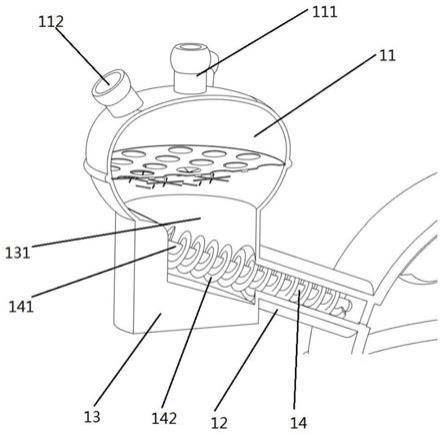
1.本发明涉及环氧防锈漆制备工艺系统领域。
背景技术:
2.环氧防锈漆是适用于各类钢结构的防锈防蚀,也可以作为混凝土防腐蚀底漆;环氧防锈漆涂抹到金属钢材表面,能避免钢材结构受到腐蚀生锈,减少钢材结构的损坏,提高钢材结构的安全性;将环氧防锈漆作为底漆对底材附着力好,并且施工性能良好,具有耐水、耐油和耐化学品的好处。
技术实现要素:
3.发明目的:为了克服现有技术中存在的不足,本发明提供一种环氧防锈漆制备方法工艺系统、制备方法与组成配比能有效的快速的生产制备出优良的环氧防锈漆的效果。
4.技术方案:为实现上述目的,本发明的技术方案如下:
5.环氧防锈漆制备方法工艺系统,包括混料结构和粉碎结构;所述粉碎结构包括粉碎腔室;所述粉碎腔室顶部一侧连通设置混料结构;所述混料结构包括混料室和输导管;所述混料室顶部通过多个导料管口与外界连通;所述混料室底部通过输导管连通于粉碎腔室;所述混料室内混合结构扭转分切混合料下漏至输导管内,且所述粉碎腔室内挤压破碎结构挤压破碎混合料;提高环氧防锈漆的分散效果。
6.进一步的,所述混料室为球型腔室;多个所述导料管口阵列间距固设于混料室顶部;多个所述导料管口对应混料室一端呈聚拢式朝向混料室中心方向倾斜设置;所述导料管口远离混料室一端渐进增大,为包裹端;所述包裹端为弹性结构,且所述包裹端对应包裹于储料罐的出料端上;所述导料管口内对应固设有分割条;所述分割条沿导料管口直径方向设置,且多根所述分割条交叉错位设置;多个所述分割条沿导料管口轴向间距设置;利于填料溶剂分散开,便于搅拌充分混合。
7.进一步的,所述混合结构包括转动凸板;所述转动凸板对应阻拦设置于混料室中部,且多个所述导料管口的出料端对应朝向于转动凸板内凹中部;所述混料室中部内壁环向开设有安装槽;所述转动凸板对应边缘对应安装于安装槽内,所述安装槽内混料室内壁上旋转装置的驱动端与转动凸板边缘驱动连接;便于多种添加溶剂混合。
8.所述转动凸板侧壁上间距贯穿开设有若干通孔;所述通孔上对应罩盖有弹性壳体,所述弹性壳体边缘对应固定于通孔内壁;所述弹性壳体为半圆型片状结构,且所述弹性壳体对应朝向转动凸板外凸一侧凸出设置;所述弹性壳体中部贯穿开设有下漏条口;所述下漏条口为十字交叉型;所述下漏条口将弹性壳体分割为多片切片;多片所述切片为弹性结构;所述下漏条口开口随转动凸板上混合料的质量相应的增大或减小,且多片所述切片之间相互展开分离或聚拢;利于分切多种添加溶剂,提高分散效果。
9.进一步的,所述切片边缘间距开设有若干缺口;若干所述缺口对应于下漏条口连通;所述缺口开口位置设置有固定杆;所述固定杆两端对应固定于缺口内壁;所述活动杆侧
壁上间距固设有若干刺条,且若干所述刺条对应处于缺口内以及下漏条口内,且若干所述刺条在下漏条口内形成牙齿状;若干所述突刺长度向弹性壳体边缘方向渐进缩短;所述转动凸板带动弹性壳体转动,且混合料通过下漏条口呈螺旋状下漏输导管内,且若干所述刺条割切于下漏的混合料;利于多种添加溶剂切割分离后重组。
10.所述转动凸板外凸侧壁若干弹性壳体之间设置有切割结构;所述切割结构包括旋转杆;所述转动凸板侧壁上旋转装置与旋转杆一端驱动连接;所述旋转杆另一端侧壁环向固设有若干切割条;所述下漏条口的出口端处于若干切割条运动轨迹范围内,且相邻切割结构的切割条层叠设置;片切添加溶剂,提高分散效果。
11.进一步的,所述混料室底部固定连通设置有固定座;所述混料室通过固定座内部空腔与输导管连通;所述输导管由固定座向下倾斜延伸连通于粉碎腔室顶部;所述空腔内设置有螺旋输送结构;所述螺旋输送结构包括旋转轴;所述固定座侧壁上旋转装置与旋转轴一端驱动连接;所述旋转轴另一端贯穿空腔倾斜延伸至输导管内;所述旋转轴侧壁上螺旋环绕固设有螺旋叶片;所述输导管出料端内对应设置有控制阀;通过螺旋输送结构将多种添加溶剂搅拌混合。
12.进一步的,所述粉碎腔室顶部为半圆型;所述挤压破碎结构包括冲压结构和配合结构;所述冲压结构对应设置于粉碎腔室顶部,所述配合结构对应设置于粉碎腔室底部;所述冲压结构向下运动冲撞于配合结构,且所述冲压结构挤压冲散于配合结构上混合料;冲压结构和配合结构相互冲击挤压破碎混合料内的颗粒物,达到更好的分散效果。
13.进一步的,所述冲压结构包括冲击块和伸缩轴;所述冲击块对应嵌合设置于粉碎腔室顶部,且所述冲击块底部高于输导管;所述粉碎腔室顶部的伸缩装置与伸缩轴一端驱动连接;所述伸缩轴另一端固定于冲击块顶部;所述冲击块底面上固设有若干半圆突凸块,若干所述半圆凸块之间间距设置;
14.所述配合结构包括底盘;所述底盘嵌合于粉碎腔室底部;且所述粉碎腔室底部的推顶装置驱动端与底盘驱动连接;所述冲击块底面与底盘表面对应设置,且所述冲击块底面面积小于底盘表面面积;所述底盘表面挖设有若干聚料槽;若干所述聚料槽与半圆凸块对应嵌合设置;所述聚料槽内开设有多个活动孔;所述活动孔内对应嵌设有活动杆;所述活动杆嵌入一端与活动孔底部之间夹设有弹性件;所述活动杆另一端突出于活动孔,若干所述活动杆突出端之间形成卡料区;所述冲击块对应挤压粉碎腔室内混合料,且所述半圆凸块冲撞粉碎聚料槽内卡料区中的填料;半圆凸块冲击卡料区内混合料颗粒挤压破碎。
15.进一步的,所述粉碎腔室侧壁环套有过滤腔;所述粉碎腔室顶部侧壁环向间距开设有若干溢出弧槽;所述粉碎腔室通过若干溢出弧槽与过滤腔连通;所述过滤腔内壁与粉碎腔室侧壁间距设置;所述过滤腔内对应可拆卸设置有过滤网结构;所述底盘带动混合料向上运动溢出于粉碎腔室流入过滤腔内;所述过滤腔底部包围粉碎腔室设置,为汇聚腔;所述汇聚腔为半圆型腔体结构;所述汇聚腔底部通过输料管连通设置有调制结构;通过调制结构更好的将混合料调制混合。
16.进一步的,所述调制结构包括调制室;所述输料管的出料端连通于调制室顶部;所述调制室内设置有调漆装置;所述调漆装置包括转动杆;所述调制室顶部转动装置与转动杆一端驱动连接;所述转动杆另一端向下延伸至调制室中部;所述转动杆延伸端侧壁固设有若干调制条;所述调制条远离转动杆一端向下延伸弯曲设置;若干所述调制条之间间隙
设置,且若干所述调制条之间形成齿爪结构;通过齿爪结构充分分散混合料。
17.进一步的,第一步:多种配料分别通过多个导料管口添加到混料室内;混合结构将混合的混合料通过下漏条口切割呈螺旋状下漏到输导管内;
18.第二步:通过转动凸板分割重组以及输导管内螺旋输送结构翻搅预先对多种添加料进行搅拌混合,然后通过输导管输送到粉碎腔室内;
19.第三步:所述粉碎腔室内混合料通过冲压结构和配合结构的挤压运动,充分分散开;并且冲击块冲撞挤压粉碎底盘上的未溶解的填料颗粒;
20.第四步:所述底盘推动混合料溢出到过滤腔内经过过滤后通入到调制室内,通过调制装置调制分散。
21.有益效果:本发明能通过多次搅拌混合更好的将多种添加溶剂均匀的分散开;包括但不限于以下有益效果:
22.1)旋转装置驱动转动凸板转动,这样混合料通过下漏条口时,混合料就被下漏条口分割,并且混合料呈螺旋状下落,这样利于混合料重组时添加料更充分的分散开;
23.2)在冲击块运动过程中,混合料被挤压从冲击块侧壁运动,相应的造成混合料运动翻滚,起到很好的搅动分散的效果;同时半圆凸块能将卡料区内聚集的颗粒填料冲击粉碎,提高分散的程度。
附图说明
24.附图1为环氧防锈漆制备系统结构图;
25.附图2为混料结构图;
26.附图3为导料管口结构图;
27.附图4为混合结构图;
28.附图5为弹性壳体结构图;
29.附图6为下漏条口结构图;
30.附图7为刺条结构图;
31.附图8为粉碎结构图;
32.附图9为挤压破碎结构图;
33.附图10为卡料区结构图;
34.附图11为调制结构图。
具体实施方式
35.下面结合附图对本发明作更进一步的说明。
36.如附图1
‑
11:环氧防锈漆制备方法工艺系统,包括混料结构1和粉碎结构2;所述粉碎结构2包括粉碎腔室21;所述粉碎腔室21顶部一侧连通设置混料结构1;所述混料结构1包括混料室11和输导管12;所述混料室11顶部通过多个导料管口111与外界连通;所述混料室11底部通过输导管12连通于粉碎腔室21;所述混料室11内混合结构3扭转分切混合料下漏至输导管12内,且所述粉碎腔室21内挤压破碎结构4挤压破碎混合料;换料结构先将添加的添加溶剂混合分散再重组,然后再经过挤压破碎结构更进一步的冲击搅拌混合,最终制备出优良的环氧防锈漆。
37.所述混料室11为球型腔室;多个所述导料管口111阵列间距固设于混料室11顶部;多个所述导料管口111对应混料室11一端呈聚拢式朝向混料室11中心方向倾斜设置;所述导料管口111远离混料室11一端渐进增大,为包裹端112;所述包裹端112为弹性结构,且所述包裹端112对应包裹于储料罐的出料端上;所述导料管口111内对应固设有分割条113;所述分割条113沿导料管口111直径方向设置,且多根所述分割条113交叉错位设置;多个所述分割条113沿导料管口111轴向间距设置;储料罐内添加溶剂通过导料管口添加到混合室内,并且导料管口内的分割条先将添加溶剂以及粉末分散,利于这些添加剂更好的在混合室内混合。
38.所述混合结构3包括转动凸板31;所述转动凸板31对应阻拦设置于混料室11中部,且多个所述导料管口111的出料端对应朝向于转动凸板31内凹中部;所述混料室11中部内壁环向开设有安装槽114;所述转动凸板31对应边缘对应安装于安装槽114内,所述安装槽114内混料室11内壁上旋转装置的驱动端与转动凸板31边缘驱动连接;
39.所述转动凸板31侧壁上间距贯穿开设有若干通孔311;所述通孔311上对应罩盖有弹性壳体32,所述弹性壳体32边缘对应固定于通孔311内壁;所述弹性壳体32为半圆型片状结构,且所述弹性壳体32对应朝向转动凸板31外凸一侧凸出设置;所述弹性壳体32中部贯穿开设有下漏条口321;所述下漏条口321为十字交叉型;所述下漏条口321将弹性壳体32分割为多片切片322;多片所述切片322为弹性结构;所述下漏条口321开口随转动凸板31上混合料的质量相应的增大或减小,且多片所述切片322之间相互展开分离或聚拢。旋转装置驱动转动凸板转动,这样混合料通过下漏条口时,混合料就被下漏条口分割,并且混合料呈螺旋状下落,这样利于混合料重组时添加料更充分的分散开。
40.所述切片322边缘间距开设有若干缺口323;若干所述缺口323对应于下漏条口321连通;所述缺口323开口位置设置有固定杆324;所述固定杆423两端对应固定于缺口323内壁;所述活动杆324侧壁上间距固设有若干刺条325,且若干所述刺条325对应处于缺口323内以及下漏条口321内,且若干所述刺条325在下漏条口321内形成牙齿状;若干所述突刺325长度向弹性壳体32边缘方向渐进缩短;所述转动凸板21带动弹性壳体32转动,且混合料通过下漏条口321呈螺旋状下漏输导管12内,且若干所述刺条325割切于下漏的混合料;混合料在下漏过程中,缺口和刺条分割混合料,这样混合料内部就会产出切割口,这样混合料下落到空腔内重组时就能更充分的接触,提高了添加料的分散范围。
41.所述转动凸板31外凸侧壁若干弹性壳体32之间设置有切割结构33;所述切割结构33包括旋转杆331;所述转动凸板31侧壁上旋转装置与旋转杆331一端驱动连接;所述旋转杆331另一端侧壁环向固设有若干切割条332;所述下漏条口321的出口端处于若干切割条332运动轨迹范围内,且相邻切割结构33的切割条332层叠设置;混合料在下落过程中被切割条打散,这样利于打散的混合料更充分的混合分散。
42.所述混料室11底部固定连通设置有固定座13;所述混料室11通过固定座13内部空腔131与输导管12连通;所述输导管12由固定座13向下倾斜延伸连通于粉碎腔室21顶部;所述空腔131内设置有螺旋输送结构14;所述螺旋输送结构14包括旋转轴141;所述固定座13侧壁上旋转装置与旋转轴141一端驱动连接;所述旋转轴141另一端贯穿空腔131倾斜延伸至输导管12内;所述旋转轴141侧壁上螺旋环绕固设有螺旋叶片142;所述输导管12出料端内对应设置有控制阀。重组的混合料通过螺旋输送结构的输送,多种添加料就被翻搅扭转
混合在一起,这样混合料中的添加料就更分散开。
43.所述粉碎腔室21顶部为半圆型;所述挤压破碎结构4包括冲压结构41和配合结构42;所述冲压结构41对应设置于粉碎腔室21顶部,所述配合结构42对应设置于粉碎腔室21底部;所述冲压结构41向下运动冲撞于配合结构42,且所述冲压结构41挤压冲散于配合结构42上混合料;添加料中存在一些添加的粉剂未完全扩散开或者存在一些未完全溶解的颗粒,通过冲压结构和配合结构的冲压粉碎,提高的分散的均匀性。
44.所述冲压结构41包括冲击块411和伸缩轴412;所述冲击块411对应嵌合设置于粉碎腔室21顶部,且所述冲击块411底部高于输导管12;所述粉碎腔室21顶部的伸缩装置与伸缩轴412一端驱动连接;所述伸缩轴412另一端固定于冲击块411顶部;所述冲击块411底面上固设有若干半圆突凸块413,若干所述半圆凸块413之间间距设置;伸缩轴带动冲击块向下冲击配合结构,这样聚集在配合结构上的颗粒粉剂就被冲击破碎,提高了分散的效果。
45.所述配合结构42包括底盘421;所述底盘421嵌合于粉碎腔室21底部;且所述粉碎腔室21底部的推顶装置驱动端与底盘421驱动连接;所述冲击块411底面与底盘421表面对应设置,且所述冲击块411底面面积小于底盘421表面面积;所述底盘421表面挖设有若干聚料槽422;若干所述聚料槽422与半圆凸块413对应嵌合设置;所述聚料槽422内开设有多个活动孔423;所述活动孔423内对应嵌设有活动杆424;所述活动杆424嵌入一端与活动孔423底部之间夹设有弹性件425;所述活动杆424另一端突出于活动孔423,若干所述活动杆424突出端之间形成卡料区426;所述冲击块411对应挤压粉碎腔室21内混合料,且所述半圆凸块413冲撞粉碎聚料槽422内卡料区426中的填料;半圆凸块对应冲击嵌合于聚料槽内,而在冲击块运动过程中,混合料被挤压从冲击块侧壁运动,相应的造成混合料运动翻滚,起到很好的搅动分散的效果;同时半圆凸块能将卡料区内聚集的颗粒填料冲击粉碎,提高分散的程度。
46.所述粉碎腔室21侧壁环套有过滤腔5;所述粉碎腔室21顶部侧壁环向间距开设有若干溢出弧槽211;所述粉碎腔室21通过若干溢出弧槽211与过滤腔5连通;所述过滤腔5内壁与粉碎腔室21侧壁间距设置;所述过滤腔5内对应可拆卸设置有过滤网结构51;所述底盘421带动混合料向上运动溢出于粉碎腔室21流入过滤腔5内;所述过滤腔5底部包围粉碎腔室21设置,为汇聚腔52;所述汇聚腔52为半圆型腔体结构;所述汇聚腔52底部通过输料管53连通设置有调制结构6。底盘向上运动时,推动混合料通过溢出弧槽溢出到过滤腔内,混合料经过过滤腔过滤后能过滤掉不能溶解的大颗粒,提高调制后环氧防锈漆的平滑度。
47.所述调制结构6包括调制室61;所述输料管53的出料端连通于调制室61顶部;所述调制室61内设置有调漆装置62;所述调漆装置62包括转动杆621;所述调制室61顶部转动装置与转动杆621一端驱动连接;所述转动杆621另一端向下延伸至调制室61中部;所述转动杆621延伸端侧壁固设有若干调制条622;所述调制条622远离转动杆621一端向下延伸弯曲设置;若干所述调制条622之间间隙设置,且若干所述调制条622之间形成齿爪结构622;经过过滤后的混合料通过齿爪结构调制混合于基料,这样能使调制出来的防锈漆分散得更均匀。
48.第一步:多种配料分别通过多个导料管口111添加到混料室11内;混合结构3将混合的混合料通过下漏条口切割呈螺旋状下漏到输导管12内;这样下漏的混合料呈螺旋状并且边缘存在若干齿口,这样重组后,能使更多的添加料均匀的分散开。
49.第二步:通过转动凸板31分割重组以及输导管12内螺旋输送结构14翻搅预先对多种添加料进行搅拌混合,然后通过输导管12输送到粉碎腔室21内;通过预先分散搅合能提高搅拌后防锈漆的均匀度。
50.第三步:所述粉碎腔室21内混合料通过冲压结构41和配合结构42的挤压运动,充分分散开;并且冲击块411冲撞挤压粉碎底盘421上的未溶解的填料颗粒;被挤压破碎后的填料颗粒能更好的溶解分散到混合料中,提高分散的均匀性。
51.第四步:所述底盘421推动混合料溢出到过滤腔5内经过过滤后通入到调制室61内,通过调制装置62调制分散;通过搅拌的混合料经过过滤后,桶调制装置调制出分散均匀的优良环氧防锈漆。
52.环氧防锈漆的产品组成配比为:填料、环氧树脂、高纯度氧化铁红、防锈添加剂、助剂、溶剂等,以多元胺加成物为固化剂;并且分为甲、乙双组份包装。
53.环氧防锈漆的物理参数:外观:铁红色;理论用量:约180g/m2,干膜约35
‑
40μm(不含施工损耗);比重:约1.3;不挥发份:≥70%;干燥时间:25℃、表干2小时,实干24小时,完全固化7天。
54.施工说明,配比:甲:乙=5:1;熟化时间:25℃30分钟;适用条件:25℃4小时;施工方法:喷涂、辊涂、刷涂;稀释剂:专用稀释剂,稀释量5
‑
10%;涂装间隔:25℃最短24小时,最长7天;涂装道数:2道;后道配套:环氧涂料、氯化橡胶涂料、丙烯酸、高氯化聚乙烯、丙烯酸、聚氨酯、氟碳树脂涂料,醇酸涂料等。
55.表面处理:钢铁表面可用手工除锈,允许表面有少量锈蚀,但应无松动的氧化皮和油污等杂物,特殊要求应喷砂除锈达sa2.5级或st3级。
56.施工条件:环境气温宜在5
‑
35℃之间,0℃以下固化缓慢,雨、雾天气和相对湿度大于85%时或在夏季炎热天气的强烈阳光下不宜施工。
57.上述是本发明的优选实施方案,相对本技术领域普通技术人员而言,在不脱离本发明原理前提的情况下,还能做出若干修改和润饰,这些修改和润饰同样视为本发明的保护范围。
再多了解一些
本文用于企业家、创业者技术爱好者查询,结果仅供参考。