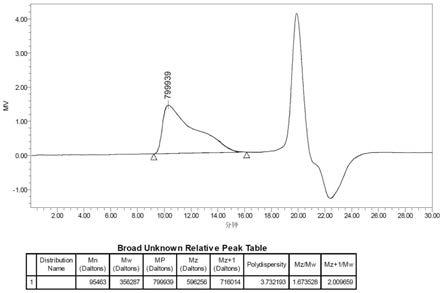
1.本发明属于胶黏剂技术领域,具体涉及一种高弹性光固化丙烯酸泡棉胶带的合成工艺。
背景技术:
2.压敏胶是一类在外力轻压下即能与被粘物粘合的胶粘剂,俗称不干胶,具有在较长时间内不会干涸的特点,而泡棉胶带是一种特殊的压敏胶带,具有密封、减震的作用,并在医疗卫生、汽车工业等众多领域中均得到了应用。常见的泡棉胶带主要有两类,其中最常见的一类是以pet哑光离型膜为基材,然后在其一面或两面涂以压敏胶再复以离型纸制造而成;另一类是聚丙烯酸酯双面泡棉胶带,胶带全部由聚丙烯酸酯类粘弹体构成,这种结构赋予了胶带的整体粘弹性,胶带整体能有效地将粘接接头里面的应力通过胶带的力学松弛耗散掉。前一类泡棉胶带通常具有较好的弹性及强度,但表层的胶粘剂容易与pet哑光离型膜脱离,容易产生残胶,此外,耐温性能及使用寿命也相对一般;后一类胶带虽然具有很好的耐候性及透光性,具有粘贴时间越长粘性越好的特点,但通常弹性较差,容易产生断裂。如何综合两类泡棉胶带的优点并获得高弹性的泡棉胶带将具有重要的应用价值,而弹性体压敏胶通常具有较好的粘弹性,目前尚未有将弹性体应用到聚丙烯酸酯双面泡棉胶带以增强其弹性的产品。
技术实现要素:
3.针对现有技术中存在的问题,本发明的目的在于提供一种操作容易、对设备要求低的高弹性光固化丙烯酸泡棉胶带的制备工艺。通过选用合适的原料采用光聚合方法制备预聚物,然后加入弹性体及光固化所需原料进行光固化,获得最终的聚丙烯酸酯泡棉胶带。
4.所述的一种高弹性光固化丙烯酸泡棉胶带的合成工艺,其特征在于包括如下步骤:(1)预聚物的制备将软单体和功能单体混合形成混合单体溶液,将其分为两部分,大部分混合单体溶液先加入反应釜中,向反应釜中加入适量的光引发剂和链转移剂,在氮气保护下进行搅拌,反应釜置于常温水浴中,充分搅拌后在紫外灯(高压汞灯或波长为365 nm的led光源)照射下进行引发聚合反应,当反应体系的粘度达到一定值后关闭紫外灯,并逐滴缓慢滴加剩余的另一小部分混合单体溶液,滴加完后继续搅拌1~3小时得到预聚物溶液;(2)光固化制备泡棉胶带将弹性体和光引发剂溶解在软单体中,然后将该混合溶液与步骤(1)所得预聚物溶液充分搅拌混合制得胶水;在一片pet哑光离型膜上滴涂上述制备的胶水后,盖上另一片pet哑光离型膜,然后在两片pet哑光离型膜的膜边贴上0.5~1.5mm厚的档条,然后用压辊制备得到胶带,经过紫外光固化后制得高弹性光固化丙烯酸泡棉胶带。
5.所述的一种高弹性光固化丙烯酸泡棉胶带的合成工艺,其特征在于步骤(1)中,所
述软单体为丙烯酸乙酯、丙烯酸丁酯或丙烯酸异辛酯,功能单体为丙烯酸或甲基丙烯酸,软单体和功能单体的质量比为7~11:1。
6.所述的一种高弹性光固化丙烯酸泡棉胶带的合成工艺,其特征在于步骤(1)中,先加入反应釜中的大部分混合单体溶液占混合单体溶液总量的65~90%,其余另一小部分混合单体溶液在聚合反应之后滴加到反应釜中。
7.所述的一种高弹性光固化丙烯酸泡棉胶带的合成工艺,其特征在于步骤(1)和步骤(2)中,所述光引发剂为2
‑
羟基
‑2‑
甲基
‑1‑
苯基
‑1‑
丙酮(1173)、1
‑
羟基环己基苯基甲酮(184)、2
‑
甲基
‑1‑
(4
‑
甲硫基苯基)
‑2‑
吗啉
‑1‑
丙酮(907)等;步骤(1)中,链转移剂为十二烷基硫醇(ndm)。
8.所述的一种高弹性光固化丙烯酸泡棉胶带的合成工艺,其特征在于步骤(1)中,光引发剂的质量是总的混合单体溶液质量的0.15~1%,链转移剂的质量是总的混合单体溶液质量的0.1~1%。
9.所述的一种高弹性光固化丙烯酸泡棉胶带的合成工艺,其特征在于步骤(2)中,所述弹性体为苯乙烯嵌段共聚物,如苯乙烯一异戊二烯一苯乙烯嵌段共聚物(sis)、苯乙烯—丁二烯—苯乙烯嵌段共聚物(sbs)、苯乙烯一乙烯/丁烯一苯乙烯嵌段共聚物(sebs)、苯乙烯—丁烯/丙烯—苯乙烯嵌段共聚物(seps)等。
10.所述的一种高弹性光固化丙烯酸泡棉胶带的合成工艺,其特征在于步骤(2)弹性体和光引发剂溶解在软单体形成的混合溶液中,按照组成原料以质量百分比计,其中软单体占比:15~25%,弹性体占比:3~5%,光引发剂:0.15~1%。所述弹性体和光引发剂溶解在软单体形成的混合溶液,与步骤(1)所得预聚物溶液进行混合的质量比是1:3~5,优选为1:3.9~4.1。
11.所述的一种高弹性光固化丙烯酸泡棉胶带的合成工艺,其特征在于步骤(2)中,胶水在pet哑光离型膜上的滴涂量为0.1~0.2 g/cm2。
12.所述的一种高弹性光固化丙烯酸泡棉胶带的合成工艺,其特征在于步骤(2)中,所述紫外光固化的操作条件是:经紫外线照射固化,紫外线辐射强度1300~1500 mw/cm2,照射固化时间是10~20秒。
13.相对于现有技术,本发明取得的有益效果是:本发明丙烯酸泡棉胶带的制备方法其工艺简单易行,绿色环保,且固化速度快、固化效率高、能耗小和固化过程中污染小。制得的丙烯酸泡棉胶带具有高粘性、高弹性及高断裂应变,且与常规泡棉胶带在泡棉芯材两面涂胶粘剂的方法不同,棉芯材和表层的胶粘剂全部由聚丙烯酸酯类粘弹体构成,从而赋予了胶带特殊的整体粘弹性,具有很高的应用价值。
附图说明
14.图1为本发明实施例1中预聚物分子量分布的凝胶渗透色谱(gpc)测试结果图。
具体实施方式
15.下面结合具体实施例对本发明作进一步说明,但本发明的保护范围并不限于此。
16.实施例1:
(1)预聚物的制备将丙烯酸丁酯和丙烯酸按照8:1的质量比混合,形成混合单体溶液。往反应釜和恒压分液漏斗中分别加入150克和50克上述配制的混合单体溶液,向反应釜中加入0.5克1173光引发剂和0.5克ndm,在氮气保护下进行搅拌,反应釜置于常温水浴中,充分搅拌后打开紫外灯(采用波长为365 nm的led光源)引发聚合反应,当反应体系的粘度达到20000 cps后关闭光源,并通过恒压分液漏斗向反应釜中缓慢滴加混合单体溶液(共计50克),半小时内滴加完后继续搅拌2小时得到预聚物溶液,预聚物的分子量分布测试结果如图1所示。
17.(2)光固化制备泡棉胶带将5克sis弹性体(牌号4114)和0.2克1173光引发剂溶解在20克丙烯酸丁酯中,然后将该混合溶液与100克步骤(1)制得的预聚物溶液充分搅拌混合制得胶水。在一片pet哑光离型膜(尺寸为10 cm
´
8 cm)上滴加约15克胶水后盖上另一片同等尺寸的pet哑光离型膜,在膜边贴上1.0毫米厚的档条,然后用压辊制备得到胶带,经过紫外光固化(所述紫外光固化的操作条件是:经紫外线照射固化,紫外线辐射强度1400 mw/cm2,照射固化时间是15秒)后制得高弹性光固化丙烯酸泡棉胶带。
18.对于实施例1制得的高弹性光固化丙烯酸泡棉胶带产品,采用硬度计(lx
‑
a)测试硬度,国标方法测试初粘(gb/t 4582
‑
2002)及剥离强度(gb/t 2792
‑
2014)。裁剪出尺寸为0.8 cm
×
3.0 cm的泡棉胶带,然后采用动态力学分析仪中测定其杨氏模量及断裂应变(取10次有效测定结果的平均值)。
19.实施例2(1)预聚物的制备将丙烯酸乙酯和丙烯酸按照7:1的质量比混合,形成混合单体溶液。往反应釜和恒压分液漏斗中分别加入160克和40克上述配制的混合单体溶液,向反应釜中加入0.5克1173光引发剂和0.5克ndm,在氮气保护下进行搅拌,反应釜置于常温水浴中,充分搅拌后打开紫外灯(采用波长为365 nm的led光源)引发聚合反应,当反应体系的粘度达到20000 cps后关闭光源,并通过恒压分液漏斗向反应釜中缓慢滴加混合单体溶液(共计40克),半小时内滴加完后继续搅拌2小时得到预聚物溶液。
20.(2)光固化制备泡棉胶带将5克sbs弹性体(牌号3411)和0.2克光引发剂(1173)溶解在20克丙烯酸丁酯中,然后将该混合溶液与100克步骤(1)制得的预聚物溶液充分搅拌混合制得胶水。在一片pet哑光离型膜(尺寸为10 cm
´
8 cm)上滴加约15克胶水后盖上另一片同等尺寸的pet哑光离型膜,在膜边贴上1.0毫米厚的档条然后用压辊制备得到胶带,经过紫外光固化(所述紫外光固化的操作条件是:经紫外线照射固化,紫外线辐射强度1400 mw/cm2,照射固化时间是15秒)后制得高弹性光固化丙烯酸泡棉胶带。
21.对于实施例2制得的高弹性光固化丙烯酸泡棉胶带产品进行性能测试,测试项目及测试方法重复实施例1中。
22.实施例3(1)预聚物的制备将丙烯酸丁酯和丙烯酸按照11:1的质量比混合,形成混合单体溶液。往反应釜和恒压分液漏斗中分别加入140克和60克上述配制的混合单体溶液,向反应釜中加入0.5克光
引发剂(1173)和0.5克ndm,在氮气保护下进行搅拌,反应釜置于常温水浴中,充分搅拌后打开紫外灯(采用波长为365 nm的led光源)引发聚合反应,当反应体系的粘度达到20000 cps后关闭光源,并通过恒压分液漏斗向反应釜中缓慢滴加混合单体溶液(共计60克),半小时内滴加完后继续搅拌2小时得到预聚物溶液。
23.(2)光固化制备泡棉胶带将5克sebs弹性体(牌号6151)和0.2克光引发剂(184)溶解在20克丙烯酸丁酯中,然后将该混合溶液与100克步骤(1)制得的预聚物溶液充分搅拌混合制得胶水。在一片pet哑光离型膜(尺寸为10 cm
´
8 cm)上滴加约15克胶水后盖上另一片同等尺寸的pet哑光离型膜,在膜边贴上1.0毫米厚的档条,然后用压辊制备得到胶带,经过紫外光固化(所述紫外光固化的操作条件是:经紫外线照射固化,紫外线辐射强度1400 mw/cm2,照射固化时间是15秒)后制得高弹性光固化丙烯酸泡棉胶带。
24.对于实施例3制得的高弹性光固化丙烯酸泡棉胶带产品进行性能测试,测试项目及测试方法重复实施例1中。
25.实施例4(1)预聚物的制备将丙烯酸丁酯和甲基丙烯酸按照10:1的质量比混合,形成混合单体溶液。往反应釜和恒压分液漏斗中分别加入150克和50克上述配制的混合单体溶液,向反应釜中加入0.5克光引发剂(1173)和0.5克ndm,在氮气保护下进行搅拌,反应釜置于常温水浴中,充分搅拌后打开紫外灯(采用波长为365 nm的led光源)引发聚合反应,当反应体系的粘度达到20000 cps后关闭光源,并通过恒压分液漏斗向反应釜中缓慢滴加混合单体溶液(共计50克),半小时内滴加完后继续搅拌2小时得到预聚物溶液。
26.(2)光固化制备泡棉胶带将4克seps弹性体(牌号4051)和0.2克光引发剂(1173)溶解在20克丙烯酸丁酯中,然后将该混合溶液与100克步骤(1)制得的预聚物溶液充分搅拌混合制得胶水。在一片pet哑光离型膜(尺寸为10 cm
´
8 cm)上滴加约15克胶水后盖上另一片同等尺寸的pet哑光离型膜,在膜边贴上1.0毫米厚的档条,然后用压辊制备得到胶带,经过紫外光固化(所述紫外光固化的操作条件是:经紫外线照射固化,紫外线辐射强度1400 mw/cm2,照射固化时间是15秒)后制得高弹性光固化丙烯酸泡棉胶带。
27.对于实施例4制得的高弹性光固化丙烯酸泡棉胶带产品进行性能测试,测试项目及测试方法重复实施例1中。
28.实施例5(1)预聚物的制备将丙烯酸异辛酯和丙烯酸按照7:1的质量比混合,形成混合单体溶液。往反应釜和恒压分液漏斗中分别加入160克和40克上述配制的混合单体溶液,向反应釜中加入0.5克光引发剂(1173)和0.5克ndm,在氮气保护下进行搅拌,反应釜置于常温水浴中,充分搅拌后打开紫外灯(采用波长为365 nm的led光源)引发聚合反应,当反应体系的粘度达到20000 cps后关闭光源,并通过恒压分液漏斗向反应釜中缓慢滴加混合单体溶液(共计40克),半小时内滴加完后继续搅拌2小时得到预聚物溶液。
29.(2)光固化制备泡棉胶带
将5克sis弹性体(牌号4114)和0.2克光引发剂(1173)溶解在20克丙烯酸丁酯中,然后将该混合溶液与100克步骤(1)制得的预聚物溶液充分搅拌混合制得胶水。在一片pet哑光离型膜(尺寸为10 cm
´
8 cm)上滴加约15克胶水后盖上另一片同等尺寸的pet哑光离型膜,在膜边贴上1.0毫米厚的档条,然后用压辊制备得到胶带,经过紫外光固化(所述紫外光固化的操作条件是:经紫外线照射固化,紫外线辐射强度1400 mw/cm2,照射固化时间是15秒)后制得高弹性光固化丙烯酸泡棉胶带。对于实施例5制得的高弹性光固化丙烯酸泡棉胶带产品进行性能测试,测试项目及测试方法重复实施例1中。
30.实施例1
‑
5为效果较好的案例,由于原料及配比不同,根据不同的应用场合,对应的胶带性能也有所差异。实施例1中预聚物的分子量分布如图1所示,只存在一个分子量峰,分布较窄(mz/mw = 1.67),说明只存在一次聚合,且通过ndm调控了分子量。
31.对比例1(1)预聚物的制备将丙烯酸丁酯和丙烯酸按照8:1的质量比混合,形成混合单体溶液。往反应釜和恒压分液漏斗中分别加入150克和50克上述配制的混合单体溶液,向反应釜中加入0.5克光引发剂(1173)和0.5克ndm,在氮气保护下进行搅拌,反应釜置于常温水浴中,充分搅拌后打开紫外灯(采用波长为365 nm的led光源)引发聚合反应,当反应体系的粘度达到20000 cps后关闭光源,并通过恒压分液漏斗向反应釜中缓慢滴加混合单体溶液(共计50克),半小时内滴加完后继续搅拌2小时得到预聚物溶液。
32.(2)光固化制备泡棉胶带将1克sis弹性体(牌号4114)和0.2克光引发剂(1173)溶解在20克丙烯酸丁酯中,然后将该混合溶液与100克步骤(1)制得的预聚物溶液充分搅拌混合制得胶水。在一片pet哑光离型膜(尺寸为10 cm
´
8 cm)上滴加约15克胶水后盖上另一片同等尺寸的pet哑光离型膜,在膜边贴上1.0毫米厚的档条,然后用压辊制备得到胶带,经过紫外光固化(所述紫外光固化的操作条件是:经紫外线照射固化,紫外线辐射强度1400 mw/cm2,照射固化时间是15秒)后制得高弹性光固化丙烯酸泡棉胶带。对比例1制得的高弹性光固化丙烯酸泡棉胶带产品进行性能测试,测试项目及测试方法重复实施例1中。
33.对比例2(1)预聚物的制备将丙烯酸异辛酯和丙烯酸按照8:1的质量比混合,形成混合单体溶液。往反应釜和恒压分液漏斗中分别加入180克和20克上述配制的混合单体溶液,向反应釜中加入0.5克光引发剂(1173)和0.5克ndm,在氮气保护下进行搅拌,反应釜置于常温水浴中,充分搅拌后打开紫外灯(采用波长为365 nm的led光源)引发聚合反应,当反应体系的粘度达到20000 cps后关闭光源,并通过恒压分液漏斗向反应釜中缓慢滴加混合单体溶液(共计20克),半小时内滴加完后继续搅拌2小时得到预聚物溶液。
34.(2)光固化制备泡棉胶带将5克sbs弹性体(牌号3411)和0.2克光引发剂(1173)溶解在20克丙烯酸丁酯中,然后将该混合溶液与100克步骤(1)制得的预聚物溶液充分搅拌混合制得胶水。在一片pet哑光离型膜(尺寸为10 cm
´
8 cm)上滴加约15克胶水后盖上另一片同等尺寸的pet哑光离型膜,在膜边贴上1.0毫米厚的档条,然后用压辊制备得到胶带,经过紫外光固化(所述紫外光
固化的操作条件是:经紫外线照射固化,紫外线辐射强度1400 mw/cm2,照射固化时间是15秒)后制得高弹性光固化丙烯酸泡棉胶带。对比例2制得的高弹性光固化丙烯酸泡棉胶带产品进行性能测试,测试项目及测试方法重复实施例1中。
35.对比例3(1)预聚物的制备将丙烯酸丁酯和丙烯酸按照8:1的质量比混合,形成混合单体溶液。往反应釜和恒压分液漏斗中分别加入150克和50克上述配制的混合单体溶液,向反应釜中加入0.5克光引发剂(1173)和0.5克ndm,在氮气保护下进行搅拌,反应釜置于常温水浴中,充分搅拌后打开紫外灯(采用波长为365 nm的led光源)引发聚合反应,当反应体系的粘度达到20000 cps后关闭光源,并通过恒压分液漏斗向反应釜中缓慢滴加混合单体溶液(共计50克),半小时内滴加完后继续搅拌2小时得到预聚物溶液。
36.(2)光固化制备泡棉胶带将8克sis弹性体(牌号4114)和0.2克光引发剂(1173)溶解在20克丙烯酸丁酯中,然后将该混合溶液与100克步骤(1)制得的预聚物溶液充分搅拌混合制得胶水。在一片pet哑光离型膜(尺寸为10 cm
´
8 cm)上滴加约15克胶水后盖上另一片同等尺寸的pet哑光离型膜,在膜边贴上1.0毫米厚的档条,然后用压辊制备得到胶带,经过紫外光固化(所述紫外光固化的操作条件是:经紫外线照射固化,紫外线辐射强度1400 mw/cm2,照射固化时间是15秒)后制得高弹性光固化丙烯酸泡棉胶带。对比例1制得的高弹性光固化丙烯酸泡棉胶带产品进行性能测试,测试项目及测试方法重复实施例1中。
37.将实施例1
‑
5及对比例1
‑
3的测试结果汇总于表1中。
38.对比例1与实施例1相比,降低了弹性体的用量,如表1所示,对比例1的断裂应变显著低于实施例1,断裂应变与弹性体组分的用量密切相关;对比例2与实施例1相比,降低了预聚物中未固化单体的含量,相当于增加了大分子量组分的占比,结果显示预聚物分子量的增加使得最终胶带的剥离强度增加,但对杨氏模量及断裂应变影响较小;对比例3与实施例1相比,增加了弹性体的用量,对比例3的硬度和杨氏模数显著低于实施例1,但断裂应变并没用明显提升,导致泡棉胶的整体性能下降。
39.本说明书所述的内容仅仅是对发明构思实现形式的列举,本发明的保护范围不应当被视为仅限于实施例所陈述的具体形式。
再多了解一些
本文用于企业家、创业者技术爱好者查询,结果仅供参考。