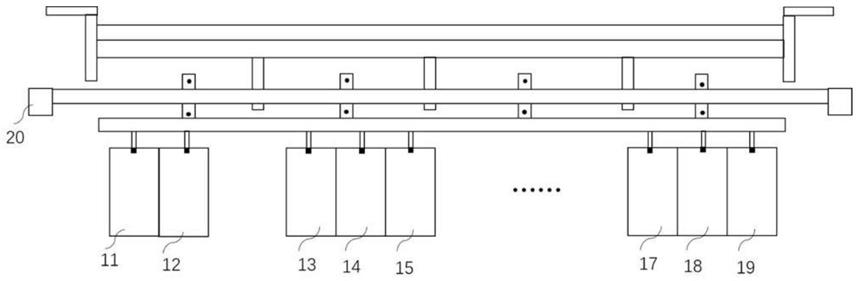
1.本发明涉及一种pcb电镀技术领域,特别涉及一种盲孔填孔的电镀方法及电镀装置。
背景技术:
2.现有技术中,由于印制电路板两面均需进行电镀,每个电镀缸都拥有两个阳极和一个阴极,其中阴极在电镀缸的正中央,通过带金属触点的夹具来固定印制电路板,底部有均匀排布的气孔;阳极在电镀缸两侧各有一排,每排都是由连续排列的钛篮组成,钛篮内部放置磷铜球提供铜源,或者在电镀缸的两侧各有一排钛网阳极。在电镀铜填充盲孔过程中,由于电镀过程的初始期长,电镀时间短会出现盲孔凹陷偏大的问题,或者由于盲孔过深,盲孔内部加速剂不够导致电镀填孔存在空洞的问题。
3.因此,当电路板的盲孔纵横比越来越大时,传统的电镀装置和电镀方法已经无法满足需求。因此需要新的电镀方法和电镀装置来改善盲孔填充的问题。针对较高纵横比盲孔进行电镀时,电镀铜填充盲孔的是利用盲孔的孔形特点和添加剂的吸附特性,改变电镀过程中盲孔内、外的电流密度分布,使孔内铜沉积速率更快,形成“孔底上移(bottom
‑
up)”的过程,从而实现盲孔填充。传统采用pcb板两侧及底边设置喷头组件,电镀添加剂均匀的加入进电镀液,通过侧喷溶液和底喷空气来进行电镀溶液的交换。由于电镀盲孔一般分为三个时期,初始期、爆发期、稳定期。根据曲率提升吸附物覆盖率(ceac)模型,在电镀填孔过程中,孔底由于几何外形收缩,曲率提升,导致加速剂覆盖率(浓度)提升,因此铜生长速率加快,进而实现“孔底上移(bottom
‑
up)”的填孔效果。如果能快速在盲孔底部吸附一定浓度的加速剂,那么在填孔初期不需要等待孔底几何外形收缩就可以获得较快的铜生长速率,而几何外形收缩带来的加速剂覆盖率提升将进一步加快孔底铜生长速率,因此可以获得更强烈的bottom
‑
up效果,从而缩短填孔时间。
技术实现要素:
4.基于此,有必要提供一种电镀方法及电镀装置,能够减少深盲孔的凹陷偏大或者空洞问题,从而使印制电镀板盲孔填充效果更好,保证印制电路板的可靠性。为了实现上述目的,本发明提供了一种电镀方法,
5.(1)清洗待镀件表面的氧化物和油污等异物;
6.(2)将待镀件浸泡在第一酸浸槽中10~300s;
7.(3)将待镀件放入第一电镀槽中进行电镀;
8.(4)将待镀件水洗干净,然后放入第一加速槽中加速5~120s;
9.(5)将待镀件水洗干净,然后浸泡在第二酸浸槽中10~300s;
10.(6)将待镀件放入第二电镀槽中进行电镀;
11.(7)将待镀件水洗干净,然后放入下一个加速槽中加速5~120s;
12.(8)将待镀件水洗干净,然后浸泡在下一个酸浸槽中10~300s;
13.(9)将待镀件放入下一个电镀槽中进行电镀;
14.(10)重复步骤(7)~步骤(9)n
‑
1次。
15.可选地,所述所有酸浸槽中溶液组成相同,包含50~150ml/l的浓硫酸;所述浸泡过程中,溶液必须采用强制对流。
16.可选地,所有电镀槽中溶液组成相同,包含五水硫酸铜160~280g/l、浓硫酸20~100g/l、氯离子20~80mg/l以及有机添加剂;所述电镀过程中,溶液比如采用强制对流,溶液温度18~40℃,电镀时间5~60min。
17.可选地,所述第二电镀槽至第n 1电镀槽中溶液组成相同,但第二电镀槽与第一电镀槽中溶液组成不同;第一电镀槽中包含五水硫酸铜50~120g/l、浓硫酸160~260g/l、氯离子20~80mg/l,第二电镀槽、
……
第n 1电镀槽中包含五水硫酸铜160~280g/l、浓硫酸20~100g/l、氯离子20~80mg/l;所述电镀过程中,溶液比如采用强制对流,溶液温度18~40℃,电镀时间5~60min。
18.可选地,所有加速槽中溶液组成相同,包含浓硫酸50~150ml/l和氧化剂;所述加速过程中,溶液无强制对流。
19.可选地,加速槽溶液的氧化剂可以为,双氧水和过硫酸钠中的至少一种。
20.另一方面,本技术涉及一种电镀装置,包括待镀件、多段式电镀槽,其中多段式电镀槽包括第一电镀模块和第二电镀模块,所述第一电镀模块包括酸浸槽和电镀槽;所述第二电镀模块包括加速槽、酸浸槽、电镀槽。
21.可选地,第二电镀模块的数量大于等于2。
22.有益的技术效果:对于印制电路板的深盲孔填充,该电镀方法可以缩短深盲孔电镀填孔时间,提高生产效率,同时对于极深盲孔的填充,可以有效地降低深盲孔产生填孔空洞的风险,提高盲孔填充的可靠性。
附图说明
23.图1为本发明的电镀装置示意图:
24.附图标记:第一酸浸槽11,第一电镀槽12,第一加速槽13,第二酸浸槽14,第二电镀槽15,第n加速槽17,第n 1酸浸槽18,第n 1电镀槽19,天车20。
具体实施方式
25.为使本发明上述目的,特征和优点能够更加明显易懂,下面结合对本发明的具体实施方式做详细说明,在下面的描述中阐述了很多具体细节以便于充分理解本发明。但是本发明能够以很多不同于在此描述的其他方式来实施,本领域技术人员可以在不违背本发明内涵的情况下做类似改进,因此本发明不受下面公开的具体实施例的限制。
26.下面结合附图和实施例对本发明作进一步说明:
27.如图1所示,本发明公开的电镀系统10包括第一酸浸槽11、第一电镀槽12、第一加速槽13、第二酸浸槽14、第二电镀槽15、
……
第n加速槽17、第n 1酸浸槽18、第n 1电镀槽19、天车20,其中,n=1,2,3,4
……
。
28.1.将待镀件进行除油、微蚀、酸洗等前处理步骤,清洗待镀件表面的氧化物和油污等异物。
29.2.将待镀件浸泡在第一酸浸槽中10~300s。
30.3.将待镀件放入第一电镀槽中进行电镀;第一电镀槽中包含五水硫酸铜50~120g/l、浓硫酸160~260g/l、氯离子20~80mg/l,在第一电镀槽时,盲孔的底部和板面都有一定浓度的加速剂吸附,所述电镀过程中,溶液比如采用强制对流,溶液温度18~40℃,电镀时间5~60min。
31.4.将待镀件水洗干净,然后放入第一加速槽中加速5~120s;第一加速槽的溶液的组成为过硫酸钠50~120g/l、硫酸50g/l,且在加速槽中的溶液保持静止状态,将待镀件放入加速槽,控制加速时间5~120s,其加速时间根据加速槽中溶液的浓度进行控制,加速槽中的溶液对铜具有微蚀作用,;利用盲孔的孔底和板面在溶液中的对流差异,使孔内的加速剂保留,吸附在板面的加速剂随着铜的氧化而解吸附,从而使盲孔内部保留一定量的加速剂。
32.5.将待镀件水洗干净,然后浸泡在第二酸浸槽中10~300s。
33.6.将待镀件放入第二电镀槽中进行电镀,第二电镀槽、
……
第n 1电镀槽中溶液组成相同,但第二电镀槽与第一电镀槽中溶液组成不同,第二电镀槽、
……
第n 1电镀槽中包含五水硫酸铜160~280g/l、浓硫酸20~100g/l、氯离子20~80mg/l,所述电镀过程中,溶液比如采用强制对流,溶液温度18~40℃,电镀时间5~60min。
34.7.重复步骤(4)~步骤(6)n
‑
1次。
35.8.将待镀件水洗干净,然后放入第n加速槽中加速5~120s,n次循环,加速剂将在盲孔底部进行n次积累,从而加快盲孔底部的铜沉积速率。
36.9.将待镀件水洗干净,然后浸泡在第n 1酸浸槽中10~300s;
37.10.将待镀件放入第n 1电镀槽中进行电镀。
38.虽然在本文中参照了特定的实施方式来描述本发明,但是应该理解的是,这些实施例仅仅是本发明的原理和应用的示例。因此应该理解的是,可以对示例性的实施例进行许多修改,并且可以设计出其他的布置,只要不偏离所附权利要求所限定的本发明的精神和范围。应该理解的是,可以通过不同于原始权利要求所描述的方式来结合不同的从属权利要求和本文中所述的特征。还可以理解的是,结合单独实施例所描述的特征可以使用在其他所述实施例中。
再多了解一些
本文用于企业家、创业者技术爱好者查询,结果仅供参考。