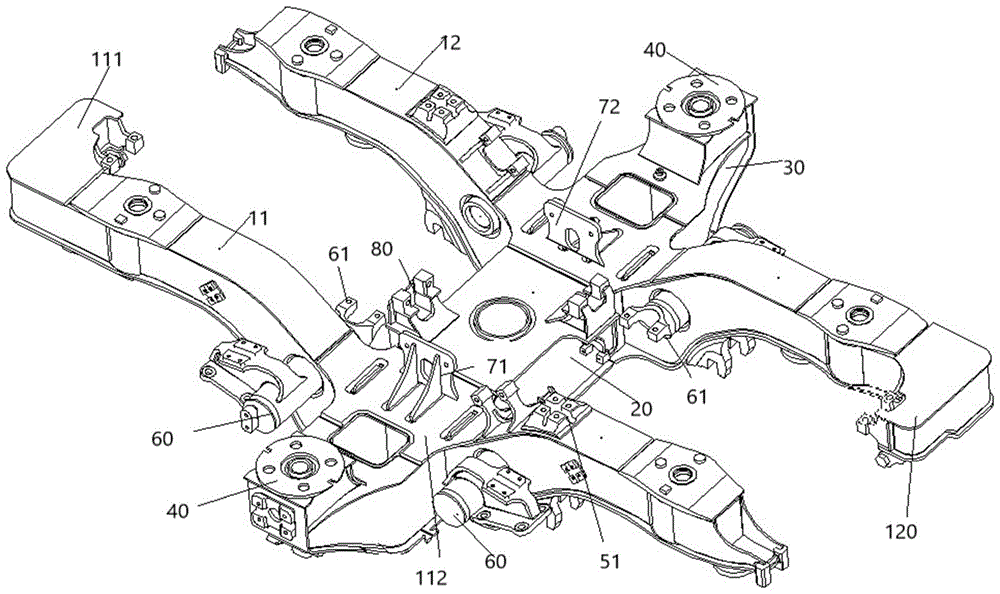
本实用新型涉及轨道车辆技术领域,具体涉及一种转向架的构架。
背景技术:
随着高速铁路的发展,车型种类日趋增加,运营维护管理困难,检修维护成本较高,同时随着速度的提高,动车组的牵引功率急剧提升,牵引电机的重量大大增加,对转向架构架强度及转向架动力学性能产生较大影响。
转向架包括构架、一系悬挂装置和定位装置,构架与轮对通过一系悬挂装置和定位装置连接。目前构架包括两纵梁以及焊接于两纵梁之间的两根圆钢管,圆钢管的端面焊接于纵梁的侧面,焊接截面变化比较大,应力集中比较大,大大影响了构架的使用安全性。
因此,如何提高构架的使用安全性,是本领域内技术人员一直追求的目标。
技术实现要素:
本实用新型提供了一种转向架的构架,包括以下部件:
一个横梁主体,所述横梁主体为箱型结构;
两个箱型纵梁主体,两个所述纵梁主体分别焊接于所述横梁主体的两端部,所述横梁主体、所述两个纵梁主体三者形成h型;
所述纵梁主体包括中间连接段,所述中间连接段包括上盖板、下盖板、内侧板和外侧板,所述上盖板部分侧缘向内延伸形成所述横梁主体的箱体部分上壁,所述下盖板部分侧缘向内延伸形成所述横梁主体的箱体部分下壁;
并且,用于安装轴箱的安装座设置于所述纵梁主体的内侧。
与现有技术中横梁主体为圆管相比,本实用新型中的横梁主体的连接部分与纵梁主体使用同一上盖板、下盖板形成,二者连接位置逐渐过渡,避免了二者连接截面突变,大大降低了两者连接位置的强度,提高构架使用安全性。
并且,本实用新型中用于安装轴箱的安装座设置于纵梁主体的内侧,这样可以尽量缩小量纵梁主体之间的距离。试验证实,将轴箱的安装座置于纵梁主体内侧,两纵梁主体之间的中心距离可以降低至1200mm以内,在一种具体实施例中两纵梁主体之间的中心距离可以为1140mm,大大提高了构架的使用灵活性。
可选的,所述横梁主体包括上板体、下板体以及两个立板,四者围成箱体结构,并且所述两个立板的两端均延伸至所述上板体和所述下板体相应端部的外侧;两个所述立板与相应侧的所述中间连接段的内侧板焊接;所述上盖板部分侧缘向内延伸形成第一内延伸段,所述下盖板部分侧缘向内延伸形成第二内延伸段,所述第一内延伸段、所述第二内延伸段分别与所述横梁主体的上板体、下板体对接焊接;两个所述立板与相应侧的所述中间连接段的内侧板焊接。
可选的,两所述上盖板分别固定有第一横向止挡块和第二横向止挡块,所述第一横向止挡块和所述第二横向止挡块分别限定车体横向运动的两个极限位置。
可选的,还包括横向贯穿所述纵梁主体的支撑管,所述支撑管的内端部穿出所述纵梁主体形成第一齿轮箱吊座,所述支撑管向外延伸至所述纵梁主体的外部形成有制动吊座和和高度阀安装座。
可选的,所述纵梁主体其中一端部向内折弯形成折弯箱体段,所述折弯箱体段具有朝向所述第一齿轮箱吊座的开口,所述开口位置设置有第二齿轮箱吊座,所述第一齿轮箱吊座与其同侧的所述第二齿轮箱吊座共同形成齿轮箱的吊座。
可选的,还包括形成腔体的附加箱体,所述附加箱体的数量为两个,对称布置于纵向中心面的两侧,且两个所述附加箱体分别位于所述纵梁主体的外侧,所述附加箱体的腔体与相应侧所述纵梁主体内部形成的气室连通;所述附加箱体的顶壁外部设置有空气弹簧安装座,所述附加箱体设置有通过腔体连通的进口和出口。
可选的,所述上盖板和所述下盖板分别包括横向延伸至所述外侧板之外的第一外延伸段和第二外延伸段,所述附加箱体的顶壁、底壁分别与所述第一外延伸段、所述第二外延伸段对接焊接,其余两侧壁内端均焊接于所述外侧板。
可选的,所述构架还包括牵引拉杆座,所述牵引拉杆座用于安装一系悬挂的纵向拉杆的一端,所述横梁主体的上板体具有纵向延伸且伸出相应立板外壁的第一延伸部,所述牵引拉杆座至少部分安装于所述第一延伸部的上表面。
可选的,所述构架还包括电机横向减振器座,具有用于限制电机横向振动位移的结构;所述电机横向减振器座安装于所述第一延伸部的下表面。
可选的,所述下板体具有纵向延伸至相应侧立板外壁的第二延伸部,所述第二延伸部的上表面设置有电机横向止挡座,所述电机横向止挡座还与相应所述立板外侧壁焊接固定,所述电机横向止挡座上还设置有吊装孔。
可选的,所述电机横向止挡座包括两个组件,每一个所述组件包括围成空腔结构的第一板和第二板,所述第一板的下表面与所述第二延伸部焊接,后端与所述立板焊接,所述第一板和第二板上端焊接固定,所述第一板设置有吊装孔,所述第二板配合电机限位。
可选的,所述横梁主体上板体和下板体设置有同轴通孔,所述通孔内部安装有钢管,所述箱体结构内部设置有加强筋。
可选的,两所述纵梁主体的纵向中心面距离在1200mm以内。
可选的,每一所述纵梁主体设置有弹簧套筒,用于安装一系橡胶;所述弹簧套筒的下端开口且包括露置于所述纵梁主体底壁外部的管段,所述弹簧套筒的上端焊接于所述纵梁主体的顶壁内表面;所述弹簧套筒的数量为两个,关于所述纵梁主体横向中心面对称。
附图说明
图1是本实用新型一种具体实施例中构架的结构示意图;
图2为图1所示构架的俯视图;
图3为图1所示构架的局部示意图;
图4为本实用新型一种具体实施例中纵梁组件的局部结构示意图;
图5为本实用新型一种具体实施例中横梁组件的局部结构示意图;
图6为图5所示横梁组件的另一方向示意图;
图7为横梁组件的局部放大图。
其中,图1-7中附图标记与部件之间的一一对应关系如下所示:
11-第一纵梁主体;111-折弯箱体段;112-第一上盖板;12-第二纵梁主体;120-折弯箱体段;121-第二上盖板;1211-第一内延伸段;122-下盖板;1221-第二内延伸段;20-横梁主体;21-上板体;211-第一延伸部;22-下板体;221-第二延伸部;23-立板;24-加强筋;231-延伸段;30-附加箱体;40-空气弹簧安装座;50-第二齿轮箱安装座;53-电机吊座;60-支撑柱;61-第一齿轮箱安装座;62-制动吊座;63-高度阀安装座;71-第一横向止挡块;72-第二横向止挡块;80-牵引拉杆座;81-电机横向减振座;82-电机横向止挡座;821-第一板;822-第二板;821a-吊装孔;90-弹簧套筒。
具体实施方式
为了使本领域的技术人员更好地理解本实用新型的技术方案,下面结合附图和具体实施例对本实用新型作进一步的详细说明。
请参考图1、图2和图3,图1是本实用新型一种具体实施例中构架的结构示意图;图2为图1所示构架的俯视图;图3为图1所示构架的局部示意图。
本实用新型提供的转向架的构架,该构架包括一个横梁组件、两个纵梁组件,其中横梁组件包括横梁主体20,横梁主体20为箱型结构;也就是说,横梁主体20内部为中空结构。两个纵梁组件,每一纵梁组件包括箱型纵梁主体,两个纵梁主体分别焊接于横梁主体的两端部,横梁主体20、两个纵梁主体三者形成h型。横梁主体20大致位于纵梁主体的中间位置。
为了描述技术方案的简洁,本文将两纵梁主体分别定义为第一纵梁主体11和第二纵梁主体12,横梁主体位于第一纵梁主体11和第二纵梁主体12之间。第一纵梁主体11的上盖板定义为第一上盖板112,第二纵梁主体12的上盖板定义为第二上盖板121。第一上盖板112和第二上盖板121的形状相同。两纵梁主体的下盖板结构请参考上盖板结构,图中未示出,但是并未妨碍本文技术方案的理解。
其中,纵梁主体包括中间连接段,中间连接段包括上盖板、下盖板、内侧板和外侧板,上盖板部分侧缘向内延伸形成横梁主体20的箱体部分上壁,下盖板部分侧缘向内延伸形成横梁主体的箱体部分下壁。
通过上述描述可知,与横梁主体为圆管相比,本实用新型中的横梁主体20的连接部分与纵梁主体使用同一上盖板、下盖板形成,二者连接位置逐渐过渡,避免了二者连接截面突变,大大降低了两者连接位置的强度,提高构架使用安全性。
并且,本实用新型中用于安装轴箱的安装座设置于纵梁主体的内侧,这样可以尽量缩小量纵梁主体之间的距离。试验证实,将轴箱的安装座置于纵梁主体内侧,两纵梁主体之间的中心距离可以降低至1200mm以内,在一种具体实施例中两纵梁主体之间的中心距离可以为1120mm-1150mm,大大提高了构架的使用灵活性。
本文中的上述中心距离是指第一纵梁主体11与第二纵梁主体12的纵向中心面之间的距离。
在一种具体实施例中,横梁主体20包括上板体21、下板体22以及两个立板23,四者围成箱体结构,并且两个立板的两端均延伸至上板体21和下板体22相应端部的外侧;也就是说,形成横梁主体20的上板体21、下板体22和两立板23的长度不同,两立板23的长度大于上板体21、下板体22的长度,立板23伸出上板体21和下板体22外端部。如图5所示立板的两端均具有延伸段231,延伸段231伸出上板体21和下板体22相应外端部。
纵梁主体的上盖板部分侧缘向内延伸形成第一内延伸段,下盖板部分侧缘向内延伸形成第二内延伸段,第一内延伸段、第二内延伸段分别与横梁主体的20上板体、下板体对接焊接;两个立板与相应侧的中间连接段的内侧板焊接。例如图4中给出了第二纵梁主体12的第二上盖板121和下盖板122,其中第二上盖板121的第一内延伸段1211和下盖板的第二内延伸段1221可参见图。
该实施方式中,纵梁主体的上盖板的第一内延伸段伸至两立板之间,端部与横梁主体的上板体对焊,并且第一内延伸段的两侧也与两立板相应位置焊接,同理,纵梁主体的下盖板的第二内延伸段也位于两立板之间,第二内延伸段与横梁主体20的下板体对焊,第二内延伸段的两侧与两立板相应位置焊接。这样横梁主体20与纵梁主体连接位置也形成箱体结构,并且连接位置变化连续,进一步增加构架的使用强度。在上述实施例的基础上,两上盖板上分别固定有第一横向止挡块71和第二横向止挡块72,第一横向止挡块71和第二横向止挡块72分别限定车体横向运动的两极限位置。
第一横向止挡块71和第二横向止挡块72可以相对设置,形状不限只要能够限定车体的横向运动即可。
在有一种具体实施方式中,构架还进一步包括横向贯穿纵梁主体的支撑管60,支撑管60的内端部穿出纵梁主体形成第一齿轮箱吊座61,支撑管60向外延伸至纵梁主体的外部形成有制动吊座62和和高度阀安装座63。高度阀安装座63是为了安装高度阀。制动吊座62和高度阀安装座63的结构不限定。
本实施方式中,第一齿轮箱吊座61、制动吊座62和高度阀安装座63为一体结构,优化构架结构,提高装配灵活性。
上述各实施例中,纵梁主体其中一端部向内折弯形成折弯箱体段,折弯箱体段具有朝向第一齿轮箱吊座的开口,开口位置设置有第二齿轮箱吊座,第一齿轮箱吊座与其同侧的第二齿轮箱吊座共同形成齿轮箱的吊座。两纵梁主体的折弯箱体段分居两端,也就是说,两纵梁主体的折弯箱体段不位于同一端部。
如图1和图2所示,第一纵梁主体的折弯箱体段111位于左端,第二纵梁主体12的折弯箱体段120位于右端。左端和右端是以图1和图2中各部件之间的相对位置关系来描述的。第一纵梁主体的折弯箱体段111内部设置有第二齿轮箱吊座50,与第一纵梁主体11左侧的第一齿轮箱吊座61,共同形成齿轮箱的吊座。
同理,第二纵梁主体的折弯箱体段120内部设置有第二齿轮箱吊座50,与第二纵梁主体12右侧的第一齿轮箱吊座61共同形成该位置处齿轮箱的吊座。
本实施方式中一方面折弯箱体段可以加强纵梁主体的支撑强度,另一方面第二齿轮箱吊座位于纵梁主体的折弯箱体段内部,结构紧凑,减少空间占据。
在一种具体实施例中,上述各实施例中的构架还可以包括形成腔体的附加箱体30,附加箱体30的数量为两个,对称布置于纵向中心面的两侧,且两个附加箱体30分别位于纵梁主体的外侧,附加箱体30的腔体与相应侧纵梁主体内部形成的气室连通;附加箱体30的顶壁外部设置有空气弹簧安装座40,附加箱体30设置有通过腔体连通的进口和出口。附加箱体30的进口与气源直接或者间接连通,出口与空气弹簧连通。通常中间连接段的内部空腔也可以设置为气箱,中间连接段内部的气腔与附加箱体30的腔体连通,共同形成空气弹簧工作所需气源的存储空间。
在一种具体实施方式中,上盖板和下盖板分别包括横向延伸至外侧板之外的第一外延伸段和第二外延伸段,附加箱体30的顶壁、底壁分别与第一外延伸段、第二外延伸段对接焊接,其余两侧壁内端均焊接于外侧板。
也就是说,上盖板、下盖板分别形成附加箱体30部分顶壁、部分底壁,这样可以使附加箱体30和纵梁主体形成一体,使二者形成结构更加紧凑。
上述各实施例中,横梁主体的两立壁均设置有电机吊座51和电机吊座止挡挡。电机吊座止挡安装后,电机吊座止挡的中心与电机高度一致,避免增加力矩。
具体地,每一纵梁主体还可以设置有弹簧套筒90,用于安装一系橡胶;弹簧套筒90的下端开口且包括露置于纵梁主体底壁外部的管段,弹簧套筒90的上端焊接于纵梁主体的顶壁内表面;弹簧套筒90的数量为两个,关于纵梁主体横向中心面对称。
纵梁主体的顶壁与弹簧套筒90相对位置还设置有通孔,方便弹簧套筒的固定。请参考图2,第一纵梁主体11上设置有通孔11a,第二纵梁主体12上设置有通孔12a。
上述各实施例中,构架还包括牵引拉杆座80,牵引拉杆座80用于安装一系悬挂的纵向拉杆的一端,横梁主体20的上板体21具有纵向延伸且伸出相应立板23外壁的第一延伸部211,牵引拉杆座80至少部分安装于第一延伸部211的上表面。在实现一系悬挂的纵向拉杆安装的前提下,可实现结构尽量紧凑。通常沿纵向具有两个牵引拉杆座80,分居于横梁主体20的端部,当然,具体位置可以根据实际车型而定。牵引拉杆座80的具体结构本文也不做具体限定。
在一种具体的实施方式中,构架还包括电机横向减振器座81,具有用于限制电机横向振动位移的结构;电机横向减振器座81安装于第一延伸部211的下表面。该实施例中结构进一步紧凑,不占用其他空间位置,有利于构架整体的优化。
进一步地,上述各实施例中下板体22具有纵向延伸至相应侧立板23外壁的第二延伸部221,第二延伸部221的上表面设置有电机横向止挡座82,电机横向止挡座还与相应立板外侧壁焊接固定,电机横向止挡座82上还设置有吊装孔。
也就是说,本实用新型中的电机横向止挡座在实现对电机横向限位的同时,又具有吊装配合的功能,即吊装设备通过连接吊装孔可以实现构架的吊装。
具体地,电机横向止挡座82包括两个组件,两个组件间隔预定距离布置,每一个组件包括围成空腔结构的第一板821和第二板822,第一板的下表面与第二延伸部221焊接,后端与立板23焊接,第一板821和第二板822上端焊接固定,第一板821设置有吊装孔821a,第二板822配合电机限位。
该实施方式中第一板821和第二板822围成空腔结构,在实现吊装和止挡功能的前提下,可以尽量降低整体重量。
横梁主体20的上板体21和下板体22设置有同轴通孔,通孔内部安装有钢管25,箱体结构内部设置有加强筋24。中央牵引装置位于横梁主体20上方和下方的构件可以通过横梁主体20上设置的通孔实现连接,大大提高了中央牵引装置的布置灵活性。并且箱体结构内部的加强筋24起到了增加横梁主体20使用强度的目的。
在上述构架的基础上,本实用新型还提供了一种转向架,其包括上述任一项的转向架的构架。
因本实用新型的转向架包括上述构架,故该转向架也具备构架的上述技术效果。
以上仅是本实用新型的优选实施方式,应当指出,对于本技术领域的普通技术人员来说,在不脱离本实用新型原理的前提下,还可以做出若干改进和润饰,这些改进和润饰也应视为本实用新型的保护范围。
本文用于企业家、创业者技术爱好者查询,结果仅供参考。