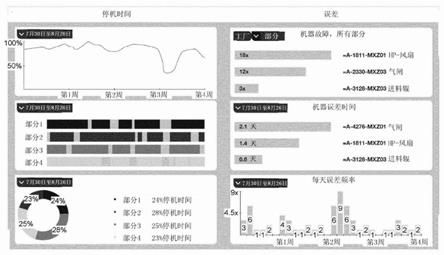
1.本发明涉及工业过程控制和/或监视系统。具体地,本发明涉及根据权利要求1的用于通过监视源自工业过程中使用的部件的测量数据和/或过程参数来检测工业设备或生产工厂中设备故障的异常或早期指示的方法,分别地,本发明涉及根据权利要求15的用于通过监视源自工业过程中使用的部件的测量数据和/或过程参数来检测工业设备或生产工厂中设备故障的异常或早期指示的系统。本发明包括自适应闭环和/或开环控制装置,其用于研磨和辊系统的自动化闭环和/或开环控制,更具体地具有辊框架的磨机工厂,以及一般地磨机系统和研磨工厂。除了其应用于用于控制和操纵研磨和辊系统的控制装置之外,本发明还一般地涉及用于检测和测量源自工业过程中使用的部件的信令中的异常的系统和方法。根据本发明的装置的可能应用还涉及如下研磨和辊系统:对一种或各种辊驱动器的操作参数例如辊温度、辊间隙、辊速度、辊压制力和/或电力给予进行实时或准实时测量和监视;以及/或者在谷物研磨工厂中的生产调节和加工期间对成分或质量参数——例如测量的变量,如水含量、蛋白质含量、淀粉损伤、面粉(或研磨中间体)的灰分含量(矿物质)、残余淀粉含量、研磨细度等——进行实时或准实时测量,以便对工厂和过程进行过程监视(测量、监视)和开环和/或闭环控制。
背景技术:
2.在工业过程和装置设置中,控制系统用于监视、控制、操纵和用信令通知工业或化学过程的设施、工厂或其他设备以及操作/过程等。通常,执行控制和监视的系统使用分布在工业过程中的关键位置处的现场装置,该现场装置通过过程控制回路耦接至控制电路系统。术语“现场装置”是指在分布式控制或过程监视系统中执行功能的任何装置,包括在测量中使用的所有装置,例如传感器和测量装置、工业过程的控制、监视和信令以及处理设施。例如,每个现场装置可以包括通信装置和电路系统,用于通过过程控制回路与过程控制器、其他现场装置或其他电路系统进行通信,特别是有线或无线通信。在一些装备中,过程控制回路还用来向现场装置输送经调节的电流和/或电压以为现场装置供电。过程控制回路还承载模拟或数字格式的数据。通常,如果需要,现场装置用来感测或控制工业过程和/或特定装备中的过程变量,以监视现场装置的局部环境。
3.这样的系统的技术问题之一基于以下事实:对大型工业资产(例如,在谷物磨机、食品加工厂中)的控制和监视通常产生大量的过程和警报/故障数据。通常的情况是,许多警报/故障被触发,然而,这些警报/故障通常被忽略或关闭以保持过程和控制运行。此外,警报/故障可以由机器上的简单维护事件触发,并且没有进一步的技术关注。此外,来自例如马达电流的过程数据可能频繁地显示基于阈值的非典型值并且不总是引起对个别事件的关注。需要提供警报/故障信令到重要事件的简短列表的自动化提取,上述重要事件相对于典型操作是异常的。这个简短列表将实现停机时间事件的有效预防性维护和根本原因分析,这些停机时间事件在工业过程中代价非常高昂并且应当被最小化。提前识别异常模式
是一个挑战,因此期望无监督的方法。
4.此外,机器或其他工业装备例如工厂、发动机、磨机或涡轮机等由于多种原因而发生故障。如以上所提及的,已知的工厂或机器故障通常由传感器检测,并且一旦检测到故障,就将故障报告给操作者以进行校正或者将故障用信令通知给适当分配的警报装置。然而,用于检测故障而采用的常规策略通常是基于机器、工厂或装置中先前发生的已知问题而发展的。可以通过自动推断与和特定问题相关联的已知异常行为相对应的传感器简档来确定这些先前发生的情况。然而,对于先前从未发生过的问题,故障往往在没有任何警告或先前指示的情况下出现。在这样的情况下,修复的成本可能显著大于早期检测到故障的情况。此外,故障或即将发生的故障的后期检测可能危及机器的安全。因此,期望提供以自动且准确的方式检测机器中的未知异常行为的系统和方法。
5.特别是在谷物磨机和食品加工厂中,根据传感器数据的异常检测是数据挖掘的重要应用。使用研磨生产作为示例,为了确保安全和优化的研磨和防止主要系统故障,对设备的远程监视是生产过程中的重要部分。远程监视的关键任务是异常检测,即在故障发生之前检测故障的早期指示。例如,辊压力和辊温度是确保稳定生产的关键要素,并且为此进行监视。在现有技术中,已经投入了很多努力来使异常检测自动化,但是这仍然是非常具有挑战性的任务。如上面已经部分讨论的那样,存在若干技术挑战。诸如温度、压力、位移、流速、振动等的传感器数据是有噪声的,传感器值可能不连续地改变,并且相关结构甚至会每天改变。需要结合智能监视和检测系统和方法来自动地处理不想要的噪声。变量和多个依赖关系很重要,因此,变量不应当被单独分析,因为这可能产生错误警报。此外,被监视的系统经常不稳定,因为操作条件可能随时间变化,例如环境条件,如空气压力或相对空气湿气/局部空气湿度。因此,还需要诊断信息,例如哪些变量表现出异常。然而,已知现有技术方法通常在实践中具有严重的问题,并且不能处理多种操作模式和多变量可变方式的异常得分二者。大多数系统不能有效地提供可变方式的信息,这在测量参数维度通常可能很大的许多工业应用中是特别成问题的。
6.us 2011/288836揭示了用于检测航空发动机中的异常的方法和系统。该方法和系统使用时间回归来定义航空发动机的控制器的行为模型,时间回归将控制器的行为建模为与控制器相关并包括对控制器的过去行为的测量和对控制器的命令及状态测量的数据集的函数;针对每个新的数据集连续地重新计算行为模型;以及监视行为模型的统计变化,以检测表示发动机的操作异常的控制器的行为异常。us 2016/371600 a揭示了随时间监视从系统记录的数据的系统和方法。本文描述的技术包括检测和分类系统事件以及提供正常系统操作和异常检测的指示的能力。本公开内容的系统和方法可以以如下方式表示在被监视的系统中发生的事件,该方式使得事件的时间特性可以被捕获并用于检测、分类和/或异常检测,这在处理复杂系统和/或事件时会是特别有用的。us 2017/139398揭示了多个生产设施和分析装置通过雾网络连接。分析装置基于通过雾网络获取的检测器的检测信息执行数据分析,并将与多个生产设施中的每一个的异常或生产对象的异常有关的确定信息作为数据分析的结果存储。多个生产设施中的每一个基于存储在分析装置中的确定信息来确定多个生产设施中的每一个的异常或生产对象的异常。ep 3 379 360揭示了异常检测系统1包括算术装置1h101,该算术装置1h101执行如下处理:学习预测性模型的处理,该预测性模型基于装置上的操作数据来预测监视目标装置的行为;调节异常得分使得正常操作下的操作
数据的异常得分落入预定义范围内的处理,该异常得分基于从监视目标装置获取的操作数据与通过预测性模型获得的预测结果的偏差;基于经调节的异常得分来检测异常或异常的迹象的处理;以及在输出装置上显示关于异常得分和检测结果中的至少一个的信息的处理。
7.最后,在现有技术系统中,警报/故障消息通常记录在自动化系统软件和控制系统中,其中,难以在这种日志形式的数据中深入探索和查看趋势。因此,操作者依靠其对警报/故障事件的观察来监视工厂健康状况。需要允许更好地输出警报/故障消息的信令和可视化,使得操作者可以容易地跟踪工厂操作、安全和健康状况。可视化还将使得诸如所有者和维护提供者的其他个人能够获得洞察并且能够更好地与操作者进行通信。在大型加工厂中避免/测量工厂停机时间是重要的,因为它代表了显著的收入损失。
技术实现要素:
8.本发明的目的是克服从现有技术中已知的缺点和技术问题。具体地,目的是提供用于检测源自工业过程中使用的部件的测量数据和传感器数据中的异常的准确且有效的控制系统和方法。系统应当能够提供自动化技术以有效地将大量警报/故障信息提取成一些触发的、重要的事件,这些触发的、重要的事件相对于典型操作是异常的。系统应当能够实时或准实时地执行控制和监视过程。更具体地,本发明的目的是提供用于辊系统的研磨线的自动优化和控制的智能的、自适应的开环/闭环控制装置,辊系统的研磨线可以用来以优化且自动的方式执行研磨和/或碾碎,并且提高了磨机的可靠性并同时通过对发生的异常自动作出反应来优化操作。
9.根据本发明,可以借助于独立权利要求和从属权利要求中特别描绘的元素和组合来实现和达到本发明的目的。应理解,前面的一般描述和以下详细描述二者仅是示例性和说明性的,而不是对所描述的本发明的限制。
10.根据本发明,实现了用于通过监视源自工业过程中使用的部件的传感器数据或测量数据来检测工业设备或生产工厂中设备故障的异常或早期指示的系统和方法的以上提及的目的,具体是以下情况:在于借助于测量装置或传感器测量工业过程中使用的部件的传感器数据和/或测量数据,并且在工业过程中使用的部件正常运行的时间段内在接收到的传感器数据和/或测量数据的数据流内识别相等大小的时间帧或时间段,传感器数据和/或测量数据包括多个测量参数的传感器值;在于针对所识别的相等大小的时间帧中的每一个,多个测量参数的传感器值被转换为可观察的二进制处理码,并且二进制处理码被分配给持有可存储马尔可夫链状态的序列的数据存储或数据结构;在于生成包括可定义数目的可变隐马尔可夫模型参数值的多维数据结构,其中,借助于应用于所分配的二进制处理码的序列的机器学习模块来确定多维数据结构的可变模型参数,并且其中,通过基于所识别的相等大小的时间帧的传感器数据和/或测量数据学习发生的警报事件的正常状态频率来改变和训练多维数据结构的可变隐马尔可夫模型参数;在于通过将具有所述可变隐马尔可夫模型参数值的经训练的多维数据结构应用于与所测量的传感器数据和/或测量数据具有相同的相等大小的时间帧的预采样的二进制处理码来对多个概率状态值进行初始化和存储;在于通过对存储的概率状态值的对数结果值进行排序来确定异常得分的对数阈值;以及在于部署具有可变隐马尔可夫模型参数值的所述经训练的多维数据结构,以使用异常得
分的阈值来监视来自工业设备或工厂的新测量的传感器数据和/或测量数据,以检测可能指示即将发生的系统故障的异常传感器数据值,其中,为了在异常传感器数据值下触发,新测量的传感器数据和/或测量数据的概率状态值的对数结果值被生成,并基于异常得分的所述对数阈值与存储的概率状态值进行比较。此外,存在不同方法来提供有效相关性的二进制向量距离,例如基于n行的窗的经典汉明距离(其中,n=1,经典汉明距离)。对于向量a和b,该距离等于n行窗上的a和b中的1的数量除以a的长度。另一种方法基于杰卡德距离。j(a,b)=1
‑
|a∩b||a∪b|。在实施方式变型中,可以周期性地生成距离,并且如果通过上述示例方法的有效相关性异常,则算法能够检测异常。
11.重要的是要注意,本发明的系统和方法原则上在将模拟信号转换为二进制信号或码(基于阈值)和不将模拟信号转换为二进制信号或码(基于阈值)的情况下工作。然而,将模拟信号转换为二进制信号或码尤其具有以下优点:时间序列异常检测通常依赖于阈值和移动平均值或类似值来检测异常。结果可能是由于振荡/噪声信号(工业过程中的典型情况)而检测到太多异常事件。例如,对于时间序列和异常检测,某人可以调节阈值以具有或多或少的灵敏度(参见图13,其中异常由灰色竖直线标记)。在该方法中,将已经超过阈值的事件中的每一个取为真/1值(否则为假/0)以生成二进制序列。这使我们能够查看阈值交叉的频率,使得可以基于异常频率对异常进行分类。优点是不需要担心阈值和振荡/噪声工业iot数据的过度灵敏性。在看不到二进制转换的这些优点的情况下,还可以使用算法的扩展来找到模拟过程数据中的异常。可以应用移动平均值和方差阈值来生成二进制序列。然后可以使用上面的异常检测算法。结果是当过程非典型地超过阈值时将识别异常。图14示出了过程数据的异常。在图9中,基于应用于过程数据的阈值来生成二进制序列。在下面的步骤中,将所描述的异常检测方法应用于二进制序列并且相应地标记异常时间段。重要的是要注意,上述将模拟信号异常转换为二进制向量然后应用根据本发明的统计hmm异常检测即基于隐马尔可夫模型(hmm)的结构的本发明的系统和方法在技术上是唯一的,并且不由任何现有技术系统提供。本发明使用hmm进行异常检测,而现有技术系统使用不同的技术来使用hmm标记异常。特别地,现有技术系统不使用本发明正使用的阈值步骤。此外,现有技术系统未提及将模拟信号转换为二进制序列,这也是权利要求1的微分器的一部分。
12.关于对权利要求中的任何权利要求的潜在创造性步骤或明显的异议,这比新颖性要主观得多,并且我无法评论各地区的专利官员将如何应用他们的主观决定和当地法律。尽管hmm的使用肯定是公知的技术,但权利要求非常特定于应用(谷物研磨等),并且说明书对适合我们过程的确切实现方式是相当具体的。hmm中肯定有关于异常检测的大量文献,但没有文件教导hmm专门应用于这些类型的工业过程,而不是用于警报数据。此外,科学论文/论题往往是不明确的,因为它们没有如此陈述权利要求。
13.例如,机器学习模块可以通过应用最大似然参数估计来处理所分配的二进制处理码的序列,以训练具有可变隐马尔可夫模型参数的多维数据结构,其中,马尔可夫链的可存储参数状态的序列的元素被假定为彼此独立的测量,并且其中,通过使概率的乘积最大化来改变多维数据结构的模型参数,以便获得多维数据结构的经训练的模型参数。例如,可以迭代地改变多维数据结构的模型参数,直到超过预定义的收敛阈值。为了确定异常得分的所述阈值,例如可以基于所识别的时间帧的传感器数据和/或测量数据的发生警报事件的不同频率来应用平均过程。本发明尤其具有以下优点:它提供了用于自动检测在源自工业
过程中使用的部件的数据中的异常下分别触发的新颖的方法和系统。它提供了用于控制和监视大型工业资产(例如,在谷物磨机、食品加工厂中)的高效自动化系统,这些大型工业资产通常产生难以处理的大量过程和警报/故障数据。
14.应注意,机器因每个相关警报(例如,违反辊温度限制、超过辊压力阈值等)而停止,与根据本发明的异常检测系统无关。然而,本发明提供用于例如与工业多变量时间序列数据相关联的无监督异常检测的新颖系统和方法。无监督检测尤其可以在“未知
‑
未知”场景中是非常重要的,在这种场景下,操作者不知道潜在的故障并且没有观察到这样的未知故障的任何先前发生。本发明的系统还可以提供数据质量评估、丢失值填补以及附加的或新的特征生成、验证和评估。本发明允许基于将正常操作简档(例如,指示正常范围内的值的所有传感器)与在操作的当前状态下报告的差异进行比较来确定未知故障。传感器可以与一台机器的各种可测量元素相关联,例如振动、温度、压力和环境变化等。在一些情况下,确定未知故障与发现即将发生的故障(例如,早期检测)有关。在一些情况下,确定未知故障与早期检测以及故障可能发生在过去但对当前操作有影响的其他情况有关。此外,本发明允许有效地过滤和区分由机器上的简单维护事件触发且不引起关注的警报/故障。这也适用于来自例如马达电流的过程数据,其可以频繁地显示基于阈值的非典型值并且不总是引起对个别事件的关注。本发明允许将从传感器和测量装置流式传输的警报/故障数据高效且自动地提取成重要事件的简短列表,这些重要事件相对于典型操作异常。这个简短列表为停机事件的有效预防性维护和根本原因分析的新颖方法提供了基础,这些停机事件在工业过程中代价非常高昂并且应当被最小化。本发明允许提前识别异常模式,使得通过控制和监视机器的正确操作的本发明使无监督的完全自动化的方法在技术上成为可能。因此,本发明允许特别是与工业多变量时间序列数据相关联的无监督的异常检测。无监督检测在“未知
‑
未知”场景中是非常重要的,在这种场景下,操作者不知道潜在的故障并且没有观察到这样的未知故障的任何先前发生。本发明能够将正常操作或机器/发动机简档(例如,指示正常范围内的值的所有传感器)与机器/发动机的当前状态下报告的差异进行比较来确定未知故障。传感器可以与一台机器的各种可测量元素相关联,例如振动、温度、压力和环境变化等。在一些情况下,确定未知故障(例如,评估)与发现即将发生的故障(例如,早期检测)有关。在一些其他情况下,确定未知故障与早期检测以及故障发生在过去的情况有关。此外,本发明允许以新的方式获得洞察并查看以该日志形式的传感器数据和/或警报/故障消息的趋势,这也使得操作者对警报/故障事件的连续监视变得多余。本发明还允许对警报/故障消息的新颖监视,使得操作者可以容易地跟踪工厂操作和健康状况。新颖的监视还使得诸如所有者和维护提供者的其他个人能够获得自动化洞察并且能够更好地与操作者进行通信。本发明允许避免/测量大型加工厂中的工厂停机时间,因为它代表显著的收入损失。
15.在实施方式变型中,例如,所选择的时间帧的灵敏度可以基于对阈值的动态调节而被自动地调整。该实施方式变型尤其具有以下优点:可以通过训练多维数据结构的可变隐马尔可夫模型参数来优化收敛速度。
16.在另一实施方式变型中,例如,异常时间帧跨同一工业生产线的许多资产进行评估,其中,为了在异常得分下触发,异常时间帧被应用于工厂停机时间的根本原因分析。此外,作为变型,例如可以基于工厂停机时间的所述根本原因分析来生成维护服务信令。该实
施方式变型尤其具有以下优点,即允许本发明跨各种资产和工业生产线的鲁棒应用。另一优点是:该实施方式变型允许实现基于云和/或基于网络的自动维护和/或服务应用和信令。
17.在又一实施方式变型中,为了确定异常得分的所述阈值,使用模式识别来针对相等大小的所识别的时间帧中的每一个生成频率模式以初始化可存储参数状态的多个马尔可夫链序列,其中,每个可存储参数状态是多个测量参数的函数,其中,借助于所应用的模式识别,确定可存储参数状态的多个序列中的每个序列的加权因子和/或平均值和/或方差,并且从所使用的一组相等大小的所识别的时间帧中去除不相关的时间帧。该实施方式变型尤其具有以下优点:可以通过训练多维数据结构的可变隐马尔可夫模型参数来优化收敛速度。因此,模式识别和加权因子允许通过将所测量的数据样本与参考数据进行比较来应用噪声数据样本中的每个变量的相关异常度量,即使当变量中的一些变量高度相关时也是如此。因此,可以通过集中于每个变量的最重要的依赖关系来去除由噪声引入的虚假依赖关系。例如,可以通过拟合稀疏图形高斯模型作为最大似然估计来以自适应方式执行邻域选择。然后可以通过拟合的条件分布之间的距离来生成每个测量参数的相关异常度量。
18.在实施方式变型中,生成作为数字信号或脉冲的选通信号,从而提供适当的时间窗,其中,从测量数据的许多测量的时间帧中选择新测量的传感器数据的发生的异常时间帧,并且正常时间帧会被消除或丢弃,并且其中,对发生的异常时间帧的选择触发适当的信令生成以及到所分配的警报和/或监视和/或控制/操纵装置的转换。该实施方式变型尤其具有以下优点:它通过生成如下适当的操纵信令来允许有效的机器间信令,该操纵信令控制由所检测到的工业设备或生产工厂中的设备故障的异常或早期指示触发的相关联装置的操作。
19.在再一实施方式变型中,用于自动检测工业设备或生产工厂中设备故障的异常或早期指示的上述方法和系统应用于智能的、自适应的闭环和开环控制方法,该方法用于磨机工厂和/或磨机工厂的辊系统的研磨线的自优化控制的闭环和/或开环控制装置,其中,研磨线包括多个处理单元,多个处理单元可借助于闭环和开环控制装置各自单独驱动,并且在其操作期间可基于操作过程参数单独调节,其中,闭环和开环控制装置包括基于上述用于检测异常的方法的模式识别模块,控制装置的操作由模式识别模块的信令触发,并且其中,基于所发送的触发信号借助于控制装置来操纵和调整磨机工厂的操作。作为变型,例如,闭环和/或开环控制装置可以包括在处理单元中具有定义的处理序列的批控制器,其可借助于操作性过程配方和控制装置进行调节,其中,可借助于操作性过程配方从一种或更多种起始材料生产定义数量的最终产品,其中,基于与操作性过程配方具体相关联的操作性批过程参数来控制处理单元,并且其中,借助于控制装置基于新测量的传感器数据的一个或更多个发生的和检测到的异常时间帧来调整或优化操作批控制器。例如,控制装置还可以包括第二模式识别模块,该第二模式识别模块用于识别具有多维批过程参数模式的操作性过程配方,其中,操作性过程配方包括至少一种或更多种起始材料、研磨线的处理单元内的研磨过程的定义的序列、以及与研磨线的各个处理单元相关联地存储的操作性批过程参数,其中,闭环和开环控制装置包括用于存储具有历史批过程参数的历史操作性过程配方的存储器装置,其中,过程配方的历史批过程参数各自定义正常范围内的优化的批过程的过程典型的、多维批过程参数模式,其中,新的操作性过程配方的输入导致借助于由模式
识别模块基于相关联的多维批过程参数模式进行的模式识别,触发和/或选择所存储的历史操作性过程配方中的一个或更多个作为最接近的批过程参数模式,并且其中,在借助于控制装置基于触发的最接近的批正常过程参数模式检测到新测量的传感器数据的一个或更多个发生的异常时间帧时,借助于闭环和开环控制装置生成具有新的批过程参数的新的批过程参数模式,基于生成的具有相关联的批过程参数的操作性过程配方在适当时借助于闭环和开环控制装置致动和调节处理单元。该实施方式变型尤其具有以下优点:允许提供用于辊系统的研磨线的自动优化和控制的智能的、自适应的开环/闭环控制装置,辊系统的研磨线可以用来以优化且自动的方式执行研磨和/或碾碎,并且提高了磨机的可靠性并同时优化操作或者对发生的异常自动作出反应。
20.注意,作为现场装置的传感器和测量装置用于感测或控制工业过程中的工业设备或工厂的过程变量。然而,在一些装备中,可能期望监视现场装置的局部环境。此外注意,例如,异常检测系统或方法可以包括附加的阈值评估器模块,以针对相应传感器信号中的一个或更多个存储每个接收的技术状态数据的上阈值和下阈值。阈值评估器将所接收到的技术状态数据与阈值进行比较,并且如果相应的数据值落在由相应的上阈值和下阈值限定的区间之外,则不管异常检测系统或方法的评估如何生成特定技术状态数据的异常指示。换言之,基于阈值的传感器数据评估可以为异常指示的检测提供捷径。如果特定技术状态数据值位于由上下阈值限定的容差范围之外,则无论异常检测提供的结果如何都立即检测相应的异常指示。例如,阈值可以(例如,由操作者)基于先前经验预先定义,或者阈值作为捷径值可以由机器学习模块根据历史传感器数据学习。
21.本发明的其他方面将借助于所附权利要求中特别描绘的元素和组合来实现和获得。应理解,前面的一般描述和以下详细描述二者仅是示例性和说明性的,而不是对所描述的本发明的限制。
附图说明
22.将参照附图通过示例的方式更详细地说明本发明,在附图中:
23.图1示出了示意性地示出工业工厂中的监视和适应过程的图,具有用于工业工厂的自优化控制的智能、自适应控制装置。
24.图2示出了示意性地示出工业工厂中的监视和适应过程的图。来自传感器的数据例如每3分钟被定期发送。
25.图3至图12示出了根据图2的示例性工厂的优质研磨部分中的工厂故障/暂停事件(停机时间)。在操作状态概述中示出了由于研磨/清洁/第一清洁部分中的机械误差而导致的主要故障暂停事件。分别针对2017年和2018年的示例性数据示出了单个传感器级别下的频繁故障。在磨机级别部分处以及针对各个传感器示出了异常。还示出了用于优化和预防性维护的信令。
26.图3示出了示意性地示出在2017年至2018年的时间段内示例性磨机产量的监视的图。
27.图4示出了示意性地示出在2017年至2018年的时间段内示例性f1产量的监视的图。
28.图5示出了示意性地示出在2017年至2018年的时间段内示例性研磨部分研磨暂停
汇总的监视的图。在该示例中,2018年的暂停事件总数为80,总持续时间为2天27小时11分钟。研磨部分中的最长暂停为2018年1月1日的14小时51分钟。2017年的暂停事件总数为275,总持续时间为9天8小时58分钟。总和不包括丢失的事件。
29.图6a至图6o示出了示意性地示出在2017年11月01日至11月30日的时间段内示例性研磨工厂的误差监视的图。
30.图7示出了示意性地示出在2017年至2018年的时间段内示例性研磨工厂的误差监视频率汇总的图。该图按周数示出了第二清洁部分(mueps001)、研磨部分(mueps002)和第一清洁部分(re1ps001)机械误差故障的工厂暂停事件。上面绘制了大于10分钟的丢失数据。竖直条指示故障何时发生并被放大(15h)以使得短时间尺度的故障事件可见。较粗的竖直线指示较长的故障事件或者靠近在一起的几个短故障事件。不包括短于3分钟的故障(每3分钟采样数据)。
31.图8a和图8b示出了示意性地示出2018年的按持续时间划分的示例性前10个故障警报的图。
32.图9示出了示意性地示出在2017年至2018年的时间段内示例性工厂的清洁部分中的误差监视的图。如果对分拣机需要预防性维护或进一步监视,则本发明的系统和方法允许生成信令。本发明的异常检测方法能够识别需要预防性维护或监视的设备。该图示出了一些初步结果,其中对于清洁部分用橙色标记异常周。图9示出了检测到异常故障频率的初步结果。竖直条指示故障何时发生并略微被放大以使短时间尺度的故障事件可见。颜色条指示每个故障信号的分类。假定标记为灰色的时间段是典型的工厂操作。标记为蓝色的时间段被分类为正常操作,并且标记为橙色的周被分类为异常。丢失的数据时间段被分类为正常操作并未被指示。请注意,分拣机、高位传感器
‑
wt、流量平衡器203和清洁部分仅是不同机器的示例。因此,在图9中,分拣机还可以更一般地被引用为整个系统的“机器1”,高位传感器
‑
wt被引用为“机器2”,流量平衡器203被引用为“机器3”,并且清洁部分被引用为“机器4”。
33.图10示出了示意性地示出通过工厂中的传感器位置对示例性研磨工厂的清洁部分中的误差监视的图。具有形式a
‑
xxxx的附图标记表示在研磨工厂的清洁部分的操作期间捕获测量数据的传感器和测量装置,并且在处理中的不同位置中被采用。
34.图11示出了示意性地示出通过重量秤和流量平衡器对示例性研磨工厂的清洁部分中的误差监视的图。
35.图12示出了示意性地示出传感器数据和测量数据中的误差/故障相关性的图。本发明的用于检测工厂的操作的异常的控制装置的系统和新颖方法能够处理大量的相关性和传感器值。图12的和弦图o示出了同时发生的故障,这意味着机械故障之间的可能相关性。
36.图13示出了示意性地示出具有过程数据的二进制转换的本发明的实施方式变型的图。通常,时间序列异常检测算法依赖于阈值和移动平均值或类似值来检测异常。结果可能是由于振荡/噪声信号(工业过程中的典型情况)而检测到太多异常事件。在本发明中,某人可以调节阈值以具有或多或少的灵敏度(参见图13,其中异常由竖直线标记)。将已经超过阈值的事件中的每一个取为真/1值(否则为假/0)以生成二进制序列。这使得能够查看阈值交叉的频率,以便可以基于异常频率对异常进行分类。技术优点是不需要担心阈值和振
荡/噪声工业iot数据的过度灵敏性。
37.图14示出了示意性示出过程数据的异常检测的图,其中,在第一步骤中,基于应用于过程数据的阈值来生成二进制序列(参见图14)。在第二步骤中,将本文中描述的异常检测应用于二进制序列,并且相应地标记异常时间段。将模拟信号异常转换为二进制向量然后应用根据本发明的统计hmm(隐马尔可夫模型)异常检测结构在技术上是唯一的,并且不能从任何现有技术系统中得出。
38.图15示出了示意性地示出基于停机时间和误差传感器数据的过程数据的异常检测的其他图,其中左列示出了随时间各个部分内的停机时间测量,并且右列在上图中示出了测量的所有机器的机器故障,中间图是机器的误差时间,并且下图是按天测量的误差频率。
39.图16示出了示意性地示出图15所示示例的传感器数据和测量数据中的误差/故障相关性的其他图。图16示出了用于触发源自工业过程中使用的部件的传感器数据或测量数据来检测工业设备或生产工厂中设备故障的异常或早期指示的本发明的系统和方法如何允许基于检测的和测量的警报频率以及相关性和异常来提供适当的操纵信号。因此,本发明的系统允许如下操作的技术上全新的方式:触发警报事件之间的相关性、和/或及时使警报事件可视化、和/或对异常停机时间/警报的异常检测、和/或警报回放以及相应的电子信令生成。
40.附图标记列表
41.1 工业设备/生产工厂
42.11 生产线
43.12 工厂停机时间
44.13 监视装置
45.14 控制/操纵装置
46.15 警报装置
47.2 测量装置/传感器
48.3 相等大小的时间帧
49.31 异常时间帧
50.4 测量和/或过程参数
51.41 传感器参数/测量参数
52.42 过程变量
53.43 异常传感器数据值
54.5 工业处理部件/工业装置
55.6 工业过程
56.61 发生的警报事件
57.611 发生的警报事件的频率
58.612 发生的警报事件的频率模式
59.7 用于检测工业设备或生产工厂中的设备故障的异常或早期指示的系统
60.71 监视装置
61.8 机器学习模块
62.81 多维数据结构
63.811、812、
……
、81x 可变隐马尔可夫模型参数值
64.821、822、
……
、82x 可存储马尔可夫链状态
65.831、832、
……
、83x 训练的模型参数
66.82 发生的警报事件的正常状态频率
67.83 概率状态值
68.84 对数阈值
69.841 异常得分
70.85 对数结果值
71.86 预定义的收敛阈值
72.9 二进制转换器/微分器
73.91 二进制处理码
74.911 生成的二进制处理码
75.912 预采样的二进制处理码
76.92 阈值
再多了解一些
本文用于企业家、创业者技术爱好者查询,结果仅供参考。