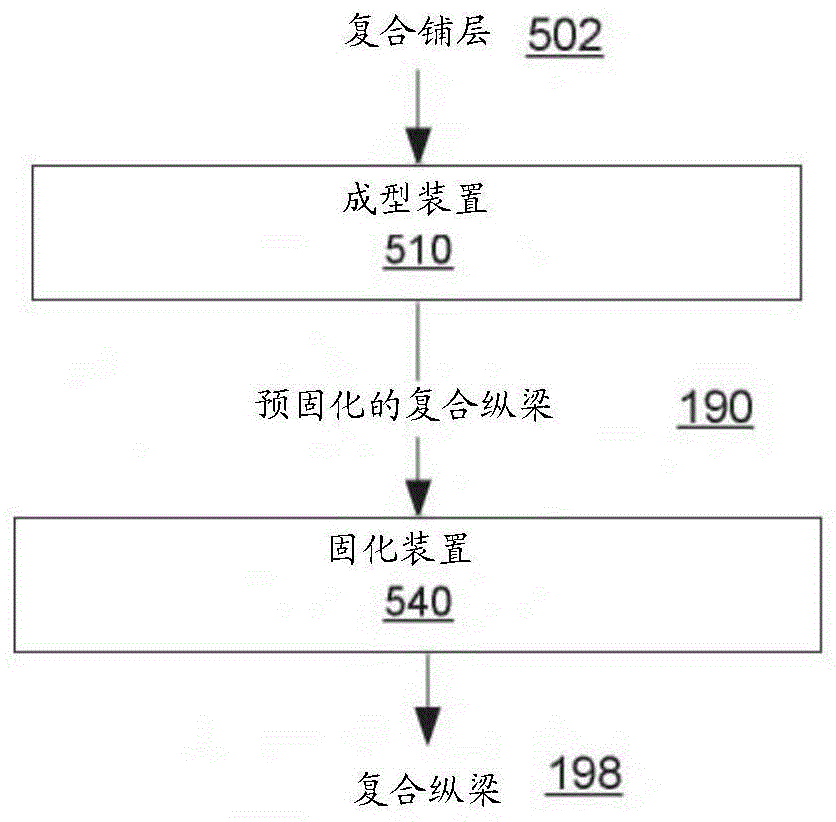
本发明涉及用于支撑多种不同预固化的复合纵梁(compositestringer)的方法和装置。
背景技术:
飞机利用各种零件(例如纵梁)抵抗弯曲、扭转、剪切和直接负荷。纵梁通常由轻质复合材料使用例如具有纤维嵌入树脂基体的带或织物制成。例如,在成型工具中加工复合铺层(layup)以限定形状。然后将成形的零件转移到固化装置中进行固化。直到固化完成为止,纵梁需要足够的支撑来保持其形状。除了从一个纵梁到另一个纵梁变化的横截面轮廓外,这种形状通常还由平面内和/或平面外弯曲限定。此外,成形的纵梁可以在固化之前经受各种操作,诸如修整、检查、安装另外的零件等。对未固化的纵梁的这种支撑通常由成型工具或固化工具提供,这限制了这些工具中的任何一种的生产量并减慢了整体加工速度。
所需要的是在成型之后和固化之前用于支撑多种不同的预固化的复合纵梁的新方法和装置。
技术实现要素:
提供了在成型之后和固化之前用于支撑多种不同的预固化的复合纵梁的方法和装置。后成型加工装置包括具有槽道的基座,该槽道用于接收不同纵梁的帽部分。该装置还包括至少部分地在槽道内延伸的支撑结构。支撑结构被配置为贴合不同的帽部分并保持这些帽部分的形状。例如,支撑结构由柔性材料制成,其贴合任何形状变化。在一些示例中,支撑结构由与预固化的复合纵梁中的每个一起再成形的夹紧材料(jammingmaterial)制成。后成型加工装置用于支撑不同的预固化的复合纵梁,同时对这些纵梁执行各种操作,诸如纵梁修整、检查、安装囊状物和条状物(noodles)等。
在一些示例中,提供了用于支撑预固化的复合纵梁的后成型加工装置。复合纵梁包括帽部分,其在预固化的复合纵梁之间具有不同的横截面。后成型加工装置包括基座、支撑结构和罩(cover)。基座包括槽道,其具有槽道宽度和槽道高度。槽道宽度大于预固化的复合纵梁的帽部分的宽度。槽道高度大于预固化的复合纵梁的帽部分的高度。支撑结构至少部分地在槽道内并沿槽道的长度延伸。支撑结构被配置为当预固化的复合纵梁中的相应一个由后成型加工装置支撑时,贴合帽部分中的每个并保持帽部分中的每个的横截面形状。罩被配置为附接到基座,使得预固化的复合纵梁中的相应一个定位在罩和基座之间,同时由后成型加工装置支撑。
还提供了一种制造复合纵梁的方法。该方法包括:在成型装置上成型预固化的复合纵梁,该预固化的复合纵梁包括帽部分;以及将预固化的复合纵梁从成型装置转移至后成型加工装置。后成型加工装置包括基座和支撑结构,基座包括槽道,并且支撑结构至少部分地在槽道内并沿槽道的长度延伸并且贴合帽部分和保持帽部分的横截面形状。该方法还包括在将预固化的复合纵梁定位在后成型加工装置上时,在预固化的复合纵梁上安装囊状物。该方法包括在将预固化的复合纵梁定位在后成型加工装置上时,将条状物安装在囊状物和预固化的复合纵梁之间的界面处并且在基座的支撑表面的平面内。该方法还包括将预固化的复合纵梁与囊状物和条状物一起从后成型加工装置转移至固化装置,并在固化装置上固化预固化的复合纵梁,从而成型复合纵梁。
在一些示例中,方法包括将包括帽部分的预固化的复合纵梁转移至后成型加工装置。后成型加工装置包括:基座,其包括槽道;以及支撑结构,其至少部分地在槽道内并沿槽道的长度延伸,和贴合预固化的复合纵梁的帽部分并保持预固化的复合纵梁的帽部分的横截面形状。方法继续从后成型加工装置中移出预固化的复合纵梁,并将包括另外的帽部分的另外的预固化的复合纵梁转移至后成型加工装置。后成型加工装置的支撑结构贴合另外的预固化的复合纵梁的另外的帽部分,并保持另外的预固化的复合纵梁的另外的帽部分的横截面形状,其不同于预固化的复合纵梁的帽部分的横截面形状。
附图说明
图1a是制造复合纵梁的工艺流程图。
图1b是根据本公开的其他示例制造复合纵梁的工艺流程图。
图1c、1d和1e是复合纵梁的不同示例。
图2a是根据本公开的一些示例的包括柔性支撑结构的后成型加工装置的示意横截面视图。
图2b是根据本公开的一些示例的图2a中的后成型加工装置的示意横截面视图,其显示了贴合预固化的复合纵梁的帽部分的柔性支撑结构。
图2c是根据本公开的一些示例的图2a和2b中的后成型加工装置的示意横截面视图,其显示了抵靠基座密封并封闭预固化的复合纵梁的罩。
图2d是根据本公开的一些示例的包括柔性支撑结构和柔性插入件的后成型加工装置的示意横截面视图,柔性支撑结构和柔性插入件都定位在槽道中。
图2e是根据本公开的一些示例的后成型加工装置的示意横截面视图,其图解了锥形槽道。
图2f是根据本公开的一些示例的后成型加工装置的示意俯视图,其图解了囊状物密封件。
图3a是根据本公开的一些示例的包括预成型的支撑结构的后成型加工装置的示意横截面视图,该预成型的支撑结构由夹紧材料制成。
图3b是根据本公开的一些示例的图3a中的后成型加工装置的示意横截面视图,其显示了接合预固化的复合纵梁的柔性支撑结构。
图3c是根据本公开的一些示例的图3a和3b中的后成型加工装置的示意横截面视图,其显示了抵靠基座密封并封闭预固化的复合纵梁的罩。
图4是根据本公开的一些示例的对应制造复合纵梁的方法的工艺流程图。
图5a是根据本公开的一些示例的放置在成型基座的加工表面上并在空腔(cavity)上延伸的层压铺层的示意图示。
图5b是根据本公开的一些示例的通过成型装置成形为预固化的复合纵梁的层压铺层的示意图示。
图5c是根据本公开的一些示例的由后成型加工装置支撑的预固化的复合纵梁的示意图示。
图5d是根据本公开的一些示例的在由后成型加工装置支撑预固化的复合纵梁时安装在预固化的复合纵梁中的囊状物的示意图示。
图5e是根据本公开的一些示例的在由后成型加工装置支撑预固化的复合纵梁时在囊状物和预固化的复合纵梁之间的界面处安装的条状物的示意图示。
图5f是根据本公开的一些示例的抵靠后成型加工装置的基座密封的罩的示意图示。
图5g是根据本公开的一些示例的与囊状物和条状物一起转移至固化装置的预固化的复合纵梁的示意图示。
图5h是根据本公开的一些示例的从固化装置移出的复合纵梁的示意图示。
图5i是根据本公开的一些示例的由后成型加工装置支撑的另外的预固化的复合纵梁的示意图示。
图6a和6b是根据本公开的一些示例的后成型加工装置的俯视示意视图,其显示了平面内弯曲。
图7是根据本公开的一些示例的对应于在后成型加工装置中支撑预固化的复合纵梁的方法的工艺流程图。
图8是对应于制造和维护飞机的方法的工艺流程图。
图9图解了根据本公开的一些示例的飞机的示例的方框图。
具体实施方式
在下面的描述中,阐述了许多具体细节以便提供对所提出的概念的透彻理解。在一些示例中,在没有一些或全部这些具体细节的情况下实践所提出的概念。在其他情况下,没有详细描述众所周知的过程操作,以免不必要地使所描述的概念模糊。尽管将结合具体示例描述一些概念,但是应当理解,这些示例并非旨在是限制性的。
介绍
复合纵梁和其他形状的复合结构被用于许多应用,诸如飞机、陆地车辆等。这些复合结构的制造涉及对预固化成形零件的各种处理和加工,诸如修整、检查、囊状物安装等。在固化之前,这些成形的零件需要足够的支撑来保持形状,由于这些预固化零件的形状和大小的差异,这可能是具有挑战性的。例如,现代飞机使用数百种不同的复合纵梁,这些复合纵梁具有不同的大小、横截面形状、平面内弯曲和/或平面外弯曲。为这些复合纵梁的每种类型提供专用支撑件是具有挑战性的且昂贵的,这增加了已经大量数量的在复合纵梁制造中使用的专用工具。
图1a和1b图解了代表制造复合纵梁以及用于各种操作的对应工具的不同示例的两个工艺流程图。呈现图1a和1b以提供关键零件、工具和步骤的一些背景和一般概括。在两个示例中,过程开始于成型装置510成形复合铺层502,由此成型预固化的复合纵梁190。然后固化装置540使预固化的复合纵梁190固化,由此成型复合纵梁198。预固化的复合纵梁190和复合纵梁198具有大体相同的形状,但是不同的材料和机械性质。例如,预固化的复合纵梁190的树脂没有完全交联或没有如复合纵梁198的树脂一样交联。如此,预固化的复合纵梁190依然能够改变形状并且在固化之前需要支撑。
成型装置510和固化装置540都经过具体成形,以适应复合纵梁198的特定设计。因此,在完成成型操作之后和开始固化操作之前,成型装置510和固化装置540之一或两者都可以用于支撑预固化的复合纵梁190,这对应于图1a中所示的示例。然而,该方法占用成型装置510和固化装置540中的一个或两个进行非这些装置的核心功能的操作。此外,这些操作中的许多操作甚至是预固化的复合纵梁190的存储都可能花费大量时间段。结果,成型装置510和固化装置540之一或两者的生产量可能受到与预固化的复合纵梁190相关的这些中间操作和存储的限制。
参考图1b,后成型加工装置100用于在预固化的复合纵梁190成型/成形之后接收预固化的复合纵梁190。后成型加工装置100还用于支撑预固化的复合纵梁190直至固化操作为止。后成型加工装置100有效地减轻了成型装置510和固化装置540的负担,提高了它们的加工生产量。后成型加工装置100用于对预固化复合纵梁190执行的各种操作,以及在一些示例中,用于存储预固化的复合纵梁190。
然而,如果后成型加工装置被具体且永久地成形以适应每个具体复合纵梁的形状,则这种后成型加工装置的数量将与不同的纵梁的数量相同。从节省空间和成本的角度来看,这种方法是不期望的,并且由于需要大量的另外的工具而会使整个过程复杂化。此外,由于设计变化,具体且永久性地成形的后成型加工装置可能并不总是可堆叠的,这使它们的存储复杂化。还应注意的是,基于后成型加工装置的复杂性,供应基座(supplybase)受到限制。而且,3d几何形状增加了穿梭纵梁往返的复杂性。最后,3-d几何形状可能会增加重量,这会由于各种原因(包括维护)而阻碍手动操作。
图1c、1d和1e中显示了复合纵梁——或更具体地说预固化的复合纵梁190的不同示例——的设计变化。在每个示例中,预固化的复合纵梁190包括凸缘部分196,其限定了接触表面197。接触表面197用于将由预固化的复合纵梁190形成的复合纵梁连接至其他零件,例如飞机的复合蒙皮。这些其他零件限定了接触表面197的形状。在一些示例中,接触表面197是平面的。可选地,接触表面197,并且更一般地整个纵梁,具有平面外弯曲。
每个预固化的复合纵梁190还包括帽部分191,其相互连接并定位于凸缘部分196之间。帽部分191延伸远离接触表面197,这限定了纵梁空腔192。帽部分191由帽部分191的高度(h)限定,该高度(h)被限定为与接触表面197的最大偏差。帽部分191还由帽部分191的宽度(w)限定,该宽度(w)被限定为凸缘部分196之间的间隙。
参照图1c,在一些示例中,帽部分191由直壁形成。可选地,在一些示例中,帽部分191由连续的弯曲壁形成,例如,如图1e所示。图1d图解了其中由直壁和弯曲壁的组合形成帽部分191的示例。图1c、1d和1e图解了这些附图中所示的预固化的复合纵梁190需要来自后成型加工装置100的不同类型的支撑。此外,图1c、1d和1e图解了预固化的复合纵梁190不是可堆叠的。因此,如果将永久刚性的支撑件用于这些预固化的复合纵梁,则这些支撑件也将不是可堆叠的。为了区分预固化的复合纵梁的目的,图1e中所示的示例可以称为另外的预固化的复合纵梁199。使用相同的后成型加工装置100加工不同类型的预固化的复合纵梁在下面参考图4进行描述。
所描述的方法和装置用于支撑各种不同的预固化的复合纵梁,诸如图1a-1c中所示的复合纵梁。更具体地,相同的后成型加工装置被配置为支撑其帽部分具有不同横截面轮廓的预固化的复合纵梁。具体地,后成型加工装置包括槽道和至少部分地在槽道内延伸的支撑结构。支撑结构被配置为贴合预固化的复合纵梁的不同成形的帽部分中每个,并在提供支撑的同时保持这些帽部分的形状。在一些示例中,支撑结构由柔性材料制成,该柔性材料贴合帽部分的任何形状。可选地,支撑结构由夹紧材料制成,并且与预固化的复合纵梁中的每个一起再成形。
在本公开的示例中,所公开的后成型加工装置用于支撑不同的预固化的复合纵梁,同时对这些纵梁执行各种操作,诸如纵梁修整、检查、安装囊状物和条状物等。此外,在一些示例中,所公开的后成型加工装置用于存储预固化的复合纵梁。总体而言,将所公开的后成型加工装置添加到整个过程流中允许增加其他装置诸如成型装置和固化装置的加工生产量。总体而言,所公开的后成型加工装置通过将成型和固化装置之间的间隙与这些后成型加工装置合并而提供了纵梁安装的高速自动化。
所描述的方法还包括并入对齐配件,以确保纵梁和囊状物之间的合适对齐,以用于终端配件(deadendfitting)。囊状物的偏移有助于在固化期间提供合适的支撑和功能。例如,在一些情况下,囊状物终止于部件边缘的内部。具体示例包括门结构、窗结构和会聚结构(如,具有非常尖的端部的飞机结构)。
应该注意的是,空腔是用于成型纵梁的工具,容纳纵梁和囊状物。如果囊状物未延伸过纵梁,则囊状物将干扰(interfere)工具或在工具内部留下不可接受的大的间隙。由于在装备(kitting)阶段将囊状物对齐并锁定到纵梁,因此有利的是将囊状物变址(index)在正确的位置,以避免在以后的阶段返工。
另外,一些囊状物在插入到对应纵梁之前接收一层或多层包裹在这些囊状物周围的材料。在一些示例中,该组件包括玻璃层片,其与纵梁的端部对齐以在纵梁内部添加腐蚀保护。在其他示例中,该组件包括碳包裹物,其为纵梁增加强度。在这些后面的示例中,囊状物包裹物与纵梁对齐。
后成型加工装置的示例
图2a是根据一些示例的用于支撑预固化的复合纵梁190的后成型加工装置100的示意横截面视图。后成型加工装置100包括基座110、支撑结构120和任选的罩130。在一些示例中,后成型加工装置100不具有罩130,或至少在一些操作中在没有罩130的情况下使用。
基座110由诸如碳纤维、铝、拉挤聚酯/玻璃固溶体(solution)等刚性材料形成。基座110包括支撑表面114,当存在罩130时,支撑表面114面对罩130。支撑表面114被配置为抵靠罩130密封,并且在一些示例中,包括一个或多个密封特征(feature)。在后成型加工装置100的操作期间,支撑表面114用于支撑纵梁190的凸缘部分196,例如通过压缩支撑表面114和罩之间的凸缘部分196。在一些示例中,支撑表面114是平面的。通常地,支撑表面114贴合纵梁190的凸缘部分196的形状。
基座110还包括槽道112,该槽道112部分延伸穿过基座110并具有开口113。开口113将支撑表面114的两个部分分开。如图2a所示,槽道112具有槽道宽度(cw)和槽道高度(ch)。在平行于支撑表面114的方向上(沿y轴)测量槽道宽度(cw)。在垂直于支撑表面114的方向上(沿z轴)测量槽道高度(ch)。在一些示例中,槽道宽度(cw)沿基座110的长度(x轴(如,参见图2f))是恒定的。在相同或其他示例中,槽道高度(ch)沿基座110的长度(x轴)是恒定的。在一些示例中,槽道宽度(cw)沿槽道高度(z轴)是恒定的,例如,图2a中所示。这种类型的槽道112可以被称为直槽道。可选地,槽道宽度(cw)沿着槽道高度(z轴)不同,例如,如图2e所示。在此示例中,槽道宽度(cw)在开口113处最大。这种类型的槽道112可以被称为锥形槽道,并允许堆叠后成型加工装置100。
当使用后成型加工装置100支撑预固化的复合纵梁190时,槽道112用于容纳预固化的复合纵梁190的帽部分191。参照图2b,帽部分191突出到槽道112中,而凸缘部分196搁置在支撑表面114上。应当注意,相同的后成型加工装置100用于支撑不同类型的预固化的复合纵梁190,其可以具有不同形状和大小的帽部分191。因此,槽道宽度(cw)大于预固化的复合纵梁190的帽部分191的宽度,或更具体地,大于在后成型加工装置100上加工的所有预固化的复合纵梁190中最宽的帽部分191的宽度。出于本公开的目的,例如,当帽部分191具有锥形或弯曲的横截面时,帽部分191的宽度被限定为最大宽度。此外,槽道高度大于预固化的复合纵梁190中帽部分191的高度,或更具体地,大于在后成型加工装置100上加工的所有预固化的复合纵梁190中最高的帽部分191的高度。通常,槽道112的横截面轮廓足以容纳使用后成型加工装置100加工的纵梁190的任何帽部分191。
尽管图2a-2c示出了槽道112的矩形横截面轮廓,但是能够容纳预固化的复合纵梁190的帽部分191的任何横截面轮廓都在本公开的范围内,诸如图2e中所示的锥形轮廓、半圆形轮廓等。在一些示例中,槽道112的横截面轮廓对应于帽部分191的横截面轮廓,如,两者都是锥形的。
参照图2a,支撑结构120至少部分地在槽道112内并且沿着槽道112的长度延伸。在一些示例中,当预固化的复合纵梁190由后成型加工装置100支撑并使用后成型加工装置100进行加工时,支撑结构120被配置为贴合每个帽部分191并保持该帽部分191的横截面形状。应注意的是,相同的支撑结构120用于不同类型和轮廓的帽部分191。支撑结构120能够在提供足够的支撑的同时贴合这些不同的类型和轮廓。
在一些示例中,支撑结构120由弹性材料形成,其配置为在贴合不同类型的帽部分191时改变形状。合适的弹性材料的一些示例包括但不限于乳胶、硅氧烷(如,过氧化物或铂固化的硅)和其他类似材料。材料选择的一些考虑因素包括重量、清洁能力、耐溶剂性、刚度、撕裂强度、断裂伸长和硬度。
在一些示例中,如图1a中示意性地示出,支撑结构120在槽道112的侧壁处附接到基座110。在这些示例中,支撑表面114保持暴露并且可用于与预固化的复合纵梁190的凸缘部分196界面结合。换言之,当将凸缘部分196定位在支撑表面114上时,如压缩在支撑表面114和罩130之间,支撑结构120不干扰。这些示例在图2a和2b中示意性地示出。
在一些示例中,支撑结构120包括夹紧材料或塑性可变形材料。为了本公开的目的,夹紧材料被定义为能够在一个条件下改变其形状并且在另一条件下保持其形状的材料。更具体地,支撑结构120与预固化的复合纵梁190之一共成型或共成形,然后在支撑该纵梁的同时保持该纵梁的形状。例如,支撑结构120的形状最初与预固化的复合纵梁190的形状不同。应当注意,在此阶段,预固化的复合纵梁190尚未成型。将支撑结构120和复合材料铺层两者都装载到成型装置中,下面描述其各种示例,并且在成型预固化的复合纵梁190时调整支撑结构120的形状。因此,支撑结构120与预固化的复合纵梁190共成型或共成形。
在支撑该特定的纵梁时,在后成型加工装置100的各种操作期间,该形状由支撑结构120保持。在一些示例中,在加工相同类型的多个纵梁(例如,帽部分的横截面形状相同)时,将保留该形状。当要支撑不同类型的纵梁时,如通过与该另一纵梁共同成型或成形来改变支撑结构120的形状。这些示例在图3a和3b中示意性显示。
参照图3a,在一些示例中,支撑结构120包括在基座110的支撑表面114上和槽道112的外部延伸的支撑凸缘124。类似于支撑结构120的部分——延伸到槽道112中并支撑纵梁190的帽部分191,支撑凸缘124被具体地成形以支撑纵梁190的凸缘部分196。在一些示例中,支撑凸缘124的形状不同于支撑表面114的形状。因此,相同的后成型加工装置100可用于支撑具有不同形状的凸缘部分的纵梁。
在一些示例中,支撑结构120可从基座110移出。例如,支撑结构120从基座110移出,以改变支撑结构120的形状,如,当支撑结构120由夹紧材料形成时。在一些示例中,不同类型的支撑结构120与相同基座110一起使用。
罩130配置为附接到基座110,使得预固化的复合纵梁190中的相应一个定位在罩130和基座110之间,同时由后成型加工装置100支撑。更具体地,预固化的复合纵梁190的凸缘部分196被定位在罩130和支撑表面114之间,并且在一些示例中被压缩在罩130和支撑表面114之间,如例如图3c中示意性所示。罩130配置为抵靠基座110密封。具体地,罩130包括与密封件接收器115接合的真空密封件132。
在一些示例中,基座110包括与槽道112流体连接并配置为控制槽道112内部和支撑结构120下的压力的通孔(pass-through)116。例如,通孔116用于维持支撑结构120下的压力与环境中相同,如,当将预固化的复合纵梁190的帽部分191插入槽道112并与支撑结构120接合时,或更具体地,当帽部分191将支撑结构120更深地推入槽道112从而减小支撑结构120下的体积时。
在一些示例中,后成型加工装置100还包括柔性插入件140,如图2d中所示。柔性插入件140与槽道112一起且在支撑结构120下方定位,并且用于向帽部分191提供另外的支撑。柔性插入件140允许使用如此支撑结构120,其非常柔性的并且与例如在不具有柔性插入件140的情况下使用支撑结构120时相比能够贴合帽部分191的更大变化。在一些示例中,柔性插入件140由弹性橡胶制成,诸如
参照图2f,在一些示例中,后成型加工装置100包括通孔式囊状物密封件180和终端囊状物密封件182。应注意的是,在下面参照图5d-e进一步描述的囊状物520是如由硅氧烷、
制造复合纵梁的方法的示例
图4是根据一些示例的对应于制造复合纵梁198(参见如图1b)的方法400的工艺流程图。复合纵梁198应该区分于预固化的复合纵梁190,后者是用于形成复合纵梁198的中间结构。因此,在一些示例中,预固化的复合纵梁190和复合纵梁198具有相同的大小和形状。因此,图1c-1e代表预固化的复合纵梁190和复合纵梁198两者。在一些示例中,复合纵梁198包含纤维增强复合材料,其也可以称为增强复合材料。这种类型的材料包括一种或多种基于非均质聚合物的组分和一种或多种基于非聚合物的组分(如,碳纤维)。下面参考图4和图5a-g更详细地描述了方法400。
方法400包括(方框410)成型预固化的复合纵梁190,如使用复合铺层502。该操作使用成型装置510(如图5a和5b所示)执行,成型装置510备不同于后面的操作中使用的后成型加工装置100(图5c-5f中所示)。如上所述,由于使用后成型加工装置100执行各种后面的操作,后成型加工装置100增加了成型装置510的生产量。
在一些示例中,复合铺层502包括未固化的预浸渍的增强带或织物,其可以被称为预浸料。带或织物包括嵌入在基质材料(诸如聚合物,或更具体地环氧树脂或酚醛树脂)内的纤维,诸如石墨纤维。在一些示例中,带或织物是单向的或是机织的,这取决于所得复合纵梁198所需的设计和增强程度。
在成型操作期间(方框410),将复合铺层502定位在成型装置510上,如图5a所示。在一些示例中,如当支撑结构120与预固化的复合纵梁190一起共成型时,支撑结构120被定位在复合铺层502与成型装置510之间。这些示例在下面参考方框412进一步描述。成型装置510包括带有成型空腔512的成型基座511,成型空腔512限定预固化的复合纵梁的帽部分191的形状。参照图5b,成型装置510还包括成型模具513,其将复合铺层502的一部分推入成型空腔512中并抵靠成形空腔512的壁。
完成此操作后,将复合铺层502成型为预固化的复合纵梁190。预固化的复合纵梁190包括帽部分191,其设置在成型模具513与成型空腔512的壁之间。预固化的复合纵梁190还包括凸缘部分196,其在成型空腔512的外部延伸,且例如贴合成型基座511的成型表面514。在一些示例中,成型模具513包括特定配置的囊状物,其按压凸缘部分196。这些囊状物在成型帽部分191之前被加压并接触凸缘部分196,在一些示例中达到不同的压力水平,以在形成帽部分191时允许复合铺层502在成型表面514上滑动。
在一些示例中,在成型装置上成型预固化的复合纵梁190包括(方框412)成型后成型加工装置100的支撑结构120。例如,支撑结构120包括夹紧材料,其各种示例和特征如上所述。在一些示例中,支撑结构120在与预固化的复合纵梁190分开的操作中成形。可选地,支撑结构120和预固化的复合纵梁190在相同的总体操作中共成型或共成形,如,由方框412表示的操作是由方框410表示的操作的一部分,如图4所示。换句话说,将支撑结构120与复合铺层502一起放置到成型装置510中。在此阶段,支撑结构120的形状不同于预固化的复合纵梁190的形状,预固化的复合纵梁190将在成型装置510上成型并由其限定。例如,支撑结构120先前已被用于支撑具有不同形状的另一预固化的复合纵梁190。在由方框410和方框412表示的并行操作期间,成型预固化的复合纵梁190,同时支撑结构120也被共成型或共成形。该支撑结构成型操作(方框412)也可以被称为形状改变操作。
在一些示例中,方法400还包括预固化的复合纵梁190的修整,如,切割预固化的复合纵梁190的部分。例如,使用超声刀进行切割。
方法400继续(方框420)将预固化的复合纵梁190从成型装置510转移到后成型加工装置100。比如,在图5b-5c中显示了预固化的复合纵梁190从成型装置510到后成型加工装置100的转移。以上描述了后成型加工装置100的各种示例。在一些示例中,预固化的复合纵梁190被无支撑地转移。可选地,将预固化的复合纵梁190与支撑结构120一起转移。
在一些示例中,转移操作包括控制基座110的槽道112内部的压力。例如,将预固化的复合纵梁190的帽部分191插入槽道112可能引起空气从槽道112移位,如通过通孔116。
在一些示例中,转移操作包括(方框422)拉伸后成型加工装置100的支撑结构120。在这些示例中,由于帽部分被插入到槽道112中,因此支撑结构120由与预固化的复合纵梁190的帽部分191的形状贴合的弹性材料形成。更具体地,弹性材料配置为当与帽部分191中的每一个贴合时改变形状。如上所述,在一些示例中,帽部分191具有不同的横截面形状。如图2a-2b所示,支撑结构120的这种拉伸特征允许支撑具有不同大小的帽部分191的预固化复合纵梁190。
在一些示例中,转移操作包括(方框424)调整后成型加工装置100的形状。图6a和6b示出了后成型加工装置100的基座110,其具有由第一轴线601限定的枢轴点。为了简单起见,未示出后成型加工装置100的其他零件,诸如支撑结构120等。枢轴点允许基座110具有平面内弯曲,并容纳直的预固化的复合纵梁(在图6a中所示的配置)和具有平面内弯曲的预固化的复合纵梁(在图6b中所示的配置)。尽管在图6a和6b中仅示出了一个枢轴点,但是本领域普通技术人员将理解,可以存在任何数量的枢轴点。此外,在一些示例中,后成型加工装置100具有平面外弯曲功能。应该注意的是,预固化的复合纵梁的一些程度的弯曲,尤其是局部弯曲,可以由基座110内的槽道112侧面容纳,而不使基座110弯曲。
在一些示例中,方法400包括(方框430)检查预固化的复合纵梁190。在预固化的复合纵梁190定位在后成型加工装置100上时执行该检查。例如,检查涉及检查预固化的复合纵梁190的表面的皱纹、气泡、异物碎屑(fod)、松散纤维、皱纹和形状。应当注意,检查操作是远离成型装置510和固化装置540进行的,从而允许在这些装置上进行其他预固化的复合纵梁的加工,并增加整体工艺生产量。
方法400包括(框440)在预固化的复合纵梁190上安装囊状物520,如在图5d中示意性地示出。在将预固化的复合纵梁190定位在后成型加工装置100上时安装囊状物520。在一些示例中,将囊状物520包裹在囊状物包裹物中,然后在移出囊状物520时将其固化为纵梁的蒙皮。囊状物520在固化操作期间使用以在预固化的复合纵梁190内部提供支撑。在一些示例中,囊状物520是由硅氧烷、聚氨酯或类似材料(包括其任意组合)组成的固体物体。在一些示例中,囊状物520被成形以与预固化的复合纵梁190基本对应。
方法400包括(方框450)将条状物530安装在囊状物520与预固化的复合纵梁190之间的界面处并且在基座110的支撑表面114的平面内,如图5e中示意性所示。在将预固化的复合纵梁190定位在后成型加工装置100上时执行此安装操作。条状物530也称为圆角填料(radiusfiller)。
在一些示例中,方法400包括(方框460)在将预固化的复合纵梁190定位在后成型加工装置100上时,压实预固化的复合纵梁190。例如,压实操作涉及将后成型加工装置100的罩130抵靠后成型加工装置100的基座110密封,如图5f示意性地示出。在一些示例中,压紧操作还包括至少使预固化的复合纵梁190的凸缘部分196与后成型加工装置100的罩130接触。
在一些示例中,方法400包括展现(staging)和运输预固化的复合纵梁190。这些操作在将预固化的复合纵梁190定位在后成型加工装置100上时执行。此外,后成型加工装置100用于存储预固化的复合纵梁190,同时为预固化的复合纵梁190提供支撑。
方法400继续(方框490)将预固化的复合纵梁190从后成型加工装置100转移到固化装置540。比如,在图5f-5g中示出了预固化的复合纵梁190从后成型加工装置100到固化装置540的转移。在一些示例中,将预固化的复合纵梁190与囊状物520和/或条状物530一起转移,在将预固化的复合纵梁190定位在后成型加工装置100上时,将囊状物520和/或条状物530安装到预固化的复合纵梁190上。
方法400包括(方框492)在固化装置540上固化预固化的复合纵梁190,从而成型复合纵梁198,如图5g和5h中示意性示出。例如,如图5g所示的预固化的复合纵梁190经受热和压力以使预固化的复合纵梁190内的树脂交联。与预固化的复合纵梁190不同,图5h所示的复合纵梁198不需要预固化的复合纵梁190所需的支撑水平。因此,后成型加工装置100不用于复合纵梁198。
在一些示例中,使用另加的预固化复合纵梁199(例如图1e中示出了其中一个示例)重复方法400的各种操作(判定框494)。具体地,另外的预固化的复合纵梁199具有与先前使用相同后成型加工装置100加工的预固化的复合纵梁190不同的设计。图1c-1e显示了预固化的复合纵梁的各种不同的设计。预固化的复合纵梁的其他示例设计也是可能的。
具体地,方法400包括在另外的成型装置上410成型另外的预固化的复合纵梁199。与可以在各种不同设计的预固化的复合纵梁上通用的后成型加工装置100不同,成型装置是专用工具。在一些示例中,在成型另加的预固化复合纵梁199的该操作过程中,支撑结构120进行再成型或再成形。更具体地,在支撑另外的预固化的复合纵梁199时与支撑预固化的复合纵梁190时,支撑结构120具有不同的形状。
方法400继续(方框420)将该另加的预固化的复合纵梁199从成型装置转移到后成型加工装置100。如上所述,另外的预固化的复合纵梁199具有与预固化的复合纵梁190不同的设计,并且更具体地,不同的横截面轮廓。
在一些示例中,方法400继续在将另外的预固化的复合纵梁199定位在后成型加工装置100上时,在另外的预固化的复合纵梁199上安装另外的囊状物。此外,在另外的预固化的复合纵梁199定位在后成型加工装置100上时,将条状物安装在另外的预固化的复合纵梁199上。然而,这些操作是任选的。
方法400继续将另外的预固化的复合纵梁199连同另外的囊状物和另外的条状物从后成型加工装置100转移到另外的固化装置,并且使用另外的固化装置来固化预固化的复合纵梁190,从而成型另外的复合纵梁。
图7是根据本公开的一些示例的使用后成型加工装置100支撑预固化的复合纵梁190的方法700的工艺流程图。方法700包括(方框720)将预固化的复合纵梁190转移到后成型加工装置100,例如在图5c中示意性地示出。上面描述了预固化的复合纵梁190的各种示例。例如,预固化的复合纵梁190包括帽部分191,其在将预固化的复合纵梁190转移到后成型加工装置100时被支撑。后成型加工装置100包括基座110,其包括槽道112。后成型加工装置100还包括支撑结构120,该支撑结构120至少部分地在槽道112内并沿槽道112的长度延伸。
当将预固化的复合纵梁190转移到后成型加工装置100时,与预固化的复合纵梁190的帽部分191贴合的支撑结构120在例如图5c中示意性地示出。更具体地,当预固化的复合纵梁190定位在后成型加工装置100中时,支撑结构120保持预固化的复合纵梁190的帽部分191的横截面形状。在一些示例中,支撑结构120由柔性材料制成,提供这种贴合(共形,conformal)支撑。在其他示例中,支撑结构120由与每种新的预固化的复合纵梁一起再成形的夹紧材料制成。
在一些示例中,转移操作(方框720)包括(方框722)拉伸后成型加工装置100的支撑结构120,例如图2a-2b中示意性地示出。在这些示例中,支撑结构120由弹性材料形成,其在帽部分插入槽道112中时贴合预固化的复合纵梁190的帽部分191的形状。支撑结构120的这种拉伸特征允许支撑具有不同大小的帽部分191的预固化的复合纵梁190。
在一些示例中,转移操作(方框720)包括(方框724)调整后成型加工装置100的形状。图6a和6b图解了后成型加工装置100的基座110,其具有由第一轴线601限定的枢轴点。为了简单起见,未示出后成型加工装置100的其他零件,诸如支撑结构120。枢轴点允许基座110具有平面内弯曲,并容纳直的预固化的复合纵梁(在图6a中所示的配置)和具有平面内弯曲的预固化的复合纵梁(在图6b中所示的配置)。尽管在图6a和6b中仅示出了一个枢轴点,但是本领域普通技术人员将理解,可以存在任何数量的枢轴点。此外,在一些示例中,后成型加工装置100具有平面外弯曲功能。应该注意的是,预固化的复合纵梁的一些程度的弯曲,尤其是局部弯曲,可以由基座110内的槽道112侧面容纳,而不使基座110弯曲。
在一些示例中,转移操作(方框720)包括(方框726)抵靠后成型加工装置100的基座110定位后成型加工装置100的罩130,例如图5f示意性地显示。在一些示例中,罩130抵靠基座110密封。此外,在一些示例中,该罩定位操作(方框726)至少压实预固化的复合纵梁190的凸缘部分196。
在一些示例中,转移操作(框架720)包括(方框728)控制基座110的槽道112内部的压力。例如,将预固化的复合纵梁190的帽部分191插入槽道112可能引起空气从槽道112移位,如通过通孔116。
在一些示例中,方法700包括(方框730)存储预固化的复合纵梁190。更具体地,(方框740)在从后成型加工装置100移出预固化的复合纵梁190之前,将预固化的复合纵梁190存储在后成型加工装置100中。
方法700继续(方框740)从后成型加工装置100中移出预固化的复合纵梁190。例如,预固化的复合纵梁190被转移到固化装置540,例如图5g中示意性地示出。可选地,将预固化的复合纵梁190转移到其他仪器上,如进行检查。
方法700进行,或更具体地重复(判定框794),其中(方框720)将另外的预固化的复合纵梁199转移到后成型加工装置100,例如图5i中示意性地显示。另外的预固化的复合纵梁199包括另外的帽部分193,使得另外的预固化的复合纵梁199的另外的帽部分193的横截面形状不同于预固化的复合纵梁190的帽部分191的横截面形状,如图5c所示。然而,尽管横截面形状存在这种差异,但后成型加工装置100的支撑结构120仍贴合另外的预固化的复合纵梁199的另外的帽部分193。此外,支撑结构120保留另外的预固化的复合纵梁199的另外的帽部分193的横截面形状。
飞机示例
在一些示例中,上文所述的方法和系统被用于飞机上,并且更一般地被航空航天工业使用。具体地,这些方法和系统可以在飞机制造期间以及飞机维修和保养期间使用。
因此,上述设备和方法适用于图8所示的飞机制造和维修方法900以及图9所示的飞机902。在生产前期间,方法900包括飞机902的规格和设计904以及材料采购906。在生产期间,进行飞机902的零件和子组件制造908以及系统集成910。此后,飞机902经历认证和交付912,以便被投入使用914。在客户服务期间,飞机902被安排进行日常维护和保养916,其还包括修改、重新配置、翻新等。
在一些示例中,方法900的每个过程都由系统集成商、第三方和/或操作者(例如客户)执行或进行。为了描述的目的,系统集成商包括但不限于任何数量的飞机制造商和主系统分包商;第三方包括但不限于任何数量的销售商、分包商和供应商;操作者可以是航空公司、租赁公司、军事实体、服务组织等。
如图9所示,由方法900生产的飞机902包括具有多个系统920的机身918和内部922。系统920的示例包括推进系统924、电气系统926、液压系统928和环境系统930中的一个或多个。可以包括任意数量的其他系统。尽管示出了航空示例,但是本文描述的示例的原理适用于其他工业,例如汽车工业。
可以在方法900的任何一个或多个阶段中采用本文介绍的设备和方法。例如,以类似于飞机902在使用中时生产的零件或子组件的方式来制造或制作与制造908相对应的零件或子组件。再者,在制造908和系统集成910期间利用一个或多个设备示例、方法示例或其组合,例如,通过实质上加快飞机902的组装或降低飞机902的成本。类似地,在飞机902使用时,例如但不限于维护和保养916时,利用设备示例、方法示例或其组合中的一个或多个。
进一步实施例
进一步,描述包括根据以下条款的实施例:
条款1.用于支撑预固化的复合纵梁的后成型加工装置,所述预固化的复合纵梁包括帽部分,其在所述预固化的复合纵梁之间具有不同的横截面,所述后成型加工装置包括:
基座,其包括槽道,所述槽道具有槽道宽度和槽道高度,其中:
所述槽道宽度大于所述预固化的复合纵梁的所述帽部分的宽度,和
所述槽道高度大于所述预固化的复合纵梁的所述帽部分的高度;
支撑结构,其在所述槽道内并沿所述槽道的长度至少部分地延伸,并配置为当由所述后成型加工装置支撑所述预固化的复合纵梁中对应一个时贴合所述帽部分中每个且保持所述帽部分中每个的横截面形状;和
罩,其配置为附接至所述基座,使得所述预固化的复合纵梁中对应一个被定位在所述罩和所述基座之间,同时由所述后成型加工装置支撑。
条款2.根据条款1的后成型加工装置,其中所述支撑结构由弹性材料形成,所述弹性材料配置为当贴合所述帽部分中每个时改变形状。
条款3.根据条款2的后成型加工装置,其中所述支撑结构在所述槽道的侧壁处附接至所述基座。
条款4.根据条款1-3中任一项的后成型加工装置,其中所述支撑结构包括夹紧材料或塑性可变形材料。
条款5.根据条款4的后成型加工装置,其中所述支撑结构与所述预固化的复合纵梁中对应一个共成型。
条款6.根据条款4的后成型加工装置,其中所述支撑结构包括在所述基座的支撑表面上且在所述槽道外部延伸的支撑凸缘。
条款7.根据条款4的后成型加工装置,其中所述支撑结构可从所述基座移出。
条款8.根据条款1-7中任一项的后成型加工装置,其中所述基座包括通孔,其与所述槽道流体地连接且配置为控制所述槽道内部的压力。
条款9.根据条款1-8中任一项的后成型加工装置,进一步包括柔性插入件,其与所述槽道一起且在所述支撑结构下方定位。
条款10.根据条款1-9中任一项的后成型加工装置,其中所述罩配置为抵靠所述基座密封。
条款11.制造复合纵梁的方法,所述方法包括:
在成型装置上成型预固化的复合纵梁,所述预固化的复合纵梁包括帽部分;
将所述预固化的复合纵梁从所述成型装置转移至后成型加工装置,所述后成型加工装置包括:
基座,其包括槽道,和
支撑结构,其在所述槽道内并沿所述槽道的长度至少部分地延伸,并配置为贴合所述帽部分且保持所述帽部分的横截面形状;和
在将所述预固化的复合纵梁定位在所述后成型加工装置上时,将囊状物安装在所述预固化的复合纵梁上;
在将所述预固化的复合纵梁定位在所述后成型加工装置上时,将条状物安装在所述囊状物和所述预固化的复合纵梁之间的界面处并且在所述基座的支撑表面的平面内;
将所述预固化的复合纵梁连同所述囊状物和所述条状物从所述后成型加工装置转移至固化装置;和
在所述固化装置上固化所述预固化的复合纵梁,由此成型所述复合纵梁。
条款12.根据条款11的方法,进一步包括在将所述预固化的复合纵梁定位在所述后成型加工装置上时,检查所述预固化的复合纵梁。
条款13.根据条款11-12中任一项的方法,进一步包括在将所述预固化的复合纵梁定位在所述后成型加工装置上时,压实所述预固化的复合纵梁。
条款14.根据条款13的方法,其中压实所述预固化的复合纵梁包括抵靠所述后成型加工装置的所述基座密封所述后成型加工装置的罩。
条款15.根据条款14的方法,其中压实所述预固化的复合纵梁包括使所述预固化的复合纵梁的至少凸缘部分接触所述后成型加工装置的罩。
条款16.根据条款11-15中任一项的方法,其中在所述成型装置上成型所述预固化的复合纵梁包括成型所述后成型加工装置的支撑结构。
条款17.根据条款11-16中任一项的方法,其中将所述预固化的复合纵梁从所述成型装置转移至所述后成型加工装置包括控制所述基座的槽道内部的压力。
条款18.根据条款11-17中任一项的方法,其中将所述预固化的复合纵梁从所述成型装置转移至所述后成型加工装置包括拉伸所述后成型加工装置的支撑结构。
条款19.根据条款11-18中任一项的方法,进一步包括:
在另外的成型装置上成型另外的预固化的复合纵梁;
将所述另外的预固化的复合纵梁从所述成型装置转移至所述后成型加工装置,其中所述另外的预固化的复合纵梁具有与所述预固化的复合纵梁不同的横截面轮廓;
在将所述另外的预固化的复合纵梁定位在所述后成型加工装置上时,在所述另外的预固化的复合纵梁上安装另外的囊状物;
在将所述另外的预固化的复合纵梁定位在所述后成型加工装置上时,在所述另外的预固化的复合纵梁上安装另外的条状物;
将所述另外的预固化的复合纵梁连同所述另外的囊状物和所述另外的条状物一起从所述后成型加工装置转移至另外的固化装置;和
使用所述另外的固化装置固化所述预固化的复合纵梁,由此成型另外的复合纵梁。
条款20.根据条款19的方法,其中所述支撑结构当支撑所述另外的预固化的复合纵梁时具有与支撑所述预固化的复合纵梁时不同的形状。
条款21.一种方法,其包括:
将包括帽部分的预固化的复合纵梁转移至后成型加工装置,所述后成型加工装置包括:
基座,其包括槽道,和
支撑结构,其在所述槽道内并沿所述槽道的长度至少部分地延伸,并贴合所述预固化的复合纵梁的所述帽部分且保持所述预固化的复合纵梁的所述帽部分的横截面形状;和
从所述后成型加工装置移出所述预固化的复合纵梁;和
将包括另外的帽部分的另外的预固化的复合纵梁转移至所述后成型加工装置,其中所述后成型加工装置的支撑结构贴合所述另外的预固化的复合纵梁的另外的帽部分并且保持所述另外的预固化的复合纵梁的另外的帽部分的横截面形状,所述另外的预固化的复合纵梁的另外的帽部分的横截面形状不同于所述预固化的复合纵梁的帽部分的横截面形状。
条款22.根据条款21的方法,其中转移所述预固化的复合纵梁包括抵靠所述后成型加工装置的基座定位所述后成型加工装置的罩。
条款23.根据条款21-22中任一项的方法,其中转移所述预固化的复合纵梁至所述后成型加工装置包括控制所述基座的槽道内部的压力。
条款24.根据条款21-23中任一项的方法,其中转移所述预固化的复合纵梁至所述后成型加工装置包括拉伸所述后成型加工装置的支撑结构。
条款25.根据条款21-24中任一项的方法,其中在从所述后成型加工装置移出所述预固化的复合纵梁之前,所述后成型加工装置用于储存所述预固化的复合纵梁。
结论
尽管出于清楚理解的目的已经详细描述了前述概念,但是将显而易见的是,可以在所附权利要求的范围内进行某些改变和修改。应该注意的是,有许多实现方法、系统和设备的替代方式。因此,本示例被认为是说明性的而非限制性的。
本文用于企业家、创业者技术爱好者查询,结果仅供参考。