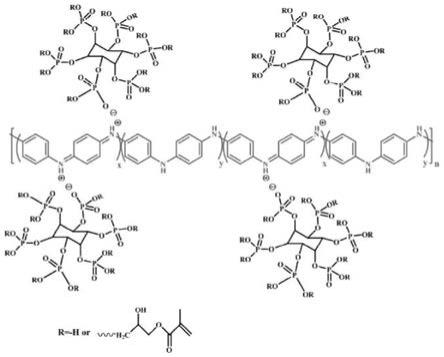
1.本发明涉及一种光敏植酸掺杂聚苯胺基紫外光固化防腐涂料的制备方法,属于金属防腐蚀涂料技术领域。
背景技术:
2.受外界腐蚀性介质侵蚀影响,金属及其合金往往会失去电子被氧化成不同价态金属氧化物,造成材料综合性能下降,给国民经济生产生活的方方面面带来不同程度的影响。目前减缓金属腐蚀最简便有效的手段仍是在金属基材上涂覆一层涂层,以隔绝水、氧气等直接接触。以导电聚苯胺为代表的防腐涂料在改善屏蔽型涂层(添加片层填料)无法满足长期防腐蚀条件的同时,还避免了因牺牲型涂层添加重金属离子填料带来的环境污染问题,倍受研究者青睐。
3.迄今为止导电聚苯胺更多的是与溶剂型涂料相结合,固化过程耗时长、耗能大,同时还会产生挥发性有机化合物(vocs)。伴随着全球范围内对环境政策的重视,紫外光固化涂料因不产生voc排放、固化速率快等优势脱颖而出。导电聚苯胺类防腐填料与光固化涂层的结合将成为未来防腐涂料发展的不二选择。
4.为解决导电聚苯胺因长程共轭结构带来的与涂料体系相容性不足缺陷问题,研究者往往选用无机酸、有机酸乃至高分子量聚合物酸作为掺杂剂,在提高聚苯胺相容性问题同时,赋予涂料多功能化选择。目前已报道的聚苯胺紫外光固化涂料中所选用的掺杂剂包括盐酸、甲磺酸(mesa)、十二烷基苯磺酸、木质素磺酸等,但这一系列质子酸往往只能单一作为掺杂剂以改善相容性,本身不具备功能性。将有色填料聚苯胺与光固化涂层结合使用时,由于深色填料对紫外光存在吸收或者反射,易引起涂料体系固化交联密度下降。另一方面光固化涂层固化交联时反应迅速、体系收缩应力来不及释放,造成涂层与金属基材的粘结作用下降,这也会影响涂层本身应对腐蚀侵蚀能力。针对上述问题,对掺杂剂的功能化设计是一种有效解决上述问题的措施。
5.目前用于聚苯胺掺杂的掺杂剂无附加功能属性,如果对其聚合物链段功能设计,以得到功能化(如双键交联、提高附着力、增强防腐性能)聚苯胺填料,并应用于紫外光固化体系中,可以较好的弥补光固化涂层应用于防腐领域时存在的不足。
技术实现要素:
6.目前质子酸多是通过对聚苯胺的掺杂,来改善因长程共轭结构带来的树脂相容性不佳问题,但质子酸本身无附加功能属性。紫外光固化树脂中引入深色颜料聚苯胺后,可能引发涂层交联密度下降以及附着力下降,造成涂层性能有所不足。如果能对掺杂剂链段设计,可以赋予其多功能化,以此来改善有色体系在紫外光固化防腐涂层领域的缺陷。
7.基于以上问题,本发明的第一个目的在于提供一种光敏植酸掺杂聚苯胺基紫外光固化防腐涂料,所述涂料包括预聚物、活性稀释剂、附着力促进剂、光引发剂以及光敏聚苯
胺,
8.所述光敏聚苯胺由聚苯胺与光敏植酸反应得到;
9.所述光敏植酸由植酸、甲基丙烯酸缩水甘油酯在阻聚剂和相转移催化剂存在的条件下反应得到。
10.进一步地,所述光敏聚苯胺的结构式如下:
[0011][0012]
其中n=30
‑
70(n表示聚合度,即该聚合物是由多少个类似重复单元组成)。
[0013]
进一步地,所述涂料组成为:预聚物70
‑
80份,活性稀释剂20
‑
30份,光引发剂1.0
‑
3.0份,附着力促进剂0.5
‑
2.5份,光敏聚苯胺0.5
‑
4.0份。
[0014]
进一步地,所述光敏聚苯胺的制备方法为将聚苯胺分散于水中,再加入光敏植酸,反应得到。
[0015]
进一步地,所述光敏植酸浓度为0.1
‑
2.0g/ml,优选为0.8
‑
1.5g/ml。
[0016]
进一步地,所述光敏植酸与聚苯胺质量比为10∶1
‑
200∶1,优选为25∶1
‑
50∶1;反应时间为1.0
‑
50h,优选为6.0
‑
25h;所述聚苯胺粒径为1.0
‑
20μm。
[0017]
进一步地,所述光敏植酸由植酸、甲基丙烯酸缩水甘油酯在阻聚剂和相转移催化剂存在的条件下反应得到。
[0018]
进一步地,所述植酸与甲基丙烯酸缩水甘油酯的投料摩尔比为1∶1
‑
1∶12;
[0019]
阻聚剂添加量为植酸与甲基丙烯酸缩水甘油酯总质量的0.1
‑
1.0wt%;
[0020]
相转移催化剂添加量为植酸与甲基丙烯酸缩水甘油酯总质量的0.5
‑
2.0wt%。
[0021]
进一步地,所述植酸与甲基丙烯酸缩水甘油酯反应的温度为60
‑
90℃,优选为80
‑
90℃,反应时间为0.5
‑
7.0h,优选为1.0
‑
2.0h,所述植酸与甲基丙烯酸缩水甘油酯反应在机械搅拌下进行,速度为100
‑
400rpm。
[0022]
进一步地,所述阻聚剂包括对苯二酚、对苯醌、对叔丁基邻苯二酚、2
‑
叔丁基对苯二酚、2,6
‑
二叔丁基对甲基苯酚、4,4
′‑
二经基联苯、酚噻嗪、β
‑
苯基萘胺中的一种或多种;所述相转移催化剂包括苄基三乙基氯化铵、四丁基溴化铵、三苯基膦、四丁基氯化铵、四丁
基硫酸氢铵、三辛基甲基氯化铵、十二烷基三甲基氯化铵、十四烷基三甲基氯化铵中的一种或多种;
[0023]
所述预聚物包括由环氧丙烯酸树脂、聚氨酯丙烯酸树脂、聚酯丙烯酸树脂、聚醚丙烯酸树脂、不饱和聚酯或丙烯酸酯官能化的聚丙烯酸酯树脂中的一种或多种;
[0024]
所述活性稀释剂包括四氢化糠基甲基丙烯酸酯、四氢化糠基丙烯酸酯、异冰片基丙烯酸酯、1,6
‑
己二醇二丙烯酸酯、二丙二醇二丙烯酸酯、三丙二醇二丙烯酸酯、月桂酸丙烯酸酯、双酚a缩水甘油双甲基丙烯酸酯或双环戊烯基乙氧化丙烯酸酯中的一种或多种;
[0025]
所述附着力促进剂包括2
‑
甲基
‑2‑
丙烯酸
‑2‑
羟乙基酯磷酸酯、磷酸氢二(甲基丙烯酰氧乙基)酯、乙烯基三甲氧基硅烷、γ
‑
甲基丙烯酰氧基丙基三甲氧基硅烷、β
‑
(3,4
‑
环氧环己基)乙基三甲氧基硅烷、γ
‑
(2,3
‑
环氧丙氧基)丙基三甲氧基硅烷或多官能磷酸酯改性丙烯酸酯中的一种或多种;
[0026]
所述光引发剂包括2
‑
羟基
‑
甲基苯基丙烷
‑1‑
酮、1
‑
羟基环已基苯基甲酮、2
‑
甲基
‑1‑
(4
‑
甲硫基苯基)
‑2‑
吗啉基
‑1‑
丙酮、2
‑
苄基
‑2‑
二甲基氨基
‑1‑
(4
‑
吗啉苯基)丁酮、安息香双甲醚、2,4,6
‑
三甲基苯甲酰基二苯基氧化膦、异丙基硫杂蒽酮、4
‑
(n,n
‑
二甲氨基)苯甲酸乙酯、二苯甲酮、4
‑
氯二苯甲酮、4,4
′‑
二甲基二苯基碘鎓盐六氟磷酸盐、对二甲氨基苯甲酸异辛酯、4
‑
甲基二苯甲酮、邻苯甲酰基苯甲酸甲酯、4
‑
苯基二苯甲酮中的一种或多种。
[0027]
本发明的第二个目的在于制备一种光敏植酸掺杂聚苯胺基紫外光固化防腐涂料,所述方法为:
[0028]
(1)光敏植酸的制备
[0029]
称取植酸、甲基丙烯酸缩水甘油酯,加入去离子水作为溶剂,并加入阻聚剂和相转移催化剂,反应得到光敏植酸;
[0030]
(2)光敏聚苯胺的制备
[0031]
将聚苯胺分散于水中,再加入(1)中所述光敏植酸,反应得到光敏聚苯胺;
[0032]
(3)一种光敏植酸掺杂聚苯胺基紫外光固化防腐涂料的制备
[0033]
将(2)中所述光敏聚苯胺加入到由预聚物、活性稀释剂、附着力促进剂和光引发剂组成的紫外光固化涂料中,得到光敏植酸掺杂聚苯胺基紫外光固化防腐涂料。
[0034]
进一步地,所述方法为:
[0035]
(1)制备光敏植酸(paga)
[0036]
植酸(pa)和甲基丙烯酸缩水甘油酯(gma)在水溶液中分散后,在相转移催化剂和阻聚剂作用下,搅拌下高温反应即得到光敏植酸。
[0037]
(2)制备光敏聚苯胺
[0038]
光敏植酸分散于水溶液中,搅拌下加入聚苯胺,超声分散后搅拌一段时间,过滤洗涤以得到光敏植酸掺杂后的光敏聚苯胺。
[0039]
(3)光敏聚苯胺基紫外光固化涂料的制备
[0040]
将光敏聚苯胺作为防腐填料,与预聚物、活性稀释剂、附着力促进剂、光引发剂共混,选用球磨分散均匀,筛网过滤后以得到光敏植酸掺杂聚苯胺基紫外光固化防腐涂料。
[0041]
进一步地,光敏植酸掺杂聚苯胺基紫外光固化涂料的制备方法中,(1)中所述植酸和甲基丙烯酸缩水甘油酯的反应摩尔比为1∶1
‑
1∶12,优选为1∶3
‑
1∶7。
[0042]
进一步地,光敏植酸掺杂聚苯胺基紫外光固化涂料的制备方法中,(1)中所述阻聚
剂为对苯二酚、对苯醌、对叔丁基邻苯二酚、2
‑
叔丁基对苯二酚、2,6
‑
二叔丁基对甲基苯酚、4,4
′‑
二经基联苯、酚噻嗪、β
‑
苯基萘胺中的一种或多种;所述阻聚剂添加量为反应性单体质量总量的0.1
‑
1.0wt%。
[0043]
进一步地,光敏植酸掺杂聚苯胺基紫外光固化涂料的制备方法中,(1)中所述的相转移催化剂为苄基三乙基氯化铵、四丁基溴化铵、三苯基膦、四丁基氯化铵、四丁基硫酸氢铵、三辛基甲基氯化铵、十二烷基三甲基氯化铵、十四烷基三甲基氯化铵中的一种或多种;所述相转移催化剂添加量为反应性单体质量总量的0.5
‑
2.0wt%。
[0044]
进一步地,光敏植酸掺杂聚苯胺基紫外光固化涂料的制备方法中,(1)中所述反应温度为60
‑
90℃,优选为80
‑
90℃,机械搅拌速度为100
‑
400rpm,反应时间为0.5
‑
7.0h,优选为1.0
‑
2.0h。
[0045]
进一步地,所述光敏植酸浓度为0.1
‑
2.0g/ml,优选为0.8
‑
1.5g/ml。
[0046]
进一步地,(2)中所述光敏植酸与聚苯胺质量比为10∶1
‑
200∶1,优选为25∶1
‑
50∶1,反应时间为1.0
‑
50h,优选为6.0
‑
25h,其中聚苯胺粒径为1.0
‑
20μm。
[0047]
进一步地,光敏植酸掺杂聚苯胺基紫外光固化涂料的制备方法中,(3)中所述紫外光固化涂料中各组分质量比组成如下:预聚物70
‑
80份,活性稀释剂20
‑
30份,光引发剂1.0
‑
3.0份,附着力促进剂0.5
‑
2.5份,光敏聚苯胺填料0.5
‑
4.0份,优选为0.5
‑
2.5份。
[0048]
进一步地,光敏植酸掺杂聚苯胺基紫外光固化涂料的制备方法中,(3)中所述预聚物组分是由环氧丙烯酸树脂、聚氨酯丙烯酸树脂、聚酯丙烯酸树脂、聚醚丙烯酸树脂、不饱和聚酯或丙烯酸酯官能化的聚丙烯酸酯树脂中的一种或多种组成。
[0049]
进一步地,光敏植酸掺杂聚苯胺基紫外光固化涂料的制备方法中,(3)中所述活性稀释剂包括四氢化糠基甲基丙烯酸酯、四氢化糠基丙烯酸酯、异冰片基丙烯酸酯、1,6
‑
己二醇二丙烯酸酯、二甲基丙烯酸二乙二醇酯、季戊四醇三丙烯酸酯、二丙二醇二丙烯酸酯、三丙二醇二丙烯酸酯、月桂酸丙烯酸酯、双酚a缩水甘油双甲基丙烯酸酯或双环戊烯基乙氧化丙烯酸酯中的一种或多种。
[0050]
进一步地,光敏植酸掺杂聚苯胺基紫外光固化涂料的制备方法中,(3)中所述的附着力促进剂为2
‑
甲基
‑2‑
丙烯酸
‑2‑
羟乙基酯磷酸酯、磷酸氢二(甲基丙烯酰氧乙基)酯、乙烯基三甲氧基硅烷、γ
‑
甲基丙烯酰氧基丙基三甲氧基硅烷、β
‑
(3,4
‑
环氧环己基)乙基三甲氧基硅烷、γ
‑
(2,3
‑
环氧丙氧基)丙基三甲氧基硅烷或多官能磷酸酯改性丙烯酸酯中的一种或多种;
[0051]
所述的光引发剂包括2
‑
羟基
‑
甲基苯基丙烷
‑1‑
酮、1
‑
羟基环已基苯基甲酮、2
‑
甲基
‑1‑
(4
‑
甲硫基苯基)
‑2‑
吗啉基
‑1‑
丙酮、2
‑
苄基
‑2‑
二甲基氨基
‑1‑
(4
‑
吗啉苯基)丁酮、安息香双甲醚、2,4,6
‑
三甲基苯甲酰基二苯基氧化膦、异丙基硫杂蒽酮、4
‑
(n,n
‑
二甲氨基)苯甲酸乙酯、二苯甲酮、4
‑
氯二苯甲酮、4,4
′‑
二甲基二苯基碘鎓盐六氟磷酸盐、对二甲氨基苯甲酸异辛酯、4
‑
甲基二苯甲酮、邻苯甲酰基苯甲酸甲酯、4
‑
苯基二苯甲酮中的一种或多种。
[0052]
进一步地,光敏聚苯胺基紫外光固化涂料的制备方法中,(3)中所述球磨分散速度为1500
‑
3000rpm,优选为2000
‑
2500rpm,分散时间为2
‑
30min;所选的筛网目数为100
‑
350目。
[0053]
本发明的第三个目的在于提供一种光敏植酸掺杂聚苯胺基紫外光固化防腐涂料的应用,将所述涂料涂布于基材表面,在uv全波段波长下固化,固化交联后得到光敏植酸掺
杂聚苯胺基紫外光固化防腐涂层,涂层干膜厚度为30
‑
70μm。
[0054]
有益效果:
[0055]
本发明提供了一种光敏植酸掺杂聚苯胺基紫外光固化防腐涂料的制备方法,聚苯胺作为一种环保绿色的防腐填料,不含重金属离子,且合成简便,当其应用于涂料中时,可以为基材提供阳极保护,自身的氧化还原循环可以生成钝化膜隔绝腐蚀介质侵蚀。光敏植酸对聚苯胺的掺杂在提高其与预聚物组分相容性同时,还在聚苯胺高分子链段上引入可参与光聚合过程的双键结构和提高附着力的磷酸酯结构。未添加填料的涂层为无色透明,聚苯胺掺杂后为深绿色填料,加入到涂层中时涂层会成有色体系。如聚苯胺、石墨烯(黑色)一类本身有颜色的填料加入到树脂中后使涂层带有颜色后,在紫外光固化过程中,这些填料本身会对紫外光进行吸收反射等,造成紫外光固化时辐照涂层的紫外光层层消弱,与基材接触的底层涂料可能未完成固化,造成交联密度下降。另一方面,填料也会占据树脂基体与金属基材的机械铆接区域,造成两者物理黏合作用下降,附着力下降。为有色颜填料体系在紫外光固化进程中聚合交联度低、瞬时反应附着力差的难题提供了一条有益思路。
[0056]
与现有技术相比较,本发明的优点在于:
[0057]
(1)在不改变预聚物或活性稀释剂组分前提下,通过对有色填料组分特殊改性达到提高紫外光固化涂层交联密度目的;
[0058]
(2)对掺杂剂结构功能化设计,在满足聚苯胺与树脂基体均匀分散的同时引入双键结构和磷酸酯结构,实现对涂层自身交联密度和附着力的提升。
附图说明
[0059]
图1为pa、gma和paga
‑
5(paga
‑
5表示pa与gma反应摩尔比为1∶5)的红外谱图;
[0060]
图2为光敏聚苯胺(paga/pani)的结构示意图;
[0061]
图3为paga/pani的红外谱图;(paga
‑
1表示pa与gma反应摩尔比为1∶1;paga
‑
3表示pa与gma反应摩尔比为1∶3;paga
‑
5表示pa与gma反应摩尔比为1∶5;paga
‑
7表示pa与gma反应摩尔比为1∶7)
[0062]
图4为paga/pani的紫外
‑
可见光吸收谱图;(paga
‑
1表示pa与gma反应摩尔比为1∶1;paga
‑
3表示pa与gma反应摩尔比为1∶3;paga
‑
5表示pa与gma反应摩尔比为1∶5;paga
‑
7表示pa与gma反应摩尔比为1∶7)
[0063]
图5为紫外光固化涂层凝胶含量测试结果(pea为未添加填料的纯树脂涂层,测试基材为低碳钢,pa
‑
pani为以pa掺杂pani的涂层作为对照组);(paga
‑
1表示pa与gma反应摩尔比为1∶1;paga
‑
3表示pa与gma反应摩尔比为1∶3;paga
‑
5表示pa与gma反应摩尔比为1∶5;paga
‑
7表示pa与gma反应摩尔比为1∶7;paga
‑
9表示pa与gma反应摩尔比为1∶9)
[0064]
图6为紫外光固化涂层拉拔附着力测试结果;(paga
‑
1表示pa与gma反应摩尔比为1∶1;paga
‑
3表示pa与gma反应摩尔比为1∶3;paga
‑
5表示pa与gma反应摩尔比为1∶5;paga
‑
7表示pa与gma反应摩尔比为1∶7;paga
‑
9表示pa与gma反应摩尔比为1∶9)
[0065]
图7为紫外光固化涂层耐中性盐雾测试。
具体实施方式
[0066]
为进一步提高对本发明涉及的制备工艺、技术特点等了解,下面结合实施例对本
发明作进一步阐述。实施例所涉及制备工艺及参数仅用于说明本发明,本发明具体权利要求书所描述并不局限于此。
[0067]
实施例1
[0068]
(1)光敏植酸(paga
‑
3)的制备:0.025mol植酸与40ml去离子水混合,再加入0.075mol的gma,加入植酸与甲基丙烯酸缩水甘油酯的0.1wt%的对苯二酚作为阻聚剂,植酸与甲基丙烯酸缩水甘油酯的0.5wt%的四丁基溴化铵,超声辅助分散后。控制机械搅拌速度为150rpm,反应物溶液在80℃油浴锅中反应0.5h得到棕黄色产物,即为光敏植酸——paga
‑
3。
[0069]
(2)光敏聚苯胺的制备:光敏植酸paga
‑
3分散于去离子水中配置浓度为0.2g/ml的共聚物溶液,在溶液中按光敏植酸与聚苯胺(聚苯胺粒径为10μm)质量比为10∶1加入聚苯胺,搅拌下控制反应时间为6.0h,过滤洗涤以得到光敏聚苯胺。
[0070]
图2为光敏聚苯胺结构示意图。
[0071]
(3)光敏聚苯胺基紫外光固化涂料的制备:将一定质量的环氧丙烯酸树脂(预聚物,30份)、聚酯丙烯酸树脂(预聚物,40份),四氢化糠基丙烯酸酯(活性稀释剂,30份)、2
‑
甲基
‑2‑
丙烯酸
‑2‑
羟乙基酯磷酸酯(附着力促进剂,0.5份)、2
‑
羟基
‑2‑
甲基
‑1‑
苯基
‑1‑
丙酮(光引发剂1173,1.0份),再加入0.5份光敏聚苯胺填料,球磨2000rpm,分散4min后再以100目的筛网对其过滤以制备紫外光固化涂料。
[0072]
实施例2
[0073]
(1)光敏植酸(paga
‑
5)的制备:0.025mol植酸与40ml去离子水混合,再加入0.125mol的gma,加入植酸与甲基丙烯酸缩水甘油酯的0.1wt%的对叔丁基邻苯二酚作为阻聚剂,植酸与甲基丙烯酸缩水甘油酯的1.0wt%的四丁基溴化铵,超声辅助分散后。控制机械搅拌速度为150rpm,反应物溶液在90℃油浴锅中反应1.0h得到棕黄色产物,即为光敏植酸——paga
‑
5。
[0074]
图1为pa、gma和paga
‑
5的红外谱图,pa的红外谱图上存在归属于p=o的特征吸收峰(1164cm
‑1)。对于gma而言,红外谱图上除了可以观察到归属于环氧基团的特征吸收峰(910cm
‑1)外,还可以看到不饱和碳碳双键特征吸收峰(1635cm
‑1和810cm
‑1)以及归属于羰基的特征吸收峰(1720cm
‑1)。相比于pa和gma,聚合反应产物的红外谱图中归属于环氧基团的特征吸收峰消失,同时还可以观察到双键基团和p=o特征吸收峰(1166cm
‑1和1048cm
‑1)的出现,表明了pa与gma发生反应,成功制备了光敏植酸——paga
‑
5。
[0075]
(2)光敏聚苯胺的制备:光敏植酸paga
‑
5分散于去离子水中配置浓度为0.8g/ml的共聚物溶液,在溶液中按光敏植酸与聚苯胺质量比为25∶1加入聚苯胺,搅拌下控制反应时间为6.0h,过滤洗涤以得到光敏聚苯胺。
[0076]
(3)光敏聚苯胺基紫外光固化涂料的制备:将一定质量的环氧丙烯酸树脂(预聚物,30份)、聚酯丙烯酸树脂(预聚物,50份),四氢化糠基丙烯酸酯(活性稀释剂,20份)、磷酸氢二(甲基丙烯酰氧乙基)酯(附着力促进剂,0.5份)、2
‑
羟基
‑2‑
甲基
‑1‑
苯基
‑1‑
丙酮(光引发剂1173,1.5份),再加入1.0份光敏聚苯胺填料,球磨2000rpm,分散4min后再以150目的筛网对其过滤以制备紫外光固化涂料。
[0077]
实施例3
[0078]
(1)光敏植酸(paga
‑
7)的制备:将0.025mol植酸与40ml去离子水混合,再加入
0.175mol的gma,加入植酸与甲基丙烯酸缩水甘油酯的0.5wt%的对叔丁基邻苯二酚作为阻聚剂,植酸与甲基丙烯酸缩水甘油酯的1.0wt%的三苯基膦,超声辅助分散后。控制机械搅拌速度为150rpm,反应物溶液在85℃油浴锅中反应2.0h得到棕黄色产物,即为光敏植酸——paga
‑
7。
[0079]
(2)光敏聚苯胺的制备:光敏植酸paga
‑
7分散于去离子水中配置浓度为1.0g/ml的共聚物溶液,在溶液中按光敏植酸与聚苯胺质量比为25∶1加入聚苯胺,搅拌下控制反应时间为10h,过滤洗涤以得到光敏聚苯胺。
[0080]
(3)光敏聚苯胺基紫外光固化涂料的制备:将一定质量的环氧丙烯酸树脂(预聚物,30份)、聚酯丙烯酸树脂(预聚物,50份),四氢化糠基甲基丙烯酸酯(活性稀释剂,20份)、2
‑
甲基
‑2‑
丙烯酸
‑2‑
羟乙基酯磷酸酯(附着力促进剂,1.0份)、1
‑
羟基环已基苯基甲酮(光引发剂,1.5份),再加入1.5份光敏聚苯胺填料,球磨2000rpm,分散6min后再以200目的筛网对其过滤以制备紫外光固化涂料。
[0081]
实施例4
[0082]
(1)光敏植酸(paga
‑
9)的制备:将0.025mol植酸与40ml去离子水混合,再加入0.2255mol的gma,加入植酸与甲基丙烯酸缩水甘油酯的0.5wt%的对苯二酚作为阻聚剂,植酸与甲基丙烯酸缩水甘油酯的0.5wt%的三苯基膦,超声辅助分散后。控制机械搅拌速度为200rpm,反应物溶液在90℃油浴锅中反应2.5h得到棕黄色产物,即为光敏植酸——paga
‑
9。
[0083]
(2)光敏聚苯胺的制备:光敏植酸paga
‑
9分散于去离子水中配置浓度为1.5g/ml的共聚物溶液,在溶液中按光敏植酸与未掺杂聚苯胺质量比为50∶1加入未掺杂聚苯胺,搅拌下控制反应时间为25h,过滤洗涤以得到光敏聚苯胺。
[0084]
(3)光敏聚苯胺基紫外光固化涂料的制备:将一定质量的环氧丙烯酸树脂(预聚物,30份)、聚氨酯丙烯酸树脂(预聚物,50份),四氢化糠基甲基丙烯酸酯(活性稀释剂,20份)、乙烯基三甲氧基硅烷(附着力促进剂,1.0份)、1
‑
羟基环已基苯基甲酮(光引发剂,3.0份),再加入2.0份光敏聚苯胺填料,球磨2500rpm,分散10min后再以300目的筛网对其过滤以制备紫外光固化涂料。
[0085]
实施例5
[0086]
光敏聚苯胺结果表征:
[0087]
光敏聚苯胺的制备是按照实施例1
‑
3中步骤(1)、(2)制备,分别制备了不同的光敏植酸用于聚苯胺的掺杂,以得到不同的光敏聚苯胺(paga
‑
3/pani、paga
‑
5/pani、paga
‑
7/pani)。
[0088]
另外,paga
‑
1/pani的制备方法为:
[0089]
光敏植酸(paga
‑
1)的制备:将0.025mol植酸与40ml去离子水共混合,再加入0.025mol的gma,加入植酸与甲基丙烯酸缩水甘油酯的0.5wt%的对苯二酚作为阻聚剂,植酸与甲基丙烯酸缩水甘油酯1.0wt%的三苯基膦,超声辅助分散后。控制机械搅拌速度为180rpm,反应物溶液在85℃油浴锅中反应1.5h得到棕黄色产物,即为光敏植酸——paga
‑
1。
[0090]
光敏聚苯胺的制备:光敏植酸paga
‑
1分散于去离子水中配置浓度为1.0g/ml的共聚物溶液,在溶液中按光敏植酸与聚苯胺质量比为25∶1加入聚苯胺,搅拌下控制反应时间为20h,过滤洗涤以得到光敏聚苯胺。
[0091]
(1)全反射傅里叶红外测试
[0092]
测试前对光敏聚苯胺进行干燥研磨处理,全反射波长扫描范围为4000
‑
550cm
‑1,图谱分辨率为4cm
‑1,扫描次数为16。
[0093]
由图3可知,未掺杂聚苯胺的红外谱图中1579cm
‑1和1492cm
‑1处的吸收峰分别对应c=n和c=c伸缩振动吸收峰,1300cm
‑1处的吸收峰则与仲芳族胺的c
‑
n拉伸相关,此外1153cm
‑1处的吸收峰与c
‑
h平面弯曲振动相关。通过paga对聚苯胺进行掺杂后,可以发现上述吸收峰位置均向低波数方向移动,同时对应光敏聚苯胺的红外谱图在1245cm
‑1处出现归属于p=o伸缩振动的吸收峰,在1630cm
‑1处出现c=c的特征吸收峰,成功证实paga对聚苯胺的成功掺杂,在聚苯胺高分子链段上成功引入了磷酸酯基团和可参与光聚合进程的c=c结构。
[0094]
(2)紫外
‑
可见光光谱
[0095]
以水为溶剂,称量一定质量的光敏聚苯胺超声分散形成聚苯胺水溶液,聚苯胺水溶液浓度不超过0.001g/ml,紫外
‑
可见光检测扫描波长设置范围为250
‑
900nm。
[0096]
因聚苯胺未掺杂时不溶于水,故未提供未掺杂时聚苯胺的紫外
‑
可见光光谱。由图4可知,通过paga对聚苯胺进行掺杂处理后,光敏聚苯胺的紫外
‑
可见光光谱中除了观察到隶属于π
‑
π*跃迁(301nm)的紫外吸收峰外,还可以观察到因掺杂剂掺杂引起的π
‑
极子带跃迁吸收峰(826nm),这进一步验证了光敏聚苯胺的成功制备。
[0097]
实施例6
[0098]
光敏植酸掺杂聚苯胺基紫外光固化涂层结果表征:
[0099]
光敏植酸掺杂聚苯胺基紫外光固化涂料(涂料组分见表1)的测试是在低碳钢上进行的,测试前需通过丙酮对基材表面的有机物及油脂进行清洗。选用框式刮膜器涂覆在低碳钢上,流平后以履带式光固化机完成涂料的固化交联,履带速率为5.7m/min,制备得到的光敏聚苯胺基紫外光固化涂料干膜厚度为50
±
5μm。
[0100]
表1光固化涂料各组分组成及比例
[0101]
原料名称组分成分占比/份环氧丙烯酸酯(ry1101)预聚物30聚酯丙烯酸酯(dr
‑
e524)预聚物50四氢化糠基丙烯酸酯(thfa)活性稀释剂202
‑
羟基
‑2‑
甲基
‑1‑
苯基
‑1‑
丙酮(1173)光引发剂3.0甲基丙烯酰氧乙基磷酸酯(pm
‑
1)附着力促进剂2.0光敏聚苯胺防腐填料0.5
[0102]
(1)凝胶含量测试
[0103]
固化交联后紫外光固化薄膜剪碎,以定量滤纸包裹,记录样品质量和滤纸质量。每组样品平行样不低于3份,样品质量不低于0.5g,置于索氏提取器中。凝胶含量测试选用丙酮作为洗脱剂,反应温度80℃,测试时长24h,以除去涂层中未凝胶组分。抽提后样品经60℃干燥24h,再次记录样品质量,具体计算如下所示:
[0104][0105]
w
测试前(后)
表示丙酮抽提前后紫外光固化薄膜质量。
[0106]
由图5可知,经丙酮24h抽提测试后,纯树脂涂层和pa
‑
pani涂层凝胶含量均保持在
70%左右,证实了如果单一以植酸掺杂聚苯胺,由于掺杂剂中不存在双键基团,不参与预聚物交联过程,因此对涂层本身交联密度影响不大。对比以paga/pani作为填料的光固化涂层,可以发现体系涂层交联密度均有不同程度的提升,这是由于paga/pani中引入带有双键结构的gma,在紫外光固化过程,参与聚合过程,导致交联密度有所改善。
[0107]
(2)拉拔附着力测试
[0108]
拉拔附着力测试参照国标gb
‑
t/5210
‑
85进行,拉拔速度设置为0.40mpa/s,拉拔数据测定为光固化涂层与基材间相互作用力值。
[0109]
由图6可知,通过拉拔测定纯树脂涂层与基材的界面作用力在2.5mpa左右,对应pa
‑
pani涂层,可以发现涂层的附着力得到了显著提升,这说明pa本身附带的磷酸根基团会与基团锚定吸附,增强两者间界面作用力。比较paga掺杂的pani涂层发现与纯树脂涂层相比,涂层附着力均有不同程度的提升,这得益于磷酸根基团的引入。但是发现paga中越多的磷酸根基团与gma反应后,掺杂得到的pani涂层附着力呈下降趋势,这可能由于越多gma接枝后,掺杂聚苯胺间空间位阻增大,造成磷酸根与基材作用困难。当接枝量达到一定程度时,填料引入反而造成界面作用力下降。
[0110]
(3)耐中性盐雾测试
[0111]
中性盐雾测试参照美标astm b117进行,以bgd 1285腐蚀试验用划痕器对光敏植酸掺杂聚苯胺基紫外光固化涂层进行划痕处理后,将其置于q
‑
fog ssp型循环盐雾试验箱进行测试,待测盐溶液浓度为5.0wt%。每隔一段时间对涂层样品进行拍照记录,根据涂层划痕处锈蚀及表面起泡程度或腐蚀覆盖面积评估涂层是否失效。
[0112]
由图7显示的划痕涂层耐中性盐雾测试结果可知,5.0wt%氯化钠溶液中暴露300h后,纯树脂涂层已发生大面积腐蚀,腐蚀介质透过划痕侵蚀基材,且随着测试时间延长,腐蚀面积扩大。对比paga/pani涂层,暴露300h后,涂层出现不同程度的腐蚀痕迹,paga
‑
1/pani涂层仅出现小面积的腐蚀痕迹,paga
‑
3/pani和paga
‑
7/pani涂层则出现局部腐蚀现象,但基材腐蚀程度明显低于纯树脂涂层。相反paga
‑
5/pani涂层在盐雾环境下测试300h后,仅在划痕处表现出金属腐蚀现象,涂层表面无桔皮、褶皱现象,涂层的耐腐蚀性能得到显著提升。
再多了解一些
本文用于企业家、创业者技术爱好者查询,结果仅供参考。