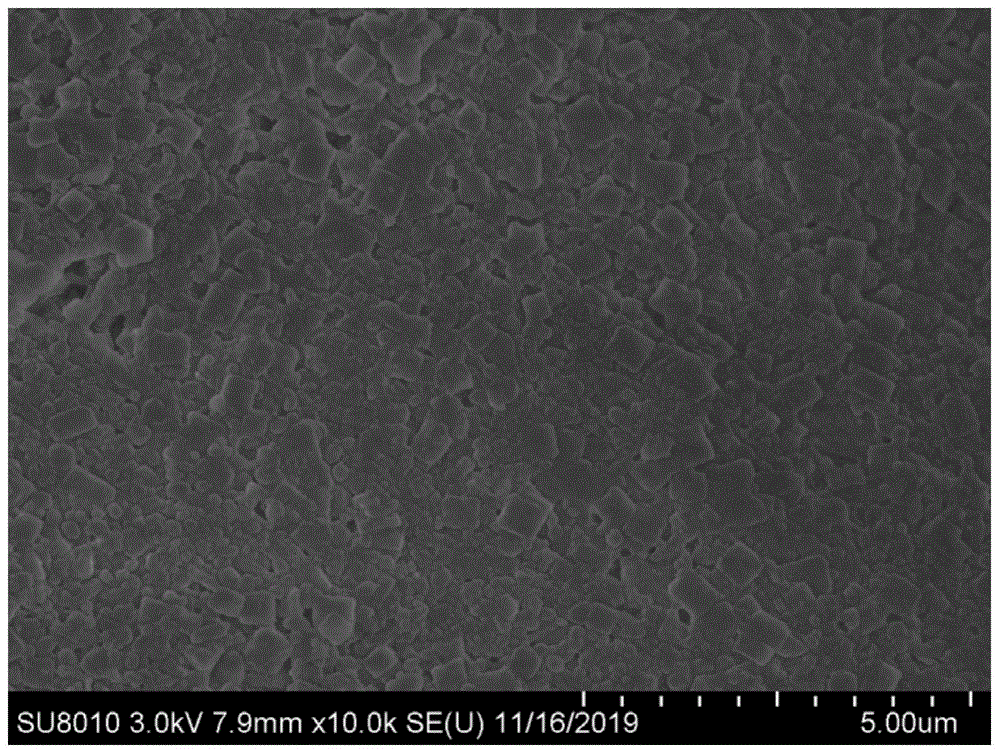
本发明属于润滑脂技术领域,具体涉及一种用于润滑脂的纳米皂基稠化剂前驱体及其制备方法与应用。
背景技术:
润滑脂作为润滑剂中一个独立的工业部分,因其优良的抗水性能、胶体稳定性、抗磨性能及宽的工作温度范围等特点而被广泛应用于工业机械、农业机械、交通运输行业、电子信息行业等领域。润滑脂主要由稠化剂稠化基础油并加入添加剂而制得,根据其所使用的稠化剂种类可以将其分为金属皂基润滑脂、有机润滑脂、烃基润滑脂及无机润滑脂。
近年来,全球润滑脂产量基本保持稳定。2017年全球润滑脂产量为116.7万吨,中国润滑脂产量占全球产量的34.97%。据统计,其中中国锂基润滑脂产量达到23.34万吨,占所有润滑脂的55.35%。但随着近年来新能源汽车市场的爆发,对蓄电池的需求飞速增长,作为重要原材料的氢氧化锂也随之价格暴涨,锂基润滑脂产品成本随之急增。而氢氧化钙价格多年保持稳定,这就为钙基润滑脂的发展带来了契机。钙基润滑脂因其生产设备与工艺简单、原材料价格较低、投资少等原因,在一些中小型企业中大量生产,其生产方式是采用常压釜皂化反应工艺生产。
中国专利cn109797032a公开一种新型无水钙基润滑脂及制备方法。其制备方法包括以下步骤:稠化,把脂肪酸、氢氧化钙、1/3~2/3的基础油投入到压力釜中,加入水,搅拌混合,反应时间为1.5h~2.5h,压力釜内压力为0.11~0.20mpa;脱水,升温至110℃~120℃,压力釜内压力为0.21~0.35mpa,保持温度并持续搅拌30~50min;成脂,持续升温至125℃~140℃,保持温度4~8min后停止加热;将剩余的基础油加入到压力釜内,持续搅拌25~35min,皂化成脂。
高宇航等(无水钙基润滑脂的研制及性能评价,石油商技,2017年第4期)公开一种无水钙基润滑脂的制备方法,投料皂化:首先在压力釜中加入3/4的基础油,然后将12-羟基硬脂酸、氢氧化钙和一定量的水加入压力釜中,混合升温至(100±1)℃并持续加压开始皂化反应。升温炼制:继续缓慢加压升温至(140±1)℃后,保持一定的压力与时间,使酸、碱完全反应,不均匀或团聚物分散打开。泄压降温,泄压后,加入剩余急冷油降至一定温度后,保温30min,控制皂纤维结构的稳定形成。加剂后处理:温度降至(80±1)℃以下时,加入添加剂,再使用均质机处理并经脱气釜脱气完成生产。
赵世民(钙基润滑脂水化过程的控制,湖南化工,第28卷第5期,1998年10月)公开一种钙基润滑脂的制备方法和形成原理,讨论分析了水化过程中容易出现的水加不进、成脂软等问题及其解决方法。文中着重表明如果没有水参与,形成的润滑脂极不稳定,往往不能成脂,故把水叫做稳定剂,它是形成钙基脂必不可少的组分。水化过程是钙基脂制备的最重要步骤之一,必须按要求仔细操作,才能制备出合乎质量要求的产品。
上述文献的生产过程中突显出几个关键问题:由于钙基润滑脂的生产原料ca(oh)2固体颗粒微溶于水,且溶解度随温度上升而下降,所以需要加水参与皂化反应;皂化反应中,未溶解氢氧化钙固体不能参与反应,易形成皂颗粒,过滤困难;另一方面,氢氧化钙在基础油中,与脂肪酸的皂化反应需要在100℃以上温度进行,且酸碱中和是放热反应,反应生成的水汽化导致出现涨罐现象;同时为防止皂颗粒形成,需加入大量水,导致泄压困难和皂跑出;排水过程也增加了能耗,延长了工时;此外产品中由于含水或排水不干净导致经常出现润滑脂较软或不成脂现象。
上述文献的生产过程中存在一个共同的步骤,就是生产过程中必须加入水,而加入水后带来的产品质量不稳定、增加能耗等问题一直都无法很好的解决。
同样,由于氢氧化锂和氢氧化钙都是碱,其皂化成脂过程类似,锂基润滑脂的生产过程中也或多或少遇到钙基润滑脂生产过程中遇到的工艺问题和产品质量问题。
纳米材料指几何尺寸达到纳米尺度并具有特殊性能的材料,其主要类型包括零维纳米颗粒与粉体、一维纳米碳管和纳米线、二维纳米薄膜及三维纳米晶块体材料等。纳米材料结构的特殊性(如大的比表面、小尺寸效应、界面效应、量子效应和量子隧道效应)赋予了其不同于传统材料的各种独特性能,其中尤以特异的电学、热学、磁学、光学及力学性能等最为引人注目,具有重要的应用和开发价值,而纳米材料的摩擦学应用同样立足于其独特的性能。
目前,传统润滑油脂依然占据着当今润滑油脂市场的主导地位,但其在高承载能力及环境友好等方面的应用局限性不容忽视。正因为如此,新型润滑油脂的研究开发受到了国内外摩擦学家和润滑油品研制开发人员的广泛关注,其中纳米颗粒材料作为润滑油添加剂的研究更成为国内外关注的焦点之一。然而,作为润滑脂的主要组成的稠化剂采用纳米材料参与皂化制备几乎未见报道。
针对以上问题,有必要提供一种高反应活性的皂基稠化剂前驱体,从而克服掉以上润滑脂生产工艺过程中的技术问题和产品质量问题。
技术实现要素:
本发明的目的是提供一种用于润滑脂的纳米皂基稠化剂前驱体,该纳米皂基稠化剂前驱体应用于制造润滑脂时,可以在不改变润滑脂生产工艺的同时大幅提高润滑脂生产过程中的皂化反应速度并使皂化反应完全,缩短反应工时;克服皂化反应过程中的跑皂,涨罐问题;同时由于其反应过程不用加水反应,即可直接生成皂基脂,降低了生产过程中能耗,所制得的润滑脂产品的性能大幅提高;本发明同时提供了用于润滑脂的纳米皂基稠化剂前驱体的制备方法与应用。
本发明所述的用于润滑脂的纳米皂基稠化剂前驱体,其是由纳米金属氢氧化物颗粒、表面活性剂和液体溶剂组成的分散体。
纳米金属氢氧化物颗粒为纳米氢氧化钙颗粒或纳米氢氧化锂颗粒中的一种或两种。
纳米金属氢氧化物颗粒的颗粒粒度≤2000nm,优选为5-500nm,更优选为5-100nm。
纳米金属氢氧化物颗粒是由金属氢氧化物颗粒经砂磨机砂磨、球磨机球磨、胶体磨研磨或均质机均质至金属氢氧化物粒径到纳米级后制备获得或者直接市场购买纳米金属氢氧化物粉体获得。
表面活性剂为脂肪酸基类改性剂、磺酸基类改性剂、硅烷偶联剂或钛酸酯偶联剂中的一种或几种,优选为脂肪酸基类改性剂、磺酸基类改性剂或钛酸酯偶联剂中的一种或几种。
脂肪酸基类改性剂为棕榈酸、油酸、亚油酸或硬脂酸中的一种或几种。
液体溶剂为矿物基础油、合成基础油或植物油基础油中的一种或几种,优选为矿物基础油。
纳米金属氢氧化物颗粒的质量为纳米皂基稠化剂前驱体总质量的10-60%,表面活性剂的质量为纳米皂基稠化剂前驱体总质量的0.1-10%,液体溶剂的质量为纳米皂基稠化剂前驱体总质量的30-85%。
纳米金属氢氧化物颗粒的质量优选为纳米皂基稠化剂前驱体总质量的30-50%。
表面活性剂的质量优选为纳米皂基稠化剂前驱体总质量的0.5-5%。
本发明所述的用于润滑脂的纳米皂基稠化剂前驱体的制备方法是纳米金属氢氧化物颗粒、表面活性剂和液体溶剂经乳化制备形成分散体。
本发明所述的用于润滑脂的纳米皂基稠化剂前驱体的制备方法还可以是在高剪切条件下将金属氧化物颗粒与水在液体溶剂中反应生成纳米金属氢氧化物颗粒并同时经表面活性剂改性、乳化制备形成分散体。
金属氧化物颗粒为氧化钙颗粒或氧化锂颗粒中的一种或两种。
本发明所述的用于润滑脂的纳米皂基稠化剂前驱体的制备方法还可以是超细金属氧化物颗粒、水和表面活性剂在液体溶剂中乳化,反应制备获得。
本发明所述的用于润滑脂的纳米皂基稠化剂前驱体的制备方法还可以是在高剪切条件下将金属氧化物颗粒与水、表面活性剂、液体溶剂在密闭高温高压环境中乳化、反应制备得到。
本发明中在高剪切条件下反应是指在反应过程中对反应体系施加高剪切力,使反应体系的雷诺数在2000-200000、5000-150000、8000-100000范围内。高雷诺数使反应区的混合程度较高,达到微观混合的程度。在反应步骤中施加高速搅拌和剪切力的设备,如市售的高剪切乳化机、高剪切均质机、超重力反应机都可以作为提供高剪切环境的设备使用。
乳化可以是液体和液体之间的作用,具体说,就是一种液体通过乳化设备以极微小液滴均匀地分散在互不相溶的另一种液体中的作用。乳化也可以是固体颗粒和液体之间的作用,具体说,是亲水性固体颗粒在适当的表面活性剂改性后,通过乳化设备,以极微小颗粒形式被分散在油中;或者亲油性颗粒在适当的表面活性剂改性后,通过乳化设备,以极微小颗粒形式被分散在水中;形成乳状液,该过程叫乳化。乳化一般通过乳化设备来实现。
乳化设备:制备乳状液的机械设备主要是乳化机,它是一种使油、水两相;或油、亲水性颗粒;或水、亲油性颗粒混合均匀形成乳液的设备,乳化机的类型主要有三种:乳化搅拌机、胶体磨和均质器。乳化设备也可以是球磨机或砂磨机,其是在将颗粒研磨至更微小的颗粒同时改性并实现乳化。
本发明中提到的乳化特指亲水性金属氢氧化物、金属氧化物颗粒在适当的表面活性剂改性后,在乳化设备中,以极微小颗粒形式被分散在基础油中。
本发明所述的用于润滑脂的纳米皂基稠化剂前驱体的应用是采用脂肪酸、纳米皂基稠化剂前驱体、基础油和添加剂制备润滑脂。
本发明采用纳米皂基稠化剂前驱体合成润滑脂的原料具体组成是:以质量百分比计,
脂肪酸为棕榈酸、油酸、葵二酸、亚油酸或硬脂酸中的一种或几种。
基础油为矿物基础油、合成基础油或植物油基础油中的一种或几种。
添加剂为润滑脂领域常用的添加剂种类,例如包括防锈剂、抗氧剂或极压抗磨剂中一种或几种。
本发明所用到的防锈剂、抗氧剂、极压抗磨剂是润滑脂领域常用的防锈剂、抗氧剂、极压抗磨剂。
本发明所述纳米皂基稠化剂前驱体的应用是指利用纳米皂基稠化剂前驱体参与润滑脂合成过程中的皂化反应并稠化基础油,从而制备出高性能的纳米皂基润滑脂。
本发明所述的用于润滑脂的纳米皂基稠化剂前驱体的应用具体是反应釜中加入基础油、脂肪酸和纳米皂基稠化剂前驱体混合升温80-110℃开始皂化反应,继续缓慢升温至115-180℃进行炼制,使酸碱完全反应,加入冷基础油进行冷却降温至80℃以下,调整体系酸碱度,加入添加剂,并用均质机均质处理,完成生产。
本发明提供的纳米皂基稠化剂前驱体可用于制造钙基润滑脂、锂基润滑脂、复合钙基润滑脂、复合锂基润滑脂、复合钙锂基润滑脂、复合磺酸钙基润滑脂以及含金属钙、锂的混合皂基润滑脂。
本发明的有益效果如下:
本发明的纳米皂基稠化剂前驱体在润滑脂制备过程中参与皂化,取得了良好的反应效果,却完全不改变现行制备润滑脂的工艺,因此既避免了润滑脂生产工厂因产品升级而需要的设备改造和投资,又可提高产品性能。
与常规采用氢氧化钙和/或氢氧化锂粉体作为皂化反应的反应物相比,本发明毋须加水即可完成皂化反应,由于氢氧化钙和/或氢氧化锂在参与皂化反应时以纳米级形态参与反应,反应活性大幅提高,因此缩短了皂化反应时间,避免了加水参与反应的水汽化导致的涨罐现象;也避免了氢氧化钙和/或氢氧化锂在反应过程中生成皂颗粒、以及后期排水过程带来的大量能源消耗。除了工艺方面带来的有益之处外,采用本发明的纳米含钙皂基稠化剂前驱体生产的润滑脂性能远优于市售含钙润滑脂,使用温度大幅提高。通过市场应用验证,采用本发明的纳米皂基稠化剂前驱体制备得到的纳米含钙润滑脂,可以部分取代甚至完全取代锂基润滑脂成为新的通用型润滑脂,具有较高的性价比,在未来将会有更广阔的市场前景。
附图说明
图1是实施例1制备得到的纳米皂基稠化剂前驱体中氢氧化钙颗粒sem电镜照片。
图2是实施例5制备得到的纳米皂基稠化剂前驱体中氢氧化钙颗粒sem电镜照片。
图3是实施例6制备得到的纳米皂基稠化剂前驱体中氢氧化钙颗粒sem电镜照片。
图4是实施例7制备得到的纳米皂基稠化剂前驱体中氢氧化钙颗粒sem电镜照片。
具体实施方式
以下结合实施例对本发明做进一步描述。
实施例1
准备基础油(sn500)680克,市售高纯氢氧化钙粉体300克,油酸9克,12-羟基硬脂酸11克。
将600克基础油和氢氧化钙粉体用高速剪切乳化机混合均匀后,加入油酸继续高速搅拌0.5hr,体系温度略有升高。停止高速搅拌,将该油相悬浊液转移至行星球磨机,粗磨2hr,再细磨2hr,细磨时选择0.2mm的锆珠,装填系数60%。将该改性氢氧化钙分散体取出、转移至装有高速剪切乳化机的釜中,再将预热至85℃的80克基础油和12-羟基硬脂酸的混合液在乳化机高速运转的条件下加入釜中,继续高速乳化0.5hr,即为含钙皂基稠化剂前驱体。该稠化剂前驱体稳定性良好,在室温条件下静置2个月没有任何沉降。取该稠化剂前驱体几滴于环己烷中超声清洗,洗掉颗粒上的基础油,再取几滴清洗掉基础油的含有氢氧化钙颗粒的环己烷体系滴在铜网上进行sem电镜分析测试,结果见图1,该稠化剂前驱体中氢氧化钙含量为30wt%,颗粒大小约为500nm,颗粒为不规则片状颗粒。
实施例2
准备基础油(sn500)680克,市售高纯氢氧化钙粉体300克,12-羟基硬脂酸11克,苯磺酸9克,环己烷700g。
将氢氧化钙粉体300克和环己烷700g以及苯磺酸9克在行星球磨机球磨2.0hr(球磨机选择0.2mm的锆珠,装填系数60%),然后将600g基础油加入球磨后的混悬体系,旋蒸,蒸出所有环己烷。再将脱除了环己烷的混合体系转移至高速剪切乳化机中高速搅拌,在高速搅拌同时,将已经加热到80℃并充分混合好的基础油和12-羟基硬脂酸混合物91g加入氢氧化钙和基础油的体系中,继续高速搅拌1.0hr。将该改性氢氧化钙分散体取出,即为含钙皂基稠化剂前驱体。该稠化剂前驱体稳定性良好,在室温条件下静置3个月没有任何沉降。该稠化剂前驱体中氢氧化钙含量为30wt%,颗粒大小约为200nm,颗粒为不规则片状颗粒。
实施例3
准备基础油(sn150)580克,市售高纯一水氢氧化锂400克,苯磺酸20克,环己烷700g。
将一水氢氧化锂400克和环己烷700g以及苯磺酸20克在行星球磨机球磨3.0hr(球磨机选择0.2mm的锆珠,装填系数60%),然后将580g基础油加入球磨后的混悬体系,旋蒸,蒸出所有环己烷和氢氧化锂的部分结晶水。将该改性氢氧化锂分散体取出,即为含锂皂基稠化剂前驱体。该稠化剂前驱体稳定性良好,在室温条件下静置3个月没有任何沉降。该稠化剂前驱体中氢氧化锂含量为35wt%,颗粒大小约为300nm,颗粒为不规则片状颗粒。
实施例4
使用如实施例1所述方法和步骤制备皂基稠化剂前驱体。不同之处如下:
市售高纯氢氧化钙粉体300克改为市售高纯氢氧化钙粉体250克和市售高纯一水氢氧化锂50克。该实施例制得的稠化剂前驱体中混合钙锂氢氧化物颗粒大小约为400nm,颗粒为不规则片状颗粒。该稠化剂前驱体中氢氧化钙含量为30wt%。该稠化剂前驱体在室温条件下静置2个月没有任何沉降。
实施例5
准备基础油(sn500)680克,市售3000目高纯氧化钙粉体227克,去离子水73克,油酸9克,12-羟基硬脂酸11克。将9克油酸、11克12-羟基硬脂酸与180克基础油混合并加热至80℃待用,将500克基础油和227克氧化钙粉体加入装有高速剪切乳化机的反应器混合乳化后,快速将200克混合好的油酸、硬脂酸、基础油混合物(基础油180克,油酸9克,硬脂酸11克)和73克水添加进基础油和氧化钙的混合体系,体系温度短暂缓慢上升后迅速突然升高,继续高速剪切乳化2hr;停止反应,最终的反应产物即为含钙皂基稠化剂前驱体。对该含钙皂基稠化剂前驱体中的颗粒采用如实施例1相同方法进行sem电镜分析测试,结果见图2,该实施例制得的稠化剂前驱体中氢氧化钙颗粒为小于1μm的絮状颗粒。该稠化剂前驱体中氢氧化钙含量为30wt%。该稠化剂前驱体在室温条件下静置2个月没有任何沉降。
实施例6
使用如实施例5所述方法和步骤制备皂基稠化剂前驱体。不同之处如下:
装有高速剪切乳化机的反应器为可以承受高温高压的密闭反应器。改性剂中油酸改为苯磺酸9克。对该含钙皂基稠化剂前驱体中的颗粒进行sem电镜分析测试,结果见图3,该实施例制得的稠化剂前驱体中氢氧化钙颗粒大小为30-40nm,颗粒为类球形颗粒。该稠化剂前驱体中氢氧化钙含量为30wt%。该稠化剂前驱体在室温条件下静置3个月没有任何沉降。
实施例7
使用如实施例5所述方法和步骤制备皂基稠化剂前驱体。不同之处如下:
装有高速剪切乳化机的反应器为可以承受高温高压的密闭反应器。反应原材料为:基础油(sn500)477.5克,氧化钙粉体375克,去离子水122.5克,苯磺酸25克。该实施例制得的稠化剂前驱体中氢氧化钙含量约为49.5wt%,对该含钙皂基稠化剂前驱体中的颗粒进行sem电镜分析测试,结果见图4,颗粒大小为30-50nm,颗粒为薄片状不规则颗粒。该稠化剂前驱体在室温条件下静置2个月没有任何沉降。
实施例8
带搅拌的玻璃三口烧瓶作为反应釜。加入240克sn500基础油,12-羟基硬脂酸70克至反应釜,在搅拌同时升温至80-90℃,待12-羟基硬脂酸在基础油中彻底融化,加入36克按照实施例1制备得到的含钙纳米皂基稠化剂前驱体,继续搅拌并升温至110℃左右开始皂化反应30分钟。再加入100克sn500基础油,继续缓慢升温至140℃左右进行炼制,在140℃左右保持3-5分钟,使酸碱完全反应,加入冷sn500基础油160克进行冷却降温至80℃以下,调整体系酸碱度,加入添加剂18g(其中防锈剂苯并三氮唑3g、抗氧剂辛基丁基二苯胺3g、极压抗磨剂亚磷酸二正丁酯12g),进一步降温并用三辊机压油3遍处理,完成生产。制得的纳米皂基润滑脂的性能测试数据见表1。
实施例9-12
使用如实施例8所述物料配比、方法和步骤制备纳米皂基润滑脂。不同之处如下:
实施例9-12的纳米皂基稠化剂前驱体是分别采用实施例4、5、6、7的方法和步骤制备得到的纳米皂基稠化剂前驱体。此外,实施例11中含钙纳米皂基稠化剂前驱体添加量36g改为22g。制得的纳米皂基润滑脂的性能测试数据见表1。
对比例1
带搅拌的玻璃三口烧瓶作为反应釜。加入265克sn500基础油,12-羟基硬脂酸70克,在搅拌同时升温至80-90℃,待12-羟基硬脂酸在基础油中彻底融化,加入10.7克氢氧化钙,继续搅拌并升温至110℃左右,在保持温度不变的情况下搅拌30分钟,皂化反应没有发生。慢慢往体系中滴加水,才开始有皂化反应发生,为保证皂化反应完全,按照中国专利cn109797032a中实施例1中水和氢氧化钙的4倍比例滴加水,加水过程持续30分钟。停止加水10分钟后,加入100克基础油,继续缓慢升温至140℃左右进行炼制,在140℃左右保持20分钟,使酸碱完全反应,加入冷基础油160克进行冷却降温至80℃以下,调整体系酸碱度,加入添加剂18g(其中防锈剂苯并三氮唑3g、抗氧剂辛基丁基二苯胺3g、极压抗磨剂亚磷酸二正丁酯12g),进一步降温并用三辊机压油3遍处理,完成生产。采用该对比例制备出的润滑脂成脂较软,成脂无光泽。所以未进行进一步的润滑脂性能测试。
对比例2
按照中国专利cn109797032a中实施例1的方法制备无水钙基润滑脂。制得的无水钙基润滑脂的性能测试数据见表1。
表1实施例7-11和对比例2的产品性能测试数据对比结果
对实施例8-12制备得到的润滑脂进行性能评估发现:实施例8-12制备得到的润滑脂滴点和其它性能都明显高于gb/t491-2008《钙基润滑脂》标准的要求。经和gb/t7324-2010《通用锂基润滑脂》标准进行对比发现,除滴点外,各项指标均可以满足gb/t7324-2010《通用锂基润滑脂》的要求,且在低温性、抗水性、极压剂感受性、抗剪切性能上优于通用锂基润滑脂。润滑脂寿命试验结果表明,实施例8-12制备得到的润滑脂可以满足120℃条件下使用要求。流变特性则显示和通用锂基润滑脂比,具有更强的形变控制力、更好的润滑性及更稳定的结构保持力。和对比例2中的无水钙基脂相比,部分性能相当,部分性能优于对比例2的无水钙基润滑脂。
目前,生产通用型锂基润滑脂和本发明生产的钙基润滑脂所用碱量均为1-2%,而氢氧化锂价格比氢氧化钙的价格高70-80倍,由此导致润滑脂成品原材料价格相差1500-3000元/t,因此在产品性能相当的条件下,采用本发明生产的皂基稠化剂前驱体参与生产的纳米皂基润滑脂和通用型锂基润滑脂比具有更高的性价比,并且生产周期缩短,生产能耗降低。本发明在工艺上可以起到节能、提高生产效率的作用,产品性能、价格上优于现有同类产品。
本文用于企业家、创业者技术爱好者查询,结果仅供参考。