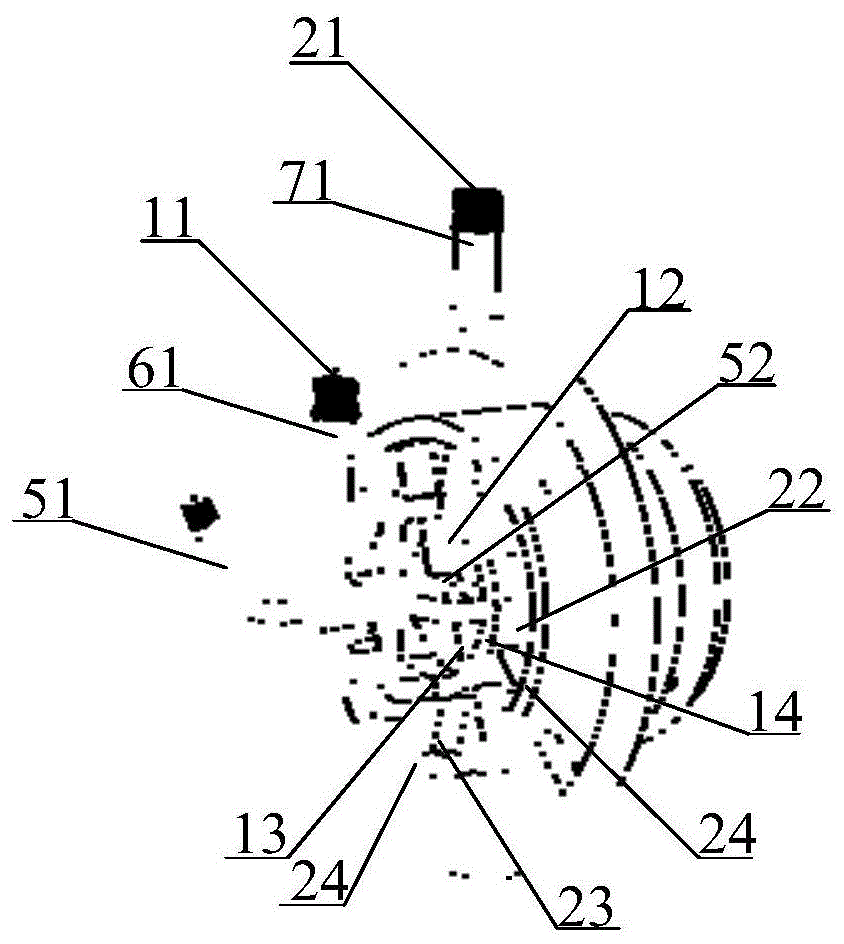
本发明属于燃气轮机燃烧室技术领域,具体涉及一种用于低排放燃气轮机的同轴分级气体燃料燃烧室头部。
背景技术:
燃气轮机污染物排放特性主要与燃烧室内的燃烧模式以及燃烧特性相关。污染物主要包括氮氧化物、一氧化碳、未燃尽碳氢、硫氧化物,其中氮氧化物是燃气轮机燃烧产生的污染物主要来源之一。热力型氮氧化物的生成机理对燃烧室中nox的生成起主导作用,因此降低燃烧室内的主燃区温度是降低氮氧化物排放的有效手段。贫预混燃烧技术可以有效的降低主燃区燃烧温度,进而降低氮氧化物的排放。针对贫预混燃烧技术,国内外研究学者提出的同轴分级贫预混燃烧技术能够有效的控制燃烧室内燃烧温度,从而在保证燃烧稳定性的同时减少污染物生成。
近年来,国内关于低污染燃烧器申请专利很多。专利201710509255.1发明了一种燃气轮机低污染燃烧室单旋流头部结构,中心旋流空气与中心天然气混合、外壁非旋流空气与外壁天然气混合从而进一步在天然气-空气混合腔进行混合,其解决头部自燃的方式是在旋流器外壁上设置切向进气小孔。专利201910312864.x提供的是一种用于气态燃料燃烧室的同轴分级旋流和掺混一体化头部。包含三级掺混/旋流一体化旋流器、燃料导管、燃料腔和燃料支板,其防止回火的方式是在第一级掺混/旋流一体化旋流器内有渐扩吹扫通道。专利202010034769.0发明了一种中心分级贫油预混低污染燃烧室,值班级位于中心,由成膜式空气雾化喷嘴和两级旋流器组成,采用中心分级分区燃烧技术,将有效解决小工况下火焰稳定和大工况下污染排放问题,该专利使用的燃料为燃油,无法适用于气体燃料。
技术实现要素:
本发明的目的在于提供一种用于低排放燃气轮机的同轴分级气体燃料燃烧室头部。
本发明的目的通过如下技术方案来实现:包括值班级燃料流路5、第一级轮毂14、第二级轮毂24、第一级燃料导管61、第二级燃料导管71;所述的第一级轮毂14内壁内侧空间由第一级平直预混通道1和第一级渐缩掺混通道3组成,第一级渐缩掺混通道3的前端与第一级平直预混通道1连通,第一级渐缩掺混通道3的末端设有第一级文氏管31;所述的第二级轮毂24内壁内侧空间由第二级平直预混通道2和第二级渐缩掺混通道4组成,第二级渐缩掺混通道4的前端与第二级平直预混通道2连通,第二级渐缩掺混通道4的末端设有第二级文氏管41;所述的值班级燃料流路包括值班级燃料导管51和中心钝体52;所述的中心钝体52设置在第一级平直预混通道1中,在中心钝体52与第一级轮毂14之间布置有一圈第一旋流叶片13;所述的第一级轮毂14的内壁与外壁之间设有第一级燃料腔62,在第一级轮毂14内壁表面上均匀排布有第一级燃料射流孔63,第一级燃料射流孔63与第一级燃料腔62连通;所述的第二级轮毂24整体位于第一级轮毂14外壁外侧,在第一级轮毂14与第二级轮毂24之间布置有一圈第二旋流叶片23,且第二旋流叶片23全部位于第二级平直预混通道2中,在第二旋流叶片23内部设有旋流叶片燃料腔73,在第二旋流叶片23表面开设有第二级燃料射流孔74,第二级燃料射流孔74与第二级渐缩掺混通道4连通;所述的第二级轮毂24的内壁与外壁之间设有第二级燃料腔72;所述的第二级燃料导管71整体位于第二级轮毂24外壁外侧,第二级燃料导管71通过燃料导管与第二级燃料腔72连通;所述的第一级燃料导管61布置在第一级轮毂14首端前方,第一级燃料导管61通过燃料支路与第一级燃料腔62连通;所述的值班级燃料导管51一端与中心钝体52前端连接,另一端从第一级燃料导管61底部伸出;所述的中心钝体52内部设有值班级燃料腔53,沿中心钝体52的斜坡面以及端面开设有值班级燃料射流孔54,值班级燃料射流孔54与第一级渐缩掺混通道3连通。
本发明还可以包括:
所述的第一级文氏管31出口端面和第二级文氏管41的喉道部位平齐。
所述的中心钝体52的斜坡面以及端面上开设的值班级燃料射流孔54的数量与第一旋流叶片13的数量相同。
所述第一旋流叶片13和第二旋流叶片23均为无损直叶片,叶片旋流角度为30°~60°,叶片个数为6~12个。
本发明的有益效果在于:
本发明中燃烧室头部末端与渐缩掺混段结合的一体化文氏管能有效的将火焰托举从而避免回火,无需布置吹扫空气或在高工况时无需打开值班级扩散燃料;中心值班级与第一级燃料管形成部分套管形式,减少了对来流空气的扰动,从而使各叶间流道气量分配均匀;第二级燃料管布置在第二级轮毂外侧,减小燃料管对第二级空气进气的影响;旋流空气与燃料分别在平直预混通道内预混后进入渐缩掺混通道加强掺混,从而燃料掺混更均匀,降低污染物排放。
附图说明
图1为本发明的总体示意图(从正面看)。
图2为本发明的剖面图。
图3为本发明中第二旋流叶片内部的旋流叶片燃料腔示意图。
图4为本发明的总体示意图(从背面看)。
图5为本发明应用于某模型燃烧室示意图。
具体实施方式
下面结合附图对本发明做进一步描述。
本发明设计了一种用于低排放燃气轮机的同轴分级气体燃料燃烧室头部,由燃料管、两级平直预混段、一级中心值班级、各级燃料腔、渐缩掺混段以及一体化文氏管组成;燃料与空气在平直预混段预混后在渐缩掺混段进一步掺混,并在旋流叶片的作用下形成回流区。点火工况时燃料由值班级燃料流路以及第一级燃料流路供给,并且随着工况提升逐渐增大第一级燃料供给并打开第二级燃料供给,同时逐渐降低值班级燃料的供给直至值班级燃料关闭,第一级与值班级的燃料供给能使燃烧火焰稳定并且迅速引燃第二级燃料。渐缩掺混段以及一体化文氏管能有效地避免回火。该燃烧器结构简单,可以实现稳定燃烧并且具有燃烧效率高且污染物排放低等特点。
一种用于低排放燃气轮机的同轴分级气体燃料燃烧室头部,包括值班级燃料流路5、第一级轮毂14、第二级轮毂24、第一级燃料导管61、第二级燃料导管71;
所述的第一级轮毂14内壁内侧空间由第一级平直预混通道1和第一级渐缩掺混通道3组成,第一级渐缩掺混通道3的前端与第一级平直预混通道1连通,第一级渐缩掺混通道3的末端设有第一级文氏管31;
所述的第二级轮毂24内壁内侧空间由第二级平直预混通道2和第二级渐缩掺混通道4组成,第二级渐缩掺混通道4的前端与第二级平直预混通道2连通,第二级渐缩掺混通道4的末端设有第二级文氏管41;
所述的值班级燃料流路包括值班级燃料导管51和中心钝体52;所述的中心钝体52设置在第一级平直预混通道1中,在中心钝体52与第一级轮毂14之间布置有一圈第一旋流叶片13;所述的第一级轮毂14的内壁与外壁之间设有第一级燃料腔62,在第一级轮毂14内壁表面上均匀排布有第一级燃料射流孔63,第一级燃料射流孔63与第一级燃料腔62连通;
所述的第二级轮毂24整体位于第一级轮毂14外壁外侧,在第一级轮毂14与第二级轮毂24之间布置有一圈第二旋流叶片23,且第二旋流叶片23全部位于第二级平直预混通道2中,在第二旋流叶片23内部设有旋流叶片燃料腔73,在第二旋流叶片23表面开设有第二级燃料射流孔74,第二级燃料射流孔74与第二级渐缩掺混通道4连通;所述的第二级轮毂24的内壁与外壁之间设有第二级燃料腔72;
所述的第二级燃料导管71整体位于第二级轮毂24外壁外侧,第二级燃料导管71通过燃料导管与第二级燃料腔72连通;所述的第一级燃料导管61布置在第一级轮毂14首端前方,第一级燃料导管61通过燃料支路与第一级燃料腔62连通;所述的值班级燃料导管51一端与中心钝体52前端连接,另一端从第一级燃料导管61底部伸出;所述的中心钝体52内部设有值班级燃料腔53,沿中心钝体52的斜坡面以及端面开设有值班级燃料射流孔54,值班级燃料射流孔54与第一级渐缩掺混通道3连通。
其中,第一级文氏管31出口端面和第二级文氏管41的喉道部位平齐。
沿中心钝体52的斜坡面以及端面开设的值班级燃料射流孔54,孔径大小为1mm~2mm,钝体斜坡面射流孔以及端面射流孔个数与第一级叶片数相同。
在第一级轮毂14内壁表面上均匀排布的第一级燃料射流孔63,孔径大小为1~1.5mm。
在第二旋流叶片23表面开设的第二级燃料射流孔74,孔径大小为0.8mm~1.5mm。
所述第一旋流叶片13和第二旋流叶片23均为无损直叶片,叶片旋流角度为30°~60°,叶片个数为6~12个。
本发明的有益效果在于:
本发明中燃烧室头部末端与渐缩掺混段结合的一体化文氏管能有效的将火焰托举从而避免回火,无需布置吹扫空气或在高工况时无需打开值班级扩散燃料;中心值班级与第一级燃料管形成部分套管形式,减少了对来流空气的扰动,从而使各叶间流道气量分配均匀;第二级燃料管布置在第二级轮毂外侧,减小燃料管对第二级空气进气的影响;旋流空气与燃料分别在平直预混通道内预混后进入渐缩掺混通道加强掺混,从而燃料掺混更均匀,降低污染物排放。
实施例1:
如图1-图5所示,本发明提供一种用于低排放燃气轮机的同轴分级气体燃料燃烧室头部,包括第一级平直预混通道1、第二级平直预混通道2、第一级渐缩掺混通道3、第二级渐缩掺混通道4、值班级燃料流路5、第一级燃料流路6、第二级燃料流路7。各级燃料流量可以单独控制,从而控制火焰筒内燃烧温度从而降低污染。
第一级平直预混通道1上开设有第一级燃料射流孔63和第一级空气入口12,第一级渐缩掺混通道3的一端与第一级平直预混通道1连通,另一端设置有第一级文氏管31;第一级空气入口12、第一级平直预混通道1、第一级渐缩掺混通道3、第一级文氏管31组成第一级空气流路;第一级平直段预混通道1位于中心钝体52和第一级轮毂14之间。第二级平直预混通道2上开设有第二级燃料射流孔74和第二级空气入口22,第二级渐缩掺混通道4的一端与第二级平直预混通道2连通,另一端设置有第二级文氏管41;第一级文氏管31端面和第二级文氏管41的喉道部位平齐;第二级平直段预混通道2位于第一级轮毂14和第二级轮毂24之间;第二级空气入口22、第二级平直预混通道2、第二级渐缩掺混通道4、第二级文氏管41组成第二级空气流路。其中两级平直预混通道1、2中安装有第一级旋流叶片13和第二级旋流叶片23,第一级旋流叶片13和第二级旋流叶片23依次为6、12个,叶片厚度依次为2mm、3mm。两级均采用无损直叶片,旋流叶片安装角均为40°,两级预混级旋流数分别为0.6、0.7。空气经过平直预混通道在旋流叶片的作用下形成旋流随后在渐缩掺混通道中加速经文氏管扩张形成回流区,文氏管能有效的防止回火。
在本实例中值班级燃料导管51、值班级燃料腔53、值班级燃料射流孔54组成值班级燃料流路;值班级燃料导管51位于中心钝体52前并与中心钝体52相连,值班级燃料腔53位于中心钝体52内部,值班级燃料射流孔位于中心钝体52末端,周向孔径大小为2mm共6个,端面孔径大小1.5mm共6个,该布置方式能有效的在低工况下形成扩散火焰从而使燃烧稳定。
在本实例中第一级燃料导管61、第一级燃料腔62和第一级燃料射流孔63组成第一级燃料流路;第一级预混级燃料从燃料入口经燃料导管61、分四个燃料导管支路进入第一级燃料腔62,并从第一级轮毂射流孔63射出。第一级燃料导管61在第一级轮毂14前方并与值班级燃料导管51同轴,第一级燃料腔62位于第一级轮毂14内,第一级轮毂射流孔63均匀排布在第一级轮毂14内侧,每叶间流道布置5个孔,孔径大小为1.5mm。第一级轮毂射流孔63布置方式可以有效的避免燃料在中心钝体52末端聚集从而避免回火现象发生。
在本实例中第二级燃料导管71、第二级燃料腔72、旋流叶片燃料腔73、第二级燃料射流孔74组成第二级燃料流路,第二级燃料导管71位于第二级轮毂24外侧,第二级燃料腔72位于第二级轮毂24内部,第二级旋流叶片23燃料腔位于旋流叶片内部,第二级燃料射流孔位于旋流器叶片上,第二级燃料射流孔孔径大小为1mm、1.2mm、1.5mm,能使燃料掺混的更均匀避免在燃烧室内燃烧出现局部高温区。
燃烧室头部燃料路的具体工作过程是:
点火工况时燃料由值班级燃料流路以及第一级燃料流路供给,并且随着工况提升逐渐增大第一级燃料流路供给并打开第二级燃料流路,同时逐渐降低值班级燃料流路的供给直至值班级燃料关闭,第一级与值班级的燃料供给能使燃烧火焰稳定并且迅速引燃第二级燃料,从而在保证燃烧稳定的同时降低污染物的生成。
燃烧室头部空气路的具体工作过程是:
空气从两级空气进口分配进入两级平直预混段并在旋流叶片的作用下形成旋转流动,随后进入渐缩掺混通道进行加速,并在一体化文氏管扩张段扩张,可以在避免回火的同时在火焰筒内形成回流区。
如图5所示为本发明应用于某模型燃烧室示意图,安装时可如图2所示在第二级渐缩掺混通道4处开设一个用于固定的螺栓孔18。本发明可以适用于环形燃烧室以及环管燃烧室,在实际应用时,根据燃气轮机具体结构和尺寸调整旋燃烧室头部尺寸。
以上所述仅为本发明的优选实施例而已,并不用于限制本发明,对于本领域的技术人员来说,本发明可以有各种更改和变化。凡在本发明的精神和原则之内,所作的任何修改、等同替换、改进等,均应包含在本发明的保护范围之内。
本文用于企业家、创业者技术爱好者查询,结果仅供参考。