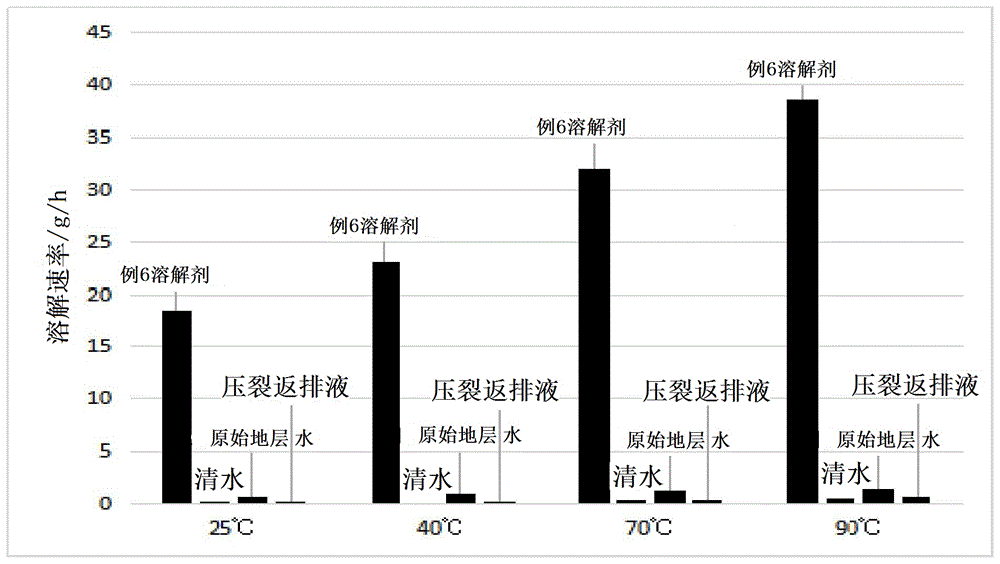
本发明提供了一种镁合金溶解剂。
背景技术:
镁合金材料作为一种新型的工具材料,由于其具有高强度、高耐温、低密度、可在卤水中随时间缓慢溶解等显著优势而大范围应用于石油天然气开发行业中,其利用途径主要包括制作成可溶压裂球、可溶桥塞、可溶堵头及其它临时性封堵部件进行使用。
虽然目前的镁合金材料经过不同的改性,其在不同的温度和不同的储层原始矿化度地层水中溶解速率相比常规的商品牌号镁合金(例如az91d、az41m、zk61m等)有很大提高,但其仍然无法满足特殊工况下的快速溶解需要,例如页岩气开发用到的可溶桥塞工具,在不注入任何外加溶解剂的情况下,仅仅依靠原始地层水或压裂返排液水质环境,一般需要在地层温度130℃温度下焖井5-7天或更长时间保证可溶桥塞完全溶解。而在低温环境下(低于50℃)可溶镁合金材料溶解更慢,因此其在低温井中应用受到限制。为了满足可溶镁合金材料在低温井中溶解更快的需求,或者为了满足部分特殊工况,例如含可溶工具的修井解堵作业、压裂施工中可溶滑套开启作业等,无论是高温井还是低温井均要求可溶镁合金材料在48小时内完全溶解,因此迫切需要研制一种外加工作液体系,通过在井筒中加入该外加工作液,使之接触可溶镁合金材料并加速镁合金材料的溶解速度。
通过调研目前还没有相关文献或者专利介绍这种促使镁合金加快溶解的工作液体系。但在油气田开发实际施工使用中,一般都采用一定浓度的盐酸体系注入井筒并接触井筒中的镁合金工具,浸泡一段时间后使得镁合金工具溶解。但该盐酸体系存在一个大的难题就是盐酸属于危化品,采购、运输和使用均受到严格监管,安全风险较大;同时盐酸体系虽然能快速溶解镁合金工件但由于盐酸属于高腐蚀性液体,即使加了缓蚀剂其对井筒中的油管或者套管钢均具有严重的腐蚀性,特别是在高于60℃的环境中腐蚀性更明显,一般严禁酸液体系在井筒中停留超过24h。所以采用盐酸体系作为镁合金溶解控制剂具有一定的局限性。
由此可以看出,研制一种非酸性的对油套管无腐蚀性影响的镁合金溶解促进剂具有现实性的迫切要求,同时也将对镁合金材料在油气田的应用起到良好的推进作用,解决现场对镁合金溶解的特殊要求。
技术实现要素:
本发明之一提供了一种镁合金溶解剂,其包括氧化剂、铵盐、氯盐、缓蚀剂和水。
在一个具体实施方式中,以所述镁合金溶解剂的总质量计作100%,所述氧化剂的含量为0.1%至5%,所述铵盐的含量以铵根离子计为0.6%至13%,所述氯盐的含量以氯离子计为0.5%至17.6%,所述缓蚀剂的含量为0.2%至1%。余量组分可以为水。
在一个具体实施方式中,以所述镁合金溶解剂的总质量计作100%,所述氧化剂的含量为0.5%至1%,所述铵盐以铵根离子的含量计为2.3%至9.9%。
在一个具体实施方式中,所述氧化剂包括无机过氧化物、重铬酸钾、高锰酸钾和氯酸盐中的至少一种。
在一个具体实施方式中,所述无机过氧化物包括过硫酸铵、过硫酸钠、过硫酸钾、过硫酸镁和过溴酸钠中的至少一种。
在一个具体实施方式中,所述氯酸盐中包括氯酸钾和/或氯酸钠。
在一个具体实施方式中,所述铵盐为可在水溶液中离解出nh4 的盐,优选地,该铵盐包括过硫酸铵、氯化铵、硫酸氢铵、碳酸铵、碳酸氢铵、硝酸铵、氟化铵和溴化铵中的至少一种。需要指出的是,过硫酸铵既可以作为过氧化物也可以作为铵盐加入到本发明的镁合金溶解剂中。
在一个具体实施方式中,所述氯盐包括氯化钠、氯化钾和氯化铵中的至少一种。另外需要指出的是,氯化铵既可以作为铵盐也可以作为氯盐加入到本发明的镁合金溶解剂中。
在一个具体实施方式中,所述缓蚀剂包括吡啶类、炔醇类和曼尼希碱类中的至少一种。
在一个具体实施方式中,所述吡啶类包括氯化苄基吡啶、氯化苄基喹啉季铵盐、溴化十二烷基吡啶、3-甲基吡啶、4-甲基吡啶和乙烯基吡啶中的至少一种。
在一个具体实施方式中,所述炔醇类包括乙炔醇、丁炔二醇、丙炔醇、己炔醇和辛炔醇中的至少一种。
在一个具体实施方式中,所述曼尼希碱类包括(c6h5)c(o)c2h4nhc2h4nhc2h4c(o)(c6h5)和/或(c6h5)c(o)ch2ch2n(c6h11)。
在一个具体实施方式中,所述(c6h5)c(o)c2h4nhc2h4nhc2h4c(o)(c6h5)为苯乙酮、甲醛与乙二胺反应产物。
在一个具体实施方式中,所述(c6h5)c(o)ch2ch2n(c6h11)为苯乙酮、甲醛与环己胺反应产物。
例如,苯乙酮、甲醛与乙二胺在2:2:1摩尔比下反应生成的(c6h5)c(o)c2h4nhc2h4nhc2h4c(o)(c6h5)。或者,苯乙酮、甲醛与环己胺在1:1:1的摩尔比下反应生成的(c6h5)c(o)ch2ch2n(c6h11)。
本发明之二提供了本发明之一中任意一项所述的镁合金溶解剂在溶解镁合金材料中的应用。
本发明的有益效果:
1.本发明的镁合金溶解剂可长时间存在于地下井筒中而对油套管钢材无明显腐蚀破坏作用。
2.本发明的镁合金溶解剂对镁合金材料溶解迅速,在40℃下,溶解速率可达到38-70g/h,相比于镁合金在清水中的溶解速度提高230倍以上,相比于镁合金在原始地层水或压裂返排液水质环境中的溶解速度提高35倍或160倍以上。
3.本发明的镁合金溶解剂液体配制简单,施工安全,注入地下工艺简单,对镁合金材料的溶解速度受温度影响小,即使在常温25℃下也能很快与镁合金材料反应,并将镁合金材料溶解完全。
附图说明
图1显示了az33m-gcy圆球分别在各溶解剂中40℃下浸泡4小时后的溶解形貌图。其中,从左到右的溶解剂依次为:清水(矿化度217mg/l,铵根离子质量百分含量为0%,氯离子质量百分含量为0.018%)、压裂返排液(主要成分为胍胶破胶液,矿化度3300mg/l,铵根离子质量百分含量为0%,氯离子质量百分含量为0.14%)、原始地层水(矿化度12700mg/l,取自川西某气井2800米地层,铵根离子质量百分含量为0%,氯离子质量百分含量为0.49%)、实施例6的溶解剂及实施例1的溶解剂。结果表明可溶镁合金az33m-gcy圆球在研制的溶解剂中的直径明显小于在清水、压裂返排液或者原始地层水中的圆球直径,特别是在实施例1的溶解剂中浸泡后的球,4小时后几乎完全溶解。所以研制的溶解剂对可溶镁合金az33m-gcy具有良好的快溶效果。
图2显示了各溶解剂在40℃对n80钢片腐蚀的不同形貌对比。其中,从左到右的溶解剂依次为:实施例1的溶解剂、实施例3的溶解剂、实施例6的溶解剂及对比例3的溶解剂。结果表明n80钢片在上述研制的溶解剂中浸泡后,表面依然有金属光泽,腐蚀极小,而在对比例3的盐酸中浸泡后,n80钢片表面变黑,失去金属光泽,腐蚀较明显。所以研制的溶解剂对油/套管管材具有良好的保护作用。
图3显示了az33m-gcy圆球分别在清水(矿化度217mg/l,铵根离子质量百分含量为0%,氯离子质量百分含量为0.018%)、原始地层水(矿化度12700mg/l,取自川西某气井2800米地层,铵根离子质量百分含量为0%,氯离子质量百分含量为0.49%)、压裂返排液(主要成分为胍胶破胶液,矿化度3300mg/l,铵根离子质量百分含量为0%,氯离子质量百分含量为0.14%)及实施例6的溶解剂(即图中的例6溶解剂)中于25℃、40℃、70℃和90℃下的溶解速率的柱状图。
具体实施方式
下面结合实施例对本发明作进一步说明,但本发明实施例仅为示例性的说明,该实施方式无论在任何情况下均不构成对本发明的限定。
将az33m-gcy镁合金材料(材料配方为:3%的铝,3%的锌,2%的铁,15%的铜,0.1%的银,1%的镍,余量为镁)以及az33m(材料配方为:3.2%的铝,2.6%的锌,0.5%的硼,0.5%的钇,余量为镁)、az91d(材料配方为:9%的铝,0.8%的锌,0.2%的锰,余量为镁)、az41m(材料配方为:4.2%的铝,0.8%的锌,0.4%的锰,余量为镁)、zk61m(材料配方为:6%的锌,0.9%的锆,余量为镁)商用镁合金材料分别加工成直径为60.0mm的圆球。
实施例1
以所述镁合金溶解剂的总质量计作100%。
氧化剂:过硫酸铵,质量百分含量1%。
铵盐:控制溶液中总铵根离子质量百分含量为5.16%,其中氧化剂中的过硫酸铵产生0.16%的铵根离子,新加入质量百分含量为15%的氯化铵产生5%的铵根离子。
氯盐:控制溶液中总氯离子质量百分含量为13%,其中铵盐中的氯化铵产生10%的氯离子,新加入质量百分含量为5%的氯化钠产生3%的氯离子。
缓蚀剂:氯化苄基吡啶,质量百分含量0.2%(25℃时溶解镁合金的含量)、0.3%(40℃时溶解镁合金的含量)、0.5%(70℃时溶解镁合金的含量)、1%(90℃时溶解镁合金的含量)。
余量为清水(市政自来水:铵根离子质量百分含量为0%,氯离子质量百分含量为0.018%。要求配液清水中原始铵根离子含量≤100mg/l,原始氯离子含量≤500mg/l,不影响铵根离子和氯离子终浓度)。
将以上物质按照氧化剂、铵盐、氯盐、缓蚀剂的顺序加入反应釜中并在常温下搅拌反应3小时,直到所有的固体粉末添加剂溶解充分并形成均匀液体即可得到镁合金溶解剂。
将az33m-gcy圆球放入3000ml上述配制的溶解剂中,分别在25℃、40℃、70℃、90℃下反应4小时,将球取出烘干后,通过天平称量溶解前与溶解后的质量差计算其溶解速率,测试结果见表1。在40℃下浸泡反应4小时后的形貌见图1。
将标准n80测试钢片放入1000ml上述配制的溶解剂中,分别在25℃、40℃、70℃、90℃下反应4小时,将钢片取出烘干后,参照石油行业标准sy-t5405-1996《酸化用缓蚀剂性能试验方法及评价指标》要求,通过天平称量腐蚀前与腐蚀后的质量差计算其腐蚀速率,测试结果见表1。在40℃下反应4小时后的形貌见图2。
将az33m、az91d、az41m、zk61m各圆球分别放入3000ml上述配制的溶解剂中,在40℃下反应4小时,将球取出烘干后,通过天平称量溶解前与溶解后的质量差计算其溶解速率,测试结果见表2。
实施例2
以所述镁合金溶解剂的总质量计作100%。
氧化剂:过硫酸铵,质量百分含量0.5%。
铵盐:控制溶液中总铵根离子质量百分含量为6.78%,其中氧化剂中的过硫酸铵产生0.08%的铵根离子,新加入质量百分含量为20%的氯化铵产生6.7%的铵根离子。
氯盐:控制溶液中总氯离子质量百分含量为17.6%,其中铵盐中的氯化铵产生13.3%的氯离子,新加入质量百分含量为7%的氯化钠产生4.3%的氯离子。
缓蚀剂:氯化苄基吡啶,质量百分含量0.2%(25℃时溶解镁合金的含量)、0.3%(40℃时溶解镁合金的含量)、0.5%(70℃时溶解镁合金的含量)、1%(90℃时溶解镁合金的含量)。
余量为清水(市政自来水:铵根离子质量百分含量为0%,氯离子质量百分含量为0.018%)。
将以上物质按照氧化剂、铵盐、氯盐、缓蚀剂的顺序加入反应釜中并在常温下搅拌反应3小时,直到所有的固体粉末添加剂溶解充分并形成均匀液体即可得到镁合金溶解剂。
将az33m-gcy圆球放入3000ml上述配制的溶解剂中,分别在25℃、40℃、70℃、90℃下反应4小时,球将取出烘干后,通过天平称量溶解前与溶解后的质量差计算其溶解速率,测试结果见表1。
将标准n80测试钢片放入1000ml上述配制的溶解剂中,分别在25℃、40℃、70℃、90℃下反应4小时,将钢片取出烘干后,参照石油行业标准sy-t5405-1996《酸化用缓蚀剂性能试验方法及评价指标》要求,通过天平称量腐蚀前与腐蚀后的质量差计算其腐蚀速率,测试结果见表1。
将az33m、az91d、az41m、zk61m各圆球分别放入3000ml上述配制的溶解剂中,在40℃下反应4小时,将球取出烘干后,通过天平称量溶解前与溶解后的质量差计算其溶解速率,测试结果见表2。
实施例3
以所述镁合金溶解剂的总质量计作100%。
氧化剂:过硫酸钠,质量百分含量1%。
铵盐:控制溶液中总铵根离子质量百分含量为6.7%,加入质量百分含量为20%的氯化铵产生6.7%的铵根离子。
氯盐:控制溶液中总氯离子质量百分含量为17.6%,其中铵盐中的氯化铵产生13.3%的氯离子,新加入质量百分含量为7%的氯化钠产生4.3%的氯离子。
缓蚀剂:溴化十二烷基吡啶,质量百分含量0.2%(25℃时溶解镁合金的含量)、0.3%(40℃时溶解镁合金的含量)、0.5%(70℃时溶解镁合金的含量)、1%(90℃时溶解镁合金的含量)。
余量为清水(市政自来水:铵根离子质量百分含量为0%,氯离子质量百分含量为0.018%)。
将以上物质按照氧化剂、铵盐、氯盐、缓蚀剂的顺序加入反应釜中并在常温下搅拌反应3小时,直到所有的固体粉末添加剂溶解充分并形成均匀液体即可得到镁合金溶解剂。
将az33m-gcy圆球放入3000ml上述配制的溶解剂中,分别在25℃、40℃、70℃、90℃下反应4小时,将球取出烘干后,通过天平称量溶解前与溶解后的质量差计算其溶解速率,测试结果见表1。
将标准n80测试钢片放入1000ml上述配制的溶解剂中,分别在25℃、40℃、70℃、90℃下反应4小时,将钢片取出烘干后,参照石油行业标准sy-t5405-1996《酸化用缓蚀剂性能试验方法及评价指标》要求,通过天平称量腐蚀前与腐蚀后的质量差计算其腐蚀速率,测试结果见表1。在40℃下反应4小时后的形貌见图2。
将az33m、az91d、az41m、zk61m各圆球分别放入3000ml上述配制的溶解剂中,在40℃下反应4小时,将球取出烘干后,通过天平称量溶解前与溶解后的质量差计算其溶解速率,测试结果见表2。
实施例4
以所述镁合金溶解剂的总质量计作100%。
氧化剂:过溴酸钠,质量百分含量1%。
铵盐:控制溶液中总铵根离子质量百分含量为5%,加入质量百分含量为15%的氯化铵产生5%的铵根离子。
氯盐:控制溶液中总氯离子质量百分含量为11.9%,其中铵盐中的氯化铵产生10%的氯离子,新加入质量百分含量为4%的氯化钾产生1.9%的氯离子。
缓蚀剂:3-甲基吡啶,质量百分含量0.2%(25℃时溶解镁合金的含量)、0.3%(40℃时溶解镁合金的含量)、0.5%(70℃时溶解镁合金的含量)、1%(90℃时溶解镁合金的含量)。
余量为清水(市政自来水:铵根离子质量百分含量为0%,氯离子质量百分含量为0.018%)。
将以上物质按照氧化剂、铵盐、氯盐、缓蚀剂的顺序加入反应釜中并在常温下搅拌反应3小时,直到所有的固体粉末添加剂溶解充分并形成均匀液体即可得到镁合金溶解剂。
将az33m-gcy圆球放入3000ml上述配制的溶解剂中,分别在25℃、40℃、70℃、90℃下反应4小时,将球取出烘干后,通过天平称量溶解前与溶解后的质量差计算其溶解速率,测试结果见表1。
将标准n80测试钢片放入1000ml上述配制的溶解剂中,分别在25℃、40℃、70℃、90℃下反应4小时,将钢片取出烘干后,参照石油行业标准sy-t5405-1996《酸化用缓蚀剂性能试验方法及评价指标》要求,通过天平称量腐蚀前与腐蚀后的质量差计算其腐蚀速率,测试结果见表1。
将az33m、az91d、az41m、zk61m各圆球分别放入3000ml上述配制的溶解剂中,在40℃下反应4小时,将球取出烘干后,通过天平称量溶解前与溶解后的质量差计算其溶解速率,测试结果见表2。
实施例5
以所述镁合金溶解剂的总质量计作100%。
氧化剂:过硫酸镁,质量百分含量1%。
铵盐:控制溶液中总铵根离子质量百分含量为2.7%,加入质量百分含量为10%的硫酸铵产生2.7%的铵根离子。
氯盐:控制溶液中总氯离子质量百分含量为0.6%,加入质量百分含量为1%的氯化钠产生0.6%的氯离子。
缓蚀剂:乙炔醇,质量百分含量0.2%(25℃时溶解镁合金的含量)、0.3%(40℃时溶解镁合金的含量)、0.5%(70℃时溶解镁合金的含量)、1%(90℃时溶解镁合金的含量)。
余量为清水(市政自来水:铵根离子质量百分含量为0%,氯离子质量百分含量为0.018%)。
将以上物质按照氧化剂、铵盐、氯盐、缓蚀剂的顺序加入反应釜中并在常温下搅拌反应3小时,直到所有的固体粉末添加剂溶解充分并形成均匀液体即可得到镁合金溶解剂。
将az33m-gcy圆球放入3000ml上述配制的溶解剂中,分别在25℃、40℃、70℃、90℃下反应4小时,将球取出烘干后,通过天平称量溶解前与溶解后的质量差计算其溶解速率,测试结果见表1。
将标准n80测试钢片放入1000ml上述配制的溶解剂中,分别在25℃、40℃、70℃、90℃下反应4小时,将钢片取出烘干后,参照石油行业标准sy-t5405-1996《酸化用缓蚀剂性能试验方法及评价指标》要求,通过天平称量腐蚀前与腐蚀后的质量差计算其腐蚀速率,测试结果见表1。
将az33m、az91d、az41m、zk61m各圆球分别放入3000ml上述配制的溶解剂中,在40℃下反应4小时,将球取出烘干后,通过天平称量溶解前与溶解后的质量差计算其溶解速率,测试结果见表2。
实施例6
以所述镁合金溶解剂的总质量计作100%。
氧化剂:重铬酸钾,质量百分含量0.5%。
铵盐:控制溶液中总铵根离子质量百分含量为3.4%,加入质量百分含量为10%的氯化铵产生3.4%的铵根离子。
氯盐:控制溶液中总氯离子质量百分含量为7.2%,其中铵盐中的氯化铵产生6.6%的氯离子,新加入质量百分含量为1%的氯化钠产生0.6%的氯离子。
缓蚀剂:乙炔醇,质量百分含量0.2%(25℃时溶解镁合金的含量)、0.3%(40℃时溶解镁合金的含量)、0.5%(70℃时溶解镁合金的含量)、1%(90℃时溶解镁合金的含量)。
余量为清水(市政自来水:铵根离子质量百分含量为0%,氯离子质量百分含量为0.018%)。
将以上物质按照氧化剂、铵盐、氯盐、缓蚀剂的顺序加入反应釜中并在常温下搅拌反应3小时,直到所有的固体粉末添加剂溶解充分并形成均匀液体即可得到镁合金溶解剂。
将az33m-gcy圆球放入3000ml上述配制的溶解剂中,分别在25℃、40℃、70℃、90℃下反应4小时,将球取出烘干后,通过天平称量溶解前与溶解后的质量差计算其溶解速率,测试结果见表1和图3。
将标准n80测试钢片放入1000ml上述配制的溶解剂中,分别在25℃、40℃、70℃、90℃下反应4小时,测试其腐蚀速率,将钢片取出烘干后,参照石油行业标准sy-t5405-1996《酸化用缓蚀剂性能试验方法及评价指标》要求,通过天平称量腐蚀前与腐蚀后的质量差计算结果见表1。在40℃下反应4小时后的形貌见图2。
将az33m、az91d、az41m、zk61m各圆球分别放入3000ml上述配制的溶解剂中,在40℃下反应4小时,将球取出烘干后,通过天平称量溶解前与溶解后的质量差计算其溶解速率,测试结果见表2。
实施例7
以所述镁合金溶解剂的总质量计作100%。
氧化剂:高锰酸钾,质量百分含量0.5%。
铵盐:控制溶液中总铵根离子质量百分含量为2.3%,加入质量百分含量为15%的硫酸氢铵产生2.3%的铵根离子。
氯盐:控制溶液中总氯离子质量百分含量为0.5%,加入质量百分含量为1%的氯化钾产生0.5%的氯离子。
缓蚀剂:氯化苄基吡啶,质量百分含量0.2%(25℃时溶解镁合金的含量)、0.3%(40℃时溶解镁合金的含量)、0.5%(70℃时溶解镁合金的含量)、1%(90℃时溶解镁合金的含量)。
余量为清水(市政自来水:铵根离子质量百分含量为0%,氯离子质量百分含量为0.018%)。
将以上物质按照氧化剂、铵盐、氯盐、缓蚀剂的顺序加入反应釜中并在常温下搅拌反应3小时,直到所有的固体粉末添加剂溶解充分并形成均匀液体即可得到镁合金溶解剂。
将az33m-gcy圆球放入3000ml上述配制的溶解剂中,分别在25℃、40℃、70℃、90℃下反应4小时,将球取出烘干后,通过天平称量溶解前与溶解后的质量差计算其溶解速率,测试结果见表1。
将标准n80测试钢片放入1000ml上述配制的溶解剂中,分别在25℃、40℃、70℃、90℃下反应4小时,将钢片取出烘干后,参照石油行业标准sy-t5405-1996《酸化用缓蚀剂性能试验方法及评价指标》要求,通过天平称量腐蚀前与腐蚀后的质量差计算其腐蚀速率,测试结果见表1。
将az33m、az91d、az41m、zk61m各圆球分别放入3000ml上述配制的溶解剂中,在40℃下反应4小时,将球取出烘干后,通过天平称量溶解前与溶解后的质量差计算其溶解速率,测试结果见表2。
实施例8
以所述镁合金溶解剂的总质量计作100%。
氧化剂:氯酸钾,质量百分含量1%。
氯盐:控制溶液中总氯离子质量百分含量为4.6%,加入质量百分含量为7%的氯化铵产生4.6%的氯离子。
铵盐:控制溶液中总铵根离子质量百分含量为9.9%,其中氯盐中的氯化铵产生2.4%的铵根离子,新加入质量百分含量为20%的碳酸铵产生7.5%的铵根离子。
缓蚀剂:丁炔二醇,质量百分含量0.2%(25℃时溶解镁合金的含量)、0.3%(40℃时溶解镁合金的含量)、0.5%(70℃时溶解镁合金的含量)、1%(90℃时溶解镁合金的含量)。
余量为清水(市政自来水:铵根离子质量百分含量为0%,氯离子质量百分含量为0.018%)。
将以上物质按照氧化剂、氯盐、铵盐、缓蚀剂的顺序加入反应釜中并在常温下搅拌反应3小时,直到所有的固体粉末添加剂溶解充分并形成均匀液体即可得到镁合金溶解剂。
将az33m-gcy圆球放入3000ml上述配制的溶解剂中,分别在25℃、40℃、70℃、90℃下反应4小时,将球取出烘干后,通过天平称量溶解前与溶解后的质量差计算其溶解速率,测试结果见表1。
将标准n80测试钢片放入1000ml上述配制的溶解剂中,分别在25℃、40℃、70℃、90℃下反应4小时,将钢片取出烘干后,参照石油行业标准sy-t5405-1996《酸化用缓蚀剂性能试验方法及评价指标》要求,通过天平称量腐蚀前与腐蚀后的质量差计算其腐蚀速率,测试结果见表1。
将az33m、az91d、az41m、zk61m各圆球分别放入3000ml上述配制的溶解剂中,在40℃下反应4小时,将球取出烘干后,通过天平称量溶解前与溶解后的质量差计算其溶解速率,测试结果见表2。
实施例9
以所述镁合金溶解剂的总质量计作100%。
氧化剂:氯酸钠,质量百分含量1%。
氯盐:控制溶液中总氯离子质量百分含量为0.7%,加入质量百分含量为1%的氯化铵产生0.7%的氯离子。
铵盐:控制溶液中总铵根离子质量百分含量为3%,其中氯盐中的氯化铵产生0.3%的铵根离子,新加入质量百分含量为10%的硫酸铵产生2.7%的铵根离子。
缓蚀剂:辛炔醇,质量百分含量0.2%(25℃时溶解镁合金的含量)、0.3%(40℃时溶解镁合金的含量)、0.5%(70℃时溶解镁合金的含量)、1%(90℃时溶解镁合金的含量)。
余量为清水(市政自来水:铵根离子质量百分含量为0%,氯离子质量百分含量为0.018%)。
将以上物质按照氧化剂、氯盐、铵盐、缓蚀剂的顺序加入反应釜中并在常温下搅拌反应3小时,直到所有的固体粉末添加剂溶解充分并形成均匀液体即可得到镁合金溶解剂。
将az33m-gcy圆球放入3000ml上述配制的溶解剂中,分别在25℃、40℃、70℃、90℃下反应4小时,将球取出烘干后,通过天平称量溶解前与溶解后的质量差计算其溶解速率,测试结果见表1。
将标准n80测试钢片放入1000ml上述配制的溶解剂中,分别在25℃、40℃、70℃、90℃下反应4小时,将钢片取出烘干后,参照石油行业标准sy-t5405-1996《酸化用缓蚀剂性能试验方法及评价指标》要求,通过天平称量腐蚀前与腐蚀后的质量差计算其腐蚀速率,测试结果见表1。
将az33m、az91d、az41m、zk61m各圆球分别放入3000ml上述配制的溶解剂中,在40℃下反应4小时,将球取出烘干后,通过天平称量溶解前与溶解后的质量差计算其溶解速率,测试结果见表2。
实施例10
以所述镁合金溶解剂的总质量计作100%。
氧化剂:过硫酸钾,质量百分含量0.8%。
铵盐:控制溶液中总铵根离子质量百分含量为4.6%,加入质量百分含量为20%的碳酸氢铵产生4.6%的铵根离子。
氯盐:控制溶液中总氯离子质量百分含量为4.3%,加入质量百分含量为7%的氯化钠产生4.3%的氯离子。
缓蚀剂:苯乙酮、甲醛与乙二胺在摩尔配比为2:2:1下的反应产物,产物分子式为(c6h5)c(o)c2h4nhc2h4nhc2h4c(o)(c6h5),质量百分含量0.2%(25℃时溶解镁合金的含量)、0.3%(40℃时溶解镁合金的含量)、0.5%(70℃时溶解镁合金的含量)、1%(90℃时溶解镁合金的含量)。
余量为清水(市政自来水:铵根离子质量百分含量为0%,氯离子质量百分含量为0.018%)。
将以上物质按照氧化剂、铵盐、氯盐、缓蚀剂的顺序加入反应釜中并在常温下搅拌反应3小时,直到所有的固体粉末添加剂溶解充分并形成均匀液体即可得到镁合金溶解剂。
将az33m-gcy圆球放入3000ml上述配制的溶解剂中,分别在25℃、40℃、70℃、90℃下反应4小时,将球取出烘干后,通过天平称量溶解前与溶解后的质量差计算其溶解速率,测试结果见表1。
将标准n80测试钢片放入1000ml上述配制的溶解剂中,分别在25℃、40℃、70℃、90℃下反应4小时,将钢片取出烘干后,参照石油行业标准sy-t5405-1996《酸化用缓蚀剂性能试验方法及评价指标》要求,通过天平称量腐蚀前与腐蚀后的质量差计算其腐蚀速率,测试结果见表1。
将az33m、az91d、az41m、zk61m各圆球分别放入3000ml上述配制的溶解剂中,在40℃下反应4小时,将球取出烘干后,通过天平称量溶解前与溶解后的质量差计算其溶解速率,测试结果见表2。
实施例11
以所述镁合金溶解剂的总质量计作100%。
氧化剂:过硫酸钠,质量百分含量0.6%。
铵盐:控制溶液中总铵根离子质量百分含量为7.3%,加入质量百分含量为15%的氟化铵产生7.3%的铵根离子。
氯盐:控制溶液中总氯离子质量百分含量为0.6%,加入质量百分含量为1%的氯化钠产生0.6%的氯离子。
缓蚀剂:苯乙酮、甲醛与环己胺在摩尔配比为1:1:1下的反应产物,产物分子式为(c6h5)c(o)ch2ch2n(c6h11),质量百分含量0.2%(25℃时溶解镁合金的含量)、0.3%(40℃时溶解镁合金的含量)、0.5%(70℃时溶解镁合金的含量)、1%(90℃时溶解镁合金的含量)。
余量为清水(市政自来水:铵根离子质量百分含量为0%,氯离子质量百分含量为0.018%)。
将以上物质按照氧化剂、铵盐、氯盐、缓蚀剂的顺序加入反应釜中并在常温下搅拌反应3小时,直到所有的固体粉末添加剂溶解充分并形成均匀液体即可得到镁合金溶解剂。
将az33m-gcy圆球放入3000ml上述配制的溶解剂中,分别在25℃、40℃、70℃、90℃下反应4小时,将球取出烘干后,通过天平称量溶解前与溶解后的质量差计算其溶解速率,测试结果见表1。
将标准n80测试钢片放入1000ml上述配制的溶解剂中,分别在25℃、40℃、70℃、90℃下反应4小时,将钢片取出烘干后,参照石油行业标准sy-t5405-1996《酸化用缓蚀剂性能试验方法及评价指标》要求,通过天平称量腐蚀前与腐蚀后的质量差计算其腐蚀速率,测试结果见表1。
将az33m、az91d、az41m、zk61m各圆球分别放入3000ml上述配制的溶解剂中,在40℃下反应4小时,将球取出烘干后,通过天平称量溶解前与溶解后的质量差计算其溶解速率,测试结果见表2。
实施例12
以所述镁合金溶解剂的总质量计作100%。
氧化剂:过溴酸钠,质量百分含量0.5%。
铵盐:控制溶液中总铵根离子质量百分含量为6.7%,加入质量百分含量为20%的氯化铵产生6.7%的铵根离子。
氯盐:控制溶液中总氯离子质量百分含量为17.6%,其中铵盐中的氯化铵产生13.3%的氯离子,新加入质量百分含量为7%的氯化钠产生4.3%的氯离子。
缓蚀剂:苯乙酮、甲醛与乙二胺在摩尔配比为2:2:1下的反应产物,产物分子式为(c6h5)c(o)c2h4nhc2h4nhc2h4c(o)(c6h5),质量百分含量0.2%(25℃时溶解镁合金的含量)、0.3%(40℃时溶解镁合金的含量)、0.5%(70℃时溶解镁合金的含量)、1%(90℃时溶解镁合金的含量)。
余量为清水(市政自来水:铵根离子质量百分含量为0%,氯离子质量百分含量为0.018%)。
将以上物质按照氧化剂、铵盐、氯盐、缓蚀剂的顺序加入反应釜中并在常温下搅拌反应3小时,直到所有的固体粉末添加剂溶解充分并形成均匀液体即可得到镁合金溶解剂。
将az33m-gcy圆球放入3000ml上述配制的溶解剂中,分别在25℃、40℃、70℃、90℃下反应4小时,将球取出烘干后,通过天平称量溶解前与溶解后的质量差计算其溶解速率,测试结果见表1。
将标准n80测试钢片放入1000ml上述配制的溶解剂中,分别在25℃、40℃、70℃、90℃下反应4小时,将钢片取出烘干后,参照石油行业标准sy-t5405-1996《酸化用缓蚀剂性能试验方法及评价指标》要求,通过天平称量腐蚀前与腐蚀后的质量差计算其腐蚀速率,测试结果见表1。
将az33m、az91d、az41m、zk61m各圆球分别放入3000ml上述配制的溶解剂中,在40℃下反应4小时,将球取出烘干后,通过天平称量溶解前与溶解后的质量差计算其溶解速率,测试结果见表2。
实施例13
以所述镁合金溶解剂的总质量计作100%。
氧化剂:过硫酸铵,质量百分含量0.6%。
氯盐:控制溶液中总氯离子质量百分含量为0.7%,加入质量百分含量为1%的氯化铵产生0.7%的氯离子。
铵盐:控制溶液中总铵根离子质量百分含量为4.1%,其中氧化剂中的过硫酸铵产生0.1%的铵根离子,氯盐中的氯化铵产生0.3%的铵根离子,新加入质量百分含量为20%的溴化铵产生3.7%的铵根离子。
缓蚀剂:氯化苄基吡啶,质量百分含量0.2%(25℃时溶解镁合金的含量)、0.3%(40℃时溶解镁合金的含量)、0.5%(70℃时溶解镁合金的含量)、1%(90℃时溶解镁合金的含量)。
余量为清水(市政自来水:铵根离子质量百分含量为0%,氯离子质量百分含量为0.018%)。
将以上物质按照氧化剂、氯盐、铵盐、缓蚀剂的顺序加入反应釜中并在常温下搅拌反应3小时,直到所有的固体粉末添加剂溶解充分并形成均匀液体即可得到镁合金溶解剂。
将az33m-gcy圆球放入3000ml上述配制的溶解剂中,分别在25℃、40℃、70℃、90℃下反应4小时,将球取出烘干后,通过天平称量溶解前与溶解后的质量差计算其溶解速率,测试结果见表1。
将标准n80测试钢片放入1000ml上述配制的溶解剂中,分别在25℃、40℃、70℃、90℃下反应4小时,将钢片取出烘干后,参照石油行业标准sy-t5405-1996《酸化用缓蚀剂性能试验方法及评价指标》要求,通过天平称量腐蚀前与腐蚀后的质量差计算其腐蚀速率,测试结果见表1。
将az33m、az91d、az41m、zk61m各圆球分别放入3000ml上述配制的溶解剂中,在40℃下反应4小时,将球取出烘干后,通过天平称量溶解前与溶解后的质量差计算其溶解速率,测试结果见表2。
实施例14
以所述镁合金溶解剂的总质量计作100%。
氧化剂:高锰酸钾,质量百分含量1%。
铵盐:控制溶液中总铵根离子质量百分含量为7.5%,加入质量百分含量为20%的碳酸铵产生7.5%的铵根离子。
氯盐:控制溶液中总氯离子质量百分含量为3.3%,加入质量百分含量为7%的氯化钾产生3.3%的氯离子。
缓蚀剂:氯化苄基喹啉季铵盐,质量百分含量0.2%(25℃时溶解镁合金的含量)、0.3%(40℃时溶解镁合金的含量)、0.5%(70℃时溶解镁合金的含量)、1%(90℃时溶解镁合金的含量)。
余量为清水(市政自来水:铵根离子质量百分含量为0%,氯离子质量百分含量为0.018%)。
将以上物质按照氧化剂、铵盐、氯盐、缓蚀剂的顺序加入反应釜中并在常温下搅拌反应3小时,直到所有的固体粉末添加剂溶解充分并形成均匀液体即可得到镁合金溶解剂。
将az33m-gcy圆球放入3000ml上述配制的溶解剂中,分别在25℃、40℃、70℃、90℃下反应4小时,将球取出烘干后,通过天平称量溶解前与溶解后的质量差计算其溶解速率,测试结果见表1。
将标准n80测试钢片放入1000ml上述配制的溶解剂中,分别在25℃、40℃、70℃、90℃下反应4小时,将钢片取出烘干后,参照石油行业标准sy-t5405-1996《酸化用缓蚀剂性能试验方法及评价指标》要求,通过天平称量腐蚀前与腐蚀后的质量差计算其腐蚀速率,测试结果见表1。
将az33m、az91d、az41m、zk61m各圆球分别放入3000ml上述配制的溶解剂中,在40℃下反应4小时,将球取出烘干后,通过天平称量溶解前与溶解后的质量差计算其溶解速率,测试结果见表2。
实施例15
以所述镁合金溶解剂的总质量计作100%。
氧化剂:质量百分含量1%的过硫酸钠和质量百分含量4%的过硫酸铵。
铵盐:控制溶液中总铵根离子质量百分含量为0.6%,4%的过硫酸铵产生0.6%的铵根离子。
氯盐:控制溶液中总氯离子质量百分含量为0.6%,加入质量百分含量为1%的氯化钠产生0.6%的氯离子。
缓蚀剂:氯化苄基喹啉季铵盐,质量百分含量0.2%(25℃时溶解镁合金的含量)、0.3%(40℃时溶解镁合金的含量)、0.5%(70℃时溶解镁合金的含量)、1%(90℃时溶解镁合金的含量)。
余量为清水(市政自来水:铵根离子质量百分含量为0%,氯离子质量百分含量为0.018%)。
将以上物质按照氧化剂、铵盐、氯盐、缓蚀剂的顺序加入反应釜中并在常温下搅拌反应3小时,直到所有的固体粉末添加剂溶解充分并形成均匀液体即可得到镁合金溶解剂。
将az33m-gcy圆球放入3000ml上述配制的溶解剂中,分别在25℃、40℃、70℃、90℃下反应4小时,将球取出烘干后,通过天平称量溶解前与溶解后的质量差计算其溶解速率,测试结果见表1。
将标准n80测试钢片放入1000ml上述配制的溶解剂中,分别在25℃、40℃、70℃、90℃下反应4小时,将钢片取出烘干后,参照石油行业标准sy-t5405-1996《酸化用缓蚀剂性能试验方法及评价指标》要求,通过天平称量腐蚀前与腐蚀后的质量差计算其腐蚀速率,测试结果见表1。
将az33m、az91d、az41m、zk61m各圆球分别放入3000ml上述配制的溶解剂中,在40℃下反应4小时,将球取出烘干后,通过天平称量溶解前与溶解后的质量差计算其溶解速率,测试结果见表2。
实施例16
以所述镁合金溶解剂的总质量计作100%。
氧化剂:过硫酸铵,质量百分含量1%。
铵盐:控制溶液中总铵根离子质量百分含量为4.7%,其中氧化剂中的过硫酸铵产生0.2%的铵根离子,新加入质量百分含量为20%的硝酸铵产生4.5%的铵根离子。
氯盐:控制溶液中总氯离子质量百分含量为0.6%,加入质量百分含量为1%的氯化钠产生0.6%的氯离子。
缓蚀剂:氯化苄基喹啉季铵盐,质量百分含量0.2%(25℃时溶解镁合金的含量)、0.3%(40℃时溶解镁合金的含量)、0.5%(70℃时溶解镁合金的含量)、1%(90℃时溶解镁合金的含量)。
余量为清水(市政自来水:铵根离子质量百分含量为0%,氯离子质量百分含量为0.018%)。
将以上物质按照氧化剂、铵盐、氯盐、缓蚀剂的顺序加入反应釜中并在常温下搅拌反应3小时,直到所有的固体粉末添加剂溶解充分并形成均匀液体即可得到镁合金溶解剂。
将az33m-gcy圆球放入3000ml上述配制的溶解剂中,分别在25℃、40℃、70℃、90℃下反应4小时,将球取出烘干后,通过天平称量溶解前与溶解后的质量差计算其溶解速率,测试结果见表1。
将标准n80测试钢片放入1000ml上述配制的溶解剂中,分别在25℃、40℃、70℃、90℃下反应4小时,将钢片取出烘干后,参照石油行业标准sy-t5405-1996《酸化用缓蚀剂性能试验方法及评价指标》要求,通过天平称量腐蚀前与腐蚀后的质量差计算其腐蚀速率,测试结果见表1。
将az33m、az91d、az41m、zk61m各圆球分别放入3000ml上述配制的溶解剂中,在40℃下反应4小时,将球取出烘干后,通过天平称量溶解前与溶解后的质量差计算其溶解速率,测试结果见表2。
实施例17
以所述镁合金溶解剂的总质量计作100%。
氧化剂:过硫酸铵,质量百分含量1%。
铵盐:控制溶液中总铵根离子质量百分含量为4.7%,其中氧化剂中的过硫酸铵产生0.2%的铵根离子,新加入质量百分含量为20%的硝酸铵产生4.5%的铵根离子。
氯盐:控制溶液中总氯离子质量百分含量为2.4%,加入质量百分含量为4%的氯化钠产生2.4%的氯离子。
缓蚀剂:氯化苄基喹啉季铵盐,质量百分含量0.2%(25℃时溶解镁合金的含量)、0.3%(40℃时溶解镁合金的含量)、0.5%(70℃时溶解镁合金的含量)、1%(90℃时溶解镁合金的含量)。
余量为清水(市政自来水:铵根离子质量百分含量为0%,氯离子质量百分含量为0.018%)。
将以上物质按照氧化剂、铵盐、氯盐、缓蚀剂的顺序加入反应釜中并在常温下搅拌反应3小时,直到所有的固体粉末添加剂溶解充分并形成均匀液体即可得到镁合金溶解剂。
将az33m-gcy圆球放入3000ml上述配制的溶解剂中,分别在25℃、40℃、70℃、90℃下反应4小时,将球取出烘干后,通过天平称量溶解前与溶解后的质量差计算其溶解速率,测试结果见表1。
将标准n80测试钢片放入1000ml上述配制的溶解剂中,分别在25℃、40℃、70℃、90℃下反应4小时,将钢片取出烘干后,参照石油行业标准sy-t5405-1996《酸化用缓蚀剂性能试验方法及评价指标》要求,通过天平称量腐蚀前与腐蚀后的质量差计算其腐蚀速率,测试结果见表1。
将az33m、az91d、az41m、zk61m各圆球分别放入3000ml上述配制的溶解剂中,在40℃下反应4小时,将球取出烘干后,通过天平称量溶解前与溶解后的质量差计算其溶解速率,测试结果见表2。
实施例18
以所述镁合金溶解剂的总质量计作100%。
氧化剂:过硫酸铵,质量百分含量1%。
氯盐:控制溶液中总氯离子质量百分含量为6.1%,加入质量百分含量为9.2%的氯化铵产生6.1%的氯离子。
铵盐:控制溶液中总铵根离子质量百分含量为13%,其中氧化剂中的过硫酸铵产生0.2%的铵根离子,氯盐中的过氯化铵产生3.1%的铵根离子,新加入质量百分含量为20%的氟化铵产生9.7%的铵根离子。
缓蚀剂:氯化苄基吡啶,质量百分含量0.2%(25℃时溶解镁合金的含量)、0.3%(40℃时溶解镁合金的含量)、0.5%(70℃时溶解镁合金的含量)、1%(90℃时溶解镁合金的含量)。
余量为清水(市政自来水:铵根离子质量百分含量为0%,氯离子质量百分含量为0.018%)。
将以上物质按照氧化剂、氯盐、铵盐、缓蚀剂的顺序加入反应釜中并在常温下搅拌反应3小时,直到所有的固体粉末添加剂溶解充分并形成均匀液体即可得到镁合金溶解剂。
将az33m-gcy圆球放入3000ml上述配制的溶解剂中,分别在25℃、40℃、70℃、90℃下反应4小时,将球取出烘干后,通过天平称量溶解前与溶解后的质量差计算其溶解速率,测试结果见表1。
将标准n80测试钢片放入1000ml上述配制的溶解剂中,分别在25℃、40℃、70℃、90℃下反应4小时,将钢片取出烘干后,参照石油行业标准sy-t5405-1996《酸化用缓蚀剂性能试验方法及评价指标》要求,通过天平称量腐蚀前与腐蚀后的质量差计算其腐蚀速率,测试结果见表1。
将az33m、az91d、az41m、zk61m各圆球分别放入3000ml上述配制的溶解剂中,在40℃下反应4小时,将球取出烘干后,通过天平称量溶解前与溶解后的质量差计算其溶解速率,测试结果见表2。
对比例1
将az33m-gcy圆球放入3000ml清水(市政自来水:铵根离子质量百分含量为0%,氯离子质量百分含量为0.018%)中,分别在25℃、40℃、70℃、90℃下反应4小时,将球取出烘干后,通过天平称量溶解前与溶解后的质量差计算其溶解速率,测试结果见表1和图3。其中,在40℃下浸泡反应4小时后的形貌见图1。
将标准n80测试钢片放入1000ml清水(市政自来水)中,分别在25℃、40℃、70℃、90℃下反应4小时,将钢片取出烘干后,参照石油行业标准sy-t5405-1996《酸化用缓蚀剂性能试验方法及评价指标》要求,通过天平称量腐蚀前与腐蚀后的质量差计算其腐蚀速率,测试结果见表1。
将az33m、az91d、az41m、zk61m各圆球分别放入3000ml清水(市政自来水)中,在40℃下反应4小时,将球取出烘干后,通过天平称量溶解前与溶解后的质量差计算其溶解速率,测试结果见表2。
对比例2
将az33m-gcy圆球放入3000ml质量浓度为20%的氯化钾溶液中,分别在25℃、40℃、70℃、90℃下反应4小时,测试其溶解速率,测试结果见表1。
将标准n80测试钢片放入1000ml质量浓度为20%的氯化钾溶液中,分别在25℃、40℃、70℃、90℃下反应4小时,将钢片取出烘干后,参照石油行业标准sy-t5405-1996《酸化用缓蚀剂性能试验方法及评价指标》要求,通过天平称量腐蚀前与腐蚀后的质量差计算其腐蚀速率,测试结果见表1。
将az33m、az91d、az41m、zk61m各圆球分别放入3000ml质量浓度为20%的氯化钾溶液中,在40℃下反应4小时,将球取出烘干后,通过天平称量溶解前与溶解后的质量差计算其溶解速率,测试结果见表2。
对比例3
15wt%盐酸 氯化苄基吡啶,其中氯化苄基吡啶在25℃溶解镁合金时加入质量为总的0.2%,在40℃溶解镁合金时加入质量为总的0.3%,在70℃溶解镁合金时加入质量为总的0.5%,在90℃溶解镁合金时加入质量为总的1%。
将az33m-gcy圆球放入3000ml上述配制的溶液中,分别在25℃、40℃、70℃、90℃下反应4小时,将球取出烘干后,通过天平称量溶解前与溶解后的质量差计算其溶解速率,测试结果见表1。
将标准n80测试钢片放入1000ml上述配制的溶液中,分别在25℃、40℃、70℃、90℃下反应4小时,将钢片取出烘干后,参照石油行业标准sy-t5405-1996《酸化用缓蚀剂性能试验方法及评价指标》要求,通过天平称量腐蚀前与腐蚀后的质量差计算其腐蚀速率,测试结果见表1。在40℃下反应4小时后的形貌见图2。
将az33m、az91d、az41m、zk61m各圆球分别放入3000ml上述配制的溶液中,在40℃下反应4小时,将球取出烘干后,通过天平称量溶解前与溶解后的质量差计算其溶解速率,测试结果见表2。
对比例4
将az33m-gcy圆球放入3000ml原始地层水(矿化度12700mg/l,取自川西某气井2800米地层,铵根离子质量百分含量为0%,氯离子质量百分含量为0.49%)中,分别在25℃、40℃、70℃、90℃下反应4小时,将球取出烘干后,通过天平称量溶解前与溶解后的质量差计算其溶解速率,测试结果见表1和图3。其中,在40℃下浸泡反应4小时后的形貌见图1。
将标准n80测试钢片放入1000ml原始地层水(矿化度12700mg/l,取自川西某气井2800米地层,铵根离子质量百分含量为0%,氯离子质量百分含量为0.49%)中,分别在25℃、40℃、70℃、90℃下反应4小时,将钢片取出烘干后,参照石油行业标准sy-t5405-1996《酸化用缓蚀剂性能试验方法及评价指标》要求,通过天平称量腐蚀前与腐蚀后的质量差计算其腐蚀速率,测试结果见表1。
将az33m、az91d、az41m、zk61m各圆球分别放入3000ml原始地层水(矿化度12700mg/l,取自川西某气井2800米地层,铵根离子质量百分含量为0%,氯离子质量百分含量为0.49%)中,在40℃下反应4小时,将球取出烘干后,通过天平称量溶解前与溶解后的质量差计算其溶解速率,测试结果见表2。
对比例5
压裂返排液(主要成分为胍胶破胶液,矿化度3300mg/l,铵根离子质量百分含量为0%,氯离子质量百分含量为0.14%)
将az33m-gcy圆球放入3000ml上述配制的压裂返排液中,分别在25℃、40℃、70℃、90℃下反应4小时,测试其溶解速率,将球取出烘干后,通过天平称量溶解前与溶解后的质量差计算结果见表1和图3。其中,在40℃下浸泡反应4小时后的形貌见图1。
将标准n80测试钢片放入1000ml上述配制的压裂返排液中,分别在25℃、40℃、70℃、90℃下反应4小时,将钢片取出烘干后,参照石油行业标准sy-t5405-1996《酸化用缓蚀剂性能试验方法及评价指标》要求,通过天平称量腐蚀前与腐蚀后的质量差计算其腐蚀速率,测试结果见表1。
将az33m、az91d、az41m、zk61m各圆球分别放入3000ml上述配制的压裂返排液中,在40℃下反应4小时,将球取出烘干后通过天平称量溶解前与溶解后的质量差计算其溶解速率,测试结果见表2。
表1溶解剂在不同温度下对镁合金材料的溶解速率及对n80钢片的腐蚀速率测试
如上表1所示,相比于清水、20%的氯化钾溶液、原始地层水及压裂返排液,实施例1至18配制的专用溶解剂对镁合金az33m-gcy的溶解速率大大提高,同时对n80钢片的腐蚀速率比较低,达到石油行业标准sy-t5405-1996《酸化用缓蚀剂性能试验方法及评价指标》技术指标要求。
表2各种溶解剂对不同镁合金材料的溶解速率测试(40℃)
如上表2所示,实施例1至18配制的专用溶解剂对各种镁合金如az33m-gcy、az33m、az91d、az41m、zk61m的溶解速率均较高,适用于大多数镁合金加工工具的井下快速溶解。
虽然本发明已经参照具体实施方式进行了描述,但是本领域的技术人员应该理解在没有脱离本发明的真正的精神和范围的情况下,可以进行的各种改变。此外,可以对本发明的主体、精神和范围进行多种改变以适应特定的情形、材料、材料组合物和方法。所有的这些改变均包括在本发明的权利要求的范围内。
本文用于企业家、创业者技术爱好者查询,结果仅供参考。