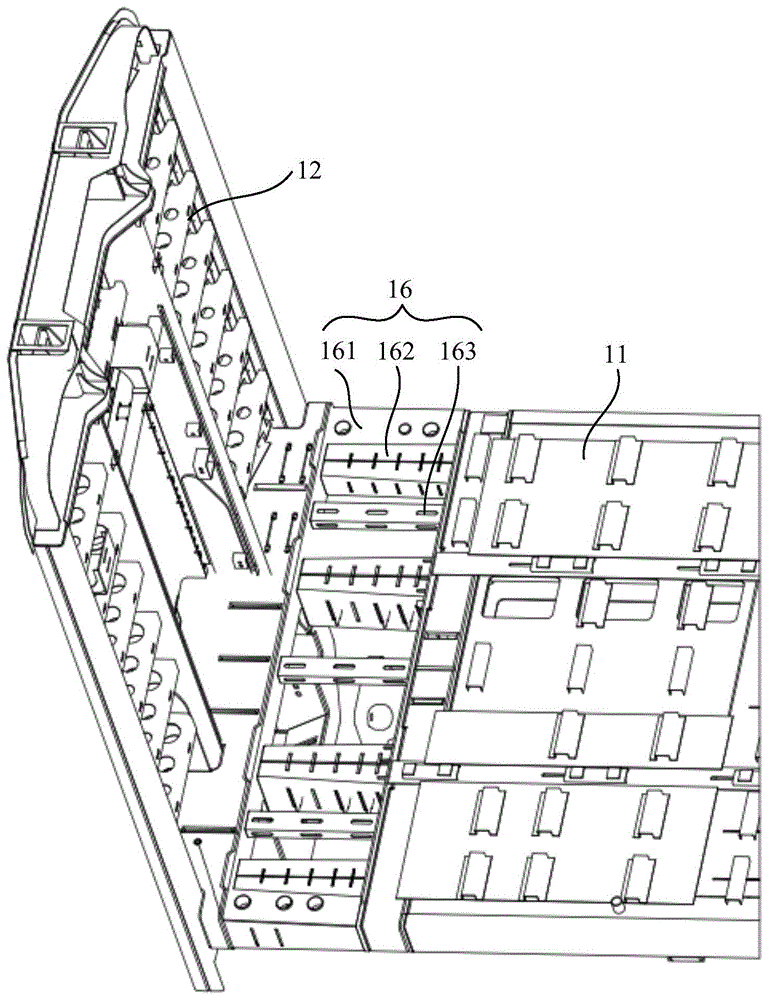
本申请涉及轨道车辆技术领域,具体地,涉及一种控制车及其车体。
背景技术:
现有双层不锈钢车主要应用于欧美国家,不锈钢车体对于车体防腐和轻量化是一个有效途径。不锈钢的车体部分是由底架、侧墙、端墙、车顶、二层地板和司机室构成的薄壁筒型整体承载结构。
现有车体的门口主要分布在端底架上,一面侧墙在两端均开有门口,在车体两个端部的门口设置有方便乘客上下车的楼梯。车体底架和侧墙采用牵枕缓结构连接,由底架伸出部分焊接,使两个大部件直接接触。车体边梁是贯穿式的,一根边梁从车体一位端到二位端,用于力的传递,边梁成为车体的侧墙和底架的分界线,边梁的上侧为一个整块的侧墙,边梁的下侧为底架。
现有技术中,车体的底架的中部鱼腹区域无法布置车门,使得乘客在进入车体后只能从一个较高的平台进入一个较低的平台,使乘客的驾乘感受较差。同时,车体底架采用牵枕缓结构的刚性连接,当车体发生碰撞时,无法实现缓冲吸能作用,碰撞力会直接传导到车体内,对乘客的身体造成伤害。
技术实现要素:
本申请实施例中提供了一种控制车及其车体,该车体在两端均设置有吸能结构,并将门口设置在中部底架上,能够在车体发生碰撞时实现缓冲吸能功能,保护乘客的身体免受伤害,还能提高乘客的乘坐舒适性。
根据本申请实施例的第一个方面,提供了一种控制车的车体,包括底架、端墙、侧墙、车顶以及司机室;所述底架包括中部底架和固定连接于所述中部底架两端的端底架;
所述司机室包括司机室骨架、前端吸能结构、前端车钩托梁以及防爬结构;所述防爬结构通过所述前端吸能结构安装于所述司机室骨架背离所述底架的一侧;所述前端车钩托梁安装于所述防爬结构的底部;
在所述底架与所述端墙之间连接有后端吸能结构;
所述前端吸能结构和所述后端吸能结构均通过在碰撞过程中的压缩变形吸收碰撞能量;
在与所述中部底架的两端部对应的所述侧墙上开设有门口,并设置有用于增强所述门口周围的所述中部底架和所述侧墙的结构强度的加强结构。
优选地,所述端墙的底部安装有后端车钩托梁,并在靠近所述端墙一侧的端底架的底部安装有与后端车钩托梁对应的后端车钩安装座;
在靠近所述司机室一端的端底架的底部安装有与所述前端车钩托梁对应的前端车钩安装座;
所述前端车钩托梁、所述前端车钩安装座、所述后端车钩托梁以及所述后端车钩安装座均用于安装回退式车钩。
优选地,所述加强结构包括焊接连接于所述侧墙的矩形加强筋、焊接连接于所述侧墙和所述底架的多个u形加强筋以及焊接于所述u形加强筋的开口侧的盖板。
优选地,所述后端吸能结构包括两个连接梁、多个后端吸能盒以及多个连接板;
所述连接梁焊接连接在所述端墙和所述底架的边梁之间;
所述后端吸能盒焊接连接在所述端墙和所述底架的端梁之间;
所述连接板焊接连接在所述端墙和所述端梁之间。
优选地,沿所述车体的宽度方向,所述后端吸能盒和所述连接板依次交替间隔设置;
所述连接梁和所述连接板均采用不锈钢板制成;
所述连接板上设置有多个开孔。
优选地,所述前端吸能结构包括多个前端吸能盒和至少一个吸能管,所述前端吸能盒和所述吸能管均固定连接于所述司机室骨架与所述前端车钩托梁之间。
优选地,所述前端吸能盒和所述后端吸能盒均包括筒形外壳以及平行设置于所述筒形外壳内的多个隔板;
所述筒形外壳设置有用于诱导溃缩变形的多个诱导孔。
优选地,所述筒形外壳包括沿所述车体的长度方向延伸的上筒壁、下同壁、左筒壁和右筒壁;
所述上筒壁和所述下同壁平行设置;
所述左筒壁和所述右筒壁之间形成开口朝向所述底架的夹角,用于使所述筒形外壳朝向所述底架的前端截面积大于所述筒形外壳朝向所述端墙的后端截面积。
优选地,所述上筒壁与所述左筒壁和所述右筒壁之间、所述下同壁与所述左筒壁和所述右筒壁之间均采用弧焊连接;
所述夹角为2°~4°;
所述筒形外壳和所述隔板均采用a588低合金高强度钢板制成。
优选地,还包括通过二层地板连接件固定安装于所述侧墙的二层地板;
所述二层地板连接件通过不锈钢折弯件焊接在所述侧墙的侧墙托架上,并与所述侧墙的侧墙立柱铆接;
所述车顶与所述侧墙的两端部通过z2角焊缝焊接连接,所述车顶与所述侧墙的中间部分通过点焊连接;
所述侧墙与所述底架之间通过点焊连接;
所述侧墙与所述端墙和所述司机室之间均采用不锈钢方形条角焊缝焊接连接。
优选地,还包括通过螺栓固定安装于所述车顶且靠近所述端墙一侧的外罩板,所述外罩板用于增强所述车体的流线型和防水性;
点焊形成的焊点直径为5.7mm、焊点间距为70mm。
根据本申请实施例的第一个方面,提供了一种控制车,该控制车包括上述技术方案提供的任意一种车体。
采用本申请实施例中提供的控制车及其车体,具有以下有益效果:
上述车体在前端设置有司机室,在后端设置有端墙;在司机室骨架的前端设置有防爬结构、前端吸能结构和前端车钩托梁,在底架与端墙之间设置有后端吸能结构,通过在车体两端设置的前端吸能结构后端吸能结构能够在碰撞过程中吸收碰撞能量,通过设置在车体两端的前端车钩托梁和后端车钩托梁安装回退式车钩,回退式车钩在轨道车辆发生碰撞时可以通过车钩的回退消耗部分碰撞能量,从而防止轨道车辆在碰撞过程中因靠近乘客的部分车体直接压缩变形而使乘客受伤的情况出现;同时,将乘客上下车的门口设置在中部底架上,使乘客从一个较低的位置逐渐进入一个较高的平台,符合进入一个空间时由下至上的基本规律,实现了人性化设计,提高了乘客的乘坐舒适性和驾乘感受。
附图说明
此处所说明的附图用来提供对本申请的进一步理解,构成本申请的一部分,本申请的示意性实施例及其说明用于解释本申请,并不构成对本申请的不当限定。在附图中:
图1为本申请实施例提供的车体的后端的部分结构示意图;
图2为本申请实施例提供的车体的前端的部分结构示意图;
图3为本申请实施例提供的在未安装二层地板和车顶时车体的结构示意图;
图4为本申请实施例提供的在未安装车顶时的车体的结构示意图;
图5为本申请实施例提供的车体的结构示意图;
图6为图5中的车体在门口设置的加强结构的结构示意图。
附图标记:
1-车体;11-底架;12-端墙;13-侧墙;14-车顶;15-司机室;16-后端吸能结构;17-门口;18-后端车钩托梁;19-加强结构;20-二层地板;21-外罩板;
111-前端车钩安装座;131-侧墙加强筋;151-司机室骨架;152-前端吸能结构;153-前端车钩托梁;154-防爬结构;161-连接梁;162-后端吸能盒;163-连接板;191-矩形加强筋;192-u形加强筋;193-盖板;1521-前端吸能盒;1522-吸能管。
具体实施方式
为了使本申请实施例中的技术方案及优点更加清楚明白,以下结合附图对本申请的示例性实施例进行进一步详细的说明,显然,所描述的实施例仅是本申请的一部分实施例,而不是所有实施例的穷举。需要说明的是,在不冲突的情况下,本申请中的实施例及实施例中的特征可以相互组合。
在本申请实施例中,以司机室所处的端部为车体的前端,与司机室相对的设置端墙的端部为车体的尾端或后端。
本申请实施例提供了一种用于轨道车辆的控制车,该控制车包括车体1,车体1的具体结构如下:
如图5结构所示,车体1包括底架11、端墙12、侧墙13、车顶14以及司机室15;司机室15位于车体1的前端,用于轨道车辆的司机乘坐并进行操控;端墙12位于车体1的后端,与司机室15相对设置,并与侧墙13、底架11和车顶14围成乘客乘坐的车厢;侧墙13固定安装于底架11的顶部,并支撑位于车体1顶部的车顶14;底架11包括中部底架11(图中未示出)和固定连接于中部底架11两端的端底架11(图中未示出);底架11由中部底架11和固定连接于中部底架11两端的端底架11共同形成,端底架11的顶部用于固定安装端墙12或司机室15,端底架11的底部还用于安装回退式车钩和转向架(图中未示出);
司机室15包括司机室骨架151、前端吸能结构152、前端车钩托梁153以及防爬结构154;防爬结构154通过前端吸能结构152安装于司机室骨架151背离底架11的一侧;前端车钩托梁153安装于防爬结构154的底部;如图2和图3结构所示,司机室15固定安装于车体1前端的端底架11,司机室15包括用于形成司机驾驶空间轮廓的司机室骨架151;司机室骨架151的前端设置有用于在碰撞过程中通过压缩变形吸收碰撞能量的前端吸能机构,通过前端吸能结构152吸收碰撞能量,减小司机室15的变形和损坏,进而保护司机的人身安全;设置于车体1最前端的防爬结构154用于防止轨道车辆在碰撞过程中产生爬叠现象,进一步减小轨道车辆碰撞之后的损失;
在底架11与端墙12之间连接有后端吸能结构16;在现有轨道车辆中,端墙12与底架11端部的端底架11直接固定连接,在轨道车辆发生碰撞过程中,车体1之间会产生刚性碰撞,当碰撞能量较大时,车体1便会发生挤压变形,使车体1朝向车内凹陷,从而会使车内人员的身体直接受到损伤;为了防止车内人员在轨道车辆碰撞过程中直接遭受车体1的挤压,如图1结构所示,在底架11和端墙12之间连接有后端吸能结构16,通过后端吸能结构16在碰撞过程中的压缩变形吸收碰撞能量,减小车内人员部分的车体1变形,从而减小车内人员的身体损伤;
在与中部底架11的两端部对应的侧墙13上开设有门口17,并设置有用于增强门口17周围的中部底架11和侧墙13的结构强度的加强结构19;现有技术中,轨道车辆将车门设置在端底架11的上部;而与现有技术不同的是,如图3、图4和图5结构所示,本申请实施例中的车体1将门口17设置在中部底架11的两端,即,将门口17设置在中部底架11靠近端底架11的部分,从而降低门槛的高度;为了满足车体1的强度要求,在设置门口17的位置增加了加强结构19,从而使得在车体1中部开设门口17之后,车体1的结构强度仍然能够满足要求。
上述车体1在前端设置有司机室15,在后端设置有端墙12;在司机室骨架151的前端设置有防爬结构154、前端吸能结构152和前端车钩托梁153,在底架11与端墙12之间设置有后端吸能结构16,通过在车体1两端设置的前端吸能结构152后端吸能结构16能够在碰撞过程中吸收碰撞能量,从而防止轨道车辆在碰撞过程中因靠近乘客的部分车体1直接压缩变形而使乘客受伤的情况出现;同时,将乘客上下车的门口17设置在中部底架11上,使乘客从一个较低的位置逐渐进入一个较高的平台,符合进入一个空间时由下至上的基本规律,实现了人性化设计,提高了乘客的乘坐舒适性和驾乘感受。
一种具体的实施方式中,如图1和图2结构所示,端墙12的底部安装有后端车钩托梁18,并在靠近端墙12一侧的端底架11的底部安装有与后端车钩托梁18对应的后端车钩安装座(图中未示出);在靠近司机室15一端的端底架11的底部安装有与前端车钩托梁153对应的前端车钩安装座111;前端车钩托梁153、前端车钩安装座111、后端车钩托梁18以及后端车钩安装座均用于安装回退式车钩。
在车体1的前端和后端分别安装有一组车钩托梁和车钩安装座,通过安装于车体1前端的前端车钩托梁153和前端车钩安装座111安装有一个回退式车钩,通过安装于车体1后端的后端车钩托梁18和后端车钩安装座也安装有一个回退式车钩;由于在车体1两端设置回退式车钩,在轨道车辆发生碰撞时,回退式车钩会在碰撞作用力的作用下发生破坏并回退,从而通过结构破坏消耗一部分碰撞能量,还能防止车钩的发生应力集中而对车体1产生破坏作用,从而发生二次事故。
为了保证车体1在开设门口17之后能够满足结构强度和刚度要求,加强结构19包括焊接连接于侧墙13的矩形加强筋191、焊接连接于侧墙13和底架11的多个u形加强筋192以及焊接于u形加强筋192的开口侧的盖板193。如图6结构所示,在底架11和侧墙13之间设置有加强结构19,加强结构19包括焊接连接在侧墙13上的矩形加强筋191,为了提高矩形加强筋191的加强作用,还可以将矩形加强筋191焊接连接在侧墙加强筋131之间,并在侧墙13和底架11之间焊接连接有多个u形加强筋192,为了提高u形加强筋192的加强效果,还可以在u形加强筋192的开口侧焊接盖板193;如图6结构所示,为了减轻车体1重量,还可以在u形加强筋192和矩形加强筋191设置减重孔。
如图1结构所示,后端吸能结构16包括两个连接梁161、多个后端吸能盒162以及多个连接板163;连接梁161焊接连接在端墙12和底架11的边梁之间;后端吸能盒162焊接连接在端墙12和底架11的端梁之间;连接板163焊接连接在端墙12和端梁之间。
后端吸能结构16固定连接在端墙12底部与车体1后端的端底架11之间,后端吸能结构16包括用于固定连接端底架11与端墙12的两个连接梁161和多个连接板163,连接梁161和连接板163可以采用不锈钢板制成,同时在端底架11和端墙12之间连接有多个吸能盒,吸能盒用于在轨道车辆发生碰撞过程中通过逐级压溃变形吸收碰撞能量,使吸能盒从车体1外侧逐渐朝车体1内侧变形吸能。
如图1结构所示,在布设后端吸能结构16的时候,沿车体1的宽度方向,后端吸能盒162和连接板163依次交替间隔设置;连接梁161和连接板163均采用不锈钢板制成;连接板163上设置有多个开孔。
由于沿车体1的宽度方向上,后端吸能盒162和连接板163依次交替间隔设置,在轨道车辆发生碰撞过程中,多个吸能盒能够同时变形吸能,使车体1沿长度方向均匀变形;同时,在连接板163上设置有开孔,从而在碰撞过程中,通过开孔能够使连接板163发生变形吸能,而不会成为防止吸能盒吸能变形的刚性支撑。
同时,如图2结构所示,前端吸能结构152包括多个前端吸能盒1521和至少一个吸能管1522,前端吸能盒1521和吸能管1522均固定连接于司机室骨架151与前端车钩托梁153之间。
不仅在车体1的后端设置有后端吸能结构16,在车体1的前端也设置有前端吸能结构152,前端吸能结构152通过吸能盒和吸能管1522进行碰撞吸能,从而将碰撞能量进行消耗,防止在轨道车辆碰撞过程中直接对司机室15产生破坏,以保护司机的人身安全。
更进一步地,前端吸能盒1521和后端吸能盒162均包括筒形外壳以及平行设置于筒形外壳内的多个隔板(图中未示出);筒形外壳设置有用于诱导溃缩变形的多个诱导孔。
前端吸能盒1521和后端吸能盒162通过筒形外壳的压缩变形进行吸收碰撞能量,同时,通过设置在筒形外壳内的多个隔板实现筒形外壳的逐级压溃,为了能够满足轨道车辆的碰撞性能指标,筒形外壳采用以下结构、材料和工艺进行制造:
筒形外壳包括沿车体1的长度方向延伸的上筒壁、下同壁、左筒壁和右筒壁;上筒壁与左筒壁和右筒壁之间、下同壁与左筒壁和右筒壁之间均采用弧焊连接;上筒壁和下同壁平行设置;左筒壁和右筒壁之间形成开口朝向底架11的夹角,用于使筒形外壳朝向底架11的前端截面积大于筒形外壳朝向端墙12的后端截面积;夹角为2°~4°,如:2°、3°、4°;筒形外壳和隔板均采用a588低合金高强度钢板制成。
在上述前端吸能盒1521和后端吸能盒162中,上筒壁、下同壁、左筒壁和右筒壁可以采用厚度为3mm、4mm、5mm的a588低合金高强度钢板弯折制成,隔板可以采用厚度为5mm的a588低合金高强度钢板制成,隔板与筒壁之间采用弧焊连接。
如图4结构所示,上述车体1还包括通过二层地板20连接件固定安装于侧墙13的二层地板20;二层地板20连接件通过不锈钢折弯件焊接在侧墙13的侧墙13托架上,并与侧墙13的侧墙13立柱铆接;车顶14与侧墙13的两端部通过z2角焊缝焊接连接,车顶14与侧墙13的中间部分通过点焊连接;侧墙13与底架11之间通过点焊连接;侧墙13与端墙12和司机室15之间均采用不锈钢方形条角焊缝焊接连接。侧墙13与车顶14和底架11之间采用点焊连接时,点焊形成的焊点直径可以为5.7mm、焊点间距可以为70mm
在上述车体1结构中,在侧墙13和端墙12之间、以及侧墙13与司机室15的焊接连接过程中,需要现在侧墙13和端墙12、以及侧墙13与司机室15形成的夹角中放入不锈钢材料的方形条材,然后再采用焊接连接的方法在方形条材与侧墙13、端墙12以及司机室15上形成角焊缝,通过角焊缝将侧墙13和端墙12连接在一起,并将侧墙13与司机室15连接在一起,从而解决了侧墙13和端墙12之间、以及侧墙13与司机室15之间连接强度不能满足要求的问题。
如图5结构所示,上述车体1还包括通过螺栓固定安装于车顶14且靠近端墙12一侧的外罩板21,外罩板21用于增强车体1的流线型和防水性。
通过设置在车体1上的外罩板21,可以将车顶14后端的裸露部分进行遮挡,防止该部分车顶14上的零部件露在外面,从而在提高车体1外观美观性的同时,还能增强车体1的流线外形和防水性能。
尽管已描述了本申请的优选实施例,但本领域内的技术人员一旦得知了基本创造性概念,则可对这些实施例作出另外的变更和修改。所以,所附权利要求意欲解释为包括优选实施例以及落入本申请范围的所有变更和修改。
显然,本领域的技术人员可以对本申请进行各种改动和变型而不脱离本申请的精神和范围。这样,倘若本申请的这些修改和变型属于本申请权利要求及其等同技术的范围之内,则本申请也意图包含这些改动和变型在内。
本文用于企业家、创业者技术爱好者查询,结果仅供参考。