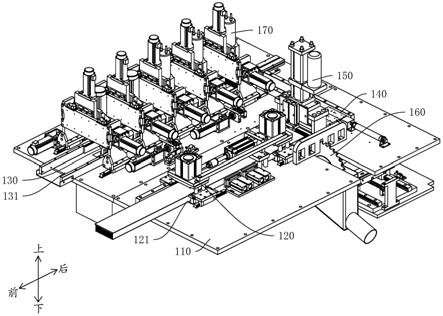
1.本发明涉及散热片加工装置领域,特别涉及一种散热片加工一体机。
背景技术:
2.随着空调行业的发展,传统定频空调因为能耗高,噪音大从而逐渐被直流变 频空调替代,而变频空调模块中igbt,整流桥等都是大功率器代,发热量大, 需要散热片辅助散热才能做设备正常工作。在散热片的生产加工过程中,主要是 工作人员将散热片原料放入切断机进而得到散热片单元,接着根据客户要求,对 散热片单元分别放入冲压机、冲孔机和攻牙机进行进一步的手动加工,但是在进 一步的加工过程中,工作人员需要不断重复进行上料、定位以及下料的工序,工 序重复,生产效率低,所需人力成本高,因此,人们为了提高生产效率,在孔位 加工时往往采用多个孔位加工的装置对工件进行加工,并使用机械夹紧臂对工件 进行夹紧
‑
提起
‑
移送,但是在传送的过程中,容易导致工件的掉落,延长生产周 期。
技术实现要素:
3.本发明目的在于提供一种散热片加工一体机,以解决现有技术中所存在的一 个或多个技术问题,至少提供一种有益的选择或创造条件。
4.本发明解决其技术问题的解决方案是:一种散热片加工一体机,包括:工作 台,所述工作台上设置有:第一输送装置,其具有第一输送道和具有第一夹紧构 件的第一移料组件,所述第一移料组件可带动所述第一夹紧构件沿所述第一输送 道来回移动;第二输送装置,其具有第二输送道和具有第二夹紧构件的第二移料 组件,所述第二输送道上具有避让空间,所述第二移料组件位于所述避让空间的 下方,所述第二移料组件可带动所述第二夹紧构件沿所述第二输送道来回移动, 所述第二夹紧构件可进出于所述避让空间;输送切换装置,所述输送切换装置具 有将所述第一输送道传送末端上的工件推送至所述第二输送道传送始端的推送 端;冲压装置,其设置在所述第一输送道的旁侧,所述冲压装置包括上下驱动构 件和具有冲头的冲边组件,所述第一输送道上设有落料通道,所述上下驱动构件 设置在所述第一输送道的上方,所述上下驱动构件可以带动所述冲边组件上下移 动,并使得所述冲头进入或退出所述落料通道;切割装置,其设置在所述第一输 送道的旁侧,所述切割装置包括切料刀,所述切料刀可沿垂直于所述第一输送道 的输送方向进行来回移动;孔位加工装置,其设置在所述第二输送道的旁侧并位 于所述第二输送装置的上方,多个所述孔位加工装置沿所述第二输送道的输送方 向间隔设置,所述孔位加工装置包括移动机构和加工端,所述移动机构设置在所 述第二输送道的上方,所述加工端设置在所述移动机构上,多个所述第二夹紧构 件阵列设置在所述第二移料组件上,相邻两个所述第二夹紧构件的间距与相邻两 个所述孔位加工装置的间距相同。
5.该技术方案至少具有如下的有益效果:使用者将原料放入第一输送道上,第 一夹紧构件夹紧原料,并通过第一移料组件带动第一夹紧构件沿第一输送道的输 送方向移动,
待原料移送至冲压装置处,上下驱动构件带动冲边组件下移,使得 冲头下移对原料进行加工并进入至落料通道内,实现对工件的冲压,待工件移送 至切割装置处,切料刀对第一输送道上的原料进行切断成工件,待工件移至第一 输送道传送末端,输送切换装置将该工件推送至第二输送道传送始端的推送端, 工件移动至对应的孔位加工装置的下方,移动机构带动加工端进行移动,并对工 件进行孔位加工,加工完毕后,多个第二夹紧构件伸出避让空间分别对多个工件 进行夹紧后,第二移料组件带动多个第二夹紧构件继续往第二输送道的输送方向 移动,使得工件移动至下一个孔位加工装置,该散热片加工一体机使得原料可以 直接通过冲压、切割、孔位加工工序,形成客户所需的工件,大幅提高工件加工 的效率,降低生产周期,生产量大,减少人力成本,而且,第二移料组件位于第 二输送道的下方,第二夹紧构件可进出于避让空间,防止工件掉落,提高工件移 动稳定性,提高生产效益。
6.作为上述技术方案的进一步改进,所述第一移料组件还包括推料气缸,所述 推料气缸设置在所述工作台上,所述第一夹紧构件包括第一滑块和第一压料气 缸,所述第一滑块滑动设置在工作台上,所述推料气缸的驱动端与所述第一滑块 相连,所述推料气缸可带动所述第一滑块沿所述第一输送道进行来回滑动,所述 第一压料气缸设置在所述第一滑块上并位于所述第一输送道的上方,所述第一压 料气缸的驱动端向下延伸并设有压料板,所述第一压料气缸可驱动所述压料板上 下移动。第一压料气缸设置在第一滑块上,需要进料时,第一压料气缸向下驱动 压料板压紧原料,接着,推料气缸带动所述第一滑块沿第一输送道的输送方向滑 动,使得第一压料气缸夹紧原料并向输送方向移动,待进料完毕,第一压料气缸 向上驱动压料板以解除对原料的夹紧,推料气缸带动第一压料气缸往回移动,循 环往复,以实现间歇上料,方便后续对原料的加工,结构可靠。
7.作为上述技术方案的另一种改进,所述上下驱动构件为增压缸,所述冲边组 件还包括自上而下设置的上模、弹簧和退料板,所述第一输送道的两侧向上凸起 形成下模,所述落料通道位于所述下模的端面,所述上模的底面设有第一导柱和 所述冲头,所述第一导柱向下延伸并穿过所述退料板,所述弹簧的一端连接所述 上模的底面,所述弹簧的另一端连接所述退料板的顶面,所述退料板可沿所述第 一导柱进行上下运动,所述退料板的端面上设有冲压通道,所述冲压通道和所述 落料通道均与所述冲头的形状、位置相对应,所述冲头伸入所述冲压通道内,所 述增压缸带动所述冲边组件向下移动时,所述弹簧呈压缩状态,所述退料板的底 面与所述下模的顶面相抵,所述冲头穿出所述冲压通道并进入所述落料通道。增 压缸带动冲边组件向下移动,使得退料板和下模相抵,增压缸继续带动上模和弹 簧下压,使得上模和退料板的竖直距离缩小,弹簧不断压缩,冲头穿出冲压通道 并作用于工件后,冲头进入至落料通道,使得冲压废料可以顺利于工件分离并排 出,冲压完毕后,增压缸带动上模向上移动,冲头也随上模上移,因为弹簧处于 压缩状态,所以退料板始终受到向下的压力,使得退料板始终与下模相抵,冲头 退出落料通道和工件,并进入到冲压通道内,增压缸继续带动上模上升,退料板 与下模分离,整个过程中,防止退料板和冲头晃动,提高结构刚度和冲压精度。
8.作为上述技术方案的另一种改进,所述切割装置还包括旋转电机和直线滑 台,所述直线滑台滑动设置在所述工作台上并位于第一输送道的下方,所述旋转 电机设置在所述直线滑台上,所述第一输送道上设有切料间隙,所述切料刀伸出 所述切料间隙处,所述切料刀的周向设有多个刀片,所述直线滑台可驱动所述旋 转电机沿垂直于所述第一输送
道的方向进行来回移动,所述旋转电机驱动所述切 料刀进行旋转,所述切料刀的旋转轴线与其中心线相互重合。工件原料具有一定 厚度,通过旋转切料刀,并带动切料刀沿垂直于第一输送道的方向进行切割,可 以提高切割强度和效果,并且切料刀的旋转轴位于第一输送道的下方,可以降低 设备高度,充分利用安装空间,紧凑安装,提高美观度。
9.作为上述技术方案的进一步改进,所述切割装置还包括定位块和第二压料气 缸,所述定位块和所述第二压料气缸均设置在所述工作台上,所述定位块和所述 第二压料气缸分别设置在所述第一输送道的两侧,所述定位块和所述第二压料气 缸均位于所述切料刀的前侧,所述第二压料气缸的驱动端上设有顶板,所述第二 压料气缸可驱动所述顶板朝所述第一输送道的方向移动。在进行原料的切割前, 第二压料气缸驱动顶板向第一输送道的方向移动,使得顶板将原料压向定位块, 实现原料在水平方向上的定位,防止切料刀切割原料时带动原料晃动,提高切割 精度,并且减少原料变形,防止原料水平方向上发生弯曲、断裂的现象。
10.作为上述技术方案的另一种改进,所述第二移料组件还包括送料气缸和第二 滑块,所述送料气缸设置在所述工作台上,所述第二滑块滑动设置在所述工作台 的底面,所述送料气缸的驱动端与所述第二滑块相连,所述送料气缸可带动所述 第二滑块沿所述第二输送道进行来回滑动,多个所述第二夹紧构件间隔设置在所 述第二滑块上,所述第二夹紧构件的数量比所述孔位加工装置的数量少一个。上 一个孔位加工装置给对应的工件加工完毕后,第二夹紧构件夹取第二输送道上的 工件,送料气缸驱动第二滑块沿第二输送道的输送方向滑动,使得多个第二夹紧 构件上的工件可以同时往下一个孔位加工装置的方向进行传送,实现工件下一步 的加工,提高运输效率,并且,第二夹紧构件的数量比孔位加工装置的数量少一 个,使得运输效率在最大化的同时,降低空间占用,降低生产成本。
11.作为上述技术方案的进一步改进,所述第二夹紧构件包括夹料气缸、齿条和 夹臂,所述夹料气缸设置在所述第二滑块上,所述齿条竖直设置在所述夹料气缸 向上延伸的驱动端上,所述齿条相对的两侧面上均设有齿牙,所述齿牙的朝向于 所述第二输送道的设置方向一致,所述夹臂的一端设有连接块,所述连接块呈圆 柱齿轮状,所述连接块旋转连接在所述第二滑块上,所述连接块的旋转轴线与所 述连接块的中心线相重合,两个所述夹臂分别啮合设置在所述齿条具有所述齿牙 的两侧,所述夹料气缸驱动所述齿条向下移动时,两个所述夹臂远离所述连接块 的一端相互靠近并可进入所述避让空间。夹料气缸驱动齿条向下移动时,两个夹 臂的顶端相互靠近进入避让空间,实现对工件的夹紧,夹料气缸驱动齿条向上移 动时,两个夹臂的顶端相互远离退出避让空间,解除对工件的夹紧,使得夹臂在 沿第二输送道往回转移的时候,防止夹臂与工件之间的干涉,结构可靠,因为工 件承托在第二输送道上,所以在夹持过程中,该夹臂可以直接拨弄工件,工件的 移动效果好,也可以防止工件因惯性发生位置偏移,提高位移稳定性,防止工件 掉落现象,降低设计成本。
12.作为上述技术方案的另一种改进,所述第二输送道的两侧均围有导向台,两 个所述导向台相互靠近的侧壁沿所述第二输送道的方向设有承托块,所述第二输 送装置还包括定位组件,所述定位组件包括定位气缸、第二导柱和固定板,所述 定位气缸设置在所述工作台上,所述定位气缸的驱动端上设有承托板,所述定位 气缸可驱动所述承托板进行上下活动,所述第二导柱设置在所述承托板的顶面, 所述导向台和所述工作台之间贯穿有定
位通道,所述第二导柱向上延伸并穿过所 述定位通道,所述固定板设置在所述第二导柱的顶端,所述固定板的底面设有向 下延伸的定位销,所述承托块的顶面设有与所述定位销位置和形状匹配的定位 孔,多个所述定位组件与多个所述孔位加工装置的数量和位置一一对应。第二夹 紧构件夹紧工件并移至下一工位后,定位气缸驱动所述承托板向下移动,第二导 柱和其上的固定板也随承托板向下移动,定位销穿过工件的孔位并进入定位孔 内,完成定位后可进行对工件的孔位加工,提高了对工件的承托和定位能力,防 止工件变形,提高加工精度,结构简单可靠,并且,提高空间利用率,减少对第 二夹紧构件和孔位加工装置的空间占用,提高美观度。
13.作为上述技术方案的另一种改进,所述输送切换装置还包括传送道,所述传 送道、所述第一输送道和所述第二输送道均水平设置在所述工作台上,所述传送 道的始末两端均与所述第一输送道和第二输送道相连通,所述传送道分别与所述 第一输送道和第二输送道相垂直,所述推送端包括均水平设置在工作台上的第一 推送气缸和第二推送气缸,所述第一推送气缸位于所述第一输送道传送末端的旁 侧,所述第一推送气缸的驱动端向所述传送道的传送方向延伸,所述第二推送气 缸位于所述传送道传送末端的旁侧,所述第二推送气缸的驱动端向所述第二输送 道的传送方向延伸。第一推送气缸将堆积在第一输送道末端的工件推送至传送道 上,第二推送气缸将挤至传送道末端的工件推向第二输送道上,适应不同设置空 间的设备,为工件运输至第二输送道上提供推送力,方便工人监测,减少堆料。
14.作为上述技术方案的另一种改进,所述移动机构包括前后驱动构件、左右驱 动构件和上下驱动构件,以第二传送道的输送方向为前,所述前后驱动构件设置 在所述工作台上,所述前后驱动构件上设有可沿前后方向移动的第一安装块,所 述左右驱动构件设置在所述第一安装块上,所述左右驱动构件上设有可沿左右方 向移动的第二安装块,所述上下驱动构件设置在所述第二安装块上,所述加工端 设置在所述上下驱动构件的下端,所述上下驱动构件可驱动所述加工端上下移 动。加工端可以是钻孔、倒角或攻丝等刀具,加工端通过前后驱动构件、左右驱 动构件和上下驱动构件,实现其可以在空间内进行三位移动,使得加工端可以在 工件的表面上进行加工,提高使用功能性和自动化效果,提高生产效率。
附图说明
15.为了更清楚地说明本发明实施例中的技术方案,下面将对实施例描述中所需 要使用的附图作简单说明。显然,所描述的附图只是本发明的一部分实施例,而 不是全部实施例,本领域的技术人员在不付出创造性劳动的前提下,还可以根据 这些附图获得其他设计方案和附图。
16.图1是本发明一实施例提供的散热片加工一体机的结构图;
17.图2是本发明一实施例提供的第一输送装置的结构图;
18.图3是本发明一实施例提供的冲压装置的结构图;
19.图4是本发明一实施例提供的切割装置的结构图;
20.图5是本发明一实施例提供的孔位加工装置的结构图;
21.图6是本发明一实施例提供的散热片加工一体机的结构图;
22.图7是本发明一实施例提供的第二输送装置和定位组件结构的正视图;
23.图8是图7结构沿a
‑
a方向的剖视图;
24.图9是本发明一实施例提供的散热片加工一体机的上视图。
25.附图中:110
‑
工作台、120
‑
第一输送装置、121
‑
第一输送道、130
‑
第二输送 装置、131
‑
第二输送道、140
‑
输送切换装置、150
‑
冲压装置、160
‑
切割装置、170
‑ꢀ
孔位加工装置、210
‑
推料气缸、220
‑
第一滑块、230
‑
第一压料气缸、240
‑
定位块、 250
‑
第二压料气缸、260
‑
切料间隙、310
‑
增压缸、320
‑
上模、330
‑
弹簧、340
‑ꢀ
退料板、350
‑
下模、360
‑
第一导柱、370
‑
冲头、410
‑
切料刀、420
‑
旋转电机、430
‑ꢀ
直线滑台、510
‑
前后驱动构件、520
‑
左右驱动构件、530
‑
上下驱动构件、540
‑ꢀ
加工端、610
‑
送料气缸、620
‑
第二滑块、630
‑
第二夹紧构件、640
‑
避让空间、710
‑ꢀ
夹料气缸、720
‑
夹臂、730
‑
定位气缸、740
‑
承托板、750
‑
第二导柱、760
‑
固定板、 770
‑
定位销、810
‑
齿条、820
‑
连接块。
具体实施方式
26.以下将结合实施例和附图对本发明的构思、具体结构及产生的技术效果进行 清楚、完整地描述,以充分地理解本发明的目的、特征和效果。显然,所描述的 实施例只是本发明的一部分实施例,而不是全部实施例,基于本发明的实施例, 本领域的技术人员在不付出创造性劳动的前提下所获得的其他实施例,均属于本 发明保护的范围。另外,文中所提到的所有连接关系,并非单指构件直接相接, 而是指可根据具体实施情况,通过添加或减少连接辅件,来组成更优的连接结构。 本发明中的各个技术特征,在不互相矛盾冲突的前提下可以交互组合。
27.在本发明的描述中,需要理解的是,涉及到方位描述,例如上、下、前、后、 左、右等指示的方位或位置关系为基于附图所示的方位或位置关系,仅是为了便 于描述本发明和简化描述,而不是指示或暗示所指的装置或元件必须具有特定的 方位、以特定的方位构造和操作,因此不能理解为对本发明的限制。
28.在本发明的描述中,若干的含义是一个或者多个,多个的含义是两个以上, 大于、小于、超过等理解为不包括本数,以上、以下、以内等理解为包括本数。 如果有描述到第一、第二只是用于区分技术特征为目的,而不能理解为指示或暗 示相对重要性或者隐含指明所指示的技术特征的数量或者隐含指明所指示的技 术特征的先后关系。
29.本发明的描述中,除非另有明确的限定,设置、安装、连接等词语应做广义 理解,所属技术领域技术人员可以结合技术方案的具体内容合理确定上述词语在 本发明中的具体含义。
30.参照图1、图3、图4、图5和图6,散热片加工一体机包括工作台110,工 作台110上设置有:第一输送装置120,其具有第一输送道121和具有第一夹紧 构件的第一移料组件,第一移料组件可带动第一夹紧构件沿第一输送道121来回 移动;第二输送装置130,其具有第二输送道131和具有第二夹紧构件630的第 二移料组件,第二输送道131上具有避让空间640,第二移料组件位于第二输送 道131下方,第二移料组件可带动第二夹紧构件630沿第二输送道131来回移动, 第二夹紧构件630可进出于避让空间640;输送切换装置140,输送切换装置140 具有将第一输送道121传送末端上的工件推送至第二输送道131传送始端的推送 端;冲压装置150,其设置在第一输送道121的旁侧,冲压装置150包括上下驱 动构件
530和具有冲头370的冲边组件,第一输送道121上设有落料通道,上下 驱动构件530设置在第一输送道121的上方,上下驱动构件530可以带动冲边组 件上下移动,并使得冲头370进入或退出落料通道;切割装置160,其设置在第 一输送道121的旁侧,切割装置160包括切料刀410,切料刀410可沿垂直于第 一输送道121的输送方向进行来回移动;孔位加工装置170,其设置在第二输送 道131的旁侧并位于第二输送装置130的上方,多个孔位加工装置170沿第二输 送道131的输送方向间隔设置,孔位加工装置170包括移动机构和加工端540, 移动机构设置在第二输送道131的上方,加工端540设置在移动机构上,多个第 二夹紧构件630阵列设置在第二移料组件上,相邻两个第二夹紧构件630的间距 与相邻两个孔位加工装置170的间距相同。
31.原料放置在第一输送道121上,然后,可以是通过第一移料组件实现间歇上 料,待原料越过切割装置160并移送至冲压装置150处,冲压装置150对原料进 行冲边并压紧,实现原料定位,接着,切割装置160将原料切割成一份分的工件, 并通过输送切换装置140将工件传送至第二输送道131,第二移料组件将工件间 歇地传送至多个孔位加工装置170处,孔位加工装置170则对移送至对应位置上 的工件进行加工。使用者使得原料可以直接通过冲压、切割、孔位加工工序,形 成客户所需的工件,提高工件加工的效率,降低生产周期,生产量大,减少人力 成本,提高生产效益。实际上,冲压装置150可以沿第一输送道121,设置在切 割装置160的上游或下游处。另外,设置在工作台110下的机壳可以呈全包围式, 机壳下部整体做斜面集屑箱,方便排屑
32.另外,在一些实施例中,第一移料组件还包括推料气缸210,推料气缸210 设置在工作台110上,第一夹紧构件包括第一滑块220和第一压料气缸230,第 一滑块220滑动设置在工作台110上,推料气缸210的驱动端与第一滑块220 相连,推料气缸210可带动第一滑块220沿第一输送道121进行来回滑动,第一 压料气缸230设置在第一滑块220上并位于第一输送道121的上方,第一压料气 缸230的驱动端向下延伸并设有压料板,第一压料气缸230可驱动压料板上下移 动。
33.具体的,因为在对工件进行后续加工的阶段中,需要在上料时进行停顿,使 得该设备可以在停顿的时间内,对散热器原料进行切割和冲压等工序,第一压料 气缸230设置在第一滑块220上,需要进料时,第一压料气缸230向下驱动压料 板压紧原料,接着,推料气缸210带动第一滑块220沿第一输送道121的输送方 向滑动,使得第一压料气缸230夹紧原料并向输送方向移动,待进料完毕,第一 压料气缸230向上驱动压料板以解除对原料的夹紧,推料气缸210带动第一压料 气缸230往回移动,循环往复,以实现间歇上料,方便后续对原料的加工,结构 可靠。在实际应用中,第一夹紧构件可以设有两个,两个第一夹紧构件之间通过 连接杆来连接,使得推料气缸210可以同时作用在两个第一夹紧构件上,并且第 一加紧构件同时对原料进行夹紧,可以提高进料稳定性,减少打滑。
34.为了提高冲压精度,在一些实施例中,上下驱动构件530为增压缸310,冲 边组件还包括自上而下设置的上模320、弹簧330和退料板340,第一输送道121 的两侧向上凸起形成下模350,落料通道位于下模350的端面,上模320的底面 设有第一导柱360和冲头370,第一导柱360向下延伸并穿过退料板340,弹簧 330的一端连接上模320的底面,弹簧330的另一端连接退料板340的顶面,退 料板340可沿第一导柱360进行上下运动,退料板340的端面上设有冲压通道, 冲压通道和落料通道均与冲头370的形状、位置相对应,冲头370伸入冲
压通道 内,增压缸310带动冲边组件向下移动时,弹簧330呈压缩状态,退料板340 的底面与下模350的顶面相抵,冲头370穿出冲压通道并进入落料通道。
35.具体的,增压缸310带动冲边组件向下移动,使得退料板340和下模350 相抵,增压缸310继续带动上模320和弹簧330下压,使得上模320和退料板 340的竖直距离缩小,弹簧330不断压缩,冲头370穿出冲压通道并作用于工件 后,冲头370进入至落料通道,使得冲压废料可以顺利于工件分离并排出,冲压 完毕后,增压缸310带动上模320向上移动,冲头370也随上模320上移,因为 弹簧330处于压缩状态,所以退料板340始终受到向下的压力,使得退料板340 始终与下模350相抵,冲头370退出落料通道和工件,并进入到冲压通道内,增 压缸310继续带动上模320上升,退料板340与下模350分离,整个过程中,防 止退料板340和冲头370晃动,提高结构刚度和冲压精度。实际上,可以是在切 割装置160对原料进行切割后,增压缸310才开始上移,提高切割时,原料的定 位效果,提高切割精度。
36.另外,在一些实施例中,切割装置160还包括旋转电机420和直线滑台430, 直线滑台430滑动设置在工作台110上并位于第一输送道121的下方,旋转电机 420设置在直线滑台430上,第一输送道121上设有切料间隙260,切料刀410 伸出切料间隙260处,切料刀410的周向设有多个刀片,直线滑台430可驱动旋 转电机420沿垂直于第一输送道121的方向进行来回移动,旋转电机420驱动切 料刀410进行旋转,切料刀410的旋转轴线与其中心线相互重合。工件原料具有 一定厚度,通过旋转切料刀410,并带动切料刀410沿垂直于第一输送道121的 方向进行切割,可以提高切割强度和效果,并且切料刀410的旋转轴位于第一输 送道121的下方,可以降低设备高度,充分利用安装空间,紧凑安装,提高美观 度。而且,进一步的,在一些实施例中,切割装置160还包括定位块240和第二 压料气缸250,定位块240和第二压料气缸250均设置在工作台110上,定位块 240和第二压料气缸250分别设置在第一输送道121的两侧,定位块240和第二 压料气缸250均位于切料刀410的前侧,第二压料气缸250的驱动端上设有顶板, 第二压料气缸250可驱动顶板朝第一输送道121的方向移动。在进行原料的切割 前,第二压料气缸250驱动顶板向第一输送道121的方向移动,使得顶板将原料 压向定位块240,实现原料在水平方向上的定位,防止切料刀410切割原料时带 动原料晃动,提高切割精度,并且减少原料变形,防止原料水平方向上发生弯曲、 断裂的现象。另外,切割装置160还可以包括集屑罩,集屑罩设置在直线滑台 430上,集屑罩包覆在切料刀410的下部,并且在底部沿切料刀410的转动方向, 斜向下的设有出屑口,方便排屑,切割装置160还可以设有加强挡板,加强挡板 设置在工作台110上并连接切料间隙260的两侧,提高工作台110强度,防止切 屑飞溅。
37.为了提高生产效率,降低空间占用,在一些实施例中,第二移料组件还包括 送料气缸610和第二滑块620,送料气缸610设置在工作台110上,第二滑块620 滑动设置在工作台110的底面,送料气缸610的驱动端与第二滑块620相连,送 料气缸610可带动第二滑块620沿第二输送道131进行来回滑动,多个第二夹紧 构件630间隔设置在第二滑块620上,第二夹紧构件630的数量比孔位加工装置 170的数量少一个。上一个孔位加工装置170给对应的工件加工完毕后,第二夹 紧构件630夹取第二输送道131上的工件,送料气缸610驱动第二滑块620沿第 二输送道131的输送方向滑动,使得多个第二夹紧构件630上的工件可以同时往 下一个孔位加工装置170的方向进行传送,实现工件下一步的加工,多个第二夹 紧构件630使得可以同时作用多个工件,提高生产效率,并且,因为最后一个孔 位加工装置170
工位的工件,可以在其下一个工件的运输过程中,沿第二输送道 131的方向被自动挤出,因此第二夹紧构件630的数量比孔位加工装置170的数 量少一个,使得运输效率在最大化的同时,降低空间占用,降低生产成本。
38.并且,在一些实施例中,第二夹紧构件630包括夹料气缸710、齿条810和 夹臂720,夹料气缸710设置在第二滑块620上,齿条810竖直设置在夹料气缸 710向上延伸的驱动端上,齿条810相对的两侧面上均设有齿牙,齿牙的朝向于 第二输送道131的设置方向一致,夹臂720的一端设有连接块820,连接块820 呈圆柱齿轮状,连接块820旋转连接在第二滑块620上,连接块820的旋转轴线 与连接块820的中心线相重合,两个夹臂720分别啮合设置在齿条810具有齿牙 的两侧,夹料气缸710驱动齿条810向下移动时,两个夹臂720远离连接块820 的一端相互靠近并可进入避让空间640。工件在第二输送道131上运输,避让空 间640设置在第二输送道131上,夹料气缸710驱动齿条810向下移动时,两个 夹臂720的顶端相互靠近进入避让空间640,实现对工件的夹紧,夹料气缸710 驱动齿条810向上移动时,两个夹臂720的顶端相互远离退出避让空间640,解 除对工件的夹紧,使得夹臂720在沿第二输送道131往回转移的时候,防止夹臂 720与工件之间的干涉,结构可靠。需要说明的是,因为工件承托在第二输送道 131上,在夹持过程中,工件朝向与运输方向相反的面上具有一夹臂720,该夹 臂720可以直接拨弄工件,工件的移动效果好,夹臂720向上伸出避让空间640, 对比于在上方夹持工件的结构,可以防止夹臂720晃动导致的工件掉落现象,并 且,无需使用上下驱动的结构对夹臂720进行移动,降低设计成本,而且,工件 朝向与运输方向相同的面上具有的夹臂720,可以在工件移动的过程中,防止工 件因惯性原因发生位置偏移,提高位移稳定性。实际上,在孔位加工时,夹持装 置可以始终处于夹紧状态,可以防止工件滑移,提高加工稳定性。另外,在夹臂 720靠近工件的侧面上部,可以设有限位台,使得限位台的底面可以和工件的表 面贴合,防止工件抖动,提高工件移动、加工时的稳定性。
39.此外,为提高工件在孔位加工过程中的定位效果,在一些实施例中,第二输 送道131的两侧均围有导向台,两个导向台相互靠近的侧壁沿第二输送道131 的方向设有承托块,第二输送装置130还包括定位组件,定位组件包括定位气缸 730、第二导柱750和固定板760,定位气缸730设置在工作台110上,定位气 缸730的驱动端上设有承托板740,定位气缸730可驱动承托板740进行上下活 动,第二导柱750设置在承托板740的顶面,导向台和工作台110之间贯穿有定 位通道,第二导柱750向上延伸并穿过定位通道,固定板760设置在第二导柱 750的顶端,固定板760的底面设有向下延伸的定位销770,承托块的顶面设有 与定位销770位置和形状匹配的定位孔,多个定位组件与多个孔位加工装置170 的数量和位置一一对应。实际上,散热片的顶板置于两个承托块的顶面上,散热 片的鳍片则设置在顶板的底面,鳍片的底端向下延伸并和第二输送道131相抵, 第二夹紧构件630夹紧工件并移至下一工位后,定位气缸730驱动承托板740 向下移动,第二导柱750和其上的固定板760也随承托板740向下移动,定位销 770穿过工件的孔位并进入定位孔内,完成定位后可进行对工件的孔位加工,提 高了对工件的承托和定位能力,防止工件变形,提高加工精度,结构简单可靠, 并且,提高空间利用率,减少对第二夹紧构件630和孔位加工装置170的空间占 用,提高美观度。需要说明的是,承托板740上可以设有两个第二导柱750,两 个第二导柱750到定位气缸730的距离相同,提高定位过程稳定性。
40.此外,在一些实施例中,输送切换装置140还包括传送道,传送道、第一输 送道121
和第二输送道131均水平设置在工作台110上,传送道的始末两端均与 第一输送道121和第二输送道131相连通,传送道分别与第一输送道121和第二 输送道131相垂直,推送端包括均水平设置在工作台110上的第一推送气缸和第 二推送气缸,第一推送气缸位于第一输送道121传送末端的旁侧,第一推送气缸 的驱动端向传送道的传送方向延伸,第二推送气缸位于传送道传送末端的旁侧, 第二推送气缸的驱动端向第二输送道131的传送方向延伸。具体的,第一推送气 缸将堆积在第一输送道121末端的工件推送至传送道上,第二推送气缸将挤至传 送道末端的工件推向第二输送道131上,适应不同设置空间的设备,为工件运输 至第二输送道131上提供推送力,方便工人监测,减少堆料。实际上,在第二输 送道131的始端可以设有拦截构件,拦截构件包括设置在工作台110上的拦截气 缸和拦截杆,拦截杆水平设置在拦截气缸的驱动端上,拦截杆的延伸方向与第二 输送道131的输送方向相互垂直,拦截气缸可驱动拦截杆上下移动,当拦截气缸 驱动拦截杆向下移动,拦截杆可以拦截位于第二输送道131始端的工件,配合输 送切换装置140的输送端,使得工件的位置更精确,方便第二夹紧构件630的夹 紧。实际上,第一输送道121和第二输送道131可以相互平行,使得进料口和出 料口均位于同一侧,方便上下料,缩短整个散热片加工一体机的长度,另外,可 以改为直下式转料,进料口和出料口位于不同一侧,使得传送道的转料路径大幅 减短,运输效率提升,方便工人在工件的生产过程中进行监测和清洗铝屑。
41.另外,移动机构包括前后驱动构件510、左右驱动构件520和上下驱动构件 530,以第二传送道的输送方向为前,前后驱动构件510设置在工作台110上, 前后驱动构件510上设有可沿前后方向移动的第一安装块,左右驱动构件520 设置在第一安装块上,左右驱动构件520上设有可沿左右方向移动的第二安装 块,上下驱动构件530设置在第二安装块上,加工端540设置在上下驱动构件 530的下端,上下驱动构件530可驱动加工端540上下移动。加工端540可以是 钻孔、倒角或攻丝等刀具,加工端540通过前后驱动构件510、左右驱动构件520 和上下驱动构件530,实现其可以在空间内进行三位移动,使得加工端540可以 在工件的表面上进行加工,提高使用功能性和自动化效果,提高生产效率。实际 上,因为第二输送装置130设置在工件的下方,使得移动机构的高度可以整体下 降,减少加工端540的晃动,提高加工精度。上下驱动构件530、左右驱动构件 520和上下驱动构件530可以是丝杆滑台或气缸等。
42.以上对本发明的较佳实施方式进行了具体说明,但本发明并不限于实施例, 熟悉本领域的技术人员在不违背本发明精神的前提下还可作出种种的等同变型 或替换,这些等同的变型或替换均包含在本技术权利要求所限定的范围内。
再多了解一些
本文用于企业家、创业者技术爱好者查询,结果仅供参考。