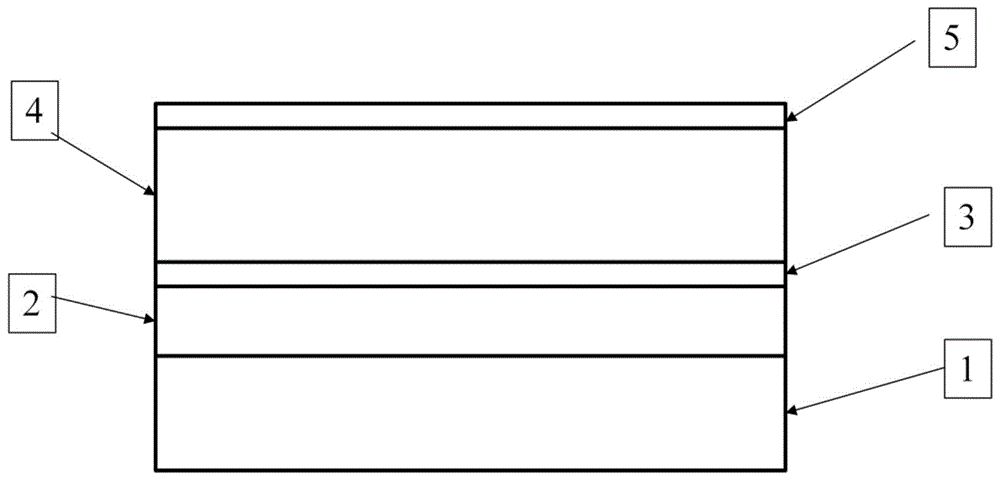
本发明属于涂层材料技术领域,尤其涉及一种输电铁塔用中熵高分子复合涂层材料及制备方法。
背景技术:
随经济的高速发展,对电力需求不断提高;特别是沿海经济发达,海岸线长,海岛数量众多,需要大量的电力保证。输电铁塔是电力安全输送的重要设备。长期服役于自然环境中,由于温度、水分、光照、腐蚀性介质、微生物等多重因素而发生腐蚀,造成严重的经济损失,威胁人民生命安全。特别是沿海地区高温、高湿、高盐气候,对输电铁塔极易造成腐蚀,而且盐雾是造成铁塔腐蚀的主要原因之一。沿海地区输电铁塔主材为碳钢,处于海洋环境的钢铁和内陆相比,容易受到各种离子的腐蚀,是造成铁塔破坏的主要原因。目前主要的防腐蚀方式主要采用热镀锌,在沿海地区铁塔热镀锌防腐蚀效果开始时较好,随铁塔开始局部锈蚀,局部锈蚀带动整塔锈蚀,使锈蚀速度呈比例增长。铁塔锈蚀后需进行维护,目前维护的方式为刷油漆,常用油漆为冷涂锌漆,油漆的防腐蚀寿命为5-10年,维护频繁,且工程量大。为延长铁塔使用寿命,亟需开展沿海地区铁塔防腐技术研究。
铁塔一般由加工好的角钢件、钢板件等各类结构件经热浸镀锌后连接而成,受其工艺所限,在浸镀锌时由于漏镀等问题经常导致涂层破损失去防护效果。此外批量热浸镀锌存在生产过程产生的酸雾、锌烟、废酸、废水等废弃物严重污染环境且无法治理,恶劣的工作环境和落后的设备直接影响工作人员的健康和安全。因此随环保政策逐渐趋紧,开发替代热浸镀锌的新型防腐技术已成为输变电工程钢构件生产的紧迫需求之一。
技术实现要素:
本发明要解决的技术问题是:提供一种输电铁塔用中熵高分子复合涂层材料及制备方法,以解决现有技术的输电线路铁塔采用的浸镀锌作为防腐材料存在的由于漏镀等问题经常导致涂层破损失去防护效果,热浸镀锌存在生产过程产生的酸雾、锌烟、废酸、废水等废弃物严重污染环境;以及抗紫外线辐照性能和耐腐蚀性能较差等技术问题。
本发明的技术方案是:
一种输电铁塔用中熵高分子复合涂层材料,它包括:znal合金涂层、环氧树脂涂层、zno粉掺杂中熵高分子复合涂层和zno掺杂有机硅涂层;所述znal合金涂层、环氧树脂涂层、zno粉掺杂中熵高分子复合涂层和zno掺杂有机硅涂层从里到外依次覆盖在铁塔基体上。
znal合金涂层采用电弧喷涂制备znal合金涂层,锌铝丝送丝速度3-10m/min,喷涂压力0.4-0.8mpa,喷涂电压30-38v,喷涂电流150-250a,喷涂距离100-300mm。
znal合金涂层的涂层厚度100-200微米,涂层表面粗糙度1-5微米,涂层结合力大于40mpa。
环氧树脂涂层(3)为zno共掺杂环氧树脂粘结层。
zno共掺杂环氧树脂粘结层的zno粉末粒度为1-5微米,掺杂量为1-5at.%,涂层厚度30-50微米。
zno粉掺杂中熵高分子复合涂层由环氧树脂、氟硅树脂以及聚氨酯、硅烷偶联剂以及氧化锌组成;环氧树脂、氟硅树脂以及聚氨酯为等比例添加,硅烷偶联剂的添加量控制在10-20wt.%,zno的添加量控制在1-5wt.%,涂层厚度40-70微米,涂层粗糙度10-50微米。
zno掺杂有机硅涂层(5)采用zno掺杂硅烷偶联剂喷涂制备。
zno掺杂量为1-5at.%,zno的粒度为5-10微米,涂层厚度20-50微米。
本发明有益效果:
本发明主要利用多层涂层结构,结合金属涂层和陶瓷掺杂的中熵高分子涂层性能上的优势,克服现有高分子涂层耐紫外和耐磨性不足的缺点,满足海边防腐蚀的需要。为实现上述目的,本发明提供的技术方案是:复合涂层由有喷znal底层、zno共掺杂环氧树脂粘结层、中熵高分子复合涂层以及有机硅复合面层构成。其制备方法是:对铁塔表面进行热喷znal合金,对热喷涂znal合金后的涂层进行zno共掺杂环氧树脂粘结层的喷涂,环氧树脂粘结层中掺杂材料采用的是氧化锌粉,提高环氧环氧树脂和底层的结合力以及抗紫外线能力;干燥后进行中熵高分子纳米复合涂层的喷涂,中熵高分子涂层由环氧树脂、氟硅树脂以及聚氨酯、硅烷偶联剂以及氧化锌进行复合而成。最后采用氧化锌掺杂有机硅复合膜作为表面防护层,提高涂层的耐磨性。
本发明是多种技术的综合利用,一是利用了多层技术,将多种涂层材料进行复合获取单一涂层材料不具备的性能;二是多种涂层材料的复合,如结合层采用电弧喷涂zlal合金,具有比纯锌更好的耐腐蚀性能;后续的多种高分子涂层中都进行了zno陶瓷粉末的添加,提高涂层的抗紫外线照射能力和耐磨耐腐蚀性能;三是将多种高分子涂层进行复合构建中熵复合涂层材料,使其具有比单一涂层材料更好的综合性能;四是利用硅烷偶联剂将多种高分子材料进行复合,硅烷偶联剂往往可以解决材料无法粘接的难题。硅烷偶联剂作为增粘剂的作用原理在于它本身有两种基团;硅烷氧基对无机物具有反应性,有机官能基对有机物具有反应性或相容性;为此中熵高分子中不但具有物理混合的效果,同时还发生化学交联,使多种高分子之间发生化学反应,使涂层形成交联的三维网络,充分提高涂层的稳定性。
因此本发明具有如下优点:
第一,与常规铁塔涂层相比,本发明是多种技术的综合应用,包括金属的电弧喷涂技术、高分子的喷涂技术,全部为绿色环保技术,避免了热浸镀锌的污染;
第二,本发明充分利用多层结构,梯度复合涂层技术,形成的涂层结构和成分有渐变,提高涂层的韧性和耐冲击性能;
第三,本发明将三种高分子材料进行复合构建中熵高分子涂层材料,提高其抗紫外线辐照性能和耐腐蚀性能;本发明中提出了构建中熵高分子涂层材料,充分利用多种高分子材料的优点,提高涂层的硬度、耐磨性、抗紫外线以及抗腐蚀性能。
第四,本发明中将zno粉末加入到涂层中,大幅度提高涂层的抗紫外线和耐磨性能,实现有机和无机涂层材料的复合;
第五,本发明将硅烷偶联剂作为粘结剂,充分利用物理混合和化学聚合,将多种材料进行有机的交联和聚合,充分提高涂层材料的致密度和结构稳定性;
综上所述,本发明所制备铁塔用中熵高分子纳米复合涂层材料将可以大幅度提高铁塔的防腐蚀性能和耐磨性,能保证变压器长期稳定工作,大幅度减少表面腐蚀的产生,施工过程简单,绿色环保,可以降低厂家的生产成本。
解决了现有技术的输电线路铁塔采用的浸镀锌作为防腐材料存在的由于漏镀等问题经常导致涂层破损失去防护效果,热浸镀锌存在生产过程产生的酸雾、锌烟、废酸、废水等废弃物严重污染环境;以及抗紫外线辐照性能和耐腐蚀性能较差等技术问题。
附图说明
图1为本发明铁塔用中熵高分子复合涂层材料结构示意图。
具体实施方式
下面结合附图和实施例对本发明的实施方式作进一步详细描述。以下实施例用于说明本发明,但不能用来限制本发明的范围。
本发明的目的在于一种铁塔用中熵高分子复合涂层材料及其制备方法。主要利用多层涂层结构,结合金属涂层和陶瓷掺杂的中熵高分子涂层性能上的优势,克服现有高分子涂层耐紫外和耐磨性不足的缺点,满足海边防腐蚀的需要。
本发明提供的技术方案是:复合涂层由有喷znal底层、zno共掺杂环氧树脂粘结层、中熵高分子复合涂层以及有机硅复合面层构成。其制备方法是:对铁塔表面进行热喷znal合金,对热喷涂znal合金后的涂层进行zno共掺杂环氧树脂粘结层的喷涂,环氧树脂粘结层中掺杂材料采用的是氧化锌粉,提高环氧环氧树脂和底层的结合力以及抗紫外线能力;干燥后进行中熵高分子纳米复合涂层的喷涂,中熵高分子涂层由环氧树脂、氟硅树脂以及聚氨酯、硅烷偶联剂以及氧化锌进行复合而成。最后采用氧化锌掺杂有机硅复合膜作为表面防护层,提高涂层的耐磨性。
本发明制备方法为:在大气环境中采用电弧喷涂制备znal合金涂层,锌铝丝送丝速度3-10m/min,喷涂压力0.4-0.8mpa,喷涂电压30-38v,喷涂电流150-250a,喷涂距离100-300mm,涂层厚度100-200微米,涂层表面粗糙度1-5微米,涂层结合力大于40mpa;喷znal合金涂层结束后进行zno共掺杂环氧树脂粘结层的喷涂,zno粉末粒度为1-5微米,掺杂量为1-5at.%,涂层厚度30-50微米;随后进行中熵高分子纳米复合涂层制备,涂层由环氧树脂、氟硅树脂以及聚氨酯、硅烷偶联剂以及氧化锌组成。环氧树脂、氟硅树脂以及聚氨酯为等比例添加,硅烷偶联剂的添加量控制在10-20wt.%,zno的添加量控制在1-5wt.%。涂层厚度40-70微米,涂层粗糙度10-50微米;最后进行保护涂层制备,有机硅保护层采用zno掺杂硅烷偶联剂喷涂制备,zno掺杂量为1-5at.%,zno的粒度为5-10微米,涂层厚度20-50微米;
如图1所示,为本发明所设计的涂层结构示意图,在铁塔基体1的基础进行电弧喷涂znal合金结合层2的制备,电弧喷涂znal合金结合层制备结束后进行掺杂zno粉的环氧树脂涂层3的制备,随后进行zno粉掺杂中熵高分子复合涂层4的制备,最后zno掺杂有机硅涂层5的制备。由于涂层结构合理,涂层和基体结合力好,具有良好的施工性能和耐候性能。
以下结合具体的实施例对本发明的技术方案作进一步说明:
实施例1:在大气环境中采用电弧喷涂制备znal合金涂层,锌铝丝送丝速度3m/min,喷涂压力0.4mpa,喷涂电压30v,喷涂电流150a,喷涂距离100mm,涂层厚度100微米,涂层表面粗糙度1微米,涂层结合力大于40mpa;喷znal合金涂层结束后进行zno共掺杂环氧树脂粘结层的喷涂,zno粉末粒度为1微米,掺杂量为1wt.%,涂层厚度30微米;随后进行中熵高分子纳米复合涂层制备,涂层由环氧树脂、氟硅树脂以及聚氨酯、硅烷偶联剂以及氧化锌组成。环氧树脂、氟硅树脂以及聚氨酯为等比例添加,硅烷偶联剂的添加量控制在10wt.%,zno的添加量控制在1wt.%。涂层厚度40微米,涂层粗糙度10微米;最后进行保护涂层制备,有机硅保护层采用zno掺杂硅烷偶联剂喷涂制备,zno掺杂量为1wt.%,zno的粒度为5微米,涂层厚度20微米;
实施例2:在大气环境中采用电弧喷涂制备znal合金涂层,锌铝丝送丝速度10m/min,喷涂压力0.8mpa,喷涂电压38v,喷涂电流250a,喷涂距离300mm,涂层厚度200微米,涂层表面粗糙度5微米,涂层结合力大于40mpa;喷znal合金涂层结束后进行zno共掺杂环氧树脂粘结层的喷涂,zno粉末粒度为5微米,掺杂量为1-5wt.%,涂层厚度50微米;随后进行中熵高分子纳米复合涂层制备,涂层由环氧树脂、氟硅树脂以及聚氨酯、硅烷偶联剂以及氧化锌组成。环氧树脂、氟硅树脂以及聚氨酯为等比例添加,硅烷偶联剂的添加量控制在20wt.%,zno的添加量控制在5wt.%。涂层厚度70微米,涂层粗糙度50微米;最后进行保护涂层制备,有机硅保护层采用zno掺杂硅烷偶联剂喷涂制备,zno掺杂量为5wt.%,zno的粒度为10微米,涂层厚度50微米;
实施例3:在大气环境中采用电弧喷涂制备znal合金涂层,锌铝丝送丝速度5m/min,喷涂压力0.5mpa,喷涂电压35v,喷涂电流200a,喷涂距离200mm,涂层厚度150微米,涂层表面粗糙度3微米,涂层结合力大于40mpa;喷znal合金涂层结束后进行zno共掺杂环氧树脂粘结层的喷涂,zno粉末粒度为3微米,掺杂量为3wt.%,涂层厚度40微米;随后进行中熵高分子纳米复合涂层制备,涂层由环氧树脂、氟硅树脂以及聚氨酯、硅烷偶联剂以及氧化锌组成。环氧树脂、氟硅树脂以及聚氨酯为等比例添加,硅烷偶联剂的添加量控制在15wt.%,zno的添加量控制在4wt.%。涂层厚度50微米,涂层粗糙度40微米;最后进行保护涂层制备,有机硅保护层采用zno掺杂硅烷偶联剂喷涂制备,zno掺杂量为4wt.%,zno的粒度为60微米,涂层厚度40微米;
实施例4:在大气环境中采用电弧喷涂制备znal合金涂层,锌铝丝送丝速度8m/min,喷涂压力0.6mpa,喷涂电压33v,喷涂电流180a,喷涂距离160mm,涂层厚度140微米,涂层表面粗糙度2微米,涂层结合力大于40mpa;喷znal合金涂层结束后进行zno共掺杂环氧树脂粘结层的喷涂,zno粉末粒度为3微米,掺杂量为2wt.%,涂层厚度40微米;随后进行中熵高分子纳米复合涂层制备,涂层由环氧树脂、氟硅树脂以及聚氨酯、硅烷偶联剂以及氧化锌组成。环氧树脂、氟硅树脂以及聚氨酯为等比例添加,硅烷偶联剂的添加量控制在15wt.%,zno的添加量控制在3wt.%。涂层厚度45微米,涂层粗糙度40微米;最后进行保护涂层制备,有机硅保护层采用zno掺杂硅烷偶联剂喷涂制备,zno掺杂量为4at.%,zno的粒度为7微米,涂层厚度30微米;
实施例5:在大气环境中采用电弧喷涂制备znal合金涂层,锌铝丝送丝速度7m/min,喷涂压力0.7mpa,喷涂电压34v,喷涂电流210a,喷涂距离220mm,涂层厚度170微米,涂层表面粗糙度3.5微米,涂层结合力大于40mpa;喷znal合金涂层结束后进行zno共掺杂环氧树脂粘结层的喷涂,zno粉末粒度为3微米,掺杂量为2at.%,涂层厚度40微米;随后进行中熵高分子纳米复合涂层制备,涂层由环氧树脂、氟硅树脂以及聚氨酯、硅烷偶联剂以及氧化锌组成。环氧树脂、氟硅树脂以及聚氨酯为等比例添加,硅烷偶联剂的添加量控制在15wt.%,zno的添加量控制在3wt.%。涂层厚度45微米,涂层粗糙度2微米;最后进行保护涂层制备,有机硅保护层采用zno掺杂硅烷偶联剂喷涂制备,zno掺杂量为3at.%,zno的粒度为6微米,涂层厚度40微米;
本发明制备的一种铁塔用中熵高分子复合涂层材料高温老化后的表面形貌,发现经过200℃高温老化后涂层表面保持完整,具有良好的耐高温性能。
本发明制备的一种铁塔用中熵高分子复合涂层材料紫外老化后的表面轮廓,发现轮廓保持良好,无明显破坏和损伤。
本发明制备的一种铁塔用中熵高分子复合涂层材料200℃高温老化后的表面原子力显微镜照片,发现表面保持完好,无缺陷。
本文用于企业家、创业者技术爱好者查询,结果仅供参考。