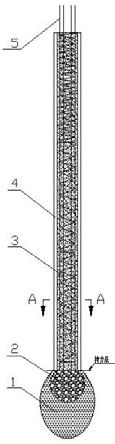
1.本发明涉及土木工程技术领域,具体为一种八齿形载体桩及其施工方法。
背景技术:
2.载体桩充分发挥了土的端阻力和桩身砼自身性能,对提高桩端承载力做出了很大的贡献,成为端承桩的代表。载体桩具有承载力高,工程成本较低的优势,但对桩周土侧阻力的利用不够,而旋挖桩由于沉渣问题对桩端土的端阻力得不到很好利用,也就使大部分桩身砼只能作为填充材料使用,而无法发挥自身性能,造成直径大和长桩长的境况,致使材料浪费大,工程造价居高不下,但它充分利用了土的侧阻力进行竖向支撑,成为摩擦桩的代表。所以载体桩和旋挖桩各有优势,但长期来却不能优势互补。
3.现有技术专利名称和专利号分别为:一种新型bnt载体桩及其施工设备,2019207853179的实用新型专利的桩端承载力得到进一步稳定提高,为载体桩技术更加完善,起到了积极作用;现有技术专利名称和专利号分别为一种载体桩以及施工设备,2013204717142的实用新型专利在很大程度上改善了繁杂的施工工艺提高了效率起到了重要作用。但它们都还有需要提高和完善的地方:1.现有技术忽视了桩周土侧阻力的利用,只是追求桩端承载力的提高;桩周土的侧阻力若得以利用也是竖向承载力的重要组成部分;2.bnt载体桩施工中,为了提高桩的综合承载力,用对桩身进行局部挤扩的方法,也能起到一定作用,但它必须将沉管成孔、填料夯实、灌注桩身混凝土、拔管等工作完成后,再换装挤扩装置,在桩身内无钢筋笼的条件下,才能实施对桩身的挤扩,最后还得用钢筋笼后植法再植入钢筋笼,又由于挤扩桩身时,挤扩装置必须深入桩身混凝土中,使原已灌满的桩身混凝土外溢,造成浪费,最后还得补满桩身混凝土。这样虽然对桩的综合承载力有一定的提高,但增繁工艺步骤降低了效率,得不偿失;3.现有技术用内夯管替代标准柱锤时的换算式,没能考虑桩管下端口,外壁与桩周土之间侧阻力的影响,而导致三击贯入度失实的问题,因此该换算式还不够严谨和完善。
技术实现要素:
4.本发明的目的在于提供一种八齿形载体桩及其施工方法,充分利用桩侧阻力,使承载力得到提高,性价比高,适用范围广。
5.为解决上述技术问题,本发明一种八齿形载体桩,包括有桩端载体和桩身,桩身为砼柱体,桩身内连接有钢筋笼,桩身外径连接有外齿,所述的外齿设有八个,八个外齿以桩身轴线为中心圆周均布,每个外齿均在桩身长度贯通,桩身和外齿截面形状为齿轮形,八个外齿的截面形状相同,每个外齿的截面形状均为梯形;桩端载体包括有挤密土体和填充料夯实体。
6.进一步的,外齿的尺寸与桩径d的关系式为:外齿齿高h=d/4;
外齿齿根宽度b=d/5;外齿齿顶宽度b=d/18;桩身与外齿的宽度d=2h+d;进一步的,桩身与外齿的实际截面积a
s
的计算公式为:a
s
=1.3252(d/2)2π;进一步的,竖向承载力计算公式为:r
a
=f
a
*a
e
μ∑q
sik
l
i
/k公式中:r
a
为载体桩单桩竖向受压承载力特征值;f
a
为经深度修正后的载体桩持力层地基承载力特征值;a
e
为载体等效计算面积;μ为实际桩身周长, μ的计算公式为:μ=2dπ;q
sik
为桩侧第i层土极限侧阻力标准值; l
i
为第i层土的厚度;k为安全系数。
7.本发明一种八齿形载体桩的施工方法,采用振动锤和标准柱锤或柴油锤为沉管动力。
8.采用振动锤为沉管动力,振动锤下端刚性连接有桩管,桩管上部设有料斗和活动观察口,桩管下端通过铰链连接活瓣桩尖,沿管外周径向焊有八个齿形体ⅰ作为桩身上八个外齿的模具,齿形体ⅰ截面为梯形,活瓣桩尖为截圆锥,活瓣桩尖顶面与桩管等径,活瓣桩尖的活瓣由四瓣组成,振动锤内连接有标准柱锤,标准柱锤通过振动锤的中孔进入桩管内,标准柱锤为钢制圆柱体,标准柱锤上端与钢丝绳连接,标准柱锤下端为平底或截锥体。
9.进一步的,振动锤为沉管动力包括有如下步骤:a、做好振动锤与桩管和活瓣桩尖的连接,并将活瓣桩尖合拢,对准桩点;b、将桩管沉到预定深度,通过桩管上部的料口投入填充料,再将桩管拔出,使桩端活瓣桩尖打开,填充料落入桩孔内;c、然后用标准柱锤通过振动锤的中孔进入桩管中,对填充料进行夯击,填充料夯实后成为填充料夯实体,最后通过桩管上部的观察口测量三击贯入度是否达到要求,如此反复直至达到要求;d、经桩管上的料口向桩管内放置钢筋笼及向桩管内灌入的砼;e、慢慢拔起桩管,随着桩管的拔起,桩管内的混凝土由于振动锤的震动力作用流入已拔起的桩管所产生的空间里,同时也填满了桩管外的八个齿形体,所形成的空腔里,成就了八个外齿;f、最后完全拔出桩管,在地基土中就会留有一个截面包括有桩身和外齿的齿轮型载体桩。
10.进一步的,柴油锤为沉管动力,柴油锤下端活动连接有夯板, 夯板下面与内夯管上端铰接,内夯管下端焊有圆形封口平板,内夯管外侧套装有外管,外管上端与钢丝绳连接,外管下端口焊有八个齿形体ⅱ,八个齿形体ⅱ沿外管周长径向分布,齿形体ⅱ截面为梯形,八个齿形体ⅰ为桩身上八个外齿的模具,外管上端设有进料口。
11.进一步的,柴油锤为沉管动力包括有如下步骤:a.首先将柴油锤、夯板和内夯管连接,并将内夯管插入外管中,然后落在桩点位置上并调正机架;b.将外管和内夯管同步沉入土中预定深度后,先拔出内夯管,在外管内投入填充料,再将内夯管压在外管内的填充料上,将外管拔出,能使外管内的填充料落入桩孔;
c.然后再用柴油锤将内管和外管再次同步打入土中,如此反复,直至满足三击贯入度要求;d.通过外管上部的进料口,将钢筋笼放入外管内,并往外管内灌入适量的混凝土,再将内夯管压在外管内的混凝土上;e.慢慢拔起外管,外管内的混凝土经外管下口流入外管和沿外管焊接的八个齿轮体所形成的空间;f.最后完全拔出外管后用振捣器将桩顶2~4米位置震实就会在地基土中留下一个截面包括有桩身和外齿的齿轮型载体桩。
12.进一步的,步骤c中要进行柴油锤与标准柱锤的等量换算,计算公式如下:n=212.3/[(zp
c
/a
s
)/y];公式中:n为标准柱锤一次的锤击力相当于柴油锤的锤击力次数;212.3为标准柱锤单位面积的锤击力212.3是个常数(来源于《载体桩技术标准 jgj/t135
‑
2018》中三击贯入度中一击的锤击能量:6米
×
3.5t
÷
[π(0.355
÷
2)2]=212.3;z为柴油锤锤击力折减系数,z取值范围为0.6~0.8,根据柴油锤的新旧程度取值,新的取大值,旧得取小值;y为外管下端口处土层的极限侧阻力修正系数,y取值1.3~3.9可根据具体地质情况用插入法,软土取小值,硬土取大值;a
s
为桩身与外齿的实际截面积;p
c
为用柴油锤的锤击能量查得的所用柴油锤的技术参数。
[0013]
本发明的有益效果是:1.解决现有技术没有侧阻力的计算内容也未考虑桩周土侧阻力的因素的问题,简便易行,使侧阻力和水平承载力都得到提高;2. 充分利用了桩周土的侧摩阻力,在竖向承载力值限定的条件下,有效减小桩径或减短桩的长度,大量节约了材料成本,大幅度降低工程造价,提高施工效率;3.填补了现有技术对桩周各土层摩擦力的利用空白,使桩周各土层的侧阻力得到了充分发挥,使很多劣质土层也能发挥出积极作用,并使单桩综合承载力提高;4.施工设备多样化,成桩质量高、承载力大、施工速度快,适应多变的地质条件,极大的拓展了施工范围。
附图说明
[0014]
图1为本发明结构示意图;图2为本发明图1的a
‑
a剖视图;图3为本发明震动锤施工设备结构示意图;图4为本发明震动锤施工方法示意图;图5为本发明柴油锤施工设备结构示意图;图6为本发明柴油锤施工方法示意图。
[0015]
图中:1.挤密土体;2.填充料夯实体;3.桩身;4.外齿;5.钢筋笼;6.振动锤;7.料斗;8.活动观察口;9.桩管;10.齿形体ⅰ;11.活瓣桩尖;12.标准柱锤;13.柴油锤;14.夯板;15.内夯管;16.外管;17.齿形体ⅱ;18.进料口。
具体实施方式
[0016]
如图1、图2所示,本发明一种八齿形载体桩,包括有桩端载体和桩身3,桩身3为砼柱体,桩身3内连接有钢筋笼5,桩身3外径连接有外齿4,所述的外齿4设有八个,八个外齿4以桩身3轴线为中心圆周均布,每个外齿4均在桩身3长度贯通,桩身3和外齿4截面形状为齿轮形,八个外齿4的截面形状相同,每个外齿4的截面形状均为梯形。桩端载体包括有挤密土体1和填充料夯实体2。
[0017]
所述的填充料夯实体2中的填充料包括卵石,碎石和水泥拌合物,所述的水泥拌合物又包括无水砼、干硬性砼、干硬性水泥砂浆、工地散落废弃的砼及碎块,合理选用填充料常会达到事半功倍的效果;外齿4提高桩侧摩擦面积,充分利用桩周土的侧阻力, 同时又加大了水平承载力方向的尺寸,使侧阻力和水平承载力同时得以提高。简单易行且一举两得,既可明显的提高桩的综合承载力,使混凝土对承载力的贡献率大大提高,又可使桩承载力与工程经济造价之比更高。
[0018]
外齿4过多会使齿间距离过小,土受剪力破坏而丧失侧阻力,外齿4过少又会使侧阻力得不到充分利用形成浪费;关于外齿4齿根部的宽度和截面形式,主要是考虑混凝土的流淌性和填充性,也考虑到混凝土强度能否满足侧阻力的要求。若呈翼片状虽能够增大侧摩阻力面积,但混凝土无法完全填充空隙,则强度也无法满足侧阻力的要求,也就不可能达到预期效果进一步的,外齿4尺寸是根据桩径的大小和齿间距以及组成条件所决定的,外齿4的尺寸与桩径d的关系式为:外齿4齿高h=d/4;外齿4齿根宽度b=d/5;外齿4齿顶宽度b=d/18;桩身3与外齿4的宽度d=2h+d;进一步的,桩身3与外齿4的实际截面积as的计算公式为:as=1.325(d/2)2π;充分地利用了桩周土层的摩擦阻力,可满足一般条件下的抗拔力要求,若有更大的抗拔力需求时,在桩端处再用混凝土夯出一个扩大头即可。前提是桩身钢筋笼的配比必须满足抗拔要求。
[0019]
在《载体桩技术标准》(4.2.3—1)与(4.2.3—2)计算式中,只给出了桩端承载力特征值的计算公式,而侧阻力的计算方法缺失。为了使设计和施工有据可依并与《载体桩技术标准 jgj/t135—2018》对接,竖向承载力计算公式为:r
a
=f
a
*a
e
μ∑q
sik
l
i
/k公式中:r
a
为载体桩单桩竖向受压承载力特征值;f
a
为经深度修正后的载体桩持力层地基承载力特征值;a
e
为载体等效计算面积,f
a
*a
e
是《载体桩技术标准》中(4.2.3—1)公式;μ为实际桩身周长,包括八个外齿的边长, μ的计算公式为:μ=2dπ;q
sik
为桩侧第i层土极限侧阻力标准值,可按《建筑桩基技术规范 jgj94—2008》表5.3.5—1取值;l
i
为第i层土的厚度;k为安全系数,一般取k=2。
[0020]
本发明所提供的一种八齿形载体桩,不但填补了以往对桩周各土层摩擦力的利用空白,使桩周各土层的侧阻力得到了充分发挥,还可使很多劣质土层也能发挥出积极作用,
并使单桩综合承载力达到了一个新的高度且简单易行。
[0021]
本发明的施工方法是采用振动锤6或柴油锤13为动力,分别采用不同的施工方式,实现八齿形载体桩的施工。为了预防施工中可能出现的环保问题,视地质条件可采用引孔的方式来解决施工中可能产生的振动问题,其次优先选用振动锤作为沉管成孔的动力,因其不会产生废气排放和大的噪音问题一种八齿形载体桩的施工方法,采用振动锤6和标准柱锤12或柴油锤13为沉管动力。
[0022]
如图3、图4所示,采用振动锤6为沉管动力,振动锤6下端刚性连接有桩管9,桩管9上部设有料斗7和活动观察口8,桩管9下端通过铰链连接活瓣桩尖11,沿管外周径向焊有八个齿形体ⅰ10作为桩身3上八个外齿4的模具,齿形体ⅰ10截面为梯形,活瓣桩尖11为截圆锥,活瓣桩尖11顶面与桩管9等径,活瓣桩尖11的活瓣由四瓣组成,活瓣合拢后形成桩尖有利于桩管顺利沉入土中,并可防止泥水进入桩管内。振动锤6内连接有标准柱锤12,标准柱锤12通过振动锤6的中孔进入桩管9内,标准柱锤12为钢制圆柱体,标准柱锤12上端与钢丝绳连接,标准柱锤12下端为平底或截锥体。料斗7是填充料的投入、钢筋笼的设置、砼的灌入等物料投入的主要通道;活动观察口8是观察和测量三击贯入度的窗口。标准柱锤12锤重3.5t,采用非标准柱锤12施工时,可通过调整标准柱锤12的提升高度,确保锤端单位面积上的冲击能量与标准三击贯入度测量时的冲击能量相同。
[0023]
进一步的,振动锤6为沉管动力包括有如下步骤:a、做好振动锤6与桩管9和活瓣桩尖11的连接,并将活瓣桩尖合拢,对准桩点;b、将桩管9沉到预定深度,通过桩管9上部的料口7投入填充料,再将桩管拔出,使桩端活瓣桩尖11打开,填充料落入桩孔内;c、然后用标准柱锤12通过振动锤6的中孔进入桩管9中,对填充料进行夯击,填充料夯实后成为填充料夯实体2,最后通过桩管9上部的观察口8测量三击贯入度是否达到要求,如此反复直至达到要求;d、经桩管9上的料口7向桩管9内放置钢筋笼5及向桩管9内灌入的砼;e、慢慢拔起桩管9,随着桩管9的拔起,桩管9内的混凝土由于振动锤6的震动力作用流入已拔起的桩管9所产生的空间里,同时也填满了桩管外的八个齿形体10,所形成的空腔里,成就了八个外齿4;f、最后完全拔出桩管9,在地基土中就会留有一个截面包括有桩身3和外齿4的齿轮型载体桩。
[0024]
用此方法施工,可用一台设备完成全部工作,使工艺得到简化、效率得到提高并可很好的达到提高单桩综合承载力的预期效果。
[0025]
如图3、图4所示,采用柴油锤13为沉管动力,柴油锤13下端活动连接有夯板14, 夯板14下面与内夯管15上端铰接,内夯管15下端焊有圆形封口平板,内夯管15外侧套装有外管16,外管16上端与钢丝绳连接,外管16下端口焊有八个齿形体ⅱ17,八个齿形体ⅱ17沿外管周长径向分布,齿形体ⅱ17截面为梯形,八个齿形体ⅰ10为桩身3上八个外齿4的模具,外管16上端设有进料口18。内夯管15下端焊有圆形封口平板,直径比外管16内径小20~40毫米,长度比外管16短50~100毫米。外管16上端设有进料口18是物料投入的重要通道,也是简化工艺提高效率的重要举措。
[0026]
进一步的,柴油锤13为沉管动力包括有如下步骤:a.首先将柴油锤13、夯板14和内夯管15连接,并将内夯管15插入外管16中,然后落在桩点位置上并调正机架;b.将外管16和内夯管15同步沉入土中预定深度后,先拔出内夯管15、在外管16内投入填充料,再将内夯管15压在外管16内的填充料上,将外管16拔出,能使外管16内的填充料落入桩孔;c.然后再用柴油锤13将内管15和外管16再次同步打入土中,如此反复,直至满足三击贯入度要求;d.通过外管16上部的进料口18,将钢筋笼5放入外管16内,并往外管16内灌入时量的混凝土,再将内夯管15压在外管16内的混凝土上;e.慢慢拔起外管16,外管16内的混凝土经外管16下口流入外管16和沿外管16焊接的八个齿轮体所形成的空间;f.最后完全拔出外管16后用振捣器将桩顶2~4米位置震实就会在地基土中留下一个截面包括有桩身3和外齿4的齿轮型载体桩。
[0027]
进一步的,步骤c中要进行柴油锤13与标准柱锤12的等量换算,计算公式如下:n=212.3/[(zpc/as)/y];公式中:n为标准柱锤12一次的锤击力相当于柴油锤13的锤击力次数;212.3为标准柱锤12单位面积的锤击力;z为柴油锤13锤击力折减系数,z取值范围为0.6~0.8,根据柴油锤13的新旧程度取值,新的取大值,旧得取小值;y为外管下端口处土层的极限侧阻力修正系数,y取值1.3~3.9,可根据具体地质情况用插入法,软土取小值,硬土取大值;a
s
为桩身3与外齿4的实际截面积;p
c
为用柴油锤13的锤击能量查得的所用柴油锤的技术参数。
[0028]
用此方法施工,同样也只用一台设备,完成全部的施工作业。简化工艺、提高效率,达到提高单桩综合承载力的效果。同时它还具有三击贯入度受客观影响小,比较直观,便于监督的优点。
[0029]
本发明一种多齿载体桩及其施工方法中施工设备多样化,成桩质量高、承载力大、施工速度快,适应多变的地质条件,极大的拓展了施工范围。
再多了解一些
本文用于企业家、创业者技术爱好者查询,结果仅供参考。