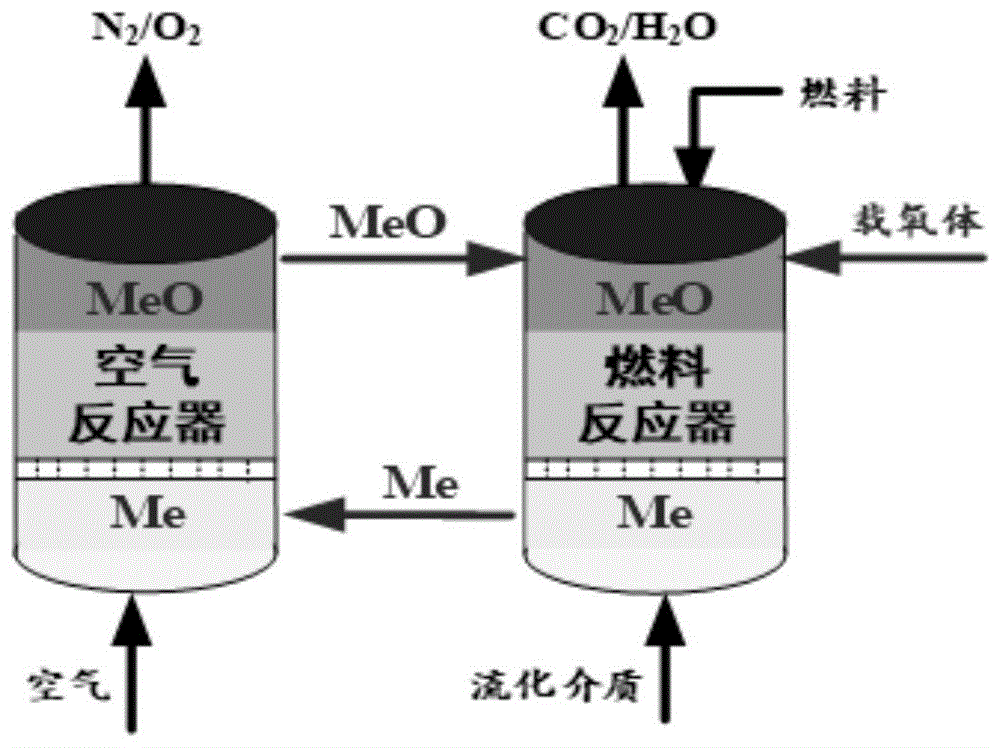
本发明涉及环保及能源利用技术领域,尤其涉及一种有机固废热解耦合化学链燃烧脱除污染物的方法及装置。
背景技术:
有机固体废弃物是指人类在生产、消费、生活和其他活动中产生的固态、半固态有机废弃物质。随着经济的发展和人们生活水平的提高,有机固体废弃物(下称“有机固废”)的产量日益增加,如果不妥善处理,将会严重危害生态环境和人体健康。
目前,有机固废处理处置的方式主要有填埋、堆肥和焚烧。大量研究表明,卫生填埋和堆肥化两种方法不仅需要占用大量的土地、耗用时间长,而且废弃物的渗透液会对附近的生态环境造成严重的破坏。焚烧是目前最广泛采用的有机固废处置手段,它可使废弃物中的毒性有机物和致病微生物经过高温分解而失去毒性,具有减容、减重率高,处理方法快等优点,同时通过回收焚烧过程中产生的热量实现垃圾的能源化利用。总体来看,焚烧技术是最适合处置有机固废的方式,该技术不仅能回收能量,还能实现彻底的无害化和减量化。然而,有机固废焚烧烟气中含有大量的sox、nox和二噁英及重金属颗粒等有害物质,容易对环境造成污染,同时污泥焚烧设备初期投资大,焚烧废气处理费用高、难度大。
热解气化技术是一种新兴的有机固废处置技术,它是指在一定的温度和压力条件下,在无氧或缺氧环境下,通过一系列的热化学反应,将固体废弃物中的有机物转化为含有h2、ch4、co、cnhm等可燃性气体、焦油和灰渣的过程。与焚烧相比,热解气化后产生so2和nox,等有害气体排放量少,大部分重金属被固定在灰渣中,浸出毒性低,处理成本相对较低。但由于有机固废具有很高的挥发分,从而在热解气化过程中会产生一定量的焦油及n/s/cl等污染物,造成一定的环境风险。
化学链燃烧(chemicalloopingcombustion,clc)是一种新颖的燃烧技术(如图1所示),它是通过链式反应利用金属氧化物载氧体(meo)中的晶格氧在燃料反应器中将燃料完全氧化成co2和h2o,反应后的还原态载氧体(me)在空气反应器中被空气重新氧化恢复晶格氧循环使用的过程。在燃料反应器的惰性氛围中,燃料首先发生热解释放还原态n/s/cl污染物及焦油(具有一定的还原性)。脱除还原态污染物比脱除氧化态污染物要更容易实现,如hcn和nh3在化学链燃烧过程中就能被载氧体氧化为为无害的n2,而nox则需要更为复杂的sncr/scr系统才能有效脱除。此外,通过将外源金属离子负载于载氧体上,调控金属离子种类及负载量,可在燃料反应器中实现焦油及n/s/cl污染物的一体化脱除。与传统焚烧相比,化学链燃烧极大降低了污染物的脱除难度,但有机固废中常含有成分复杂的灰分,容易引起载氧体的烧结和腐蚀,降低载氧体的循环反应活性和寿命。因此,探索和开发一种初期投资少、运行成本低,污染物排放低的有机固废处置技术,是缓解我国日益严峻的固废处置形势的重要举措。
技术实现要素:
本发明提供了一种有机固废热解耦合化学链燃烧脱除污染物的方法及装置,与传统焚烧技术相比具有初期投资小,焚烧废气处理费用低、难度小等优势,与热解气化技术相比具有焦油及n/s/cl污染物一体化脱除的特点,处理流程简单,成本低。
本发明的目的是提出了一种有机固废热解耦合化学链燃烧脱除污染物的装置,包括空气反应器、燃料反应器和热解气化器,所述的热解气化器套设于燃料反应器的外部,所述的空气反应器与燃料反应器通过u型返料器连接,所述的空气反应器顶端与顶部输送管的一端连通,顶部输送管另一端与第一旋风分离器的顶端连通,第一旋风分离器的底端与设置在燃料反应器顶端的载氧体返料器连接,所述的空气反应器底部设置有空气入口,所述的燃料反应器下部设置有流化气喷嘴和若干个射流器,所述的热解气化器一侧设置有进料器。第一旋风分离器顶部设置有烟气余热利用及净化系统,包括余热利用锅炉、小型石灰浆液吸收塔或火力电厂的烟气净化系统。
优选地,所述的燃料反应器下部设置有流化气喷嘴和设置于流化气喷嘴两侧的第一射流器和第二射流器,所述的第一射流器由第一射流喷嘴和第一l型射流室组成,所述的第二射流器由第二射流喷嘴和第二l型射流室组成,所述的热解气化器底部两侧设置有第一射流气喷嘴和第二射流气喷嘴,第一射流气管路内的射流气由第一射流喷嘴在第一l型射流室入口处喷出,高速射流气产生局部负压将热解气化器内的固废热解气吸入第一l型射流室,第二射流气管路内的射流气由第一射流喷嘴在第一l型射流室入口处喷出,高速射流气产生局部负压将热解气化器内的固废热解气吸入第二l型射流室。
进一步优选,所述的燃料反应器顶端与第二旋风分离器连通,燃料反应器内的烟气通过第二旋风分离器气固分离后的烟气通过第二旋风分离器出口管路分别作为燃料反应器底部射流气管路内的射流气、通过流化气管路进入流化气喷嘴的流化气和返料气管路内的返料气。
进一步优选,所述的u型返料器底部设置有流通返料气的返料气管路。
进一步优选,所述的空气反应器底部设置有第一天然气入口,所述的射流气管路包括第一射流气管路和第二射流气管路,所述的第一射流气管路上设置有第二天然气入口,所述的第二射流气管路上设置有第三天然气入口。
进一步优选,所述的空气入口处设置有空气控制阀,返料气管路上设置有返料气控制阀,所述的第一天然气入口处设置有第一天然气控制阀,所述的第二天然气入口处设置有第二天然气控制阀,所述的第三天然气入口处设置有第三天然气控制阀,所述的流化气管路设置有流化气控制阀,所述的第一射流气管路上设置有第一射流气控制阀,所述的第二射流气管路上设置有第二射流气控制阀。
进一步优选,所述的第二旋风分离器出口管路上设置有二氧化碳捕集装置。
优选地,所述的热解气化器下部设置有排渣器。
本发明还保护一种有机固废热解耦合化学链燃烧脱除污染物的方法,通过上述有机固废热解耦合化学链燃烧脱除污染物的装置来实现,包括如下步骤:
s1:将载氧体分别置于空气反应器、u型返料器、载氧体返料器和燃料反应器中,启动提供空气的空气增压风机,使用空气作为流化气,打开空气切换阀,并通过控制空气控制阀、返料气控制阀、第一射流气控制阀、流化气控制阀和第二射流气控制阀控制空气反应器、燃料反应器、u型返料器和载氧体返料器的气体流速,实现载氧体的循环流态化;
s2:打开第二天然气控制阀和第三天然气控制阀,增加天然气投入,通过燃料反应器内的电火花点火器点燃,烟气和载氧体经u型返料器输送至空气反应器,打开第一天然气控制阀,使天然气在空气反应器内燃烧,待空气反应器和燃料反应器均提升至800℃~1000℃后,依次关闭第一天然气控制阀、第二天然气控制阀和第三天然气控制阀,同时关闭空气切换阀,打开烟气管路上的烟气增压风机,开启烟气管路上的烟气旁路控制阀,将燃料反应器的流化气和射流气切换为燃料反应器的烟气管路内的再循环烟气;
s3:将储料仓内的有机固废通过进料器连续输入热解气化器中,同时开启第一射流气控制阀和第二射流气控制阀,热解气化器内的热解气被第一l型射流室和第二l型射流室中产生的负压卷吸入燃料反应器中,热解气在载氧体作用下发生化学链燃烧,氧化态载氧体反应后得到还原态载氧体,有机固废反应后的残余固体从热解气化器下部经排渣器输出;
s4:反应后的还原态载氧体进入u型返料器,在返料气的作用下进入空气反应器,还原态载氧体在空气气氛中充分氧化得到氧化态载氧体并释放热量,这些热量被氧化态载氧体和反应后的贫氧空气吸收;氧化态载氧体和贫氧空气进入空气反应器上部的快速床,经顶部输送管输送至第一旋风分离器,贫氧空气和氧化态载氧体分离,氧化态载氧体经载氧体返料器最后落入燃料反应器中;氧化态载氧体为热解气燃烧提供氧源,为维持化学链燃烧反应提供热量。
本发明将热解气化作为有机固废的前置处理,产生的热解气通入化学链燃烧装置,既实现了有机固废的高效无害化处置,又避免了灰分对载氧体的负面作用,是一种极具创新性的有机固废处置思路。本发明以热解气化耦合化学链燃烧的方式处理有机固体废弃物,既实现了有机固废高效减量化、无害化和资源化,又极大降低了处置过程中的污染物脱除难度,为有机固废高效清洁处置及资源化利用提供一种新的途径。
本发明提出的有机固体废弃物热解气化耦合化学链燃烧脱除污染物的方法包括有机固废热解气化和气体产物化学链燃烧两个流程,其原理示意图如图2所示。所述的有机固废热解气化过程为:通过热解气化器将有机固废原料转化为热解气。所述的气体产物化学链燃烧过程为:通过化学链燃烧装置将含有大量焦油及n/s/cl污染物的有机固废热解气转化为洁净尾气(co2/h2o/n2)并将s/cl元素固化在载氧体上。
化学链燃烧装置包括燃料反应器和空气反应器。在燃料反应器中,热解气与金属氧化物载氧体反生反应,焦油和可燃气体(h2/co/ch4等)转化为为co2和h2o,n污染物转化为n2,s/cl污染物固化于载氧体上;在空气反应器中,还原态载氧体在空气中充分煅烧以重新氧化,此过程释放大量的热,可满足燃料反应器和热解气化反应器的热量需求,实现整个热解耦合化学链燃烧系统的自热运行。空气反应器可能产生少量s/cl污染物气体,可通过配套小型石灰浆液吸收塔或利用现有火力电厂的烟气净化系统实现脱除。
优选地,所述的载氧体为天然金属矿石,所述的天然金属矿石选自铁矿石、铜矿石、锰矿石和镍矿石中的一种以上。
与现有技术相比,本发明的有益效果是:
1、相比化学链燃烧装置,本发明提出的装置通过将化学链燃烧中的热解过程解耦出来,形成热解 化学链燃烧双级反应单元,避免了有机固废复杂灰分与载氧体的接触,提高了载氧体的使用寿命。
2、相比空气焚烧装置,本发明提出的装置利用化学链燃烧低污染排放的特性处理固废热解气,可实现焦油及n/s/cl污染物的一体化脱除。
3、本发明提出的装置初期投资小,运行成本低,适合应用于小处理量的场景,可搭配小型烟气净化系统或利用现有热力电厂的烟气净化系统脱除空气反应器产生的少量s/cl污染气体。
4、选用天然金属矿石作为载氧体(铁矿石/铜矿石/锰矿石/镍矿石等),通过负载/掺杂k/ca/na/ni/mn/cu等外源离子,提升载氧体对焦油及n/s/cl污染物的脱除性能。
5、相比热解气化装置,热解气化耦合化学链燃烧系统可在几乎无氧的气氛下实现自热运行,还原态载氧体在空气反应器中煅烧释放大量的热足以供给热解气化反应器和燃料反应器的反应需要。
附图说明
图1为化学链燃烧技术原理示意图;
图2为本发明提出的有机固废热解耦合化学链燃烧脱除污染物的原理示意图;
图3为本发明有机固废热解耦合化学链燃烧脱除污染物的装置结构示意图,图中顶部输送管的箭头为载氧体和烟气的流动方向,燃料反应器顶部的箭头为烟气的流动方向,燃料反应器底部的箭头为流化气的流动方向;
图4为本发明热解过程与化学链转化过程的n元素形态分布对比图;
附图标记说明:1、空气反应器;1-1、空气增压风机;1-2、空气控制阀;1-3、倒锥型喷嘴;1-4、多孔布风板;1-5、第一天然气控制阀;1-6、顶部输送管;1-7、第一旋风分离器;1-8、载氧体返料器;2、u型返料器;2-1、返料气控制阀;3、燃料反应器;3-1、烟气旁路控制阀;3-2、烟气增压风机;3-3、第二旋风分离器;3-4、第一电火花点火器;3-5、多孔布风板;3-6、第一l型射流室、3-7、倒锥型流化气喷嘴;3-8、流化气控制阀;3-9、第一射流喷嘴、3-10、第二天然气控制阀;3-11、第一射流气控制阀;3-12、第二射流气控制阀;3-13、第三天然气控制阀;3-14、第二射流喷嘴;3-15、第二l型射流室;3-16、第二电火花点火器;4、热解气化器;4-1、储料仓;4-2、螺旋进料器;4-3、第一射流气喷嘴;4-4、第一射流气控制阀;4-5、第一螺旋排渣器;4-6、第二螺旋排渣器;4-7、第二射流气控制阀;4-8、第二射流气喷嘴;5、空气切换阀。
具体实施方式
以下实施例是对本发明的进一步说明,而不是对本发明的限制。除特别说明,本发明使用的设备和试剂为本技术领域常规市购产品。
如图1所示,一种有机固废热解耦合化学链燃烧脱除污染物的装置,包括空气反应器1、燃料反应器3和热解气化器4,热解气化器4套设于燃料反应器3的外部,空气反应器1与燃料反应器3通过u型返料器2连接,空气反应器1顶端与顶部输送管1-6的一端连通,顶部输送管1-6另一端与第一旋风分离器1-7的顶端连通,第一旋风分离器1-7的底端与设置在燃料反应器3顶端的载氧体返料器1-8连接,空气反应器1底部设置有空气入口,燃料反应器3下部设置有流化气喷嘴和若干个射流器,下述实施例中流化气喷嘴优选倒锥型流化气喷嘴3-7,热解气化器4一侧设置有进料器,下述实施例优选进料器为螺旋进料器4-2,便于更方便进料,螺旋进料器4-2上设置有储料仓4-1。第一旋风分离器1-7顶部设置有烟气余热利用及净化系统,包括余热利用锅炉、小型石灰浆液吸收塔或火力电厂的烟气净化系统。
燃料反应器3下部设置有倒锥型流化气喷嘴3-7和设置于倒锥型流化气喷嘴3-7两侧的第一射流器和第二射流器,第一射流器由第一射流喷嘴3-9和第一l型射流室3-6组成,第二射流器由第二射流喷嘴3-14和第二l型射流室3-15组成,热解气化器4底部两侧设置有第一射流气喷嘴4-3和第二射流气喷嘴4-8,第一射流气管路内的射流气经第一射流喷嘴3-9在第一l型射流室3-6入口处产生局部负压,将热解气化器内的固废热解气吸入第一l型射流室3-6,第二射流气管路内的射流气经第二射流喷嘴3-14在第二l型射流室3-15入口处产生局部负压,将热解气化器内的固废热解气吸入第二l型射流室3-15。
燃料反应器3顶端与第二旋风分离器3-3连通,燃料反应器3内的烟气通过第二旋风分离器3-3气固分离后,烟气通过第二旋风分离器出口管路分别作为燃料反应器底部射流气管路内的的射流气、通过流化气管路进入流化气喷嘴的流化气和返料气管路内的返料气。
u型返料器2底部设置有流通返料气的返料气管路。空气反应器底部设置有第一天然气入口,射流气管路包括第一射流气管路和第二射流气管路,第一射流气管路上设置有第二天然气入口,第二射流气管路上设置有第三天然气入口。
空气入口处设置有空气控制阀1-2,返料气管路上设置有返料气控制阀2-1,第一天然气入口处设置有第一天然气控制阀1-5,第二天然气入口处设置有第二天然气控制阀3-10,第三天然气入口处设置有第三天然气控制阀3-13,流化气管路设置有流化气控制阀3-8,第一射流气管路上设置有第一射流气控制阀3-11,第二射流气管路上设置有第二射流气控制阀3-12。第二旋风分离器出口管路上设置有二氧化碳捕集装置。
该装置各反应器的工作过程如下:
空气反应器1:空气反应器1上部为快速床,下部为鼓泡床,使用空气作为流化气(流速受空气控制阀1-2和空气增压风机1-1控制;空气反应器下部设置的多孔布风板1-4的作用为限制流化态载氧体的下边界,空气通过底部的倒锥型喷嘴1-3和多孔布风板1-4进入空气反应器;来自燃料反应器的还原态载氧体进入u型返料器2(u型返料器2下部有返料气输入,受返料气控制阀2-1控制),在返料气的作用下还原态载氧体进入空气反应器1;还原态载氧体在空气气氛中充分氧化并释放大量的热,这些热量被载氧体和反应后的贫氧空气吸收;氧化态载氧体和贫氧空气进入空气反应器1上部的快速床,经顶部输送管1-6输送至第一旋风分离器1-7,贫氧空气和载氧体分离,载氧体经载氧体返料器1-8,最后落入燃料反应器3中;还原态载氧体在空气反应器1中充分氧化,并作为热载体吸收氧化反应热,最后输送至燃料反应器3中,为热解气燃烧提供氧源,为维持反应温度提供热量。
燃料反应器3:燃料反应器3为鼓泡流化床,燃料反应器3上部与载氧体返料器1-8、第二旋风分离器3-3分别相连通,载氧体返料器1-8作用为接收来自空气反应器1中的氧化态载氧体,第二旋风分离器3-3的作用为防止出口烟气夹带载氧体颗粒;燃料反应器3下部设置有倒锥型流化气喷嘴3-7和由第一射流喷嘴3-9、第二射流喷嘴3-14、第一l型射流室3-6和第二l型射流室3-15组成的射流器;燃料反应器3的出口烟气经第二分离器出口管路排出,出口烟气一部分经第二分离器出口管路上的旁路排出进入co2捕集装置(排出流量受烟气旁路控制阀3-1控制),另一部分进入烟气增压风机3-2,增压后用于供给流化气和射流气;流化气的作用为维持燃料反应器3内部的载氧体流化态,射流气的作用为制造第一l型射流室3-6和第二l型射流室3-15内的局部负压,卷吸来自热解气化器4中的有机固废热解气;热解气在燃料反应器3内与流态化氧化态载氧体充分反应,实现热解气燃烧。
热解气化器4:有机固废原料连续输入储料仓4-1中,由螺旋进料器4-2输送至热解气化器4(热解气化器内沿烟道下降布置有一些挡板,用于延长有机固废在热解气化器中的停留时间,从而实现充分热解气化);热解气化器下部设有第一射流气喷嘴4-3和第二射流气喷嘴4-8,气速受第一射流气控制阀4-4第二射流气控制阀4-7控制,利用高速射流在第一l型射流室3-6和第二l型射流室3-15入口处产生局部负压,将固废热解气吸入第一l型射流室3-6和第二l型射流室3-15;固废反应剩余残渣由第一螺旋排渣器4-5和第二螺旋排渣器4-6排出。
实施例1
一种有机固废热解耦合化学链燃烧脱除污染物的方法,通过上述有机固废热解耦合化学链燃烧脱除污染物的装置来实现,包括如下步骤:
s1:将5%ca负载铁矿石载氧体分别置于空气反应器1、u型返料器2、载氧体返料器1-8和燃料反应器3中,启动提供空气的空气增压风机1-1,使用空气作为流化气,打开空气切换阀5,并通过控制空气控制阀1-2、返料气控制阀2-1、第一射流气控制阀3-11、流化气控制阀3-8和第二射流气控制阀3-12控制空气反应器1、燃料反应器3、u型返料器2和载氧体返料器1-8的气体流速,实现载氧体的循环流态化;
s2:打开第二天然气控制阀3-10和第三天然气控制阀3-13,增加天然气投入,通过燃料反应器内的第一电火花点火器3-4和第二电火花点火器3-16点燃,烟气和还原态载氧体经u型返料器2输送至空气反应器1,打开第一天然气控制阀1-5,使天然气在空气反应器1内燃烧,待空气反应器1和燃料反应器3均提升至800℃~1000℃后,依次关闭第一天然气控制阀1-5、第二天然气控制阀3-10和第三天然气控制阀3-13,同时关闭空气切换阀5,打开第二旋风分离器出口管路上的烟气增压风机3-2,开启第二旋风分离器出口管路上的烟气旁路控制阀3-1,将燃料反应器3的流化气和射流气切换为燃料反应器3的第二旋风分离器出口管路内的再循环烟气;
s3:将储料仓4-1内的污泥通过螺旋进料器4-2连续输入热解气化器4中,同时开启第一射流气控制阀4-4和第二射流气控制阀4-7,热解气化器4内的热解气被第一l型射流室3-6和第二l型射流室3-15中产生的负压卷吸入燃料反应器3中,热解气在载氧体作用下发生化学链燃烧,氧化态载氧体反应后得到还原态载氧体,有机固废反应后的残余固体从热解气化器4下部经第一螺旋排渣器4-5和第二螺旋排渣器4-6输出;
s4:反应后的还原态载氧体进入u型返料器2,在返料气的作用下进入空气反应器1,还原态载氧体在空气气氛中充分氧化得到氧化态载氧体并释放热量,这些热量被氧化态载氧体和反应后的贫氧空气吸收;氧化态载氧体和贫氧空气进入空气反应器1上部的快速床,经顶部输送管1-6输送至第一旋风分离器1-7,贫氧空气和氧化态载氧体分离,氧化态载氧体经载氧体返料器1-8最后落入燃料反应器3中;氧化态载氧体为热解气燃烧提供氧源,为维持化学链燃烧反应提供热量。
实施例2
与实施例1的不同之处在于:载氧体变为5%k负载铁矿石载氧体。
实施例3
与实施例1的不同之处在于:载氧体变为5%na负载铁矿石载氧体。
实施例4
与实施例1的不同之处在于:
处理的固废有污泥变为农林有机固废,载氧体变为fe基载氧体。
实施例5
与实施例1的不同之处在于:
处理的固废有污泥变为农林有机固废,载氧体变为fe基载氧体 水蒸气。
实施例6
与实施例1的不同之处在于:
处理的固废有污泥变为农林有机固废,载氧体变为nife2o4载氧体。
对比例1
与实施例1的不同之处在于:不使用载氧体,直接使用空气中的氧气作为氧化剂,来实现实施例1中的反应。
对比例2
与实施例1和对比例1的不同之处在于:不使用任何氧化剂(包括空气和载氧体),原料仅在高温缺氧的条件下发生热分解。
将实施例1和对比例1得到的氮氧化物相比较,如表1所示:
表1燃烧方式的nox排放对比
化学链燃烧的nox排放远低于空气燃烧,原因在于化学链过程的特殊条件能够抑制甚至彻底阻断三种主要nox的形成:首先,化学链燃烧温度较低(<1000℃),远低于空气燃烧的温度,能够较为彻底地避免热力型nox的生成;其次,燃料反应时与空气中的氮元素充分隔离,从根本上避免了快速型nox的产生;最关键的是,燃料反应没有气态分子氧参与,反应气氛的氧化性被大幅削弱,燃料型nox的生成几率显著降低。固废热解产生以hcn和nh3为主的nox前驱体,载氧体可将其直接氧化为无害的n2。如表1所示,与空气燃烧相比,化学链燃烧可显著减少nox的生成。如图4所示,与热解相比,使用不同载氧体的化学链燃烧过程均能有效降低hcn及nh3的含量。可见,热解耦合化学链燃烧在含n污染物减排方面具有巨大优势,可减少对sncr/scr等脱硝设备的投入,节省脱硝初期投资和运维成本。
将实施例1和对比例1得到的脱硫效率相比较,如表2所示:
表2不同载氧体脱硫效率
化学链燃烧可将s元素捕捉并固定在载氧体中,实现s污染物的脱除。化学链燃烧硫释放规律与空气燃烧相似,在载氧体的作用下,固废热解产生的h2s、cos等还原性s污染物被氧化为so2。与空气燃烧的区别在于,载氧体可通过改性获得吸收固定so2的能力,如负载碱(土)金属成分等,将气态so2转化为稳定的硫酸盐固体,从而实现s污染物的脱除。如表2所示,化学链燃烧可实现源头脱硫,减轻含s烟气对尾部烟道的腐蚀。实施例1中脱硫效率接近50%可使用小型脱硫设施,而空气燃烧需要装备大型脱硫设施,给污染物处理增加场地和运行维护等方面的成本。
将实施例1、实施例2、实施例3及对比例1得到的脱氯效率相比较,如表3所示:
表3不同载氧体脱氯效率
固废热解产生的cl污染物主要为hcl,cl污染物脱除原理与s污染物类似,载氧体通过改性获得吸收固定cl的能力,从而实现源头脱除cl污染物,减轻含cl烟气对烟道的腐蚀。如表3所示,选择合适的载氧体可实现源头脱氯。
将实施例4、实施例5、实施例6和对比例2得到的烟气焦油含量相比较,如表4所示:
表4焦油含量对比
与燃烧相比,固废热解温度较低,会产生大量的焦油,而焦油结构较稳定,在缺氧条件下分解需要极高的温度。载氧体一般为过渡金属氧化物,其具有的氧化活性能够脱除部分焦油,同时载氧体的某些还原产物是性能优异的焦油裂解催化剂,如:金属fe及其低价氧化物、金属ni等。如表4所示,与热解相比,化学链转化过程的烟气焦油含量大幅降低。由于反应过程与化学链燃烧类似,因而也具有脱除n/s/cl污染物的效果。
热解耦合化学链燃烧过程同时具有热解/燃烧的优点,并克服了各自的缺点,因此具有较大的实用价值和应用潜力。
以上仅是本发明的优选实施方式,应当指出的是,上述优选实施方式不应视为对本发明的限制,本发明的保护范围应当以权利要求所限定的范围为准。对于本技术领域的普通技术人员来说,在不脱离本发明的精神和范围内,还可以做出若干改进和润饰,这些改进和润饰也应视为本发明的保护范围。
本文用于企业家、创业者技术爱好者查询,结果仅供参考。