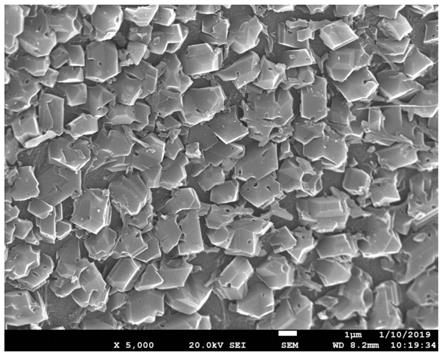
一种金刚石
‑
金属界面结构、复合材料及制备方法
技术领域
1.本技术涉及金刚石导热材料领域,具体而言,涉及一种金刚石
‑
金属界面结构、复合材料及制备方法。
背景技术:
2.随着电子器件逐渐小型化和高集成化,对器件散热提出了更高的要求,迫切需要开发新型的高导热电子封装材料。金刚石颗粒增强金属基复合材料具有高导热、热膨胀系数可调节等优点,是理想的电子封装用热管理材料。但是,金刚石与金属间的界面能较高,金属对金刚石的润湿性差,造成较高的界面热阻,无法充分发挥金刚石增强金属基复合材料高导热的特性。同时,在金刚石
‑
金属复合材料后续加工的过程中,由于界面结合强度较低,存在金刚石颗粒脱落情况,严重影响金刚石
‑
金属复合材料的加工精度和表面粗糙度。
3.现有技术中为提高界面把持力,防止金刚石颗粒脱落,主要通过在金刚石表面金属化,但其多用于磨削加工领域,未考虑界面热阻,并不适用于导热材料领域。如专利cn106835054a通过利用双辉等离子体的轰击溅射作用和fe、co、ni等铁族金属的石墨化催化作用,在单晶表面形成均匀分布的微坑,使表面粗化、活化,提高表面金属化涂层与单晶金刚石的结合强度。专利cn109628884a通过对金刚石颗粒的离子刻蚀处理,再蒸镀含初生tic的ti合金层,显著提高了金刚石胎体对磨粒的把持力。专利cn110079801a通过表面镀覆复合金属层的方法提高对金刚石的把持,先在金刚石表面镀覆一层钛层,在镀钛层上面再镀覆一层加强键合层,在加强键合层上再镀覆一层加厚连接层。以上方法尽管提高了金刚石的把持力,但工艺复杂,同时未考虑界面热阻的大小。
4.另外,现有技术中,专利cn110438457a公开的金刚石表面改性方法镀层厚度在5
‑
15μm,镀层较厚热阻较高,而且金刚石与金属界面之间的结合力也不高。专利cn109825815a使用石墨烯调节金刚石
‑
铜界面热阻,但无法同时提高界面结合力。专利cn111009497a通过对半导体基底进行蚀刻形成沟槽,然后沉积类金刚石薄膜制备半导体衬底;专利cn112216739a中通过在硅衬底层制备条纹状凹槽,然后在其上形成金刚石介质层,上述专利针对的是半导体衬底的处理,并未解决复合材料中金刚石颗粒与金属基结合力低,易脱落的问题。
5.针对以上金刚石颗粒增强金属基复合材料中存在的界面热阻高和界面结合强度差的技术难题,本技术提出了具有异形结构的金刚石
‑
金属界面结构及其相应的制备工艺,采用该界面结构的复合材料,热导率、界面结合强度以及加工精度显著提高,而且制备工艺简单,易实施。
技术实现要素:
6.为了克服现有技术的上述缺点,本技术的目的在于提供一种金刚石
‑
金属界面结构、复合材料及制备方法,所述界面结构热阻低、强度高,所制复合材料的热导率、强度和加工精度得到显著提升。
7.第一方面,本技术提供了一种金刚石
‑
金属界面结构,其特征在于,金刚石颗粒与金属之间具有界面层,所述界面层的界面结构包含异形结构。
8.在一优选的方案中,所述异形结构为柱状形、锥形、梯台形和/或波浪形,高度为100~1000nm。
9.在一优选的方案中,所述金刚石颗粒为完整晶型,粒径为40~400μm。
10.在一优选的方案中,所述界面层的成分为碳化物,所述碳化物选自tic、cr3c2、wc、b4c、和zrc中的一种。
11.第二方面,本技术提供一种上述金刚石
‑
金属界面结构的制备方法,其特征在于采用反应刻蚀法进行制备,包括以下步骤:
12.(1)在金刚石颗粒表面形成镀层,所述镀层中包括碳化物易形成元素和活性金属元素,所述碳化物易形成元素选自ti、cr、w、b、zr中的一种;所述活性金属元素选自al、zn、fe、cu、ni中的一种;
13.(2)对镀覆后的金刚石颗粒进行热处理,使得热处理后的金刚石颗粒表面镀层由易形成元素碳化物和活性金属元素构成;
14.(3)将热处理后的金刚石颗粒置于酸性溶液中进行蚀刻处理以去除活性金属元素;
15.(4)蚀刻处理后的金刚石颗粒进行清洗、烘干,得到界面结构为异形结构的金刚石颗粒。
16.在一优选的方案中,所述步骤(1)中,通过磁控溅射的方式在金刚石颗粒表面形成镀层,其中,磁控溅射功率为5~15kw,溅射时间1~8h;所形成镀层的厚度为100~1000nm。
17.在一优选的方案中,所述步骤(2)中,在真空条件下进行热处理,所述热处理温度高于碳化物易形成元素与金刚石反应所需温度,过热度50~100℃,热处理时间1~4h。
18.在一优选的方案中,所述步骤(3)中,蚀刻温度90~110℃,蚀刻时间30~60min,酸性溶液为30~50vol%的硫酸或硝酸溶液。
19.第三方面,本技术提供一种金刚石
‑
金属复合材料,其特征在于,金刚石颗粒与金属之间具有界面层,所述界面层的结构为前述的界面结构。
20.第四方面,本技术提供一种金刚石
‑
金属复合材料的制备方法,采用具有界面结构的金刚石颗粒,或采用前述方法制备界面结构为异形结构的金刚石颗粒,通过压力熔渗所述金刚石颗粒以制备金刚石
‑
金属复合材料。
21.本技术具有以下有益的技术效果:
22.1)金刚石
‑
金属复合材料的界面处引入具有异形结构的界面层,解决了同时兼顾金刚石
‑
金属界面热阻和界面结合强度的问题,提高了所制复合材料的导热率和界面强度。
23.2)异形结构界面制备时,通过在金刚石颗粒表面镀覆由碳化物易形成元素和活性金属元素组成的混合镀层,经高温热处理获得易形成元素碳化物,后经蚀刻处理去除活性金属元素,由此制得具有异形结构的界面,制备工艺简单,易实施。
24.3)异形结构界面制备时,通过协同调整磁控溅射、热处理和反应刻蚀等相关工艺参数,以实现对界面处易形成元素碳化物层的分布和异形结构高度的有效控制,保证了采用该界面时,所制备的金刚石
‑
金属复合材料不仅具有较高的热导率,同时具有更高的加工精度,满足大功率电子器件用热管理材料高性能、高精度的需求。
附图说明
25.为了更清楚地说明本技术实施例的技术方案,下面将对本技术实施例中所需要使用的附图作简单地介绍,应当理解,以下附图仅示出了本技术的某些实施例,因此不应被看作是对范围的限定,对于本领域普通技术人员来讲,在不付出创造性劳动的前提下,还可以根据这些附图获得其他相关的附图。
26.图1为具有柱状结构界面的示意图;
27.图2为具有梯台状结构界面的示意图;
28.图3为实施例1界面层结构的sem图;
29.图4为实施例2界面层结构的sem图;
30.图5为为实施例3界面层结构的sem图;
31.图6为为实施例5界面层结构的sem图;
32.图中标号为:1
‑
金刚石
ꢀꢀ2‑
界面
ꢀꢀ3‑
金属基体
具体实施方式
33.为使本技术实施例的目的、技术方案和优点更加清楚,下面将对本技术实施例中的技术方案进行清楚、完整地描述。实施例中未注明具体条件者,按照常规条件或制造商建议的条件进行。所用试剂或仪器未注明生产厂商者,均为可以通过市售购买获得的常规产品。
34.本技术提供了一种金刚石
‑
金属界面结构,其特征在于,金刚石颗粒与金属之间具有界面层,所述界面层的界面结构包含异形结构。
35.发明人发现,与金刚石
‑
金属复合材料界面处平面化结构的界面层相比,异形结构的界面减少了声子散射,有利于提高声子在界面的传输效率,从而降低金刚石
‑
金属间的界面热阻;且该界面结构的引入,可实现金属基体与界面层之间的结合由常见的冶金结合转为冶金结合和机械啮合协同作用,有利于提高金刚石与金属的界面结合强度。
36.在优选的实施方式中,所述异形结构包括但不限于为:柱状形、锥形、梯台形、针状形和/或波浪形等,所述界面层的成分为碳化物,所述碳化物包括但不限于选自tic、cr3c2、wc、b4c、和zrc中的一种。如图所示,图1为界面结构为柱状形的结构示意图,图2为界面结构为梯台形的结构示意图;其中,所述异形结构的高度为100~1000nm(例如200nm、250nm、300nm、350nm、400nm、450nm、500nm、550nm、600nm、650nm、700nm、750nm、800nm、850nm、900nm或950nm等),该高度是指柱、锥、梯台、针或波浪的高度;一般情况下,异形结构的高度小于磁控溅射时所形成镀层的厚度;但有时随着对金刚石热处理时间的延长,异形结构的高度会出现等于或大于镀层厚度的情况。通过控制异形结构的高度,可有效兼顾复合材料的热导率和界面结合强度,但如果异形结构高度过高,超过1000nm,一方面会导致界面热阻提高,另一方面会由于应力过大,导致金刚石和碳化物层之间的界面开裂;异形结构高度过低,会导致界面结合力降低,造成复合材料的强度降低;另一方面,高度过低会造成金刚石表面包覆不全的情况,即存在金刚石裸露表面,造成界面热阻增大,复合材料热导率降低;优选异形结构高度为400~700nm,更优选490~610nm。
37.在优选的实施方式中,金刚石颗粒为完整晶型,粒径为40~400μm(例如80μm、100μm、150μm、170μm、200μm、230μm、250μm、280μm、300μm、320μm、350μm或370μm等)。采用完整晶
型的金刚石可实现热导率的进一步提高;通过控制金刚石颗粒粒径,可实现对复合材料强度和热导率的调控。
38.本技术还提供了一种上述金刚石
‑
金属界面结构的制备方法,其特征在于采用反应刻蚀法进行制备,包括以下步骤:
39.(1)在金刚石颗粒表面形成镀层,所述镀层中包括碳化物易形成元素和活性金属元素,所述碳化物易形成元素选自ti、cr、w、b、zr中的一种;所述活性金属元素选自al、zn、fe、cu、ni中的一种;
40.(2)对镀覆后的金刚石颗粒进行热处理,使得热处理后的金刚石颗粒表面镀层由易形成元素碳化物和活性金属元素构成;
41.(3)将热处理后的金刚石颗粒置于酸性溶液中进行蚀刻处理以去除活性金属元素;
42.(4)蚀刻处理后的金刚石颗粒进行清洗、烘干,得到界面结构为异形结构的金刚石颗粒。
43.本技术通过在金刚石颗粒表面镀覆由碳化物易形成元素(ti、cr、w、b或zr)和活性金属元素(al、zn、fe或cu)组成的混合镀层,在高温条件下进行热处理时,碳化物易形成元素可扩散至金刚石表面参与界面反应,碳化物在活性点形核长大,由于竞争生长形成非连续的凸起结构;而活性金属元素可起到降低金刚石表面能,使其石墨化,促进界面反应的发生;进一步的,在后续的蚀刻处理时,可去除该活性金属元素,以形成具有异形结构的界面,从而实现了在降低金刚石
‑
金属间界面热阻的同时,提高了金刚石与金属的界面结合强度。优选的,碳化物易形成元素和活性金属元素之间的摩尔比例为1:2~3:1,通过控制二者的比例,可实现异形结构形状和尺寸(如高度和宽度等)的控制。
44.在优选的实施方式中,所述步骤(1)中,通过磁控溅射的方式在金刚石颗粒表面形成镀层,其中,磁控溅射功率为5~15kw(例如6kw、7kw、8kw、9kw、10kw、11kw、12kw、13kw或14kw等),溅射时间1~8h(例如2h、3h、4h、5h、6h或7h);所形成镀层为连续分布,厚度为100~1000nm(例如150nm、200nm、250nm、300nm、350nm、400nm、450nm、500nm、550nm、600nm、650nm、700nm、750nm、800nm、850nm、900nm或950nm等)。控制磁控溅射的功率5~15kw与时间1~8h,一方面,可实现金刚石颗粒表面镀层连续分布,避免了由于基体金属和金刚石直接接触所导致的界面热阻较高的问题;另一方面,通过控制溅射功率和时间,可以调整相应镀层的厚度,并在后续热处理和酸蚀工艺中,结合相应的热处理和酸蚀工艺的参数,可获得所需异性结构高度界面的金刚石颗粒。
45.在优选的实施方式中,所述步骤(2)中,在真空条件下进行热处理,所述热处理温度高于碳化物易形成元素与金刚石反应所需温度,过热度50~100℃(例如55℃、60℃、65℃、70℃、75℃、80℃、85℃、90℃或95℃等),热处理时间1~4h(例如1.5h、2h、2.5h、3h或3.5h等)。
46.在高于碳化物易形成元素与金刚石反应所需温度的50~100℃下对镀覆后的金刚石颗粒进行热处理,可以加快碳化物易形成元素与金刚石之间的界面反应,提高碳化物产生的效率,同时促使碳化物元素向金刚石表面扩散;若过热度小于50℃,界面反应发生的速度慢,碳化物产生的少;若过热度高于100℃,工艺实施困难,而且对反应炉体要求较高;通过控制过热度50~100℃和热处理时间1~4h,可以保证界面反应速度和碳化物产生的量,
并实现碳化物均匀扩散以及对异形结构高度的控制。
47.在优选的实施方式中,所述步骤(3)中,蚀刻温度90~110℃,蚀刻时间30~60min(例如35min、40min、45min、50min或55min等),酸性溶液为30~50vol%(例如32vol%、35vol%、37vol%、40vol%、43vol%、45vol%或48vol%等)的硫酸或硝酸溶液。
48.示例性地,在处理cu活性金属元素时,采用硝酸处理;处理al、zn、fe、ni等活性金属元素时,采用硫酸处理;30~50vol%浓度范围的酸性溶液,可有效的蚀刻活性金属元素,若浓度高于50vol%,会造成易形成元素碳化物结构的破坏,导致复合材料的强度和导热率降低;若浓度低于30vol%,会影响蚀刻速率。
49.本技术提供一种金刚石
‑
金属复合材料,其特征在于,金刚石颗粒与金属之间具有界面层,所述界面层结构为前述的界面结构。其中,所述的金属选自cu、al、ag等。
50.本技术提供一种金刚石
‑
金属复合材料的制备方法,采用具有前述界面结构的金刚石颗粒,或采用前述方法制备界面结构为异形结构的金刚石颗粒,通过压力熔渗所述金刚石颗粒以制备金刚石
‑
金属复合材料。其中,所述的金属选自cu、al、ag等。
51.具体的压力熔渗工艺流程典型但非限制性的包括:将具有异形结构的金刚石颗粒放入模具中,然后将金属基体置于金刚石颗粒上方,在熔渗炉中,升高至一定温度,施加压力,实现熔融金属基体渗入金刚石颗粒间的孔隙中去,由此制备金刚石
‑
金属复合材料。
52.下面结合实施例对本发明进行具体说明。
53.实施例1
54.选取100μm完整晶型金刚石颗粒作为原料。金刚石经稀酸煮沸、去离子水漂洗、80℃烘干处理。
55.(1)处理后的金刚石采用磁控溅射在金刚石颗粒表面镀ti、ni混合金属层,ti与ni的摩尔比为1:1。沉积以99.99%的ti、ni为靶材,溅射功率5kw,溅射时间3h。金刚石增重为15wt%,混合镀层厚度约为200nm。
56.(2)将镀覆后的金刚石在真空条件下进行热处理,过热度为50℃,热处理温度为750℃,热处理时间1h,ti扩散至金刚石表面反应生成tic,获得tic和ni的金刚石颗粒。
57.(3)将上述金刚石颗粒置于40vol%的硫酸溶液中,加热至100℃进行蚀刻去除ni,蚀刻时间60min。
58.(4)采用去离子水清洗蚀刻处理后的金刚石颗粒,烘干后获得含异形结构界面层的金刚石颗粒。
59.图3为所制金刚石颗粒界面层结构的sem图,可以看出,该界面结构为锥状结构。
60.压力熔渗制备金刚石
‑
cu复合材料:
61.将具有锥状结构的金刚石颗粒放入模具中,然后将cu置于金刚石颗粒上方,在熔渗炉中,升温至1200℃,施加30mpa压力,实现熔融cu渗入金刚石颗粒间的孔隙中去,由此制备金刚石
‑
cu复合材料。
62.实施例2
63.选取200μm完整晶型金刚石颗粒作为原料。金刚石经稀酸煮沸、去离子水漂洗、80℃烘干处理。
64.(1)处理后的金刚石采用磁控溅射在金刚石颗粒表面镀cr、fe混合金属层,cr与fe的摩尔比为2:1。沉积以99.99%的cr、fe为靶材,溅射功率8kw,溅射时间3.5h。金刚石增重
为20wt%,混合镀层厚度约为300nm。
65.(2)将镀覆后的金刚石在真空条件下进行热处理,过热度为100℃,热处理温度为900℃,热处理时间2h,cr扩散至金刚石表面反应生成cr3c2,获得cr3c2和fe的金刚石颗粒。
66.(3)将上述金刚石颗粒置于30vol%的硫酸溶液中,加热至100℃进行蚀刻去除fe,蚀刻时间60min。
67.(4)采用去离子水清洗蚀刻处理后的金刚石颗粒,烘干后获得含异形结构界面层的金刚石颗粒。
68.图4为所制金刚石颗粒界面层结构的sem图,可以看出,该界面结构为锥状结构。
69.压力熔渗制备金刚石
‑
cu复合材料:
70.将具有锥状结构的金刚石颗粒放入模具中,然后将cu置于金刚石颗粒上方,在熔渗炉中,升温至1200℃,施加30mpa压力,实现熔融cu渗入金刚石颗粒间的孔隙中去,由此制备金刚石
‑
cu复合材料。
71.实施例3
72.选取300μm完整晶型金刚石颗粒作为原料。金刚石经稀酸煮沸、去离子水漂洗、80℃烘干处理。
73.(1)处理后的金刚石采用磁控溅射在金刚石颗粒表面镀b、cu混合金属层,b与cu的摩尔比为1:1。沉积以99.99%的b、cu为靶材,溅射功率10kw,溅射时间6h。金刚石增重为25wt%,混合镀层厚度约为1000nm。
74.(2)将镀覆后的金刚石在真空条件下进行热处理,过热度为100℃,热处理温度为1050℃,热处理时间3h,b扩散至金刚石表面反应生成b4c,获得b4c和cu的金刚石颗粒。
75.(3)将上述金刚石颗粒置于45vol%的硝酸溶液中,加热至110℃进行蚀刻去除cu,蚀刻时间90min。
76.(4)采用去离子水清洗蚀刻处理后的金刚石颗粒,烘干后获得含异形结构界面层的金刚石颗粒。
77.图5为所制金刚石颗粒界面层结构的sem图,可以看出,该界面结构为柱状结构。
78.压力熔渗制备金刚石
‑
cu复合材料:
79.将具有柱状结构的金刚石颗粒放入模具中,然后将cu置于金刚石颗粒上方,在熔渗炉中,升温至1230℃,施加35mpa压力,实现熔融cu渗入金刚石颗粒间的孔隙中去,由此制备金刚石
‑
cu复合材料。
80.实施例4
81.选取200μm完整晶型金刚石颗粒作为原料。金刚石经稀酸煮沸、去离子水漂洗、80℃烘干处理。
82.(1)处理后的金刚石采用磁控溅射在金刚石颗粒表面镀b、cu混合金属层,b与cu的摩尔比为2:1。沉积以99.99%的b、cu为靶材,溅射功率10kw,溅射时间2.5h。金刚石增重为10wt%,混合镀层厚度约为400nm。
83.(2)将镀覆后的金刚石在真空条件下进行热处理,过热度为xxx,热处理温度为1050℃,热处理时间2h,b扩散至金刚石表面反应生成b4c,获得b4c和cu的金刚石颗粒。
84.(3)将上述金刚石颗粒置于45vol%的硝酸溶液中,加热至100℃进行蚀刻去除cu,蚀刻时间50min。
85.(4)采用去离子水清洗蚀刻处理后的金刚石颗粒,烘干后获得含异形结构界面层的金刚石颗粒。
86.压力熔渗制备金刚石
‑
al复合材料:
87.将具有异形结构的金刚石颗粒放入模具中,然后将al置于金刚石颗粒上方,在熔渗炉中,升温至750℃,施加20mpa压力,实现熔融al渗入金刚石颗粒间的孔隙中去,由此制备金刚石
‑
al复合材料。
88.实施例5
89.选取400μm完整晶型金刚石颗粒作为原料。金刚石经稀酸煮沸、去离子水漂洗、80℃烘干处理。
90.(1)处理后的金刚石采用磁控溅射在金刚石颗粒表面镀zr、cu混合金属层,zr与cu的摩尔比为1:1。沉积以99.99%的zr、cu为靶材,溅射功率6kw,溅射时间3.5h。金刚石增重为20wt%,混合镀层厚度约为500nm。
91.(2)将镀覆后的金刚石在真空条件下进行热处理,过热度为50℃,热处理温度为900℃,热处理时间3h,zr扩散至金刚石表面反应生成zrc,获得zrc和cu的金刚石颗粒。
92.(3)将上述金刚石颗粒置于45vol%的硝酸溶液中,加热至100℃进行蚀刻去除cu,蚀刻时间40min。
93.(4)采用去离子水清洗蚀刻处理后的金刚石颗粒,烘干后获得含异形结构界面层的金刚石颗粒。
94.图6为所制金刚石颗粒界面层结构的sem图,可以看出,该界面结构为针状结构。
95.压力熔渗制备金刚石
‑
al复合材料:
96.将具有针状结构的金刚石颗粒放入模具中,然后将al置于金刚石颗粒上方,在熔渗炉中,升温至750℃,施加25mpa压力,实现熔融al渗入金刚石颗粒间的孔隙中去,由此制备金刚石
‑
al复合材料。
97.实施例6
98.与实施例1的区别在于,步骤(1)中,溅射功率15kw,溅射时间4h,金刚石增重为25wt%,混合镀层厚度约为350nm;步骤(2)中热处理时间2h;步骤(3)蚀刻时间50min。
99.实施例7
100.与实施例1的区别在于,步骤(2)中,过热度为75℃,热处理温度为775℃。
101.实施例8
102.与实施例1的区别在于,与实施例1的区别在于,步骤(2)中,过热度为100℃,热处理温度为800℃。
103.实施例9
104.与实施例1的区别在于,步骤(2)中,过热度为40℃,热处理温度为740℃。
105.实施例10
106.与实施例1的区别在于,步骤(2)中,过热度为110℃,热处理温度为810℃。
107.实施例11
108.与实施例1的区别在于,步骤(3)中,蚀刻溶液浓度为30vol%。
109.实施例12
110.与实施例1的区别在于,步骤(3)中,蚀刻溶液浓度为50vol%。
111.实施例13
112.与实施例1的区别在于,步骤(3)中,蚀刻溶液浓度为55vol%。
113.实施例14
114.与实施例1的区别在于,步骤(3)中,蚀刻溶液浓度为25vol%。
115.实施例15
116.与实施例1的区别在于:
117.步骤(1)中,金刚石颗粒表面镀w、zn混合金属层,w与zn的摩尔比为1:1;溅射功率15kw,溅射时间6h。金刚石增重为25wt%,混合镀层厚度约为500nm;
118.步骤(3)中,过热度50℃,热处理温度为1150℃,热处理时间4h。
119.实施例16
120.与实施例1的区别在于:步骤(1)中,金刚石颗粒表面镀ti、al混合金属层;ti与al的摩尔比为1:1;溅射功率10kw,溅射时间1h。金刚石增重为5wt%,混合镀层厚度约为100nm。
121.对比例1
122.与实施例1的区别在于,步骤(1)镀层为ti金属层,经步骤(2)热处理后,在金刚石表面生成tic,未采取步骤(3)的蚀刻处理,所得界面为平面化界面结构。
123.对比例2
124.与实施例2的区别在于,步骤(1)镀层为cr金属层,经步骤(2)热处理后,在金刚石表面生成cr3c2,未采取步骤(3)的蚀刻处理,所得界面为平面化界面结构。
125.对比例3
126.与实施例3的区别在于,金刚石颗粒处理时,未采取步骤(3)的蚀刻处理,所得界面为平面化界面结构。
127.对比例4
128.与实施例4的区别在于,金刚石颗粒处理时,未采取步骤(3)的蚀刻处理,所得界面为平面化界面结构。
129.性能测试:
130.界面结构高度:采用sem对抛光截面碳化物高度进行测量,取平均高度,锥状结构高度的2/3。
131.导热率:gb/t 22588
‑
2008闪光法测导热系数试验方法
132.抗弯强度:gb/t 6569
‑
2006精细陶瓷弯曲强度试验方法
133.实施例及对比例测试结果见表1:
134.表1.实施例及对比例测试结果
135.[0136][0137][0138]
根据表1可知:
[0139]
实施例1
‑
16中所制得金刚石
‑
金属复合材料,其界面均为具有异形结构的界面,从所制复合材料的性能数据可以看出,金刚石
‑
铜导热率超过600w/mk,抗弯强度大于400mpa;金刚石
‑
铝导热率超过500w/mk,抗弯强度大于350mpa。
[0140]
对比实施例1、7
‑
10可以看出,热处理时,若过热度低于50℃,会出现界面反应发生的速度慢,碳化物反应未充分的问题,造成复合材料的强度和导热率有所降低;过热度高于100℃时,碳化物充分反应,但过高温度对复合材料的强度和导热率提升不明显,且工艺实施困难。
[0141]
对比实施例1、11
‑
14可以看出,刻蚀处理时,若酸性溶液的浓度低于30vol%,会出现蚀刻速率慢,活性元素残留的问题,对材料的性能不利;高于50vol%时,会出现碳化物结构的破坏,导致复合材料的强度和导热率降低。
[0142]
对比实施例1和对比例1,对比例1的界面成分为tic,界面结构为平面化结构,可以看出,采用该界面结构的金刚石颗粒所制复合材料的导热率为522w/m
·
k、抗弯强度为206mpa,远低于实施例1中所制复合材料的导热率和抗弯强度。
[0143]
对比实施例2和对比例2,对比例2的界面成分为cr3c2,界面结构为平面化结构,可以看出,采用该界面结构的金刚石颗粒所制复合材料的导热率和抗弯强度,远低于实施例2中采用异形结构界面的金刚石颗粒所制复合材料的性能。
[0144]
对比实施例3和对比例3,二者采用了相同的镀覆工艺和热处理工艺,区别在于对比例3未经刻蚀处理,从所制复合材料的性能数据可以看出,对比例3的抗弯强度和导热率等性能数据远低于实施例3的。
[0145]
对比实施例4和对比例4,二者采用了相同的镀覆工艺和热处理工艺,区别在于对比例4未经刻蚀处理,从所制复合材料的性能数据可以看出,对比例4的抗弯强度和导热率等性能数据远低于实施例4的。
[0146]
以上所述仅为本技术的实施例而已,并不用于限制本技术的保护范围,对于本领域的技术人员来说,本技术可以有各种更改和变化。凡在本技术的精神和原则之内,所作的任何修改、等同替换、改进等,均应包含在本技术的保护范围之内。
再多了解一些
本文用于企业家、创业者技术爱好者查询,结果仅供参考。