第一辅床二次风气化剂入口
42第二辅床二次风气化剂入口
43第三辅床二次风气化剂入口
44第四辅床二次风气化剂入口
具体实施方式
在实现本发明的过程中,发现可以在循环硫化床气化炉运行过程中结合煤脱碱方法以避免炉膛底部结渣问题,然而现有的煤的脱碱方法,是将待脱碱的原煤进行破碎,得到煤粉;再将煤粉与含水溶性有机溶剂的洗脱液进行混合;再向混合液中通入二氧化碳气体,在20~60℃下搅拌、浸洗3~24h后,经固液分离、干燥,得到脱碱煤。该方法脱碱效果好、反应条件温和,但步骤多、周期长,难以实现大规模应用。再者,煤中的污染物经浸洗后转移到溶液中,容易造成二次污染,而不适用于本发明。
由此,本发明创造性地提出了一种燃料脱碱装置及方法、循环流化床气化装置及方法,具体地,将高碱燃料从辅床给入系统,辅床为鼓泡流化床,以水蒸气或贫氧水蒸气为流化介质,被气固分离器分离下来的高温循环半焦经上返料器进入辅床,作为热载体为辅床提供热源,高碱燃料在500~900℃条件下进行干燥、热解、部分气化和脱碱反应,生成高温脱碱固体燃料和富碱粗燃料气。贫氧水蒸气指的是氧气和水蒸气的混合气,或氧气、空气和水蒸气的混合气,其中的氧不充分,燃料焦不足以完全燃烧,氧气的浓度控制在使得燃料燃烧放热产生的热量将燃料脱碱装置内的物料温度在脱碱反应温度范围内。因辅床为鼓泡流化床,流化速度低、温度温和,颗粒破碎、磨损程度较传统循环流化床气化炉弱得多,从而可以有效抑制颗粒粉化,为高碱燃料中的碱金属充分析出提供了重要前提;再者,在辅床内,高碱燃料停留时间长、反应充分,高碱燃料中30-70%的碱金属在此阶段析出,大幅降低了煤中的碱金属含量,从而获得高温脱碱固体燃料。此处的“高碱燃料”指的是高碱煤或生物质等高碱燃料。
由辅床生成的高温脱碱固体燃料经下返料器通入到主床,与主床底部通入的主气化剂进行燃烧、气化反应。与高碱燃料相比,高温脱碱固体燃料中的碱金属含量大幅降低,极大的抑制了循环流化床气化装置中结渣问题的发生,从而可实现纯烧高碱燃料循环流化床气化装置的连续稳定运行。
为使本发明的目的、技术方案和优点更加清楚明白,以下结合具体实施例,并参照附图,对本发明作进一步的详细说明。
根据本发明的实施例,提供了一种燃料脱碱装置,为鼓泡流化床,包括:燃料入口,位于燃料脱碱装置的上部,用于向燃料脱碱装置输送燃料;辅气化剂入口,位于燃料脱碱装置的下部,用于向高碱燃料脱碱装置输送辅气化剂,其中燃料和辅气化剂在加热下发生脱碱反应;脱碱固体燃料溢流口,位于燃料脱碱装置的上部,用于输出脱碱反应产生的脱碱固体燃料;富碱燃料气出口,位于燃料脱碱装置的上部,用于输出脱碱反应产生的富碱燃料气。其中通过燃料脱碱装置,使得燃料中的碱金属在高温及流化作用的条件下充分析出,从而可以成功将燃料转化为常规低碱含量固体燃料。“加热”的方式可以是借助外热源方式,或者是通过燃料自身的部分燃烧放热实现加热。
根据本发明的实施例,脱碱装置的壁面与水平面夹角在45~90°之间任一角度,以增加燃料脱碱装置中上部横截面积,降低流化速度,强化脱碱反应。
根据本发明的实施例,燃料脱碱装置的中部还带有二次风喷口,二次风喷口与水平面的夹角为0~60°之间任一角度。通过二次风喷口通入二次风,会强化燃料脱碱装置内粒扰动及反应,从而促进脱碱过程,所述二次风为水蒸气或贫氧水蒸气。
燃料脱碱装置流化速度为0.2-1.0m/s,辅气化剂为水蒸气,或贫氧水蒸气,或者其他含氧气体。
优选地,燃料脱碱装置的气化剂为水蒸气。试验研究表明,水蒸气做流化介质时,一方面,可以实现燃料充分流化,使燃料发生干燥、热解和脱碱反应;另一方面,水蒸气可以促进燃料溶性和醋酸溶性碱金属的析出,大幅降低燃料中的碱金属含量,从而抑制结渣。再者,水蒸气与燃料焦间的反应速率显著低于与氧气间的燃烧气化反应,反应不完全,燃料脱碱装置内碳浓度高,灰浓度低,可以较好的控制反应进程、避免燃料脱碱装置内结渣问题的发生。可选地,可以贫氧水蒸气为流化介质,保持燃料脱碱装置为还原性气氛并维持较高的温度,以促进燃料脱碱装置内的干燥、热解、气化及脱碱过程从而促进碱金属的析出以获得低碱含量的固体燃料。
根据本发明的实施例,该燃料脱碱装置还包括循环半焦入口,位于燃料脱碱装置的上部,用于向燃料脱碱装置输送循环半焦燃料。利用循环半焦作为热载体为燃料脱碱装置提供热源。
根据本发明的实施例,还提供了使用上述燃料脱碱装置的燃料脱碱方法,包括:自燃料脱碱装置上部的高碱燃料入口向燃料脱碱装置输送燃料;自燃料脱碱装置下部的辅气化剂入口向燃料脱碱装置输送辅气化剂,使高碱燃料和辅气化剂在加热下发生脱碱反应;自燃料脱碱装置上部的脱碱固体燃料溢流口输出脱碱反应产生的脱碱固体燃料;自燃料脱碱装置上部的富碱燃料气出口输出脱碱反应产生的富碱燃料气。将燃料直接通入到燃料脱碱装置内,使得燃料中的碱金属在高温及流化作用的条件下充分析出,实现了对燃料中碱金属的高温、高效、在线脱除,从而可以成功将燃料转化为常规低碱含量固体燃料,可有效避免结渣问题。解决了传统水洗法存在的水资源消耗量大、不可溶碱金属去除率低等缺点,避免了水洗法带来的二次污染。
根据本发明的实施例,脱碱反应的温度为500~900℃,优选为700~900℃。既有利于将燃料中的碱金属最大程度的转移至气相中,从而获得脱碱固体燃料,也能抑制结渣问题发生。
根据本发明实施例,还提供了一种循环流化床气化装置,如图1至3所示,包括:主床,自下而上分别包括氧化区和还原区,主床的位于氧化区的底部设置有主气化剂入口和返料口,主床的位于还原区的位置设置有富碱煤气入口;下返料器,与主床的返料口连通,用于向氧化区输送脱碱固体燃料;辅床,即燃料脱碱装置,辅床的脱碱固体煤溢流口与下返料器连通,用于向下返料器输送脱碱固体煤,辅床的富碱煤气出口与主床的富碱煤气入口连通,用于向主床的还原区输送富碱煤气。辅床和下返料器的设置及二者的配合是本发明的关键,同时也体现了本发明突出的技术优势:下返料器不仅具有常规返料器的功能,同时还具有隔绝碱金属蒸汽进入气化炉底部的功效,以及实现辅床还原区和主床底部氧化区隔离的功效。具体描述如下:
(1)下返料器可以将辅床生成的高温脱碱固体燃料成功输送到主床底部密相区,从而实现物料由低压向高压的输送,并与主床底部通入的主气化剂进行燃烧、气化反应。与高碱燃料相比,由于高温脱碱固体燃料中的碱金属含量大幅降低,极大的抑制了炉膛底部结渣问题的发生。本方案中,将辅床生成的高温脱碱固体燃料通入到主床,成功将高碱燃料的利用难题简化为常规低碱燃料的优质利用,因此不存在结渣问题,从而可实现纯烧高碱煤气化炉的连续稳定运行。
(2)基于下返料器内固体物料的料封作用,下返料器可实现主床与辅床的高效物理隔离,在辅床内生成的粗燃料气及气相碱金属蒸汽通过连通管输送到主床内远离底部高温区的区域,避免进入到主床的高温区域,实现与脱碱燃料的有效隔离,从而有效抑制富碱粗燃料气与炉膛底部高温、高灰浓度固体物料接触而引发结渣。
(3)设置辅床的目的是在还原性气氛、不结渣的前提下进行高碱燃料的高效、安全脱碱,并为主床的高温气化过程提供脱碱燃料。主床底部为氧化性气氛,辅床为还原性气氛。由此可见,下返料器可实现主床底部氧化区和辅床还原区的隔离,避免主床的气化剂反窜到辅床而引起结渣。
由辅床生成的富碱粗燃料气经连通管通入到主床,优选地,连通管与主床的接口不低于返料口,使富碱粗燃料气通入到主床的还原区、而非氧化区,从而可有效避免与主床底部高温区物料接触、抑制与燃料灰反应生成低温共熔体而引发结渣。进一步地,将富碱粗燃料气通入到主床的还原区具有有益效果,富碱粗燃料气中的碱金属可作为煤焦气化反应的催化剂,促进由主床底部向上输送的高温物料发生气化反应,从而促进碳的转化并提升燃料气化效率。进一步地,将富碱粗燃料气通入到主床还原区的有益效果还在于,可促进高温半焦与富碱粗燃料气间的相互作用,实现辅床生成的焦油的裂解和热解污染物的转化。
根据本发明的实施例,主气化剂入口用于向氧化区通入主气化剂,主气化剂为空气,或氧气和水蒸气的混合气,或氧气、空气和水蒸气的混合气。
根据本发明的实施例,进入辅床的燃料为煤,煤粒径优选为0~40mm。高碱煤水分含量高,机械强度差,易粉化,过细的颗粒不仅会导致给料不畅,还会增加细颗粒的逃逸,使得飞灰含碳量高,导致系统碳转化率和冷煤气效率低。高碱煤循环流化床气化工程实践证明,可以采用0~40mm的高碱煤做为燃料,相对于常规循环流化床气化炉的入炉燃料粒径要求为0~10mm而言,一方面可降低高碱燃料的粉化程度,另一方面可降低备煤成本,具有更高的经济效益。
根据本发明的实施例,主床还包括粗燃料气出口,位于主床的还原区上方;循环流化床气化装置还包括:气固分离器,与主床的粗燃料气出口连通,用于将来自于主床的粗燃料气气固分离,得到循环半焦燃料;上返料器,分别与辅床的循环半焦入口和所述气固分离器连通,用于将所述气固分离器输出的循环半焦燃料输送至所述辅床。上返料器与辅床相连,起到料封作用。实现辅床还原气氛区与主床底部氧化气氛区的有效隔离,避免了碱金属蒸汽与主床底部高温物料直接接触而发生结渣。主床生成的粗燃料气携带气相碱金属蒸汽从气固分离器出口排出,可实现与高温循环半焦的有效分离,避免再次进入系统而增加结渣风险。
根据本发明的实施例,还提供了使用上述循环流化床气化装置进行的高碱循环流化床气化方法,包括:将燃料与辅气化剂通入到辅床以进行脱碱反应,产生脱碱固体燃料和富碱燃料气;将脱碱固体煤通入主床的氧化区,与通入到主床的主气化剂发生气化反应,生成气固物料;将富碱燃料气通入主床的还原区,在还原性气氛下与气固物料相互作用,生成粗燃料气。将高碱燃料与辅气化剂通入到辅床,与被气固分离器分离下来的高温循环半焦混合,发生干燥、热解、部分气化和脱碱反应,生成高温脱碱固体燃料和富碱粗燃料气。将辅床生成的高温脱碱燃料通过下返料器输送到主床底部,与通入到主床的主气化剂发生气化反应,生成高温气固物料;将辅床生成的富碱粗燃料气通过连通管输送到主床返料口及以上位置,在还原性气氛下与主床内的高温气固物料发生相互作用,生成粗燃料气和底渣;主床生成的粗燃料气携带气相碱金属蒸汽从气固分离器出口排出,实现与循环半焦的有效分离;底渣从主床底部排出。底渣为固态。
根据本发明的实施例提供的循环流化床气化方法,主床的流化速度为1.5-5.5m/s,反应温度在850℃和1200℃之间,具体的在气化炉在运行过程中,控制炉膛底部最高温度比燃料灰在弱还原性气氛状态下的软化温度低50~150℃,从而抑制炉膛底部超温结渣。燃料灰指燃料完全燃烧、气化后余下的残渣。
以下列举具体实施例来对本发明的技术方案作详细说明。需要说明的是,下文中的具体实施例仅用于示例,并不用于限制本发明。
实施例1
以下结合图1,以高碱煤作为燃料为例,来说明一种适用于高碱煤的循环流化床气化装置,其包括主床10、气固分离器11、上返料器12、辅床13和下返料器14。
主床10与气固分离器11连通,气固分离器11与上返料器12连通,上返料器12与辅床13连通,辅床13与主床10经连通管连通,辅床13与下返料器14连通,下返料器14与主床10连通。
在辅床13上设置有燃料入口20、辅气化剂入口21、高温循环半焦入口22、高温脱碱固体燃料溢流口23和富碱粗燃料气出口24。
在主床10上设置有主气化剂入口30、富碱粗燃料气入口31、主床返料口32、粗燃料气出口33和底渣出口34。
高碱煤从燃料入口20进入到辅床13,主床10生成的粗煤气经气固分离器11分离后的高温循环半焦从气固分离器11的底部进入到上返料器12,上返料器12具有将高温循环半焦输送到辅床的功能,同时实现气固分离器11与辅床13的有效隔离,避免辅气化剂入口21通入的辅气化剂和辅床13内生成的富碱粗煤气反窜到气固分离器11而导致分离效率降低问题。高温循环半焦经上返料器12输送至辅床13,与加入的高碱燃料,在重力的作用下向辅床13底部移动;辅床13的底部设置有辅气化剂入口21,在辅气化剂的作用下,辅床13底部的物料向上运动,并与新鲜的高碱燃料充分混合、换热,实现新鲜高碱燃料在辅床13内进行干燥、热解、部分气化和脱碱反应,生成高温脱碱固体燃料和富碱粗煤气。通过调控辅气化剂的流量,可调控辅床13内提升气体的表观速度,保证物料充分流化及脱碱过程;再者,可调控停留时间,实现对高碱燃料反应进程和脱碱深度的有效控制,获得脱碱固体燃料,降低结渣倾向性。反应后生成的高温脱碱固体燃料从辅床溢流口23离开辅床13,进入下返料器14。
由辅床生成的高温脱碱固体煤经下返料器14通入到主床10,与主床10底部设置的主气化剂入口30通入的主气化剂进行燃烧、气化反应。下返料器14具有将生成的高温脱碱固体煤输送到主床10的功能,同时实现主床10与辅床13的有效隔离,避免由辅床13生成的富碱粗煤气进入到主床10的高温区域,从而有效抑制富碱粗煤气与炉膛底部高温、高灰浓度固体物料接触而引发结渣。进一步地,基于下返料器内物料的料封作用,下返料器还具避免主床10底部通入的主气化剂反窜到辅床的作用,使得辅床内高碱煤在还原性气氛下高效脱碱,从而避免辅床内结渣现象发生。与高碱煤相比,高温脱碱固体煤中的碱金属含量大幅降低,极大的抑制了循环流化床气化装置结渣问题的发生,从而可实现纯烧高碱煤气化炉的连续稳定运行。再者,可通过调控主气化剂的流量来控主床10内提升气体的表观速度,实现对反应过程的强化调控,从而提升碳转化率和冷煤气效率。
由辅床13生成的富碱粗煤气经连通管通入到主床10,优选地,连通管与主床的接口不低于返料口,使富碱粗煤气通入到主床的还原区、而非氧化区,从而可有效避免与炉膛底部高温区物料接触、抑制与煤灰反应生成低温共熔体而引发结渣。在辅床内生成的富碱粗煤气可输送到主床返料口及以上位置,避免了与炉膛底部高温区物料直接接触、反应生成低温共熔体而引发结渣。富碱粗煤气中的碱金属可作为燃料焦气化反应的催化剂,促进由主床底部向上输送的高温物料发生气化反应,促进高碱煤中c的转化率提升燃料气化效率
在主床10内,最终生成的粗煤气携带碱金属蒸汽从主床10顶部离开、进入气固分离器11,碱金属蒸汽随煤气离开反应系统。主床10生成的底渣从主床10底部排出系统。
实施例2
参见图2,为本发明的一个优选实施例,与实施例1的结构类似,主要区别在于,辅床13带一定的倾斜角度。辅床13的壁面与水平面之间的夹角α在45~90°之间。辅气化剂从辅气化剂入口通入到辅床13底部,在携带辅床13底部物料向上运动的过程中,与新鲜的高碱煤和上返料器12输送来的高温半焦混合、反应的过程中,形成一定量的热解气和气化气,因体积膨胀使得辅床13中上部的速度高于底部速度,会增加细颗粒物的逃逸、影响新鲜高碱燃料的停留时间及脱碱反应。因此,通过对辅床13设置倾斜角度,会增加辅床中上部的横截面积,从而降低其流化速度,强化高碱煤在辅床13内的脱碱反应。
实施例3
参见图3,为本发明的另一个优选实施例,,与实施例1的结构类似,主要区别在于,辅床13带二次风喷口,二次风喷口结构如图4所示。辅床13的二次风气化剂入口与水平面之间的夹角β在0~60°之间。二次风的通入,会强化辅床13内的颗粒扰动及反应,从而促进脱碱过程。
以上所述的具体实施例,对本发明的目的、技术方案和有益效果进行了进一步详细说明,应理解的是,以上所述仅为本发明的具体实施例而已,并不用于限制本发明,凡在本发明的精神和原则之内,所做的任何修改、等同替换、改进等,均应包含在本发明的保护范围之内。
本文用于企业家、创业者技术爱好者查询,结果仅供参考。